JOB SPECIFIC Date: 2/2/2021 RIC No: 2020-CT-054
Total Page:16
File Type:pdf, Size:1020Kb
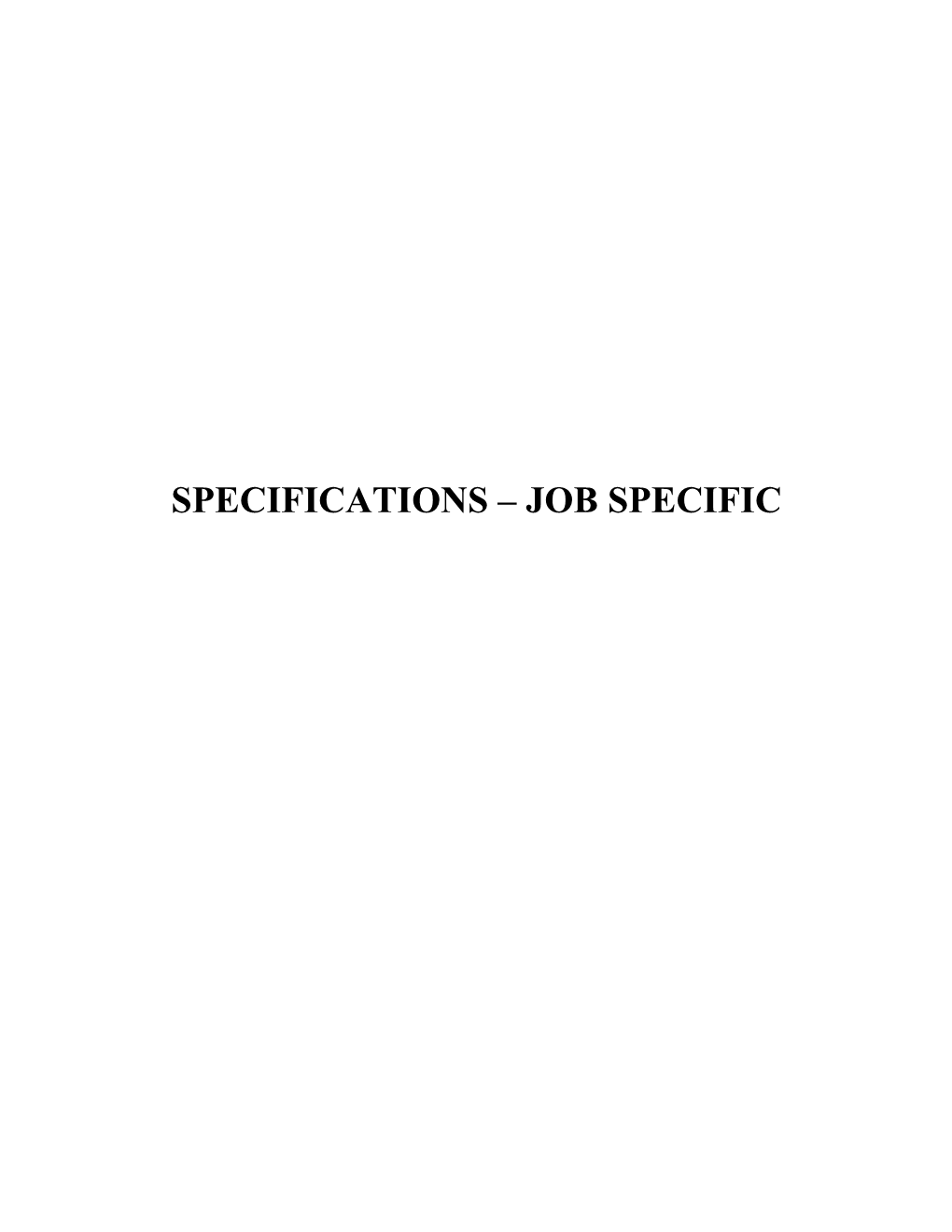
Load more
Recommended publications
-
Hem-Fir Mass Timber Research Project
https://www.google.ca/imgres?imgurl=https%3A%2F%2Fd30y9cdsu7xlg0.cloudfront.net%2Fpn g%2F12462- 200.png&imgrefurl=https%3A%2F%2Fthenounproject.com%2Fterm%2Femail%2F12462%2F&dMarch 2020 ocid=jH9Kq4AvAehGEM&tbnid=ajL6wHzB9jAbAM%3A&w=200&h=200&bih=860&biw=8 Hem-Fir Mass Timber Research Project Report 604-688-2424 Ext. 304 Ference & Company 550 – 475 West Georgia Street [email protected] Vancouver, BC V6B 4M9 www.ferenceandco.com Prepared for Forestry Innovation Investment EXECUTIVE SUMMARY Purpose and Scope of Study The purpose of the study is to evaluate and summarize any technical or other impediments to using hem-fir in mass timber products. The different mass timber products included in the study are cross-laminated timber (CLT), glue-laminated timber (glulam), dowel-laminated timber (DLT) and nail-laminated timber (NLT). Method of Study Thirty-one semi-structured interviews were conducted with key informants to obtain insights regarding the suitability of hem-fir for use in mass timber projects from a variety of perspectives including regulatory, technical, supply chain and market acceptance factors. The key informants were from a variety of organizations including regulatory agencies, research organizations, mass timber manufacturers, hem-fir timber suppliers, architects, structural engineers, building contractors, industry associations and government. In addition, a detailed document and literature review was conducted to obtain the available published information on the regulatory, technical and market factors affecting the use of hem-fir in mass timber products. Key Findings The key study findings are: 1. The size of the mass timber industry in BC is still small. There currently exists only one CLT manufacturer while an additional CLT manufacturer will be operational next year. -
Crosslam® CLT Ground Protection Matting Engineered for the Environment and Your Bottom Line
CrossLam® CLT Ground Protection Matting Engineered for the environment and your bottom line. The Structurlam Advantage ENVIRONMENTAL RESPONSIBILITY DEPENDABILITY In addition to protecting the environment at your jobsite, Our quality control processes and procedures are second every CrossLam® CLT mat we make promotes sustainability. to none. Every mat is designed to give you a predictable, All of our products are engineered with low VOC, exterior dependable service life. grade polyurethane adhesives that contain no added urea- formaldehyde and are deemed to be inert, creating no impact INNOVATION to the environment. Our manufacturing process sets CrossLam® CLT matting solutions apart from “old school” matting fabrication. The solvent-free We aim to mitigate the environmental impacts of our and formaldehyde-free polyurethane adhesive used in our manufacturing process and exceed all regulations regarding proprietary press design allows CrossLam® CLT to be the most emissions and waste material. We currently utilize residual fiber consistent engineered matting on the market today. The process as biofuel and are always looking to incorporate environmental and laminating of layers in crosswise directions reduces wood aspects into our product development. expansion and shrinkage for consistent stability throughout the life cycle of the mat. DURABILITY We grade-select the softwood lumber that goes into our matting ® PARTNERSHIP Why CrossLam CLT Matting? products to maximize their in-service performance, extending Structurlam helps you stay ahead of your competition by the wear surface and service life. All of which increases your providing a superior product. Because CrossLam® CLT lasts longer, It all adds up to savings. return on investment and lowers your cost of ownership. -
