Americium-241 Radioisotope Thermoelectric Generator Development for Space Applications
Total Page:16
File Type:pdf, Size:1020Kb
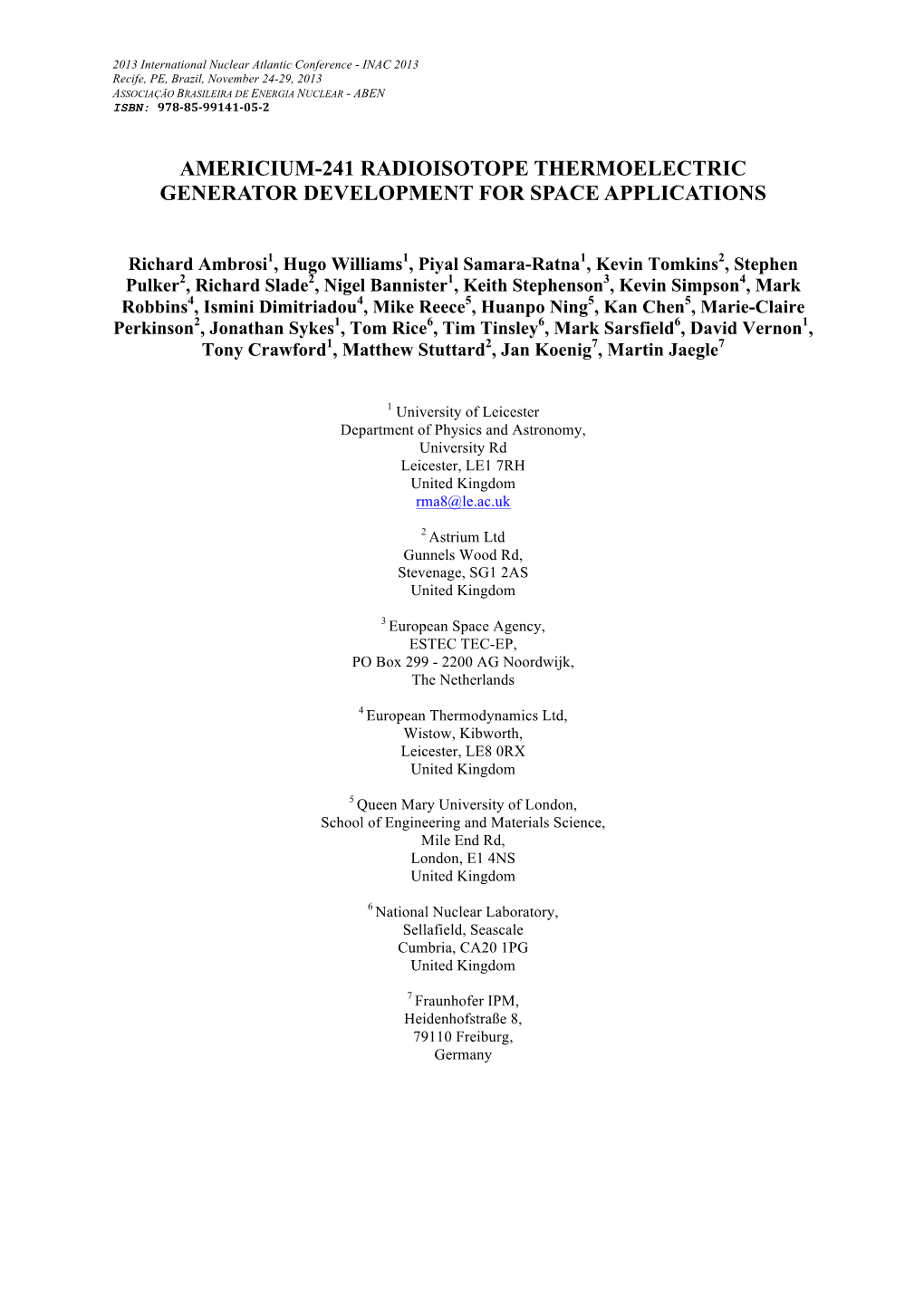
Load more
Recommended publications
-
Table 2.Iii.1. Fissionable Isotopes1
FISSIONABLE ISOTOPES Charles P. Blair Last revised: 2012 “While several isotopes are theoretically fissionable, RANNSAD defines fissionable isotopes as either uranium-233 or 235; plutonium 238, 239, 240, 241, or 242, or Americium-241. See, Ackerman, Asal, Bale, Blair and Rethemeyer, Anatomizing Radiological and Nuclear Non-State Adversaries: Identifying the Adversary, p. 99-101, footnote #10, TABLE 2.III.1. FISSIONABLE ISOTOPES1 Isotope Availability Possible Fission Bare Critical Weapon-types mass2 Uranium-233 MEDIUM: DOE reportedly stores Gun-type or implosion-type 15 kg more than one metric ton of U- 233.3 Uranium-235 HIGH: As of 2007, 1700 metric Gun-type or implosion-type 50 kg tons of HEU existed globally, in both civilian and military stocks.4 Plutonium- HIGH: A separated global stock of Implosion 10 kg 238 plutonium, both civilian and military, of over 500 tons.5 Implosion 10 kg Plutonium- Produced in military and civilian 239 reactor fuels. Typically, reactor Plutonium- grade plutonium (RGP) consists Implosion 40 kg 240 of roughly 60 percent plutonium- Plutonium- 239, 25 percent plutonium-240, Implosion 10-13 kg nine percent plutonium-241, five 241 percent plutonium-242 and one Plutonium- percent plutonium-2386 (these Implosion 89 -100 kg 242 percentages are influenced by how long the fuel is irradiated in the reactor).7 1 This table is drawn, in part, from Charles P. Blair, “Jihadists and Nuclear Weapons,” in Gary A. Ackerman and Jeremy Tamsett, ed., Jihadists and Weapons of Mass Destruction: A Growing Threat (New York: Taylor and Francis, 2009), pp. 196-197. See also, David Albright N 2 “Bare critical mass” refers to the absence of an initiator or a reflector. -
小型飛翔体/海外 [Format 2] Technical Catalog Category
小型飛翔体/海外 [Format 2] Technical Catalog Category Airborne contamination sensor Title Depth Evaluation of Entrained Products (DEEP) Proposed by Create Technologies Ltd & Costain Group PLC 1.DEEP is a sensor analysis software for analysing contamination. DEEP can distinguish between surface contamination and internal / absorbed contamination. The software measures contamination depth by analysing distortions in the gamma spectrum. The method can be applied to data gathered using any spectrometer. Because DEEP provides a means of discriminating surface contamination from other radiation sources, DEEP can be used to provide an estimate of surface contamination without physical sampling. DEEP is a real-time method which enables the user to generate a large number of rapid contamination assessments- this data is complementary to physical samples, providing a sound basis for extrapolation from point samples. It also helps identify anomalies enabling targeted sampling startegies. DEEP is compatible with small airborne spectrometer/ processor combinations, such as that proposed by the ARM-U project – please refer to the ARM-U proposal for more details of the air vehicle. Figure 1: DEEP system core components are small, light, low power and can be integrated via USB, serial or Ethernet interfaces. 小型飛翔体/海外 Figure 2: DEEP prototype software 2.Past experience (plants in Japan, overseas plant, applications in other industries, etc) Create technologies is a specialist R&D firm with a focus on imaging and sensing in the nuclear industry. Createc has developed and delivered several novel nuclear technologies, including the N-Visage gamma camera system. Costainis a leading UK construction and civil engineering firm with almost 150 years of history. -
