A Functional Modified Graphene Oxide/Nanodiamond/Nano Zinc
Total Page:16
File Type:pdf, Size:1020Kb
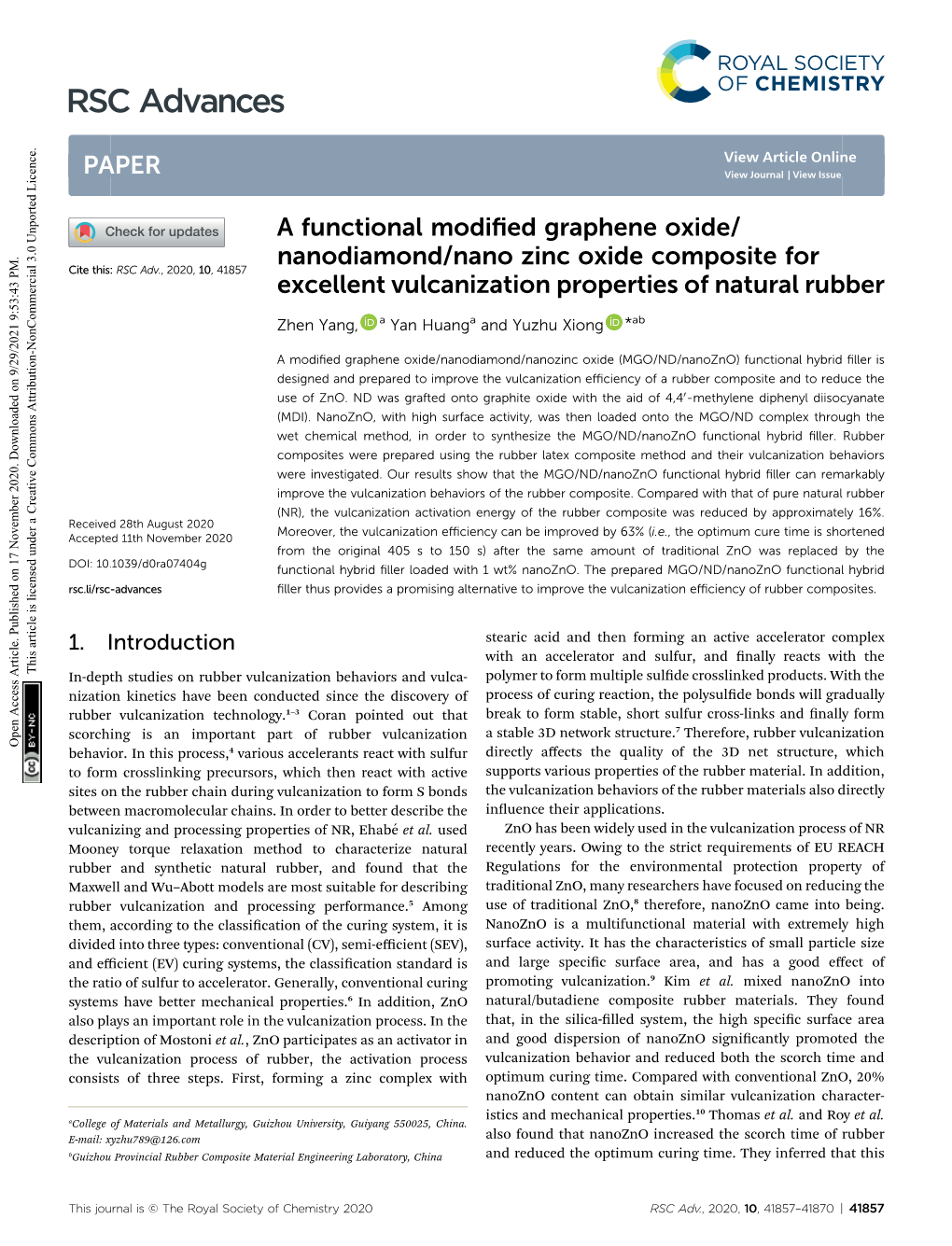
Load more
Recommended publications
-
Forensic Analysis of Fire Debris Residues
INDIANAPOLIS-MARION COUNTY FORENSIC SERVICES AGENCY Doctor Dennis J. Nicholas Institute of Forensic Science 40 SOUTH ALABAMA STREET INDIANAPOLIS, INDIANA 46204 PHONE (317) 327-3670 FAX (317) 327-3607 EVIDENCE SUBMISSION GUIDELINE #4 FORENSIC ANALYSIS OF FIRE DEBRIS RESIDUES INTRODUCTION A fire investigation is an unenviable task. The devastation, charred debris, collapsed structures, water soaked ashes, together with the smoke and stench, makes the task uninviting and seemingly impossible. The basic role of an investigator at a fire scene is twofold: firstly to determine the origin of the fire (the site where the fire began), and secondly to examine closely the site of origin to try and determine what it was that caused a fire to start at or around that location. An examination would typically begin by trying to gain an overall impression of the site and the fire damage; this could be done at ground level or from an elevated position. From this, one might proceed to an examination of the materials present, the fuel load, and the state of the debris at various places. Fire debris is a general term used to define the materials collected from a fire scene for laboratory examination. When a fire investigator suspects that a fire might have been deliberately set using accelerants such as ignitable liquids, it is possible to collect and analyze fire debris to see if such products are present. Combustion requires three elements — heat, oxygen, and fuel. Fire will be extinguished when any one of these three elements is absent. Fire does not burn solids or liquids (in general), but rather the gases formed above them. -
Residues of Fire Accelerant Chemicals Volume I: Risk
RESIDUES OF FIRE ACCELERANT CHEMICALS VOLUME I: RISK ASSESSMENT Prepared for: Intermountain Region USDA Forest Service Ogden, UT By: Headquarters: 8000 Westpark Drive, Suite 400 McLean, VA 22102 October 16, 2002 Abstract This report summarizes the results of quantitative human health and ecological risk assessments of chemical residues in the environment from the use of a variety of accelerants to ignite prescribed burns. On a per-unit basis for each ignition method, no risks were identified for human health, nor for general wildlife species. However, consideration should be given at the planning stage to protecting sensitive aquatic species in small watersheds that have limited potential for diluting residue chemicals that may run off or erode to surface water. Table of Contents 1.0 Introduction.............................................................................................................................1 1.1 Background: Fire Accelerants.....................................................................................1 1.2 Identification of Accelerant Residues ..........................................................................2 1.3 Overview of the Human Health Risk Assessment .......................................................4 1.4 Overview of the Ecological Risk Assessment..............................................................4 2.0 Human Health Hazard Assessment.........................................................................................6 2.1 Background Information ..............................................................................................6 -
Model 950-ASH Arson Scanner Hydrocarbons and Accelerants Detector Operation and Maintenance
