Efficient Synchronous Extraction of Nickel, Copper, and Cobalt
Total Page:16
File Type:pdf, Size:1020Kb
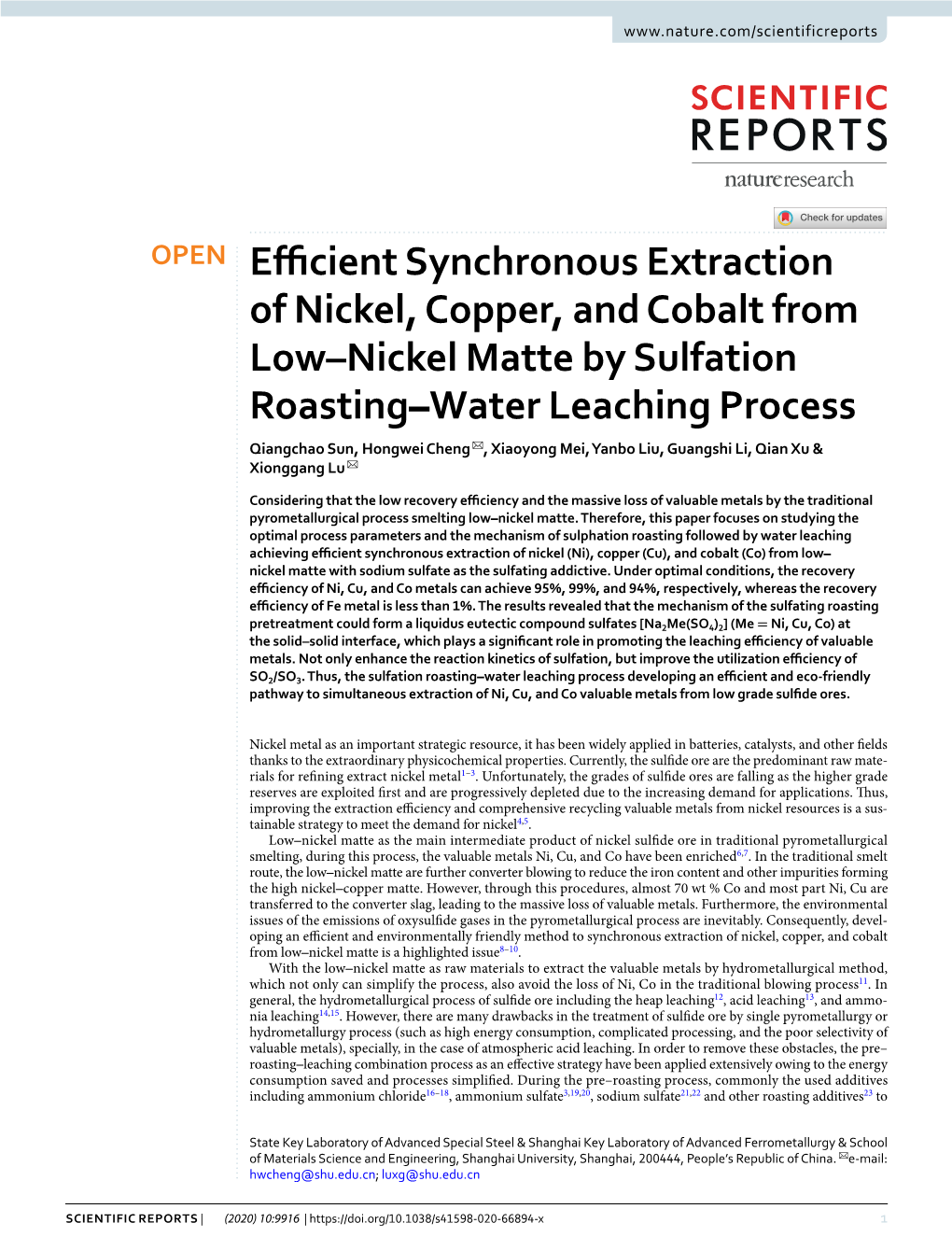
Load more
Recommended publications
-
Principles of Extractive Metallurgy Lectures Note
PRINCIPLES OF EXTRACTIVE METALLURGY B.TECH, 3RD SEMESTER LECTURES NOTE BY SAGAR NAYAK DR. KALI CHARAN SABAT DEPARTMENT OF METALLURGICAL AND MATERIALS ENGINEERING PARALA MAHARAJA ENGINEERING COLLEGE, BERHAMPUR DISCLAIMER This document does not claim any originality and cannot be used as a substitute for prescribed textbooks. The information presented here is merely a collection by the author for their respective teaching assignments as an additional tool for the teaching-learning process. Various sources as mentioned at the reference of the document as well as freely available material from internet were consulted for preparing this document. The ownership of the information lies with the respective author or institutions. Further, this document is not intended to be used for commercial purpose and the faculty is not accountable for any issues, legal or otherwise, arising out of use of this document. The committee faculty members make no representations or warranties with respect to the accuracy or completeness of the contents of this document and specifically disclaim any implied warranties of merchantability or fitness for a particular purpose. BPUT SYLLABUS PRINCIPLES OF EXTRACTIVE METALLURGY (3-1-0) MODULE I (14 HOURS) Unit processes in Pyro metallurgy: Calcination and roasting, sintering, smelting, converting, reduction, smelting-reduction, Metallothermic and hydrogen reduction; distillation and other physical and chemical refining methods: Fire refining, Zone refining, Liquation and Cupellation. Small problems related to pyro metallurgy. MODULE II (14 HOURS) Unit processes in Hydrometallurgy: Leaching practice: In situ leaching, Dump and heap leaching, Percolation leaching, Agitation leaching, Purification of leach liquor, Kinetics of Leaching; Bio- leaching: Recovery of metals from Leach liquor by Solvent Extraction, Ion exchange , Precipitation and Cementation process. -
Principles of Metallurgy
Chapter 13 Principles of Metallurgy In class 8 you have studied about certain properties of metals like, malleability, ductility, sonarity etc. Metals play an important role in our daily life. We use various metals for various purposes like gold and silver as jewellary, copper, iron, alluminium for making conducting wires and for making utensils etc. We use many house hold articles made up of metals and their alloys at our home. • Can you mention some articles that are made up of metals? • Do metals exist in nature in the form same as that we use in our daily life? • Have you ever heard the words like ore, mineral and metallurgy? • Do you know how these metals are obtained? To understand these questions you need to know about metallurgy. In this chapter we discuss various concepts related to metallurgy and the process by which we are able to obtain the pure form of metal that we use in our daily life. “Metallurgy is the process of extraction of metals from their ores”. Human history in terms of materials had the Bronze Age and Iron Age pertaining to the metals they started to use the bronze (an alloy of copper and tin) and iron. Now we have more than 75% metals among the elements available. Occurrence of the metals in nature • How the metals are present in nature? The earth’s crust is the major source of metals. Sea water also contains some soluble salts such as sodium chloride and magnesium chloride etc. 286 X Class Principles of Metallurgy Some metals like gold (Au), silver (Ag) and copper (Cu) are available in nature in free state (native) as they are least reactive. -
