Effect of Turning Amount on Metallurgical Qualities And
Total Page:16
File Type:pdf, Size:1020Kb
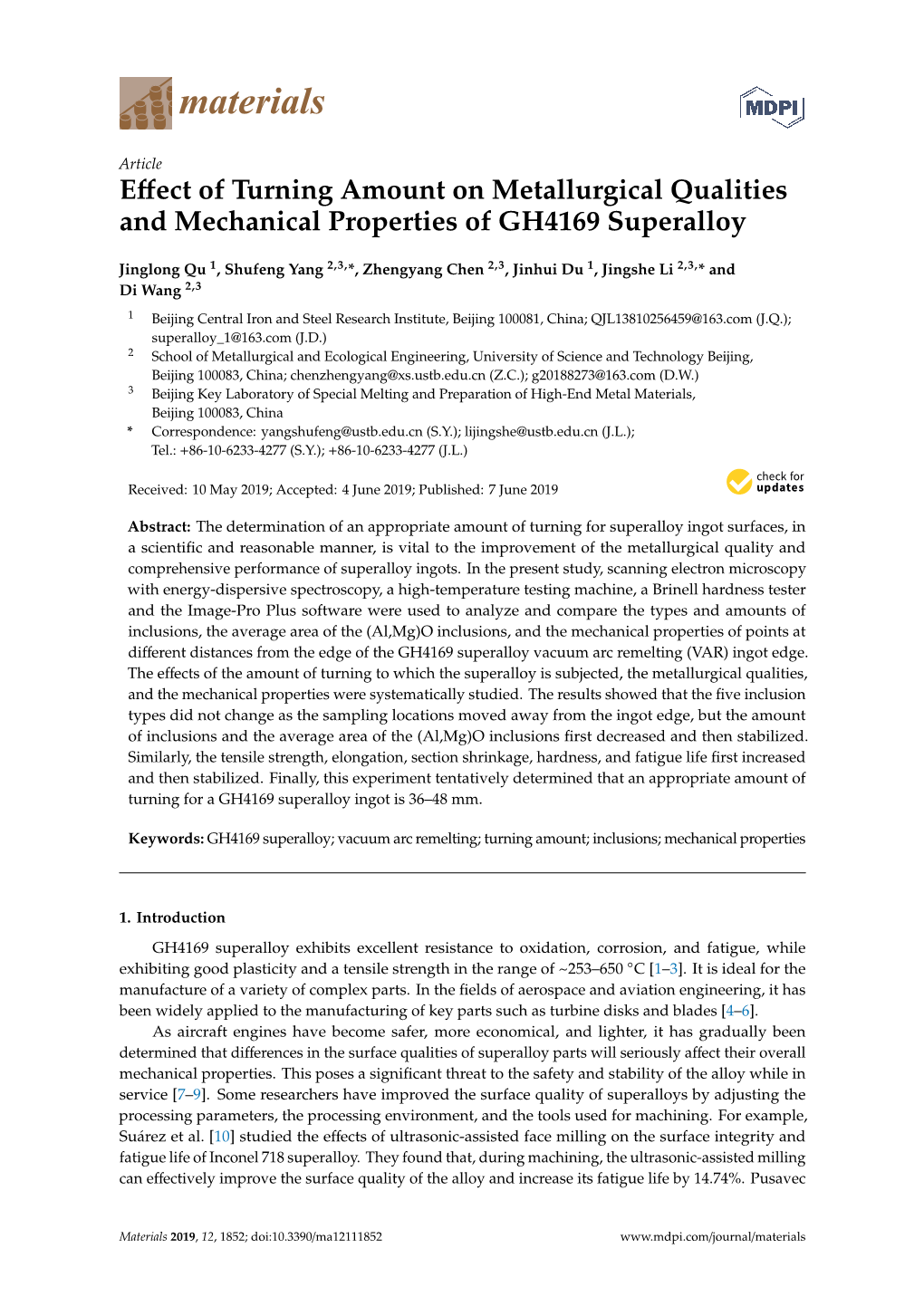
Load more
Recommended publications
-
Progress the Business and Technology of Heat Treating ® May/June 2008 • Volume 8, Number 3
An ASM International® HEATPublication TREATING PROGRESS THE BUSINESS AND TECHNOLOGY OF HEAT TREATING ® www.asminternational.org MAY/JUNE 2008 • VOLUME 8, NUMBER 3 HEAT TREATMENT OF LANDING GEAR HEAT TREAT SIMULATION MICROWAVE HEATING SM Aircraft landing gear, such as on this U.S. Navy FA18 fighter jet, must perform under severe loading conditions and in many different environments. HEAT TREATMENT OF LANDING GEAR The heat treatment of rguably, landing gear has Alloys Used perhaps the most stringent The alloys used for landing gear landing gear is a complex requirements for perform- have remained relatively constant operation requiring ance. They must perform over the past several decades. Alloys A under severe loading con- like 300M and HP9-4-30, as well as the precise control of time, ditions and in many different envi- newer alloys AF-1410 and AerMet ronments. They have complex shapes 100, are in use today on commercial temperature, and carbon and thick sections. and military aircraft. Newer alloys like control. Understanding the Alloys used in these applications Ferrium S53, a high-strength stainless must have high strengths between steel alloy, have been proposed for interaction of quenching, 260 to 300 ksi (1,792 to 2,068 MPa) landing gear applications. The typical racking, and distortion and excellent fracture toughness (up chemical compositions of these alloys to100 ksi in.1/2, or 110 MPa×m0.5). are listed in Table 1. contributes to reduced To achieve these design and per- The alloy 300M (Timken Co., distortion and residual formance goals, heat treatments Canton, Ohio; www.timken.com) is have been developed to extract the a low-alloy, vacuum-melted steel of stress. -
Development of Low-Cost Casting Titanium Alloys: an Integrated Computational
Development of Low-cost Casting Titanium Alloys: An Integrated Computational Materials Engineering (ICME) Guided Study Dissertation Presented in Partial Fulfillment of the Requirements for the Degree Doctor of Philosophy in the Graduate School of The Ohio State University By Zhi Liang Graduate Program in Materials Science and Engineering The Ohio State University 2018 Dissertation Committee Professor Alan A. Luo, Advisor Professor Glenn Daehn Professor Ji-cheng Zhao Copyrighted by Zhi Liang 2018 Abstract Titanium alloys have proved to be important lightweight structural materials since 1960’s, due to their excellent intermediate temperature mechanical properties, corrosion resistance and weldability. Their good property-to-weight ratios make them ideal for many high-end and weight-sensitive applications. However, the application of titanium alloys is still limited due to the high costs in raw materials and manufacturing, indicating the importance of developing new cost-effective titanium alloys. Compared with other lightweight structural alloys (e.g. aluminum, magnesium), the raw material cost for titanium alloys is generally considered as expensive due to its expensive alloying elements such as vanadium, molybdenum, and tin. The cost issue is further amplified by the difficulties in using conventional machining methods for component-shaping due to the low thermal conductivity. Therefore, cost-effective titanium alloys should address either aspect. This work focuses on the goal of developing new cost-effective Ti-Al-Fe- Mn titanium alloys for the casting process via Integrated Computational Materials Engineering (ICME) approach by using cheaper alloying elements and net-shape manufacture process. Calculation of Phase Diagram (CALPHAD) work on the Ti-Al-Mn ternary system was conducted to establish the reliable thermodynamic database to guide the alloy design. -
