General Information Name of Manufacturer Sanofi
Total Page:16
File Type:pdf, Size:1020Kb
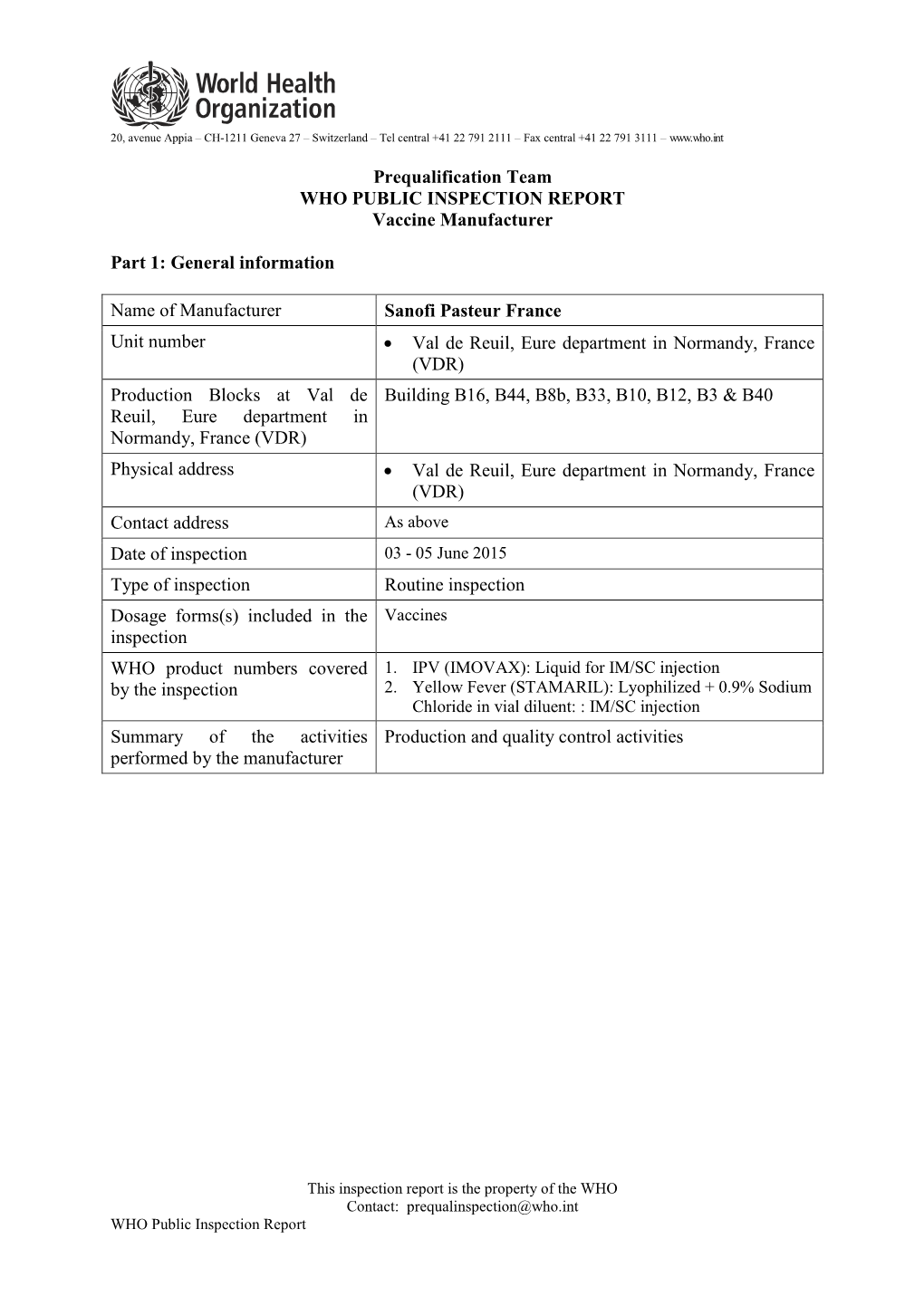
Load more
Recommended publications
-
Impact De L'arasement D'un Barrage Sur Les Transferts Sédimentaires, La Remise En Suspension Des Polluants Organiques Et M
Long-term accumulation of metals and persistent pollutants (PAHs, PCBs, organochlorine pesticides) from Eure river watershed (France) in sediments: possible consequences of a dam removal THOMAS GARDES1,2,*, YAN LABERDESQUE1,2, EDOUARD PATEAU2, MAXIME DEBRET2, YOANN COPARD2, JULIEN DELOFFRE2, STÉPHANE MARCOTTE3, ANNE-LISE DEVELLE4, PIERRE SABATIER4, ERIC CHAUMILLON5, FLORENCE PORTET-KOLTALO1 1University of Rouen-Normandy, UMR CNRS 6014 COBRA, 55 rue Saint Germain, 27000 Evreux, France. 2University of Rouen-Normandy, UMR CNRS 6143 M2C, 3 place Emile Blondel, 76821 Mont-Saint-Aignan Cedex, France. 3INSA of Rouen, Normandy University, UMR CNRS 6014, avenue de l'Université, 76801 Saint-Etienne-du-Rouvray Cedex, France. 4University of Savoie Mont Blanc, UMR CNRS 5204 EDYTEM, 5 boulevard de la mer Caspienne, 73370 Le Bourget du Lac Cedex, France. 5University of La Rochelle, UMR CNRS 7266 LIENSs, 2 rue Olympe de Gouges, 17000 La Rochelle, France. *[email protected] Table of contents 1. SCIENTIFIC CONTEXT : OSS 276 PROJECT 2. MATERIALS AND METHODS 2.1. The Eure Watershed 2.2. Core Sampling 2.3. Core Dating by XRF Core Scanner data comparison 3. LONG-TERM ACCUMULATION OF ORGANIC AND METALLIC POLLUTANTS 3.1. ∑16PAHs 3.2. ∑7PCBs 3.3. Trace-Metal Elements : Pb 4. CONCLUSIONS AND PROSPECTS 18-22 June 2017 - Thomas Gardes 16th ICCE 2017 - Oslo, Norway 2 SCIENTIFIC CONTEXT METERIALS AND METHODS LONG-TERM ACCUMULATION OF ORGANIC AND METALLIC POLLUTANTS CONCLUSIONS AND PROSPECTS • Context of the European Water Framework Directive (2000/60/CE) -
Sols Et Sous-Sols
1 DREAL Centre Val de Le sol : des avancées Loire dans la connaissance Septembre 2015 Le sol, défini comme la couche supérieure de la croûte terrestre, est un milieu mul- tifonctionnel et complexe qui sert de support aux activités humaines. Il est soumis à de multiples menaces dont les plus importantes sont l'érosion, l'artificialisation et les pollutions. Celles-ci peuvent affecter de façon durable le fonctionnement des écosystèmes, la qualité des ressources en eau, la capacité à maintenir une ac- tivité économique, et impacter la santé humaine. Malgré l'importance de son rôle le sol reste encore peu connu et ne bénéficie pas d'une protection juridique spé- cifique comme d'autres milieux. La préservation des fonctionnalités du sol passe par la réalisation de leur inventaire et de leur cartographie. Près des deux tiers de la surface de la région Centre-Val de Loire sont dédiés à l'activité agricole qui dépend fortement du maintien de la qualité du sol. Tous les usages du territoire peuvent être remis en cause par une dégradation des composantes de la qualité des sols. Le sol, une ressource