Vacuum Brazing of the New Rfq for the J-Parc Linac T
Total Page:16
File Type:pdf, Size:1020Kb
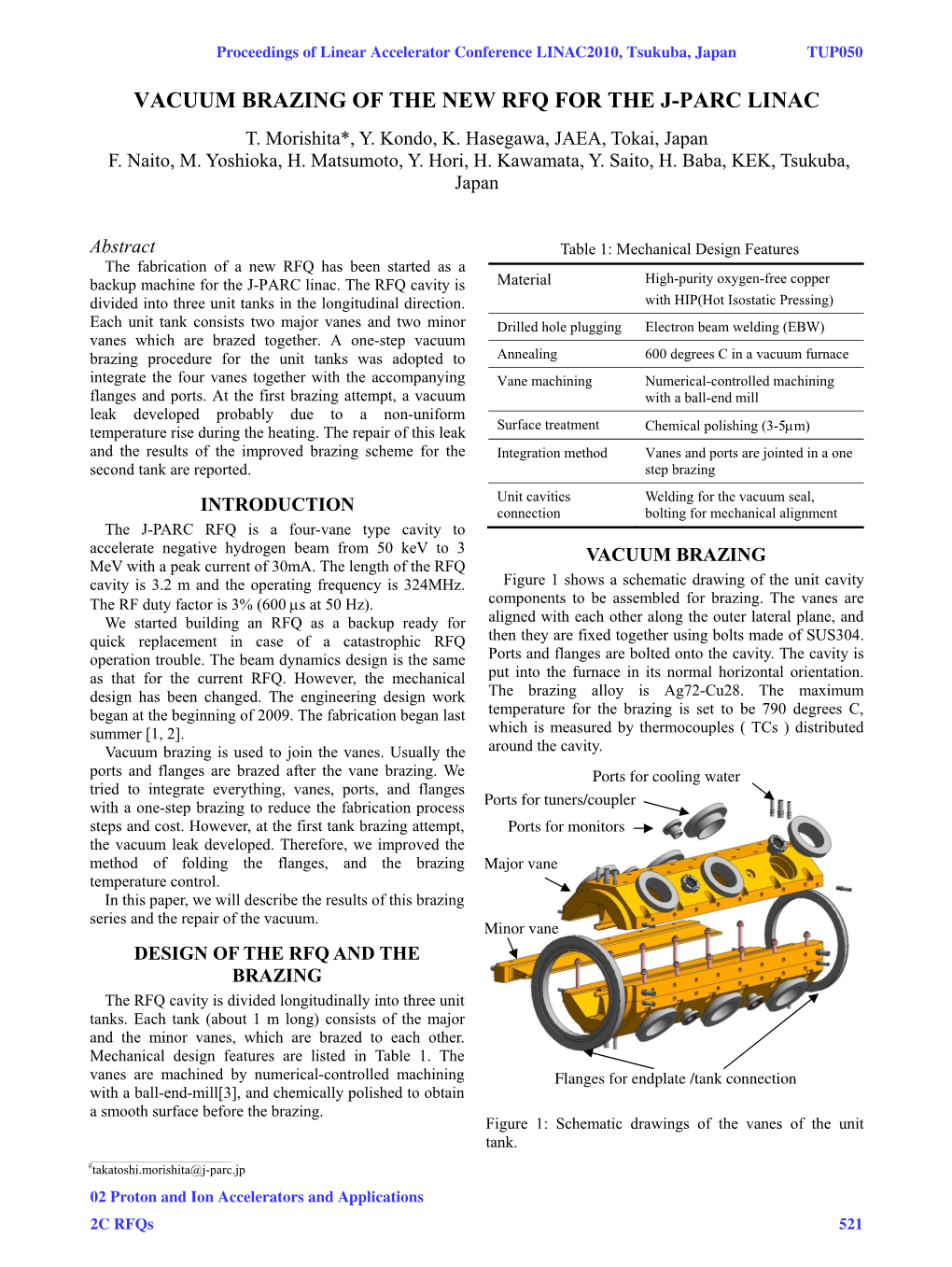
Load more
Recommended publications
-
An Analysis of the Metal Finds from the Ninth-Century Metalworking
Western Michigan University ScholarWorks at WMU Master's Theses Graduate College 8-2017 An Analysis of the Metal Finds from the Ninth-Century Metalworking Site at Bamburgh Castle in the Context of Ferrous and Non-Ferrous Metalworking in Middle- and Late-Saxon England Julie Polcrack Follow this and additional works at: https://scholarworks.wmich.edu/masters_theses Part of the Medieval History Commons Recommended Citation Polcrack, Julie, "An Analysis of the Metal Finds from the Ninth-Century Metalworking Site at Bamburgh Castle in the Context of Ferrous and Non-Ferrous Metalworking in Middle- and Late-Saxon England" (2017). Master's Theses. 1510. https://scholarworks.wmich.edu/masters_theses/1510 This Masters Thesis-Open Access is brought to you for free and open access by the Graduate College at ScholarWorks at WMU. It has been accepted for inclusion in Master's Theses by an authorized administrator of ScholarWorks at WMU. For more information, please contact [email protected]. AN ANALYSIS OF THE METAL FINDS FROM THE NINTH-CENTURY METALWORKING SITE AT BAMBURGH CASTLE IN THE CONTEXT OF FERROUS AND NON-FERROUS METALWORKING IN MIDDLE- AND LATE-SAXON ENGLAND by Julie Polcrack A thesis submitted to the Graduate College in partial fulfillment of the requirements for the degree of Master of Arts The Medieval Institute Western Michigan University August 2017 Thesis Committee: Jana Schulman, Ph.D., Chair Robert Berkhofer, Ph.D. Graeme Young, B.Sc. AN ANALYSIS OF THE METAL FINDS FROM THE NINTH-CENTURY METALWORKING SITE AT BAMBURGH CASTLE IN THE CONTEXT OF FERROUS AND NON-FERROUS METALWORKING IN MIDDLE- AND LATE-SAXON ENGLAND Julie Polcrack, M.A. -
Integrated Media Solutions Connecting Metalworking Buyers and Sellers PRINT ONLINE EMAIL EVENTS
MEDia GUIDE Integrated Media Solutions Connecting Metalworking Buyers and Sellers PRINT ONLINE EMAIL EVENTS mmsonline.com Integrated Media Solutions Connecting Metalworking Buyers and Sellers Profile of the Manufacturing Technology Buyer • Uses at least 5 media types to find work-related information • Looks for product or process solutions at least once a month • Values technology and service more than price • Is college educated and technically minded • Carries a laptop computer and smartphone • Is around 50 years old • Initiates contact with vendors 6915 Valley Avenue Cincinnati, OH 45244-3029 U.S.A. 513-527-8000 • 800-950-8020 Fax: 513-527-8801 mmsonline.com BUYING CYCLE Modern Machine Shop serves prospects at each stage of the buying cycle. Industrial Equipment Buying Cycle AWARENESS RESEARCH CONSIDERATION VENDOR SELECTION The market actively This market segment Prospects have Final comparison of consumes push media knows they have an immediate requirements, known alternatives. to learn about things interest in certain topics and are actively seeking they did not know. and technologies to act solutions. STAGES upon in the future. PUSH MEDIA is the PUSH MEDIA still With the prospect now in Brand impression is the best means to introduce dominates, but the control of the information largest influence in final new products and segment is more focused. gathering process, PULL purchasing decision. establish brand, which MEDIA becomes most is essential in the later Trade Magazines important. Brand is a primary Industry Websites stages of -
UAI Sheet Metal Fabrication
