Estimator-Based Sliding Mode Control of an Optical Disc Drive Under Shock and Vibration
Total Page:16
File Type:pdf, Size:1020Kb
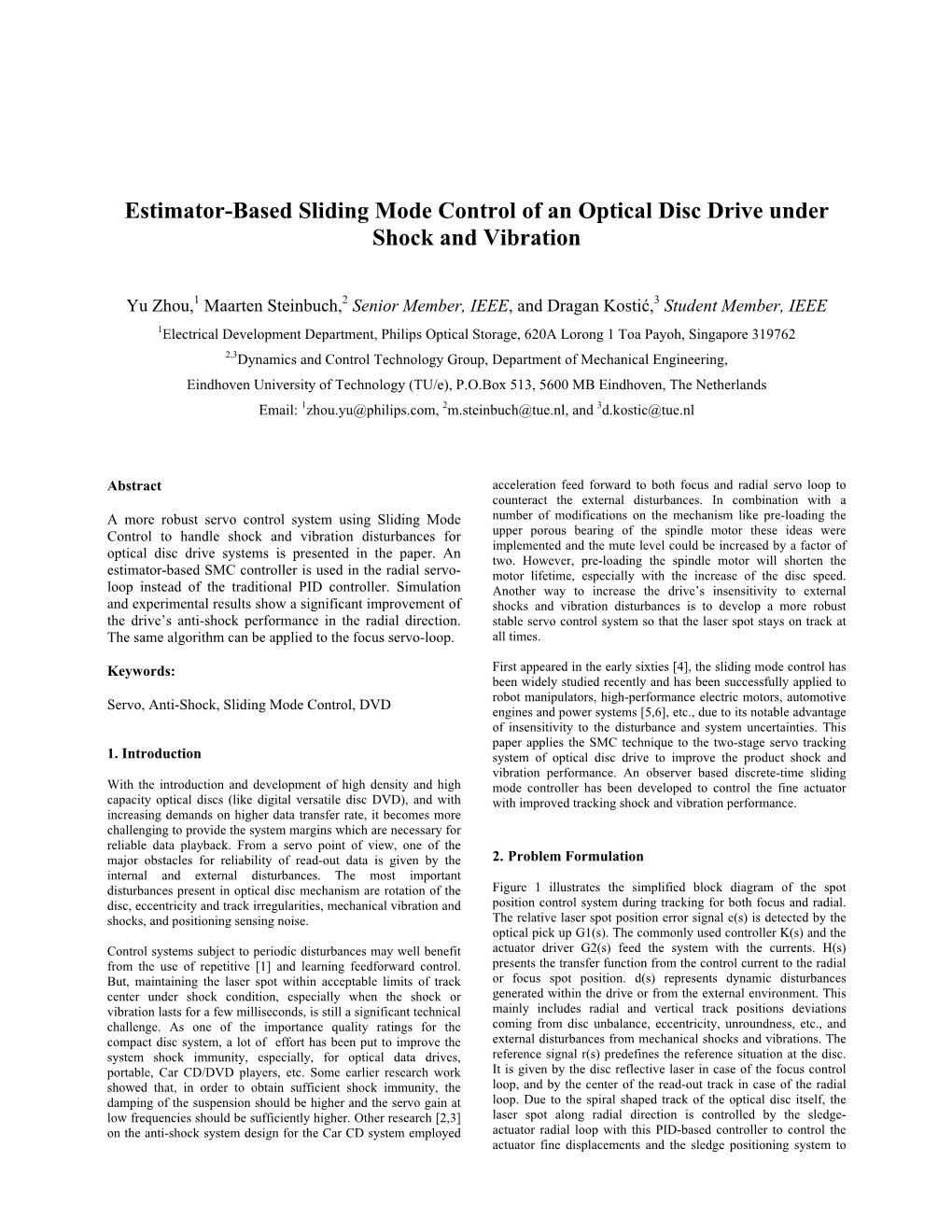
Load more
Recommended publications
-
Saf784x One Chip CD Audio Device with Integrated MP3/WMA Decoder Rev
SAF784x One chip CD audio device with integrated MP3/WMA decoder Rev. 02 — 9 May 2008 Product data sheet 1. General description The SAF784x is a single-chip solution CD audio decoder with on-chip MP3 and WMA decoding, digital servo, audio DAC, sample-rate converter, preamplifier, laser driver and integrated ARM7TDMI-S microprocessor. The device contains all of the required ROM and RAM, including an internal re-programmable Flash ROM, and is targeted at low-cost compressed audio CD applications. The design is a one-chip CD audio decoder IC, with additions to allow low-cost system implementation of MP3 and WMA decoding. 2. Features 2.1 Features n Channel decoder and digital servo n 32-bit embedded ARM7 RISC microprocessor supporting both 32-bit and 16-bit (‘Thumb’) instruction sets n Maximum ARM operating frequency of 76 MHz, equivalent to 68 MIPS n Decoding of compressed audio stream (MP3/WMA) on ARM7 core n All memories required for MP3/WMA decoding embedded on chip: combination of 130 kB mask-programmed internal program ROM (to reduce wait-states on high-speed code, e.g. decompression algorithms), 42 kB boot ROM, 64 kB of internal re-programmable Flash ROM (for simple re-programming of application code) 110 kB internal SRAM n Programmable clock frequency for ARM microprocessor - allowing users to trade-off power consumption and processing power depending on requirements n Block decoder hardware to perform C3 error correction n Sample-rate converter circuit to convert compressed audio sample rates (in the range 8 kHz to 48 kHz) to an output rate of 44.1 kHz n Microprocessor access to digital representations of the diode input signals from the optical pickup; the microprocessor can also generate the servo output signals RA, FO, SL, allowing the possibility of additional servo algorithms in software n Programmable PDM outputs (effectively sine and cosine) to allow use of stepper motor for sledge mechanism n Microprocessor access to audio streams, both from the internal CD decoder and an external stereo auxiliary input (e.g. -
Media Draft Appendix
Media Draft Appendix October, 2001 P C Hariharan Media Historical evidence for written records dates from about the middle of the third millennium BC. The writing is on media1 like a rock face, cave wall, clay tablets, papyrus scrolls and metallic discs. Writing, which was at first logographic, went through various stages such as ideography, polyphonic syllabary, monophonic syllabary and the very condensed alphabetic systems used by the major European languages today. The choice of the medium on which the writing was done has played a significant part in the development of writing. Thus, the Egyptians used hieroglyphic symbols for monumental and epigraphic writing, but began to adopt the slightly different hieratic form of it on papyri where it coexisted with hieroglyphics. Later, demotic was derived from hieratic for more popular uses. In writing systems based on the Greek and Roman alphabet, monumental writing made minimal use of uncials and there was often no space between words; a soft surface, and a stylus one does not have to hammer