Standard Rake Size and Rationale Rationale: to Maximize Revenue Per Rake Without Incurring Additional Operating Cost
Total Page:16
File Type:pdf, Size:1020Kb
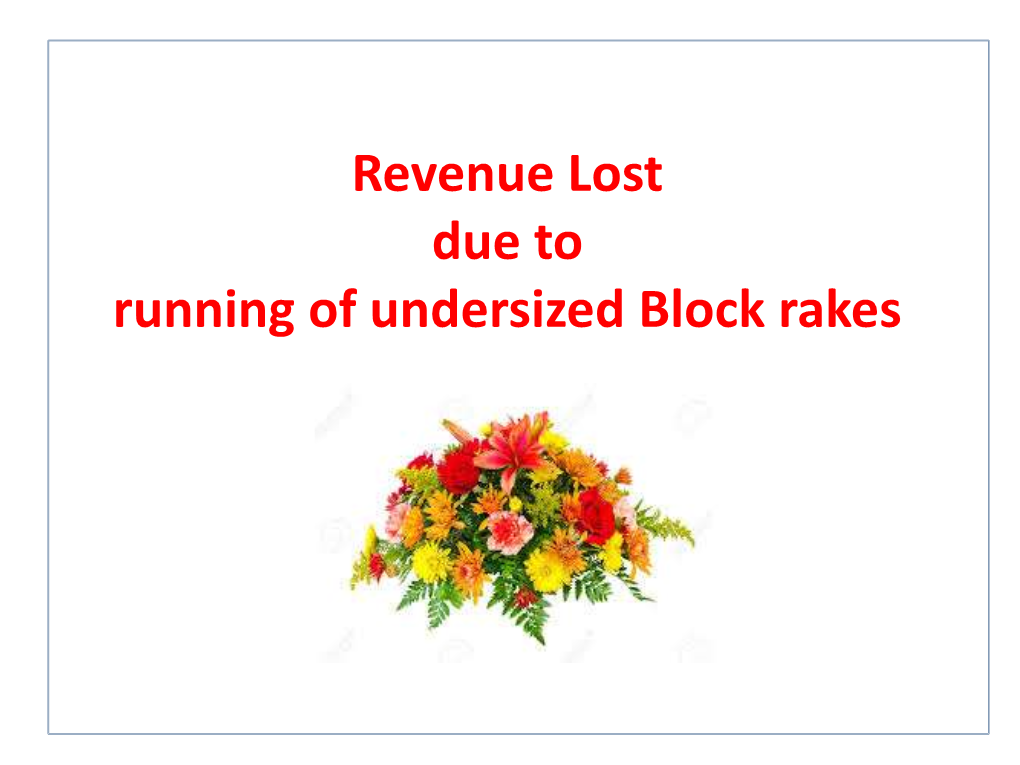
Load more
Recommended publications
-
MOI July October 2011
Vol.6, Issue 2-3 July-October -2011 The Forgotten Fast of Irom Sharmila Armed Forces Special Powers Act, 1958 We should be there: The Left and Cancell Koodankulam Project the Anna moment Lip-Service to Inclusive Growth Odisha's Little Gandhians Planning Commission's Poverty Definition: A Historic Victory of Domestic Workers Struggle An Insult to the Poor July - October 2011 Send in subscriptions, sponsorships, donations, and articles to: The Movement of India (MoI) National Alliance of Peoples' Movements (NAPM) C/O 6/6 (Basement), Jangpura B, Mathura Road, New Delhi – 110 014, India. Phone: 011 2437 4535; Mobile: +91 9818 905316 Email: [email protected] July - October 2011 1. Editorial 4 2. The Forgotten Fast of Irom Shrmila 5 3. Why Did NAPM Decide to Support Anna Hazare's Anti-Corruption Movement 10 4. We should be there: The Left and the Anna moment 12 5. Lip-Service to Inclusive Growth 17 6. How little can a person live on? 20 7. “Planning Commission's Poverty Definition: An Insult to the Poor” 23 8. Koodankulam: A Nuclear Chain Reaction 25 9. Cancell Koodankulam Project 27 10. Odisha's Little Gandhians 29 11. A Historic Victory of Domestic Workers Struggle 32 12. News & Notes 34 The Why Did NAPM Decide Forgotten M.Ravishankar Fast to Support Anna Hazare's of Irom Sharmila Anti-Corruption Movement Lip-Service “Planning Commission's Poverty Definition: to An Insult to the Poor” Inclusive Growth July - October 2011 his issue of the MOI covers a significant period in the democratic history of the Tcountry. -
T E N D E R D O C U M E N T Open Tender No. Metro/T-Coml./CP
T E N D E R D O C U M E N T Open Tender No. Metro/T-Coml./CP/Chemist Stall/8/2015 To The President of India, Acting Through the Chief Operations Manager, Metro Railway, Kolkata I/We ________________________________________________________________have read the various conditions of Tender attached hereto and hereby agree to abide by the said conditions. I/We also agree to keep this tender open for acceptance for a period of 90 days, from the date fixed for opening of the same or for a further period as may be mutually agreed upon and in default thereof, I/We shall be liable for forfeiture of my/our Earnest Money(s) of ____________.00 in full. I/We offer to take the exclusive license for running of Chemist Stalls at the areas of Metro Railway locations as specified in Annexure – I of this Tender paper in consideration of the works detailed in the schedules as per estimated rate(s) quoted vide Clause 19.0 of the terms and conditions of the tender for a initial period of five(5) years. I/We also hereby agree to abide by all terms and conditions as laid down by the Metro Railway in this Tender Document. 1.0 (i) A sum of ______________.00 furnished in prescribed form and sent herewith as Earnest Money mentioned above. (ii) If I/We do not deposit the Security Deposit as mentioned in Clause 4.0 of the terms and conditions of this tender, in the prescribed form within thirty (30) days from the date of issue of Letter of Acceptance (LOA), then : (a) The full amount of the Earnest Money shall stand forfeited to the Metro Railway and; (b) Besides forfeiture of Earnest Money as stated in Para 1.0(ii)(a) above, I/We shall be deemed to have committed breach of contract and thus I/We shall be liable for such penal measure as prescribed in Clause 3.3 of the terms and conditions of the Tender Documents. -
