Kta 3702 (2014-11)
Total Page:16
File Type:pdf, Size:1020Kb
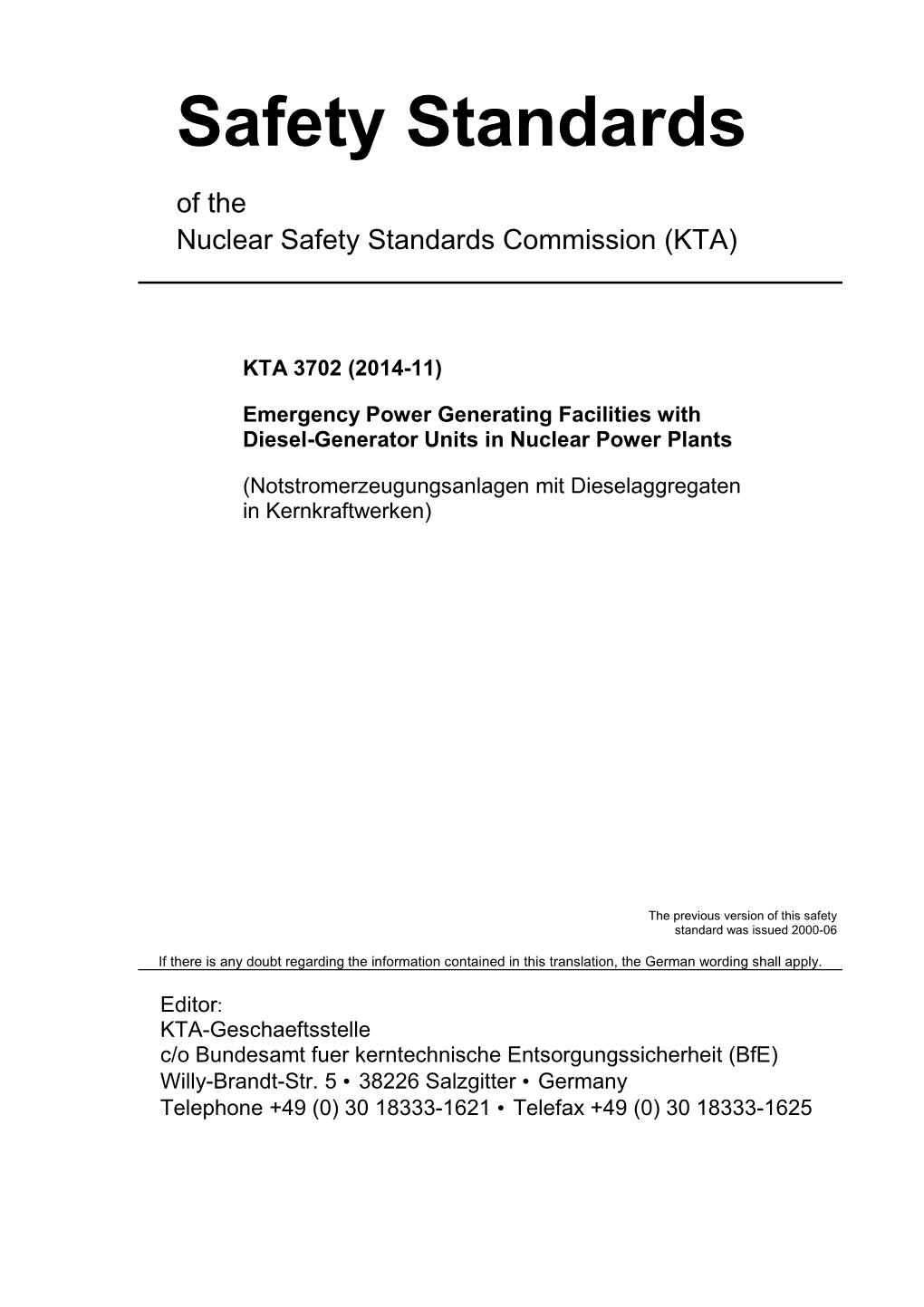
Load more
Recommended publications
-
Reliability Analysis for the Emergency Power System of a Pressurized
CORE Metadata, citation and similar papers at core.ac.uk Provided by Digital Repository @ Iowa State University Iowa State University Capstones, Theses and Retrospective Theses and Dissertations Dissertations 1984 Reliability analysis for the emergency power system of a pressurized water reactor facility during a loss of offsite power transient See-Meng Wong Iowa State University Follow this and additional works at: https://lib.dr.iastate.edu/rtd Part of the Nuclear Engineering Commons Recommended Citation Wong, See-Meng, "Reliability analysis for the emergency power system of a pressurized water reactor facility during a loss of offsite power transient " (1984). Retrospective Theses and Dissertations. 7741. https://lib.dr.iastate.edu/rtd/7741 This Dissertation is brought to you for free and open access by the Iowa State University Capstones, Theses and Dissertations at Iowa State University Digital Repository. It has been accepted for inclusion in Retrospective Theses and Dissertations by an authorized administrator of Iowa State University Digital Repository. For more information, please contact [email protected]. INFORMATION TO USERS This reproduction was made from a copy of a document sent to us for microfilming. While the most advanced technology has been used to photograph and reproduce this document, the quality of the reproduction is heavily dependent upon the quality of the material submitted. The following explanation of techniques is provided to help clarify markings or notations which may appear on this reproduction. 1.The sign or "target" for pages apparently lacking from the document photographed is "Missing Page(s)". If it was possible to obtain the missing page(s) or section, they are spliced into the film along with adjacent pages. -
City of Plattsburgh (SUNY)
56 - City of Plattsburgh (SUNY) August 2016 Notice The opinions expressed in this report do not necessarily reflect those of the New York State Energy Research and Development Authority (hereafter “NYSERDA”) or the State of New York, and reference to any specific product, service, process, or method does not constitute an implied or expressed recommendation or endorsement of it. Further, NYSERDA, the State of New York, and the contractor make no warranties or representations, expressed or implied, as to the fitness for particular purpose or merchantability of any product, apparatus, or service, or the usefulness, completeness, or accuracy of any processes, methods, or other information contained, described, disclosed, or referred to in this report. NYSERDA, the State of New York, and the contractor make no representation that the use of any product, apparatus, process, method, or other information will not infringe privately owned rights and will assume no liability for any loss, injury, or damage resulting from, or occurring in connection with, the use of information contained, described, disclosed, or referred to in this report. NYSERDA makes every effort to provide accurate information about copyright owners and related matters in the reports we publish. Contractors are responsible for determining and satisfying copyright or other use restrictions regarding the content of reports that they write, in compliance with NYSERDA’s policies and federal law. If you are the copyright owner and believe a NYSERDA report has not properly attributed your work to you or has used it without permission, please email [email protected] ii PON 3044 Final Report – Plattsburgh Table of Contents Executive Summary ...................................................................................................................................... -