non renouvelable à préserver e sol, la couche supérieure de la croûte ment urbain, activités industrielles et agri- L terrestre, est constitué d'un mélange de coles. Les menaces que ces pressions font particules minérales, de matière organique, peser sur le sol sont clairement identifiées d'eau, d'air et d'organismes vivants. Sa for- aux niveaux français et européen : artificia- mation résulte de processus complexes d'al- lisation et imperméabilisation, tassement, tération des roches sous l'effet du climat, et érosion, diminution des teneurs en ma- des activités biologiques (pédogénèse) aux- tières organiques, inondation et glissements quels s'ajoutent les activités humaines. -
LA VALLÉE DE L'eure D'acquigny À MENILLES, LA BASSE VALLÉE DE L'iton (Identifiant National : 230009110)
Date d'édition : 27/10/2020 https://inpn.mnhn.fr/zone/znieff/230009110 LA VALLÉE DE L'EURE D'ACQUIGNY À MENILLES, LA BASSE VALLÉE DE L'ITON (Identifiant national : 230009110) (ZNIEFF Continentale de type 2) (Identifiant régional : 8401) La citation de référence de cette fiche doit se faire comme suite : DREAL Haute-Normandie, .- 230009110, LA VALLÉE DE L'EURE D'ACQUIGNY À MENILLES, LA BASSE VALLÉE DE L'ITON. - INPN, SPN-MNHN Paris, 57P. https://inpn.mnhn.fr/zone/znieff/230009110.pdf Région en charge de la zone : Haute-Normandie Rédacteur(s) :DREAL Haute-Normandie Centroïde calculé : 517618°-2456965° Dates de validation régionale et nationale Date de premier avis CSRPN : 26/11/2010 Date actuelle d'avis CSRPN : 08/09/2020 Date de première diffusion INPN : 23/10/2020 Date de dernière diffusion INPN : 23/10/2020 1. DESCRIPTION ............................................................................................................................... 2 2. CRITERES D'INTERET DE LA ZONE ........................................................................................... 7 3. CRITERES DE DELIMITATION DE LA ZONE .............................................................................. 7 4. FACTEUR INFLUENCANT L'EVOLUTION DE LA ZONE ............................................................. 7 5. BILAN DES CONNAISSANCES - EFFORTS DES PROSPECTIONS ........................................... 8 6. HABITATS ..................................................................................................................................... -
Coteaux Calcaires De La Vallée De L'eure
Secteurs potentiels de restauration de la biodiversité en Normandie Coteaux calcaires de la vallée de l’Eure Mesures de protection/ Localisation Département : Eure gestion connues E.P.C.I. : CC du Pays du Neubourg, CA Agglo du Pays de Dreux, CC Eure-adrie-Seine, CA f Zone Spéciale de Conservation Seine Normandie Agglomération, CA Seine Eure, CA Evreux Portes de Normandie. (Directive Habitats) Communes : Acquigny, Le Boulay-Morin, Ailly, Le Cormier, Amfreville-sur-Iton, Le f Site classé Mesnil-Jourdain, Le Plessis-Hebert, Autheuil-Authouillet, Louviers, Boisset-Les- f