Morphing Aircraft Technology – New Shapes for Aircraft Design
Total Page:16
File Type:pdf, Size:1020Kb
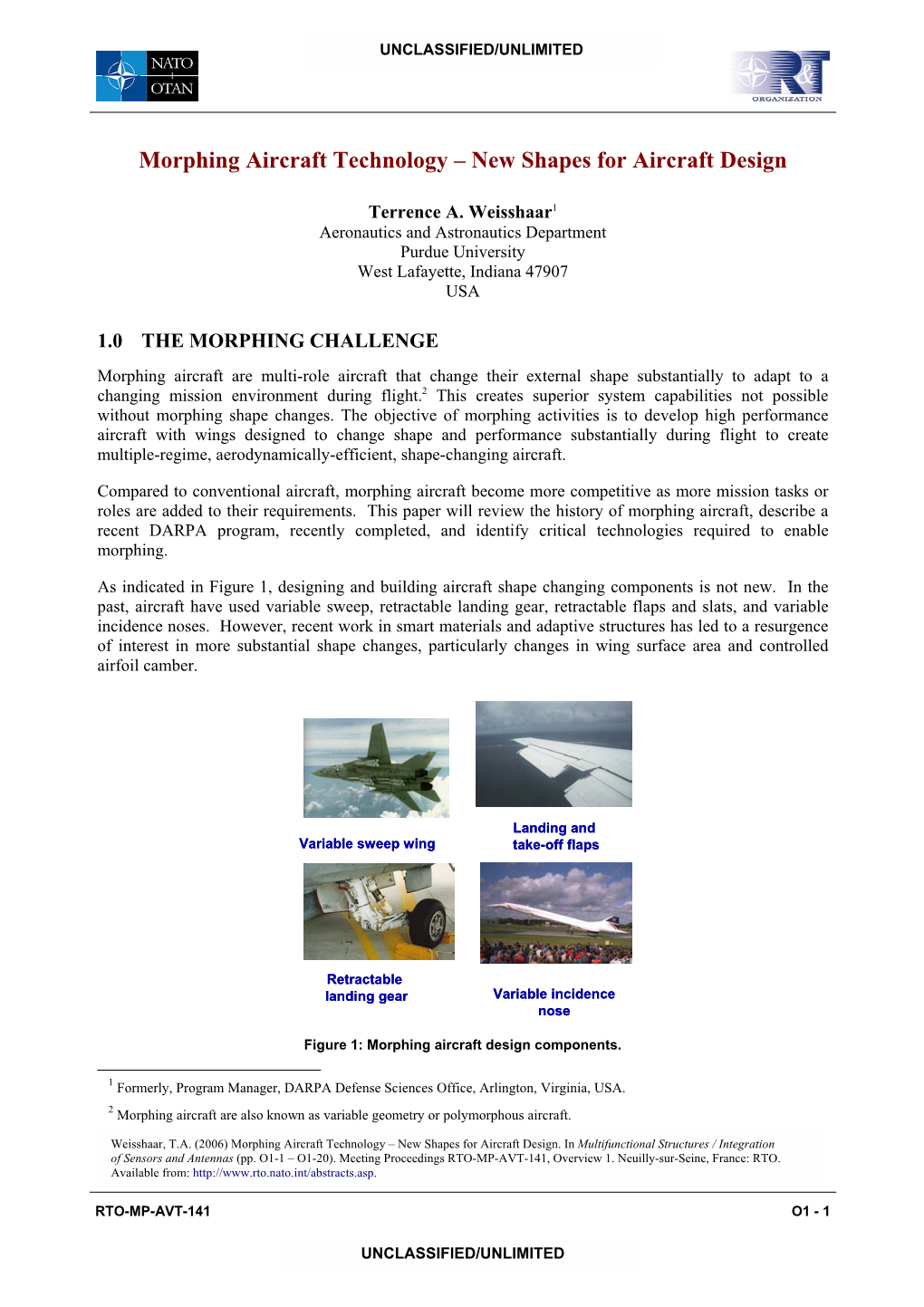
Load more
Recommended publications
-
LESSON 3 Significant Aircraft of World War II
LESSON 3 Significant Aircraft of World War II ORREST LEE “WOODY” VOSLER of Lyndonville, Quick Write New York, was a radio operator and gunner during F World War ll. He was the second enlisted member of the Army Air Forces to receive the Medal of Honor. Staff Sergeant Vosler was assigned to a bomb group Time and time again we read about heroic acts based in England. On 20 December 1943, fl ying on his accomplished by military fourth combat mission over Bremen, Germany, Vosler’s servicemen and women B-17 was hit by anti-aircraft fi re, severely damaging it during wartime. After reading the story about and forcing it out of formation. Staff Sergeant Vosler, name Vosler was severely wounded in his legs and thighs three things he did to help his crew survive, which by a mortar shell exploding in the radio compartment. earned him the Medal With the tail end of the aircraft destroyed and the tail of Honor. gunner wounded in critical condition, Vosler stepped up and manned the guns. Without a man on the rear guns, the aircraft would have been defenseless against German fi ghters attacking from that direction. Learn About While providing cover fi re from the tail gun, Vosler was • the development of struck in the chest and face. Metal shrapnel was lodged bombers during the war into both of his eyes, impairing his vision. Able only to • the development of see indistinct shapes and blurs, Vosler never left his post fi ghters during the war and continued to fi re. -
Wing-Folding Mechanism of the Grumman Wildcat
WING-FOLDING MECHANISM OF THE GRUMMAN WILDCAT An American Society of Mechanical Engineers Historic Mechanical Engineering Landmark DESIGNATION CEREMONY AT THE KALAMAZOO AVIATION HISTORY MUSEUM KALAMAZOO, MICHIGAN May 15, 2006 A Mechanical Engineering Landmark The innovative wing folding mechanism (STO-Wing), developed by Leroy Grumman in early 1941 and first applied to the XF4F-4 Wildcat, manufactured by the Grumman Aircraft Engineering Corporation, is designated an ASME Historic Mechanical Engineering Landmark. (See Plaque text on page 6) Grumman People Three friends were the principal founders of the Grumman Aircraft Engineering Corporation (Now known as Northrop Grumman Corporation), in January 1930, in a garage in Baldwin, Long Island, New York. (See photo of Leon Swirbul, William Schwendler, and Leroy Grumman on page 7) Leroy Randle (Roy) Grumman (1895-1982) earned a Bachelor of Science degree in mechanical engineering from Cornell University in 1916. He then joined the U. S. Navy and earned his pilot’s license in 1918. He was later the Managing Director of Loening Engineering Corporation, but when Loening merged with Keystone Aircraft Corporation, he and two of his friends left Loening and started their own firm — Grumman Aircraft Engineering Corporation. William T. Schwendler (1904-1978) earned a Bachelor of Science degree in mechanical engineering from New York University in 1924. He was reluctant to leave Long Island, so he chose to join Grumman and Swirbul in forming the new company. Leon A. (Jake) Swirbul (1898-1960) studied two years at Cornell University but then left to join the U.S. Marine Corps. Instrumental in the founding and early growth of Grumman, he soon became its president. -