Steellock INTERLOCKING MAT SYSTEM
SteelLock INTERLOCKING MAT SYSTEM Start on Solid Ground Strad is committed to helping develop North America’s resources responsibly and effi ciently. To do this, Strad has continually worked to provide customers with superior solutions and services in the energy industry. Strad’s Environmental and Access Matting Solution is just one area where we have made a name for ourselves as the global leader for innovative and reliable matting products and services. Constantly challenging the status quo, Strad continues to provide advances in design, terrain adaptive features and construction materials that increase access to remote locations, protect sensitive terrain and reduce reclamation costs. SteelLock Interlocking Mats Strad’s steel-framed interlocking system SteelLock is constructed without nails, bolts or pins, and provides a durable base that will not pull apart. SteelLock mats are used for access roadways to remote locations, but can also be used as a rig mat for platforms or construction sites to protect sensitive terrain from damage and reduce reclamation costs. Strad’s SteelLock is the only mat in the industry with corner attachments that results in laying fewer access mats and making it easier to navigate curves. Strad’s SteelLock mats are the industry standard for high strength, fl exible roadways and pad matting solutions. Key Features • Steel wide fl ange construction • Pivots at joints to accommodate grade • Corner attachment options • 3 beam design • Steel frame with interlocking ends increases safety • Adapts to uneven terrain -
Midstream Tiger Industrial Rentals Catalog of Rental Equipment
INFRASTRUCTURE R ENTAL EQUIPMENT CATALOG 2019 When it comes to supplying essential rental equipment, you need a INFRASTRUCTURE INFRASTRUCTURE reliable company that gets the job done right. That’s the mark of Tiger. INFRASTRUCTURE RENTAL EQUIPMENT TABLE OF CONTENTS TIGER MATS 4 GENERATORS & LIGHT TOWERS 22 ECOmatsTM 6 25 kVA Portable Generator 23 Tiger Poly Mat 8 45 kVA Portable Generator 23 Tiger Laminate Mat 10 85 kVA Portable Generator 23 Tiger Hardwood Mat 12 125 kVA Portable Generator 24 150 kVA Portable Generator 24 PUMPS 14 220 kVA Portable Generator 24 6” x 6” Vac-Assist Pumps (6612T) 15 300 kVA Portable Generator 25 6” x 6” Vac-Assist Pumps (6NNT) 15 4,000 Watt Portable Light Tower 25 4” x 4” Vac-Assist Pump (4NNT) 16 LED Portable Light Tower 25 Super 6 Pump (6NHTA) 16 6” x 6” Self Prime Pump (6STX) 18 CLEANING & WASHING UNITS & FUEL POD 26 6” x 3” High Head Vac-Assist Pump (3HC) 18 4K PSI Trailer Mount Hot Water Pressure Washer 26 3” x 6” Vac-Assist Pumps (3617MX) 19 4K PSI Trailer Mount Hot Water Pressure Washer 4” x 6” Vac-Assist Pump (4622MX) 19 2 Skid (Double Trouble) 26 325 HP Medium Head 10” x 8” Pump (8NHTA) 20 528 Gallon Double Wall Fuel Pod 26 600 HP High Head 10” x 8” Pump (8NHTH) 20 8” x 6” x 14” Centrifugal Diesel Pump 21 BLAST RESISTANT BUILDINGS 27 to view the SCAN W-440 Triplex Pump 21 8’ x 20’ Blast Resistant Building 27 our capabilities video 2 TIGER INDUSTRIAL RENTALS W: tigerindustrialrentals.com | T: +1 888-866-0047 / +1 409-832-9336 TIGER INDUSTRIAL RENTALS W: tigerindustrialrentals.com | T: +1 888-866-0047 / +1 409-832-9336 3 VERSATILITY TIGER NOW HAS MORE MATTING SOLUTIONS Nobody can move mats like Tiger! We now have 6 matting solutions for clients in the commercial construction industry. -