Precision in Sheet Metal Fabrication Your Single Strategic Source • Solutions Based Engineering Support • Serial Production Metal Fabrication • Automated Manufacturing • Certified eldingW • State of the Art Powder Paint Capabilities • Assembly & Validation Made in ISO 9001:2008 A Name Synonymous with Quality UAI has built a solid reputation as a preferred designer, manufacturer, powder coater, assembler and Tier One OEM supplier of certified metal tanks, trailers, skids and steel metal products crafted to stringent [ISO-9001:2008] quality standards. We are constantly finding new ways to go beyond fabrication, to become a true integrated business partner to our valued OEM customers. Our growing list of loyal customers, many of which are world class OEM Fortune 100 manufacturers across numerous industries, verifies UAI’s performance and commitment to 100% product quality, 100% on-time delivery and expert design support. Manufacturing Horsepower Welding Painting Our qualified engineers and • Laser Cutting • All welders are internally AWS • Twin large capacity 6 stage skilled craftsmen work • 6-Axis Plasma Cutting D1.1 & D1.3 certified. Other pre-treatment & wash within a 250,000+ square • 40’ Automatic Drill-Line AWS certifications as required with nano-ceramic sealer foot facility, utilizing ISO • Shearing • Internal Certified Welding • Automated dry off and cure 9001 certified processes • Forming Instructors • Internal paint capability and lean manufacturing • Punching • Lean 6 Sigma black & means complete control of principles to give customers • CNC Machining green belts on staff quality, lead-time and costs both the uncompromising • AWS Certified Welding • Flexible robotic welding • Paint options achieve from quality and the globally • Robotic Welding systems 1,000 hrs. -
Conventional Deep Drawing Vs Incremental Deep Drawing
MED, JNTUH August 2018 CONVENTIONAL DEEP DRAWING VS INCREMENTAL DEEP DRAWING A. Chennakesava Reddy Professor, Department of Mechanical Engineering JNTUH College of Engineering, Hyderabad 1. Conventional Deep Drawing Process: Deep drawing is a sheet metal forming process in which a sheet metal blank is radially drawn into a forming die by the mechanical action of a punch. It is thus a shape transformation process with material retention. The process is considered "deep" drawing when the depth of the drawn part exceeds its diameter. This is achieved by redrawing the part through a series of dies. The flange region (sheet metal in the die shoulder area) experiences a radial drawing stress and a tangential compressive stress due to the material retention property. These compressive stresses (hoop stresses) result in flange wrinkles (wrinkles of the first order). Wrinkles can be prevented by using a blank holder, the function of which is to facilitate controlled material flow into the die radius. Figure 1: Example of deep drawn part. Figure 2: Conventional deep drawing process. The total drawing load consists of the ideal forming load and an additional component to compensate for friction in the contacting areas of the flange region and bending forces as well as unbending forces at the die radius. The forming load is transferred from the punch radius through the drawn part wall into the deformation region (sheet metal flange). In the drawn part wall, which is in contact with the punch, the hoop strain is zero whereby the plane strain condition is reached. In reality, mostly the strain condition is only approximately plane. -
SOLDERING OR UNSOLDERING; WELDING; CLADDING OR PLATING by SOLDERING OR WELDING; CUTTING by APPLYING HEAT LOCALLY, E.G