5.2 Drag Reduction Through Higher Wing Loading David L. Kohlman
5.2 Drag Reduction Through Higher Wing Loading David L. Kohlman University of Kansas |ntroduction The wing typically accounts for almost half of the wetted area of today's production light airplanes and approximately one-third of the total zero-lift or parasite drag. Thus the wing should be a primary focal point of any attempts to reduce drag of light aircraft with the most obvious configuration change being a reduction in wing area. Other possibilities involve changes in thickness, planform, and airfoil section. This paper will briefly discuss the effects of reducing wing area of typical light airplanes, constraints involved, and related configuration changes which may be necessary. Constraints and Benefits The wing area of current light airplanes is determined primarily by stall speed and/or climb performance requirements. Table I summarizes the resulting wing loading for a representative spectrum of single-engine airplanes. The maximum lift coefficient with full flaps, a constraint on wing size, is also listed. Note that wing loading (at maximum gross weight) ranges between about 10 and 20 psf, with most 4-place models averaging between 13 and 17. Maximum lift coefficient with full flaps ranges from 1.49 to 2.15. Clearly if CLmax can be increased, a corresponding decrease in wing area can be permitted with no change in stall speed. If total drag is not increased at climb speed, the change in wing area will not adversely affect climb performance either and cruise drag will be reduced. Though not related to drag, it is worthy of comment that the range of wing loading in Table I tends to produce a rather uncomfortable ride in turbulent air, as every light-plane pilot is well aware. -
Subsonic Aircraft Wing Conceptual Design Synthesis and Analysis
View metadata, citation and similar papers at core.ac.uk brought to you by CORE provided by GSSRR.ORG: International Journals: Publishing Research Papers in all Fields International Journal of Sciences: Basic and Applied Research (IJSBAR) ISSN 2307-4531 (Print & Online) http://gssrr.org/index.php?journal=JournalOfBasicAndApplied --------------------------------------------------------------------------------------------------------------------------- Subsonic Aircraft Wing Conceptual Design Synthesis and Analysis Abderrahmane BADIS Electrical and Electronic Communication Engineer from UMBB (Ex.INELEC) Independent Electronics, Aeronautics, Propulsion, Well Logging and Software Design Research Engineer Takerboust, Aghbalou, Bouira 10007, Algeria [email protected] Abstract This paper exposes a simplified preliminary conceptual integrated method to design an aircraft wing in subsonic speeds up to Mach 0.85. The proposed approach is integrated, as it allows an early estimation of main aircraft aerodynamic features, namely the maximum lift-to-drag ratio and the total parasitic drag. First, the influence of the Lift and Load scatterings on the overall performance characteristics of the wing are discussed. It is established that the optimization is achieved by designing a wing geometry that yields elliptical lift and load distributions. Second, the reference trapezoidal wing is considered the base line geometry used to outline the wing shape layout. As such, the main geometrical parameters and governing relations for a trapezoidal wing are -
