Corporate Responsibility Report Responsibility Corporate
Total Page:16
File Type:pdf, Size:1020Kb
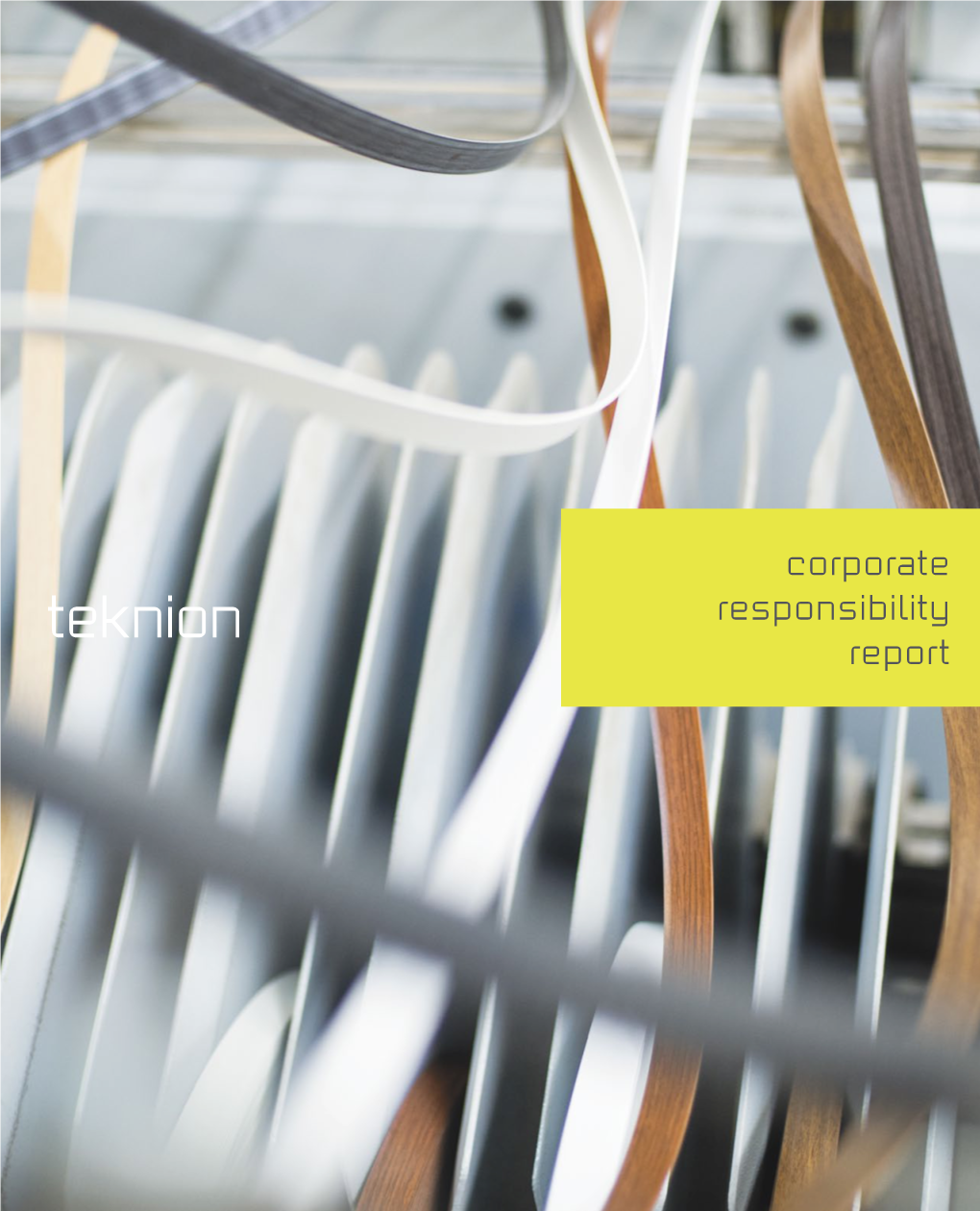
Load more
Recommended publications
-
Rapport Sur La Responsabilité De L'entreprise
rapport de l’entreprise sur la responsabilité rapport sur la responsabilité de l’entreprise PRÉSENTATION ET AXES D’INTERVENTION 2 Un message de David Feldberg 3 Un message de Scott Deugo 6 Environnement 18 Santé, sécurité et bien-être 26 Inclusion et diversité 32 Engagement et éducation 1 message de david feldberg UN MESSAGE DE DAVID, CHEF DE LA DIRECTION Chers amis, e suis heureux de vous dévoiler les résultats de nos plus récentes initiatives en matière de responsabilité J de l’entreprise. La publication du présent rapport me fait réaliser à quel point notre entreprise et notre industrie ont progressé au cours des quinze dernières années. En effet, nous et nos pairs avons réussi à placer la durabilité à un niveau qui constitue la référence pour les autres industries. Il devient par contre difficile d’avoir des objectifs plus ambitieux, car nous ne nous sommes pas contentés de cueillir les fruits à portée de main. Dans ce contexte, l’innovation passe par le respect continu des grandes valeurs qui sont au cœur de Teknion depuis plus de 30 ans : un esprit d’entreprise chez tous les employés et un leadership fort. Teknion a été fondée en 1983 par le Malgré notre croissance, nous sommes demeurés agiles et père de David, Saul Feldberg. Il n’avait accessibles. Nous avons nos propres usines de fabrication afin alors que trois employés et un espace de de pouvoir défier le statu quo et faire avancer nos objectifs de 3 000 pieds carrés. David est devenu durabilité au-delà des attentes. C’est grâce à cet engagement président et chef de la direction en 1994, envers notre culture, nos employés et nos usines que nous et a guidé la croissance de l’entreprise : poursuivrons sur notre lancée. -
For Immediate Release – August 20, 2009 What: United States Disc
For Immediate Release – August 20, 2009 What: United States Disc Golf Championship When: October 7 – 10, 2009 Where: Winthrop University Recreational Complex / Rock Hill, South Carolina What is at Stake: The title of United States Disc Golf Champion and more than $80,000 in prize money Who is Competing: Nearly 200 of the world’s top disc golf professionals, representing the United States, Canada, Sweden, Finland, Norway, and Japan Top Players to Watch: Nate Doss – 2-time World Champion, Defending US Champion Avery Jenkins – Current World and Japan Open Champion Ken Climo – 12-time World Champion, 5-time US Champion Barry Schultz – 2-time World Champion, 3-time US Champion David Feldberg – 2005 US Champion and 2008 World Champion Beneficiaries: Habitat for Humanity, Educational Disc Golf Experience, and York County Schools Corporate Partners: Innova Champion Discs, Rock Hill Coca-Cola Bottling Company, First Citizens Bank, Comer Distributing Company, Wingate by Wyndham, Kicker Audio, Keen Footwear Summary: For the 11th consecutive year, York County will host disc golf’s most prestigious event. Discs will soar hundreds of feet with pinpoint accuracy as competitors face the toughest course, the strongest field, for the most money, and under greater pressure than at any other event. The intense action at the US Championship is always dramatic and guaranteed fun for all ages. Ticket Information: Single Day Pass: $10.00 VIP Pass: $25.00 * Free Admission for Ages 12 and under * Free Admission for Winthrop University students with ID * Free Tournament Disc for first 1000 Single Day Ticket Holders Contact: Jonathan Poole, Event Director 800.476.3968 (toll free) 803.366.5028 (local) 704.724.1352 (cell) [email protected] www.usdgc.com . -