B23K CPC COOPERATIVE PATENT CLASSIFICATION B PERFORMING OPERATIONS; TRANSPORTING (NOTES omitted) SHAPING B23 MACHINE TOOLS; METAL-WORKING NOT OTHERWISE PROVIDED FOR (NOTES omitted) B23K SOLDERING OR UNSOLDERING; WELDING; CLADDING OR PLATING BY SOLDERING OR WELDING; CUTTING BY APPLYING HEAT LOCALLY, e.g. FLAME CUTTING; WORKING BY LASER BEAM (making metal-coated products by extruding metal B21C 23/22; building up linings or coverings by casting B22D 19/08; casting by dipping B22D 23/04; manufacture of composite layers by sintering metal powder B22F 7/00; arrangements on machine tools for copying or controlling B23Q; covering metals or covering materials with metals, not otherwise provided for C23C; burners F23D) NOTES 1. This subclass covers also electric circuits specially adapted for the purposes covered by the title of the subclass. 2. In this subclass, the following term is used with the meaning indicated: • "soldering" means uniting metals using solder and applying heat without melting either of the parts to be united WARNINGS 1. The following IPC groups are not in the CPC scheme. The subject matter for these IPC groups is classified in the following CPC groups: B23K 35/04 - B23K 35/20 covered by B23K 35/0205 - B23K 35/0294 B23K 35/363 covered by B23K 35/3601 - B23K 35/3618 2. In this subclass non-limiting references (in the sense of paragraph 39 of the Guide to the IPC) may still be displayed in the scheme. Soldering, e.g. brazing, or unsoldering (essentially requiring the use 1/018 . Unsoldering; Removal of melted solder or other of welding machines or welding equipment, see the relevant groups residues for the welding machines or welding equipment) 1/06 . -
Virtual Manufacturing on the Web: Extrusion Die Design
VIRTUAL MANUFACTURING ON THE WEB: EXTRUSION DIE DESIGN A Thesis Presented to The Faculty of the Fritz J. and Dolores H. Russ College of Engineering and Technology Ohio University In Partial Fulfillment Of the Requirement for the Degree Master of Science Sripada Shivananda August 1998 Acknowledgment I wish to express my sincere thanks to my advisor, Dr. Bhavin Mehta, for his valuable advice and providing me with the information and the facilities required for the thesis. I would also like to thank my wife for her constant encouragement and support during the completion of this thesis. Sripada Shivananda August 1998 Table of Contents Table of Contents ........................................................................................................ i List of Figures .............................................................................................................. iv List of Tables ......................................................................................................................v INTRODUCTION ..............................................................................................................1 1.1 Overview ................................................................................................................1 1.2 Internet ..................................................................................................................2 1.3 Virtual Manufacturing .........................................................................................2 1.4 Virtual Reality .......................................................................................................4 -
Under the Direction of Dr. Gracious Ngaile)
