Emission Factor Documentation for AP-42 Section 12.5, Steel Minimills
Total Page:16
File Type:pdf, Size:1020Kb
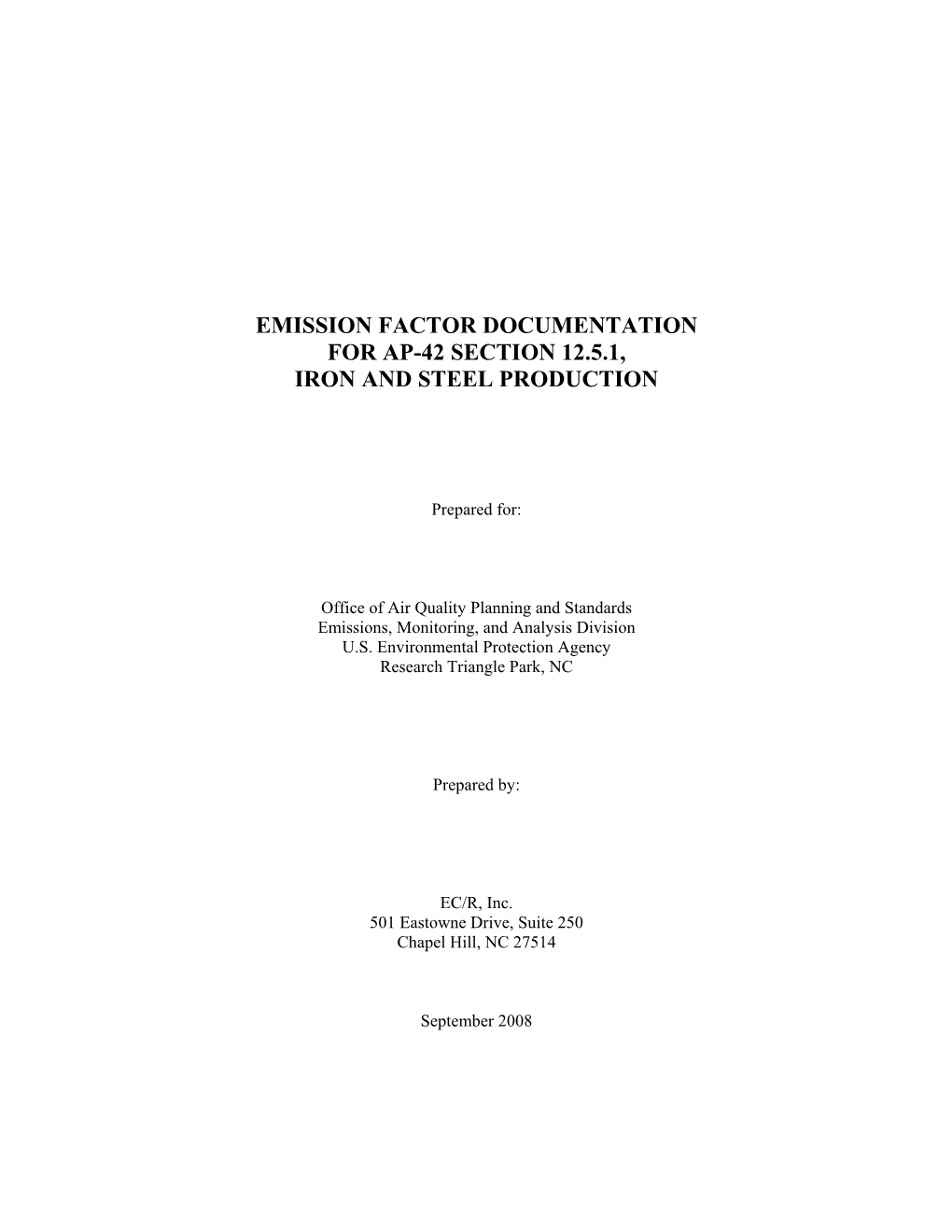
Load more
Recommended publications
-
United States Patent [151 3,659,831 Reber Et Al
United States Patent [151 3,659,831 Reber et al. [451 May 2, 1972 [54] INTEGRAL QUENCH FURNACE AND 2,681,136 6/1954 lpsen .................................... ..266/4 R TRANSFER MECHANISM 2,747,855 5/1956 lpsen . ..266/4 R [72] Inventors: Russell H. Reber, Orange; Harold E. 2,965,369 12/1960 Acker et al .......... ..266/4 R Mescher, Pico Rivera, both of Calif. 3,381,947 5/1968 Beggs . ..266/4 R 3,410,547 11/1968 Bielefeldt... .....266/5 R [73] Assignee: Paci?c Scientific Company, City of Com 3,441,452 4/1969 Westeren ............................. ..266/4 R merce, Calif. FOREIGN PATENTS OR APPLICATIONS [22] Filed: Aug. 25, 1969 987,910 8/1951 France ................................. ..266/4 R [21] Appl.N0.: 852,671 Primary Examiner—-Gerald A. Dost Atrorney—-Fowler, Knobbe & Martens [52] U.S.Cl. ........................... ..266/4A,148/153,214/18R, 214/26 [57] ABSTRACT [51] im. Cl. .................................................. ..C21d1/66 [58] Field ofSearch ........... ..148/153, 155; 214/18 R, 23-26, An integral quench furnace system and transfer mechanism 214/32; 266/4 R, 4 A, 4 B, 6 R for removing a heat treated charge from the furnace chamber into the quench media and onto an unloading platform. The [56] References Cited transfer mechanism includes a forked loading cart mounted on the quench chamber A-frame for movement into the fur UNITED STATES PATENTS nace and onto the unloading platform through a hydraulic motor driven chain and sprocket arrangement, 1,840,327 1/1932 Paulsen ................... ............ ..214/26 1,848,898 3/1932 McFarland ............................ ..2l4/26 22 Claims, 13 Drawing Figures Patented May 2, 1972 3,659,831 i0 Sheets-Sheet l INVENTORS. -
Design and Implementation of Energy Saving Control and Regulation System for Metallurgical Furnace
Design and Implementation of Energy Saving Control and Regulation System for Metallurgical Furnace ShuWen Chen, YongShen Chen, and WeiWei Guo { [email protected]} School of materials and metallurgy University of Science and Technology Liaoning Anshan 114051, China Abstract. This paper from the perspective of saving fuel gas, reasonable design of temperature control system. The thermostat is designed S7-200 series PLC adoption. The communication method of the computer and programmable controller (PLC) temperature control system is described. Software part of the application of the PLC principle to achieve system control. Hardware part of the temperature sensing element thermocouple temperature field, flow meter, fuel flow regulation, adjusting the thermocouple output electrical signal supply line for comparison with the given values, if there is a difference, the difference through the operational amplifier and issued a directive to the actuator, the actuator to perform the task. The simulation interface of the application configuration, virtual reality condition, the master-slave real-time monitoring system composed of computer and PLC to give full play to the their respective advantages in the industrial control, realize the decentralized control and centralized monitoring and other new features. Write part of the program, to research on energy efficient and reasonable utilization as the theme, combined with typical furnace, energy for metallurgical furnace the huge energy consumption equipment rational utilization and effective control method is put forward to improve the reasonable design of the program, resulting in applications get effective implementation, for enterprises to save energy, create economic benefits to contribute. Keywords: PLC; control; computer; configuration technology. 1 Introduction So far the majority of domestic metallurgical furnace is built in the last century, the control system configuration has been outdated. -
