3. Sizing the Cogeneration Plant
Total Page:16
File Type:pdf, Size:1020Kb
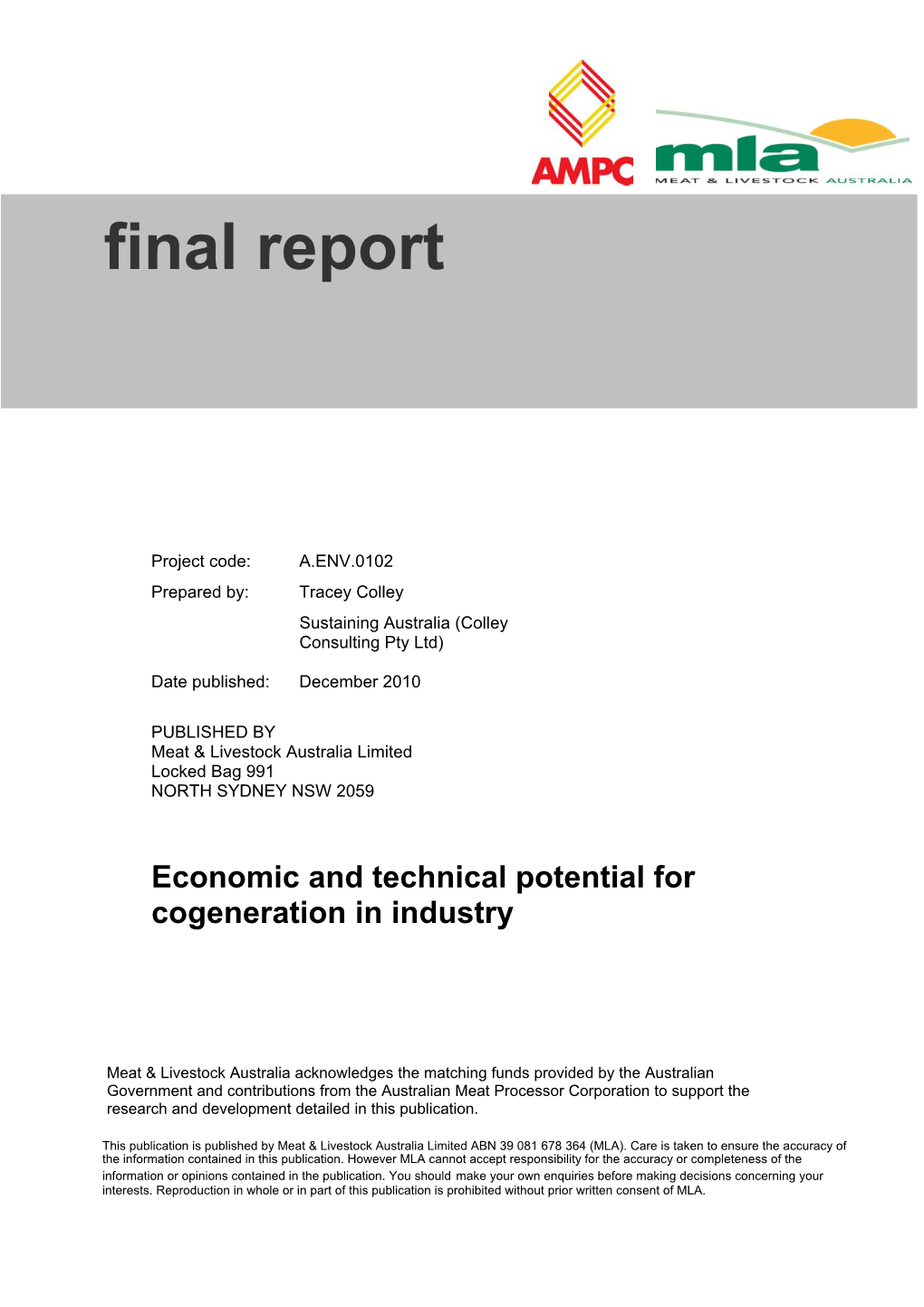
Load more
Recommended publications
-
Energy 2020 (Report 11: 2020–21)
FINANCIAL AUDIT REPORT 4 February 2021 Energy 2020 Report 11: 2020–21 • Queensland • • Audit Office Better public services As the independent auditor of the Queensland public sector, including local governments, the Queensland Audit Office: • provides professional audit services, which include our audit opinions on the accuracy and reliability of the financial statements of public sector entities • provides entities with insights on their financial performance, risk, and internal controls; and on the efficiency, effectiveness, and economy of public service delivery • produces reports to parliament on the results of our audit work, and on our insights, advice, and recommendations for improvement • conducts investigations into claims of financial waste and mismanagement raised by elected members, state and local government employees, and the public • shares wider learnings and best practice from our work with state and local government entities, our professional networks, industry, and peers. We conduct all our audits and reports to parliament under the Auditor-General Act 2009 (the Act). Our work complies with the Auditor-General Auditing Standards and the Australian standards relevant to assurance engagements. • Financial audit reports summarise the results of our audits of over 400 state and local government entities. • Performance audit reports cover our evaluation of some, or all, of the entities’ efficiency, effectiveness, and economy in providing public services. Depending on the level of assurance we can provide, these reports may also take the form of: • Audit insights, which provide some evaluation and share our insights or learnings from our audit work across government • Audit briefs, which set out key facts, involve some evaluation, and may include findings and recommendations • Audit overviews, which help clients and stakeholders understand complex issues and subjects. -
Demand Management Plan 2021-22
Demand Management Plan April 2021 Demand Management Plan 2021-22 Contents Message from our Executive 3 About us 4 Introduction 4 Our network 4 Our core service area 5 Demand management 6 What is it? 6 Customers participating in our DM Program 8 Challenges and opportunities shaping our strategies and plan 9 Case study: The challenges caused by minimum demand 12 Our strategy and plan 14 Overview 14 Our principles 14 Case study: Electric vehicles - Discovering customer charging and energy use 15 Our strategies and initiatives 16 Case study: New load control tariffs deliver customer and network benefits 17 Our program 18 DM Program budget and targets for 2021-22 20 Covid-19 impacts 20 Energex forecast expenditure and targets 20 Ergon Energy Network forecast expenditure and targets 20 2 Demand Management Plan 2021-22 Message from our Executive We are experiencing (DER) such as rooftop solar PV This Plan sets out our five-year unprecedented rates of customers and Electric Vehicles (EVs). This strategy for our DM program connecting small scale renewables will support greater DER on during this time of transformation. such as rooftop solar photovoltaic our network, new technologies Our Plan is only as strong as our (PV) systems, along with such as batteries and EVs and partnerships with our customers, large scale renewables (solar access to new markets that offer DM providers and other industry farms and wind farms) to our incentives to customers for their partners. We therefore look network. It’s not slowing down; services. Dynamic customer forward to continuing to work if anything, COVID-19 and the connections for DER will also with our existing and new conditions of the past year have support distribution networks customers during 2021-22 and only accelerated the take up of in providing safe and secure beyond; as we energise our renewables across the network. -
