ABSTRACT LI, XINGYU. Key Material Factors of Digital Printing On
Total Page:16
File Type:pdf, Size:1020Kb
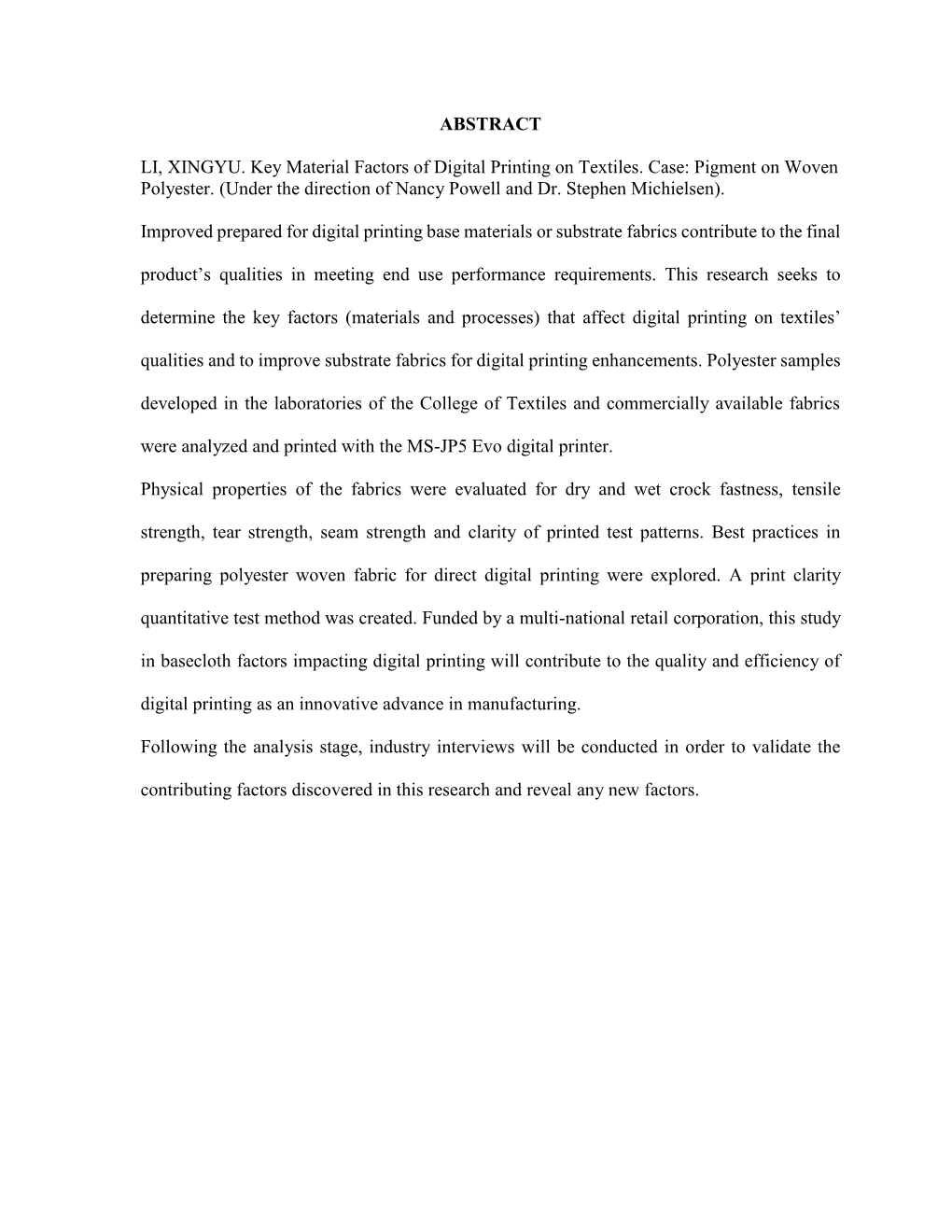
Load more
Recommended publications
-
Natural Materials for the Textile Industry Alain Stout
English by Alain Stout For the Textile Industry Natural Materials for the Textile Industry Alain Stout Compiled and created by: Alain Stout in 2015 Official E-Book: 10-3-3016 Website: www.TakodaBrand.com Social Media: @TakodaBrand Location: Rotterdam, Holland Sources: www.wikipedia.com www.sensiseeds.nl Translated by: Microsoft Translator via http://www.bing.com/translator Natural Materials for the Textile Industry Alain Stout Table of Contents For Word .............................................................................................................................. 5 Textile in General ................................................................................................................. 7 Manufacture ....................................................................................................................... 8 History ................................................................................................................................ 9 Raw materials .................................................................................................................... 9 Techniques ......................................................................................................................... 9 Applications ...................................................................................................................... 10 Textile trade in Netherlands and Belgium .................................................................... 11 Textile industry ................................................................................................................... -
Choosing the Proper Short Cut Fiber for Your Nonwoven Web
Choosing The Proper Short Cut Fiber for Your Nonwoven Web ABSTRACT You have decided that your web needs a synthetic fiber. There are three important factors that have to be considered: generic type, diameter, and length. In order to make the right choice, it is important to know the chemical and physical characteristics of the numerous man-made fibers, and to understand what is meant by terms such as denier and denier per filament (dpf). PROPERTIES Denier Denier is a property that varies depending on the fiber type. It is defined as the weight in grams of 9,000 meters of fiber. The current standard of denier is 0.05 grams per 450 meters. Yarn is usually made up of numerous filaments. The denier of the yarn divided by its number of filaments is the denier per filament (dpf). Thus, denier per filament is a method of expressing the diameter of a fiber. Obviously, the smaller the denier per filament, the more filaments there are in the yarn. If a fairly closed, tight web is desired, then lower dpf fibers (1.5 or 3.0) are preferred. On the other hand, if high porosity is desired in the web, a larger dpf fiber - perhaps 6.0 or 12.0 - should be chosen. Here are the formulas for converting denier into microns, mils, or decitex: Diameter in microns = 11.89 x (denier / density in grams per milliliter)½ Diameter in mils = diameter in microns x .03937 Decitex = denier x 1.1 The following chart may be helpful. Our stock fibers are listed along with their density and the diameter in denier, micron, mils, and decitex for each: Diameter Generic Type -
Inkjet Printing-A Revolutionary Ecofriendly Technique for Textile Printing
Indian Journal of Fibre & Textile Research Vol. 26. March-June 2001. pp. 156-161 Inkjet printing-A revolutionary ecofriendly technique for textile printing Sanjay Gupta" National In stitute of Fash ion Technology. Hauz Khas, Ne w Dcl hi 110016, India Some of thc aspects of inkjct or di gital printing, such as com pari son bctwecn conventional and di gita l printing. di git al printing systcms, suitablc inks bascd on dyes and pi gments, colour man agc ment software, application and iuture scope of digit al printing, arc brieny discussed in view of the demand-activated manufac turing architect to satisfy th e chan gin g fa shi on