Copper Worldwide Vol 7 No 1 Jan-Feb 2017
JANUARY/FEBRUARY 2017 VOLUME 7 | 1 See Buyers Guide pp26-27 n Key Words: Innovation and sustainability n News: Głogów Smelter Kamoa-Kakula More copper mined Project issues n Smelting features: Converting (2 of 3) Two-step method at Dongying n Spotlight: Electrorefining progress UMMC n Optimisation: A 4-step process n Copper in Germany: Jonathan Barnes on Europe’s copper major n Copper semis: Producers and capacity survey n Events: 30th Intl Copper 16th World Copper Conference Copper/Cobre 2016 Coming up in 2017 n Contracts: Outotec re-orders Toquepala Steerhorn Chuquicamata n Buyers Guide - In search of added value ISSN 2046-9438 www.copperworldwide.com www.copperworldwide.com CONTENTS | 1 We transform … Key Words the world of copper 3 Innovation and sustainability News Kamoa-Kakula progress; Rise in mined 4 copper; Głogów starts up flash furnace; Project acceptance study; IWCC Technical Seminars; MIDAS undersea research results; The MD issue around commissioning; MKM into e-mobility; Market in surplus; Aurubis update; Glencore knowhow; Peru output Spotlight Electrometallurgy 2016 review; 6 UMMC tankhouse Contracts & People Outotec re-ordering and Toquepala 20 contract; Steerhorn cathodes; Gas management in France; Iran and Indonesia The Głogów Copper Smelter (see page 5) items; Chuquicamata acid plants ordered; Copper crucible restoration Inside this issue ELECTROREFINING/ 16TH WORLD ELECTROWINNING COPPER CONFERENCE The SX-EW cost burden; G Corner top Preview and latest CRU analysis 9 in refining; Dias d’Ávila milestone; 19 Ion exchange processing SAFETY AND Copper working process – from the melting bath to the fi nal product PLANT INTEGRATION MAINTENANCE AND CONTROL Stories relating to these SMS group has been active in the copper fi eld for more Our integrated solutions are a byword for robust and reli- Optimisation of control systems via the two key operational areas than 50 years. -
Recovery of Value Added Products from Red Mud and Foundry Bag
RECOVERY OF VALUE-ADDED PRODUCTS FROM RED MUD AND FOUNDRY BAG-HOUSE DUST by Keegan Hammond i A thesis submitted to the Faculty and the Board of Trustees of the Colorado School of Mines in partial fulfillment of the requirements for the degree of Master of Science (Metallurgical and Materials Engineering). Golden, Colorado Date ______________ Signed: ____________________________ Keegan Hammond Signed: ____________________________ Dr. Brajendra Mishra Thesis Advisor Golden, Colorado Date ______________ Signed: ____________________________ Dr. Chester VanTyne Interim Department Head Department of Metallurgical and Materials Engineering ii ABSTRACT “Waste is wasted if you waste it, otherwise it is a resource. Resource is wasted if you ignore it and do not conserve it with holistic best practices and reduce societal costs. Resource is for the transformation of people and society.”1 Red mud is a worldwide problem with reserves in the hundreds of millions of tons and tens of millions of tons being added annually. Currently there is not an effective way to deal with this byproduct of the Bayer Process, the primary means of refining bauxite ore in order to provide alumina. This alumina is then treated by electrolysis using the Hall-Héroult process to produce elemental aluminum. The resulting mud is a mixture of solid and metallic oxides, and has proven to be a great disposal problem. This disposal problem is compounded by the fact that the typical bauxite processing plant produces up to three times as much red mud as alumina. Current practice of disposal is to store red mud in retention ponds until an economical fix can be discovered. -
