Matra Bagheera
Total Page:16
File Type:pdf, Size:1020Kb
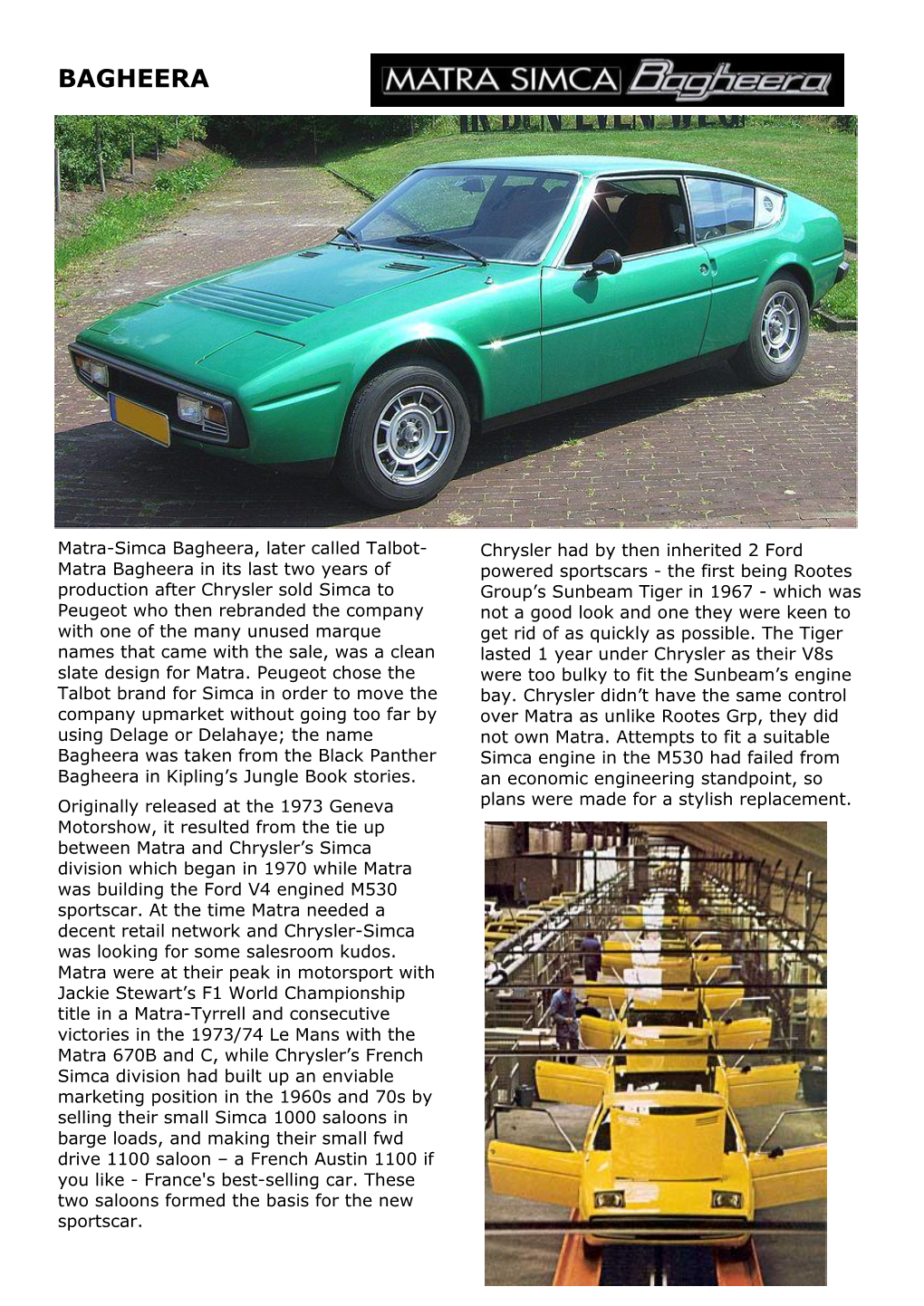
Load more
Recommended publications
-
Barreiros Simca Peugeot: Evolución De Sus Motorizaciones
Barreiros Simca Peugeot: Evolución de sus motorizaciones Scott Hebrón 1º edición Introducción Existen algunas preguntas a las que muchos aficionados y conductores querrían encontrar una respuesta firme referente a las mecánicas Barreiros Simca Peugeot. ¿Compartían algo de mecánica o motorización los motores entre ellos? ¿Pervivió Barreiros hasta la extinción de los motores Simca, a principios de los 90? ¿Se continuaron fabricando motores de inspiración Simca o Barreiros tras la desaparición de estas marcas? Mucho se ha escrito y divulgado al respecto, a veces con opiniones contrarias, sin embargo lo que se trata de buscar es una respuesta objetiva, contrastada, suficientemente documentada, a ese tipo de preguntas y similares. ¿Por qué es importante esto? Por varias razones: principalmente, por la pervivencia en la mente automovilística de un imperio español con extraordinaria calidad y calado. Asimismo, por la huella en el tiempo que habría dejado palpable la 1 estupenda calidad, tanto mecánica como de construcción y diseño, de unos motores legendarios ya en la época en la que se construyeron. Barreiros nació en 1945 con BECOSA (Barreiros Empresa Constructora, S.A.) y concluyó su actividad automovilística en 1969 cuando Chrysler la absorve totalmente. La americana Chrysler ya había comprado en 1967, dentro de su política de expansión europea, la francesa Simca y la inglesa Rootes. En 1978 Chrysler Europe vende todas sus filiales a la francesa Peugeot, recreando ésta, poco tiempo después, la marca Talbot para unificarlas. Este entramado de fechas y marcas es esencial conocerlo para entender el dispar movimiento de versiones y tecnología que se movió entre tan variadas marcas por esas fechas. -
Air Dryer Cartridge 5001004902 New
AIR DRYER CARTRIDGE 5001004902 NEW Product Images PARTS THAT ARE NOT INCLUDED, CAN BE OFFERED ON REQUEST This is general information. Depending on the engine model, deviations are possible WWW.HAMOFA.COM PARTS THAT ARE NOT INCLUDED, CAN BE OFFERED ON REQUEST This is general information. Depending on the engine model, deviations are possible WWW.HAMOFA.COM Additional Information MARKE RENAULT Replaces Ref. No. Agrale 6008099011006 Askam 25242T Astra 0010 7163 Astra 0017 4767 Astra 0819 0948 Astra 5 0313 7484 Astra 5 0313 7742 Bluebird 5008414 BMC 9P917828 DAF 1504900 DAF 1505970 DAF 1518683 DAF 1527756 DAF 6993878 DAF BBU8146 DAF BBU9424 Demag 76117673 Dennis 4324102227 Dennis 4324102227WHITE Dennis 6528852 ERF 1368731 Faun 99707305720 Fendt F 931 882 140 010 Fiat 0017 4767 Fiat 0190 0812 Fiat 0190 7612 Fiat 0299 2261 Fiat 0812 3564 Fiat 0819 0948 Fiat 1990 7612 Fiat 21 3091 2136 Fiat 