D3.1. State of the Art FUSE-IT
D3.1. State of the Art FUSE-IT Editors: Son Han, Shohreh Ahvar, Noël Crespi, Reza Farahbakhsh, Bahram Alinia (IMT-TSP) Contributors: CCS, CEA-LIST, Evoleo, ICAM, iMINDS, IMT-TSP, ISEP/GCAD, SOGETI, Thales Services, ULR Reviewer: Hélia POUYLLAU (Thales RT) Draft history V.0.1.0 15 Dec 2014 Initial Version (Reviewed by Thales RT) V.1.0.0 30 Jan 2015 Release 1 - Revisions needed: - 3.1.4. Physical Detection and Anti-intrusion Sensors [Thales Services - Introduction] - 3.3.3. Network Operation Centers (NOC) [CCS - Solutions & Products] - 3.4.3. Security Operation Centers (SOC) [CCS – Figure 3.4.4, Situation awareness, limitation of SIEM and/or ad-hoc orchestrator] - 4.1.3. Internet of Things Alliances [SOGETI, technical details] V.1.0.1 30 May 2015 - Revisions needed as in V.1.0.0 - Added Smart Grid and Smart Grid Standards (ISEP/GECAD) - Updated 4.1.3 Internet of Things Alliances (SOGETI) V. Final 22 June 2015 - Updated 3.1.1 Smart Energy sensors, 3.2.2 Building Automation & SCADA (ICAM) - Updated 4.1.3 Internet of Things Alliances (SOGETI) V.Update 8 August 2015 - Added 4.4 Security Standards (IMT) - Updated 4.2.1 Building Automation Standards (IMT) - Added 3.4.1 Smart meters and cyber security (Thales Services) - Added 3.1.3 Heterogeneous traffic data , 3.1.4 Opportunistic spectrum access sensors and 3.4.3 Attacks and threats in IoT (ULR) <FUSE-IT> D3.1. State of the Art Table of Contents 1 Introduction ....................................................................................................................................... 6 1.1 Overview .................................................................................................................................. 6 1.2 FUSE-IT Components ............................................................................................................. 7 2 Related Projects .............................................................................................................................. -
Design of Electrical Power Systems for Nuclear Power Plants
GUIDE NO. AERB/NPP/SG/D-11 (Rev.1) GOVERNMENT OF INDIA AERB SAFETY GUIDE DESIGN OF ELECTRICAL POWER SYSTEMS FOR NUCLEAR POWER PLANTS ATOMIC ENERGY REGULATORY BOARD AERB SAFETY GUIDE NO. AERB/NPP/SG/D-11 (Rev.1) DESIGN OF ELECTRICAL POWER SYSTEMS FOR NUCLEAR POWER PLANTS Atomic Energy Regulatory Board Mumbai-400094 India July 2020 Price Orders for this guide should be addressed to: Chief Administrative Officer Atomic Energy Regulatory Board Niyamak Bhavan Anushaktinagar Mumbai-400094 India SPECIAL DEFINITIONS (Specific for the Guide) Alternate Power Sources 1 Alternate on-site (e.g. Standby AC power sources / Main generators of other units at multi-unit site) or off-site (e.g. hydro/gas based power station) power sources which can be used to supply power to emergency electric power supply buses. These power supply sources are not part of the electrical power supply system of the NPP. DEC Power Source Power Source reserved for supplying power to the plant when there is total loss of power in all the emergency electric power supply systems during station blackout and also during other design extension conditions (DECs). Electrical Grid The part of electrical power system used for evacuation of power generated in NPP and receiving