on, are conducive to cursive writing. Early scribes did not have a wide choice of media or writing instruments. Charcoal, pigments derived from mineral ores, awls and chisels have all been used on hard media. Cuneiform writing on clay tablets, and Egyptian hieroglyphic and hieratic writing on papyrus scrolls, permitted the use of a stylus made from reeds. These could be shaped and kept in writing trim by the scribe, and the knowledge and skill needed for their use was a cherished skill often as valuable as the knowledge of writing itself. -
DVD±R/RW INTERNAL DVD-REWRITABLE KIT Movie Video Music Data Photo
14488_DS-Panama.qxd 19-04-2004 14:42 Page 1 DVD±RDVD±R/RW INTERNAL DVD-REWRITABLE KIT movie video music data photo Product Code: PX-712A PX-712SA Interface: E-IDE (ATAPI) Serial ATA Data Buffer: 8MB Features: GigaRec: Record up to 900 MB with 80 minute CDs Record up to 1 GB with 99 minute CDs KING OF QUALITY SecuRec: Secure your data with password protection Silent Mode: For silent operation and longer durability Q-Check: C1/C2 error check, FE/TE check, Beta/Jitter check, PI/PO check Buffer Underrun Proof Technology: Stops Buffer Underrun Errors PoweRec Technology: For best quality recording VariRec: Make audio CDs with a personal touch Disk loading: Auto Tray Recording speed: CD-R: 48x: 7.200 kB/s DVD+R: 12x: 16.620 kB/s DVD-R: 6-8x: 8.310-11.080 kB/s 32x: 4.800 kB/s 6x-8x: 8.310-11.080 kB/s 6x: 8.310 kB/s 16x: 2.400 kB/s 6x: 8.310 kB/s 4x: 5.540 kB/s 8x: 1.200 kB/s 4x: 5.540 kB/s 2x 2.770 kB/s 4x: 600 kB/s 2.4x: 3.324 kB/s CD-RW: 24x: 3.600 kB/s DVD+RW: 4x: 5.540 kB/s DVD-RW: 4x: 5.540 kB/s 10x: 1.500 kB/s 2.4x: 3.324 kB/s 2x: 2.770 kB/s 4x: 600 kB/s 1x: 1.385 kB/s / Reading speed: CD: 48x: 7.2 MB/s DVD: 16x: 21.6 MB/s DVD±RDVD±R RW Access Time: CD: < 100ms DVD: < 150ms INTERNAL DVD-REWRITABLE KIT Firmware: FlashROM for fast and easy upgrades Compatible formats: CD (Read/Write) DVD (Read/Write) CD-DA, CD-Extra, CD-ROM Mode-1, CD-ROM DVD-ROM, DVD-Video, Multiborder, Multisession, DVD+VR, DVD-VR Mode-2, CD-ROM XA, Photo-CD, Video-CD, DVD+R/RW (Write) Multisession, CD TEXT, CD-I, CD+G, Mixed CD DVD+R:Disc at Once, Multisession, Incremental Recording 2 CD-R/RW (Write) DVD+RW: Sequential Write, Random Access Write YEAR Track at Once, Disc at Once, Packet Write (variable DVD-R/RW (Write) and fixed), Session at Once, CD-MRW (Mt. -
Sharp CD-PC1881V.Pdf
CD-PC1881V SERVICE MANUAL No. S0961CDPC1881 CD-PC1881V CD-PC1881V Video CD Mini System consisting of CD-PC1881V (main unit), CP-C881 (front speakers), CP-SW881 (sub woofer), NTSC/PAL GBOXS0026AWM1 (center speaker) and GBOXS0027AWM1 (surround speakers). • In the interests of user-safety the set should be restored to its original condition and only parts identical to those specified be Manufactured under license from Dolby Laboratories Licensing used. Corporation. DOLBY, the double-D symbol and “PRO LOGIC” are trademarks of Dolby Laboratories Licensing Corporation. CONTENTS Page SAFETY PRECAUTION FOR SERVICE MANUAL ........................................................................................................... 2 VOLTAGE SELECTION ..................................................................................................................................................... 2 AC POWER SUPPLY CORD AND AC PLUG ADAPTOR ................................................................................................. 