ZNIEFF de type 2 Prevanches, Menilles, Boncourt, Merey, Brosville, Mesnil-sur-L’estree, Caillouet- f ZNIEFF de type 2 Orgeville, Terres de Bord, Cailly-sur-Eure, Canappeville, Muzy, Chambray, Neuilly, Croisy-sur-Eure, Normanville, Croth, Pacy-sur-Eure, Clef-Vallée-d’eure, Parville, Epieds, Pinterville, Evreux, Rouvray, Ezy-sur-Eure, Fains, Saint-Vigor, Fontaine- sous-Jouy, Vaux-sur-Eure, Gadencourt, Garennes-sur-Eure, Hardencourt-Cocherel, Heudreville-sur-Eure, Hondouville, Houetteville, Houlbec-Cocherel, Irreville, Ivry- la-Bataille, Jouy-sur-Eure, La Haye-le-Comte, La Vacherie Statuts de propriété f Propriété privée f Domaine communal f Forêt publique Milieux principaux Pelouses calcicoles, boisements calcicoles, landes sèches, cavités. DIRECTION RÉGIONALE DE L’ENVIRONNEMENT, DE L’AMÉNAGEMENT ET DU LOGEMENT NORMANDIE Enjeux principaux Principales espèces rares et/ou protégées Les milieux ouverts calcicoles sont menacées par Reconnues pour leur valeur paysagère, les pelouses des l’enfrichement progressif, préjudiciable à la préservation coteaux calcaires présentent aussi une extraordinaire de la biodiversité des pelouses. C’est au stade de la variété botanique, entomologique et ornithologique. pelouse rase que la flore patrimoniale est la plus riche. -
Schema De Coherence Territoriale Du Pays D'avre
SCHEMA DE COHERENCE TERRITORIALE DU PAYS D’AVRE D’EURE ET D’ITON 2 / Projet d’Aménagement et de Développement Durables (PADD) Le Pays d’Avre, d’Eure et d’Iton : Territoire privilégié d’accueil, de développement et de diversités Avril 2015 PADD SOMMAIRE PREAMBULE 5 LES ORIENTATIONS DU PADD 13 ORIENTATION 1 / UN TERRITOIRE QUI FIXE LA QUALITE DE SON CADRE DE VIE COMME CONDITION DE SON DEVELOPPEMENT 15 I. STRUCTURER LE DEVELOPPEMENT PAR UN MAILLAGE COHERENT ET HIERARCHISE DU TERRITOIRE ......... 17 1. Mailler le territoire pour un développement maîtrisé .................................................................. 17 2. Préserver le cadre de vie par une urbanisation plus compacte et plus structurée ..................... 18 3. Proscrire le mitage des espaces ................................................................................................ 19 II. MAINTENIR ET DEVELOPPER LES RICHESSES ENVIRONNEMENTALES, PAYSAGERES ET AGRICOLES .......... 20 1. Protéger et rétablir les continuités écologiques, ainsi que le paysage «remarquable» .............. 20 2. Préserver les grandes plaines agricoles et des surfaces herbagères stratégiques aux élevages .. ................................................................................................................................................... 21 3. Conserver le paysage bâti et non bâti «ordinaire» ..................................................................... 21 III. DEVELOPPER L’URBANISATION EN ACCORD AVEC LA NATURE DES SITES .............................................. -
Annexe Plan De Prevention Des Risques D'inondation
