Bindery Techniques ® Olumeolume 6 of the Standard Looks at Binding Techniques, the All-Important final Stage of Print Production
Total Page:16
File Type:pdf, Size:1020Kb
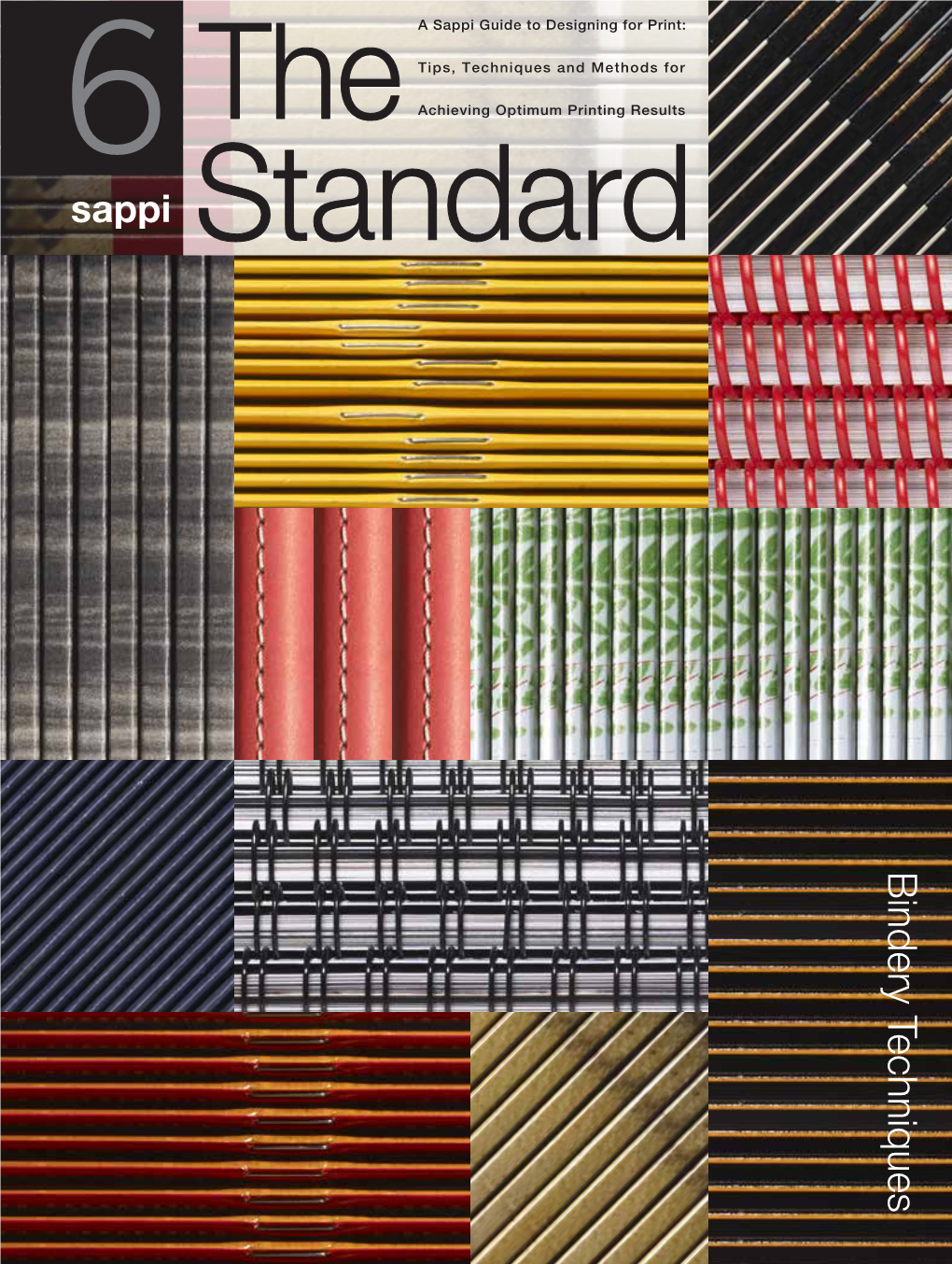
Load more
Recommended publications
-
DARK ENTRIES GR: You Know,In Rlng-Otaku
words Anne lshii illustrationI MartinCendreda DARK ENTRIES GR: You know,in Rlng-otaku. They Rmg, and the mol Suzuki Method think aboutthat, in some way,an o KS: Interruptsm lutelynot, Anne. that. I ride motorc Tn ra,all-t scare someone,you have to inspire lear, nol lorce it. at a gym,for cryinl anyotaku who woL You have to allude to the horror. not show it. of a fun timeis h: the opensky wear not stayingcoupe overa vioeotape. ive years ago, four teenagers watched a haunted videotape in a rented cabin lf you arrangefor an interviewwith Suzuki, his and made permanent horror-Iilm history. Since the little wet Japanese qirl managerwill stipulatethat you understandthe GR: Yeah,but mos with long black hair in a white nightgown lirst stepped out of the hidden followingthree points:1. KoliSuzuki is NOTa At least in the U.S weli to avenqe her death, there have been no less than six films made, and horrorwr ter,2. KoliSuzuki did NOTwrite Jl-On, in Japan? at least two more film projects in the pipeline based on the worl<s of Scdoko/,So- 3. Koi Suzuklneeds an interpreter.As hisinter- morro creator, Koji Suzuki. But don't ask him what he thinks atrout those movres. preterand pub ic st, I havewatched practically KS: Lots of otaku Don'i ask him about Hideo Nakata's vision or Naomi Watts'acting ability. Definitely everyman, woman, and child on Earthtry to get it's kind of neatth don't ask him about Ju-On, The Eye, or The Rinq 2 ("MV r?jngr has created a lot ol him excitedabout the movies,and Suzuki is just the true testof a f: bastard children."). -
Book Review of the Ring Written by Koji Suzuki
BOOK REVIEW OF THE RING WRITTEN BY KOJI SUZUKI FINAL PROJECT In Partial Fulfillment of the Requirement For S-1 Degree in Literature In English Department, Faculty of Humanities Diponegoro University Submitted by: Gaetano Ardhanto A2B009046 FACULTY OF HUMANITIES DIPONEGORO UNIVERSITY SEMARANG 2014 PRONOUNCEMENT The writer states truthfully that this project is compiled by his without taking the result from other research in any university, in S-1, S-2, and S-3 degree and in diploma. In addition, the writer ascertains that he does not take the material from other publications or someone‘s work except for the references mentioned in bibliography. Semarang, 4 December 2013 Gaetano Ardhanto ii MOTTO AND DEDICATION First, you must decide. Then you must follow through. That‘s the only way you can get anything accomplished. (Lacus Clyne) This final project dedicated to my beloved family iii APPROVAL Approved by Advisor On 4 December 2013 Dr. Suharno, M.Ed. NIP. 195205081983031001 iv VALIDATION Approved by Strata I Final Project Examination Committee Faculty of Humanities Diponegoro University On 4 March 2014 Advisor, Reader, Dr. Suharno, M.Ed. Dra. Astri Adriani Allien, M.Hum NIP. 195205081983031001 NIP. 196006221989032001 v ACKNOWLEDGEMENT Praise is to God Almighty, who has given strength and true spirit so this final project on —Book review of The Ring written by Koji Suzuki“ came to a completion. On this occasion, the writer would like to thank all those people who have contributed to the completion of this research report. The deepest gratitude and appreciation is extended to Dr. Suharno, M.Ed. ± the writer‘s advisor- who has given his continuous guidance, helpful correction, moral support, advice and suggestion. -
Reviews of the Ring Series the Ring Series, Also Known As “Ringu