trends and new market requ irements. Keywords: Inkjet printing, Rotary scrcen printing, Textile printing 1 Introduction has been pushing the print production towards th e In ITMA 1999, an array of diffe rent technologies developing countries. As a result, Far East has the fo r di gital printing on fabric was presented. Though major share of 50% with the USA hav ing only II % the idea had been around for nearly IS years, it was and the EU, 15 %. A major reason for thi s shift is th e not until now th at equipment adequate enough for long, polluting and capital intensive nature of production on tex til es was show n. However, th e conventional tex tile printin g. Di gital printing has the 'different competing technologies th at were di splayed potential to reverse this trend. showed a lack of clear-cut direction and served onl y Changing fas hion trend s an d new market to confuse buyers, most of wh om were un exposed and requirements are also pushing th e dri ve for digital un ed ucated about the capabilities of these printing. -
Yarn Numbering Systems
TECHNICAL BULLETIN 6399 Weston Parkway, Cary, North Carolina, 27513 • Telephone (919) 678-2220 TRI 1014 YARN NUMBERING SYSTEMS © 2003 Cotton Incorporated. All rights reserved; America’s Cotton Producers and Importers. TABLE OF CONTENTS Page INTRODUCTION 1 DIRECT SYSTEMS 1 INDIRECT SYSTEMS 2 CONVERSION 4 PLIED YARNS 4 YARN DIAMETER 5 YARN NUMBERING SYSTEMS - TABLE 1 6 CONVERSION FACTORS - TABLE 2 7 YARN NUMBERING SYSTEMS INTRODUCTION Textiles are often sold on a weight basis and consequently it is natural to express the size of "thickness" of a yarn in terms of weight (or mass). There are two basic ways in which this may be done. These are: (a) by saying how much a given length of yarn weighs, or (b) by saying what length of yarn one would have in a given weight. Generally these are known as the direct and indirect systems of yarn numbering, respectively. In other words: Weight(or mass) Direct yarn number = Length Length Indirect yarn number = Weight(or mass) It will be noted that one is the inverse of the other. In the first case, the number gets larger as the yarn or strand gets coarser. In the second case, the number gets smaller as the yarn or strand gets coarser. Each system has its advantages and disadvantages and each has found areas in which, by custom, it is used. It so happens that because long, thin strands are usually involved, the length figures are usually large and the weight figures are small. Consequently, the yarn numbers would get impossibly large or impossibly small unless special units are used. -
Textile Industry Needs Christopher D
The Journal of Cotton Science 21:210–219 (2017) 210 http://journal.cotton.org, © The Cotton Foundation 2017 ENGINEERING & GINNING Textile Industry Needs Christopher D. Delhom, Vikki B. Martin, and Martin K. Schreiner ABSTRACT lthough the immediate customer of the gin is Athe cotton producer, the end user of the ginned The immediate customers of cotton gins are lint is the textile mill, retailers, and eventually the the producers; however, the ultimate customers consumer. Thus, it is essential for the ginner to are textile mills and consumers. The ginner has satisfy both the producers and the textile industry. the challenging task to satisfy both producers and Consequently, the ginner needs to be aware of the the textile industry. Classing and grading systems needs of the textile industry. are intended to assign an economic value to the The intent of the cotton classing and grading bales that relates to textile mill demands and the system is to assign an economic value to the bale that quality of the end product. International textile documents its properties as it relates to the quality of mills currently are the primary consumers of U.S. the end product. Since the last edition of the Cotton cotton lint where it must compete against foreign Ginners Handbook in 1994, the customers of U.S. origins. International textile mills manufacture cotton have changed radically, shifting from primar- primarily ring-spun yarns, whereas domestic mills ily domestic to international mills. International mills manufacture predominantly rotor spun yarns. Pro- have been accustomed primarily to hand-harvested ducers and ginners must produce cottons to satisfy cotton that has been processed at slow ginning all segments of the industry, i.e., domestic and in- rates. -