5 0313 7484 Fiat 5 0313 7742 Fiat 58 0138 2289 Fiat 80 1011 2016 Fiat 8512 7004 Fiat 9844 6957 Fruehauf CF352490 Heuliez 0299 2261 Heuliez 5 0344 6090 Iveco 0017 4767 Iveco 0190 0812 Iveco 0190 7612 Iveco 0299 2261 Iveco 0812 3564 Iveco 0819 0948 Iveco 0819 0984 Iveco 17 4767 Iveco 190 7612 Iveco 1990 7612 Iveco 21 3091 2136 Iveco 299 2261 Iveco 5 0005 0616 Iveco 5 0313 5256 Iveco 5 0313 7484 Iveco 5 0313 7742 Iveco 50 0183 0112 Iveco 50 0186 5037 Iveco 50 0601 6342 Iveco 80 1000 2016 Iveco 80 1011 2016 Iveco 812 3564 Iveco 819 0948 JCB 15/920105 John Deere AL204884 Kamaz 00100000 King Long 35G4211501 Kögel 326549 Liebherr 571352308 Mack 950011 MAN 04.32410.2227 MAN 08.15210.2008 MAN 79.20036.1087 MAN 79.20036.1090 MAN 81.52102.0008 MAN 81.52102.0009 MAN 81.52102.0010 MAN 81.52102.0013 Ersetzt Ref. -
Wear Sensors Catalogue 2010/2011
2010/2011 Wear Sensors Catalogue 2010/2011 NUCAP EUROPE, S.A. JOPE EUROPE, S.L. Polígono Arazuri - Orcoyen Polígono Industrial Egués Calle D, Nº 2 Calle Z, Nº 23 31170 Arazuri, Navarra, SPAIN 31486 Egués, Navarra, SPAIN Catalogue T: (+34) 948 281 090 T: (+34) 948 330 615 F: (+34) 948 187 294 F: (+34) 948 361 698 [email protected] [email protected] www.nucap.eu www.jope.es Shims Wear Sensors Catalogue 2010/2011 Wear Sensors Catalogue 2010/2011 © JOPE EUROPE, 2010 Polígono Industrial Egués Calle Z, Nº 23 31486 Egués, Navarra, SPAIN T: (+34) 948 330 615 F: (+34) 948 361 698 [email protected] www.jope.es Diseño: Intro Comunicación, 2010 General Index New reference information 7 Connectors 8 Terminals 11 NEW > OLD references 15 OLD > NEW references 19 Manufacturer Index 23 W1 Wear sensors for passenger cars 33 W2 Clip on wear sensors for passenger cars 79 W3 Clip on wear sensors for industrial vehicles 117 Kits 137 Accesories 141 WVA > JOPE Index 145 Manufacturer > OE > JOPE Index 157 New reference information Wx xx xx xx New reference information Version W1 Wear sensor for passenger cars Lenght, colour, material, etc. W2 Clip on wear sensor for passenger cars W3 Clip on wear sensor for industrial vehicles Connector type Terminal type See page 08 See page 11 Example W2065003 Old 9A004 Clip on wear sensor Version 03 for passenger cars Connector type 06 Terminal type 50 GENERAL CATALOGUE 2010/2011 7 Connectors 00 15 01 02 16 03 5.5 17 04 5.5 18 05 19 06 20 07 21 22 08 09 23 10 24 11 12 25 BLACK 13 26 14 8 JOPE EUROPE WHITE 37 27 BLUE 28 38 VIOLET 29 30 39 -
Résultat De La Vente Du 19/06/20109