2 SPECIFICATIONS .............................................................................................................................................................. 3 NAMES OF PARTS ........................................................................................................................................................... 4 OPERATION MANUAL ...................................................................................................................................................... 7 -
Cd Ripping Guide
CD RIPPING GUIDE for an average user Nikola Kasic Ver.7.0, March 2007 INTRODUCTION The time has come for me to rip my CD collection and put it on my home server. Actually, I tried to do it an year ago and was hit by the complexity of the subject and postponed it for some later time. I simply wasn't ready to dig deeply enough to master offsets, cue sheets, gaps and other issues. I thought it's just a matter of putting CD in the drive, choose file format and click button, and being overwhelmed with technical issues/choices I just gave up, being scared that if I make a wrong choice I'll have to re-rip all my collection later again. I don't consider myself an audiophile. My CD collection is about 150-200 CDs and I don't spend too much time listening music from CDs. My hi-fi (home theater) equipment is decent, but doesn't cost a fortune and has a dedicated room. However, it's good enough to make it easily noticeable when CD has errors, or music is ripped at low bitrate. Therefore, I prefer that equipment is limiting factor when enjoying music, rather then the music source quality. My main reason for moving music from CDs to files might sound strange. I had DVD jukebox (Sony, 200 places) which I was filling with CDs and only a few DVDs and really enjoyed not having to deal with CDs and cases all over the place. They were protected from kids and I had photo album with sleeves where I was storing CD covers, so it was easy to find disc number in jukebox. -
RF Amplifier for CD Players
CONTENTS 1. PROJECT STRUCTURE … … … … … … … … … … … … … … ....1 2. SCHEMATIC DIAGRAM STRUCTUR … … … … … … … … ....2 3. KSM1000BBC TECHNICAL DATA … … … … … … … … … … .3 4. MM1538 DATA BOOK (instead of FAN8038) … … … … . … ..31 5. CXA2550 DATA BOOK … … … … … … … … … … … … … . … .55 6. CXD3068Q DATA BOOK … … … … … … … … … … … … … … 68 7. SST39VF020 DATA BOOK … … … … … … … … … … … .. … .206 8. SPCA717A DATA BOOK … … … … … … … … … … … … . … .229 9. BH3541F/BH3544F DATA BOOK … … … … … … … … … … .257 10. MAIN BOARD TOP SILKSCREEN DIAGRAM … … … . … .265 11. MAIN BOARD BOTTOM SILKSCREEN DIAGRAM … … .266 12. SCHEMATIC DIAGRAM … … … … … … … … … … .. … … … .267 Dram 39VF020 (16M*4) (EPPROM) CXA2550N SPCA717A TV Set (RF AMP) CXD3068Q SPCA716A (TV Encoder) KSM1000BBC (SONY) BH3544 FAN8038 (DSP) (MPEG+MCU) WM8714 (Pickup) (Power AMP) (Driver) (D/A Converter) Line_controller BA4510 DC-DC (with Lcd display) (Filter) HEADPHONE (Converter) PV400S Project Structure Diagram Briefness introduce main part of system Pickup KSM-1000BBC CD-deck compatible with CD, CD-R, Can be playing 12 cm & 8cm Discs. RF AMP The CXA2550N is 3-Beam Head Amp IC of SONY, Compatible with CD, CD-R. Driver The FAN8038 is 4CH H bridge driver and DC-DC converter control circuit, battery charge control circuit on a chip. DSP The CXD3068Q is a digital signal processor LSI for CD player, this LSI incorporates a digital servo. MPEG The SPCA716A A /V decoder is a single-chip VCD decoder, this LSI incorporates a MCU. TV ENCODER The SPCA717A is a single-chip VCD encoder. D/A The WM8714 is -
