Radius of Curvature Metrology for Segmented Mirrors
Total Page:16
File Type:pdf, Size:1020Kb
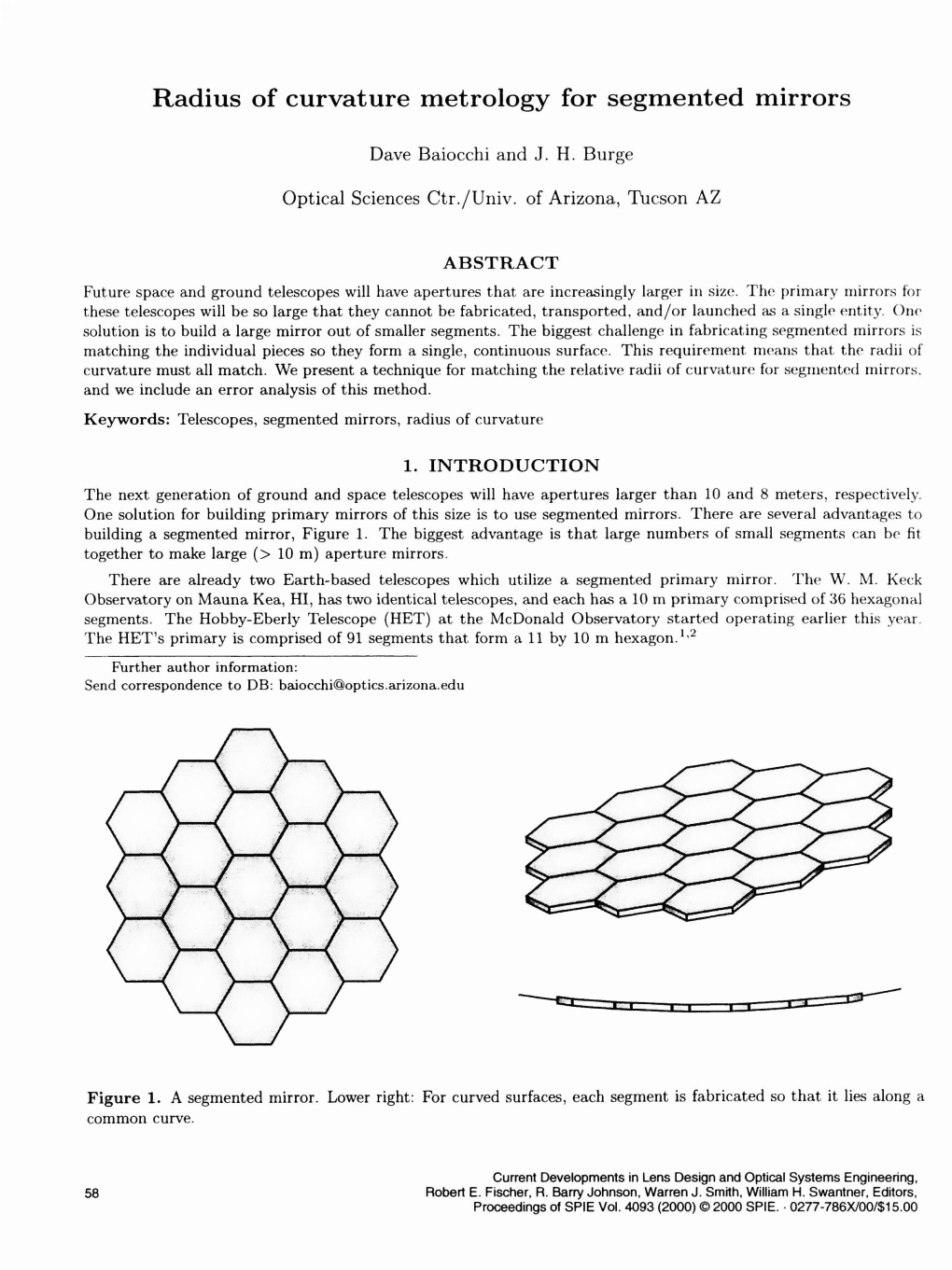
Load more
Recommended publications
-
Distributed Control of a Segmented Telescope Mirror
Distributed Control of a Segmented Telescope Mirror by Dan Kerley B.Eng., University of Victoria, 2004 A Thesis Submitted in Partial Fulfillment of the Requirements for the Degree of MASTER OF APPLIED SCIENCE in the Department of Mechanical Engineering Dan Kerley, 2010 University of Victoria All rights reserved. This thesis may not be produced in whole or in part, by photocopy or other means, without the permission of the author ii Distributed Control of a Segmented Telescope Mirror by Dan Kerley B.Eng., University of Victoria, 2004 Supervisory Committee Dr. Edward Park (Department of Mechanical Engineering) Supervisor Dr. Afzal Suleman (Department of Mechanical Engineering) Department Member Dr. Panajotis Agathoklis (Department of Electrical & Computer Engineering) Outside Member Ms. Jennifer Dunn (Herzberg Institute of Astrophysics) Additional Member iii SUPERVISORY COMMITTEE Dr. Edward Park (Department of Mechanical Engineering) Supervisor Dr. Afzal Suleman (Department of Mechanical Engineering) Department Member Dr. Panajotis Agathoklis (Department of Electrical & Computer Engineering) Non-Department Member Ms. Jennifer Dunn (Herzberg Institute of Astrophysics) Additional Member ABSTRACT As astronomers continue to examine fainter objects and farther back in time, they require increasingly large telescopes due to the fundamental diffraction of optical elements. Therefore several of the next generation optical telescopes will employ extremely large primary mirrors. However to realistically construct mirrors of these magnitudes they will need to be assembled as a collection of many smaller mirrors. This mirror segmentation leads to the additional challenge of aligning the smaller mirror elements with respect to one another, and maintain that alignment in the presence of disturbances on the optical surface and its supporting structure. -
Thirty Meter Telescope Observatory Software Architecture K
FRBHMUST03 Proceedings of ICALEPCS2011, Grenoble, France THIRTY METER TELESCOPE OBSERVATORY SOFTWARE ARCHITECTURE K. Gillies#, C. Boyer, TMT Observatory Corporation, Pasadena, CA 91105, USA Abstract architecture takes advantage of these prior solutions when The Thirty Meter Telescope (TMT) will be a ground- possible. It’s then possible to focus attention on the based, 30-m optical-IR telescope with a highly problems unique to TMT and reuse common solutions for segmented primary mirror located on the summit of the parts of the software system that are known or of little Mauna Kea in Hawaii. The TMT Observatory Software risk. We can also improve upon the solutions used in the (OSW) system will deliver the software applications and previous generation of systems when experience has infrastructure necessary to integrate all TMT software into shown that aspects of the known solutions have issues. a single system and implement a minimal end-to-end The complexity of some aspects of the TMT software science operations system. At the telescope, OSW is control system scale with the telescope aperture size, and focused on the task of integrating and efficiently the software must also scale to handle this complexity. controlling and coordinating the telescope, adaptive Segmented mirror control for TMT requires more moving optics, science instruments, and their subsystems during parts behind the mirror and with it more sophisticated observation execution. From the software architecture control software than existing segmented mirror systems. viewpoint, the software system is viewed as a set of It’s also true that not every aspect of TMT software software components distributed across many machines complexity scales with the size of the aperture. -