ABSTRACT LOWRIE, JAMES BALLANFONTE. Development of a Micro-Tube Hydroforming System. (Under the direction of Dr. Gracious Ngaile). The rising demand for small parts with complex shapes for micro-electrical mechanical systems (MEMS) and medical applications has caused researchers to focus on metal forming as a possible way to mass produce miniature components. Studies into the miniaturization of macro-scale metal forming processes have mainly been focused in the sheet metal and extrusion fields and only a few researchers have attempted to take on the problem of miniaturizing the tube hydroforming process. The research that has been done into micro- tube hydroforming has been limited to simple expansion studies and no researchers have yet been able to combine axial feeding of the ends of the micro-tubular blank with simultaneous expansion of the tube. This has significantly reduced the complexity of the micro-parts which can be created using the tube hydroforming system. Combining material feed and expansion must be accomplished in order to create a micro-tube hydroforming process which is capable of producing metallic components with complex tubular geometries. The major objective of the research presented in this thesis is the development of a micro- tube hydroforming system which is capable supplying both axial feed and expansion to the tube simultaneously. This was accomplished by first breaking down the concepts of the conventional hydroforming tooling so that they could be analyzed for problems when being scaled down. Once the problems with the conventional tooling and the basic needs of the hydroforming system were established, the information was used to develop a new form a hydroforming tooling, called floating die tooling, which could apply both material feed and expansion to tubular blanks. -
The Dynisco Extrusion Processors Handbook 2Nd Edition
The Dynisco Extrusion Processors Handbook 2nd edition Written by: John Goff and Tony Whelan Edited by: Don DeLaney Acknowledgements We would like to thank the following people for their contributions to this latest edition of the DYNISCO Extrusion Processors Handbook. First of all, we would like to thank John Goff and Tony Whelan who have contributed new material that has been included in this new addition of their original book. In addition, we would like to thank John Herrmann, Jim Reilly, and Joan DeCoste of the DYNISCO Companies and Christine Ronaghan and Gabor Nagy of Davis-Standard for their assistance in editing and publication. For the fig- ures included in this edition, we would like to acknowledge the contributions of Davis- Standard, Inc., Krupp Werner and Pfleiderer, Inc., The DYNISCO Companies, Dr. Harold Giles and Eileen Reilly. CONTENTS SECTION 1: INTRODUCTION TO EXTRUSION Single-Screw Extrusion . .1 Twin-Screw Extrusion . .3 Extrusion Processes . .6 Safety . .11 SECTION 2: MATERIALS AND THEIR FLOW PROPERTIES Polymers and Plastics . .15 Thermoplastic Materials . .19 Viscosity and Viscosity Terms . .25 Flow Properties Measurement . .28 Elastic Effects in Polymer Melts . .30 Die Swell . .30 Melt Fracture . .32 Sharkskin . .34 Frozen-In Orientation . .35 Draw Down . .36 SECTION 3: TESTING Testing and Standards . .37 Material Inspection . .40 Density and Dimensions . .42 Tensile Strength . .44 Flexural Properties . .46 Impact Strength . .47 Hardness and Softness . .48 Thermal Properties . .49 Flammability Testing . .57 Melt Flow Rate . .59 Melt Viscosity . .62 Measurement of Elastic Effects . .64 Chemical Resistance . .66 Electrical Properties . .66 Optical Properties . .68 Material Identification . .70 SECTION 4: THE SCREW AND BARREL SYSTEM Materials Handling . -
Reducing Abrasive Particle Generation in Dry Rotary Swaging by Utilizing DLC Hard Coated Dies
