Plasma Diagnostics and Plasma-Surface Interactions in Inductively Coupled Plasmas
Total Page:16
File Type:pdf, Size:1020Kb
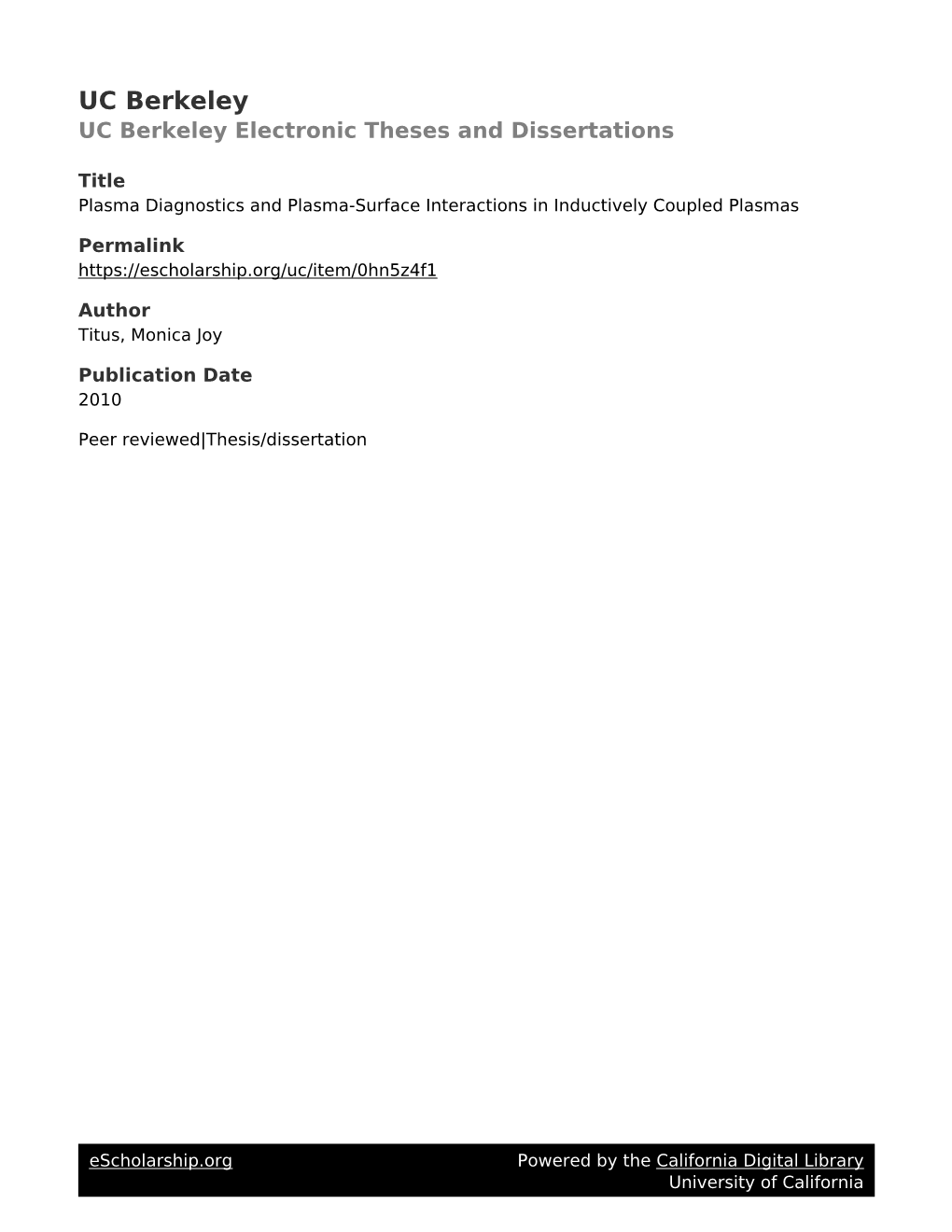
Load more
Recommended publications
-
Microwave Power Coupling with Electron Cyclotron Resonance Plasma Using Langmuir Probe
PRAMANA c Indian Academy of Sciences Vol. 81, No. 1 — journal of July 2013 physics pp. 157–167 Microwave power coupling with electron cyclotron resonance plasma using Langmuir probe SKJAIN∗, V K SENECHA, P A NAIK, P R HANNURKAR and S C JOSHI Raja Ramanna Centre for Advanced Technology, Indore 452 013, India ∗Corresponding author. E-mail: [email protected] MS received 14 April 2012; revised 16 January 2013; accepted 26 February 2013 Abstract. Electron cyclotron resonance (ECR) plasma was produced at 2.45 GHz using 200– 750 W microwave power. The plasma was produced from argon gas at a pressure of 2 × 10−4 mbar. Three water-cooled solenoid coils were used to satisfy the ECR resonant conditions inside the plasma chamber. The basic parameters of plasma, such as electron density, electron temperature, floating potential, and plasma potential, were evaluated using the current–voltage curve using a Langmuir probe. The effect of microwave power coupling to the plasma was studied by varying the microwave power. It was observed that the optimum coupling to the plasma was obtained for ∼ 600 W microwave power with an average electron density of ∼ 6 × 1011 cm−3 and average electron temperature of ∼ 9eV. Keywords. Electron cyclotron resonance plasma, Langmuir probe, electron density, electron temperature. PACS Nos 52.50.Dg; 52.70.–m; 52.50.Sw 1. Introduction The electron cyclotron resonance (ECR) plasma is an established source for delivering high current, high brightness, stable ion beam, with significantly higher lifetime of the source. Such a source has been widely used for producing singly and multiply charged ion beams of low to high Z elements [1–3], for research in materials sciences, atomic and molecular physics, and as an accelerator injector [4,5]. -
Plasma Diagnostics Lecture.Key
LA3NET School | Salamanca, Spain | October 1st, 2014 Advanced diagnostics Plasma density profile measurements and synchronisation of lasers to accelerators J. Osterhoff and L. Schaper Deutsches Elektronen-Synchrotron DESY Outline > Importance of the plasma density profile > Measurement techniques > Interferometry > Absorption spectroscopy > Rayleigh scattering > Raman scattering > Laser induced fluorescence > Synchronisation of lasers to accelerators > Summary Jens Osterhoff | plasma.desy.de | LA3NET School, Salamanca | Oct 1, 2014 | Page 002 Access to novel in-plasma beam-generation techniques requires control over plasma profile in LWFA/PWFA > Density down-ramp injection J. Grebenyuk et al., NIM A 740, 246 (2014) IB & 1kA > Laser-induced ionization injection (Trojan Horse injection) B. Hidding et al., Physical Review Letters 108, 035001 (2012) IB & 5kA > Beam-induced ionization injection A. Martinez de la Ossa et al., NIM A 740, 231 (2014) IB & 7.5kA > Wakefield-induced ionization injection A. Martinez de la Ossa et al., Physical Review Letters 111, 245003 (2013) IB & 10 kA Jens Osterhoff | plasma.desy.de | LA3NET School, Salamanca | Oct 1, 2014 | Page 003 Access to novel in-plasma beam-generation techniques requires control over plasma profile in LWFA/PWFA > Density down-ramp injection J. Grebenyuk et al., NIM A 740, 246 (2014) n0 = 1.2 x 1018 cm-3 IB & 1kA > Laser-induced ionization injection (Trojan Horse injection) B. Hidding et al., Physical Review Letters 108, 035001 (2012) Driver: Eb = 1 GeV, Ib = 10 kA, Qb = 574 pC σz = 7 μm, σx,y = 4 μm, εx,y = 1 μm IB & 5kA injection > Beam-induced ionization injection A. Martinez de la Ossa et al., NIM A 740, 231 (2014) acceleration IB & 7.5kA > Wakefield-induced ionization injection A. -