off-site power. Electrical Protection System A part of electrical system that protects an equipment or system. This encompasses all those electrical, electronic, mechanical, thermal, pneumatic devices and circuitry right from and including sensors, which generate a signal for protection. Electrical Separation Means for preventing one electric circuit from influencing another through electrical phenomena. Emergency Electric Power System (EEPS) That portion of electrical power system provided for supplying electric power to safety-related and safety systems of an NPP during its operational states as well as during accident conditions. -
Automating Emergency Power Supply System Testing in Hospitals | 3 White Paper
Automating Emergency Power Supply System Testing in Hospitals by Markus F. Hirschbold, Ginni Stieva Executive summary The testing of emergency power supply systems (EPSS) in hospitals plays a critic al role to ensure backup power is available when needed. Due to the shortcomings of manual testing, more hospitals are switching to automated EPSS test systems. This paper demonstrates how automated EPSS tes ting increases reliability due to the accurate monitoring and recording of test parameters, provides tra ceability in case of unanticipated problems with the EPS system or litigation, and helps reduce the staffing burden for such tests. 998 -2 095 - 01 -3 0 - 1 2 AR 0 Contents Executive Summary ............................................................................................ 3 Introduction ........................................................................................................ 4 Why EPSS Testing is Critical ................................................................................ 6 Major Outages Resulting from EPSS Failures ....................................................... 7 Financial Risk of EPSS Failure during a Blackout ................................................. 8 Preventable Adverse (Sentinel) Events ................................................................. 9 Improper Testing Can Cause Reliability to Decrease ...........................................10 Advantages of Automated EPSS Testing ............................................................12 Conclusion ........................................................................................................14 -
Emergency Power Systems at Nuclear Power Plants Symposium May 3 – 4, 2017 Munich, Germany
Emergency Power Systems at Nuclear Power Plants Symposium May 3 – 4, 2017 Munich, Germany TÜV SÜD Industrie Service GmbH TÜV SÜD Akademie GmbH About the Symposium Program Committee After two successful conferences in 2013 and 2015 the third AREVA GmbH (DE), International Symposium Emergency Power Systems at Nuclear Manfred Schwemmlein Power Plants will be organized in May 3 – 4, 2017 in Munich, Caterpillar Motoren GmbH & Co. KG (DE), Germany. Gert Hoffmeister This event addresses the objectives of designers, manufactur- Mitsubishi Heavy Industries, Ltd. (JP) ers, utilities, regulators, vendors and academic organizations. MTU Friedrichshafen GmbH (DE), This international conference for users of emergency power Andreas Görtz systems with its presentations, discussions and its exchange Wärtsilä Finland Oy (FI), of experience emphasizes the importance of reliable power Bjarne Forsbacka, Juha Kerttula, Sari Kojo supplies in case of loss of other power sources in nuclear power plants. Westinghouse Electric Germany GmbH (DE), Tanja Schuler The objective of the Symposium is to support the continuous improvement process for