Reviews of The Ring Series The Ring series, also known as “Ringu” or just “Ring”, is considered the founding factor in the west’s interest in Japanese horror and helped bridge the gap between international films. Based on a series of novels written by Koji Suzuki, the films revolve around a cursed videotape that kills anyone who watches it after seven days. Though the first book is a horrormystery, its two sequels Spiral and Loop are a medical mystery and a science fiction mystery respectively, all having intriguing storylines and plot twists that explore the sinister virus that originates from the videotape rather than a haunting curse. The Ring series has spawned a TV movie, two TV series, a fantastic Japanese film series, a crumby Korean film, and a respectible American movies too. And we’re gonna review all of them in this megareview. The franchise reflects a lot of modern fears in society – a fear of technology, urban legends, deadly illnesses (the AIDS scare in the 1980s and 1990s), unexpected pregnancy (as seen in Spiral), and the more traditional scares of evil and monsters. The main antagonist, Sadako Yamamura, takes a lot of inspiration from Japanese mythology and traditions. She is an “onryō”, or a vengeful female spirit, sporting the traditional long stringy hair and wears a white dress. Her origin is based on several folktales, most notably about a woman who is chucked down a well, where she dies and rises as a ghost. Obviously, there will be spoilers for the books and films throughout these minireviews, so be weary. -
Ring Alternative Loops and Their Loop Ringsl Edgarg
Resenhas IME-USP 1995, Vol. 2, No. l, 47 - 82. Ring Alternative Loops and their Loop Ringsl EdgarG. Goodaire2 and Cesar Polcino Milies3 Abstract: In 1983, a few examples of Moufang loops whose loop rings are alternative, but not associative, were dis covered. Since that tim~, there has been a great deal of worle devoted to the study of such loops and to their loop rings. Tlus paper is a survey of some of the more important results in this still relatively young area. Key words: Alternative Ring, Moufang loop. Loop of Units, Torsion Uluts, Trivial Units, Isomorphism Problem. AMS classification: Primary 17D05; Secondary 20N05, 16S34. CONTENTS 1. Loops whose Loop Rings are Alternative 47 1.1. Historical Background 47 1.2. Alternative Rings 50 1.3. Moufang Loops 52 1.4. Alternative Loop Rings 53 1.5. RA Loops 56 1.6. The Nucleus and Centre of an Alternative Loop Ring 61 2. The Isomorphism Problem 62 2.1. Background 62 2.2. Loop Rings over the Integers 63 2.3. Loop Algebras over Fields 65 3. Trivial Units 70 3.1. Units of Finite Order 70 3.2. Central units 72 3.3. Can the torsion units form a subloop? 74 4. Some Conjectures of H. J. Zassenhaus 75 4.1. Group Rings 75 4.2. Loop Rings 76 References 79 1. Loops WHOSE Loop RINGS ARE ALTERNATIVE 1.1. Historical Background. The formula (a2 + b2)(c2 + d2) = (ac - bd)2 + (be + ad)2 which shows that the product of two sums of t.wo squares is again the 1 Primary 17D05; Secondary 20N05, 16S34 2The research was supported by the Natural Sciences and Engineering Research Council of Canada, Grant No. -
Loop (Paperback)
ZTKUKUMEXMWN < eBook ~ Loop (Paperback) Loop (Paperback) Filesize: 9.08 MB Reviews Definitely among the best publication We have possibly read through. I really could comprehended everything using this published e ebook. Its been written in an exceedingly straightforward way and it is simply after i finished reading through this ebook through which basically altered me, change the way i believe. (Mr. Malachi Block) DISCLAIMER | DMCA Q0WQ11KSEUEB ^ eBook # Loop (Paperback) LOOP (PAPERBACK) HarperCollins Publishers, United Kingdom, 2007. Paperback. Condition: New. Language: English . Brand New Book. Stunning Japanese novel with a chilling twist - the follow-up to Ring and Spiral.Kaoru s father, Hideyuki, lies dying in a Tokyo