SVV Résultat de la vente du 19/06/20109 LOT LIBELLE ADJUDICATION 1 NOREV : Simca 9 Aronde (BE), bo (ABE) 30 2 NOREV : Simca 9 Aronde (BE), bo (ABE) 25 3 NOREV : Citroën 15 Six familiale (ABE), bo (EM) 4 NOREV : Ford Vedette (BE), bo (ABE) 35 5 NOREV : ensemble de 2 : Simca 9 Aronde (EM), bo (EM) et Ford Vedette (EM), bo (EM) 35 6 NOREV : Renault 4CV (BE), bo (ABE) 30 7 NOREV : ensemble de 2 Citroën DS 19 (EM), bo (ABE) 55 8 NOREV : Renault Frégate grand pavois (ABE), bo (ABE) 30 9 NOREV : ensemble de 2 : Peugeot 203 (ABE), bo (EM) et Simca Versaille (BE) 40 10 NOREV : ensemble de 2 : Dyna Panhard (BE) et Peugeot 403 (ABE), bo (ABE) 11 NOREV : ensemble de 3 : Jaguar 2,4l (BE), bo (ABE), Maserati Sport 200 SI (EM), bo (EM) et 55 Porsche Carrera (ABE), bo (ABE) 12 NOREV : ensemble de 2 Simca Chambord (BE), bo (EM) et Chrysler New-Yorker (BE), bo 55 (ABE) 13 NOREV : ensemble de 2 : Simca plein ciel (ABE), bo (ABE) et Simca Aronde (EM), bo (ABE) 40 14 NOREV : ensemble de 2 : Renault Dauphine (BE), bo (ABE) et Renault Floride (ABE), bo 35 (ABE) 15 NOREV : ensemble de 2 Lancia Aurelia (EM), bo (EM) et Alfa Romeo Giulietta (BE), bo (BE) 40 16 NOREV : ensemble de 3 : Peugeot 201 (BE), bo (ABE), Citroën 5HP (BE), bo (ABE) et 30 Peugeot 172R 1927 (BE) 17 NOREV : ensemble de 3 : Peugeot 201 (BE), bo (ABE), Citroën 5HP (BE), bo (ABE) et 30 Peugeot 172R 1927 (BE), bo (ABE) 18 NOREV : ensemble de 3 : Renault Juvaquatre (BE), bo (ABE), Simca 8 1200 (BE), bo (ABE) 40 et Simca 5 (BE), bo (ABE) 19 NOREV : ensemble de 2 Citroën 11CV 1936 (BE), bo (ABE) 35 -
Les Grandes Dates De Poissy
Les grandes dates de Poissy 70 ans d’histoire, 7 décennies d’une épopée riche, LA COLLECTION porteuse des plus belles pages de l’histoire de l’automobile Près du Site PSA PEUGEOT CITROËN de POISSY, française. 7 décennies qui ont vu des hommes courageux au venez découvrir 70 véhicules qui ont construit, depuis 1938, savoir faire incontesté : concevoir et fabriquer les l’histoire de cette usine, sous les marques : automobiles qui ont perpétué la légende pisciacaise sur les FORD, SIMCA, CHRYSLER FRANCE & TALBOT. routes de France et du monde. VISITES Lundi 14 à 17h, Samedi 9 à 12h & 14 à 17h Autres jours sur RDV à prendre : à la CAAPY 01 30 19 41 15 aux horaires ci-dessus, 1938 Naissance de l’usine ou à l’Office de tourisme de Poissy au 01 30 74 60 65. de Poissy TARIFS Adultes : 5 euros Groupes (10 pers. mini) scolaires & étudiants : 3 euros 1954 SIMCA rachète Enfants de moins de 10 ans : gratuit. Ford France LOCATION DE VEHICULES ANCIENS Pour vos événements familiaux ou professionnels, consultez nous pour louer : De Ford SAF à PSA Peugeot Citroën 1963 SIMCA devient une - un véhicule avec chauffeur marque de Chrysler - un véhicule en présentation statique. 70 ans d’histoire automobile PLAN D’ACCÈS Ave VersVers N184N184 nu e de l'E CAAPY etet A15A15 VersVers VersVers A15A15 u Création de Triel-sTriel-sur-Seir-Seine rope TECHNOPARC StSt Ouen 1970 ACCUEIL 5 l'Al'Aumône LesLes Mureareaux 5 N190N D55D 1 0 9 3 0 D30D Chrysler France CARRIÈRESCARRIÈRES Voie SNCF / RER Ave nu VersVers SOUS-POISSYSOUS-POISSY e Gambett Po Av. -
Electronic Edition Pacific Citroën News