A Demonstration of Wavefront Sensing and Mirror Phasing from the Image Domain
Mon. Not. R. Astron. Soc. 000, 000–000 (0000) Printed 6 August 2018 (MN LATEX style file v2.2) A Demonstration of Wavefront Sensing and Mirror Phasing from the Image Domain Benjamin Pope1;2?, Nick Cvetojevic1;3;4, Anthony Cheetham1, Frantz Martinache5, Barnaby Norris1, Peter Tuthill1 1Sydney Institute for Astronomy, School of Physics, University of Sydney, NSW 2006, Australia 2Astrophysics, University of Oxford, Denys Wilkinson Building, Keble Rd, Oxford OX1 3RH, UK. 3Centre for Ultrahigh bandwidth Devices for Optical Systems (CUDOS), Institute of Photonics and Optical Science (IPOS), School of Physics, University of Sydney, Sydney, NSW 2006, Australia 4Australian Astronomical Observatory, NSW 2121, Australia 5Laboratoire Lagrange, CNRS UMR 7293, Observatoire de la Côte d’Azur, Bd de l’Observatoire, 06304 Nice, France 6 August 2018 ABSTRACT In astronomy and microscopy, distortions in the wavefront affect the dynamic range of a high contrast imaging system. These aberrations are either imposed by a turbulent medium such as the atmosphere, by static or thermal aberrations in the optical path, or by imperfectly phased subapertures in a segmented mirror. Active and adaptive optics (AO), consisting of a wave- front sensor and a deformable mirror, are employed to address this problem. Nevertheless, the non-common-path between the wavefront sensor and the science camera leads to persis- tent quasi-static speckles that are difficult to calibrate and which impose a floor on the image contrast. In this paper we present the first experimental demonstration of a novel wavefront sensor requiring only a minor asymmetric obscuration of the pupil, using the science camera itself to detect high order wavefront errors from the speckle pattern produced. -
The First Active Segmented Mirror at ESO
Telescopes and Instrumentation The First Active Segmented Mirror at ESO Frédéric Gonté, Christophe Dupuy, The design and integration phases of onal mirrors have to be aligned with a Christoph Frank, Constanza Araujo, APE, which started in 2005, have been precision better than 15 nm rms. It was Roland Brast, Robert Frahm, completed and the test phase will start clearly not feasible to produce a scaled- Robert Karban, Luigi Andolfato, in June 2007 during which time APE down version of the full primary mirror. Regina Esteves, Matty Nylund, will be installed at the focus of one of the However, from a statistical point of view, Babak Sedghi, Gerhard Fischer, Lothar VLT unit telescopes in 2008. a mirror with approximately 50 segments Noethe, Frédéric Derie (all ESO) is already representative of a mirror with Initially the APE team wanted to contract many more segments in terms of the the design and manufacture of the ASM study of issues like alignment algorithms The Active Phasing Experiment (APE) is to a private company. However, when or the effect of misalignments on image part of the Extremely Large Telescope no company could be found which could quality. The main requirements for the Design Study which is supported by the meet the rather stringent requirements, ASM can be summarised as: European Framework Programme 6. it was decided to develop the ASM in- – 61 segments in four rings around the This experiment, which is conducted in house, involving ESO groups in Integra- central segment collaboration with several partners is tion, Optics, Electronics, Software and – Segment size 17 mm to minimise the a demonstrator to test and qualify newly- the ELT Project Office. -