Effect of Compound Jacketing Rolling on Microstructure and Mechanical
EFFECT OF COMPOUND JACKETING ROLLING ON MICROSTRUCTURE AND MECHANICAL PROPERTIES OF SUPERALLOY GH4720Li Jinglong Qu 1, Minqing Wang 1, Jianxin Dong 2, Guilin Wu 3, Ji Zhang 1 1 Central Iron and Steel Research Institute, Superalloy Department, No.76, Xueyuan Nanlu, Beijing, 100081, China 2 University of Science and Technology Beijing, Department of Materials Science and Technology, No.30, Xueyuan Lu, Beijing, 100083,China 3 Northeast Special Steel Group Co., Ltd., Liaoning Fushun, 113001, China Keywords: GH4720Li Alloy, Compound Jacketed Rolling, Microstructure, γ′ phase Abstract In this paper, a compound jacketed rolling technique for superalloy GH4720Li is experimentally investigated. The results show that microstructure of GH4720Li is susceptible to hot working parameters. When rolling temperature is about 1130ºC, a fine-grained microstructure, excellent mechanical properties and high yield strength can be obtained. In addition, the rolling temperature can be controlled effectively, friction force between ingot and roller can be reduced, surface cracking induced by rolling can be avoided, and uniform microstructure can be obtained using compound jacketing. When accumulative strain of rolling is greater than 65%, the coarse columnar dendritic microstructure can be refined completely and grain size of ASTM 8 obtained. After heat treatment, GH4720Li bars exhibit excellent mechanical properties. Introduction GH4720Li is a high strength and difficult-to-deform superalloy with excellent mechanical, corrosion resistant and oxidation resistant properties. It is now widely used in aircraft and land-based turbine discs. In practice, the temperature required for a long-term use of GH4720Li is below 700 °C. The weight percent of Al+Ti is as high as 7.5%, and the amount of γ′ strengthening phase is as high as 40%. -
Primary Mill Fabrication
Metals Fabrication—Understanding the Basics Copyright © 2013 ASM International® F.C. Campbell, editor All rights reserved www.asminternational.org CHAPTER 1 Primary Mill Fabrication A GENERAL DIAGRAM for the production of steel from raw materials to finished mill products is shown in Fig. 1. Steel production starts with the reduction of ore in a blast furnace into pig iron. Because pig iron is rather impure and contains carbon in the range of 3 to 4.5 wt%, it must be further refined in either a basic oxygen or an electric arc furnace to produce steel that usually has a carbon content of less than 1 wt%. After the pig iron has been reduced to steel, it is cast into ingots or continuously cast into slabs. Cast steels are then hot worked to improve homogeneity, refine the as-cast microstructure, and fabricate desired product shapes. After initial hot rolling operations, semifinished products are worked by hot rolling, cold rolling, forging, extruding, or drawing. Some steels are used in the hot rolled condition, while others are heat treated to obtain specific properties. However, the great majority of plain carbon steel prod- ucts are low-carbon (<0.30 wt% C) steels that are used in the annealed condition. Medium-carbon (0.30 to 0.60 wt% C) and high-carbon (0.60 to 1.00 wt% C) steels are often quenched and tempered to provide higher strengths and hardness. Ironmaking The first step in making steel from iron ore is to make iron by chemically reducing the ore (iron oxide) with carbon, in the form of coke, according to the general equation: Fe2O3 + 3CO Æ 2Fe + 3CO2 (Eq 1) The ironmaking reaction takes place in a blast furnace, shown schemati- cally in Fig. -