ISSN 1542-8303 PCN 84A Pacific Citroën News Fall 2020 Electronic Edition The Publication Of: Northwest Citroën Owner’s Club - Citroën Autoclub Canada - 2CVBC - Citroën Car Club Events Calendar . Page 02 CCC Palos Verdes Tour Page 06 Faux-pas . Page 15 Books . Page 02 Wendtland Collection . Page 08 Repro Radiators . Page 16 DS9 Range . Page 03 Mullin Museum VIII . Page 10 Adverts . Page 17 Farewells . Page 04 Type G, ELV 1945 . Page 11 CCC Online Store . Page 18 Letters . Page 05 Raid BC Part II . Page 12 Parts & Suppliers . Page 19 Paintless Dent Removal Page 14 Dates(s) Location 2021 Event Information DUE TO CHANGING COVID-19 CONDITIONS PLEASE CONSULT THE EVENT VENUES OR ORGANIZERS BEFORE ATTENDING Mar 21 Sun WA Newcastle NWCOC Spring Drive Tour Newcastle to Auburn. Info: [email protected] June 2 - 6* F Paris Retromobile 2021. Paris Expo Porte-de-Versailles, gates 1, 2, 3. Note the dates are postponed from NOTE DATE the traditional February calendar. CHANGE www.retromobile.com July 27- Aug 1* CH Delémont 24th Worldmeeting of 2 CV Friends. https://www.2cv2021.ch/?lang=en Sep 17 -19 CA Pismo Beach Rendez Vous 2021. This year at the Shore Cliff Hotel, 2555 Price St, Pismo Beach, CA 93449 NOTE DATE 2021 registration form to follow. CHANGE www.citroencarclub.us 2022 Event Infomation Aug 3-7* 2022 PL Torún 17th ICCCR 2020 in Toruń, Poland. https://www.icccr2020.pl/english/ NOTE DATE Rescheduled to August, 2022, due to pandemic concerns. CHANGE * Indicates event not sponsored by CCC-NWCOC-CAC Books -From Richard Bonfond: Here is info on a new book by Thijs van der Zanden and Julian Marsh. -
User Guide to SIMCA 13.Pdf
User Guide to SIMCA By MKS Umetrics Version 13 1992-2012 MKS Umetrics AB, all rights reserved Information in this document is subject to change without notice and does not represent a commitment on part of MKS Umetrics. The software, which includes information contained in any databases, described in this document is furnished under license agreement or nondisclosure agreement and may be used or copied only in accordance with the terms of the agreement. It is against the law to copy the software except as specifically allowed in the license or nondisclosure agreement. No part of this user guide may be reproduced or transmitted in any form or by any means, electronic or mechanical, including photocopying and recording, for any purpose, without the express written permission of MKS Umetrics. Umetrics patents and trademarks: OPLS/O2PLS®, SWE-9802229-6, USA-6754543, SEQUENTIAL MODELING, USA-7523384 OSC®, SWE-0000563-7, USA-6853923 DESIGN SPACE USA-8086327 PLS-TREE®, Pending RED - MUP®, VALUE FROM DATA®, OPLS®, O2PLS®, O2-PLS®, OPLS-DA®, O2PLS-DA™ PLS-TREE™, S-PLOT™, EZinfo®, SBOL®, FABSTAT®, BATCH FINGERPRINT®, SIMCA®. ID #2043 User guide edition date: April 23, 2012 AN MKS COMPANY MKS Umetrics AB Stortorget 21 SE-211 34 Malmö Sweden Phone: +46 (0)40 664 2580 Email: [email protected] Welcome Welcome to the user guide for SIMCA 13. This is your guide to SIMCA and its capabilities. This user guide does not include in-depth background material to multivariate data analysis. For such information, see the book Multi- and Megavariate Data Analysis. Content The help is parted into 16 chapters, two appendices, and a reference list. -