hospital, his body ravaged by viral cancer. This nightmarish incurable disease has sprung out of nowhere and has begun to aect organisms all over the planet.Twenty years ago Hideyki worked on a virtual reality project which replicated evolution on earth, called the Loop. The project failed when the organisms within it inexplicably stopped reproducing normally and started cloning. Nearly all of the other scientists who worked on the Loop are already dead - from cancer.To get to the heart of the mystery, Kaoru must travel to the other side of the planet, to the Mojave desert. The secret he encounters there will overturn everything he thought he knew about the world - and his own identity.In this suspense-filled follow-up to `Ring and `Spiral , Suzuki masterfully confounds the reader with a stunning new twist on the Ring mythology. Read Loop (Paperback) Online Download PDF Loop (Paperback) ODUYWUING8EF > PDF \\ Loop (Paperback) Oth er Books Klara the Cow Who Knows How to Bow (Fun Rhyming Picture Book/Bedtime Story with Farm Animals about Friendships, Being Special and Loved. -
ABSTRACT BALL, SARAH KELLY VIRGINIA MCKAY. the Uncanny in Japanese and American Horror Film: Hideo Nakata’S Ringu and Gore Verbinski’S Ring
ABSTRACT BALL, SARAH KELLY VIRGINIA MCKAY. The Uncanny in Japanese and American Horror Film: Hideo Nakata’s Ringu and Gore Verbinski’s Ring. (Under the direction of Maria Pramaggiore.) In the last few decades, interest in the uncanny in the body of literary theory has surged. The uncanny is a ubiquitous presence 21st century American and abroad, and it provides a useful metaphor for understanding the implications of some of the conventions of post-modernism. This thesis explores a contemporary definition of the uncanny as manifested through two film interpretations (Ringu and Ring) of the same source material, a novel titled Ringu by Koji Suzuki. Through a brief exploration of the historical evolution of the idea of the uncanny and the various critical cruxes surrounding it, I have developed six working characteristics of the uncanny as a base for my analysis of Ringu and Ring. Furthermore, I have explored the social, historical, and cultural underpinnings of Suzuki’s original novel and its path to Japanese and eventually American theatres. Within the narrative of both films, the uncanny is manifested through extended use of the doppelganger and repetition. There is no significant difference in the films’ rendering of the uncanny through narrative. The films differ slightly in their presentation of uncanny sound and visual elements: Ringu relies primarily on sound and characters’ internal experience to produce the uncanny, whereas Ring focuses on the visual and characters’ external experience. The films unify their internal rendering of the uncanny with their metatextual (and commercial) behavior with the gaze, an aspect of both films that implicates the viewer in their propagation of the uncanny and the film franchise. -
Code Loops Are R42 Loops
CORE Metadata, citation and similar papers at core.ac.uk Provided by Elsevier - Publisher Connector JOURNAL OF ALGEBRA 130, 385-387 (1990) Code Loops Are R42 Loops ORIN CHEIN * Department of Mathematics, Temple University, Philadelphia, Pennsylvania 19122 AND EDGAR G. GOODAIRE~ Department of Mathematics and Statisrics, Memorial University of Newfoundland, St. John’s, Newfoundland, Canada AIC 5S7 Communicated by George Glauberman Received December 22, 1988 1. INTRODUCTION In [9], Griess considers a class of loops, called code loops, which have applicability to a construction of the monster and its nonassociative algebra (see [7]). In [6], the authors characterize these loops as Moufang loops which have at most one nonidentity square (and hence also at most one nonidentity commutator and at most