An Investigation of a Single-Stage Red Mud Reducing Roasting Process with the Cast Iron and Aluminate Slag Production
LIGHT METALS, CARBON MATERIALS An investigation of a single-stage red mud reducing roasting process with the cast iron and aluminate slag production K. G. Anisonyan, Senior Researcher1, e-mail: [email protected] D. Yu. Kopyev, Researcher1 K. V. Goncharov, Researcher1 G. B. Sadykhov, Chief Researcher1 1 A. A. Baikov Institute of Metallurgy and Material Science of the Russian Academy of Sciences, Federal State Budgetary Science Institution. Red mud is a technogenic waste product, a result of alumina production. It is a fine-dispersed material containing up to 60% Fe2O3 and up to 20% Al2O3. For each ton of alumina produced of bauxites there is more than 1 ton of red mud. In the absence of effective recycling technologies, red mud is practically not used and is almost completely stored in special sludge deposits, which negatively affects the environ- ment. Tens of millions of tons of red mud are sent to the dumps every year in the world. More than 100 million tons of red mud has been piled up in Russia. High content of iron and aluminium in red mud requires a pro- cessing which provides an effective separation of these components and obtaining original iron- and aluminium-bearing products. In this connection, the present paper is focused on developing a single-stage reducing roasting process with simultaneous generation of cast iron, a product for steel industry, and the aluminate slag suitable for alumina production. The main stage of the red mud complex processing technology under develop- ment is a single-stage reducing roasting process which results in the cast iron and aluminate slag obtain- ing; the latter is further treated by water leaching for aluminium precipitation from solution. -
Lead Poisoning in the Smelting and Refining of Lead
U. S. DEPARTMENT OF LABOR BUREAU OF LABOR STATISTICS ROYAL MEEKER, Commissioner BULLETIN OF THE UNITED STATES ) (WHOLE 1 A 1 BUREAU OF LABOR STATISTICS) ' * * (NUMBER lTL 1 INDUSTRIAL ACCIDENTS AND HYGIENE SERIES: No. 4 LEAD POISONING IN THE SMELTING AND REFINING OF LEAD f FEBRUARY 17, 1914 WASHINGTON GOVERNMENT PRINTING OFFICE 1914 Digitized for FRASER http://fraser.stlouisfed.org/ Federal Reserve Bank of St. Louis Digitized for FRASER http://fraser.stlouisfed.org/ Federal Reserve Bank of St. Louis CONTENTS. Lead poisoning in the smelting and refining of lead: Page. Introduction............................................................................................................... 5-17 Dangerous processes in the smelting and refining of lead....... ............... 6-8 Dust and fumes.................................................................................................. 9-11 Sanitary equipment.......................................................................................... 11 Medical care....................................................................................................... 11 Disadvantages of a shifting force................................................................. 11,12 Prevalence of lead poisoning in the industry............................................. 12-14 Prevention of lead poisoning in the smelting industry............................ 14-17 Construction............................................................................................... 15 Sanitary equipment................................................................................. -
The Research of the Carbothermic Solid–Phase Red Mud Reduction