Method for the Transport of Sponge Iron Verfahren Zum Transportieren Von Eisenschwamm Procede De Transport D'eponge De Fer
Europaisches Patentamt (19) European Patent Office Office europeenpeen des brevets EP 0 515 744 B1 (12) EUROPEAN PATENT SPECIFICATION (45) Date of publication and mention (51) intci.6: C21B 13/00, B65G 53/06 of the grant of the patent: 29.04.1998 Bulletin 1998/18 (21) Application number: 91304911.0 (22) Date of filing: 30.05.1991 (54) Method for the transport of sponge iron Verfahren zum Transportieren von Eisenschwamm Procede de transport d'eponge de fer (84) Designated Contracting States: • Flores-Verdugo, Marco Aurelio AT DE ES FR IT SE Monterrey, Nuevo Leon (MX) • Garza- Ondarza, Jose Javier (43) Date of publication of application: San Nicolas de los Garza, Nuevo Leon (MX) 02.12.1992 Bulletin 1992/49 (74) Representative: Garratt, Peter Douglas et al (73) Proprietor: HYLSA, S.A. de C.V. Mathys & Squire Monterrey Nuevo Leon (MX) 100 Grays Inn Road London WC1X8AL (GB) (72) Inventors: • Becerra-Nova, Jorge Octavio (56) References cited: Apodaca, Nuevo Leon (MX) EP-A- 0 021 222 DE-A- 3 201 608 • Viramontes-Brown, Ricardo Garza Garcia, Nuevo Leon (MX) DO ^> Is- lo Note: Within nine months from the publication of the mention of the grant of the European patent, any person may give notice the Patent Office of the Notice of shall be filed in o to European opposition to European patent granted. opposition a written reasoned statement. It shall not be deemed to have been filed until the opposition fee has been paid. (Art. a. 99(1) European Patent Convention). LU Printed by Jouve, 75001 PARIS (FR) EP 0 515 744 B1 Description The present invention relates to a method applicable in the production of iron and steel, wherein a direct reduction process is employed to produce an intermediate product in the form of a particulate solid, commonly known as sponge 5 iron or Direct Reduced Iron (DRI). -
Blast Furnace
Blast furnace From Wikipedia, the free encyclopedia Jump to: navigation, search Blast furnace in Sestao, Spain. The actual furnace itself is inside the centre girderwork. A blast furnace is a type of metallurgical furnace used for smelting to produce metals, generally iron. In a blast furnace, fuel and ore are continuously supplied through the top of the furnace, while air (sometimes with oxygen enrichment) is blown into the bottom of the chamber, so that the chemical reactions take place throughout the furnace as the material moves downward. The end products are usually molten metal and slag phases tapped from the bottom, and flue gases exiting from the top of the furnace. Blast furnaces are to be contrasted with air furnaces (such as reverberatory furnaces), which were naturally aspirated, usually by the convection of hot gases in a chimney flue. According to this broad definition, bloomeries for iron, blowing houses for tin, and smelt mills for lead, would be classified as blast furnaces. However, the term has usually been limited to those used for smelting iron ore to produce pig iron, an intermediate material used in the production of commercial iron and steel. Contents [hide] • 1 History o 1.1 China o 1.2 Ancient World elsewhere o 1.3 Medieval Europe o 1.4 Early modern blast furnaces: origin and spread o 1.5 Coke blast furnaces o 1.6 Modern furnaces • 2 Modern process • 3 Chemistry • 4 See also • 5 References o 5.1 Notes o 5.2 Bibliography • 6 External links [edit] History Blast furnaces existed in China from about the 5th century BC, and in the West from the High Middle Ages. -