Strategic Plan for the 2016-2020 Period ©ADP-LE BRAS Gwen - Zoo Studio
Strategic plan for the 2016-2020 period ©ADP-LE BRAS Gwen - Zoo Studio - 1 - Augustin de Romanet Chairman & Chief Executive Officer of Aéroports de Paris ONNECT 2020, the Aéroports de Paris strategic plan for the 2016-2020 period, espouses the vision of the airport as a node connecting local areas, passengers, airlines and the multiple skills of the men and women who work there every day. In a changing world, where the major airport "Ccities are in competition, our task remains the same - connecting people with one another, guaranteeing the fastest and smoothest traffic of goods and services - but it obliges us to be more efficient. Our strategic plan for the next five years is based on the Economic Regulation Agreement (ERA) that we have just signed with the French government, but it goes much further than that. It is a plan that nurtures the competitiveness of the whole air transport sector and local areas. With CONNECT 2020, Aéroports de Paris wishes to express its full potential to pursue the ambition of being a leader in airport design, construction and operations. For the next five years, we have defined three main strategic priorities: to optimise, to attract and to expand, that apply to all our activities. Optimise by making the most of our resources in order to improve operational efficiency and provide a better service for the airlines. Over the next five years, we are undertaking an unprecedented capital expenditure programme of €4.6 billion, of which €3 billion is allocated to regulated activities, including our core business: airports. We are also continuing with our efforts in productivity, by bringing costs per passenger down by 8%. -
Vehicle Make, Vehicle Model
V8, V9 VEHICLE MAKE, VEHICLE MODEL Format: VEHICLE MAKE – 2 numeric VEHICLE MODEL – 3 numeric Element Values: MAKE: Blanks 01-03, 06-10, 12-14, 18-25, 29-65, 69-77, 80-89, 90-94, 98-99 MODEL: Blanks 001-999 Remarks: SEE REMARKS UNDER VEHICLE IDENTIFICATION NUMBER – V12 2009 181 ALPHABETICAL LISTING OF MAKES FARS MAKE MAKE/ NCIC FARS MAKE MAKE/ NCIC MAKE MODEL CODE* MAKE MODEL CODE* CODE TABLE CODE TABLE PAGE # PAGE # 54 Acura 187 (ACUR) 71 Ducati 253 (DUCA) 31 Alfa Romeo 187 (ALFA) 10 Eagle 205 (EGIL) 03 AM General 188 (AMGN) 91 Eagle Coach 267 01 American Motors 189 (AMER) 29-398 Excaliber 250 (EXCL) 69-031 Aston Martin 250 (ASTO) 69-035 Ferrari 251 (FERR) 32 Audi 190 (AUDI) 36 