Woven Silks Glenna Teague North Carolina State University
International Textile and Apparel Association 2014: Strengthening the Fabric of our Profession, (ITAA) Annual Conference Proceedings Association, Legacy and Friendships! Jan 1st, 12:00 AM Woven Silks Glenna Teague North Carolina State University Follow this and additional works at: https://lib.dr.iastate.edu/itaa_proceedings Part of the Fashion Design Commons Teague, Glenna, "Woven Silks" (2014). International Textile and Apparel Association (ITAA) Annual Conference Proceedings. 115. https://lib.dr.iastate.edu/itaa_proceedings/2014/design/115 This Event is brought to you for free and open access by the Conferences and Symposia at Iowa State University Digital Repository. It has been accepted for inclusion in International Textile and Apparel Association (ITAA) Annual Conference Proceedings by an authorized administrator of Iowa State University Digital Repository. For more information, please contact [email protected]. Charlotte, North Carolina 2014 Proceedings Woven Silks Glenna Teague, North Carolina State University, USA Woven, Silk, Design, Innovative The purpose of this design was to create a modern looking garment by using a fusion of both new and old age textile and apparel design skills. Hand weaving is a lost art form that needs to be revived by students and young textile professionals, thus being part of the inspiration for this garment. Inspiration was also drawn from a colorful piece of artwork at the North Carolina Museum of Art. Frank Philip Stella’s Raqqa II is a fusion of bright, vibrant colors that seamlessly intertwine, following the curves and edges of the canvas. I believe that the shapes formed by the bands of color, mirror the shape of the model’s body because of the form fitting dress. -
History of Weaving
A Woven World Teaching Youth Diversity through Weaving Joanne Roueche, CFCS USU Extension, Davis County History of Weaving •Archaeologists believe that basket weaving and weaving were the earliest crafts •Weaving in Mesopotamia in Turkey dates back as far as 7000 to 8000 BC •Sealed tombs in Egypt have evidence of fabrics dating back as far as 5000 BC •Evidence of a weavers workshop found in an Egyptian tomb 19th Century BC •Ancient fabrics from the Hebrew world date back as early as 3000 BC History of Weaving (continued) •China – the discovery of silk in the 27th Century BCE •Swiss Lake Dwellers – woven linen scraps 5000 BCE •Early Peruvian textiles and weaving tools dating back to 5800 BCE •The Zapotecs were weaving in Oaxaca as early as 500 BC Weavers From Around the World Master weaver Jose Cotacachi in his studio in Peguche, Ecuador. Jose’s studio is about two and a half miles from Otavalo. Weavers making and selling their fabrics at the Saturday market in Otavalo, Ecuador. This tiny cottage on the small island of Mederia, Portugal is filled with spinning and weaving. Weavers selling their fabrics at an open market in Egypt. The painting depicts making linen cloth, spinning and warping a loom. (Painting in the Royal Ontario Museum.) Malaysian weavers making traditional Songket – fabric woven with gold or silver weft threads. A local Tarahumara Indian weaving on a small backstrap loom at the train station in Los Mochis. Weavers In Our Neighborhood George Aposhian learned Armenian pile carpets from his father and grandparents who immigrated to Salt Lake City in the early 1900’s. -
Instant Conductors