Département de l’Eure Elaboration du PLAN LOCAL D’URBANISME ANNEXE PLAN DE PREVENTION DES RISQUES D’INONDATION (PPRI) Approbation Vu pour être annexé à la délibération du Conseil Municipal en date du : Extra-Muros - 61, quai de Seine - 75 019 Paris - Tél : 01 53 95 29 90 - Fax : 01 45 78 31 77 Direction Départementale de l’Equipement de l’Eure PLAN DE PREVENTION DES RISQUES D’INONDATION « EURE – AVAL » ………………………………………………………………………………………...………………………………………… RAPPORT DE PRESENTATION AOUT 2003 Service Aménagement du Territoire et de l’Environnement SOMMAIRE Préambule 2 A. Contexte législatif du PPR 2 1. Textes de loi 2 2. Effets du PPR 2 3. Objectifs poursuivis par le PPR 3 B. Prescription du PPR 3 C. Nature des phénomènes d’inondation pris en compte 4 D. Principes adoptes pour l’élaboration du PPR 5 1. Choix de la crue de référence 5 2. Caractérisation des aléas 5 3. Prise en compte des enjeux 5 E. Zonage et règlement PPR 6 1. Choix du zonage PPR 6 2. Règlement PPR 8 Plan de Prévention des risques d’inondation « Eure Aval » – Rapport de présentation 1 PRÉAMBULE La présente note accompagne et présente le Plan de Prévention des Risques Inondation (PPR) des communes d’Incarville, Louviers, Pinterville, Acquigny, et Heudreville sur Eure. Elle vise à fournir les informations essentielles qui ont motivé l’élaboration du PPR, qui ont servi à sa réalisation et qui sont utiles à son application. A. CONTEXTE LÉGISLATIF DU PPR 1. Textes de loi La loi n°87.565 du 22 juillet 1987 relative à l’organisation de la sécurité civile, à la protection de la forêt contre l’incendie et à la prévention des risques majeurs a institué (articles 40.1 à 40.7) la mise en application des Plans de Prévention des Risques Prévisibles (PPR). -
Les Lotissements Remarquables Identifiés Dans L'eure – Val De Reuil
Service Territorial de l'Architecture et du Patrimoine de l'Eure (DRAC Haute-Normandie) Connaissance n°51 – 28 octobre 2012 - France POULAIN et Guillaume YON Les lotissements remarquables identifiés dans l'Eure – Val de Reuil La Direction Générale des Patrimoines au sein du ministère de la Culture et de la Communication a demandé à l'ensemble de ses services déconcentrés de réaliser un travail d'inventaire durant l'année 2012 concernant les lotissements remarquables sortis de terre depuis l'après-guerre. Les Essentiels « Connaissance » n°47, 48, 49, 50 et 51 ainsi que l'Essentiel « Conseil » n°32 en sont issus. Si Val de Reuil ne peut servir d'exemples pour le reste du département, il a quand même été étudié car c'est un projet d’aménagement qui peut être considéré comme « mémorable ». Val-de-Reuil symbolise les difficultés d’une ville nouvelle à prendre racine dans un terreau nouveau. Dans les années 1960, fondée sur l’idée d’une prise de conscience collective des problèmes de l’architecture et de la ville, l’Etat décide la construction de villes nouvelles pour remédier à la croissance désordonnée de certaines grandes agglomérations. Neuf villes sont ainsi créées en France au début des années 1970. Le projet d’une ville nouvelle dans la boucle de la Seine voit le jour pour limiter l’expansion de l’agglomération parisienne et de l’agglomération rouennaise. Répondant à des impératifs économiques, démographiques et déjà environnementaux, le programme était de réaliser une opération pilote d’urbanisation intégrée à l’environnement rural, c’est-à-dire une ville à la campagne. -