one nonidentity associator). Moufang loops with one or more of these “uniqueness” properties play an important role in the authors’ work on loops which have alternative loop rings [2-5, 81. For example, a nonassociative loop which has an alter- native loop ring over a ring of characteristic different from two must be a Moufang loop with a unique nonidentity commutator and associator (which coincide). It is the purpose of the present paper to prove that a nonassociative Moufang loop with a unique nonidentity square (i.e., a nonassociative code loop) must, in fact, have an alternative loop ring over any ring of characteristic two. * The research of this author was supported by a grant from the American Philosophical Society and by a research leave from Temple University. + The research of this author was supported in part by Grant A9087 from the Natural Sciences and Research Council of Canada. -
Suzuki Koji. First Printing - Februarysth, 1999
- ringworld books 3/ll/03 5:48 PM T I I I the Ring/ Ringu $y: SuzukiKoji. First printing - June20th, 1991. sroRy:Wren magazinereporterAsakawa Kazuyuki's niece dies suddenlyunder rnysterious circumstances, he decidesto do a titfle investigatinginto the causeof her death.He findsout that,though separatedby distance,his niecedied at exacilythe sametime as lhree of her triends-He also leamsthat all four of themhad watcheda videotape- a tape that kills whomeverwatcfresit exacflyseven days later. NqrEsAND tMpREsSlOruS; Author suzuki Koji presentsa story that, whileengaging, is not quite as polished as in f?asen.The charac'tersans also very differentfrom theironscreen counterparts,with AsakawaKazuyuki being a manied man and Ryuji a sadisticboor home whose past may or may not involve rape. AIso, the famous televison scene is noaftwere to be found: Rn6l director Nakata Hideo credited Wdeadrornefor its inspiration. THEMOVIES ring This version of the Rirg cover was designed by Chip Kidd for the rasen upcomingEnglish-language edition tom Vertical,Inc. Jvlr.Kidd had this ring2 to say on his inspirationfor the design: ring 0 ringvirus This obviouslyuses the Japanese'risingsun'flag and manipulatesit to - the ring remake a more complexextreme. At the centerof the'sun'is a death's head, in tha ring2 a stark bfack and white mntrast to the vibrant color of the sunburst.The tifle is presented in an endless loop, whictr mimics the predicament of TELEVISIONSPECIALS the characters." ring:kanzenban ring:saishuushou Reported by Alan Gleason, The Book &.The Campufer magazine. resen:the series AVAtLABrLtry:Japanese, Chinese, French, German, Thai, Russian,English (04-1mg). FEATURES lost $cenes $ee lere for the Russian version of the novel posted entirety online. -
Science-Fiction Books
Science-Fiction Loop, Suzuki Koji Spiral, Suzuki Koji About the Author: Book Summary: He is a Japanese writer, who was born in The story follows on from the first Ring novel, and Hamamatsu and currently lives in Tokyo. Suzuki is establishes the origin of Sadako Yamamura's cursed the author of the Ring cycle of novels, which has videotape. The idea is that if the tape is watched by been adapted into a manga series. His first book, a woman who is ovulating, she can impregnate Ring (also known as Ringu) has been made into a herself in such a woman and therefore live again. Japanese film, which was remade into a US movie. The woman turns out to be Mai Takano. Fluent in English, he has written several books on It also contains a plot about a former classmate of the subject of fatherhood. Ryuji Takayama from medical school performing He is currently on the selection committee for the his autopsy. In so doing, he discovers that Ryuji Japan Fantasy Novel Award. kept a record of the events that lead to his death. The doctor is unsure of what to do because the Book Summary: record clearly states a danger to the public, but it also includes supernatural events, so going public The story revolves around a simulated reality, could ruin his reputation. exactly the same as our own, known as the Loop: created to simulate the emergence and evolution of life. It is in this alternate universe that the events of the previous novels, Ring and Spiral took place. -