University of Central Florida STARS Electronic Theses and Dissertations, 2004-2019 2015 Instant Conductors Mary Petralia University of Central Florida Part of the Creative Writing Commons Find similar works at: https://stars.library.ucf.edu/etd University of Central Florida Libraries http://library.ucf.edu This Masters Thesis (Open Access) is brought to you for free and open access by STARS. It has been accepted for inclusion in Electronic Theses and Dissertations, 2004-2019 by an authorized administrator of STARS. For more information, please contact [email protected]. STARS Citation Petralia, Mary, "Instant Conductors" (2015). Electronic Theses and Dissertations, 2004-2019. 1466. https://stars.library.ucf.edu/etd/1466 INSTANT CONDUCTORS by MARY PETRALIA A.A. Eastern Florida State College, 2008 B.A. University of Central Florida, 2012 A thesis submitted in partial fulfillment of the requirements for the degree of Master of Fine Arts in Creative Writing in the Department of English in the College of Arts and Humanities at the University of Central Florida Orlando, Florida Fall Term 2015 Major Professor: Russ Kesler © 2015 Mary Petralia ii ABSTRACT Instant Conductors is a collection of poems meant to engage the reader in conversation about the imperfect nature of the world in relation to the imperfect nature of readerly experience. Walt Whitman wrote, “I have instant conductors all over me whether I pass or stop / they seize every object and lead it harmlessly through me.” And so the things on these pages are intent on transmitting what one experiences in the minutiae of memory and routine: the sounds that surround a blackwater tidepool, what one imagines happens behind the closed doors of the friendly neighbors, or what’s heard in the whispers of an elderly man sitting in a waiting room. -
Textile Printing
TECHNICAL BULLETIN 6399 Weston Parkway, Cary, North Carolina, 27513 • Telephone (919) 678-2220 ISP 1004 TEXTILE PRINTING This report is sponsored by the Importer Support Program and written to address the technical needs of product sourcers. © 2003 Cotton Incorporated. All rights reserved; America’s Cotton Producers and Importers. INTRODUCTION The desire of adding color and design to textile materials is almost as old as mankind. Early civilizations used color and design to distinguish themselves and to set themselves apart from others. Textile printing is the most important and versatile of the techniques used to add design, color, and specialty to textile fabrics. It can be thought of as the coloring technique that combines art, engineering, and dyeing technology to produce textile product images that had previously only existed in the imagination of the textile designer. Textile printing can realistically be considered localized dyeing. In ancient times, man sought these designs and images mainly for clothing or apparel, but in today’s marketplace, textile printing is important for upholstery, domestics (sheets, towels, draperies), floor coverings, and numerous other uses. The exact origin of textile printing is difficult to determine. However, a number of early civilizations developed various techniques for imparting color and design to textile garments. Batik is a modern art form for developing unique dyed patterns on textile fabrics very similar to textile printing. Batik is characterized by unique patterns and color combinations as well as the appearance of fracture lines due to the cracking of the wax during the dyeing process. Batik is derived from the Japanese term, “Ambatik,” which means “dabbing,” “writing,” or “drawing.” In Egypt, records from 23-79 AD describe a hot wax technique similar to batik. -
Autumn Winter 19 Guide
DRESD ARTISANS OF BLACK TIE Autumn/Winter 2019 Cloth selection: Dormeuil & Alumo Made in Europe *** TIER I $3,000 - $5,000 ~ Example black tie ensemble ~ Ceremonial 2-piece suit in black wool barathea, self covered buttons, peak lapels faced in black silk satin. - Ceremonial dress shirt in white cotton, signature 9cm collar, french cuffs, self bib front, concealed placket, matching monogrammed pocket square. - Ceremonial 6.5cm hand finished classic butterfly bow tie in black silk satin. - Ceremonial whole cut oxford dress shoes in patent black leather. *** Suite 220, 33 Pirie Street Adelaide SA 5000, Australia Phone: +61 423 399 978 WWW.DRESD.COM.AU !1 of !3 DRESD ARTISANS OF BLACK TIE Autumn/Winter 2019 Cloth selection: Dormeuil & Alumo Made in Europe *** TIER II $5,000 - $7,000 ~ Example black tie ensemble ~ Ceremonial jacket in black cotton & silk velvet, self covered buttons, self faced peak lapels. - Ceremonial trouser in black wool & silk twill. Ceremonial dress shirt in white cotton, signature 9cm collar, french cuffs, self bib front, concealed placket, matching