emergency power systems Chairman increase familiarity with international regulation and standards Anton Kollmer, pinpoint and discuss new challenges TÜV SÜD Industrie Service GmbH (DE) The Symposium is intended for specialists at Nuclear power plants and operating companies Power plant design companies Nuclear supervisory and licensing authorities CONFERENCE FEE AND VENUE Engine manufacturers 780,00 € plus current VAT (if applicable) Expert organizations The conference fee covers the symposium materials, Technical an academic institutions beverages during the breaks, lunch and the evening event. The Symposium is also aimed at professionals from industry, TÜV SÜD · Auditorium Chiemsee government agencies and other institutions with similar Westendstraße 199, 80686 Munich, Germany responsibilities. -
Hydrogen Fuel Cell Emergency Power System
Hydrogen Fuel Cell Emergency Power System Installation and Performance of Plug Power GenCore 5B48 Unit Lech Birek Stanisław Molitorys HYDROGEN FUEL CELL EMERGENCY POWER SYSTEM Installation and Performance of Plug Power GenCore 5B48 Unit Lech Birek Stanisław Molitorys A 30 credit units Master´s thesis Supervisor: Ingolfur Orn Thorbjornsson A Master’s thesis done at RES │ the School for Renewable Energy Science in affiliation with University of Iceland & the University of Akureyri Akureyri, February 2009 Hydrogen Fuel Cell Emergency Power System Installation and Performance of Plug Power GenCore 5B48 Unit A 30 credit units Master’s thesis © Lech Birek, Stanisław Molitorys, 2009 RES │ the School for Renewable Energy Science Solborg at Nordurslod IS600 Akureyri, Iceland telephone: + 354 464 0100 www.res.is Printed in 14/05/2009 at Stell Printing in Akureyri, Iceland ABSTRACT Backup systems are crucial elements of modern electrical grids. They are used in places where an interruption in power supply can cause significant damage, e.g. in hospitals, banks or telecommunication towers. There are many solutions for how emergency power can be delivered. Hydrogen fuel cells are an emerging technology with great potential for the future. Fuel cells combine the advantages of batteries and diesel generators, and eliminate some of their significant disadvantages. They can work as long as they are supplied with fuel via a simple and efficient electrochemical reaction and at the same time they are quiet, produce no emissions and require minimum maintenance. The aim of this thesis is to present the idea of hydrogen fuel cells as reliable backup power systems. The work consisted of two parts: one practical, the other theoretical. -
IAEA Nuclear Energy Series Electric Grid Reliability and Interface With
IAEA Nuclear Energy Series IAEA Nuclear No. NG-T-3.8No. Plants Power with Nuclear Electric Grid Reliability and Interface IAEA Nuclear Energy Series No. NG-T-3.8 Basic Electric Grid Reliability Principles and Interface with Nuclear Power Plants Objectives Guides Technical Reports INTERNATIONAL ATOMIC ENERGY AGENCY VIENNA ISBN 978–92–0–126110–6 ISSN 1995–7807 IAEA NUCLEAR ENERGY SERIES PUBLICATIONS STRUCTURE OF THE IAEA NUCLEAR ENERGY SERIES Under the terms of Articles III.A and VIII.C of its Statute, the IAEA is authorized to foster the exchange of scientific and technical information on the peaceful uses of atomic energy. The publications in the IAEA Nuclear Energy Series provide information in the areas of nuclear power, nuclear fuel cycle, radioactive waste management and decommissioning, and on general issues that are relevant to all of the above mentioned areas. The structure of the IAEA Nuclear Energy Series comprises three