The Coopers Family Tasting Notes
The Coopers family tasting notes. A family owned Australian icon, Coopers Brewery has been passionately brewing a range of unique and original beers for six generations, which are enjoyed all around the world. Drinking and tasting a Coopers beer is an experience in discovering a beer full of character and flavour. Coopers strives to bring joy to the drinker from the first instant you see the glass being filled to the time when you drain the last drop. Coopers beers are enjoyed for far more than just how they taste. How a Coopers beer appears so attractive in the glass, and how they taste when you drink one, is all to be savoured as part of the tasting experience. Coopers produces a variety of beers, from low alcohol lagers through to stronger ales and stouts. Coopers are known for their natural conditioned (bottle fermented) Ales. This traditional method has been used at Coopers since 1862 and gives these beers their cloudy appearance. After fermentation, a special technique of natural conditioning the same strain of yeast used for the primary fermentation is used and added to the beer prior to it being packed into bottles, cans or kegs using state of the art equipment. A secondary fermentation and natural conditioning is then carried out in the package in such a way that the yeast is maintained in a healthy state during this second fermentation. Come and meet the whole family and discover the background to the beers and why they have been loved and appreciated since Thomas Cooper first made them in 1862. -
Case Study Sparq Solutions
CASE STUDY SPARQ SOLUTIONS Technology: Windows® 7 and Microsoft® Office® Managed 2010, from older operating systems Windows 7 and Office suites. The aim of the Productivity Managed Productivity Program is to Microsoft Office 2010 realise the productivity benefits enabled Program Returns by Windows 7 and Office 2010. $3.9m a Year A preliminary business case suggested that this project would Background: deliver more than $1.5 million in productivity benefits annually. SPARQ Solutions provides Information and Communications Technology (ICT) The Windows 7 and Office 2010 services to Queensland’s electricity upgrade program scoped to replace suppliers, Energex and Ergon Energy. and upgrade the technology, did not include an instructor-led classroom SPARQ partners closely with Energex training program but relied upon and Ergon Energy to achieve their users maintaining their exisiting business goals by developing ICT level of competency through local strategies that enable business change support groups and self-help. and growth. Being jointly owned by Energex and Ergon Energy enables This resulted in the a disconnect SPARQ to provide value for money between the migration activity and the to all Queenslanders through provision of training support to users, cost-savings, economies of scale and which meant that the productivity value-added solutions and services. benefits would not be realised, and in fact productivity would be reduced With headquarters in Brisbane, and if users were less effective in the offices in Rockhampton, Townsville, new operating environment. Mackay, Maryborough, Cairns and Toowoomba, SPARQ employs The Solution: approximately 500 staff and contractors who are highly skilled in To develop an enterprise-wide program a range of ICT business applications of user education and training support, and support services, and who SPARQ Solutions’ Applications Capability support more than 8,000 users. -