monogrammed pocket square. - Ceremonial 6.5cm hand finished classic butterfly bow tie in black silk satin. - Ceremonial whole cut oxford dress shoes in patent black leather. ~ Evening dress change ~ Evening dress shirt in black cotton, signature 9cm collar, french cuffs, self bib front, concealed placket, matching monogrammed pocket square. - Evening 6cm hand finished pointed butterfly bow tie in black silk faille. *** Suite 220, 33 Pirie Street Adelaide SA 5000, Australia Phone: +61 423 399 978 WWW.DRESD.COM.AU !2 of !3 DRESD ARTISANS OF BLACK TIE Autumn/Winter 2019 Cloth selection: Dormeuil & Alumo Made in Europe *** TIER III $7,000 - $9,000 ~ Example black tie ensemble ~ Ceremonial jacket in black wool & silk jacquard, self covered buttons, self faced peak lapels. -
H'mong Ancient Methods of Indigo Dyeing and Beeswax Batik in Cat
International Journal of Science and Research (IJSR) ISSN: 2319-7064 ResearchGate Impact Factor (2018): 0.28 | SJIF (2019): 7.583 H’mong Ancient Methods of Indigo Dyeing and Beeswax Batik in Cat CAT Village, Hoang Lien Commune, SAPA Town, Lao Cai Province, Vietnam Le Thi Hanh Lien1*, Nguyen Thi Hai Yen2, Dao Thi Luu3, Phi Thi Thu Hoang4, Nguyen Thuy Linh5 1, 2, 3, 4 Institute of Geography, Vietnam Academy of Science and Technology, 18 Hoang Quoc Viet Road, Nghia Do, CauGiay District, Ha Noi, Vietnam 5Management Development Institute of Singapore *Corresponding author: lehanhlien2017[at]gmail.com Abstract: Indigo dyeing and beeswax batik are the two traditional crafts that have long been associated with the H’Mong people in Sa Pa in general, Cat Cat village in particular and still preserved until the presentday. Through many stages of making indigo dye combined with sophisticated techniques and the ingenuity, meticulousness of the artisans in each motif and pattern, unique beeswax batik and indigo dyeing products have been created bringing the cultural identity of the H’mong people. These handicraft products have become a highlight to attract tourists to learn and discover local cultural values and they are meaningful souvenirs for visitors after each trip. In recent years, the development of the community-based tourism model in Cat Cat village has brought many benefits to the local community. Meanwhile, it has also contributed to creating opportunities for the development and restoration of H’mong traditional crafts. Keywords: indigo dyeing, beeswax batik, H’Mong, Cat Cat, Sa Pa 1. Introduction cultural and religious life of the H'Mong. -
Reflecting Noble Luxury and Refinement, New Lightweight Wool Materials Are of Key Interest to Designers, Retailers and Bespoke Tailors
Reflecting noble luxury and refinement, new lightweight wool materials are of key interest to designers, retailers and bespoke tailors. Beyond demanding perfected fits and wool’s signature aesthetic, discerning consumers expect emotional, sensorial tactility in garments. Responding to luxury market demands, leading Italian and English spinners and weavers are introducing exclusive fine-micron yarns and fabrics, derived from rare Australian merino. Stylesight explores Baruffa Group’s finest wool yarns for first-class sweater knits, cut-and-sew jersey, and wovens. Vogue Australia December 2012 / Elizabeth Debicki in wool, on location at Haddon Rig, a Merino wool farm in New South Wales. With seductive, magnetic charm, lighter weight but often still densely constructed wovens and knits are key on men and women's runways and at textile trade shows. Wool—traditionally a winter fiber—evolves with cutting-edge superfine qualities from 150s and 180s up to 250s. Offering noble refinement and unique trans-seasonal possibilities, wool moves beyond its pastime connotations. Gossamer knits / Posh mesh / Lightweight jerseys / Dense, hefty yet lightweight wools Finest wool Fabrics F/W 13 Dormeuil Limited Edition - finest wool yarns Zegna Baruffa Lane Record Bale - finest wool fabric Loro Piana Borgosesia Finest wool Fabrics Taylor & Lodge Meticulous fiber selection from choice breeds, along with revolutionary spinning and weaving technologies, is core to new noble wool productions. Wools characterized by strength, elasticity, fluidity, low pilling and