Naimnet CD Ripping Engine
NaimNet CD Ripping Engine Steve Harris Naim Audio Southampton Road, Salisbury, SP1 2LN, England 1. Introduction data is reconstructed. Typically the Naim server will rip a This paper describes the issues of making quality copies CD in about 8 minutes, which is approximately 3 times of audio from a CD onto a hard drive. During the slower than burst mode, but gives a far higher level of development of the NaimNet Server and Hard Disk confidence that the extraction of data off the disc was Player range, it became very apparent that there was a done properly. large variation in systems for extracting audio data from CDs. From analysis the issues came down to: • Secure Mode ripping and techniques to get the audio samples off the disc • Copy protected and non compliant CDs • Offset Correction • Capturing track lead-in and lead-out • The CD mechanism and the firmware running inside it. 2. Burst Mode vs. Secure Mode Ripping PCs have shown that a CD can be copied to hard drive within a couple of minutes. Unfortunately, due to the weak error correction system implemented on audio Comparison of ripped track using Naim Rip versus CDs, the resultant audio files can be not bit-perfect. The Rip using a common media player issues can range from subtle but audible unnecessary interpolation to random clicks and pops when copying 3. Copy Protected CDs used CDs. This type of ripping is known as “Burst mode” One of the key requirements of a CD ripping engine is to and assumes that the sectors being read from the disc ensure that it can handle a wide range of real world CDs. -
MMC-2 Packet Commands for C/DVD Devices
Document Number 97-108R0 File name MM2-09r0.doc MMC-2 Packet Commands for C/DVD Devices Content: Clause 9 of SFF8090-.09 Packet Commands for C/DVD Devices Technical Editor: Ron Roberts Sierra-Pac Technology PO Box 2389 Shingle Springs, CA 95682 E-mail: [email protected] Doc No. 97108R0 9.0 Packet Commands for C/DVD Devices 9.1 Packet Command Implementation Requirements The first byte of all Command Packets shall contain an operation code as defined in this Specification. This specification is broken down into separate sections. This section describes all commands that are generic to all C/DVD Logical Units. There are separate sections for commands specific to DVD and CD media only. 9.1.1 FLUSH CACHE Command The FLUSH CACHE command ensures that logical blocks in the cache memory, have their most recent data value recorded on the physical medium. If a more recent data value for a logical block exists in the cache memory than on the physical medium, then the logical blocks from the cache memory shall be written to the physical medium. Logical blocks are not necessarily removed from the cache memory as a result of the cache flush operation. Note that this command does not make use of the range allowed in the SYNCHRONIZE CACHE, SCSI version of this command. This definition replaces the definition in the SCSI Standard. The Immediate bit shall be reserved and not used. As the only method to report errors from the flush operation when the immediate type operation is used would be to use deferred errors, this feature shall not be supported by Logical Units that comply with this specification. -