Re-Examining the Role of Nuclear Fusion in a Renewables-Based Energy Mix
Re-examining the Role of Nuclear Fusion in a Renewables-Based Energy Mix T. E. G. Nicholasa,∗, T. P. Davisb, F. Federicia, J. E. Lelandc, B. S. Patela, C. Vincentd, S. H. Warda a York Plasma Institute, Department of Physics, University of York, Heslington, York YO10 5DD, UK b Department of Materials, University of Oxford, Parks Road, Oxford, OX1 3PH c Department of Electrical Engineering and Electronics, University of Liverpool, Liverpool, L69 3GJ, UK d Centre for Advanced Instrumentation, Department of Physics, Durham University, Durham DH1 3LS, UK Abstract Fusion energy is often regarded as a long-term solution to the world's energy needs. However, even after solving the critical research challenges, engineer- ing and materials science will still impose significant constraints on the char- acteristics of a fusion power plant. Meanwhile, the global energy grid must transition to low-carbon sources by 2050 to prevent the worst effects of climate change. We review three factors affecting fusion's future trajectory: (1) the sig- nificant drop in the price of renewable energy, (2) the intermittency of renewable sources and implications for future energy grids, and (3) the recent proposition of intermediate-level nuclear waste as a product of fusion. Within the scenario assumed by our premises, we find that while there remains a clear motivation to develop fusion power plants, this motivation is likely weakened by the time they become available. We also conclude that most current fusion reactor designs do not take these factors into account and, to increase market penetration, fu- sion research should consider relaxed nuclear waste design criteria, raw material availability constraints and load-following designs with pulsed operation. -
Compilation and Evaluation of Fission Yield Nuclear Data Iaea, Vienna, 2000 Iaea-Tecdoc-1168 Issn 1011–4289
IAEA-TECDOC-1168 Compilation and evaluation of fission yield nuclear data Final report of a co-ordinated research project 1991–1996 December 2000 The originating Section of this publication in the IAEA was: Nuclear Data Section International Atomic Energy Agency Wagramer Strasse 5 P.O. Box 100 A-1400 Vienna, Austria COMPILATION AND EVALUATION OF FISSION YIELD NUCLEAR DATA IAEA, VIENNA, 2000 IAEA-TECDOC-1168 ISSN 1011–4289 © IAEA, 2000 Printed by the IAEA in Austria December 2000 FOREWORD Fission product yields are required at several stages of the nuclear fuel cycle and are therefore included in all large international data files for reactor calculations and related applications. Such files are maintained and disseminated by the Nuclear Data Section of the IAEA as a member of an international data centres network. Users of these data are from the fields of reactor design and operation, waste management and nuclear materials safeguards, all of which are essential parts of the IAEA programme. In the 1980s, the number of measured fission yields increased so drastically that the manpower available for evaluating them to meet specific user needs was insufficient. To cope with this task, it was concluded in several meetings on fission product nuclear data, some of them convened by the IAEA, that international co-operation was required, and an IAEA co-ordinated research project (CRP) was recommended. This recommendation was endorsed by the International Nuclear Data Committee, an advisory body for the nuclear data programme of the IAEA. As a consequence, the CRP on the Compilation and Evaluation of Fission Yield Nuclear Data was initiated in 1991, after its scope, objectives and tasks had been defined by a preparatory meeting. -