F—18 Navy Air Combat Fighter
74 /2 >Af ^y - Senate H e a r tn ^ f^ n 12]$ Before the Committee on Appro priations (,() \ ER WIIA Storage ime nts F EB 1 2 « T H e -,M<rUN‘U«sni KAN S A S S F—18 Na vy Air Com bat Fighter Fiscal Year 1976 th CONGRESS, FIRS T SES SION H .R . 986 1 SPECIAL HEARING F - 1 8 NA VY AIR CO MBA T FIG H TER HEARING BEFORE A SUBC OMMITTEE OF THE COMMITTEE ON APPROPRIATIONS UNITED STATES SENATE NIN ETY-FOURTH CONGRESS FIR ST SE SS IO N ON H .R . 9 8 6 1 AN ACT MAKIN G APP ROPR IA TIO NS FO R THE DEP ARTM EN T OF D EFEN SE FO R T H E FI SC AL YEA R EN DI NG JU N E 30, 1976, AND TH E PE RIO D BE GIN NIN G JU LY 1, 1976, AN D EN DI NG SEPT EM BER 30, 1976, AND FO R OTH ER PU RP OSE S P ri nte d fo r th e use of th e Com mittee on App ro pr ia tio ns SPECIAL HEARING U.S. GOVERNM ENT PRINT ING OFF ICE 60-913 O WASHINGTON : 1976 SUBCOMMITTEE OF THE COMMITTEE ON APPROPRIATIONS JOHN L. MCCLELLAN, Ark ans as, Chairman JOH N C. ST ENN IS, Mississippi MILTON R. YOUNG, No rth D ako ta JOH N O. P ASTORE, Rhode Island ROMAN L. HRUSKA, N ebraska WARREN G. MAGNUSON, Washin gton CLIFFORD I’. CASE, New Je rse y MIK E MANSFIEL D, Montana HIRAM L. -
The Birth of Powered Flight in Minnesota / Gerald N. Sandvick
-rH^ AEROPLANE AUTOMOBILE MOTORCYCLE RACES il '^. An Event in the History of the Northwest-Finish Flight by Aeroplanes GLEN H. CURTISS and Seat> for 25,000 People at these Price* 'ml Tu'Wly •nvi>n Bou-a nr Otaod HtiiiKl T(o BARNEY OLDFIELD DON'T MISS IT F IniiiKp at (Irnnd HUnd Bpxti .... UD wbo have tnvclcd fMter than any othrr lium«ii hrintrn A MaKnili'-fi" Pronrtun-.t llinb Spctd F.viutft. Not a I'ull Monn.-iit G :l•"^ <n Mill) ttn rolu diiyi. Jiiiir ^i. 'iX it. Sb $SO.M in k rKRc from Start to Khiifth. Tlie latttt-st Aeropbinf. tlic K.isH-i.t Aiito Car, \ii'imin><-l'». iiineial ulmliminu. lio>, pukMl in ptrblns the Fu.^iest }|orst.' PitTeiJ AKanisi V.ach Otlur In H Gr«siil Triple Kacfl >ii-"lnii pm ant (ocnipim nr iLiii>ri'iiplM) BOC AEROPLANE vs. AUTOMOBaE K(>*prT>-il Urn'a en 8<ila, Hli>ii<Miyo11>, Mctre^llao UvMc Co., 41 OIdfl«i(i. with bu llghlr.inj Ben; r»r. ^nd Kimrbirr. BIKili ttu^'-i nnut). •)• r>U, Wir^ke « DfWTT. PltUl Ud Bohert. wUb bU DuTtcq ckr, bgalnit world t rn^'irds on » iir VxT .-•n.-xil iilnnuti.-n mrtrnr. WnlUr B Wllmot. OMWtkl outar tfftck WALTER R. WILMOT. General Mqr. M.u.k.. %:. iii.i llmi-r, Miiiiif.'MI* T 0 Phooe, ABHM IT*. THE BIRTH OF POWERED FLIGHT IN MINNESOTA Gerald N. Sandvick AVIATION in Minnesota began in the first decade of the Aviation can be broadly divided into two areas: aero 20th century. -
Experimental Determination of Improved Aerodynamic Characteristics Utilizing Biplane Wing Configurations
Scholars' Mine Masters Theses Student Theses and Dissertations 1974 Experimental determination of improved aerodynamic characteristics utilizing biplane wing configurations Elmer Carl Olson Follow this and additional works at: https://scholarsmine.mst.edu/masters_theses Part of the Aerospace Engineering Commons Department: Recommended Citation Olson, Elmer Carl, "Experimental determination of improved aerodynamic characteristics utilizing biplane wing configurations" (1974). Masters Theses. 