Introduction Features
INTRODUCTION This service manual provides a variety of service compatible computer. It can write as much as 700 information. Mbytes of digital data into CD-R/RW disc, and can It contains the mechanical structure of the CD- read as much as 650 Mbytes of digital data stored R/RW Drive and the electronic circuits in in a CD-ROM, CD-R and CD-RW disc. schematic form. This CD-R/RW Drive was This CD-R/RW Drive can easily meet the manufactured and assembled under our strict upcoming MPC level 3 specification, and its quality control standards and meets or exceeds Enhanced Intelligent Device Electronics (E-IDE) industry specifications and standards. and ATAPI interface allows Plug and play This CD-R/RW drive is an internal drive unit integration in the majority of today’s PCs without designed for use with IBM PC, HP Vectra, or the need of an additional interface card. FEATURES 1. General 1) Enhanced IDE interface. 2) Internal 5.25 inch, halfheight CD-R/RW Drive. 3) 2 Mbytes buffer memory. 4) Audio CD like tray loading of a disc without using a caddy. 5) Power loading and power ejecting of a disc. The disc can also be ejected manually. 6) Supports Power saving mode and Sleep mode. 7) Vertical and Horizontal operation. 8) Super Link Function. 2. Supported disc formats 1) Reads and writes data in each CD-ROM, CD-ROMXA, CD-I FMV, Video CD, and CD-EXTRA 2) Reads data in Photo CD (Single and Multi session). 3) Reads and writes standard CD-DA. -
CD and DVD Forensics.Pdf
422_CD_DVD_FM.qxd 11/8/06 6:20 PM Page i Visit us at www.syngress.com Syngress is committed to publishing high-quality books for IT Professionals and delivering those books in media and formats that fit the demands of our cus- tomers. We are also committed to extending the utility of the book you purchase via additional materials available from our Web site. SOLUTIONS WEB SITE To register your book, visit www.syngress.com/solutions. Once registered, you can access our [email protected] Web pages. There you may find an assortment of value-added features such as free e-books related to the topic of this book, URLs of related Web sites, FAQs from the book, corrections, and any updates from the author(s). ULTIMATE CDs Our Ultimate CD product line offers our readers budget-conscious compilations of some of our best-selling backlist titles in Adobe PDF form. These CDs are the perfect way to extend your reference library on key topics pertaining to your area of exper- tise, including Cisco Engineering, Microsoft Windows System Administration, CyberCrime Investigation, Open Source Security, and Firewall Configuration, to name a few. DOWNLOADABLE E-BOOKS For readers who can’t wait for hard copy, we offer most of our titles in download- able Adobe PDF form. These e-books are often available weeks before hard copies, and are priced affordably. SYNGRESS OUTLET Our outlet store at syngress.com features overstocked, out-of-print, or slightly hurt books at significant savings. SITE LICENSING Syngress has a well-established program for site licensing our e-books onto servers in corporations, educational institutions, and large organizations. -
Ripstation V4.4.13.0 Operating Manual