Nuclear Energy & the Environmental Debate
FEATURES Nuclear energy & the environmental debate: The context of choices Through international bodies on climate change, the roles of nuclear power and other energy options are being assessed by Evelyne ^Environmental issues are high on international mental Panel on Climate Change (IPCC), which Bertel and Joop agendas. Governments, interest groups, and citi- has been active since 1988. Since the energy Van de Vate zens are increasingly aware of the need to limit sector is responsible for the major share of an- environmental impacts from human activities. In thropogenic greenhouse gas emissions, interna- the energy sector, one focus has been on green- tional organisations having expertise and man- house gas emissions which could lead to global date in the field of energy, such as the IAEA, are climate change. The issue is likely to be a driving actively involved in the activities of these bodies. factor in choices about energy options for elec- In this connection, the IAEA participated in the tricity generation during the coming decades. preparation of the second Scientific Assessment Nuclear power's future will undoubtedly be in- Report (SAR) of the Intergovernmental Panel on fluenced by this debate, and its potential role in Climate Change (IPCC). reducing environmental impacts from the elec- The IAEA has provided the IPCC with docu- tricity sector will be of central importance. mented information and results from its ongoing Scientifically there is little doubt that increas- programmes on the potential role of nuclear ing atmospheric levels of greenhouse gases, such power in alleviating the risk of global climate as carbon dioxide (CO2) and methane, will cause change. -
The Nuclear Fuel Cycle
THE COLLECTION > From the uranium mine> toI wNTasRtOeD dUisCpToIsOaN l 1 > The atom 2 > Radioactivity 3 > Radiation and man 4 > Energy 5 > Nuclear energy: fusion and fission 6 > How a nuclear reactor works 7 > The nuclear fuel cycle 7 > The nuclear fuel cycle FROM RESEARCH 8 > Microelectronics 9 > The laser: a concentrate of light TO INDUSTRY 10 > Medical imaging 11 > Nuclear astrophysics 12 > Hydrogen 7 >>TThhee nnuucclleeaarr ffuueell ccyyccllee UPSTREAM THE REACTOR: PREPARING THE FUEL IN THE REACTOR: FUEL CONSUMPTION DOWNSTREAM THE REACTOR: REPROCESSING NUCLEAR WASTE NUCLEAR WASTE © Commissariat à l’’Énergie Atomique et aux Energies Alternatives, 2005 Communication Division Bâtiment Siège - 91191 Gif-sur-Yvette cedex www.cea.fr ISSN 1637-5408. From the uranium mine to waste disposal 7 > The nuclear fuel cycle From the uranium mine to waste disposal 7 > The nuclear fuel cycle 2 > CONTENTS > INTRODUCTION 3 Uranium ore is extracted from open-pit mines – such as the McClear mines in Canada seen here – or underground workings. a m e g o C © “The nuclear fuel cycle includes an erray UPSTREAM THE REACTOR: of industrial operations, from uranium PREPARING THE FUEL 4 e mining to the disposal of radioactive l Extracting uranium from the ore 5 waste.” c Concentrating and refining uranium 6 y Enriching uranium 6 c Enrichment methods 8 l introduction uel is a material that can be burnt to pro - IN THE REACTOR: FUEL CONSUMPTION 9 Fvide heat. The most familiar fuels are wood, e Preparing fuel assemblies 10 coal, natural gas and oil. By analogy, the ura - e g a nium used in nuclear power plants is called Per unit or mass (e.g. -
Radiation Detection and Measurement for Non-Destructive Characterization and Control in Nuclear Media