Délégation À L'aménagement Du Territoire Et À L'action Régionale (DATAR) ; Directeur Et Services Rattachés ; Chargé De Mission (1966-1981)
Premier ministre ; Délégation à l'aménagement du territoire et à l'action régionale (DATAR) ; Directeur et services rattachés ; Chargé de mission (1966-1981) Répertoire (19850747/1-19850747/16) Archives nationales (France) Pierrefitte-sur-Seine 1985 1 https://www.siv.archives-nationales.culture.gouv.fr/siv/IR/FRAN_IR_012742 Cet instrument de recherche a été encodé en 2011 par l'entreprise diadeis dans le cadre du chantier de dématérialisation des instruments de recherche des Archives Nationales sur la base d'une DTD conforme à la DTD EAD (encoded archival description) et créée par le service de dématérialisation des instruments de recherche des Archives Nationales 2 Archives nationales (France) INTRODUCTION Référence 19850747/1-19850747/16 Niveau de description fonds Intitulé Premier ministre ; Délégation à l'aménagement du territoire et à l'action régionale (DATAR) ; Directeur et services rattachés ; Chargé de mission Date(s) extrême(s) 1966-1981 Nom du producteur • Chargé de mission (délégation interministérielle à l'aménagement du territoire et à l'attractivité régionale) Localisation physique Pierrefitte DESCRIPTION Présentation du contenu Sommaire Dossiers de M. Paul Mingasson, chargé de mission. Art 1 (86 AJ bis 790) : Mission d’études en Angleterre sur l’urbanisme, 1977. Art 1 (86 AJ bis 790). Aménagement du Sud-Picardie et des vallées de l’Ysieux et de la Theve, 1974-1981. Art 1-2 (86 AJ bis 790-791). Aménagement de la ville nouvelle du Vaudreuil, 1968-1979. Art 3 (86 AJ bis 792) : Rénovation de Paris (dont aménagement de la villette et des halles), 1966-1981. Art 2, 4-15 (86 AJ bis 791, 793-804) : Désindustrialisation et urbanisation des départements de la région parisienne (dont aménagement de la Défense), 1965-1982. -
Pont-De-L'arche
L La maison M Le Vieux Manoir à une porte qui traversait le en avant-solier ou Manoir de Manon rempart. La rue présente de The Gabled House The Old Manor House belles et pittoresques maisons e e e à pans de bois. Pont-de-l’Arche Ce type de maison à encorbel- Cette bâtisse des XVI , XII et XVIII The name of the street is a lements ayant pour spécificité siècle, fut habitée par la Duchesse distortion of ‘basse sentelle’ which Cité médiévale • A medieval town de comporter des arcades était de Longueville, plus tard par le means ‘low path’. This street un type d’architecture courant compositeur Jules Massenet puis reached as far as the Seine via