Numerical Simulation in Whole Space for Resistivity Logging Through Casing Under Approximate Conditions
Total Page:16
File Type:pdf, Size:1020Kb
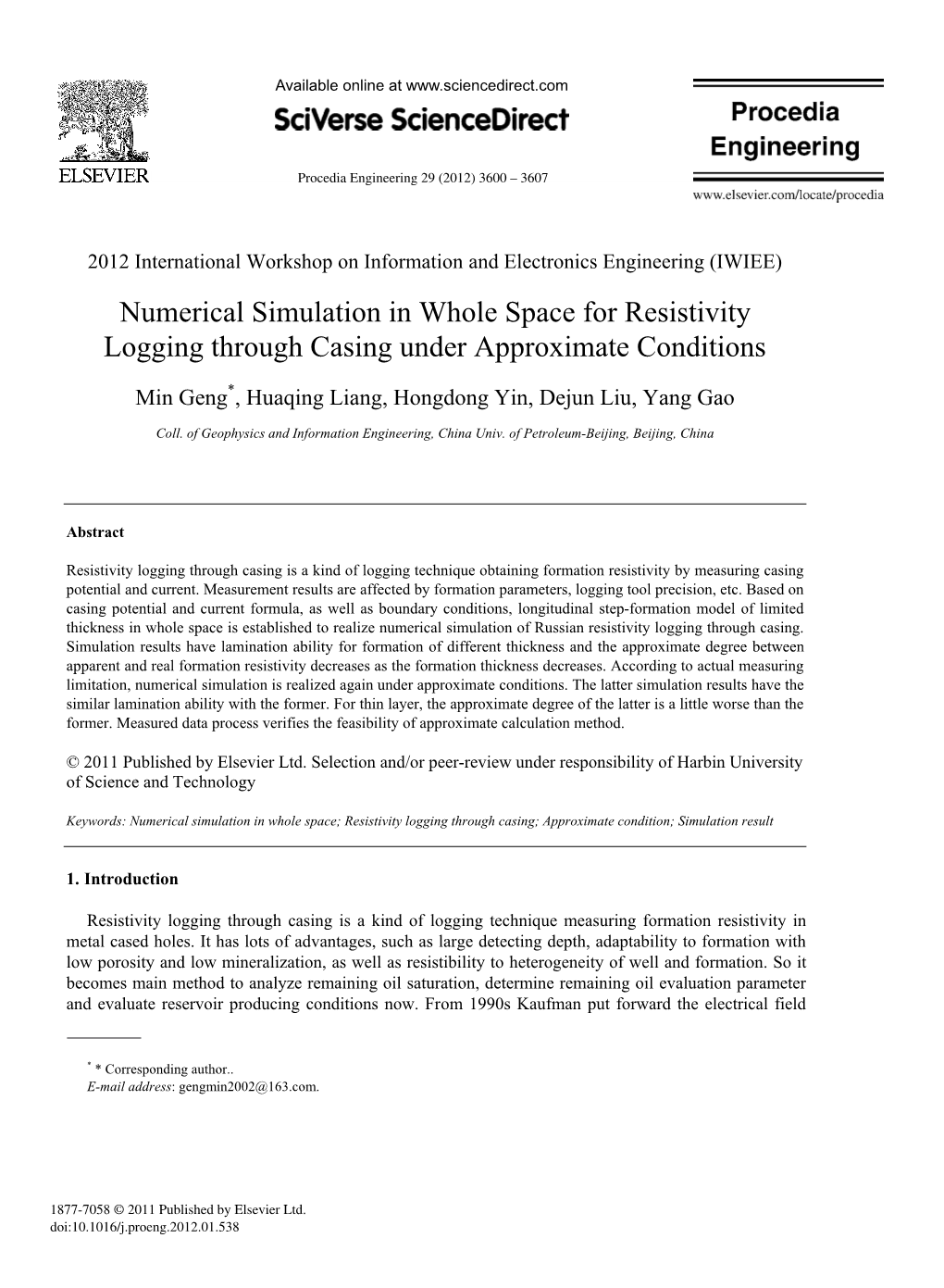
Load more
Recommended publications
-
Downhole Physical Property Logging of the Blötberget Iron Deposit, Bergslagen, Sweden Geofysisk Borrhålsloggning I Apatitjärnmalmer, Norra Bergslagen
Independent Project at the Department of Earth Sciences Självständigt arbete vid Institutionen för geovetenskaper 2017: 32 Downhole Physical Property Logging of the Blötberget Iron Deposit, Bergslagen, Sweden Geofysisk borrhålsloggning i apatitjärnmalmer, norra Bergslagen Philip Johansson DEPARTMENT OF EARTH SCIENCES INSTITUTIONEN FÖR GEOVETENSKAPER Independent Project at the Department of Earth Sciences Självständigt arbete vid Institutionen för geovetenskaper 2017: 32 Downhole Physical Property Logging of the Blötberget Iron Deposit, Bergslagen, Sweden Geofysisk borrhålsloggning i apatitjärnmalmer, norra Bergslagen Philip Johansson Copyright © Philip Johansson Published at Department of Earth Sciences, Uppsala University (www.geo.uu.se), Uppsala, 2017 Abstract Downhole Physical Property Logging of the Blötberget Iron Deposit, Bergslagen, Sweden Philip Johansson Geophysical methods are frequently applied in conjunction with exploration efforts to increase the understanding of the surveyed area. Their purpose is to determine the nature of the geophysical response of the subsurface, which can reveal the lithological and structural character. By combining geophysical measurements with the drill core data, greater clarity can be achieved about the structures and lithology of the borehole. The purpose of the project was to give the student an opportunity to discover borehole logging operations and to have a greater understanding of the local geology, in particular the iron mineralizations in the apatite iron ore intersected by the boreholes. -
Anomalies in Resistivity Logs Caused by Borehole Environment
Anomalies in Resistivity Logs Caused by Borehole Environment Ko Ko Kyi, Retired Principal Petrophysicist Resistivity logs are critical input data for petrophysical evaluation as they are used for identification of possible hydrocarbon bearing intervals, as well as determination of water saturation in reservoirs of interest. Therefore, it is important to ensure that resistivity logs are properly acquired, using appropriate type of resistivity logging tools, suitable for the borehole environment, such as hole size, type of mud, mud salinity etc., in which these tools are deployed. Generally, resistivity logging tools are divided into two main types, namely induction tools and laterolog tools. Induction resistivity tools are used in non-conductive or fresh mud and the laterolog resistivity tools are used in conductive or high salinity muds. In addition to the drilling mud, hole size also has an effect on the resistivity logging tools. Wireline logging tools are generally 3 ½ to 4 inches in diameter and are not suitable for very big holes as the mud around the tool will have significant influence on the tool response. Even Logging While Drilling (LWD) tools have limitations on the size of the hole in which they can be deployed effectively. A very saline mud inside a large borehole can have serious effects on the response of an induction logging tool. Borehole size, as well as eccentricity of the LWD resistivity tool can have deleterious effects on resistivity logs. LWD resistivity tools work on similar principle as the wireline induction resistivity tool and therefore borehole size, high salinity mud, eccentricity can cause anomalous readings of the LWD resistivity tool. -