Fiat 205 (FIAT) 33 Austin/Austin 191 (AUST) 12 Ford 206 (FORD) Healey 82 Freightliner 259 (FRHT) 29-001 Avanti 250 (AVTI) 83 FWD 260 (FWD) 98-802 Auto-Union-DKW 269 (AUTU) 69-398 Gazelle 252 (GZL) 69-042 Bentley 251 (BENT) 92 Gillig 268 69-052 Bertone 251 (BERO) 23 GMC 210 (GMC) 90 Bluebird 267 (BLUI) 25 Grumman 212 (GRUM) 34 BMW 191 (BMW) 72 Harley- 253 (HD) 69-032 Bricklin 250 (BRIC) Davidson 80 Brockway 257 (BROC) 69-036 Hillman 251 (HILL) 70 BSA 253 (BSA) 98-806 Hino 270 (HINO) 18 Buick 193 (BUIC) 37 Honda 213 (HOND) 19 Cadillac 194 (CADI) 29-398 Hudson 250 (HUDS) 98-903 Carpenter 270 55 Hyundai 215 (HYUN) 29-002 Checker 250 (CHEC) 08 Imperial 216 (CHRY) 20 Chevrolet 195 (CHEV) 58 Infiniti 216 (INFI) 06 Chrysler 199 (CHRY) 84 International 261 (INTL) 69-033 Citroen 250 (CITR) Harvester 98-904 Collins Bus 270 38 Isuzu 217 (ISU ) 64 Daewoo 201 (DAEW) 88 Iveco/Magirus -
Amédée Gordini
Amédée Gordini the programme as per the contract, and so the Nanterre directors asked Gordini just to race as much as possible in any events to maintain publicity. It was for this reason that HT Pigozzi suggested to Amédée Gordini that he enter the Spa 24 Hours in Belgium. The 3 Balillas used in the Bol D’Or were back in action. Gordini’s own car (7514 RJ 6), using the recently updated engine with the aluminium cylinder head developed by Gordini, which was now delivering 55hp, would be shared in a drive with Jacques Blot. A second Balilla was prepared for Marino Zanardi with Albert Alin as co-driver, the latter’s diligent unpaid work and his passion for racing rewarded with a drive. Finally, a third Balilla was to be driven by Georges Sarret/Paul Ducos. Rain and cold weather put off the spectators, and not many were there to witness the start, which saw 35 competitors get away at 4pm. Alfa Romeos, Delahayes, and Lagondas led proceedings in this long test of endurance, in conditions that meant just 18 cars were left in the race when Sommer/Severi crossed the finishing line as victors in their Alfa Romeo 8C 2900. Gordini finished 14th overall, and first in the 1100cc sports class, his two other cars in Gordini and Blot at the Spa 24 Hours. (Courtesy CH-AG) third and fourth places in class. 1100cc class: 1, 3, and 4 at the Spa 24 Hours. (Courtesy TM-AP) 24 Struggle and strife: 1950-1952 Pau: the first major race of the year. -
Pacific Citroën News PCN Spring 2019 79
ISSN 1542-8303 Pacific Citroën News PCN Spring 2019 79 The Publication Of: Northwest Citroën Owner’s Club - Citroën Autoclub Canada - 2CVBC - Citroën Car Club Events Calendar . Page 02 DS 19 Brake Calipers . Page 10 Ivan Frank . Page 03 The Lost Lady . Page 13 BC Italian-French Car Show . Page 04 Adverts . Page 14 Mercer Island Tour . .Page 06 Parts & Suppliers . Page 16 Point Defiance Picnic . Page 07 Concours de Maryhill . Page 17 Mullin Museum III . Page 