TECHNOGEN-2019 IV Congress “Fundamental research and applied developing of KnE Materials Science recycling and utilization processes of technogenic formations” Volume 2020 Conference Paper The Research of the Carbothermic Solid–Phase Red Mud Reduction Process in the Presence of Sodium Sulphate Dmitry Zinoveev1, Pavel Grudinsky1, Artem Semenov1, Valery Dyubanov1, and Alexander Petelin2 1A.A. Baikov Institute of Metallurgy and Materials Science, Russian Academy of Sciences, Moscow, Russia 2National University of Science and Technology MISiS, Moscow, Russia Abstract Russia has accumulated about 600 million tons of the red mud that is alumina production waste generated by Bayer method, but currently only a small amount of the total accumulated red mud is recycled. Solid–phase carbothermic reduction of red mud in the presence of sodium salts with magnetic separation can be a promising method for iron extraction. In this paper, the effect of the addition of sodium sulphate on the reduction of iron–containing phases and the growth of iron grains during Corresponding Author: Dmitry Zinoveev solid–phase carbothermic reduction of red mud was investigated. The results show [email protected] that 10% sodium sulphate additive significantly accelerate the growth of reduced iron grains, but decrease the degree of its reduction at temperatures above 1100∘C. The Published: 31 December 2020 explanation of mechanism of sodium sulphate effect on the iron grain growth was Publishing services provided by proposed. Optimization of sodium sulphate amount, temperature and holding time Knowledge E can lead the development of effective technology of iron extraction from red mud by solid–phase carbothermic reduction. Dmitry Zinoveev et al. -
Oxygen Enriched Atmosphere Roasting Clarence Wells Jr
Montana Tech Library Digital Commons @ Montana Tech Bachelors Theses and Reports, 1928 - 1970 Student Scholarship 4-30-1948 Oxygen Enriched Atmosphere Roasting Clarence Wells Jr Follow this and additional works at: http://digitalcommons.mtech.edu/bach_theses Part of the Ceramic Materials Commons, Environmental Engineering Commons, Geology Commons, Geophysics and Seismology Commons, Metallurgy Commons, Other Engineering Commons, and the Other Materials Science and Engineering Commons Recommended Citation Wells, Clarence Jr, "Oxygen Enriched Atmosphere Roasting" (1948). Bachelors Theses and Reports, 1928 - 1970. 256. http://digitalcommons.mtech.edu/bach_theses/256 This Bachelors Thesis is brought to you for free and open access by the Student Scholarship at Digital Commons @ Montana Tech. It has been accepted for inclusion in Bachelors Theses and Reports, 1928 - 1970 by an authorized administrator of Digital Commons @ Montana Tech. For more information, please contact [email protected]. OXYGEN ENRICHED ATJrOSPHERE ROA&TING A Thesis Submitted to the Department of Metallurgy Montan~ School of Mines In Partial Fulfillment of the Refluirements for tbe Degree Bachelor of Science in Metallurgical Engineering oy Clarence ~"ells, Jr. April 30, 1948 OXYGEN ENRICHED ATMOSPHERE ROASTING A Thesis Submitted to the Department of Metallurgy Montana School of Mines In Partial Fulfillment of the Requt.r-emerrt >3 !cr the Degree Bachelor of Scic~ce in Metallurgical Engineering 19343 by Clarence Wells, Jr. April 30, 1948 TABLE -OF CONTENTS ~ CHAPTER I PAGE I GENERAL INTRODUCTION ••••••••••••••••••••••• 1 II THEORY ••••••••••••••••••••••••••••••••••••• 4 Reasons for oxygen atmosphere •••••••••••• 4 Amount of heat produced •••••••••••••••••• 5 Furnace requirements ••••••••••••••••••••• 6 Furnace capacity ......................... 6 Types of draft •• ••• ••••• •••• • • • •• • •••• • • • 6 Wall friction •••••••••••••••••••••••••••• ? Variable operating conditions •••••••••••• ? MOist feed •••••••••••••• ................ -