46. Integration of Sfl and Ild Electrical Resistivity Logs During Leg 133: an Automatic Modeling Approach1
McKenzie, J.A., Davies, P.J., Palmer-Julson, A., et al, 1993 Proceedings of the Ocean Drilling Program, Scientific Results, Vol. 133 46. INTEGRATION OF SFL AND ILD ELECTRICAL RESISTIVITY LOGS DURING LEG 133: AN AUTOMATIC MODELING APPROACH1 Peter D. Jackson2 and Richard D. Jarrard3 ABSTRACT An automatic technique is developed for integrating two electrical resistivity logs obtained during Leg 133, namely, the deep induction log (ILD) and the spherically focussed log (SFL). These logs are routinely run by the Ocean Drilling Program in lower resistivity sedimentary environments, where drilling through soft, poorly consolidated lithologies often results in variable hole diameters. Examples are given to show the superior resolution of the SFL, compared to the ILD, in lithologies encountered during Leg 133, but also the degradation of the SFL response caused by variable hole conditions. A forward modeling program is used to calculate the ILD response, and a corrective scheme is developed that uses the SFL log as the starting point of an "iterative-corrective" procedure that uses, in effect, the ILD log to correct the SFL log for degradation caused by changes in the diameter of the borehole. The calculated induction log (using the corrected SFL log as the input model) is shown to be near to the ILD measured downhole. The authors consider this to be proof that the corrected SFL is a better estimate of the formation resistivity downhole (Rt) than either the SFL or ILD taken alone. Corrections are shown to be substantial in poor hole conditions, and examples are given where geological cyclicity might be confused with hole effects if uncorrected logs were to be used. -
A New Logging-While-Drilling Method for Resistivity Measurement
sensors Article A New Logging-While-Drilling Method for y Resistivity Measurement in Oil-Based Mud Yongkang Wu 1, Baoping Lu 2, Wei Zhang 2,3, Yandan Jiang 1, Baoliang Wang 1,* and Zhiyao Huang 1 1 State Key Laboratory of Industrial Control Technology, College of Control Science and Engineering, Zhejiang University, Hangzhou 310027, China; [email protected] (Y.W.); [email protected] (Y.J.); [email protected] (Z.H.) 2 Sinopec Research Institute of Petroleum Engineering, Beijing 100101, China; [email protected] (B.L.); [email protected] (W.Z.) 3 State Key Laboratory of Shale Oil and Gas Enrichment Mechanisms and Effective Development, Beijing 100101, China * Correspondence: [email protected] This paper is an extended version of an earlier conference paper: “Wu, Y.K.; Ni, W.N.; Li, X.; Zhang, W.; y Wang, B.L.; Jiang, Y.D. and Huang, Z.Y. Research on characteristics of a new oil-based logging-while-drilling instrument. In Proceedings of the 11th International Symposium on Measurement Techniques for Multiphase Flow, Zhenjiang, China, 3–7 November 2019.” Received: 21 December 2019; Accepted: 11 February 2020; Published: 16 February 2020 Abstract: Resistivity logging is an important technique for identifying and estimating reservoirs. Oil-based mud (OBM) can improve drilling efficiency and decrease operation risks, and has been widely used in the well logging field. However, the non-conductive OBM makes the traditional logging-while-drilling (LWD) method with low frequency ineffective. In this work, a new oil-based LWD method is proposed by combining the capacitively coupled contactless conductivity detection (C4D) technique and the inductive coupling principle. -
Thermochemical Oxidation of Methane Induced by High-Valence Metal Oxides in a Sedimentary Basin