Dot 25933 DS1.Pdf
Final Report Contract No. BDK80 977-23 Analysis of Movable Bus Stop Boarding and Alighting Areas Prepared for: Research Center Florida Department of Transportation 605 Suwannee Street, M.S. 30 Tallahassee, FL 32399-0450 Prepared by: Nakin Suksawang, Ph.D., P.E., Assistant Professor Albert Gan, Ph.D., Professor Priyanka Alluri, Ph.D., Research Associate Kirolos Haleem, Ph.D., Research Associate Katrina Meneses, Graduate Research Assistant Fabian Cevallos, Ph.D., Transit Program Director Dibakar Saha, Graduate Research Assistant Lehman Center for Transportation Research Florida International University 10555 West Flagler Street, EC 3680 Miami, FL 33174 Phone: (305) 348-3116 Fax: (305) 348-2802 E-mail: [email protected] May 2013 DISCLAIMER The opinions, findings, and conclusions expressed in this publication are those of the authors and not necessarily those of the State of Florida Department of Transportation. iii METRIC CONVERSION CHART SYMBOL WHEN YOU KNOW MULTIPLY BY TO FIND SYMBOL LENGTH in inches 25.4 millimeters mm ft feet 0.305 meters m yd yards 0.914 meters m mi miles 1.61 kilometers km mm millimeters 0.039 inches in m meters 3.28 feet ft m meters 1.09 yards yd km kilometers 0.621 miles mi SYMBOL WHEN YOU KNOW MULTIPLY BY TO FIND SYMBOL AREA in2 square inches 645.2 square millimeters mm2 ft2 square feet 0.093 square meters m2 yd2 square yard 0.836 square meters m2 ac acres 0.405 hectares ha mi2 square miles 2.59 square kilometers km2 mm2 square millimeters 0.0016 square inches in2 m2 square meters 10.764 square feet ft2 m2 square meters 1.195 square yards yd2 ha hectares 2.47 acres ac km2 square kilometers 0.386 square miles mi2 SYMBOL WHEN YOU KNOW MULTIPLY BY TO FIND SYMBOL VOLUME fl oz fluid ounces 29.57 milliliters mL gal gallons 3.785 liters L ft3 cubic feet 0.028 cubic meters m3 yd3 cubic yards 0.765 cubic meters m3 mL milliliters 0.034 fluid ounces fl oz L liters 0.264 gallons gal m3 cubic meters 35.314 cubic feet ft3 m3 cubic meters 1.307 cubic yards yd3 NOTE: volumes greater than 1000 L shall be shown in m3 iv Technical Report Documentation Page 1. -
800-836-5011 Icon’S History
Equipment Distributors, Inc. 800-836-5011 www.iconjds.com ICON’S HISTORY The ICON Vision: We will revolutionize the trench shoring and guided auger boring industry by achieving new benchmarks of quality that exceed current industry standards through creativity, teamwork, and partnerships. Brian Crandall incorporated ICON Equipment Distributors In 2004, ICON became the national distributor and dealer in 1982 to provide shoring services to the contracting in- for Bohrtec, Gmbh. Bohrtec is the world’s leading man- dustry. As an innovator for the industry, ICON was the ufacturer of a guided auger boring system that utilizes fi rst shoring distributor to receive engineering approval pilot tube technology to install sewers directly on line and for the slide rail system from the City of New York, the grade. The addition of the Bohrtec machines has and will NY/NJ Port Authority and dozens of Transportation De- continue to enhance the company’s ability to take on partments throughout the United States. From the start, more interesting and challenging projects. ICON developed a reputation as a company that provides Currently, ICON serves over 1,600 customers across the safe shoring solutions for both small and large construc- U.S. and more than 8,000 slide rail projects have been tion projects. Even some of the most diffi cult excavations completed to date. Built on site at ICON’s manufacturing were able to be completed with ease due to the modular- facilities, slide rail systems are rented and sold to con- ity of the system. tractors throughout the United States. In addition to slide The 90’s brought growth to the organization with the rail systems, ICON provides steel and aluminum trench opening of branch offi ces in several East Coast cities. -