Radiation detection and measurement for non-destructive characterization and control in nuclear media. Abdallah Lyoussi (CEA) IEEE DL Capetown, July 7-17, 2018 IEEE NPSS International School for Real Time Systems in Particle Physics 2018 A. LYOUSSI (CEA/DEN/CAD) FRANCE [email protected] SUMMARY INTRODUCTION Specific features, constraints and requirements Examples of radiation measurements and associated instrumentation for : - In Pile Measurements - Radioactive waste characterization and control Conclusions and prospects RADIATION DETECTION & MEASUREMENTS: APPLICATION DOMAINS / SUB-DOMAINS Domain « Materials Science & Industry » Domain NDT / Neutronography K / Industrial «Geophysics» measurement/Imagery Oil & Gas A Neutron and Photons Moisture monitoring B J facilities Applications of Reactor monitoring / C In‐core I Instrumentation Domain and radiation Reactor monitoring / Fundamental Physics D «F. Physics & Space » detection Ex‐core H systems Nuclear facility E systems Homeland security Domain Environment Control F «Security » & Dose Rate Monitors Domain «Nuclear» G Medical imaging Domain «Medical» Nuclear Media : Nuclear Fuel Cycle Concentration Mining Natural Conversion Uranium Enrichment © CEA Reprocessed Depleted Uranium Uranium Storage Vitrified Plutonium HLW Compacted ILW UOx Fuel Storage Ultimate Fabrication Rad Wastes MOX Fuel MA FP Fabrication L&ILW-VC Spent fuel Reprocessing Plant Reactor Storage Spent MOX fuel Nuclear Fuel Cycle : Instrumentation & measurement are key aspects for control & characterization Main -
The Actinide Research Quarterly Highlights Recent Achievements and Ongoing Programs of the Nuclear Materials Technology (NMT) Division
1st quarter 2001 TheLos Actinide Alamos National Research Laboratory N u c l e a r M Quarterlya t e r i a l s R e s e a r c h a n d T e c h n o l o g y Researcher Provides a Historical Perspective for Plutonium Heat Sources In This Issue We begin the seventh year of Actinide Research Quarterly For more than 30 years, by focusing on Los Alamos has designed, major programs in 4 developed, manufactured, NMT Division. The Pit Manufacturing and tested heat sources for publication team Project Presents Many radioisotope thermoelectric also welcomes its Challenges generators (RTGs). These new editor, Meredith powerful little “nuclear “Suki” Coonley, who is 6 batteries” produce heat assuming the position Can Los Alamos from the decay of radioac- while Ann Mauzy Meet Its Future Nuclear tive isotopes—usually takes on acting Challenges? plutonium-238—and can management provide electrical power duties in IM-1. 9 and heat for years in Detecting and satellites, instruments, K.C. Kim Predicting Plutonium and computers. Aging are Crucial to continued on page 2 Stockpile Stewardship 12 Pit Disassembly and Conversion Address a ‘Clear and Present Danger’ 14 Publications and Invited Talks Newsmakers 15 Energy Secretary Spencer Abraham Addresses Employees artist rendering of Rover Pathfinder on Mars from NASA/JPL Nuclear Materials Technology/Los Alamos National Laboratory 1 Actinide Research Quarterly This article was contributed by Gary Rinehart (NMT-9) Early development efforts from the Each Multihundred Watt RTG provided about 157 mid-1960s through the early 1970s focused watts of power at the beginning of the mission. -
Toxicological Profile for Plutonium