a Circuit découverte • Discovery tour au Moyen-Âge et jusqu’au XVIIe/ par le photographe Jacques- gate through the town walls. Along XVIIIe siècle. Il disparut avec Henri Lartigue. the street are several beautiful and picturesque half-timbered houses. les guerres. Cet édifice est le The Duchess of Longueville lived in this th dernier de notre territoire. Ce 17 century house, which was later the home of the composer Jules Massenet type d’encorbellement a permis VILLAGE D’ARTISTES and subsequently the photographer AN ARTISTS’ TOWN de faire passer le trottoir sous Jacques-Henri Lartigue. le 1er étage sans raser la maison La ville vit naître Eustache lors de l’élargissement de la rue Hyacinthe Langlois (1777-1837) au XIXe siècle. qui fut peintre et dessinateur, élève de David, mais aussi This type of corbelled house with Pont-de-l’Arche et son histoire arcades was very common between graveur, poète et conservateur History of Pont-de-l’Arche the Middle Ages and the 17th and du Musée des Antiquités de Pont-de-l’Arche est située au cœur de la Haute-Normandie, à la rencontre des pittoresques vallées de la 18th centuries, but went out of use Rouen, dont il fut le fondateur. -
L'irrigation En Région Centre 60% 54%
DOSSIER Janvier 2011 Dossier IRRIGATION Les principales caractéristiques technico-économiques de l’irrigation en région Centre Ce dossier a pour objectif de présenter les informations disponibles concernant l’irrigation dans le Centre. Il permet de situer la région en terme d’utilisation de l’eau pour l’irrigation en lien avec les cultures et les territoires. Il fait aussi le point sur la place de la région Centre par rapport au niveau national. Les données proviennent des différentes sources de l a statistique agricole (statistique annuelle, données du Réseau d’Information Comptable Agricole, enquêtes structures des exploitations, recensements agricoles, données administratives) mais également d’autres partenaires (DREAL, Agences de l’eau, SOeS, Ch ambre régionale d’agriculture, Agence Bio, FranceAgriMer,…) Une note méthodologique, en fin de document, décrit de façon détaillée les principales sources utilisées. Ce dossier est mis à jour chaque année, en septembre, suite à la publication des chiffres de la statistique agricole annuelle. 1 Liste des éléments du dossier : DONNEES GENERALES SUR L’IRRIGATION EN REGION CENTRE .......................................................... 3 -1- Les prélèvements d’eau................................................................................................................................ 3 -1-a- Volumes d’eau prélevés........................................................................................................................ 3 -1-b- Origine des prélèvements d’eau en région Centre -
Décret En Conseil D'etat Du 14 Novembre 2017 Déclarant D'utilité Publique Le Projet De