High Speed Infra Red Furnace
International Journal of Modern Engineering Research (IJMER) www.ijmer.com Vol. 3, Issue. 5, Sep - Oct. 2013 pp-2962-2970 ISSN: 2249-6645 High Speed Infra Red Furnace 1, Mr.Amalorpava Dass. J, 2, Mr.Mohanraj.N 3, Mr. Senthil Vel.C, Mr.Gugan raja.PL) 1.Asst.Professor Aalim Muhammed Salegh College of Engineering,IAF, Avadi, Chennai-600055, 2..Asst.Professor Sri Krishna College of Technology, Covaipudur, Coimbatore-641042. 3. Asst.Professor Aalim Muhammed Salegh College of Engineering,IAF, Avadi, Chennai-600055, 4. Lecturer, VKS College of engineering and technology, desiyamangalam, kulithalai,karur-639120. ABSTRACT This project is designed to improve Electrical versus Thermal efficiency. Nowadays electrical heating system converts 65% of the electrical power into thermal power. We have introduced infrared penetration heating system to improve efficiency up to 95% thermal efficiency and 100% electrical efficiency. We are going to construct a furnace model to improve our system. A real fabrication model is to analyze IR heating system. The capacity of infrared lamps used inside the furnace will be about 500watts. IR lamps will be used to provide heat. From the furnace, the temperature is sensed by the thermocouple, which is based on the principle of Seeback effect. The function of a thermocouple is to convert heat energy to mill voltage and it is fed to a signal conditioner to improve the sensitivity and also to improve the non-linear Property of thermocouple. Temperature acquired from the thermocouple is indicated on the screen of the computer. The computer will also compare the temperature acquired with the set temperature and control action if any will be done by the solid-state relay that avoids instantaneous heating. -
A Review of Steelmaking Technologies
International Journal of Science and Research (IJSR) ISSN (Online): 2319-7064 Index Copernicus Value (2013): 6.14 | Impact Factor (2014): 5.611 A Review of Steelmaking Technologies Sudipto Shekhor Mondol Department of Mechanical Engineering, Heritage Institute of Technology Abstract: Steelmaking is the method of developing steel from iron ore (usually haematite) and scrap. The impurities such as nitrogen, sulphur, silicon, phosphorus and excess carbon are separated out from the raw iron and alloying elements such as nickel, manganese, vanadium, molybdenum and chromium are added to impart different properties to steel. The technology of steelmaking has made great advancements with time. This paper describes the modern technologies used in a steel plant while reviewing the conventional processes as well. Keywords: Steelmaking, Steel, Blast furnace, Open hearth furnace, Darva glass 1. Introduction 2.2 Limestone Steel is one of the strongest materials on earth. It has Rocks are blasted and the stones are transported to thesteel changed the course of our history, shaping our civilisation industry. and the way we live. But today scientists are reengineering steel’s molecular structure creating new forms with the 2.3 Coke potential to build higher, further and stronger than the World has ever seen. Steel is an alloy of iron and carbon. It is the Bituminous or soft coal is converted into coke. This takes world’s most useful and inexpensive metal. Steel is made of the place of charcoal previously used as fuel. The coal is crystals and the dislocations inside the crystals helps to first crushed and then heated in ovens until the moisture and deform. -
INVENTOR Sweezy Aaro?Ez-Maess by 22