Will Schusterick 2010 US Champion
Will Schusterick 2011 2010 US Champion Cover Photo by: Tim Day, USDGC Photo by: USDGC Let the Good Times Fly Twenty-eight years after Innova introduced the first true golf disc, the company is still at the forefront of golf disc technology and equipment. When researching new discs and products, we still do our best work on the course like we’ve always done. We love to play and we want others to enjoy disc golf as much as we do. Having the right equipment helps foster that love. You can see our passion and commitment to the sport in our discs, targets and other disc golf supplies that both players and retailers have come to rely on. It is about more than just quality, it is about getting the right fit, the right feel and the right flight. This commitment continues even after the sale. Innova’s success in disc golf is made possible by the many customers, be it retailer or player, that consistently choose our products. For that, all of us at Innova Champion Discs say thank you, and invite all of you to be a part of another incredible year in disc golf. Thanks again. See you out on the course. Sincerely, Dave Dunipace and Harold Duvall Sarah Stanhope, 2010 Women’s World Champion Photo by: Scott Walker INNOVA GOLF DISCS What’s New 4-5 Discmania Golf Discs 6-7 Echo Star & R-Pro Discs 8-9 Signature Discs 10-11 Plastic & Disc Types 12-13 Disc Directory 14-15 Putt & Approach Discs 16-21 Mid-Range Discs 22-27 Fairway Drivers 28-31 Distance Drivers 32-41 Disc Golf DVDs 41 Disc Golf Sets 42 I-Dye Golf Discs 42 Glow Golf Discs 43 DX LITE Golf Discs -
Office Insight Ad#5
TM officeinsight 4 1706 all ignorance toboggans into know e.e. cummings West Edge Emergent Solutions: Where IIDA/NY Pioneering Design Langdon Wilson: Tomorrow’s Design and Organization Series: The High Line Design Meet Classroom Today Team Six design firms. On Tuesday, An office’s physical space should take Six environments. April 11, IIDA/NY into account the type of workplace A 600 sq.-ft. space. presented The business owners envision. This is And a whole lot of High Line De- what Dave Ancel, Ed.D, Emergent manufacturers. sign team, its’ Solutions, Inc., discussed at NeoCon second install- West in a seminar called “The Future ment in its Pio- neering Design Series. of Workplace Design.” Full Story, page 3 Full Story, page 5 Full Story, page 8 NeoCon West: Allsteel Break- fast Pritzker Prize Winner: Who? The Calibre Awards On the second day of NeoCon West, In the 28-year The 18th an- a rainy Tuesday in LA, Allsteel invited existence of nual IIDA industry professionals to a breakfast the $100,000 Southern Cal- at its downtown LA showroom (444 S. Pritzker Prize ifornia Cali- Flower Blvd.). for architec- bre Awards ture, it has took place on never gone to March 28th anyone as lit- at the Beverly tle known in- Hilton. ternationally as this year’s winner. It is safe to say that 99% or more of U.S. architects have never be- fore heard of Paulo Mendes da Rocha from Sao Paulo, Brazil. Full Story, page 10 Full Story, page 12 Special Feature Departments Business/Tech Material of the Week 4th Quarter Financial Review Noteworthy Re-Sited Financial Affairs Projects Industry Stock Prices Events Job Site officeinsightTM 04.17.06 2 of 18 Tickets are selling out fast for Boston, New York & Dallas. -