08 Rendezvous 2019 . Page 18 Dates(s) Location 2019 Event Information Jul 30 - Aug 4* HR Samobor 23rd Worldmeeting of 2CV Friends in Croatia. Info: https://www.2cv.hr/en/ Aug 25 Sun WA Seattle Cit-Chat BBQ. 1 PM at Axel and Uschi’s Call 206-439-0202 or e-mail [email protected] for direc- tions, RSVP not required. The Membership will be voting on a proposal to raise the NWCOC annual dues to $30.00. Bring: Meat for BBQ and/or other dishes. We will provide: German Bratwurst, soft drinks, and enter- tainment! If it rains: The party room in the garage will be ready and the grill will be covered. NWCOC Silent Auction! Bring: Please bring items to donate to the NWCOC Silent Auction. Proceeds are used to support our club. These need not be Citroën or even car related! Please make sure that auto parts are clean or wrapped for protection. Bid: The Silent Auction augments the club treasury and we count on it! Be ready to take home some fabulous items! Sep 7 Sat BC Vancouver Tour de Côte sur Mer. -
Wiper Blades for Passenger Cars, Trucks and Agricultural Vehicles
WIPER BLADES FOR PASSENGER CARS, TRUCKS AND AGRICULTURAL VEHICLES www.hella.com/easychange SEE FURTHER WITH HELLA Since 1899, the family-owned company has been developing premium-quality components and systems for the automotive industry and is one of the largest global providers in this sector. Major European manufacturers rely on parts and technology from HELLA not only to achieve better safety, but also higher levels of comfort, convenience and environmental compatibility on the road. In addition to wiper blades, HELLA also offers first-class accessories such as auxiliary lights, horns and lamps. With 118 locations around the world, HELLA puts the drive in innovations. Approximately one fifth of the 30,000 employees work on new technologies and products in the research and development team. TABLE OF CONTENTS Clear vision without streaks 04 Easier than ever: Changes with EASYCHANGE 04 How do I know when its time to change my wiper blades? 05 Wiper blades for Passenger Car, Commercial and Agricultural vehicles 06 Overview of wiper blades 08 Passenger car vehicle applications 10 Commercial vehicle applications 124 Agricultural vehicle applications 132 Overview of Parts 138 Explanation of symbols 140 138 | 139 www.hella.com/easychange Visit our website. A simple web configurator will help you to select the right wiper blades. www.hella.com/easychange | 01 CLEAR VISION WITHOUT STREAKS Drivers frequently put wiper blades to the test under difficult You can always depend on wiper blades from HELLA. The rubber conditions as they must withstand temperatures of -30 to edge of the blades are coated with graphite so that they can be +70 degrees and deal with snow, dust, sleet and dirty mud-laden subjected to the most intense of loads on a continual basis.