3426. https://scholarsmine.mst.edu/masters_theses/3426 This thesis is brought to you by Scholars' Mine, a service of the Missouri S&T Library and Learning Resources. This work is protected by U. S. Copyright Law. Unauthorized use including reproduction for redistribution requires the permission of the copyright holder. For more information, please contact [email protected]. EXPERIMENTAL DETERMI NATI ON OF IMPROVED AEROBYNAMIC CHARACTERI STICS UTI LI ZING BI PLANE ~<VING CONFIGURATIONS BY ELMER CARL OLSON , 1 949- A 'I'HESIS Presented t o the Facult y o f the Graduat e School o f t he UNIVERS I TY 0 F MISSOURI - ROLLA In Part ial Fu lfillment o f the Requi r ements f o r the Degree MASTER OF SCIENCE I N AE ROSPACE ENGINEERING 1974 T 2981 14 0 pages Ap prove d b y c.l 24081.7 ii ABSTRACT Improving the aerodynamic characteristics of an airplane wi th respect to a higher lift coefficient, a lower drag coefficient and a higher lift over drag ratio as a function of angle of attack will make it more efficient, thus conserving energy or improving performance. Investigations were carried out to determine if the aerodynamic characteristics of biplane wing systems could be made more efficient, for low subsonic speeds, than a monoplane of comparable area and aspect ratio . -
Aircraft of Today. Aerospace Education I
DOCUMENT RESUME ED 068 287 SE 014 551 AUTHOR Sayler, D. S. TITLE Aircraft of Today. Aerospace EducationI. INSTITUTION Air Univ.,, Maxwell AFB, Ala. JuniorReserve Office Training Corps. SPONS AGENCY Department of Defense, Washington, D.C. PUB DATE 71 NOTE 179p. EDRS PRICE MF-$0.65 HC-$6.58 DESCRIPTORS *Aerospace Education; *Aerospace Technology; Instruction; National Defense; *PhysicalSciences; *Resource Materials; Supplementary Textbooks; *Textbooks ABSTRACT This textbook gives a brief idea aboutthe modern aircraft used in defense and forcommercial purposes. Aerospace technology in its present form has developedalong certain basic principles of aerodynamic forces. Differentparts in an airplane have different functions to balance theaircraft in air, provide a thrust, and control the general mechanisms.Profusely illustrated descriptions provide a picture of whatkinds of aircraft are used for cargo, passenger travel, bombing, and supersonicflights. Propulsion principles and descriptions of differentkinds of engines are quite helpful. At the end of each chapter,new terminology is listed. The book is not available on the market andis to be used only in the Air Force ROTC program. (PS) SC AEROSPACE EDUCATION I U S DEPARTMENT OF HEALTH. EDUCATION & WELFARE OFFICE OF EDUCATION THIS DOCUMENT HAS BEEN REPRO OUCH) EXACTLY AS RECEIVED FROM THE PERSON OR ORGANIZATION ORIG INATING IT POINTS OF VIEW OR OPIN 'IONS STATED 00 NOT NECESSARILY REPRESENT OFFICIAL OFFICE OF EOU CATION POSITION OR POLICY AIR FORCE JUNIOR ROTC MR,UNIVERS17/14AXWELL MR FORCEBASE, ALABAMA Aerospace Education I Aircraft of Today D. S. Sayler Academic Publications Division 3825th Support Group (Academic) AIR FORCE JUNIOR ROTC AIR UNIVERSITY MAXWELL AIR FORCE BASE, ALABAMA 2 1971 Thispublication has been reviewed and approvedby competent personnel of the preparing command in accordance with current directiveson doctrine, policy, essentiality, propriety, and quality. -
4. Lunar Architecture