Recalibrated & Reactivated ATM List.Xlsx
Recalibrated & Reactivated ATM List as on 18-Jan-2017 Sr. Reactivation ATM ID Location Address City State Pin Code No. Status Andaman & GF/FF, Survey no. 104/1/2, Junglighat, 1 EPOAB650 Port Blair branch Port Blair Nicobar 744103 Activated Port blair - 744103 Islands Yes Bank Ltd., Ground Floor, Satya Akarsha, T S No. 2/5, Door No. 5-87-32, Andhra 2 SGUNC554 Guntur Branch Guntur 522007 Activated Lakshmipuram main road, Guntur, Pradesh Andhra Pradesh 522 007. Ground Floor, H. No. 9-9-2, New Ward Narasaoropet no. 16, Old Ward No. 4, Block No. 2, Opp. Andhra 3 SNAWN551 Narasaoropet 522601 Activated Branch Angele Talkies, Arundalpeta, Pradesh Narasaraopet, Guntur, Andhra Pradesh – Ground floor, KO Rise, 16/2961, Andhra 4 SNEPB671 Nellore Jawaharlal Nehru Road, Near V R Nellore 524001 Activated Pradesh College, Nellore, Andhra Pradesh. PIN – Ground floor, D. No. 75-6-25,Prakash Andhra 5 SRAPB651 Rajahmundry Nagar, RAJAHMUNDRY, E.G. Dt. A.P - - Rajahmundry 533103 Activated Pradesh 533103. Floor, 13-3-92/A1 Tilak Road Tirupati, Andhra 6 STIPB483 Tirupati Tirupati 517501 Activated Andhra Pradesh 517501 Pradesh KRANTI ARCADE, D NO. 40/1/59, Andhra 7 SVJWN217 Vijaywada NEAR BENZ CIRCLE, M.G. Vijaywada 520010 Activated Pradesh ROAD,VIJAYWADA- 520010 Ground floor, 29-37-21, Durga Vijaywada II Andhra 8 SELNC884 Agraharam, Next to Vijetha Hospital, Vijaywada 520002 Branch Pradesh Eluru Road, Vijayawada, Andhra Pradesh K.T.Road, Beside Muthoot Gold, Opp. Andhra 9 SCPO1218 CHITTINAGAR Vijaywada 520001 Activated Musizd, Chittinagar, Vijayawada - 520001 Pradesh Do- No-Near Kanada durga vardhi, Andhra 10 SMAPO363 Manipal Hospital Tadepalli, Vijayawada-522501, Andhra Vijaywada 522501 Activated Pradesh pradesh. -
Warehouse / Godown for Rent in Santragachi, Howrah (P61174322
https://www.propertywala.com/P61174322 Home » Howrah Properties » Commercial properties for rent in Howrah » Warehouses / Godowns for rent in Santragachi, Howrah » Property P61174322 Warehouse / Godown for rent in Santragachi, Howrah 6.48 lakhs Modern RCC Warehouse In Santragachi, Advertiser Details Howrah Santragachi, NH-6, Howrah, Santragachi, Howrah - 7111… Area: 36000 SqFeet ▾ Bathrooms: Four Floor: Ground Total Floors: Two Facing: South Furnished: Unfurnished Lease Period: 24 Months Monthly Rent: 648,000 Rate: 18 per SqFeet +5% Scan QR code to get the contact info on your mobile Age Of Construction: 1 Years View all properties by Win World Real Estate Available: Immediate/Ready to move Description Pictures 36000 Sq.Ft. Modern RCC Warehouse/Godown/Factory for rent near Santragachi, Howrah, with dock level and double height close to NH-6, with facility for Heavy vehicle parking, 24 hour water and power supply , Security, Vaastu Compliant, Labour quarter, Toilet, Washroom and many other modern amenities, suitable for all kinds of Manufacturing Unit/Godowns/Warehouse. The property is in the prime industrial belt of Howrah. An ideal purpose for Manufacturing or Small Scale Industry (SSI unit), Medical Store Room or RCC Warehouse Storage for FMCG. Sufficient space for loading/unloading, Kolkata is 30 minutes drive and railway station is also nearby. For more details , inspection and finalization please contact- Win world real estate(Web- Winworldrealestate). Please mention that you found this ad on PropertyWala.com when you call. Features -
