Innovation in Design of Traditional Mashru Textile for Product Diversification
Total Page:16
File Type:pdf, Size:1020Kb
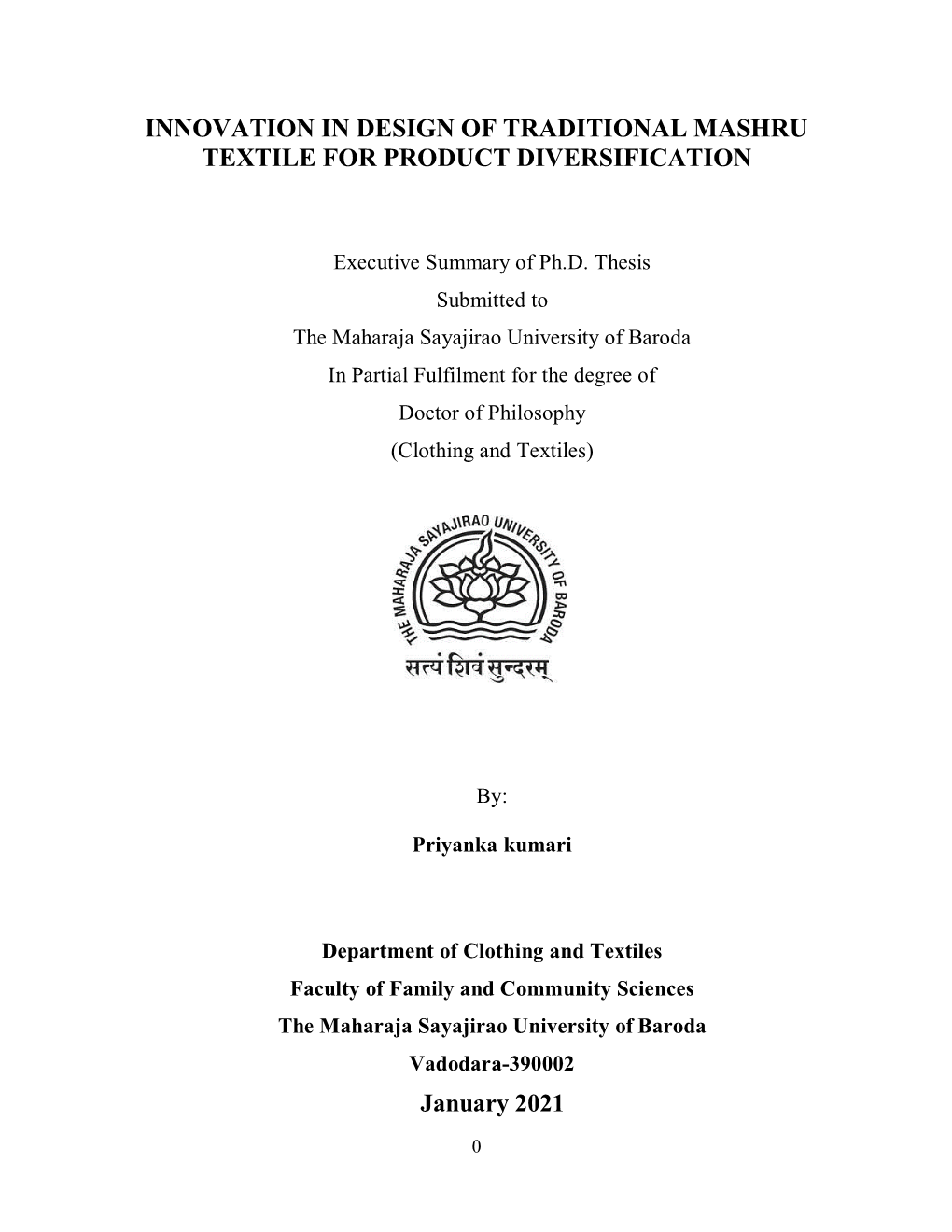
Load more
Recommended publications
-
500 Years of Filipina Fashion
500 YEARS OF FILIPINA FASHION 2020 Asian Pacific Heritage Month 500 Years of Filipina Fashion By: Charity Bagatsing Doyl Research for this presentation includes: The Boxer Codex Emma Helen Blair’s The Philippine Islands 1493-1898 William Henry Scott’s Barangay Philippine Folklife Museum Foundation The Henry Otley Beyer Library Collection Thank You Dean Cameron, DaShond Bedford and Spokane Public Library. They do not however on this account go naked, they wear well made collarless robes which reach the ankles and are of cotton bordered with colors. When they are mourning, these robes are white. They take off this robes in their houses, and in places where garments are unnecessary. But everywhere and always they are very attentive to cover their persons with great care and modesty. Wherein they are superior to other nations, especially to the Chinese.” Father Chirino - Relacion de las Islas Filipinas 1602 One of the earliest records of Philippine fashions comes from the 16th century manuscript known as the Boxer Codex. 15th century Filipinos were described to wear stylish and lavishly beaded clothing from only the best and most expensive materials available at that time. In 1591, the Chinese merchants sold over 200,000 robes of cotton and silk up and down the islands. This shopping spree caused such an alarm to the Spanish regime because chiefs and slaves wore the same extravagant silk and lavishly beaded outfits, making it impossible to judge their rank from their dress. Another concern was the exorbitant amount of money Filipinos spent on their clothes, which the colonizers maintained should go to the Spanish treasury instead of the pockets of the Chinese traders. -
DRAPE: Dressing Any Person
DRAPE: DRessing Any PErson Peng Guan1;∗ Loretta Reiss1;∗ David A. Hirshberg2;y Alexander Weiss1;∗ Michael J. Black1;2;y; z 1Dept. of Computer Science, Brown University, Providence 2Max Planck Institute for Intelligent Systems, Tubingen¨ Figure 1: DRAPE is a learned model of clothing that allows 3D human bodies of any shape to be dressed in any pose. Realistic clothing shape variation is obtained without physical simulation and dressing any body is completely automatic at run time. Abstract 1 Introduction We describe a complete system for animating realistic clothing Clothed virtual characters in varied sizes and shapes are necessary on synthetic bodies of any shape and pose without manual inter- for film, gaming, and on-line fashion applications. Dressing such vention. The key component of the method is a model of cloth- characters is a significant bottleneck, requiring manual effort to de- ing called DRAPE (DRessing Any PErson) that is learned from a sign clothing, position it on the body, and simulate its physical de- physics-based simulation of clothing on bodies of different shapes formation. DRAPE handles the problem of automatically dressing and poses. The DRAPE model has the desirable property of “fac- realistic human body shapes in clothing that fits, drapes realistically, toring” clothing deformations due to body shape from those due and moves naturally. Recent work models clothing shape and dy- to pose variation. This factorization provides an approximation to namics [de Aguiar et al. 2010; Feng et al. 2010; Wang et al. 2010] the physical clothing deformation and greatly simplifies clothing but has not focused on the problem of fitting clothes to different synthesis. -
Innovation in Design of Traditional Mashru Textiles for Product Diversification