Nov. 21, 1939. H. J. NESS 2,181,093 HEAT TREATMENT OF METALS Filed Jan. 26, 1938 MM 1// M 1. 11221,MM-77 1222 / / / / / /27 / /2222277/2 / / / / / / / / / 2.7/ / /- /, ., ,. ,. M2 2 2.M& N NSy 70 A/A A/yd 6AS INVENTOR sweezy Aaro?ez-MAess BY 22. --Cee ATAORNEY | Patented Nov. 21, 1939 2,181,093 UNITED STATES PATENT office 2,181,093 EEAT TREAMNT OF METALS arold J. Ness, Bloomfield, N.J., assignor to Nes alloy Products, inc., New York, N. Y., a corpool ration of New Jersey Application January 26, 1938, serial No. 186,941 2 Claims. (C. 148-16) This invention relates to the metallurgy of both surface of the part and may be discovered only ferrous and non-ferrous metals and more particul on failure of the part in use. Similar decarburi larly to the provision of an atmosphere for the zation and scaling problems arise in the reheating heating and heat treatment of such metals for of billets and the heating of bars, wire bars and 5 mechanical working, normalizing, hardening, etc. slabs for rolling, piercing, as in tube making, in This application is a continuation in part of the SOaking of steel ingots, and in the heat treat my applications Serial No. 67,547, fled March 6, ment of finished or partially finished parts for 1936, and entitled "Metallurgical process and ap hardening, normalizing, etc. Troublesome oxide paratus', Serial No. 79,968, filed May 15, 1936, formations also Occur in the heating and heat 0. and entitled 'Metallurgical process', and Serial treatment of such metals as brass, copper and 0 No. -
Selected Aspects of Metallurgical and Foundry Furnace Dust Utilization
Polish J. of Environ. Stud. Vol. 20, No. 1 (2011), 101-105 Original Research Selected Aspects of Metallurgical and Foundry Furnace Dust Utilization Jan Jezierski*, Krzysztof Janerka** Department of Foundry, Silesian University of Technology, Towarowa 7, 44-100 Gliwice, Poland Received: 26 March 2010 Accepted: 9 June 2010 Abstract One of the biggest problems in the metallurgical and foundry industries is the large quantity of dust gen- erated during production processes. The most important is furnace dust created when the molten metal is pre- pared and subsequently sucked out by the dust removal system. At the Department of Foundry, experiments using the pneumatic injection method were carried out to utilize these kinds of materials and some results were successfully introduced into industrial applications. The results of dust injection into cupola and metallurgical EAFs (for slag foaming) were presented in this paper. The ideas behind the industrial set-ups, the process para- meters, and the results obtained are described. The paper proves that pneumatic the injection technique could and should be continuously considered as an effective method for waste dust utilization. Keywords: pneumatic powder injection, waste utilization, metallurgical furnace, furnace dust, powder injection lance Introduction A total of 20 kg of dust per ton of steel is produced which, according to reports [1, 2, 6], results in millions of tons of Almost every metallurgical process generates a large dust created annually. A similar problem, although on a quantity of various kinds of waste. Major pollution released smaller scale, exists in foundry plants for casting alloy into the atmosphere during the steel making process melting processes and, according to [7], one type of includes solid particles (dust), carbon (II) oxide, nitrogen foundry (cast iron) is considered in reports to produce 750- oxides, and some volatile organic compounds. -
Utilization of Slags from Foundry Process