2 Bedroom Independent House for Rent in Ultadanga, Kolkata
https://www.propertywala.com/P48673192 Home » Kolkata Properties » Residential properties for rent in Kolkata » Independent Houses for rent in Ultadanga, Kolkata » Property P48673192 2 Bedroom Independent House for rent in Ultadanga, Kolkata 12,000 1st Floor Of An Independent House At Advertiser Details Ultadanga NA, Ultadanga, Kolkata - 700037 (West Bengal) Area: 670 SqFeet ▾ Bedrooms: Two Bathrooms: One Floor: First Total Floors: Three Facing: South Furnished: Unfurnished Monthly Rent: 12,000 Rate: 18 per SqFeet +155% Available: Immediate/Ready to move Scan QR code to get the contact info on your mobile Description Pictures Entire 1st floor is available for rent for small family (only service holders are preferred) near Bidhannagar Rly. station. Bidhannagar rly station is 10 min walking distance. Vegetable market is 2 minutes walking distance. Nearby metro station is Sovabazar and Shyambazar. Buses for all routes are easily available. Property is approx 3 minutes walking distance from bus stand. Electricity is totally separated. Balcony Bedroom **** 2 Months Security Deposit is required. Bedroom Balcony When you contact, don't forget to mention that you saw this ad on PropertyWala.com. Features Bedroom Bedroom Interior Tiles Flooring Location Bedroom Kitchen Bathroom Bathroom Bathroom * Location may be approximate Landmarks Public Transport KOLKATA RAILWAY STATION (<1km…Bidhan Nagar Road (<1km), SEALDAH RAILWAY STATION (<5km… Dumdum (<4km), SHYAMBAZAR METRO STATION-GA… Sealdah Main (<5km), Howrah (<6km), Karunamoyee Bus Station (<6km), -
Strassenbahnen Ausserhalb Europas/Tramways Outside Europe Stand:31.12.2020/Status:31.12.2020 Afrika/Africa
STRASSENBAHNEN AUSSERHALB EUROPAS/TRAMWAYS OUTSIDE EUROPE STAND:31.12.2020/STATUS:31.12.2020 AFRIKA/AFRICA: :جمهوريّة مصر العربيّة/ÄGYPTEN/EGYPT/DSCHUMHŪRIYYAT MISR AL-ʿARABIYYA :اﻹسكندرية/ALEXANDRIA/AL-ISKANDARIYA :TURĀM AR-RAML/ترام الرمل/TRAM AL RAMLEH :محطة الرمل/EL RAMLEH-محطة النصريا ا/(LINE 1:EL NASR(VICTORIA 12.08.2019 https://www.youtube.com/watch?v=jr0MWtgEjsM EL NASR(VICTORIA)-EL RAMLEH 01:07:29 Abd-Alrahman Kaled Midra :محطة الرمل/EL RAMLEH-محطة النصر/(LINE 2:EL NASR(VICTORIA 12.08.2019 https://www.youtube.com/watch?v=cddgR2xPYbs EL NASR(VICTORIA)-EL RAMLEH 01:09:39 Abd-Alrahman Kaled Midra :محطة الرمل/EL RAMLEH-سان ستيفان/LINE 5:SAN STEFANO :محطة الرمل/EL RAMLEH-سان ستيفان/LINE 6:SAN STEFANO :TURĀM AL-MADINA/ترام المدينة/TRAM AL MADINA :المتراس/EL METRAS-النزهة/LINE 1:EL NOZHA :كرموز/KARMOUZ-النزهة/LINE 2:EL NOZHA :ساحة سانت كاترين/SAINT CATHERINE SQUARE-موراهام بك/LINE 4:MORAHAM BEY :رأس التين/RAS EL TIN-موراهام بك/LINE 6:MORAHAM BEY :كاثرين/CATHERINE-النزهة/LINE 10:EL NOZHA :الشنداء/EL SHONDAA-النزهة/LINE 11:EL NOZHA :محطة الرمل/EL RAMLEH-رأس التين/LINE 15:RAS EL TIN 20.09.2020 https://www.youtube.com/watch?v=Wm6ly-SHoxA RAS EL TIN-EL RAMLEH 33:02 (LINKES SEITENFENSTER/LEFT WINDOW!) ahmed salah 1 :كرموز/KARMOUZ-ساحة سانت كاترين/LINE 16:SAINT CATHERINE SQUARE :ساحة سانت كاترين/SAINT CATHERINE SQUARE-النزهة/LINE 18:EL NOZHA :إل ماكس/EL MAX-الشنداء/LINE 19:EL SHONDAA ÄTHIOPIEN/ETHOPIA/YÄ-ITYOPPtƏYA FEDERALAWI DIMOKRASIYAWI RIPÄBLIK/ የኢትዮጵያ ፌዴራላዊ ዲሞክራሲያዊሪፐብሊክ: ADDIS ABEBA/አዲስ አበባ: LINE:GREEN LINE:AYAT/አያት-TOR HAILOCH/በር ሃይሎክ: -