Lecture 14: Pyro Metallurgical Extraction (Roasting)
Lecture 14: Pyro metallurgical extraction (Roasting) Contents Introduction Roasting Sources of energy Determination of calorific value of gaseous fuel Amount of air Types of roasting Conclusions References Keywords: roasting, dead roasting, sulphatizing roasting Introduction: In Pyro metallurgicalextraction of metal, thermal energy is one of the important inputs. Different unit processeslike roasting, smelting, converting and refining require large amount of thermal energy. This lecture discusses roasting. Roasting Roasting is the oxidation of metal sulphides to give metal oxides and sulphur dioxide. Typical examples are: 2 ZnS 3 O 2 ZnO 2 SO 2 FeS 5.5 O FeO 4 SO 2 PbS 3 O 2 PbO 2 SO In addition other reactions may take place: formation of SO and metal sulphates and formation of complex oxides such as ZnO. FeO. Typically,sulphide ores of copper, zinc and lead are roasted either partially or completely. Copper sulphide ores are roasted partially; whereas ores of lead and Zinc are roasted completely into oxides for subsequent treatment. This SO is then a byproduct. Roasting is usually carried out below the melting points of the sulphides and oxides involved, usually below900 1000. Both reactants and products are in the solid state. In roasting ore concentrate is mixed with for oxidation. Normally excess air is used for roasting. Fuel may or may not be used. Sources of energy Different sources of thermal energy are a) Heat of reaction: Combustion of S to SO or SO releases 70940 k cal⁄ kg mol and 93900 k cal⁄kg mol of thermal energy respectively. Several oxidation reactions like Fe FeO, FeS FeO, ZnS ZnO and so on releases thermal energy. -
Principles of Roasting with Its Types
PRINCIPLES OF ROASTING WITH ITS TYPES By: Walid Khalid Abdulkader VARIOUS METALLURGICAL PROCESSES Hydrometallurgy is a method for obtaining metals from their ores. It is a technique within the field of extractive metallurgy involving the use of aqueous chemistry for the recovery of metals from ores, concentrates, and recycled or residual materials Electrometallurgy is a term used for processes that refine or purify metals using electricity. It can also be a general term for electrical processes used to plate one metal with another for decorative or corrosion resistance purposes. Pyrometallurgy is a branch of extractive metallurgy. It consists of the thermal treatment of minerals and metallurgical ores and concentrates to bring about physical and chemical transformations in the materials to enable recovery of valuable metals METALLURGY -PYRO metallurgy deals with the extraction of -Pyro minerals from ore by treating them with heat. Pyro- metallurgy Calcination Roasting Smelting Sintering ROASTING In roasting, the ore is heated in a regular supply of air in a furnace at a temperature below the melting point of the metal. Roasting is a metallurgical process involving gas–solid reactions at elevated temperatures with the goal of purifying the metal component(s). Often before roasting, the ore has already been partially purified, e.g. by froth floatation. The concentrate is mixed with other materials to facilitate the process. This process is generally applied to sulphide minerals. During roasting, the sulfide is converted to an oxide, and sulfur is released as sulfur dioxide, a gas. For the ores Cu2S (chalcocite) and ZnS (sphalerite), balanced equations for the roasting are:- 2 Cu2S + 3O2 → 2 Cu2O + 2 SO2 2 ZnS + 3 O2 → 2 ZnO + 2 SO2 PROCESSES There are several different types of roast, each one intended to produce a specific reaction and to yield a roasted product (or calcine) suitable for the particular processing operation to follow. -