Simulation of Intrinsic Inclusion Motion and Dissolution During the Vacuum Arc Remelting of Nickel Based Superalloys W
SIMULATION OF INTRINSIC INCLUSION MOTION AND DISSOLUTION DURING THE VACUUM ARC REMELTING OF NICKEL BASED SUPERALLOYS W. Zhang, P.D. Lee and M. McLean Department of Materials, Imperial College London SW7 2BP, UK R.J. Siddall Special Metals Limited, Wiggin Works, Holmer Road Hereford HR4 9SL, UK dissolution of intrinsic particles for typical melt conditions of Abstract INCONEL 7 18’. Vacuum Arc Remelting (VAR) is one of the state-of-the-art Introduction secondaryre-melting processesthat are now routinely used to improve the homogeneity, purity and defect concentration in The VAR process has been investigated previously by both modern turbine disc alloys. The last is of particular importance experimental and mathematicaltechniques. Early mathematical since, as the yield strength of turbine disc alloys has approachessolved for heat transfer and approximated the fluid progressively increasedto accommodateincreasingly stringent flow by using an enhancedthermal conductivity in the molten design requirements, the fracture of these materials has region [l]. The next stage of modeling complexity become sensitive to the presence of ever smaller defects, incorporated the fluid flow using a quasi-steady state particularly inclusions. During the manufacture of these alloys assumption [2,3]. More recently Jardy et al. [4] presented a extrinsic defects can be introduced in the primary alloy model that simulated the transient growth of the ingot and production stage from a variety of sources; these include macrosegregation.In the last few years some authors have ceramic particles originating from crucibles, undissolved used macromodelsto investigate how the formation of defects tungsten (or tungsten carbide) and steel shot. In addition such as freckles correlated to operational parameters[.5,6]. -
Solidification of Alloy 718 During Vacuum Arc Remelting with Helium
SOLIDIFICATION OF ALLOY 718 DURING VACUUMARC REMELTING WITH HELIUM GAS COOLING BETWEEN INGOT AND CRUCIBLE L. G. Hosamani, W. E. Wood* and J. H. Devletian* Precision Castparts Corp., Portland, Oregon * Department of Materials Science and Engineering Oregon Graduate Center Beaverton, Oregon Abstract There is an increased demand for larger and better-quality vacuum arc melted superalloy ingots. However, as the ingot size increases, the ten- dency for segregation increases. The segregation can be minimized either by decreasing the melt rate or by improving the heat transfer from the ingot. The former technique results in decreased productivity and in- creased energy consumption during melting. The heat transfer from the ingot to the cooling water in VAR is mainly controlled by the heat transfer coefficient between the ingot and crucible. This heat transfer coefficient can be increased by introducing a gas of high thermal conductivity, like helium, in the shrinkage gap between the ingot and crucible. Even though this technique is being used by superalloys manufacturers, no systematic study has been carried out to quantify the effect of helium gas pressure. Hence, the present experimental work was undertaken to study the effect of helium gas cooling on the heat extraction rate, molten metal pool depth, mushy zone size and segregation during vacuum arc remelting of alloy 718. The experiments were carried out in a laboratory vacuum arc furnace capable of making 210 mm diameter ingots weighing up to 150 kgs. In this paper, the effect of helium gas pressure on the solidification behavior of alloy 718, like molten metal pool depth, surface quality of the ingot, dendrite arm spacing, mushy zone size and Laves phase, have been discussed. -