16 novembre 2017 JOURNAL OFFICIEL DE LA RÉPUBLIQUE FRANÇAISE Texte 34 sur 154 Décrets, arrêtés, circulaires TEXTES GÉNÉRAUX MINISTÈRE DE LA TRANSITION ÉCOLOGIQUE ET SOLIDAIRE TRANSPORTS Décret du 14 novembre 2017 déclarant d’utilité publique les travaux de construction du contournement est de Rouen – Liaison A 28-A 13, comprenant les liaisons autoroutières entre l’autoroute A 28 (commune de Quincampoix), l’autoroute A 13 (commune d’Incarville) et la route départementale RD 18E (commune de Saint-Etienne-du-Rouvray), conférant le statut autoroutier à ces liaisons et portant mise en compatibilité des schémas de cohérence territoriale de la Métropole Rouen Normandie, du Pays entre Seine et Bray et de Seine Eure Forêt de Bord ainsi que des documents d’urbanisme des communes d’Alizay, Igoville, Incarville, Le Manoir, Léry, Les Damps, Val-de-Reuil et Le Vaudreuil, dans le département de l’Eure, et des communes de Bois-l’Evêque, Boos, Fontaine-sous-Préaux, Gouy, Isneauville, La Neuville-Chant- d’Oisel, Les Authieux-sur-le-Port-Saint-Ouen, Montmain, Oissel, Préaux, Quévreville-la-Poterie, Quincampoix, Roncherolles-sur-le-Vivier, Saint-Aubin-Celloville, Saint-Aubin-Epinay, Saint- Etienne-du-Rouvray, Saint-Jacques-sur-Darnétal, Tourville-la-Rivière et Ymare, dans le dépar- tement de la Seine-Maritime NOR : TRAT1707082D Le Premier ministre, Sur le rapport du ministre d’Etat, ministre de la transition écologique et solidaire, Vu le code de l’environnement, notamment ses articles L. 122-1, L. 122-2 à L. 122-3-3, L. 123-1 à L. 123-6, L. 123-9 à L. 123-19, L. -
Liste Des Écoles Ecole Adresse Tél
Circonscription de Louviers - Liste des écoles Ecole Adresse Tél. Courriel Ecole primaire Arc-en- Allée du Jardin d'Edouard [email protected] ciel 27400 Acquigny 09 67 28 08 61 1 rue de l'église Ecole primaire [email protected] 27600 Ailly 02 32 53 40 87 3 Route Evreux Ecole primaire [email protected] 27400 Amfreville-sur-Iton 02 32 50 45 25 5 Rue des Ecoles Ecole primaire [email protected] 27430 Andé 02 32 59 93 86 Ecole maternelle Le 4 allee Charles Perrault [email protected] Chat Botte 27940 Aubevoye 02 32 53 12 78 Ecole maternelle Le 30 rue de la Chartreuse [email protected] Petit Charlemagne 27940 Aubevoye 02 32 53 72 83 Ecole élémentaire Les 5 rue Maurice Ravel [email protected] prunus 27940 Aubevoye 02 32 53 01 99 Ecole élémentaire 32 rue de la Chartreuse [email protected] Grand Charlemagne 27940 Aubevoye 02 32 53 27 07 Ecole élémentaire 23 rue Jean de Becker Remy [email protected] H.Bernard 27940 Aubevoye 02 32 53 05 28 Ecole élémentaire Le Allee Edith Piaf [email protected] Soleil 27940 Aubevoye 02 32 53 80 95 Ecole maternelle 12 chemin de l'Epine Blanche [email protected] intercommunale 27700 Bernières-sur-Seine 02 32 54 69 49 8 rue des Ecoles Ecole primaire [email protected] 27400 Canappeville 02 32 50 50 65 7 place Etienne Lemeilleur Ecole primaire [email protected] 27600 Fontaine-Bellenger 02 32 52 99 32 Ecole maternelle Flora 19 rue de la Colonie [email protected] Tristan 27600 Gaillon 02 32 53 39 98 Ecole maternelle L.