Mississippi Landmarks Volume 14, Number 1
volume 14, number 1 RESEARCH, EDUCATION, AND EXTENSION VICE PRESIDENT’S Mississippi LandMarks is published quarterly by the Division of Agriculture, Forestry, and Veterinary Medicine at Mississippi State University. More Mississippians are living away from the farm than PRESIDENT in any other time in the state’s Mark E. Keenum history. As our population VICE PRESIDENT becomes more urban, we Gregory A. Bohach often hear that people are disconnected from agriculture DIRECTOR, MSU EXTENSION SERVICE and, therefore, do not value it as Gary B. Jackson they once did. In response, we humbly submit these facts: We DEAN, COLLEGE OF AGRICULTURE AND LIFE SCIENCES all eat food, wear clothes, live in homes constructed with forest DEAN, COLLEGE OF FOREST RESOURCES products, and use some sort of transportation. Everyone in DIRECTOR, FOREST AND WILDLIFE RESEARCH CENTER the world depends on agriculture for some aspect of daily life, DIRECTOR, MISSISSIPPI AGRICULTURAL AND FORESTRY and we are thankful for the Mississippi producers who work to EXPERIMENT STATION provide our food, fiber, and fuel. George M. Hopper We also are proud to play our part in helping those producers DEAN, COLLEGE OF VETERINARY MEDICINE leverage the latest scientific discoveries to help them remain Kent H. Hoblet efficient, sustainable, and profitable. Preliminary estimates for the 2017 crops indicate agriculture continues to contribute more than Mississippi LandMarks is produced by the $7 billion to the state’s economy. Several commodities saw gains Office of Agricultural Communications. over 2016, including poultry, soybean, and cotton. EXECUTIVE EDITOR Part of our work with producers includes the annual Row Elizabeth Gregory North Crops Short Course, which took place in December at The Mill in Starkville. -
Full PDF Brochure
800-836-5011 www.iconjds.com UTILITY & CONSTRUCTION MATTING SYSTEMS WOOD MATS Heavy-Duty Wood mats are used by the utility, construction and drilling industry to support the heaviest machinery and equipment the market has to offer. Mat lengths available up to 40’ long and can be 3.5” to 18” thick depending on the application. Loading and unloading of wood mats is generally done with a forklift, loader, excavator or crane onsite. Shipping can be handled by outside carrier flat bed load or by train depend- ing on the quantity ordered for rental or sale. Crane/Dragline Mats Constructed using mixed hardwood, Douglas Fir or ICON offers a full line of wood and composite Oak timbers. g matting systems for the utility and construc- Sizes up to 40’ in length g Thickness from 6” to 18” tion industry. Whether you are looking for g Exposed bolts or cable matting systems needed for crane support, pipeline projects, temporary road access, Laminated Mats trestle bridges or other unique applications g Standard 8’x16’, 3-ply mats or special order we can supply a product built to your unique g Cables or chains specifications that meets the strictest industry standards, ensuring you a superior Emtek® Mats g product every time. Available mat products Engineered hardwood glue-laminated mats g include but are not limited to; crane mats, Thickness from 3.5” to 7.5” g Design values available for each thickness dragline mats, Emtek® engineered laminated mats and durable and re-usable composite DuraDeck mats. ICON has partnered with some of the nation’s largest suppliers so we can always provide competitive pricing, fast delivery and the best personalized customer service. -