MATEC Web of Conferences 190, 14011 (2018) https://doi.org/10.1051/matecconf/201819014011 ICNFT 2018 Reducing Abrasive Particle Generation in Dry Rotary Swaging by Utilizing DLC Hard Coated Dies Florian Böhmermann1,*, Marius Herrmann2, Oltmann Riemer1, and Bernd Kuhfuss2,3 1IWT Leibniz Institute for Materials Engineering, Laboratory for Precision Machining, Badgasteiner Straße 3, 28359 Bremen, Germany 2bime Bremen Institute for Mechanical Engineering, University of Bremen, Badgasteiner Straße 1, 28359 Bremen, Germany 3MAPEX Center for Materials and Processing, University of Bremen, Am Fallturm 1, 28359, Bremen, Germany Abstract. The emphasis of this paper is the investigation of the impact of the diamond like carbon (DLC) hard coating system on the amount of abrasive particles being generated during dry rotary swaging. Rotary swaging experiments applying coated and uncoated macro structured forming dies were carried out against aluminum and steel work pieces varying the process parameter feed velocity. It was found that DLC coatings effectively reduce the generation of abrasive particles from the work piece. For dry machining of aluminum the amount was reduced to a tenth of the original quantity achieved with uncoated dies. The results are discussed with regard to the mechanics of interfacing surfaces. Additionally, forming dies exhibiting macro structures surfaces of improved design were introduced and applied in dry rotary swaging experiments, which allowed minimizing the abrasive particle generation. Keyword: Sustainable machining, Cold forming, Die 1 Introduction Furthermore, macro structured reduction zones of forming dies were used to control the axial reaction force Rotary swaging is an incremental bulk metal forming that counteracts the feed force. The features, here, were process for the manufacture of rotational symmetric sine wave structures with propagation parallel to the feed lightweight components, e.g. -
Advanced Sheet Metal Design Faster
SOLIDWORKS Advanced Sheet Metal Advanced Sheet Metal – Design Faster Steve Lynch Rapid Sheet Metal SOLIDWORKS Intro NESWUC 2012 • Dedicated to quick turn prototype sheet metal parts • 15 seats of SolidWorks 2013 • CAD Quotes in under 8 hours • Unfinished parts in 7 days • Plated parts in 9 days • We do not design parts • 2,500 unique parts quoted a month on average • Quoting & Manufacturing from 3D CAD Data SOLIDWORKS Overview NESWUC 2012 • Counter Sinks – How to find through hole size • Hardware – RSM web site table – Mate references – Hole Sizes +.003 -.000 • Rapid Forming tools – Forming tools from our web site • Be careful with SolidWorks Sheet Metal Defaults – Bend Radii – Material selection • Custom Properties – Add data to your part, Assembly, and Print fast! • Welded box & cover with equations – Save time, make it once – Get the idea completed and manufactured – Add welding locking features rapidly • Advanced Bend Relief examples – Using library feature – Using subtract bodies SOLIDWORKS Overview Cont. NESWUC 2012 • Videos – Hem – Offset – Bump forming • Design Fast – Use shell – Delete face – Get the idea down then engineer the design • Pictures of before and after – Welding – Solid parts cut for manufacturing SOLIDWORKS Counter Sinks NESWUC 2012 82° Counter Sink in .119” steel. 82° Counter Sink in .047” steel. SOLIDWORKS Counter Sinks NESWUC 2012 82° Counter Sink in .119” steel. 82° Counter Sink in .047” steel. SOLIDWORKS Counter Sinks NESWUC 2012 82° Counter Sink in .047” thick steel. SOLIDWORKS Counter Sinks NESWUC 2012 Ø.143 Before Ø.160 After Ø.017 Delta Ø.160 SOLIDWORKS Counter Sinks NESWUC 2012 It’s better not dimensioning your through holes SOLIDWORKS Hardware – RSM Hardware table NESWUC 2012 http://www.rapidsheetmetal.com/resources Rapid reference to Hardware data SOLIDWORKS Hardware – Mate Reference NESWUC 2012 Problem Rivets and hardware with countersunk edges are hard to auto mate SOLIDWORKS Hardware – Mate Reference NESWUC 2012 We have noticed it is common to select this top edge as the default Mate reference. -