ARTICLE DOI: 10.1038/s41467-018-07267-x OPEN Thermochemical oxidation of methane induced by high-valence metal oxides in a sedimentary basin Wen-Xuan Hu1, Xun Kang1, Jian Cao1, Xiao-Lin Wang1, Bin Fu2 & Hai-Guang Wu1 Thermochemical oxidation of methane (TOM) by high-valence metal oxides in geological systems and its potential role as a methane sink remain poorly understood. Here we present evidence of TOM induced by high-valence metal oxides in the Junggar Basin, located in 1234567890():,; northwestern China. During diagenesis, methane from deeper source strata is abiotically 13 oxidized by high-valence Mn(Fe) oxides at 90 to 135 °C, releasing C-depleted CO2, soluble Mn2+ and Fe2+. Mn generally plays the dominant role compared to Fe, due to its lower Gibbs free energy increment during oxidation. Both CO2 and metal ions are then incorporated into authigenic calcites, which are characterized by extremely negative δ13C values (−70 to −22.5‰) and high Mn content (average MnO = 5 wt.%). We estimate that as much as 1224 Tg of methane could be oxidized in the study area. TOM is unfavorable for gas accumulation but may act as a major methane sink in the deep crustal carbon cycle. 1 State Key Laboratory for Mineral Deposits Research, School of Earth Sciences and Engineering, Nanjing University, Nanjing 210023, China. 2 Research School of Earth Science, The Australian National University, Canberra ACT 0200, Australia. These authors contributed equally: Wen-Xuan Hu, Xun Kang. Correspondence and requests for materials should be addressed to W.-X.H. (email: [email protected]) or to X.K. -
Borehole Logging Techniques Applied to Base Metal Ore Deposits; !!3: Geophysics and Geochemistry in the Search for Metallic Ores; Peter J
12. BORLHOlE lOGGING TECHNIQUES APPLIED TO BASE MLTAL ORE DEPOSITS W.E. Glenn UURI-I arth Science laboratory, Salt lake City, Utah P.H. Nelson lawrence Berkeley laboratory, Berkeley, California Glenn, W.E. and Nelson, P.ll., Borehole logging techniques applied to base metal ore deposits; !!3: Geophysics and Geochemistry in the Search for Metallic Ores; Peter J. Hood, editor, Geological Survey of Canada, Economic Geology Report 31, p. 273-294, 1979. Abstract Interest in the application of borehole logging to metallic mineral exploration and deposit evaluation has grown substantially in recent years. However, borehole logging tools and techniques were developed primarily by the petroleum industry and neither the tools nor their application are directly suited to the needs of the metallic mineral industry. Lack of generally available commercial logging services for small diameter holes and for the measurement of quantities Kuch as magnetic susceptibility, induced polarization, and ore grade has inhibiLed the growth of borehole logging in metallic mineral mining. The need to study new mining technology and to search at greater depths for new ore deposits has created a demand for a slim-hole logging capability. The requirements range from elemental and mineralogical analyses, through properties used in geophysical exploration to bulk rock properties for either conventional or novel mining techniques. This paper reviews the presently available capabilities for downhole analyses for geological information, for geophysical properties and for fluid flow. Much of the review is based upon direct experience with a facility operated in-house by a major metals mining company. Resume n y a eu au cours des dernU~res annees un interet croissant pour l'application de la diagraphie par trou de sonde a l'exploration des mineraux metalliques et a l'evaluation des giKements. -
Borehole Logging and Slug Tests for Evaluating the Applicability of Electrical Resistivity Tomography for Groundwater Exploration in Nampula Complex, Mozambique