Plasma Physics Laboratory
MAY 1978 PPPL-1445 UC-20f <-'/C-7- -/ TOKAMAK PLASMA DIAGNOSIS BY SURFACE PHYSICS TECHNIQUES BY S. A. COHEN PLASMA PHYSICS LABORATORY WISER PRINCETON UNIVERSITY PRINCETON, NEW JERSEY- This work was supported by the U. S. Department of Energy v v;- Contract No. EY-76-C-02-3073. Reproduction, translation, „ : >v| publication, use and disposal, in whole or in part, by or S» for the United States Govemme:"i: is -ipi^-h-•<• »,-• :;,•*'$$* NOTICE This report was prepared as an account of work sponsored by the United States Gov ernment. Neither the United States nor the United States Energy Research and Development: Administration, nor any of their employees, nor any of their contractors, subcontractors, or their employees, makes any warranty, express cr implied, or assumes any legal liability or responsibility for the accuracy, completeness or usefulness of any information, apparatus, product or process disclosed, or represents that its use would not infringe privately owned rights. Printed in the United States of America. Available from National Technical Information Service U. S. Department of Commerce 5285 Port Royal Road Springfield, Virginia 22151 Price: Printed Copy $ * ; Microfiche $3.00 NTIS *Pages Selling Price 1-50 $ 4.00 51-150 5.45 151-325 7.60 326-500 10.60 501-1000 13.60 ]' i"i •:'.! -n t.ed a I : he Th rd International Con i"e ronce . m I'L Sut'' •><:•e lnti ir.tcV ion ; in Controlled I-'union Devices, I'll I 1,-ibor.j lory, ' J K '', •7 Apr i I 1978- ABSTRACT The utilization of elementally-sensitive surface techniques as plasma diagnostics is discussed with emphasis on measuring impurity fluxes, charge states, and energy distributions in the plasma edge. -
Basics of Plasma Spectroscopy
Home Search Collections Journals About Contact us My IOPscience Basics of plasma spectroscopy This content has been downloaded from IOPscience. Please scroll down to see the full text. 2006 Plasma Sources Sci. Technol. 15 S137 (http://iopscience.iop.org/0963-0252/15/4/S01) View the table of contents for this issue, or go to the journal homepage for more Download details: IP Address: 198.35.1.48 This content was downloaded on 20/06/2014 at 16:07 Please note that terms and conditions apply. INSTITUTE OF PHYSICS PUBLISHING PLASMA SOURCES SCIENCE AND TECHNOLOGY Plasma Sources Sci. Technol. 15 (2006) S137–S147 doi:10.1088/0963-0252/15/4/S01 Basics of plasma spectroscopy U Fantz Max-Planck-Institut fur¨ Plasmaphysik, EURATOM Association Boltzmannstr. 2, D-85748 Garching, Germany E-mail: [email protected] Received 11 November 2005, in final form 23 March 2006 Published 6 October 2006 Online at stacks.iop.org/PSST/15/S137 Abstract These lecture notes are intended to give an introductory course on plasma spectroscopy. Focusing on emission spectroscopy, the underlying principles of atomic and molecular spectroscopy in low temperature plasmas are explained. This includes choice of the proper equipment and the calibration procedure. Based on population models, the evaluation of spectra and their information content is described. Several common diagnostic methods are presented, ready for direct application by the reader, to obtain a multitude of plasma parameters by plasma spectroscopy. 1. Introduction spectroscopy for purposes of chemical analysis are described in [11–14]. Plasma spectroscopy is one of the most established and oldest diagnostic tools in astrophysics and plasma physics 2. -