Exergy Analysis of Incremental Sheet Forming
Exergy Analysis of Incremental Sheet Forming M.A. Dittrich1, T.G. Gutowski1, J. Cao2, J.T. Roth3, C. Xia4, V. Kiridena4, F. Ren4, H. Henning5 1Laboratory for Manufacturing and Productivity, Massachusetts Institute of Technology, 77 Massachusetts Avenue, MA 02139 Cambridge, USA, T. Gutowski: [email protected], M.A. Dittrich: [email protected] 2Dept. of Mechanical Engineering, Dept. of Civil and Environmental Engineering, Northwestern University, 2145 Sheridan Rd. Evanston, IL 6020, USA 3Mechanical Engineering Faculty, Penn State Erie, The Behrend College 5091 Station Road Erie, PA 16563 Erie, USA 4Ford Research and Innovation Center, MI 48124 Dearborn, USA 5Institut für Fertigungstechnik und Werkzeugmaschinen, Gottfried Wilhelm Leibniz Universität Hannover, An der Universität 2, 30823 Garbsen, Germany sheet metal forming processes to large production runs [1]. Abstract Due to the problems in small lot production, aerospace industry frequently replaces forming processes by Research in the last 15 years has led to die-less incremental machining processes in order to eliminate the need for forming processes that are close to realization in an costly die sets. As a consequence, up to 95% of the material industrial setup. Whereas many studies have been carried is machined away [2], which has both a negative financial out with the intention of investigating technical abilities and and environmental impact. economic consequences, the ecological impact of incremental sheet forming (ISF) has not been studied so far. In order to overcome the limitations of conventional drawing processes, alternative sheet metal forming Using the concept of exergy analysis, two ISF technologies, techniques like single sided (SSIF) and double sided namely single sided and double sided incremental forming, incremental forming (DSIF) have been developed. -
METAL FABRICATION TECHNOLOGY Curriculum Guide for Academic Year 2016-2017
METAL FABRICATION TECHNOLOGY Curriculum Guide for Academic Year 2016-2017 Table of Contents Associate in Science Degree, p. 1 Certificates of Achievement, p. 2 Core Skills, p. 2 Advanced Skills, p. 2 Certificates of Accomplishment, p. 3 Robotic Welding Automation, p. 3 Core Skills Certificate Recommended, but not required, classes, p. 3 Advanced Skills Certificate Recommended, but not required, classes, p. 3 Career Opportunities, p. 3 Program Mission and Outcomes, p. 4 Legend, p. 4 Students planning to transfer to a four-year college or university should refer to the ASSIST web site at www.assist.org and consult a counselor before beginning a program of study Please call 562-938-4561 for the LAC, or 562-938-3920 for PCC to schedule a meeting with a counselor. Students may also wish to visit the Transfer Center on either campus. Program of study leading to: Associate in Science (A.S.) Degree4922 In Completed REQUIRED COURSES UNITS Progress Grade ELECT 253 OSHA Standards for Construction Safety 2 MTFAB 50 Introduction to Metalworking 4 MTFAB 220B Advanced Metal Layout/ Fabrication 4 MTFAB 220C Power Metalworking Machine Operations 4 MTFAB 260 Blueprint Reading for Metal Fabrication 3 MTFAB 421 Metal Fabrication and Layout 1 WELD 50 Introduction to Welding 4 TOTAL UNITS 22 For graduation with an Associate in Science (A.S.) Degree with a major in Metal Fabrication Technology: 1. Minimum Unit Requirements: §Any course that appears on a curriculum guide and the General Education Pattern (Plan A) may fulfill both major and general education requirements (Approved by College Curriculum Committee Spring 2012).