INNOVATION IN DESIGN OF TRADITIONAL MASHRU TEXTILES FOR PRODUCT DIVERSIFICATION Synopsis of Proposed Ph. D. Thesis By Priyanka Kumari (Registration No: Fo FCSC/2/150, Dated: August 7th 2013) Guided By Prof. (Dr.) Anjali Karolia Department of Clothing and Textiles Dean Faculty of Family and Community Sciences Department of Clothing and Textiles Faculty of Family and Community Sciences The Maharaja Sayajirao University of Baroda Vadodara, Gujarat India June 2019 Endorsement from the Supervisor Ms. Priyanka Kumari has researched extensively on the topic “Innovation in Design of Traditional Mashru Textile for Product Diversification” vide registration no. FoFCSC/2/150 (Dated: 07-08-2013). She has presented her progress of work in seminars well attended by teachers and students of department. She has presented following papers: “Design intervention for handloom silk fabric of Bihar”, in International conference on Empowering Khadi and Handloom through Design Intervention Organized by Consortium of Green Fashion, an initiative of School of Fashion Technology, Pune and in association with Department of Clothing and Textiles faculty of Family and community Science The Maharaja Sayajirao University of Baroda on 30th September and 01st October 2016. “Mesmerizing Mashru Craft and Need of Geographical Indication (GI)”, in International Case Symposium on Fashion, Retail & Management Organized by Department of Fashion Management Studies–NIFT,Bhubneshwar India on 19th and 20th November 2015. She has published following papers: “Voyage of a traditional woven craft – Mashru” , in proceedings of International Textiles and Costume Congress -2015 organized by Marmara University, Istanbul , Turkey on 4th -6th November 2015 (ISBN:978-605-87108- 4-9) “Mesmerizing Mashru Craft and need of Geographical Indication (GI)” in book named “Case Handbook of Fashion, Retail and Management”, Publisher- Pragun Publication, year of publication-2018, [ISBN 978-93-80397-90-0] Ms. -
BELT RAILWAY of CHICAGO Special Instructions
BELT RAILWAY OF CHICAGO Special Instructions General Code Operating Rules 5th Edition Applies Maximum Speed A “Dimensional Load” is any load with a width of 11 Maximum speed permitted on BRC is 25 MPH feet 0 inches to 11 feet 6 inches as noted on the unless otherwise restricted. train consist. If a train has a dimensional load, the Conductor must advise the Dispatcher prior to Maximum speed must be maintained to the extent moving the train. possible, consistent with safety and efficiency. Crew members are responsible for knowing, maintaining, If a conductor has a dimensional load and has and not exceeding maximum speed for their train. received “pink message” notification of an Unnecessary delays must be avoided. excessive dimension load on another train that their Chicago Operating Rules Association (CORA) train may meet or pass, the conductor must notify Operating Guide the train dispatcher before moving the train. Employees operating in the Chicago Terminal District are required to have a current copy of the The Conductor must notify other crew members of CORA guide available for reference while on duty. the presence of both excessive dimension loads BRC Rules govern except as modified in the and dimensional loads before movement. CORA. 1.37 Maximum Gross Weight Limit 1.36 Shipments of Excessive Height / Width Maximum gross weight limitation is 143 Tons. The following classes of equipment are covered by Work equipment, cars, or platforms (other than 6 instructions from the BRC Clearance Bureau via a axle passenger cars and 6 axle locomotive cranes) “Pink Message” authority: with a gross weight greater than the route’s approved limit must not be moved over structures • Excessive dimensional loads unless authorized by the Engineering Department • Shipments including idler cars or cleared by clearance Bureau. -
Building Character the Civitas Way
Civitas The Official Magazine of Ark Academy #13 Autumn 2014 Autumn #13 Building Character the Civitas Way Building Character the Civitas Way Warm Welcome… Dear Parents, This edition of Civitas is entitled ‘Building Character the Civitas way’. How do we all build character? Well, certainly we can try and model it and we have also talked a great deal about great character traits in assemblies and tutor periods. We have focussed on resilience, integrity and gratitude. These have produced some really reflective moments. The last assembly helped us reflect on what we are grateful for, it is so easy to assume that what we have is the norm, and of course so much is not. So I am grateful to our students and staff for going that extra mile in Charity Week (marvellous moments abound but ‘Strictly’ will be forever a favourite) . I am grateful for my good health this tiring term and all the people who have supported me, and more importantly, the school. I am grateful to the teachers and support staff who step up to the plate when other staff are sick. Students who help each other and particularly help students catch up with or help understand their work. Then there is integrity or doing the right thing when no-one is watching. Please look at our ‘Good Deed Feed’, it warms the heart. There are many unsung heroes, who model what we aspire to be – good citizens, friendly, supportive, kind and life enablers. These are traits that lead for a happy life. Resilience.....aaah the Holy Grail. -