GM Meena Glory
https://www.propertywala.com/gm-meena-glory-kolkata GM Meena Glory - Rajarhat, Kolkata apartmetns with the world of happiness GM Meena Glory is presented by GM Group at Rajarhat, Kolkata offers residential project that hosts 2/3 BHK Apartment/Flat. Project ID: J460981189 Builder: GM Group Location: GM Meena Glory, Rajarhat, Kolkata (West Bengal) Completion Date: Dec, 2016 Status: Completed Description Gm Meena Glory at Rajarhat, Kolkata east by gm group is a residential project.The project offers apartment with perfect combination of contemporary architecture and features to provide comfortable living with configurations of 2 & 3 Bhk and size of the apartment ranges in between 91.51 sq. mtr and 136.57 sq.mtr. Amenities: Gymnasium Children's Play Area 24*7 Security Sports facility 24*7 Water supply Club house Lift Available Car Parking Community Hall GM Group welcomes you to the world of happiness – Meena Glory. Located in the prime location of Dassdrone, Rajarhat, this residential complex is only 5 minutes drive away from both Big Bazar and Haldiram while City Centre II in New Town is within 2 minutes drive away only. Airport and Ultadanga are only 10 and 15 minutes drive away respectively. Start your glorious living with GM Group. Features Luxury Features Security Features Lifts Security Guards Intercom Facility Recreation Land Features Swimming Pool Park Fitness Centre / GYM Club / Community Center Water Connection Club / Community Center Other features Immediate posession Society: GM Meena Glory Gallery Pictures Front View Bedroom -
ATM List As on 1-March-2016
YES BANK ATM List as on 1-March-2016 Sr. Pin Type of ATM ID Location Address City State No. Code Machine Andaman & GF/FF, Survey no. 104/1/2, Junglighat, Port 1 EPOAB650 Port Blair branch Port Blair Nicobar 744103 ATM blair - 744103 Islands Ground and First floor, “Sun Tower”, VAIZAGH - Andhra 2 SVINC712 T.S.No.1187 of Block No.53, Waltair Main Visakhapatnam 530007 ATM WALTAIR RD Road, Vishakhapatnam -530007, Andhra Pradesh Pradesh. KRANTI ARCADE, D NO. 40/1/59, NEAR Andhra 3 SVJWN217 Vijaywada BENZ CIRCLE, M.G. ROAD,VIJAYWADA- Vijaywada 520010 ATM Pradesh 520010 Sripuram, Opp. to Governor Bunglow, Andhra 4 SWAPO208 Waltair Club Visakhapatnam 530001 ATM Visakhapatnam- 530001 Pradesh Do- No-Near Kanada durga vardhi, Tadepalli, Andhra 5 SMAPO363 Manipal Hospital Vijaywada 522501 ATM Vijayawada-522501, Andhra pradesh. Pradesh 27-4-40, Suhani Mall, T.S No: 145 Market Andhra 6 SSOPO442 Suhani Mall Ward, Ward No:26, Choultry Junction, Visakhapatnam 530020 ATM Pradesh Suryabagh Main Road, Visakhapatnam -530020 Navel Park, Near Schindhya Junction Naval Andhra 7 WNAPO626 Navel Park Visakhapatnam 530014 ATM Base Post office, Visakhapatnam, Pin-530014 Pradesh Shipwright Indian navy, Vishakhapatnam - 104 Area , Andhra 8 NINPO640 School - Indian Naval Quarters, Maripalla, Vishakhapatnam, Visakhapatnam 530009 ATM Pradesh Navy AP (SVN Colony -Near Shipwright School) Shop No.-G8-15-1, Assila Mitta, RTC Complex, Andhra 9 SASPO744 ASSILA MITTA NH-5 Road, Opposite Sanghvi Jewellers, Visakhapatnam 530016 ATM Pradesh Vishakhapatnam, Andhra Pradesh- 5300156 -