Model 950-ASH Arson Scanner Hydrocarbons and Accelerants Detector Operation and Maintenance www.arsondetection.com M950-ASHTM1218 © December 2018 Model 950-ASH Table of Contents Cover 1 Table of Contents 2 Top View 3 Features & Benefi ts 4 Introduction 5 Principle of Operation 6 Operation: Powering ON 7 Operation: Setting the Sensitivity 8 Operation: Detecting Hycrocarbons / Accelerants 9-10 Operation: Purging the Sensor 11 Principle of Operation for Ultraviolet and White LED Arrays 12 How Ultraviolet Light is Used in Arson Investigations 13-15 Recommended Investigation Techniques 16 Storage and Maintenance 17 Removal / Replacement of Sensor 18-19 Battery Run Time & Battery Charging 20 Troubleshooting 21 Hydrocarbon, Accelerants, and Gases Detected by Model 950-ASH 22 Model 950-ASH Warranty Information 23 WARNING!! - Model 950-ASH Should Not Be Used To Detect Carbon Monoxide! Page 2 Model 950-ASH Top View Telescoping Sensor and Probe Locking LED Arrays Clips Quick Start Analog Meter Guide Sensor Display Guard Power Indicator Mute Indicator Mute Switch Audio Sound Coiled Extension Cord High/Low Range Switch Port Power On/Off and Detection Range Control Hydrocarbon/Accelerant Detection Indicators Meter Backlight Rubber Grip Indicators for Low Battery & Charging Purge Switch USB and Indicator Charging Light / UV Switch Jack and Indicator PagePage 3 Model 950-ASH Features & Benefi ts • Portable, easy to use, rugged. • Detects approximately 125 hydrocarbons and accelerants including heating gases. • High/Low Range aids in pinpointing source of high hydrocarbon/accelerant concentration. • Solid State Sensor, housed in a protective guard, with a coiled extension cord. • Audio and Visual displays indicate detection of suspect material. -
Identification of Accelerants, Fuels and Post-Combustion Residues Using A
Analyst Identification of accelerants, fuels and post -combustion residues using a colorimetric sensor array Journal: Analyst Manuscript ID: AN-ART-04-2015-000806.R1 Article Type: Paper Date Submitted by the Author: 14-Jul-2015 Complete List of Authors: Li, Zheng; University of Illinois at Urbana-Champaign, Jang, Minseok; University of Illinois at Urbana-Champaign, Askim, Jon; University of Illinois at Urbana-Champaign, Suslick, Kenneth; University of Illinois at Urbana-Champaign, Chemistry Page 1 of 7 Please do notAnalyst adjust margins 1 2 3 4 Analyst 5 6 7 ARTICLE 8 9 10 11 Identification of accelerants, fuels and post-combustion residues 12 13 using a colorimetric sensor array 14 Received 00th January 20xx, a a a a Accepted 00th January 20xx Zheng Li, Minseok Jang, Jon R. Askim and Kenneth S. Suslick* 15 16 DOI: 10.1039/x0xx00000x A linear (1x36) colorimetric sensor array has been integrated with a pre-oxidation technique for detection and identification of a variety of fuels and post-combustion residues. The pre-oxidation method permits the conversion of fuel 17 www.rsc.org/ 18 vapor into more detectable species and therefore greatly enhances the sensitivity of the sensor array. The pre-oxidation 19 technique used a packed tube of chromic acid on an oxide support and was optimized in terms of the support and 20 concentration. Excellent batch to batch reproducibility was observed for preparation and use of the disposable pre- 21 oxidation tubes. Twenty automotive fuels including gasolines and diesel from five gasoline retailers were individually 22 identifiable with no confusions or misclassifications in quintuplicate trials. -
Occupational'asthma'(HP)% Maleic%Anhydride%