Giant Segmented Mirror Telescope: a Point Design Based on Science Drivers
Giant Segmented Mirror Telescope: a point design based on science drivers Stephen E. Strom, Larry Stepp, Brooke Gregory AURA New Initiatives Office ABSTRACT We describe a 'point design' for a 30m Giant Segmented Mirror Telescope (GSMT) aimed at meeting a set of initial science goals developed over a period of two years by working groups comprised of more than 60 astronomers. The paper summarizes these goals briefly, captures the top-level performance requirements that follow from them, and describes a plausible, first-cut technical solution developed as part of an overall systems-level analysis. The key features of the point design are: (1) a fast (f/1) primary; (2) an adaptive secondary that serves both to compensate for the effects of wind buffeting and as the first stage of three adaptive optics systems: (i) multi-conjugate AO; (ii) high-performance on-axis AO; (iii) ground-level seeing compensation; (3) a radio telescope structure; (4) multiple instrument ports (prime focus; Nasmyth foci; direct Cass); (5) an hierarchical control system comprising multiple active and adaptive elements. Keywords: Giant Segmented Mirror Telescope, telescope conceptual design 1. INTRODUCTION Najita and Strom1 summarize the science enabled by the enormous gains in sensitivity and angular resolution afforded by a 30-m class telescope. Among the key programs described therein are: • Quantifying the distribution of gas and galaxies at redshifts z > 3 in order to understand the link between emerging large-scale structure and the observed fluctuations in the -
Building the Gateway to the Universe 3
B UILDING THE GATEWAY TO T HE UN IVERSE T HIRTY M ETER TEL ESCOPE 42581_Book.indd 2 10/12/10 11:11 AM CONTENTS 02 The Story of TMT is the History of the Universe 04 Breakthroughs and Discoveries in Astronomy 08 Grand Challenges of Astronomy 12 A Brief History of Astronomy and Telescopes 14 The Best Window on the Universe 16 The Science and Technology of TMT 26 Technology, Innovation, and Science 28 Turning Starlight into Insight On the cover Artist’s concept of the Thirty Meter Telescope. The unique dome design optimizes TMT’s view while minimizing its size. The louvered openings surrounding the dome enable the observatory to balance the air temperature inside the dome with that of the surrounding atmosphere, ensuring the best possible image with the telescope. Photo-illustration: Skyworks Digital 42581_Book.indd 3 10/12/10 11:11 AM B UILDING THE GATEWAY TO T HE UN IVERSE 42581_Book.indd 1 10/12/10 11:11 AM THE STORY OF TMT IS THE HISTORY OF THE U N IVERSE The Thirty Meter Telescope (TMT) will take us on an exciting journey of dis- covery. The TMT will explore the origin of galaxies, reveal the birth and death of stars, probe the turbulent regions surrounding supermassive black holes, and uncover previously hidden details about planets orbiting distant stars, including the possibility of life on these alien worlds. 2 T HIRTY METERT ELESCO PE 42581_Book.indd 2 10/12/10 11:11 AM Photo-illustration: Dana Berry MAUNA KEA HAWAII SELECTED AS PREFERRED SITE FULLY INTEGRATED LASER GUIDE STAR ADAPTIVE OPTICS INTERNATIONAL SCIENCE PARTNERSHIP BUILDING THE GATEWAY TO THE UNIVERSE 3 42581_Book.indd 3 10/12/10 11:11 AM B REAKTHROUG HS A ND DISCOV ERI ES I N ASTRONOMY Research in astronomy has revealed exciting details about our place in the cosmos. -
Adaptive Optics for the Thirty Meter Telescope