4. Lunar Architecture 4.1 Summary and Recommendations As defined by the Exploration Systems Architecture Study (ESAS), the lunar architecture is a combination of the lunar “mission mode,” the assignment of functionality to flight elements, and the definition of the activities to be performed on the lunar surface. The trade space for the lunar “mission mode,” or approach to performing the crewed lunar missions, was limited to the cislunar space and Earth-orbital staging locations, the lunar surface activities duration and location, and the lunar abort/return strategies. The lunar mission mode analysis is detailed in Section 4.2, Lunar Mission Mode. Surface activities, including those performed on sortie- and outpost-duration missions, are detailed in Section 4.3, Lunar Surface Activities, along with a discussion of the deployment of the outpost itself. The mission mode analysis was built around a matrix of lunar- and Earth-staging nodes. Lunar-staging locations initially considered included the Earth-Moon L1 libration point, Low Lunar Orbit (LLO), and the lunar surface. Earth-orbital staging locations considered included due-east Low Earth Orbits (LEOs), higher-inclination International Space Station (ISS) orbits, and raised apogee High Earth Orbits (HEOs). Cases that lack staging nodes (i.e., “direct” missions) in space and at Earth were also considered. This study addressed lunar surface duration and location variables (including latitude, longi- tude, and surface stay-time) and made an effort to preserve the option for full global landing site access. Abort strategies were also considered from the lunar vicinity. “Anytime return” from the lunar surface is a desirable option that was analyzed along with options for orbital and surface loiter. -
HELP from ABOVE Air Force Close Air
HELP FROM ABOVE Air Force Close Air Support of the Army 1946–1973 John Schlight AIR FORCE HISTORY AND MUSEUMS PROGRAM Washington, D. C. 2003 i Library of Congress Cataloging-in-Publication Data Schlight, John. Help from above : Air Force close air support of the Army 1946-1973 / John Schlight. p. cm. Includes bibliographical references and index. 1. Close air support--History--20th century. 2. United States. Air Force--History--20th century. 3. United States. Army--Aviation--History--20th century. I. Title. UG703.S35 2003 358.4'142--dc22 2003020365 ii Foreword The issue of close air support by the United States Air Force in sup- port of, primarily, the United States Army has been fractious for years. Air commanders have clashed continually with ground leaders over the proper use of aircraft in the support of ground operations. This is perhaps not surprising given the very different outlooks of the two services on what constitutes prop- er air support. Often this has turned into a competition between the two serv- ices for resources to execute and control close air support operations. Although such differences extend well back to the initial use of the airplane as a military weapon, in this book the author looks at the period 1946- 1973, a period in which technological advances in the form of jet aircraft, weapons, communications, and other electronic equipment played significant roles. Doctrine, too, evolved and this very important subject is discussed in detail. Close air support remains a critical mission today and the lessons of yesterday should not be ignored. This book makes a notable contribution in seeing that it is not ignored. -
Boiseboise Beebee DIGEST FW 190A-9