Detailed Plan of Development December 2016
Department of Infrastructure, Local Government and Planning Yeerongpilly Transit Oriented Development Detailed Plan of Development December 2016 Yeerongpilly TOD Detailed Plan of Development 1 © State of Queensland, December 2016. Published by the Department Infrastructure, Local Government and Planning, 1 William Street, Brisbane Qld 4000, Australia Licence: This work is licensed under the Creative Commons CC BY 4.0 Australia licence. To view a copy of the licence, visit www.creativecommons.org/licenses/by/4.0/. Enquiries about this licence or any copyright issues can be directed to the department by email to [email protected] or in writing to PO Box 15009, City East, Qld 4002. Attribution: The State of Queensland, Department Infrastructure, Local Government and Planning. The Queensland Government supports and encourages the dissemination and exchange of information. However, copyright protects this publication. The State of Queensland has no objection to this material being reproduced, made available online or electronically but only if it is recognised as the owner of the copyright and this material remains unaltered. Disclaimer: While every care has been taken in preparing this publication, the State of Queensland accepts no responsibility for decisions or actions taken as a result of any data, information, statement or advice, expressed or implied, contained within. To the best of our knowledge, the content was correct at the time of publishing. An electronic copy of this report is available on the Department of Infrastructure, Local Government and Planning’s website at www.dilgp.qld.gov.au. Contents PART A: Introduction and background PART B: Detailed Plan of Development Figures 1. -
Kosher Certificate
KC# 137933 - 1 23 Tamuz, 5775 July 10, 2015 Coopers Brewery Ltd 461 South Road Regency Park South Australia 5010 AUSTRALIA (t) +618 8440 1800 (f) +618 8440 1888 www.coopers.com.au The following products sold by Coopers Brewery Limited are certified Kosher with the listed restrictions. Name K-ID Status Restriction Size Amber Malt VHJ-KQML Pareve No Marking Required Brooklyn Lager SXK-HSXC Pareve No Marking Required Caramalt DZB-QCSN Pareve No Marking Required Carlsberg Lager VVK-HHVQ Pareve No Marking Required Coopers Australian Bitter Homebrew Concentrate MWW-VXSL Pareve No Marking Required Coopers Australian Pale Ale Homebrew Concentrate KSN-TCGM Pareve No Marking Required Coopers Best Extra Stout Beer STD-CRTD Pareve No Marking Required Coopers Birell Brewed Soft Drink XKT-PJWQ Pareve No Marking Required Coopers Canadian Blonde Homebrew Concentrate GQM-FGTG Pareve No Marking Required Coopers Celebration Ale NJH-ZGBH Pareve No Marking Required Coopers Dark Ale Beer FMT-CLFH Pareve No Marking Required Coopers Dark Ale Homebrew Concentrate RPC-TDJH Pareve No Marking Required Coopers Draught Homebrew Concentrate GMZ-TZWR Pareve No Marking Required Coopers English Bitter Homebrew Concentrate JVT-HNPM Pareve No Marking Required Coopers European Lager Homebrew Concentrate GPG-JZGJ Pareve No Marking Required Coopers Extra Strong Vintage Ale Beer FHM-SFKP Pareve No Marking Required 15.221 This certificate is VALID UNTIL July 1, 2016 Verify authenticity by entering K-ID at www.digitalkosher.com Rabbi Mordechai Gutnick, Rabbinic Administrator KC# 137933 - 2 23 Tamuz, 5775 July 10, 2015 Coopers Brewery Ltd 461 South Road Regency Park South Australia 5010 AUSTRALIA (t) +618 8440 1800 (f) +618 8440 1888 www.coopers.com.au The following products sold by Coopers Brewery Limited are certified Kosher with the listed restrictions. -