ACMT%Board%Review% Miscellaneous%Toxicants% Brandon'Wills,'DO,'FACEP,'FACMT' Fellowship%Director,%Medical%Toxicology% Department%of%Emergency%Medicine% VCU%Medical%Center% Virginia%Poison%Center% VCU TOX 2.2.10 Miscellaneous Toxicants 2.2.10.1 Acrolein 2.2.10.2 Acrylamides 2.2.10.3 Acrylates 2.2.10.4 Amines 2.2.10.5 Aniline Compounds 2.2.10.6 Azides 2.2.10.7 Bromide Compounds 2.2.10.8 Butadienes 2.2.10.9 Carbon Disulfide 2.2.10.10 Chlorates 2.2.10.11 Coal Tar Products 2.2.10.12 Diamines 2.2.10.13 Dibromochloropropane (DBCP) 2.2.10.14 Dimethylacetamide (DMAC) 2.2.10.15 Dimethylformamide (DMF) 2.2.10.16 Dinitrobenzene 2.2.10.17 Dinitrotoluene (DNT) 2.2.10.18 Epichlorohydrin 2.2.10.19 Ethylene Dibromide (EDB) 2.2.10.20 Ethylenediamine (EDA) 2.2.10.21 Fluoride Compounds 2.2.10.22 Fuels 2.2.10.23 Hexachloro-1,3-Butadiene (HCBD) 2.2.10.24 Isocyanates (eg, toluene diisocyante) 2.2.10.25 Maleic Anhydride 2.2.10.26 Mercaptans 2.2.10.27 Methylene Diamine (MDA) 2.2.10.28 Nitriles 2.2.10.29 O-Phenylenediamine (OPD) 2.2.10.30 Phosphorus/phosphides 2.2.10.31 Phthalates 2.2.10.32 Polymers 2.2.10.33 Resins 2.2.10.34 Styrene 2.2.10.35 Trimellitic Anhydride 2.2.10.36 Triorthocresylphosphate (TOCP) 2.2.10.37 Xylidine Our%Gameplan% Organize%your%memory% Using%study%aids%(quick%look%at%flashcards)% 60%min:%brief%reviewP%focus%on%test%rather%than%content%% 20%min:%Miscellaneous+Toxicants+Jeopardy%overview% Sources% Dr.%Sean%Bryant% Dr.%Mike%Greenburg% Sullivan,%2nd%Ed% Greenburg,%2nd%Ed% My%board%review%notes% http://pubchem.ncbi.nlm.nih.gov/%(structures)% -
F-500 Project
Introduction This project was undertaken to address concerns encountered in the field by fire investigators and Accelerant Detection Canine Teams in relation to the potential of ignitable liquid “masking” properties of certain fire suppression additives. As modern fire suppression tactics evolve, certain chemical additives are commonly being introduced into the extinguishment phase of fire department operations. The introduction of these chemical additives present a concern to the fire investigation community relative to their potential affect on the forensic investigation of a fires cause, where factors relative to the fires ignition and spread may rely on the identification or confirmation of ignitable liquid residues as often relied upon to identify the use of an accelerant in an intentionally set fire. Today’s fire and arson investigators have many resources available to them to better pinpoint the origin and cause of a fire. One of those resources includes the use of a certified accelerant detection K9 team. This team is a valuable tool in identifying the presence of ignitable liquids through the use of their keen olfactory senses. For detection to be possible the K9 Team, much like the forencic laboratory Analyst, rely on the presence of ignitable liquid vapor residue in or on substrate materials left after a fire occurs. The concern over the use of a suppression additive focuses on its potential to mask or chemically alter the ignitable liquid to a state K9 Shadow making a positive indication which would inhibit the canine or crime laboratory from for ignitable liquid in Arson Bureau test identifying the presence of the original ignitable liquid in facility. -
High-Performance Ceramic/Epoxy Composite Adhesives Enabled by Rational Ceramic Bandgaps J