water Article Borehole Logging and Slug Tests for Evaluating the Applicability of Electrical Resistivity Tomography for Groundwater Exploration in Nampula Complex, Mozambique Farisse Chirindja 1,2,*, Jan-Erik Rosberg 1 and Torleif Dahlin 1 1 Engineering Geology, Lund University, Box 118, S-221 00 Lund, Sweden; [email protected] (J.-E.R.); [email protected] (T.D.) 2 Geology Department, Eduardo Mondlane University, Av. Mozambique km 1.5, P.O. Box 273, Maputo, Mozambique * Correspondence: [email protected]; Tel.: +46-72-871-9300 Academic Editors: Arjen Y. Hoekstra and Trevor Elliot Received: 8 December 2016; Accepted: 3 February 2017; Published: 8 February 2017 Abstract: In Nampula province, Mozambique, there is a high number of water wells considered as having failed for having too low a pumping yield. Two Electrical Resistivity Tomography (ERT) measurement campaigns were conducted in the area for evaluating the reasons of failures. However, in some cases it was difficult to verify and interpret the ERT results by only using the inadequate lithological description presented in drilling reports. In this paper the integration of borehole logging and slug testing is presented as a solution to add more information and to enhance the interpretation of ERT models. The borehole logging tool measured resistivity, magnetic susceptibility and natural gamma. The logging results proved that the ERT models are accurate in estimating the resistivity for basement (>1400 Wm), fractured layer (220–1400 Wm), semi-weathered layer with clay accumulation (10–220 Wm), and weathered and leached layer (220–2700 Wm). The slug testing gave results of high hydraulic conductivity (K) values where the ERT indicates well-developed weathered and fractured layers, and low K values where these are less developed. -
Formation Factor Logging In-Situ by Electrical Methods. Background And
Technical Report TR-02-27 Formation factor logging in-situ by electrical methods Background and methodology Martin Löfgren, Ivars Neretnieks Department of Chemical Engineering and Technology, Royal Institute of Technology October 2002 Svensk Kärnbränslehantering AB Swedish Nuclear Fuel and Waste Management Co Box 5864 SE-102 40 Stockholm Sweden Tel 08-459 84 00 +46 8 459 84 00 Fax 08-661 57 19 +46 8 661 57 19 Formation factor logging in-situ by electrical methods Background and methodology Martin Löfgren, Ivars Neretnieks Department of Chemical Engineering and Technology, Royal Institute of Technology October 2002 Keywords: Matrix diffusion, Formation factor, In-Situ, Geophysical logging, KLX02 This report concerns a study which was conducted for SKB. The conclusions and viewpoints presented in the report are those of the author(s) and do not necessarily coincide with those of the client. Abstract Matrix diffusion has been identified as one of the most important mechanisms governing the retardation of radionuclides escaping from a deep geological repository for nuclear waste. Radionuclides dissolved in groundwater flowing in water-bearing fractures will diffuse into water filled micropores in the rock. Important parameters governing the matrix diffusion are the formation factor, the surface diffusion and sorption. This report focuses on the formation factor in undisturbed intrusive igneous rock and the possibility of measuring this parameter in-situ. The background to and the methodology of formation factor logging in-situ by electrical methods are given. The formation factor is here defined as a parameter only depending on the geometry of the porous system and not on the diffusing specie. -
Jfes Symposium