Australia's Winning Serve
AUSTRALIA’S WINNING SERVE COOPERS 2017 ANNUAL REPORT COOPERS ANNUAL REPORT 2017 II PLAYING TO OUR STRENGTHS From Grand Slam tennis in Melbourne to a barbecue under the stars in the outback, as the nation’s only locally-owned major brewery, you can be sure that Coopers will be serving for Australia… and for every Australian. COOPERS ANNUAL REPORT 2017 1 CONTENTS 3 Highlights 20 Non-alcoholic 4 Chairman and Managing Director’s Report 20 DIY Beer 6 Beer Industry Update 20 Malt Extract 8 Capex 21 BrewArt 8 Work Health and Safety 22 Morgan’s 8 Training 22 Mr Beer 10 Sponsorship 23 Awards 12 Marketing 24 Shareholders 14 Premium Beverages 24 155th Celebration 15 Partner Brands 24 Vale 16 Vintage 25 6th Generation 17 Airport Alehouse 26 Foundation 18 New Products 28 Guiding Principles COOPERS ANNUAL REPORT 2017 2 HIGHLIGHTS New $65 million malting plant under construction Total beer sales reach a record 83.8 million litres, the 24th consecutive year of growth First year as the official beer and cider sponsor for the Australian Open, one of the world’s four Grand Slam tennis tournaments BrewArt system wins 2016 Canstar Blue Innovation Excellence Award Coopers Original Pale Ale wins ALIA award for ninth time in 10 years Limited edition Amber Ale and Legends Summer Lager launched Reduction in injury rates Coopers Brewery Foundation launches new sustainable giving program and passes $4 million mark in donations Directors and Shareholders celebrated the 155th Anniversary of Thomas Cooper’s first brew New packaging for Coopers Premium Lager and Coopers Premium Light COOPERS ANNUAL REPORT 2017 3 CHAIRMAN AND MANAGING DIRECTOR’S REPORT Coopers Brewery achieved a further year of sales growth during 2016–17, with beer sales rising 2.9% to a record 83.8 million litres. -
WORKING with ENERGEX Now Locate Faults in the Network Faster Than Ever Before Through Satellite Navigation, Tracking and Dispatch
a number of ENERGEX’s host systems. ENERGEX crews WORKING WITH ENERGEX now locate faults in the network faster than ever before through satellite navigation, tracking and dispatch. The FFA In an Australian first, ENERGEX crews are now computer system provides field crews with unprecedented access to electronic information about outages and using high-tech mobile-linked laptop computer customer premises from their vehicle. The reduction in systems in maintenance vehicles to help them phone calls, travel time and paper will help increase restore power faster after outages. An industry efficiency significantly during storms and other peak periods. Millions of people across more than 25,000 team made up of Integral, ENERGEX, SPARQ, square kilometres throughout South East Queensland LiTMUS Group, MDSI – Advantex (now Ventyx) and northern New South Wales now benefit from the and led by prime contractor TUSC (now Ericsson), new system that provides faster response times and more accurate information to field crews. was the key to the success of this project. INTEGRAL VALUE ADD Based in South East Queensland, ENERGEX has been providing electricity to Queenslanders for more than Integral’s role in this project was to integrate the Ventyx 100 years. ENERGEX manages sophisticated energy Service Suite FFA technology with the existing ENERGEX distribution networks and delivers world-class energy host systems. products, services and expertise to one of Australia’s fastest growing communities. “This was a particularly rewarding project for Integral as it extensively used our integration methodologies, THE CHALLENGE intellectual property and best practice based ENERGEX had a low level automation system in place approaches, to build a robust and scalable SOA for its field workers that was not handling the increased (Service Orientated Architecture) based solution. -