Methods Employed in Optical Emission Spectroscopy Analysis: a Review
Ingeniería y Ciencia ISSN:1794-9165 | ISSN-e: 2256-4314 ing. cienc., vol. 11, no. 21, pp. 239–267, enero-junio. 2015. http://www.eafit.edu.co/ingciencia This article is licensed under a Creative Commons Attribution 4.0 By Methods Employed in Optical Emission Spectroscopy Analysis: a Review D. M. Devia 1, L. V. Rodriguez-Restrepo 2and E. Restrepo-Parra 3 Received: 15-06-2014 | Acepted: 25-09-2014 | Onlínea: 01-30-2015 PACS: 52.25.Dg, 31.15.V- doi:10.17230/ingciencia.11.21.12 Abstract In this work, different methods employed for the analysis of emission spec- tra are presented. The proposal is to calculate the excitation temperature (Texc), electronic temperature (Te) and electron density (ne) for several plasma techniques used in the growth of thin films. Some of these tech- niques include magnetron sputtering and arc discharges. Initially, some fundamental physical principles that support the Optical Emission Spec- troscopy (OES) technique are described; then, some rules to consider dur- ing the spectral analysis to avoid ambiguities are listed. Finally, some of the more frequently used spectroscopic methods for determining the phy- sical properties of plasma are described. Key words: OES; plasma parameters; elemental determination; line intensity; broadening; shifting 1 Universidad Tecnológica de Pereira, Pereira, Colombia, [email protected]. 2 Universidad Nacional de Colombia, Sede Manizales, Colombia, [email protected] . 3 Universidad Nacional de Colombia, Sede Manizales, Colombia [email protected]. Universidad EAFIT 239j Methods Employed in Optical Emission Spectroscopy Analysis: a Review Métodos empleados en el análisis de espectroscopía óptica de emisión: una revisión Resumen En este trabajo se presentan diferentes métodos empleados para el análisis de espectros ópticos de emisión. -
10 Frontiers in Low Temperature Plasma Diagnostics Book of Abstracts
10 th Frontiers in Low Temperature Plasma Diagnostics April 28 th – May 2nd 2013 Rolduc, Kerkrade, The Netherlands Book of Abstracts We wish to express a warm welcome to all attendees to the 10 th Workshop on Frontiers in Low Temperature Plasma Diagnostics (FLTPD) in the historic Conference Centre Rolduc, Kerkrade, the Netherlands from 28 th of April to 2 nd of May. The Workshop is the continuation of a very successful biennial series that began in 1995 at Les Houches (France). It is co- organized by the Eindhoven University of Technology (TU/e) and the Dutch Institute for Fundamental Energy Research (DIFFER), two institutions which are strongly involved in the plasma physics and technology research in the Netherlands. The workshop offers the opportunity to present recent results on plasma diagnostics. The aim of the workshop is to bring together experts in the field of low temperature plasma diagnostics. It is an important and fruitful opportunity for the new generation of plasma scientists to share and discuss the knowledge of these diagnostics with the leading scientists of the field. To facilitate interaction among participants free time is scheduled on Monday and Tuesday afternoon. In line with the nine previous meetings, the program consists of expert presentations from 10 invited speakers, 16 topical speakers and 57 posters. Several companies will exhibit their products. The excursion on Wednesday is to the historical city of Aix-la-Chapelle / Aachen where a guided tour of the cathedral or the city is arranged. The conference dinner is on Wednesday evening. During the conference dinner, two prizes will be awarded for the best poster and the best oral presentation for which only students are eligible. -