Removal of Calcium Containing Inclusions During Vacuum Arc Remelting
REMOVAL OF CALCIUM CONTAINING INCLUSIONS DURING VACUUM ARC REMELTING by EVA SAMUELSSON M.Sc, Royal Institute Of Technology, Stockholm, 1981 A THESIS SUBMITTED IN PARTIAL FULFILMENT OF THE REQUIREMENTS FOR THE DEGREE OF MASTER OF APPLIED SCIENCE in THE FACULTY OF GRADUATE STUDIES Department Of Metallurgical Engineering We accept this thesis as conforming to the required standard THE UNIVERSITY OF BRITISH COLUMBIA November 1983 © Eva Samuelsson, 1983 In presenting this thesis in partial fulfilment of the requirements for an advanced degree at the University of British Columbia, I agree that the Library shall make it freely available for reference and study. I further agree that permission for extensive copying of this thesis for scholarly purposes may be granted by the Head of my Department or by his or her representatives. It is understood that copying or publication of this thesis for financial gain shall not be allowed without my written permission. Department of Metallurgical Engineering The University of British Columbia 2075 Wesbrook Place Vancouver, Canada V6T 1W5 Date: 15 November 1983 i i Abstract The mechanism of removal of calcium containing inclusions in steel during Vacuum Arc Remelting has been investigated. Laboratory Electron Beam and industrial Vacuum Arc remelting electrodes and ingots were examined. Properties of the steels were determined with the aid of chemical and metallographic methods. It is proposed that the major mechanism of removal is rejection of calcium aluminates to a free surface. One third of the calcium sulphide is rejected with the calcium aluminates. The remainder reacts with aluminium oxide in the aluminates according to the following reaction: CaS + 1/3A1203= CaO + 2/3[Al] + [S] Subsequently, the calcium oxide is also rejected and the dissolved sulphur reacts with sulphide forming elements during solidification. -
Technical Aspects of Critical Materials Use by the Steel Industry
NBSIR 83-2679-1 01) Technical Aspects of Critical Materials Use by the Steel Industry Volume I: Summary Report Center for Materials Science National Bureau of Standards U.S. Department of Commerce ~QC 190 . 1)56 83-2679- 1933 1 WATIOI'AL bureau OF STANDARDS LIBRARY _ QC I NBSIR 83-2679-1 Technical Aspects of Critical Materials Use by the Steel Industry Volume I: Summary Report Robert Mehrabian John D. McKinley Bruce W. Steiner Kirit J. Bhansali April 1983 U.S. Department of Commerce, Malcolm Baldrige, Secretary National Bureau of Standards, Ernest Ambler, Director ' Preface This report was prepared by the Center for Materials Science (CMS) for the Department of Commerce as a technical chapter in the Department's study of "Critical Materials Requirements of the U.S. Steel Industry." That study resulted from a Commerce Department responsibility under the "National Materials and Minerals Policy, Research and Development Act of 1980," (PL 96-479) to "continually identify and assess — (materials needs) cases as necessary to ensure an adequate and stable supply of materials to meet national security, economic well being, and industrial production needs." This report reviews technical opportunities for research in process improvement and in alternative materials development that would reduce U.S. dependency on critical materials. The advanced technologies reviewed here, in addition to their impli- cations for critical materials conservation, represent trends leading to better quality and lower cost steel products. Thus, they may also con- tribute positively to the industry's more immediate concern for improved markets. The report draws extensively on material presented at a public workshop sponsored jointly by the National Bureau of Standards, Bureau of Mines, and the Army Research Office. -