www.nature.com/scientificreports OPEN High-performance ceramic/epoxy composite adhesives enabled by rational ceramic bandgaps J. B. Hu High over-all properties, including low dielectric loss, high breakdown strength, high mechanical shock strength, high thermal conductivity and high weight stability, are very difcult to simultaneously achieve in electrical-insulation applicable cured potting-adhesive materials. To deal with this challenge, in this work, we have designed and fabricated a series of epoxy based composite potting-adhesives flled with low-cost and high-performance inorganic micro-particles including alpha-silica, alpha- alumina and alpha-SiC. Combination employment of high-molecular-weight and low-molecular-weight epoxy resins as matrices has been made. Heat-induced curing or crosslink of resin matrices has been carried out. Large band gap of silica fller has endowed the cured composite with high breakdown strength and ageing breakdown strength, and meanwhile relatively high deformation trait of silica has led to high shock strength of cured composite. Silica fller has been found to be superior to other two fllers, namely, optimal over-all properties such as dielectric, breakdown, mechanical and thermal features have been obtained in silica flled cured composite. High breakdown strength of ~48 MV m−1 and shock strength of ~9950 J m−2 have been achieved in silica loaded composite. This work might open up the way for large-scale fabrication of promising epoxy-based hybrid potting-adhesives. Recently, potting adhesive materials with promising electrical, mechanical and thermal properties have triggered general attention and research interest in the feld of fabricating aerospace applicable special power supplies1. -
Analysis of the Tracheal Contents Using Headspace Gas Chromatography-Mass Spectrometry to Screen for Accelerant Use
ANALYSIS OF THE TRACHEAL CONTENTS USING HEADSPACE GAS CHROMATOGRAPHY-MASS SPECTROMETRY TO SCREEN FOR ACCELERANT USE Nobuyuki Adachi* **, Hiroshi Kinoshita*, Minori Nishiguchi*, Motonori Takahashi*, Harumi Ouchi*, Taka- ko Minami*, Kiyoshi Matsui*, Takehiko Yamamura*, Hiroyuki Motomura***, Nao Ohtsu*, Shie Yoshida*, Kiyoshi Ameno**** and Shigeru Hishida* *Department of Legal Medicine, Hyogo College of Medicine, 1-1 Mukogawa-cho, Nishinomiya, Hyogo, 663-8501, Japan **Joint –Use Research facilities, Hyogo College of Medicine, 1-1 Mukogawa-cho, Nishinomiya, Hyogo, 663-8501, Japan ***Forensic Science Laboratory, Hyogo Prefectural Police Headquarters, 4-1, Shimoyamate -dori 5-chome, Chuo-ku, Kobe, 650-8510, Japan ****Department of Forensic Medicine, Faculty of Medicine, Kagawa University, 1750-1 Ikenobe, Miki, Kita, Kagawa, 761-0793, Japan Summary We describe here the usefulness of analysis of tracheal contents in a case of death by fire, which revealed that the deceased had used the accelerants. The analysis of tracheal contents provides useful information for the determination of the circumstances of the scene. Key words: burning – accelerants, gas chromatography – mass spectrometry – alipathic hydrocarbons Souhrn Analýza obsahu průdušnice plynovou chromatografií rovnovážné plynné fáze – hmotnostní spektrometrií, která stanoví, zda byly použity hořlaviny Autoři poukazují na užitečnost analýzy tracheálního obsahu v případě smrti uhořením, která odhalila, že zemřelá použila hořlavinu. Analýza obsahu průdušnice poskytuje důležité informace, které umožňují stanovit okolnosti na místě činu. Klíčová slova: hoření – hořlaviny, plynová chromatografie – kvantitativní spektrometrie – alifatické uhlovodíky Soud. Lék., 54, 2008, No. 1, p. 2–3 Chromatographic separation was done in a fused–silica capillary INTRODUCTION column DB-5MS (30 m X 0.25 mm I.D., 0.25 μm film thickness) (J&W Scientific, Folsom, CA, USA). -
The Use of Canines in Accelerant Detection That Need to Be Realised