The 20th Formation Evaluation Symposium of Japan, October 1 - 2, 2014 ARE THE LWD RESISTIVITY LOGS TELLING THE WHOLE STORY? Ko Ko Kyi and Nur Fatihah M Zulkifli PETRONAS Carigali Sdn. Bhd. This paper was selected for presentation by a JFES program committee following the whole process of Exploration and Production cycle review of an abstract submitted by the author(s). are numerous, starting from being used as a tool to correlate between wells all the way up to hydrocarbon ABSTRACT resource assessment. One of the main uses of resistivity logs is formation fluid identification and differentiation Resistivity logs are crucial data in formation evaluation, between hydrocarbon bearing zones and water bearing as they are used to compute water saturation, an input intervals. This is based on the profile and motif of the parameter for hydrocarbon resource assessment. resistivity logs, by making use of many resistivity logs Therefore, it is important that these logs are reliably and with different depths of investigation. Therefore, it is accurately measured. Resistivity logs are acquired by important that resistivity logs are properly recorded with logging tools usually conveyed either by electric wireline diligent calibration procedure being implemented for the or Logging While Drilling LWD equipment. These resistivity logging tools. The resistivity logs also need to measured resistivity logs need to be corrected for various be corrected for borehole and environmental effects, such borehole, environmental and other effects to derive the as bed thickness corrections, shoulder bed corrections, true formation resistivity. Wireline conveyed resistivity invasion corrections etc. tools are usually run in wells under static condition, where the mud invasion process has virtually ended. -
Download Article
4th International Conference on Machinery, Materials and Computing Technology (ICMMCT 2016) Research on Technology of Azimuthal Electromagnetic Wave Resistivity logging While Drilling and Its Application in Geosteering Hexin Li 1,a, Yongshou DAI 1 , Weining Ni 2 , Weifeng Sun 1 , Ligang Li 1 , Xiaobin Zhang 1 1 School of Information and Control Engineering, China University of Petroleum, Qingdao 266580, China; 2 SINOPEC Research Institute of Petroleum Engineering, Beijing100101, China. [email protected] Keywords: electromagnetic wave resistivity, geosteering, orientation imaging, MWD. Abstract. With the number of old oil fields exploited by horizontal well increased, the complexity and difficulty to extract oil from reservoir geology promote the further development of logging while drilling (LWD) technology. Thus, the LWD technology develops from the initial no-directional shallow measurements to current deep directional measurements. Based on electromagnetic wave propagation theory, electromagnetic wave resistivity logging while drilling technology is adopted to capture the resistivity from formation in real time. According to the polarization angles phenomena of resistivity curve, formation boundary can be detected. On the basis of conventional electromagnetic wave resistivity LWD, Schlumberger, Halliburton, Baker Hughes and GWDC have already carried out the research on azimuthal electromagnetic wave resistivity LWD measurement, and developed different kinds of azimuthal resistivity tools respectively, which can reflect the formation properties through 360° real-time orientation imaging technology directly. In this paper, the operating principles and characteristics of four different kinds of azimuthal resistivity tools are introduced in detail, which helps to point out the research direction on technology of azimuthal electromagnetic wave resistivity logging while drilling and application in geosteering in future. -
Practical Borehole Logging Procedures for Mineral Exploration, with Emphasis on Uranium