Number 35 Number www.warbirddigest.com WARBIRD P-51C BoiseBoise BeeBee DIGEST FW 190A-9 MARCH / APRIL 2011 MARCH / FRASCA’S Butcher Bird TBM Avenger 85828 UltimateUltimate RewardReward The “FIFI” Success Story DISPLAY UNTIL 5/14/11 UNTIL DISPLAY BoiseBoise BeeBee Story by Philip A. Janquart Photography by Jim Raeder 5The Paul family gather with friends, crew, volunteers, and supporters following the first flight piloted by John Maloney. OHN PAUL looked on with confident enthusiasm as pilot John Maloney maneuvered the Boise Bee—now one of only five operational P-51Cs in Jthe world—down the runway at the Nampa Municipal Airport and into the sky. It had been over 30 years in the making; John countless others, undertook a big push to bring 5(op-inset-photos) Three photos of Duane W. Beeson during his World collecting parts where he could, and squirreling the airplane to flight condition. On September 29, War Two service, during which he accumulated 25 victories while flying them away until he had what he needed to bring 2010, the effort paid off generously. his P-47 Boise Bee and later his P-51B. For his heroic achievements to life the model P-51 he remembered visiting Beeson was awarded the Distinguished Service Cross, Distinguished as a kid in Banning, California. The last two Test pilot John Maloney, who is also the vice Flying Cross with five oak leaf clusters, Silver Star, Purple Heart, Air years John and his son John-Curtiss, as well as president of Planes of Fame Air Museum in Chino, Medal with five oak leaf clusters, and Belgian Croix de Guerre. -
United States Women in Aviation Through World War I
United States Women in Aviation through World War I Claudia M.Oakes •^ a. SMITHSONIAN STUDIES IN AIR AND SPACE • NUMBER 2 SERIES PUBLICATIONS OF THE SMITHSONIAN INSTITUTION Emphasis upon publication as a means of "diffusing knowledge" was expressed by the first Secretary of the Smithsonian. In his formal plan for the Institution, Joseph Henry outlined a program that included the following statement: "It is proposed to publish a series of reports, giving an account of the new discoveries in science, and of the changes made from year to year in all branches of knowledge." This theme of basic research has been adhered to through the years by thousands of titles issued in series publications under the Smithsonian imprint, commencing with Smithsonian Contributions to Knowledge in 1848 and continuing with the following active series: Smithsonian Contributions to Anthropology Smithsonian Contributions to Astrophysics Smithsonian Contributions to Botany Smithsonian Contributions to the Earth Sciences Smithsonian Contributions to the Marine Sciences Smithsonian Contributions to Paleobiology Smithsonian Contributions to Zoology Smithsonian Studies in Air and Space Smithsonian Studies in History and Technology In these series, the Institution publishes small papers and full-scale monographs that report the research and collections of its various museums and bureaux or of professional colleagues in the world of science and scholarship. The publications are distributed by mailing lists to libraries, universities, and similar institutions throughout the world. Papers or monographs submitted for series publication are received by the Smithsonian Institution Press, subject to its own review for format and style, only through departments of the various Smithsonian museums or bureaux, where the manuscripts are given sub stantive review.