Use of Canines in Accelerant Detection > History Of Canine Use Page 3 > Selection and Training Page 4 > The Fire Scene Investigation Page 6 > Other Uses of these Canines Page 8 > Uses in Australia Page 10 > Case Study - “Gus” Page 10 > Limitations and Disadvantages Page 11 > > Overview of Canine Use Page 13 2 Use Of Canines In Accelerant Detection - By Emma Wagner History Accelerant is a substance which, when ignited gives rise to the rapid spread of fire. Common accelerants include petrol, kerosene, diesel fuel etc. and when found at a fire scene without logical explanation, can be proof of intent and preparation - thus good evidence to suggest arson. The use of canines to aid the detection of accelerant in a fire investigation was first proposed in the early 1980’s in the US State of Connecticut. Canines had been used successfully in the US for some time in drug detection and bomb detection and a feasibility study conducted on canines’ ability to detect accelerant suggested success in this area also. On 1st May 1986, a training program was initiated as part of a joint effort between three agencies; the Bureau of Alcohol, Tobacco and Firearms (BATF), the Connecticut State Police (CSP) and New Haven State’s Attorney Generals Office. A black female Labrador retriever, “Mattie” was obtained from the Guide Dog Foundation and was trained by the CSP. In the first 38-day period Mattie was trained to detect various odours associated with flammable liquids. As the training progressed, Mattie was able to detect these odours at very low levels, and tests proved that she could identify 17 different odours. -
United States Patent (19) 11 Patent Number: 6,071,994 Hummerich Et Al
US00607 1994A United States Patent (19) 11 Patent Number: 6,071,994 Hummerich et al. (45) Date of Patent: Jun. 6, 2000 54) FORMALDEHYDE-FREE AQUEOUS 5,427,587 6/1995 Arkens et al.. BNDERS 5,536,766 7/1996 Seyffer et al. .......................... 524/100 5,661,213 8/1997 Arkens et al. .......................... 524/555 (75) Inventors: Rainer Hummerich, Worms; Axel FOREIGN PATENT DOCUMENTS Kistenmacher, Ludwigshafen; Walter Denzinger, Speyer; Gunnar Schornick, O 116930 8/1984 European Pat. Off.. Neuleiningen; Bernd Reck, Grinstadt; O 445 578 9/1991 European Pat. Off.. Manfred Weber, Mannheim, all of O 583 086 2/1994 European Pat. Off.. German O 651 088 10/1994 European Pat. Off.. y 864. 151 1/1953 Germany. 73 ASSignee: BASF Aktiengesellschaft, 2217 2014450 712 10/19727/1971 Germany. Ludwigshafen, Germany 2357951 5/1975 Germany. 21 Appl. No.: 09/125,113 4408 688 9/1995 Germany. 22 PCT Filed: Feb. 19, 1997 OTHER PUBLICATIONS Patent Abstracts of Japan, vol. 014, No.220, May 10, 1990, 86 PCT No.: PCT/EP97/00770 JP Publ. No. 02 051531, Feb. 21, 1990, Appl. No.63200120, S371 Date: Aug. 18, 1998 Aug. 12, 1988, Koinuma Yasuyoshi, et al., Title: Water Soluble and Self-curing polymer and cured product thereof. S 102(e) Date: Aug. 18, 1998 Patent Abstracts of Japan, vol. 005, No. 180, Nov. 19, 1981, 87 PCT Pub. No.: WO97/31036 JPPubl. No. 56 104905, Aug. 21, 1981, Chino yasuyoshi, et y - - - al, Title: Production of Novel Modified Resin, Appl. No. PCT Pub. Date: Aug. 28, 1997 55008500, Jan. 28, 1980. 30 Foreign Application Priority Data Primary Examiner Edward J. -
Taking a Bite out of Forensic Science: the Misuse of Accelerant-Detecting Dogs in Arson Cases, 48 J