Accessibility Self-Evaluation and Transition Plan Overview, Lassen
ACCESSIBILITY SELF-EVALUATION AND TRANSITION PLAN LASSEN VOLCANIC NATIONAL PARK CALIFORNIA OCTOBER 2020 NOTE: Do not delete this page; it is for layout purposes. EXECUTIVE SUMMARY Lassen Volcanic National Park’s Accessibility Self-Evaluation and Transition Plan (SETP) includes findings from the self-evaluation process, as well as a plan for improving accessibility parkwide. The Accessibility Self-Evaluation and Transition Plan resulted from the work of an NPS interdisciplinary team, including planning, design, and construction professionals; and interpretive, resource, visitor safety, maintenance, and accessibility specialists. Site plans, photographs, and specific actions for identified park areas were developed. Associated time frames and implementation strategies were established to assist NPS park staff in scheduling and performing required actions and to document completed work. Park policies, practices, communication, and training needs were also addressed. The goals of the plan are to 1) document existing park barriers to accessibility for people with disabilities, 2) provide an effective approach for upgrading facilities, services, activities, and programs, and 3) instill a culture around creating universal access. The following are the key park experiences and associated park areas addressed in the transition plan: 1) Appreciate the dynamic landscape, scenic values, and iconic views – Bumpass Hell Trailhead, Butte Lake, Devastated Area Trailhead, Drakesbad Guest Ranch, Emerald Lake, Hat Creek Trailhead, Juniper Lake – North, Juniper -
Resource Roads and Wetlands: a Guide for Planning, Construction and Maintenance
Resource Roads and Wetlands: A Guide for Planning, Construction and Maintenance SPECIAL PUBLICATION SP-530E fpinnovations.ca 01. foreword © FPInnovations 2016. All rights reserved. Unauthorized copying or distribution prohibited. 2 01. foreword Resource Roads and Wetlands: A Guide for Planning, Construction and Maintenance SPECIAL PUBLICATION SP-530E FPInnovations Ducks Unlimited Canada Mark Partington, R.P.F., M.Sc. Beverly Gingras, M.Sc. Clayton Gillies, R.P.F., R.P.Bio. Christopher E. Smith, C.W.B. Julienne Morissette, Ph.D. Partington, M., Gillies, C., Gingras, B., Smith, C. & Morissette, J. (2016). Resource roads and wetlands: a guide for planning, construction and maintenance. (Special Publication SP-530E) Pointe-Claire, QC: FPInnovations. ISBN 978-0-86488-572-2 (Print) ISBN 978-0-86488-573-9 (PDF) ISSN 1925-0495 (Print) All photos courtesy of FPInnovations ISSN 1925-0509 (PDF) unless otherwise indicated. Funding was provided by Natural Resources Additional funding was provided through the Canada under the NRCan/FPInnovations Sustainable Forestry Initiative Conservation CFS Contribution Agreement. and Community Partnerships Grant Program. TABLE OF CONTENTS (Photo courtesy of Ducks Unlimited Canada.) 01. 04. Foreword Knowing your wetlands The issue ............................................................ 6 Benefits of wetlands ................................... 16 The problem ..................................................... 6 Classes of wetlands ..................................... 17 What this guide is .......................................... -
Reliable Solutions for Various Fields of Application