Registration Form
USDGC Headquarters Phone: 803.366.5028 2850 Commerce Drive Fax: 803.329.3472 Rock Hill, South Carolina 29730 Online: www.usdgc.com 2008 QUALIFYING PROCEDURES Section 1. Regional Qualifying Events A total of five (5) positions will be awarded at each Regional Qualifier. The top five (5) overall scores will earn an invitation to compete. Other divisions may be eligible to qualify if they are competing during identical days and course layouts as competitors in the Open Division. This is to be determined by each tournament director at his or her respective qualifying event. Any player finishing in the top five (5) who has qualified at an earlier event, or who has received an exemption or special invitation, will be excluded. Players shooting the next lowest score will become eligible. In case of a tie for the final position, the tournament director may: 1) hold a sudden death playoff to determine the winner, 2) award the spot to the player with the lowest final round score, or 3) award the spot to the player with the highest (current) PDGA Player Rating. Each position must be verified by the tournament director immediately following the event. A player may only qualify once via Regional Qualifying events. Players earning eligibility at Regional Qualifiers have 30 days to submit an application for entry along with full payment to guarantee their position in the field. This time period begins immediately following the completion of each event. Any player missing their deadline for entry automatically forfeits eligibility and may not re-qualify at Regional or Global Qualifying events. -
CITY of CHARLOTTE / OMNIA PARTNERS Furniture, Installation and Related Products and Services RFP#: 269-2019-105
CITY OF CHARLOTTE / OMNIA PARTNERS Furniture, Installation and Related Products and Services RFP#: 269-2019-105 August 6, 2019 TABLE OF CONTENTS 01 COVER LETTER 05 PRODUCT PROPOSAL Teknion Cover Letter Product Introductions 02 EXECUTIVE SUMMARY Sample Project Renderings Sample Project Isometric + Plan View Drawings Teknion’s Value Proposition Meet your Project Team 06 CONTRACTUAL REQUIREMENTS Meeting your Objectives Teknion Exceptions/Certifications 03 REQUIRED FORMS Teknion Terms and Conditions of Pricing/Install Required Form 2: Acknowledgement of Addenda Required Form 3: Proposal Submission Form Required Form 4: Pricing Worksheet Required Form 5: M/W/SBE Participation Form Required Form 6: Company Background Response Required Form 7: References Required Form 8: Certification Regarding Debarment Required Form 9: Byrd Anti‐Lobbying Certification Required Form 10: Environmental Purchasing Responses 04 OMNIA EXHIBITS Exhibit A: Response for National Cooperative Contract Exhibit F: Federal Funds Certification Exhibit G: Ownership Disclosure Form Exhibit G: Non‐Collusion Form Exhibit G: Affirmative Action Affidavit Exhibit G: Political Contribution Disclosure Form Exhibit G: Stockholder Disclosure Form Exhibit G: Certification of Non‐Involvement (Iran) Exhibit G: New Jersey Business Registration TEKNION Dear Ms. Carothers: 01 On behalf of the Teknion team, we welcome the opportunity to collaborate with Letter of your team to develop the best solution for the City of Charlotte and OMNIA Partners. As the City of Charlotte plans a change for their workspace, we assure Transmittal you, our proposed solutions address the priorities outlined within the RFP request. In conjunction with our dealer partners, Teknion will provide a comprehensive furniture program for the City of Charlotte as well as Participating Public Agencies. -