PLUTONIUM 153 5. PRODUCTION, IMPORT/EXPORT, USE, AND DISPOSAL 5.1 PRODUCTION No information is available in the TRI database on facilities that manufacture or process plutonium because this chemical is not required to be reported under Section 313 of the Emergency Planning and Community Right-to-Know Act (Title III of the Superfund Amendments and Reauthorization Act of 1986) (EPA 1998). Plutonium was the first human-made element to be synthesized in weighable amounts. 238Pu was discovered in 1940 by Seaborg and co-workers; it was synthesized by the bombardment of uranium with deutrons (2H). Isotopes with mass numbers 228–247 have been identified; all are radioactive (Clark et al. 2006). Trace amounts of plutonium are found worldwide, mostly due to fall-out from atmospheric nuclear testing, which ended in 1980 and released several isotopes of plutonium, including 238Pu, 239Pu, 240Pu, and 241Pu (Clark et al. 2006; DOE 2005a; Eisenbud and Gesell 1997). Plutonium is not considered a naturally occurring element; however, trace amounts of 239Pu are found in naturally occurring uranium ores, but the amounts are in such small amounts that extraction is not practical (Clark et al. 2006; EPA 2006b; Lide 2008). Small amounts of 244Pu exist in nature from remnants of primordial stellar nucleosynthesis (Clark et al. 2006). Small amounts of plutonium were produced in natural reactors, such as the Oklo natural reactor in Gabon, which existed about 2 billion years ago (DOE 2005a). The most common form of plutonium found in the environment is 239Pu, followed by 240Pu (DOE 1999a). Large quantities of plutonium were first produced during the 1940’s as part of the Manhattan Project in order to produce the atomic bomb. -
Mars Exploration Rover: Thermal Design Is a System Engineering Activity
SAE 041 ICES-331 Mars Exploration Rover: Thermal Design is a System Engineering Activity Glenn T. Tsuyuki, Arturo Avila, Henry 1. Awaya, Robert J. Krylo, Keith S. Novak, and Charles J. Phillips Jet Propulsion Laboratory, California Institute of Technology Copyright 0 2004 SAE International ABSTRACT The primary mission objectives were to determine the aqueous, climatic, and geologic history of a pair of sites The Mars Exploration Rovers (MER), were launched in on Mars where the conditions may have been favorable June and July of 2003, respectively, and successfully to the preservation of evidence of pre-biotic or biotic landed on Mars in early and late January of 2004, processes. The primary missions requirements were to respectively. The flight system architecture implemented deliver two identical rovers to the surface of Mars in many successful features of the Mars Pathfinder (MPF) order to conduct geologic and atmospheric investigations system: A cruise stage that transported an entry vehicle for at least 90 Sols (approximately 93 Earth days) after that housed the Lander, which in turn, used airbags to landing and to demonstrate a total traverse distance of at cushion the Rover during the landing event. The initial least 600 m, with a goal of 1000 m’. thermal design approach focused on adopting the MPF design wherever possible, and then concentrating on the The MER flight system design adapted many successful totally new Rover thermal design. Despite a features of the Mars Pathfinder (MPF) spacecraft design fundamentally sound approach, there were several that was launched in 1996 and landed on Mars on July 4, salient lessons learned. -
Radioisotope Power Systems Reference Book for Mission Designers and Planners