levels: 1 — Basic Principles and Objectives; 2 — Guides; and 3 — Technical Reports. The Nuclear Energy Basic Principles publication describes the rationale and vision for the peaceful uses of nuclear energy. Nuclear Energy Series Objectives publications explain the expectations to be met in various areas at different stages of implementation. Nuclear Energy Series Guides provide high level guidance on how to achieve the objectives related to the various topics and areas involving the peaceful uses of nuclear energy. Nuclear Energy Series Technical Reports provide additional, more detailed, information on activities related to the various areas dealt with in the IAEA Nuclear Energy Series. The IAEA Nuclear Energy Series publications are coded as follows: NG — general; NP — nuclear power; NF — nuclear fuel; NW — radioactive waste management and decommissioning. -
2011 FUEL CELL TECHNOLOGIES MARKET REPORT July 2012 Authors
2011 FUEL CELL TECHNOLOGIES MARKET REPORT July 2012 Authors This report was a collaborative effort by staff of the Breakthrough Technologies Institute, Inc., in Washington, DC. Acknowledgement The authors relied upon the hard work and valuable contributions of many men and women in government and in the fuel cell industry. The authors especially wish to thank Sunita Satyapal and the staff of the US Department of Energy’s Fuel Cell Technologies Program for their support and guidance. The authors also wish to thank Rachel Gelman of the National Renewable Energy Laboratory and the many others who made this report possible. ii Contents List of Figures .....................................................................................................................................................v List of Tables ......................................................................................................................................................vi List of Acronyms ..............................................................................................................................................vii Introduction ..........................................................................................................................................................1 Financial Data .....................................................................................................................................................3 Cost Reduction ...........................................................................................................................................3 -
Electrical System
Revision 20—04/07 KPS USAR 8-i Chapter 8: Electrical System Table of Contents Section Title Page 8.1 DESIGN BASIS . 8.1-1 8.1.1 Principal Design Criteria . 8.1-1 8.1.1.1 Performance Standards . 8.1-1 8.1.1.2 Emergency Power . 8.1-2 8.2 ELECTRICAL SYSTEM. 8.2-1 8.2.1 Network Interconnections . 8.2-1 8.2.1.1 Substation DC System . 8.2-3 8.2.2 Plant Distribution System . 8.2-4 8.2.2.1 Single Line Diagrams. 8.2-4 8.2.2.2 Main Auxiliary, Reserve Auxiliary and Tertiary Auxiliary Transformers . 8.2-4 8.2.2.3 4160V System . 8.2-4 8.2.2.4 480V System . 8.2-5 8.2.2.5 125V and 250V DC System. 8.2-6 8.2.2.6 Instrument Bus . 8.2-8 8.2.2.7 Evaluation of Layout and Load Distribution . 8.2-8 8.2.2.8 Separation Criteria . 8.2-9 8.2.2.9 Relay Room . 8.2-13 8.2.2.10 Testing . 8.2-13 8.2.3 Emergency Power . 8.2-14 8.2.3.1 Sources Description . 8.2-14 8.2.3.2 Loading Description. 8.2-17 8.2.3.3 Load Evaluation . 8.2-21 8.2.3.4 Batteries and Battery Chargers . 8.2-24 8.2.3.5 Reliability Assurance . 8.2-25 8.2.3.6 Surveillance Requirements . 8.2-27 8.2.4 Station Blackout . 8.2-27 8.2.4.1 Introduction . -