MENU Reliable solutions for various fields of application MEMBER OF INDUSTRIES Contents 4 Member of Constantia Industries 5 International focus 6 Isosport Group 7 Strategy, Mission, Vision 8 Mission statement 9 Partner in all industry fields 10 Reliable solutions 11 Technology 12 Milestones in development KOTERM PRESSED 13 A wide range of possibilities 14 Reliable solutions for all fields of industry 15 Mechanical industry 16 Paper industry 17 Food processing, 18, 19, 20 21 Chemical industry 22 Mining 23 Protection boards Funice 24 Sport / Synthetic ice panels 25 Joint development projects with clients, 26 ISOFORM extruded 27 A wide range of possibilities 28 Co-extruded sheet 29 Filled materials 30 Reliable solutions for all fields of industry 31 Thermoforming 32 Automotive industry 33 Chemical industry 34 Electrical industry 35 Sound proofing 36 Furniture industry 37 Orthopaedics/Isortho 38 Building construction 39 Fabac ISOTRACK 40 Temporary roadways 41 Wide product range 42 Reliable solutions 43 Isotrack series X, 44 45 Isotrack series H, 46 47 Isotrack tMat, 48 49 Isotrack M 50 Isotrack series L, 51 52 Isotrack eMat, 53 54 Isotrack B ISOKON info MENU MEMBER OF CONSTANTIA INDUSTRIES Overview Constantia Constantia Energy Constantia Woods & Decorative & Technical Sports Elements Components FunderMax ISOVOLTA Isosport Group Group Group 4 MENU Privately owned industrial holding since 1949. International focus Clients in numerous industries Construction & Furniture Sports & Leisure Machinery industry Aviation & Transportation Electrical industry 4 5 MENU Isosport Group – Production Plants ISOSPORT Eisenstadt Austria ISOKON Slovenske Konjice Slovenia Halászi ISOKON Hungary Velenje Togliatti Slovenia Russia Bangalore India 6 MENU We offer innovative solutions, adapted to the needs of our customers, whose basic Strategy principle is added value. -
Community Services and Public Safety Committee Regular Meeting Monday, February 24, 2020, 9:00 A.M
The Town of Hilton Head Island Community Services and Public Safety Committee Regular Meeting Monday, February 24, 2020, 9:00 a.m. Benjamin M. Racusin Council Chambers AGENDA As a courtesy to others, please silence all mobile devices during the meeting. 1. Call to Order 2. FOIA Compliance - Public notification of this meeting has been published, posted, and distributed in compliance with the South Carolina Freedom of Information Act and the requirements of the Town of Hilton Head Island. 3. Approval of Minutes a. January 27, 2020 4. Unfinished Business 5. New Business a. 4th Quarter 2019 Crime Statistics - BCSO b. Recommendation to Approve Public Art Master Plan c. Mitchelville Master Plan and Business Plan 6. Adjournment Please note that a quorum of Town Council may result if four (4) or more of their members attend this meeting. 1 Town of Hilton Head Island Community Services & Public Safety Committee Monday, January 27, 2020 at 9:00 am Benjamin M. Racusin Council Chambers MEETING MINUTES Present From the Committee: Marc Grant, Bill Harkins, Tom Lennox Present from Town Council: Tamara Becker Present from Town Staff: Scott Liggett, Josh Gruber, Charles Cousins, Shawn Colin, Jeff Buckalew, Jennifer Ray, Marcy Benson Present from Media: None 1. Call to Order 2. FOIA Compliance - Public notification of this meeting has been published, posted, and distributed in compliance with the South Carolina Freedom of Information Act and the requirements of the Town of Hilton Head Island. 3. Approval of Minutes – December 23, 2019 – Councilman Lennox moved to approve. Councilman Harkins seconded. The December 23, 2019 Minutes were unanimously approved.