Basics of Plasma Spectroscopy
Basics of Plasma Spectroscopy Hands(-)on Spectroscopy Volker Schulz-von der Gathen Institute for Experimental Physics II Chair of Physics of Reactive Plasmas Ruhr-Universität Bochum, Germany Basics of Plasma Spectroscopy | V. Schulz-von der Gathen | Int. Plasma School 2016 | Bad Honnef, October 2 2016 | 1 Disclaimer Astrophysical plasmas Atmospheric pressure plasmas He/O2 rf discharge 10 W Technical plasmas (low pressure) We confine ourselves to low-temperature plasmas. We neglect continuum radiation. We only present a very limited set of diagnostics What can we learn from the light coming out of the discharge for free? Basics of Plasma Spectroscopy | V. Schulz-von der Gathen | Int. Plasma School 2016 | Bad Honnef, October 2 2016 | 2 Outline Introduction neutrals Basics radicals atoms Emission and absorption ions plasma Atoms and molecules metastables h Detectors and spectrometers molecules electrons Equipment (Collisional radiative) models Analysis Diagnostic methods Applications: Examples Summary and conclusions Powerful diagnostic tool Basics of Plasma Spectroscopy | V. Schulz-von der Gathen | Int. Plasma School 2016 | Bad Honnef, October 2 2016 | 3 Radiation of a low temperature plasma Colors of plasmas Neutrals atoms and molecules Ions single charged Electrons ne << nn drive processes Collisions and spontaneous emission a+ e → a*+ e → a+ h ν+ e Gas discharge f s s Emission of light from the IR to the UV Basics of Plasma Spectroscopy | V. Schulz-von der Gathen | Int. Plasma School 2016 | Bad Honnef, October 2 2016 | 4 Components of a spectrum Spectral lines Continuum 26 24 22 20 18 Continuum 16 ionization limit Ar I radiation 14 2p 1 2p 2p 2p 2 3 4 2p5 2p 2p 6 7 2p8 2p9 2p10 728738 772 750795826841 696706715 764852772751801810842 12 802811 912 Lines 1s 1s2 Energy [eV] Energy 1s 3 1s5 4 10 8 104.822 6 106.666 4 2 0 3 P2,1,0 groundground level level Transitions between bound states Free-bound transitions, of atoms, ions, molecules Bremsstrahlung, … Thermal radiation Basics of Plasma Spectroscopy | V. -
Plasma Diagnostics with Langmuir Probes in Strong Magnetic Fields
Prvo srecaiye jedrskih strokovnjakov Slovenije First Meeting of the Nuclear Society of Slovenia Bovec, 11.-12.6.1992 PLASMA DIAGNOSTICS WITH LANGMUIR PROBES IN STRONG MAGNETIC FIELDS M.Stanojevič, M.Čerček, N.Jelič and T.Gyergyek J.Stefan Institute, University of Ljubljana, Jamova 39 POVZETEK - Predstavljen je teoretični model, ki opiše diagnostiko plazme z Langmuirjevo sondo v močnem magnetnem polju. Model upošteva geometrijo in obliko sonde, kar je bilo zanemarjeno v prejšnjih približnih obravnavah tega prob lema. Čeprav sonda močno zmoti plazmo in lokalno spremeni plazemsko gostoto in potencial, iz določenih delov izmerjene I-V karakteristike sonde je možno določiti nemoteno gostoto plazme, no, elektronsko temperaturo, Te, ter neznani koeficient prečne difuzije glede na smer magnetnega polja, D\. ABSTRACT - Theoretical model of plasma diagnostics with Langmuir probe in a strong magnetic field is presented. The model considers the geometry and the shape of the probe, which have been neglected in previous approximate studies of this problem. Although the plasma is strongly disturbed by the probe and plasma density and potential are locally changed, the unperturbed plasma density, no, the e electron temperature, Te, and the unknown cross-field diffusion coefficient, D lt can be determined from certain parts of the measured I-V characteristics of the probe. 1 Introduction Electrical probes or Langmuir probes are often used in plasma diagnostics be cause of their apparent simplicity (a solid object inserted into a plasma) and their easy constructing. They are also widely used in fusion devices for measuring edge plasma parameters. Langmuir probes measure electric currents which depend on their bias voltage with respect to the plasma potential. -