Journal of Casting & Materials Engineering Vol. 1 No. 4 (2017 103–109 http://dx.doi.org/10.7494/jcme.2017.1.4.103 ) Utilization of Slags from Foundry Process Alena Pribulováa*, Peter Futáša, Marianna Bartošováa, Jozef Petríka aTechnical University of Košice, Faculty of Materials, Metallurgy and Recycling, Letná 9, Košice, Slovakia *e-mail: [email protected] Received: 10 October 2017/Accepted: 10 December 2017/Published online: 31 January 2018 This article is published with open access at AGH University of Science and Technology Abstract The melting of steel or cast iron is one step of the foundry process. The foundry industry uses different types of furnac- es, and metallurgical slags are products of the pyrometallurgical processes defecting in these furnaces. Furnace slag is a non-metallic by-product that consists primarily of silicates, alumina silicates, and calcium-alumina-silicates. As a by-prod- uct of the melting process, furnace slags vary considerably in form depending on the melted metal furnace types, and slag cooling method used. Most quantity of slags from the foundry processes are created in a cupola furnace that is used for cast iron production. An electric arc furnace is usually used for steel production, but it can be used for cast iron production as well. Universal use features an electric induction furnace. Slags from the melting processes in a foundry can be in the form of gravel, or the slag from a cupola furnace can be granulated. The utilization of slags from foundry processes is very delimited in Slovakia because of their quantity. This article deals with the possibility of using foundry slag as a binder in civil engi- neering. -
INCLUSION CONTROL MODEL in the LADLE METALLURGY FURNACE Master Thesis- J
INCLUSION CONTROL MODEL IN THE LADLE METALLURGY FURNACE Master Thesis- J. Pérez McMaster University- Materials Science and Engineering INCLUSION CONTROL MODEL IN THE LADLE METALLURGY FURNACE By JORGELINA PÉREZ, Chemical Eng. A Thesis Submitted to the School of Graduate Studies in Partial Fulfillment of the Requirements for the Degree Master of Science McMaster University © Copyright by Jorgelina Pérez, Apr 2012 Final Report- Steelmaking Course i Master Thesis- J. Pérez McMaster University- Materials Science and Engineering MASTER OF SCIENCE (2011) McMaster University (Materials Science and Engineering) Hamilton, Ontario, Canada TITLE: Inclusion Control Model in Ladle Metallurgy Furnace AUTHOR: Jorgelina Pérez (Chemical Engineer, Universidad Nacional de Córdoba, Argentina) SUPERVISOR: Dr Gordon A. Irons NUMBER OF PAGES: xix, 131 Final Report- Steelmaking Course ii Master Thesis- J. Pérez McMaster University- Materials Science and Engineering ABSTRACT In Secondary Steelmaking Processes, one of the most used technologies is the Ladle Metallurgy Furnace (LMF). This unit operation enables the adjustment of the chemical composition by ferroalloy addition, electrical reheating to the aim temperature, desulphurization and float out of the inclusions produced during steel deoxidation. The inclusions are harmful to the steel cleanliness. Process parameters such as stirring and steel and slag oxidation must be controlled to obtain a final number of inclusions in the steel whose size is smaller than the critical size for each steel product. This thesis concerns the development of a mathematical model to predict inclusion control during the ladle metallurgy process. Three parameters are evaluated, the initial steel oxidation level, the impact of the slag oxidation level on the reoxidation, and the stirring power with a double effect: to float out inclusions and produce reoxidation. -
Technical Upgrading and Thermal Performance of Heating Furnace Of