Vacuum Arc Remelting (VAR)
ALD Vacuum Technologies High Tech is our Business Vacuum Arc Remelting (VAR) Vacuum Arc Remelting Processes and Furnaces ALD / VAR / 2019.05 EN ALD / VAR Vacuum Arc Remelting (VAR) ALD is one of the leading suppliers of vacuum melting furnace technologies for engineered metals 12 ton VAR furnace from ALD VAR is widely used to improve the Fields of Application VAR Applications cleanliness and refine the structure of standard air-melted or vacuum in- O Aerospace O Superalloys for aerospace duction melted ingots (called O Power generation O High strength steels consumable electrodes). VAR steels O Chemical industry O Ball-bearing steels and superalloys as well as titanium O Medical and nuclear industries O Tool steels (cold and hot work steels) for milling cutters, drill bits, etc. and zirconium and its alloys are used O Die steels in a great number of high-integrity O Melting of reactive metals (titanium, applications where cleanliness, zirconium and their alloys) for aero- homogeneity, improved fatigue space, chemical industry, off-shore and fracture toughness of the final technique and reactor technique product are essential. 02 VAR Advantages & ALD Features ALD has numerous references in the field offering the highest levels of system automatization 10 ton VAR furnace from ALD Primary benefits of VAR Further advantages Features of VAR furnaces from ALD O Removal of dissolved gases, such O Removal of Oxides by chemical and as hydrogen, nitrogen and CO physical processes O Ingot diameters up to 1,500 mm O Reduction of undesired trace O -
High Performance Vacuum Metallurgical Furnaces
ETECH SY S TEM S LLC Advanced Thermal Processing Technologies High Performance Vacuum Metallurgical Furnaces Solving Industry’s toughest problems through the science of advanced thermal processing technology. RETECH SY S TEM S LLC Advanced Thermal Processing Technologies The Retech Advantage In an industry demanding design precision for an ever-changing market, Retech understands the need for vacuum metallurgical equipment and processes that are both proven and state-of-the-art. Since 1963, Retech has supplied equipment to Europe, Asia and North America, with over half of our products built to service the international market. A solid identification with the needs of our customers, as well as understanding the importance of producing cost-effective technologies, is the foundation upon which Retech is built. As one of the industry’s leading innovators, Retech has contributed important advancements in precision pouring, plasma arc melting, consumable casting and metal powder production. Retech is the most fully integrated manufacturer of metallurgical processing equipment in the world, giving customers access to a wide range of in- house resources to achieve the individual requirements of each project. Experience and innovation, coupled with a complete engineering and manufacturing operation are key to our success. Our team of engineering, manufacturing and research specialists work with each customer to tailor relevant, reliable, cost-effective solutions for the production of high performance metals. Besides being the world’s leading supplier -