Power Failures on Ships Safety Study
Power Failures on Ships Safety study Investigation number: M2016-S1 FOREWORD On the basis of section 2 of the Safety Investigation Act (525/2011), the Safety Investigation Authority decided to initiate a safety study on power failures on ships. Senior researcher Sirpa Kannos led the investigation team until 24 February 2017, after which Lieutenant Senior Grade (retired) Jari Alanen took over as investigation team leader. As members of the joint in- vestigation team were appointed Captain (Master of Maritime Management) Teemu Leppälä, Chief Engineer Tuomo Leppälä and Captain (Master of Maritime Management) Johanna Vahtera. In addition, on site investigations were conducted by Captain Bengt Malmberg, Cap- tain Mikko Rausti and Naval Architect Niklas Rönnberg. Chief Engineer and Electrical Engi- neer Pekka Ilmiö was appointed expert on power failures. Chief Marine Safety Investigator Risto Haimila was Investigation Leader. This safety study report describes the investigation process, gives general information about power failures on ships and presents acts and regulations concerning power failures on ships. The reports on specific cases as well as a joint analysis on them are included. At the end of this report safety recommendations are presented. By implementing them, similar accidents and incidents can be avoided in the future, or their consequences can be mitigated. The purpose of safety investigation is increasing public safety, preventing accidents and inci- dents as well as mitigating damages caused by accidents. Safety investigations do not consider possible liabilities or obligations to compensate for damages. The use of investigation reports for any purpose other than to improve safety must be avoided. Power failures in narrow fairways and in areas with dense traffic can cause very serious sea- and environmental accidents. -
Defence in Depth of Electrical Systems and Grid Interaction
CSNI Draft Report DEFENCE IN DEPTH OF ELECTRICAL SYSTEMS AND GRID INTERACTION Final DIDELSYS Task Group Report 1 2 Forward The July 2006 Forsmark-1 event identified a number of design deficiencies related to electrical power supply to systems and components important to safety in nuclear power plants. While plant- specific design features at Forsmark-1 contributed to the severity of the sequence of events which occurred at Forsmark, a number of the design issues are of a generic nature as they relate to commonly used approaches, assumptions, and design standards for voltage protection of safety related equipment. The NEA Committee on the Safety of Nuclear Installations (CSNI) authorized formation of a task group in January 2008 to examine Defence in Depth of Electrical Systems and Grid Interaction with nuclear power plants (DIDELSYS). The task was defined based on the findings of an NEA sponsored workshop on lessons learned from the July 2006 Forsmark-1 event held in Stockholm, Sweden in 5-7 September 2007. The task group members participating in this review included: • John H. Bickel, ESRT, LLC (Sweden) - Chairman • Alejandro Huerta, OECD/NEA - Secretary • Per Bystedt, SSM (Sweden) • Tage Eriksson, SSM (Sweden) • Andre Vandewalle, Nuclear Safety Support Services (Belgium) • Franz Altkind, HSK (Switzerland) • Thomas Koshy, USNRC (United States) • David M. Ward, Magnox Electric Co. (United Kingdom) • Brigitte Soubies, IRSN (France) • Kim Walhstrom, STUK, (Finland) • Alexander Duchac, EC Joint Research Center Petten (European Commission)