TIM’2018 VII All- Russian Scientific and Practical Conference of Students, Graduate Students and Young Scientists on “Heat Engineering and Computer Science in Education, Science and Production” Volume 2018 Conference Paper Technical Upgrading and Thermal Performance of Heating Furnace of the Pipe Rolling Workshop Natalia Shchukina, Nikolay Loshkarev, Vladislav Lavrov, and Nikolay Spirin Ural Federal University (UrFU), Ekaterinburg, Russia Abstract The report is focused on the design and thermal performance of the continuous furnace for heating of pipe billets before piercing operating at ‘ChPRP’ PJSC. The problems arising during operation of the thermal generating unit have been analyzed. To evaluate the efficiency of existing heating system, the heat balance of the continuous furnace has been drawn up. During analysis of the results of calculated studies, disadvantages of existing furnace systems and assemblies have been Corresponding Author: revealed. In order to improve the quality of metal heating, it is proposed to install the Natalia Shchukina through-type furnace heated by means of regenerative burners, as well as provided [email protected] with the metal transportation system, ensuring more uniform heating, both along the Received: 6 June 2018 length and thickness of billets, in place of the existing furnace. When implementing Accepted: 15 June 2018 the proposed activities, a significant economic benefit is expected, which is confirmed Published: 17 July 2018 by the heat balance of the through-type furnace given in the article. Besides, to Publishing services provided by visualize the distribution of temperature and gas-dynamic flows within the operating Knowledge E space of the proposed through-type furnace, the computer simulation for evaluation Natalia Shchukina et al. -
Practical Workbook My-206 Furnaces & Refractories
MY-206 Furnaces and Refractories Department of Metallurgical Engineering PRACTICAL WORKBOOK MY-206 FURNACES & REFRACTORIES Name: _______________________________ Year: ________________________________ Batch: _______________________________ Roll No: ______________________________ Department: ___________________________ Metallurgical Engineering Department NED University of Engineering & Technology 1 MY-206 Furnaces and Refractories Department of Metallurgical Engineering PRACTICAL WORKBOOK MY-206 FURNACES & REFRACTORIES Prepared By: Engr. Waseem Khan LECTURER MYD Approved By: Dr. Amir Iqbal CHAIRMAN MYD Metallurgical Engineering Department NED University of Engineering & Technology 2 MY-206 Furnaces and Refractories Department of Metallurgical Engineering CERTIFICATE Certified that Mr. / Miss____________________________________ Student of Class ________________________ Batch ___________ Bearing Roll No. ____________________________ has completed his / her course work in the subject of________________________ as prescribed and approved by Board of Review of Metallurgical Engineering Department. His / her performance is reflected by index of his / her practical Workbook. This overall performance of the student is Excellent/ Good/ Satisfactory/ Not satisfactory. _____________ Course Teacher 3 MY-206 Furnaces and Refractories Department of Metallurgical Engineering CONTENTS PR.NO DATE PRACTICAL OBJECT REMARKS 1. To study the various fuels their significance & uses 2. To study different furnaces their uses and types 3. To study & analyze Blast furnace and its functions 4. To study about Cupola Furnace & its operations 5. To study about Electric Arc Furnace & its operations 6. To study about Induction Furnace & its operations 7. To perform screen analysis of a given sample 8. How mold (Plaster) is made for slip casting 9. How slip casting is made by mold of plaster of Paris 10. To study about the Manufacturing of Refractories 11. Determination of Refractoriness (P.C.E.) 12.