Vacuum Arc Remelting (VAR) Improving the Structure and Uniformity of the Cast Ingot
ALD Vacuum Technologies High Tech is our Business CRUCIBLE SHAPE Technical Data Disc Round Round/Square Round/Square Laboratory Remelting Systems LK 6 L 200 F 240 R 240 Non-consumable Electrode Technique • + – – Round, rectangular and ring-shaped. Equipment variable from 3 dishes Melt Disc Geometry (Ø 2.5 mm) up to 1 dish (Ø 150 mm). – – The height depends on the material and the melting power. Skull Melting + + • • Pouring Weight (Titanium) max. [kg] 0.2 2 – – Melting Power Supply [A] 500-2000 5000-7500 5000-7500 5000-7500 Consumable Electrode Technique • Laboratory Remelting Systems Mold Sizes Ø min. [mm] – 70 170 150 Ø max. [mm] – 200 240 240 for Pilot Production and R&D Length max. [mm] – 800 1300 1100 Ingot Weight max. [kg] – 200 350 370 Vacuum/Pressure Standard [mbar] 10-2 10-2 1 bar 70 bar With Diffusion Pump [mbar] 10-4 10-4 – 10-4 Cooling Water Consumption [l/min] 60-100 250 400 400 • Standard equipment + Extra equipment – Not available MetaCom / Labaratory Remelting Systems / 12.14 Systems Remelting / Labaratory MetaCom Vacuum Arc Remelting (VAR) Improving the structure and uniformity of the cast ingot 1. Copper mold 2. Melt bath 3. Non-consumable electrode 4. Consumable electrode 5. Casting mold 6. Water-cooled crucible 4 4 3 2 6 1 2 5 1 2 Non-consumable Electrode Technique Consumable Electrode Technique Skull Melting The Laboratory Systems Accessories: Vacuum Arc Remelting (VAR) ALD has continously developed Accessories that increase flexibility and The Vacuum Arc Remelting process is various laboratory systems that range of applications: using an arc between a massive source operate with non-consumable and O Automatic gas-inlet system electrode (cathode) of the material consumable electrode techniques. -
Alloy Steels
Books Alloy Steels Edited by Robert Tuttle Printed Edition of the Special Issue Published in Metals www.mdpi.com/journal/metals MDPI Alloy Steels Special Issue Editor Robert Tuttle Books MDPI • Basel • Beijing • Wuhan • Barcelona • Belgrade MDPI Special Issue Editor Robert Tuttle Saginaw Valley State University USA Editorial Office MDPI AG St. Alban-Anlage 66 Basel, Switzerland This edition is a reprint of the Special Issue published online in the open access journal Metals (ISSN 2072-6651) from 2016–2017 (available at: http://www.mdpi.com/journal/metals/special issues/ alloy steels). Books For citation purposes, cite each article independently as indicated on the article page online and as indicated below: Lastname, F.M.; Lastname, F.M. Article title. Journal Name Year, Article number, page range. First Editon 2018 Cover photo courtesy of Robert Tuttle. ISBN 978-3-03842-883-1 (Pbk) ISBN 978-3-03842-884-8 (PDF) Articles in this volume are Open Access and distributed under the Creative Commons Attribution (CC BY) license, which allows users to download, copy and build upon published articles even for commercial purposes, as long as the author and publisher are properly credited, which ensures maximum dissemination and a wider impact of our publications. The book taken as a whole is c 2018 MDPI, Basel, Switzerland, distributed under the terms and conditions of the Creative Commons license CC BY-NC-ND (http://creativecommons.org/licenses/by-nc-nd/4.0/). MDPI Table of Contents About the Special Issue Editor ...................................... vii Preface to "Alloy Steels" .......................................... ix Robert Tuttle Alloy Steels doi: 10.3390/met8020116 .......................................