Fashion Trends 2016
Fashion Trends 2016 U.S. & U.K. Report [email protected] Intro With every query typed into a search bar, we are given a glimpse into user considerations or intentions. By compiling top searches, we are able to render a strong representation of the population and gain insight into this population’s behavior. In our second iteration of the Google Fashion Trends Report, we are excited to introduce data from multiple markets. This report focuses on apparel trends from the United States and United Kingdom to enable a better understanding of how trends spread and behaviors emerge across the two markets. We are proud to share this iteration and look forward to hearing back from you. Olivier Zimmer | Trends Data Scientist Yarden Horwitz | Trends Brand Strategist Methodology To compile a list of accurate trends within the fashion industry, we pulled top volume queries related to the apparel category and looked at their monthly volume from May 2014 to May 2016. We first removed any seasonal effect, and then measured the year-over-year growth, velocity, and acceleration for each search query. Based on these metrics, we were able to classify the queries into similar trend patterns. We then curated the most significant trends to illustrate interesting shifts in behavior. Query Deseasonalized Trend 2004 2006 2008 2010 2012 2014 Query 2016 Characteristics Part 1 Part 2 Part 3 Top Risers a Spotlight on an Extensive List and Decliners Top Trending of the Top Volume Themes Fashion Trends Trend Categories To identify top trends, we categorized past data into six different clusters based on Sustained Seasonal Rising similar behaviors. -
Textiles for Dress 1800-1920
Draft version only: not the publisher’s typeset P.A. Sykas: Textiles for dress 1800-1920 Textile fabrics are conceived by the manufacturer in terms of their material composition and processes of production, but perceived by the consumer firstly in terms of appearance and handle. Both are deeply involved in the economic and cultural issues behind the wearing of cloth: cost, quality, meaning. We must look from these several perspectives in order to understand the drivers behind the introduction of fabrics to the market, and the collective response to them in the form of fashion. A major preoccupation during our time frame was novelty. On the supply side, novelty gave a competitive edge, stimulated fashion change and accelerated the cycle of consumption. On the demand side, novelty provided pleasure, a way to get noticed, and new social signifiers. But novelty can act in contradictory ways: as an instrument for sustaining a fashion elite by facilitating costly style changes, and as an agent for breaking down fashion barriers by making elite modes more affordable. It can drive fashion both by promoting new looks, and later by acting to make those looks outmoded. During the long nineteenth century, the desire for novelty was supported by the widely accepted philosophical view of progress: that new also implied improved or more advanced, hence that novelty was a reflection of modernity. This chapter examines textiles for dress from 1800 to 1920, a period that completed the changeover from hand-craft to machine production, and through Europe’s imperial ambitions, saw the reversal of East/West trading patterns. -
Undergarments : Extension Circular 4-12-2