Warehouse / Godown for Rent in Santragachi
https://www.propertywala.com/P87614391 Home » Kolkata Properties » Commercial properties for rent in Kolkata » Warehouses / Godowns for rent in Santragachi, Kolkata » Property P87614391 Warehouse / Godown for rent in Santragachi, Kolkata 5.13 lakhs Warehouse In Santragachi, Howrah Advertiser Details Santragachi, NH-6, Howrah, Santragachi, Kolkata (West B… Area: 27000 SqFeet ▾ Bathrooms: Four Floor: Ground Total Floors: Two Facing: South Furnished: Furnished Lease Period: 24 Months Monthly Rent: 513,000 Rate: 19 per SqFeet +10% Age Of Construction: 1 Years Scan QR code to get the contact info on your mobile Available: Immediate/Ready to move View all properties by Win World Real Estate Description Pictures 27000 Sq.Ft. Modern RCC Warehouse/Godown/Factory for rent near Santragachi, Howrah, with dock level and double height close to NH-6, with facility for Heavy vehicle parking, 24 hour water and power supply , Security, Vaastu Compliant, Labour quarter, Toilet, Washroom and many other modern amenities, suitable for all kinds of Manufacturing Unit/Godowns/Warehouse. The property is in the prime industrial belt of Howrah. An ideal purpose for Manufacturing or Small Scale Industry (SSI unit), Medical Store Room or Storage for FMCG. Sufficient space for loading/unloading, Kolkata is 30 minutes drive and railway station Warehouse is also nearby. For more details , inspection and finalization please contact- Win world real estate(Web- Winworldrealestate). When you contact, don't forget to mention that you saw this ad on PropertyWala.com. Features -
Warehouse / Godown for Rent in Santragachi
https://www.propertywala.com/P71736895 Home » Kolkata Properties » Commercial properties for rent in Kolkata » Warehouses / Godowns for rent in Santragachi, Kolkata » Property P71736895 Warehouse / Godown for rent in Santragachi, Kolkata 48,000 Modern RCC Warehouse In Santragachi, Advertiser Details Howrah Santragachi, NH-6, Howrah, Santragachi, Kolkata (West B… Area: 3000 SqFeet ▾ Bathrooms: Four Floor: Ground Total Floors: Two Facing: South Furnished: Unfurnished Lease Period: 24 Months Monthly Rent: 48,000 Rate: 16 per SqFeet +5% Scan QR code to get the contact info on your mobile Age Of Construction: 1 Years View all properties by Win World Real Estate Available: Immediate/Ready to move Description Pictures 3000 Sq.Ft. Modern World class RCC Warehouse/Godown/Factory for rent near Santragachi, Howrah, with dock level and double height close to NH-6, with facility for Heavy vehicle parking, 24 hour water and power supply , Security, Vaastu Compliant, Labour quarter, Toilet, Washroom and many other modern amenities, suitable for all kinds of Manufacturing Unit/Godowns/Warehouse. The property is in the prime industrial belt of Howrah. An ideal purpose for Manufacturing or Small Scale Industry (SSI unit), Medical RCC Warehouse Store Room or Storage for FMCG. Sufficient space for loading/unloading, Kolkata is 30 minutes drive and railway station is also nearby. For more details , inspection and finalization please contact- Win world real estate(Web- Winworldrealestate). When you call, don't forget to mention that you saw this ad on PropertyWala.com.