Performance and Plans for the Energex Network
Performance and plans for the Energex Network A summary of our Distribution Annual Planning Report 2019-20 to 2023-24 for our customers, communities and other stakeholders Purpose Energex’s Distribution Annual 2023-24. It provides insights benefit from significant Planning Report explains how into the key challenges we face electricity supply capability we are continuing to safely and our responses to them, or demand side management and efficiently manage the highlighting the areas where we and non-network initiatives electricity distribution network are seeking to work closely with • identify locations where in South East Queensland. our customers, the community major industrial loads would and different industry partners. This summary outlines the be best located. content in our planning report It provides information to assist This information is also with links to specific chapters interested parties to: supported by our online you can refer to for more • understand how the interactive map of the information. electricity network works electricity network and The full report details the • provide input to the future information provided in our network’s performance in 2018- development of the network Demand Management Plan and Demand Side Engagement 19 and our plans for 2019-20 to • identify locations that would Strategy. Contents Purpose 2 Message from our Executive 3 Our network 4 Our service area 4 What is shaping our plans? 5 Our engagement program 5 Safety first – a no compromise approach 6 Making electricity more affordable 7 -
Fees & Charges Additional
ADDITIONAL FEES & CHARGES BEFORE & AFTER JULY 2019 A REPORT PRODUCED BY ALVISS CONSULTING FOR THE ST VINCENT DE PAUL SOCIETY VICTORIA DECEMBER 2019 For further information regarding this report, contact: Gavin Dufty Manager, Social Policy Unit St Vincent de Paul Society Victoria Phone: 03 9895 5816 or 0439 357 129 This report has been produced by: St Vincent de Paul Society Alviss Consulting www.vinnies.org.au/energy www.alvissconsulting.com 1. About this project This project has been undertaken to document and analyse the application of fees and charges to electricity retail contracts for residential consumers in NSW, Victoria, Queensland and South Australia before and after the introduction of the Victorian Default Offer (in Victoria) and the Default Market Offer (in other states) on 1 July 2019. Additional fees and charges applied to energy contracts can cause consumer detriment for two reasons: Firstly, additional fees and charges increase product complexity and the chance of consumers making poor decisions. Energy contracts are already complex products as consumers must understand their usage and needs when comparing offers. Additional fees and charges add another layer of complexity to this process and as some fees are linked to consumer behaviour or future decisions (e.g. late payment fees and early termination fees) it can be almost impossible to determine what offers are most suitable in the long run. Secondly, significant additional fees and charges can make up a substantial proportion of many households’ energy costs, particularly for low consumption households. This is problematic in a reform environment based on demand side participation where consumers are expected to take greater responsibility to reduce their energy costs. -