Studies of Electron Cyclotron Resonance Ion Source Plasma Physics
DEPARTMENT OF PHYSICS UNIVERSITY OF JYVÄSKYLÄ RESEARCH REPORT No. 8/2005 STUDIES OF ELECTRON CYCLOTRON RESONANCE ION SOURCE PLASMA PHYSICS BY OLLI TARVAINEN Academic Disser tation for the Degree of Doctor of Philosophy To be presented, by permission of the Faculty of Mathematics and Science of the University of Jyväskylä, for public examination in Auditorium FYS-1 of the University of Jyväskylä on Decenber 16, 2005 at 12 o’clock Jyväskylä, Finland December, 2005 PREFACE PREFACE The work presented in this thesis has been carried out at the JYFL Accelerator Laboratory in the University of Jyväskylä and at Argonne National Laboratory during the years 2003-2005. First, I would like to thank my supervisor Dr. Hannu Koivisto for giving me an opportunity to work in the ion source group of the JYFL Accelerator Laboratory and for his invaluable guidance and support in the course of this work. Another person who deserves my sincere gratitude is Mr. Pekka Suominen, without whom I could not have finished this thesis. I wish to thank him not only for professional help and fruitful comments but also for all the cheerful moments that we have spent together in work, free time and international conferences and summer schools. I extend my thanks to all the people working at the JYFL Accelerator Laboratory, especially my closest colleagues in cyclotron- and RADEF-groups. I am also indebted to the technical personnel of our laboratory. I have been privileged to work and share thoughts with colleagues from accelerator laboratories all over the world. I would like to thank especially the ion source people from Argonne National Laboratory and Lawrence Berkeley National Laboratory. -
Plasma Diagnostics
Plasma Diagnostics Thomas J. Dolan ASIPP, Hefei, China 2011 American Nuclear Society Speakers Bureau dolan asipp 2011 1 Topics Goals Electric Probes Magnetic Probes Passive Particle Methods Deposition Diagnostics Active Particle Methods Passive Wave Methods visible, ultraviolet, x-ray Active Wave Methods ITER diagnostics dolan asipp 2011 2 Goals of Diagnostics space-time mapping n f(vi) or Ti f(ve) or Te J, B, E Impurity concentrations Rotation velocity Plasma waves MHD instabilities Turbulence & microinstabilities Redundancy: 2-3 techniques Accuracy: a few percent. dolan asipp 2011 3 Goals of Diagnostics Resolution Tokamaks: 1 cm 0. 1 ms Inertial: 1 m 10 ps Fourier analysis of waves (, k) Improved signal-to-noise ratios Optical filters Modulation of incident beam Statistical methods of error analysis Computer graphics displays dolan asipp 2011 4 Electrical Probes dolan asipp 2011 5 Flexible Bellows for Probe Insertion from Hutchinson, 1987 dolan asipp 2011 6 Langmuir Probe Tip from Hutchinson, 1987 dolan asipp 2011 7 Langmuir Probe dolan asipp 2011 8 Langmuir Probe Data In exponential region ln(I2/I1) = e(2 –1)/kTe Te Ion saturation current Ii 1/2 1/2 -3 ni = 171.7 Ii mi /[Ape(kTe) ]m] m dolan asipp 2011 9 Electric Probes Multiple probes voltages at different points E field an d res is tiv ity. Probe disturbs the local ppplasma parameters. Double probe reduces the error. dolan asipp 2011 10 Floating Double Probe dolan asipp 2011 11 Electric Probes • Resonance probe has rf voltage applied to couple w ith p lasma waves • Fluctuations of n and f information on turbulence (k, , …) • Probe may melt if plasma temperature high • Reciprocating probes enter and leave in ms. -