https://ntrs.nasa.gov/search.jsp?R=20160001769 2019-08-31T04:26:04+00:00Z JPL Publication 15-6 Radioisotope Power Systems Reference Book for Mission Designers and Planners Radioisotope Power System Program Office Young Lee Brian Bairstow Jet Propulsion Laboratory National Aeronautics and Space Administration Jet Propulsion Laboratory California Institute of Technology Pasadena, California September 2015 JPL Publication 15-6 Radioisotope Power Systems Reference Book for Mission Designers and Planners Radioisotope Power System Program Office Young Lee Brian Bairstow Jet Propulsion Laboratory National Aeronautics and Space Administration Jet Propulsion Laboratory California Institute of Technology Pasadena, California September 2015 This document was generated by the Jet Propulsion Laboratory, California Institute of Technology, under a contract with the National Aeronautics and Space Administration. It summarizes research carried out at Jet propulsion Laboratory and by Glenn Research Center. For both facilities, funding was provided by the NASA Radioisotope Power Systems (RPS) Program Office at Glenn Research Center. Reference herein to any specific commercial product, process, or service by trade name, trademark, manufacturer, or otherwise, does not constitute or imply its endorsement by the United States Government or the Jet Propulsion Laboratory, California Institute of Technology. © 2015 California Institute of Technology. Government sponsorship acknowledged. Abstract The RPS Program’s Program Planning and Assessment (PPA) Office commissioned the Mission Analysis team to develop the Radioisotope Power Systems (RPS) Reference Book for Mission Planners and Designers to define a baseline of RPS technology capabilities with specific emphasis on performance parameters and technology readiness. The main objective of this book is to provide RPS technology information that could be utilized by future mission concept studies and concurrent engineering practices. -
Radioisotope Thermo-Electric Generator
International Journal of Advances in Science Engineering and Technology, ISSN: 2321-9009 Volume-5, Issue-2, Aprl.-2017 http://iraj.in ENERGY STORAGE DEVICES IN SPACE CRAFT - RADIOISOTOPE THERMO-ELECTRIC GENERATOR 1S.PARVEEN, 2S.VICTOR VEDANAYAKAM 1Ph.D scholar, Assistant Professor, Department of Physics, Gates Institute of Technology, Gooty, A.P 2Assistant Professor, Department of Physics, Madanapalle Institute of Technology and Science, Madanapalle, A.P E-mail: [email protected], [email protected] Abstract - A radioisotope thermoelectric generator (RTG, RITEG) is an electrical generator that uses an array of thermo couples to convert the heat released by the decay of a suitable radioactive material intoelectricity bythe Seebeck effect. RTGs have been used as a power sources in satellites and space probes. RTGs are usually the most desirable power source for unmaintained situations that need a few hundred watts (or less) of power for durations too long for fuel cells, batteries, or generators to provide economically and in places where solar cells are not practical. Safe use of RTGs have no moving parts and are very simple: fundamentally, they consist of a fuel cell, thermocouples and shielding. These compact, reliable systems provide basic mission fuel and keep critical spacecraft components warm enough to function in the cold, dark reaches of deep space.ISRO is about to use Nuclear Technology/Radioisotope thermoelectric generators(RTGs) to power Chandrayaan-2. The mission was planned to fly on a geosynchronous satellite launch vehicle MK-II (GSLV) with an approximate lift-off massof 2650kg from SatishDhawan center on Sriharikota Island. India might have been the first country to reach moon but our tricolor was the 4th national flag to be planted on the moon’s surface.Radio isotope power systems are a nuclear powered system to generate electric power to feed communication and scientific systems on a space craft.