University of Nebraska - Lincoln DigitalCommons@University of Nebraska - Lincoln Nebraska 4-H Clubs: Historical Materials and Publications 4-H Youth Development 1951 Undergarments : Extension Circular 4-12-2 Allegra Wilkens Follow this and additional works at: https://digitalcommons.unl.edu/a4hhistory Part of the Service Learning Commons Wilkens, Allegra, "Undergarments : Extension Circular 4-12-2" (1951). Nebraska 4-H Clubs: Historical Materials and Publications. 124. https://digitalcommons.unl.edu/a4hhistory/124 This Article is brought to you for free and open access by the 4-H Youth Development at DigitalCommons@University of Nebraska - Lincoln. It has been accepted for inclusion in Nebraska 4-H Clubs: Historical Materials and Publications by an authorized administrator of DigitalCommons@University of Nebraska - Lincoln. Jan. 1951 E.G. 4-12-2 o PREPARED FOR 4-H CLOTHrNG ClUB GIRLS EXTENSION SERVICE UNIVERSITY OF NEBRASKA COLLEGE OF AGRICULTURE AND U. S. DEPARTMENT OF AGRICULTURE COOPERATING A W. V. LAMBERT, DIRECTOR C i ( Undergarments for the Well Dressed 4-H Girl Allegra Wilkens The choosing or designing of the undergarments that will make a suitable foundation for her costume is a challenge to any girl's good taste. She may have attractive under- wear if she is wise in the selection of materials and careful in making it or in choosing ready-made garments. It is not the amount of money that one spends so much as it is good judgment in the choice of styles, materials and trimmings. No matter how beautiful or appropriate a girl's outer garments may be, she is not well dressed unless she has used good judgment in making or selecting her under - wear. -
Textile Society of America Newsletter 27:2 — Fall 2015 Textile Society of America
University of Nebraska - Lincoln DigitalCommons@University of Nebraska - Lincoln Textile Society of America Newsletters Textile Society of America Fall 2015 Textile Society of America Newsletter 27:2 — Fall 2015 Textile Society of America Follow this and additional works at: https://digitalcommons.unl.edu/tsanews Part of the Art and Design Commons Textile Society of America, "Textile Society of America Newsletter 27:2 — Fall 2015" (2015). Textile Society of America Newsletters. 71. https://digitalcommons.unl.edu/tsanews/71 This Article is brought to you for free and open access by the Textile Society of America at DigitalCommons@University of Nebraska - Lincoln. It has been accepted for inclusion in Textile Society of America Newsletters by an authorized administrator of DigitalCommons@University of Nebraska - Lincoln. VOLUME 27. NUMBER 2. FALL, 2015 Cover Image: Collaborative work by Pat Hickman and David Bacharach, Luminaria, 2015, steel, animal membrane, 17” x 23” x 21”, photo by George Potanovic, Jr. page 27 Fall 2015 1 Newsletter Team BOARD OF DIRECTORS Roxane Shaughnessy Editor-in-Chief: Wendy Weiss (TSA Board Member/Director of External Relations) President Designer and Editor: Tali Weinberg (Executive Director) [email protected] Member News Editor: Ellyane Hutchinson (Website Coordinator) International Report: Dominique Cardon (International Advisor to the Board) Vita Plume Vice President/President Elect Editorial Assistance: Roxane Shaughnessy (TSA President) and Vita Plume (Vice President) [email protected] Elena Phipps Our Mission Past President [email protected] The Textile Society of America is a 501(c)3 nonprofit that provides an international forum for the exchange and dissemination of textile knowledge from artistic, cultural, economic, historic, Maleyne Syracuse political, social, and technical perspectives. -
Fashion Outfit Generation for E-Commerce Elaine M
Fashion Outfit Generation for E-commerce Elaine M. Bettaney Stephen R. Hardwick ASOS.com ASOS.com London, UK London, UK [email protected] [email protected] Odysseas Zisimopoulos Benjamin Paul Chamberlain ASOS.com ASOS.com London, UK London, UK [email protected] [email protected] ABSTRACT Combining items of clothing into an outfit is a major task in fashion retail. Recommending sets of items that are compatible with a particular seed item is useful for providing users with guidance and inspiration, but is currently a manual process that requires expert stylists and is therefore not scalable or easy to personalise. We use a multilayer neural network fed by visual and textual features to learn embeddings of items in a latent style space such that compatible items of different types are embedded close to one another. We train our model using the ASOS outfits dataset, which consists of a large number of outfits created by professional stylists and which we release to the research community. Our model shows strong performance in an offline outfit compatibility prediction