Ripstation v4.4.13.0 Operating Manual Ripstation A Division of Formats Unlimited, Inc 155 Sherwood Avenue Farmingdale, NY 11735 T: +1 631 249 9393 F: +1 631 249 9273 Authors: Robert Warnock & Patrick McGrath [email protected] www.mfdigital.com/techsupport.html © Copyright 2013 Copyright All rights within this document and related software belong to Formats Unlimited. Ripstation is a registered trademark of Formats Unlimited. BY USING THIS SOFTWARE YOU ARE AGREEING TO THESE TERMS AND CONDITIONS. This software (the SOFTWARE) is prepared as a solution to dealers, systems integrators. This SOFTWARE is provided as is and with warranty only as detailed in the applicable License agreement. Ripstation specifically disclaim to the fullest extent permitted by law all warranties, expressed or implied, including but not limited to implied warranties of merchantability and fitness for a particular purpose, with respect to this software. Ripstation shall have no liability including without limitation in negligence with respect to this software. Ripstation shall have no liability including without limitation in negligence with respect to any loss or damage directly or indirectly arising out of the use of this software. Without limiting the foregoing, Ripstation shall not be liable, including without limitation in negligence for any loss of profit, interruption of business, loss or damage to equipment or data, interruption of operations or any other damage, including but not limited to direct, special, incidental or consequential damages. This software must not be used for unauthorised duplication of CD's or any other works protected by copyright unless permitted by law. No license to infringe copyright is granted by the possession, installation and/ or use of this software. -
Datasheet Search Engine
INTEGRATED CIRCUITS DATA SHEET SAA7335 DSP for CD and DVD-ROM systems Preliminary specification 1997 Aug 11 File under Integrated Circuits, IC01 Philips Semiconductors Preliminary specification DSP for CD and DVD-ROM systems SAA7335 FEATURES • Compatibility with CD-I, CD-ROM, MPEG-video DVD-ROM and DVD-video applications • Designed for very high playback speeds • Typical CD-ROM operation up to n = 12, DVD-ROM to n = 1.9, maximum rates (tbf) • Matched filtering, quad-pass error correction In DVD modes double-pass C1-C2 error correction is used (C1-C2-C1-C2), overspeed audio playback function which is capable of correcting up to 5 C1 frame errors and included (up to 3 kbytes buffer) 16 C2 frame errors. • Lock-to-disc playback, Constant Angular Velocity The SAA7335 contains all the functions required to (CAV), pseudo-Constant Linear Velocity (CLV) and CLV decode an EFM or EFM+ HF signal directly from the laser motor control loops pre-amplifier, including analog front-end, PLL data • Interface to 32 kbytes SRAM for DVD error correction recovery, demodulation and error correction. The spindle and de-interleave motor interface provides both motor control signals from the demodulator and, in addition, contains a tachometer • Sub-code/ header processing for DVD and CD formats loop that accepts tachometer pulses from the motor unit. • Programmable HF equalizer The SAA7335 has two independent microcontroller • In DVD mode it is still compatible with Philips block interfaces. The first is a serial I2C-bus and the second is a decoders standard 8-bit multiplexed parallel interface. Both of these • Sub-CPU interface can be parallel or fast I2C-bus interfaces provide access to a total of 32 × 8-bit registers • On-chip clock multiplier.