Coopers ANNUAL REPORT 2016 Contents
coopers ANNUAL REPORT 2016 Contents Highlights 3 Chairman & Managing Director’s Report 4 Vale 6 Capex 8 Awards 9 Vintage Ale Launch 10 New Products 11 Marketing 12 Sponsorship 14 Premium Beverages 16 Partner Brands 17 BrewArt 18 Morgan’s 20 Mr Beer 20 Malt Extract 20 DIY Beer 21 Non Alcoholic 21 Foundation 22 Health Safety Training 24 Time Out For The Team 25 Shareholders 26 Working With Others 27 2 Highlights Total beer sales reach a record 81.5 million litres Construction of new malting plant underway BrewArt system launched Coopers Original Pale Ale wins ALIA award for eighth time in nine years Carlsberg Mid and FIX Hellas added to international beer portfolio New packaging for Coopers Clear and Thatchers Gold Launch of new DIY beer concentrate range Limited edition “Brew A” IPA launched as a keg offering Coopers supports ISPS Handa Women’s Australian Open golf tournament 3 Chairman & Managing Director’s Report Dr Tim Cooper AM (left) Glenn Cooper AM (right) 4 Continued sales growth and the introduction of Carlsberg Mid to our international portfolio highlighted a solid year for Coopers during 2015–16. Total beer sales rose 3.3% for the year to It also marks Coopers’ return to the malting a record 81.5 million litres. This is the 23rd business after the sale in 2002 of Adelaide consecutive year of improvement, representing Malting Company to Ausbulk, undertaken a compound annual growth rate of 9.2%. to lessen debt arising from the move from Leabrook to Regency Park. In a national market which grew modestly for the year, our packaged beer volumes rose by In February, Coopers added Carlsberg Mid 3.8%, while keg volumes recorded a pleasing, 3.5% lager to its international beer portfolio. -
Brewing Support for the Community CHAIRMAN’S REPORT
COOPERS BREWERY FOUNDATION 2015 Annual Report Brewing support for the community CHAIRMAN’S REPORT It is my pleasure to report on the Coopers Brewery Foundation activities for the 2014-2015 year. Matthew Cooper Prime Minister’s Community Business Partnership COOPERS BREWERY FOUNDATION 2015 ANNUAL REPORT I make special mention at the beginning of human clinical trials, in pursuit of a gene their time and eorts. The Committee was further The Governors of the this report of the people who contribute so therapy-based cure for the disease. assisted by Financial Controller Brad Grunert much to our Foundation. Firstly, to note the when he joined as Secretary in March, following In addition, members of sta generously donated Foundation act in an Jim’s retirement. The income raised from the sad passing on Christmas Eve 2014 of Matthew over $15,000 from regular salary deductions, honorary capacity Cooper, a Governor who served on the Board and as a suitable recipient of those funds, the Investment Fund pays the Executive Ocer’s for more than three years. Matthew lost his Governors selected Southern Cross Kids Camps, part-time salary and the surplus is reinvested. battle with cancer after a long struggle, but his GOVERNORS assisting children to overcome the cycle of abuse. Last September, I was appointed to the commitment and passion for the Foundation 3 Our suppliers and Friends have also continued reinstated Prime Minister’s Community Business never diminished during that fight. Donations to support the Foundation with donations of Partnership. This small group of like-minded made in Matthew’s memory exceeded $20,000 $210,000, and special mention goes to Bill and business philanthropists and politicians are and the proceeds were donated to Mary Potter Jo Cooper, Castlegate James and Allianz.