Adaptive Optics for the Thirty Meter Telescope Brent Ellerbroek Thirty Meter Telescope Observatory Corporation Presentation to NAOC Beijing, June 23, 2011 TMT.AOS.PRE.11.085.REL01 1 Presentation Outline TMT adaptive optics (AO) requirements The first light TMT AO system design – Narrow Field Infra-Red AO System (NFIRAOS) – Laser Guide Star Facility (LGSF) AO component development Summary TMT.AOS.PRE.11.085.REL01 2 The Thirty Meter Telescope (TMT) Project Intends to build a Thirty Meter Telescope for ground based, visible and near infra-red astronomy Is a collaboration of: – The Association of Canadian Universities for Research in Astronomy (ACURA) – The University of California – The California Institute of Technology Construction scheduled to – NAOJ (participant), NAOC begin in 2012-13 (participant), and India (observer) First light to follow after a 7- Is now concluding a Design and year construction schedule Development Phase (DDP) to – Establish the system design – Determine the cost and schedule – Select a site (Mauna Kea 13N) 3 TMT.AOS.PRE.11.085.REL01 The TMT Design Ritchey-Chretien optical design form D = 30 m, f/1 primary 492 1.42m segments 3.05 m convex secondary f/15 output focal ratio 15 arc min unvignetted FOV Articulated tertiary Nasmyth-mounted instrumentation TMT.AOS.PRE.11.085.REL01 4 Many TMT Observations Require High Angular Resolution Studying the spatial structure and star formation regions of distant galaxies Precision astrometry and photometry of crowded star fields – Has been used to determine star orbital dynamics and “weigh” the black hole at the center of our galaxy Direct detection and characterization of extra-solar planets – Expected star-to-planet contrast ratios from 106 to 109 Real-time atmospheric turbulence compensation via adaptive optics (AO) enables high resolution observations such as these from the ground 5 TMT.AOS.PRE.11.085.REL01 Sample AO Results on Large Telescopes Galactic Center Astrometry (Keck LGS AO) Multi-Conjugate AO on a 2’ FoV (VLT) Classical AO MCAO LGS AO Science Papers vs. -
The Thirty Meter Telescope: How California, Canada, China, India and Japan Are Working Together to Build a Next Generation Extremely Large Telescope
The Thirty Meter Telescope: How California, Canada, China, India and Japan are Working Together to Build a Next Generation Extremely Large Telescope Gary H Sanders SLAC National Accelerator Laboratory September 18, 2013 TMT.PMO.PRE.13.023.REL01 1 TMT on Mauna Kea TMT.PMO.PRE.13.023.REL01 2 TMT.PMO.PRE.13.023.REL01 3 Sharper Vision with TMT: Distant Galaxies from Space and Hawaii Island Hubble TMT TMT.PMO.PRE.13.023.REL01 4 Why build a 30 meter telescope? Light collection ~ diameter2 = D2 – Sets limit on sensitivity of “seeing-limited” observing TMT will have – 144 times the light collection and sharper optical resolution than the Hubble Space Telescope, and – 36 times the light collection of the Palomar telescope – 9 times the light collection of the Keck telescopes TMT.PMO.PRE.13.023.REL01 5 A Vision of TMT (1908) "It is impossible to predict the dimensions that reflectors will ultimately attain. Atmospheric disturbances, rather than mechanical or optical difficulties, seem most likely to stand in the way. But perhaps even these, by some process now unknown, may at last be swept aside. If so, the astronomer will secure results far surpassing his present expectations.“ - Hale, Study of Stellar Evolution, 1908 (p. 242) writing about the future of the 100 inch. 100 years later, TMT is being designed end-to-end to correct atmospheric disturbances to approach the diffraction limited image quality of a 30 meter aperture TMT.PMO.PRE.13.023.REL01 6 TMT Aperture Advantage Seeing-limited observations and observations of resolved sources Sensitivity D2 (~ 14 8m) Background-limited AO observations of unresolved sources Sensitivity S2D4 (~ 200 8m) High-contrast AO observations of unresolved sources S2 Sensitivity D4 (~ 200 8m) 1 S Sensitivity 1/ time required to reach a given s/n ratio throughput, S Strehl ratio. -