Helium I Line Intensity Ratios in a Plasma for the Diagnostics of Fusion Edge Plasmas
. n n > I illif fllV NIFS—346 JP9507179 Helium I Line Intensity Ratios in a Plasma for the Diagnostics of Fusion Edge Plasmas S. Sasaki, S. Takamura, S. Masuzaki, S. Watanabe, T. Kato, K. Kadota (Received - Jan. 6, 1995 ) NIFS-346 Mar. 1995 NAGOYA, JAPAN This report was prepared as a preprint of work performed as a collaboration research of the National Institute for Fusion Science (NIFS) of Japan. This document is intended for information only and for future publication in a journal after some rearrange ments of its contents. Inquiries about copyright and reproduction should be addressed to the Research Information Center, National Institute for Fusion Science, Nagoya 464-01, Japan. Helium I line intensity ratios in a plasma for the diagnostics of fusion edge plasmas S. Sasaki * Advanced Engineering Group, Keihin Product Operations, Toshiba Corporation. Suehiro-cho. Tsurumi-ku, Yokohama 230, Japan S. Takamura, S. Masuzaki, and S. Watanabe Department of Energy Engineering and Science, Nagoya University, Nagoya 464-01. Japan T. Kato National Institute for Fusion Science, Nagoya 464-01, Japan K. Kadota Plasma Science Center, Nagoya University, Nagoya 464-01, Japan Electron temperature and density are measured, and the hot electrons in a plasma are investigated using the He I line intensity ratios in the NAGDIS- I linear device (Nagoya University Divertor Simulator) [S. Masuzaki, and S. Takamura, Jpn. J. Appl. Phys. 29, 2835, (1990).]. He I line intensity ratios have been calculated with the collisional radiative model using new atomic data allowing for the presence of hot electrons, and summarized for the electron temperature and density measurements especially for the edge or diveitor plas>mas in the fusion device. -
Langmuir Probe Diagnostics with Optical Emission Spectrometry (OES) for Coaxial Line Microwave Plasma
applied sciences Article Langmuir Probe Diagnostics with Optical Emission Spectrometry (OES) for Coaxial Line Microwave Plasma Chi Chen , Wenjie Fu * , Chaoyang Zhang , Dun Lu , Meng Han and Yang Yan School of Electronic Science and Engineering and Terahertz Science and Technology Key Laboratory of Sichuan Province, University of Electronic Science and Technology of China, Chengdu 610054, China; [email protected] (C.C.); [email protected] (C.Z.); [email protected] (D.L.); [email protected] (M.H.); [email protected] (Y.Y.) * Correspondence: [email protected] Received: 28 October 2020; Accepted: 12 November 2020; Published: 16 November 2020 Featured Application: Plasma diagnostics with a dirty Langmuir Probe. Abstract: The Langmuir probe is a feasible method to measure plasma parameters. However, as the reaction progresses in the discharged plasma, the contamination would be attached to the probe surface and lead to a higher incorrect electron temperature. Then, the electron density cannot be obtained. This paper reports a simple approach to combining the Langmuir probe and the optical emission spectrometry (OES), which can be used to obtain the electron temperature to solve this problem. Even the Langmuir probe is contaminative, the probe current–voltage (I–V) curve with the OES spectra also gives the approximate electron temperature and density. A homemade coaxial line microwave plasma source driven by a 2.45 GHz magnetron was adopted to verify this mothed, and the electron temperature and density in different pressure (40–80 Pa) and microwave power (400–800 W) were measured to verify that it is feasible.