TECHNICAL REPORTSSERIES No. 259 Practical Borehole Logging Procedures for Mineral Exploration, with Emphasis on Uranium i % \ J INTERNATIONAL ATOMIC ENERGY AGENCY, VIENNA, 1986 PRACTICAL BOREHOLE LOGGING PROCEDURES FOR MINERAL EXPLORATION, WITH EMPHASIS ON URANIUM The following States are Members of the International Atomic Energy Agency: AFGHANISTAN GUATEMALA PARAGUAY ALBANIA HAITI PERU ALGERIA HOLY SEE PHILIPPINES ARGENTINA HUNGARY POLAND AUSTRALIA ICELAND PORTUGAL AUSTRIA INDIA QATAR BANGLADESH INDONESIA ROMANIA BELGIUM IRAN, ISLAMIC REPUBLIC OF SAUDI ARABIA BOLIVIA IRAQ SENEGAL BRAZIL IRELAND SIERRA LEONE BULGARIA ISRAEL SINGAPORE BURMA ITALY SOUTH AFRICA BYELORUSSIAN SOVIET JAMAICA SPAIN SOCIALIST REPUBLIC JAPAN SRI LANKA CAMEROON JORDAN SUDAN CANADA KENYA SWEDEN CHILE KOREA, REPUBLIC OF SWITZERLAND CHINA KUWAIT SYRIAN ARAB REPUBLIC COLOMBIA LEBANON THAILAND COSTA RICA LIBERIA TUNISIA COTE D'IVOIRE LIBYAN ARAB JAMAHIRIYA TURKEY CUBA LIECHTENSTEIN UGANDA CYPRUS LUXEMBOURG UKRAINIAN SOVIET SOCIALIST CZECHOSLOVAKIA MADAGASCAR REPUBLIC DEMOCRATIC KAMPUCHEA MALAYSIA UNION OF SOVIET SOCIALIST DEMOCRATIC PEOPLE'S MALI REPUBLICS REPUBLIC OF KOREA MAURITIUS UNITED ARAB EMIRATES DENMARK MEXICO UNITED KINGDOM OF GREAT DOMINICAN REPUBLIC MONACO BRITAIN AND NORTHERN ECUADOR MONGOLIA IRELAND EGYPT MOROCCO UNITED REPUBLIC OF EL SALVADOR NAMIBIA TANZANIA ETHIOPIA NETHERLANDS UNITED STATES OF AMERICA FINLAND NEW ZEALAND URUGUAY FRANCE NICARAGUA VENEZUELA GABON NIGER VIET NAM GERMAN DEMOCRATIC REPUBLIC NIGERIA YUGOSLAVIA GERMANY, FEDERAL REPUBLIC OF NORWAY ZAIRE GHANA PAKISTAN ZAMBIA GREECE PANAMA The Agency's Statute was approved on 23 October 1956 by the Conference on the Statute of the IAEA held at United Nations Headquarters, New York; it entered into force on 29 July 1957. The Headquarters of the Agency are situated in Vienna. Its principal objective is "to accelerate and enlarge the contribution of atomic energy to peace, health and prosperity throughout the world". -
Using Geophysical Logs to Estimate Porosity, ^Vater Resistivity, and Intrinsic Permeability
Using Geophysical Logs to Estimate Porosity, ^Vater Resistivity, and Intrinsic Permeability United States Geological Survey Water-Supply Paper 2321 Using Geophysical Logs to Estimate Porosity, Water Resistivity, and Intrinsic Permeability By DONALD G. JORGENSEN U.S. GEOLOGICAL SURVEY WATER-SUPPLY PAPER 2321 DEPARTMENT OF THE INTERIOR DONALD PAUL MODEL, Secretary U.S. GEOLOGICAL SURVEY Dallas L. Peck, Director Any use of trade, product, industry, or firm names in this publication is for descriptive purposes only and does not imply endorsement by the U.S. Government. UNITED STATES GOVERNMENT PRINTING OFFICE: 1989 For sale by the Books and Open-File Reports Section U.S. Geological Survey Federal Center Box 25425 Denver, CO 80225 Library of Congress Cataloging-in-Publication Data Jorgensen, Donald G. Using geophysical logs to estimate porosity, water resistivity, and intrinsic permeability. (U.S. Geological Survey Water-Supply Paper; 2321) Bibliography: p. Supt. of Docs, no.: I 19.13:2321 1. Water, Underground Methodology. 2. Geophysical well logging. 3. Porosity Measurement. 4. Groundwater flow Measurement. 5. Rocks Permeability Measurement. I. Title. II. Series. GB1001.72.G44J67 1988 622'.187 87-600025 CONTENTS Nomenclature IV Conversion factors V Abstract 1 Introduction 1 Estimating porosity and lithology 2 Estimating water resistivity 4 Qualitative methods 4 Spontaneous-potential method 4 Cross-plot method 7 Estimating permeability 11 Background and research 11 Cross-plot method 17 Summary 19 References cited 20 Appendixes: A. Estimating dissolved-solids concentration 22 B. Estimating sodium-chloride concentration 22 C. Estimating density 22 D. Estimating viscosity 24 FIGURES 1. Dual-porosity, gamma-ray, and caliper logs 3 2.