Design Considerations for a Highly Segmented Mirror
Design considerations for a highly segmented mirror Stephen Padin Design issues for a 30-m highly segmented mirror are explored, with emphasis on parametric models of simple, inexpensive segments. A mirror with many small segments offers cost savings through quantity production and permits high-order active and adaptive wave-front corrections. For a 30-m f͞1.5 parab- oloidal mirror made of spherical, hexagonal glass segments, with simple warping harnesses and three- point supports, the maximum segment diameter is ϳ100 mm, and the minimum segment thickness is ϳ5 mm. Large-amplitude, low-order gravitational deformations in the mirror cell can be compensated if the segments are mounted on a plate floating on astatic supports. Because gravitational deformations in the plate are small, the segment actuators require a stroke of only a few tens of micrometers, and the segment positions can be measured by a wave-front sensor. © 2003 Optical Society of America OCIS codes: 350.1260, 010.1080, 220.4880, 120.4640. 1. Introduction design considerations are explored here for a 30-m Multiple mirrors seem to be the only viable approach f͞1.5 visible and infrared telescope with AO. for optical telescopes with apertures much larger For a large mirror with small segments, the cost than ϳ8 m. Many designs have been proposed, and and complexity of sensors and actuators are key is- these are broadly distinguished by the size of the sues. If gradients in the telescope structural defor- subapertures. The 20–20 telescope elements, which mations are repeatable at the level of ϳ1 m across have seven 8.4-m-diameter segments,1 and the a segment diameter, changes in the segment posi- Phased Array Mirror Extendible Large Aperture tions can be measured by a wave-front sensor instead ͑PAMELA͒, with 8-cm-diameter segments,2–4 repre- of edge sensors. -
Multi-Spectral Piston Sensor for Co-Phasing Giant Segmented Mirrors 1
Multi-spectral piston sensor for co-phasing giant segmented mirrors 1 Multi-spectral piston sensor for co-phasing giant segmented mirrors and multi-aperture interferometric arrays François Hénault UMR 6525 CNRS H. Fizeau – UNS, OCA Avenue Nicolas Copernic, 06130 Grasse – France E-mail: [email protected] Abstract. This paper presents the optical design of a multi-spectral piston sensor suitable to co-phasing giant segmented mirrors equipping the Future Extremely Large Telescopes (ELTs). The general theory of the sensor is described in detail and numerical simulations have been carried out, demonstrating that direct piston and tip- tilt measurements are feasible within accuracies respectively close to 20 nm and 10 nano-radians. Those values are compatible with the co-phasing requirements, although the method seems to be perturbed by uncorrected atmospheric seeing. Keywords: Telescopes, Fourier optics, Phase retrieval, Phase-shifting interferometry PACS: 95.55.–n, 42.30.Kq, 42.30.Rx, 42.87.Bg 1 Introduction From the Hooker telescope of 100” diameter build during the 1920s on Mount Wilson to the achievement of the Very Large Telescope (VLT) array in Chile, the 20th century has unquestionably demonstrated the superiority of large reflective telescopes in the field of astronomical observations. It is commonly believed, however, that the classical operations of manufacturing, polishing and supporting large glass mirrors will soon be confronted to their technological limits, and that in view of 10-m class (or higher) ground-based telescopes, the primary mirrors will need to be composed of several smaller individual reflective facets (or segments), a major choice having been validated on the two 10-m Keck telescopes. -