A Wet and Crucib1e-Fire Methods
Bulletin No. 253 Series E, Chemistry and Physics, 44 DEPARTMENT OF THE INTERIOR UNITED STATES GEOLOGICAL SURVEY CHARLES D. WALCOTT, DIRECTOR COMPARISON A WET AND CRUCIB1E-FIRE METHODS FOB THM ASSAY OF GOLD TELLURIDE ORES WITH NOTES ON THE ERRORS OCCURRING IN THE OPERATIONS OF FIRE ASSAY AND PARTING W. F. HILLEBRAND and E. T. ALLEN WASHINGTON GOVERNMENT PRINTING OFFICE 1905 CONTENTS. Pago. Letter of transmittal. ..................................................... 5 Introduction. ___ .__._..._..._.._._...-......-- _.__.-.-.._...._.._._.-_..... 7 Part I. Assay of Cripple Creek telluride ores -...I........................ 7 Nature of the ores assayed ......-.-..-...- ... ......................... 7 Preparation of the samples. ---...-....---...............--........... 9 Combination wet and fire assay ......-.-....--..-..-...-------..--.. 9 Fire assay ..............................^............................... 12 Conduct of the assay......-.--....---..:..-..........-........... 12 Charges used in assaying slags and cupels ..............^.,....-... 12 Assays for gold and silver together............................... 12 Discussion of results........-...-.....--........-..-----..... 14 Assays for gold alone .........--.....-.--...-.....--.,..-........ 15 Comparison of results .......................... ^...................... 18 Part II. The errors in gold assaying..---..--.-..--.--.--..-.-.--..-_..... 19 Cupellation losses..--...-.......-..---.-...--.-....................... 19 Absorption and volatilization .-....-......:.........-.-......... -
Conroast: Dc Arc Smelting of Dead-Roasted Sulpidde Concentrates
CONROAST: DC ARC SMELTING OF DEAD-ROASTED SULPIDDE CONCENTRATES Rodney T. Jones Mintek Private Bag X3015, Randburg, 2125 South Africa Abstract Mintek has developed and piloted a novel process for the treatment ofnickel-copper and PGM (platinwn group metal) sulphide concentrates. The ConRoast process is based on the removal of sulphur by roasting, followed by smelting ofthe dead-roasted concentrate in a DC arc furnace using an iron-based alloy as a collector for nickel, copper, cobalt, and PGMs. The environmental benefits with respect to sulphur emissions are considerable, in that essentially all ofthe sulphur is removed from the enclosed roasting equipment in a continuous stream of S02 of an appropriate strength for feeding to a sulphuric acid plant. This process allows great flexibility with respect to the selection ofore types, and does not impose limits on the minimwn quantities of contained base metals or sulphur, and can tolerate very high contents of chromite in the concentrate. The furnace alloy is water-atomized prior to leaching. Iron may be rejected from the alloy hydrometallurgically, by precipitation as hematite for example. The ConRoast process achieves very high metal recoveries, and produces high-purity metals, and a clean high grade PGM concentrate. Sulfide Smelting 2002 Edited RL. Stephens and B.Y. Sohn TMS (The Minerals, Metals & Materials Society), 2002 435 Introduction good collection ofthe PGMs. In fact, iron collection of PGMs is far more effective than matte collection. Very clean slags are produced in the furnace, containing small enough quantities of Mintek has developed and piloted a novel process for the treatment ofnickel-copper and PGM PGMs that the slags can be discarded or even sold for purposes such as road-fill or shot (platinwn group metal) sulphide concentrates.