UIC Law Review Volume 48 Issue 4 Article 7 2015 Taking a Bite Out of Forensic Science: The Misuse of Accelerant- Detecting Dogs in Arson Cases, 48 J. Marshall L. Rev. 1149 (2015) Andrew Scott Follow this and additional works at: https://repository.law.uic.edu/lawreview Part of the Animal Law Commons, Criminal Law Commons, and the Evidence Commons Recommended Citation Andrew Scott, Taking a Bite Out of Forensic Science: The Misuse of Accelerant-Detecting Dogs in Arson Cases, 48 J. Marshall L. Rev. 1149 (2015) https://repository.law.uic.edu/lawreview/vol48/iss4/7 This Comments is brought to you for free and open access by UIC Law Open Access Repository. It has been accepted for inclusion in UIC Law Review by an authorized administrator of UIC Law Open Access Repository. For more information, please contact [email protected]. TAKING A BITE OUT OF FORENSIC SCIENCE: THE MISUSE OF ACCELERANT- DETECTING DOGS IN ARSON CASES ANDREW SCOTT* I. THE PROBLEM ............................................................... 1149 II. AN INTRODUCTION TO FORENSIC SCIENCE AND ARSON INVESTIGATION .............................................................. 1151 A. Forensic Science .....................................................1151 B. Scientific Evidence in the Courtroom ...................1152 C. Arson Investigation and the Use of Accelerant- Detecting Canines ..................................................1154 D. The Emergence of Junk Science ............................1159 III. THE SCIENCE BEHIND ARSON INVESTIGATION AND THE ROLE OF CANINE HANDLER TEAMS ............................... 1161 A. Subjectivity of Fire-Pattern Analysis and other Arson Indicators ................................................................1161 B. False Alerts and Handler Bias among Canine Handler Teams ......................................................................1163 C. Improper Use of the Canine Handler Team and the Wrongful Conviction of James Hebshie ................1166 D. The Dilemma of Unconfirmed Accelerant Alerts .1167 IV. -
Fire Service Resource Directory 2018/2019
Department of Fire Services Executive Office of Public Safety & Security Fire Service Resource Directory 2018/2019 Compiled as a Public Service in Cooperation with the Massachusetts Property Insurance Underwriting Association Mission Statement The mission of the Department of Fire Services is, through coordinated training, education, prevention, investigation, and emergency response, to provide the citizens of Massachusetts with the ability to create safer communities; to assist and support the fire service community in the protection of life and property; to promote and enhance firefighter safety; and to provide a fire service leadership presence in the Executive Office of Public Safety and Security in order to direct policy and legislation on all fire related matters. I am pleased to forward to you the 2018-2019 Massachusetts Fire Service Resource Directory which is provided as a public service to our fire service constituency I would take this opportunity as well to thank one of our true partners, the Massachusetts Property Insurance Underwriting Association and their president, Mr. John K. Golembeski, for working on statewide fire prevention programs with the Department of Fire Services over the years and for providing the resources to publish this directory Peter J Ostroskey State Fire Marshal Department of Fire Services 978-567-3100 See division listings for fax numbers www.mass.gov/dfs Stow Campus Springfield Campus P O Box 1025 - State Road 100 Grochmal Avenue Stow, MA 01775 Springfield, MA 01151 Contents Directions to the Department of Fire Services ............................................... 2 Quick Reference Numbers .............................................................. .. .. ................. 4 Emergency Resource Activation ......................................... .......................... ...... 5 Fire & Explosion Investigation Section .. .. .................. .. .... ................. .. ...... .... ......................... S Hazardous Materials Response Teams ....