task. We use our model to generate outfits and for the first time in this field perform an AB test, comparing our generated outfits to those produced by a baseline model which matches appropriate product types but uses no information on style. Users approved of outfits generated by our model 21% and 34% more frequently than those generated by the baseline model for womenswear and menswear respectively. KEYWORDS Representation learning, fashion, multi-modal deep learning 1 INTRODUCTION User needs based around outfits include answering questions such as "What trousers will go with this shirt?", "What can I wear to a Figure 1: An ASOS fashion product together with associated party?" or "Which items should I add to my wardrobe for summer?". -
Fashion Terms Style
Fashion Terms Style- particular design, shape or type of apparel item. Determined by the distinct features that create its’ overall appearance. Styles come and go. Example- a-line skirt, pencil skirt, polo shirt, sheath dress Fashion- display of the currently popular style of clothing. Favored by a large segment of the public at any time. Most accepted or up-to-date clothing. Example- skinny jeans, crop tops, ugg boots, short shorts, rompers Apparel- all men’s, women’s and children’s clothing. Example- outfits, coats Garment- one particular clothing item. Example- shirt, pants, skirt, shorts, dress Silhouette- the shape of a clothing style. They are always changing in fashion. Example- fitted, draped, poofy, skinny Fad- temporary fashion. Becomes popular fast and then dies out quickly. Can be fun if they aren’t too expensive. Example- overalls, rompers (romphims), leggings, crop tops Classic- an item that stays popular even when fashions change. Example- little black dress, black suit Fit- how tight or loose it is on the person who is wearing it. Draped garments- are wrapped or hung on the human body. Example- sari (indian), Greek inspired clothing- toga Tailored garments- made by fist cutting garment pieces and then sewing them together to fit the shape of the body. Example- suit, pants, collared buttoned-down shirt Composite garments- made by a combination of the tailored and draped methods. Example- dress with fitted bottom or top and loose bottom or top Haute couture- Custom made clothing from original designs. Highest fashions. These get copied and other cheaper companies make knock-offs. Ready-to-wear- Multiple colors and sizes of the same item are mass-produced in factories. -
Dress Codes: an Analysis of Gender in High
UNDRESSING THE DRESS CODES: AN ANALYSIS OF GENDER IN HIGH SCHOOL DRESS CODE POLICIES A Thesis Presented to the faculty of Graduate and Professional Studies in Education California State University, Sacramento Submitted in partial satisfaction of the requirements for the degree of MASTER OF ARTS in Education (Behavioral Science Gender Equity Studies) by Jaymie Arns FALL 2017 © 2017 Jaymie Arns ALL RIGHTS RESERVED ii UNDRESSING THE DRESS CODE: AN ANALYSIS OF GENDER IN HIGH SCHOOL DRESS CODE POLICIES A Thesis by Jaymie Arns Approved by: _____________________________________, Committee Chair Sherrie Carinci, Ed.D. _____________________________________, Second Reader Riana Pella, M.Ed. ______________________________ Date iii Student: Jaymie Arns I certify that this student has met the requirements for format contained in the University format manual, and that this thesis is suitable for shelving in the Library and credit is to be awarded for the thesis. __________________________, Graduate Coordinator _________________ Albert Lozano, Ph.D. Date Department of Graduate and Professional Studies in Education iv Abstract of UNDRESSING THE DRESS CODES: AN ANALYSIS OF GENDER IN HIGH SCHOOL DRESS CODE POLICIES by Jaymie Arns Statement of Problem Considered to be inherently sexual, the female body faces unique and disproportionate amounts of policing that their male peers do not (Whisner, 1982). In the educational setting, female students are required to take additional steps to ensure that they are not disrupting the learning environment at school (Glickman, 2016). These additional steps are laid out in educational policies like dress codes, which state the dress code rules, the rationales for those dress code rules, and the sanctions attached to dress code violations.