Segmented Mirrors
Human HET: CHALLENGE 1 SEGMENTED MIRROR By Brad Armosky and Mary Kay Hemenway Introduction • plan and implement investigative procedures (6.2, 7.2, 8.2, IPC, Physics, Astronomy) The astronomer’s quest to see fainter objects and farther into • relationships between science and technology (8.5) the sky leads to the desire for larger telescopes. But as the size of the telescope gets bigger, so does the price tag. Creative SCIENCE TEKS CONCEPTS engineers and astronomers use new technology, tools, and fab- • Systems (6.5, 7.5) rication methods to reduce the cost of building large tele- MATH TEKS scopes with large mirrors. For the Hobby-Eberly Telescope • Geometry and spatial reasoning (6.6, 6.7, 7.8) (HET), 91 small hexagonal mirrors together act as a single 10 • Measurement (6.8, 7.9, 8.8, 8.10) by 11 meter hexagonal mirror.The cost of this array of mir- • Underlying processes and mathematical tools (6.11, 7.13) rors is significantly less than a single monster mirror, even • Patterns, relationships, and algebraic thinking (7.4, 7.5, 8.5, 8.7,) when the complex controls needed to keep it acting as one mirror and the structure are taken into account. This design Preparation departs radically from that of the other telescopes at Divide the students into work groups and pass out materials. McDonald Observatory near Fort Davis,Texas. Each of those telescopes contains a single primary mirror mounted at the bottom end of a telescope tube. For example, Problem the Harlan J. Smith telescope holds the largest As part of the HET design team, the students’ job is to devel- primary mirror at 2.7 meters in op a large and cost-effective primary mirror. -
Optimal H2 and H∞ Control of Extremely Large Segmented Telescopes
Optimal H2 and H∞ Control of Extremely Large Segmented Telescopes Zaher M. Kassas∗∗ The University of Texas at Austin, Austin, TX, 78712, USA Robert H. Bishop† Marquette University, Milwaukee, WI, 53233, USA Extremely large telescopes (ELTs) are the next generation of ground-based reflecting telescopes of optical wavelengths. ELTs possess an aperture of more than 20 meters and share a number of common features, particularly the use of a segmented primary mirror and adaptive optics systems. In 2005, the European Southern Observatory introduced a new giant telescope concept, named the European Extremely Large Telescope (E-ELT), which is scheduled for operation in 2018. In 2009, a feasibility study proved the feasibility of the real-time (RT) control system architecture for the E-ELT’s primary mirror, which consists of nearly 1,000 mirror segments with 3,000 actuators and 6,000 sensors. The goal of the RT control system was to maintain a perfectly aligned field of mirrors at all times with a loop-time of 1 ms. The study assumed a prescribed controller algorithm. This paper prescribes two such controllers. In this respect, optimal controller designs for the primary mirror, where optimality is formulated in the H2 and H∞ frameworks are derived. Moreover, the designed controllers are simulated to show that the desired performance, which is defined in terms of imaging requirements, is met. I. Introduction Modern astronomical research requires investigating extremely faint objects that have small angular di- ameters. Large aperture telescopes provide higher spatial and spectral resolution that enables the detection of the astronomical objects in question.