Horror Books
1 Horror The Crimson Labyrinth, Kishi Yusuke Book Summary: It is said that marriage is about compromise, and no one understands this more than newlywed Noriko, who marries into the well-established Shito family. Four generations, eight in-laws—all under one roof—is an untenable proposition, unsettling at best for any bride, but Noriko’s new family members are sweet and caring. Living with them is a delight, and Noriko seems to have the perfect marriage. Yet, the appearance of a disheveled man—asking suspicious About the Author: questions about her new in-laws—plants a seed of doubt in Noriko’s mind, while she is hanging He has twice won the coveted Japan Horror laundry one morning. Paranoia grows. The unusual Association Award, and boasts bestselling status in behavior of her new family, which she once Japan. perceived as charming eccentricities, now appear to be sinister in nature. Their kind smiles, once filled Book Summary: with warmth, now disguise dark secrets. As Noriko delves deeper into the family’s machinations, she A group of travelers are stranded in the desert and awakens to the horrifying reality of “marital fed psychotropic drugs by a media crew that may or compromise.” may not be the real puppet-master in this psycho- horror knockout. Parasite Eve, Sena Hideaki Now You're One of Us, Nonami Asa About the Author: About the Author: Hideaki Sena holds a Ph.D. in pharmacology and has given numerous lectures on the subject of cell Asa Nonami is the award-winning author of The biology as well as the future of the sci-fi genre. -
A Discourse on Winning and Losing
A Discourse on Winning and Losing Col John R. Boyd, USAF, Retired Edited and Compiled by Dr. Grant T. Hammond Air University Press Curtis E. LeMay Center for Doctrine Development and Education Maxwell AFB, Alabama March 2018 Content Editor Library of Congress Cataloging-in-Publication Data James S. Howard Copy Editor Names: Boyd, John, 1927–1997, author. | Hammond, Grant Tedrick, Tammi K. Dacus 1945- editor. | Air University (U.S.). Press, publisher. Title: A discourse on winning and losing / John R. Boyd ; edited Cover Art, Book Design, and Illustrations and compiled by Grant T. Hammond. Daniel Armstrong Description: First edition. | Maxwell Air Force Base, Alabama : Composition and Prepress Production Air University Press, [2017]. | Includes bibliographical references Nedra O. Looney and index. Identifiers: LCCN 2017039845 | ISBN 978585662791 (paperback) Print Preparation and Distribution Subjects: LCSH: Military art and science. | Strategy. | Command Diane Clark of troops. Director and Publisher Classification: LCC U162 .B76 2017 | DDC 355.001—dc23 | Dr. Ernest Allan Rockwell SUDOC D 301.26/6:D 63 LC record available at https://lccn. loc.gov/2017039845 Air University Press 600 Chennault Circle, Bldg. 1405 Maxwell AFB, AL 36112-6010 http://www.airuniversity.af.mil/AUPress/ Published by Air University Press in March 2018 Facebook: https://www.facebook.com/AirUnivPress and Twitter: https://twitter.com/aupress Disclaimer Opinions, conclusions, and recommendations expressed or implied within are solely those of the authors and do not necessarily represent the official policy or position of the organizations with which they are associated or the views of the Air University Press, Air University, United States Air Force, Department of Defense, or any other US government agency.