Registered Competitors City State Country 1 Ken Climo Clearwater FL
Registered Competitors City State Country 1 Ken Climo Clearwater FL USA 2 David Feldberg Springfield OR USA 3 Nikko Locastro Creve Coeur MO USA 4 Nate Doss Santa Cruz CA USA 5 Avery Jenkins Santa Cruz CA USA 6 Jussi Meresmaa Tampere Finland 7 Manabu Kajiyama 梶山 学 Japan 8 Will Schusterick Knoxville KY USA 9 Jay Reading Wimberley TX USA 10 David Greenwell Louisville KY USA 11 Yasushi Jitsuhiro 実広 泰史 Japan 12 Simon Feasey Auckland NEW ZEALAND 13 George Smith Columbia MO USA 14 Juho Rantalaiho Turku Finland 15 Tetsuya Kikuchi 菊地 哲也 Japan 16 Jesse Heinonen Tampere Finland 17 Scott Rief Louisville KY USA 18 Gregg Hosfeld Orlando FL USA 19 Kazuo shirai 白井 一夫 Japan 20 Michael Sullivan Toronto ONT Canada 21 Kari Vesala Helsinki Finland 22 John "Rumble" Pecunia Germantown WI USA 23 Terry Miller Pewaukee WI USA 24 Atsuhito kawasaki 川崎 篤人 Japan 25 David Munk Portland OR USA 26 takamichi Roppongi 六本木 孝道 Japan 27 Sam Ferrans Rancho CA USA Cucamonga 28 Justin Romito Portland OR USA 29 Bruce Hudson Topeka KS USA 30 Luke Butch Las Vegas NV USA 31 Glen Oliviero Delta BC Canada 32 Devin Brown Honolulu HI USA 33 Luke Morstad Calgary Alberta CANADA 34 Jeff Kennedy Las Vegas NV USA 35 Al Schwartz Makawao HI USA 36 Blake Baumgardner New Braunfels TX USA 37 Hidekatsu Sakai 坂井 秀勝 Japan 38 Dave Dunipace Rancho CA USA Cucamonga 39 Koji Takayama 高山 幸司 Japan 40 Nao Nasu Toronto ONT Canada 41 Dan Laitsch Surrey BC Canada 42 Petri Behm Helsinki Finland 43 Todd Hillrichs Grand Prairie TX USA 44 Leroy Jenkins Hinckley OH USA 45 Timo Kuusela Tampere Finland 46 Junnichi Sugibuchi 杉渕 純一 Japan 47 Hiroyuki Sato 佐藤 弘幸 Japan 48 Nobuya Kawai 河合 伸哉 Japan 49 Jack Lowe Kansas City MO USA 50 David Slater Toronto ONT Canada 51 Jeremy Brill Portland OR USA 52 Brian Graham Augusta GA USA 53 Nobuhiro Kawai 河合 伸浩 Japan 54 Michiyasu Morooka 諸岡 通容 Japan 55 Janne Kotka Kangasala Finland 56 Kai Saastamoinen Tampere Finland 57 Randy Strohan Vancover BC CANADA 58 Carl Garrity Ft. -
At Orgatec 2016 Alexander Girard, Shown And
10.31.16 GIVING VOICE TO THOSE WHO CREATE WORKPLACE DESIGN & FURNISHINGS At Orgatec 2016 The conventional wisdom as to why Orgatec, held each October in Cologne, Germany, is important for North Americans to attend has always been something like, “We go to Orgatec to see the trends in Europe because we know we’ll be seeing those things here in a few years.” As with much conventional wisdom, it no longer applies. There have been and still are significant cultural differences between the way we work on this side of the Atlantic and that side. But this year at Orgatec, there was significant evidence that the trends are now starting over here and migrating that way. FULL STORY ON PAGE 3… Alexander Girard, Shown and Documented In the middle decades of the 20th Century, Modern design was in danger of becoming too austere, too dominated by the expression of structure and rugged materials. Alexander Girard, in his wide-ranging design accomplishments, made sure that visual stimulation beyond the dictates of functionalism – bright colors, ornamental patterns, expressions of whimsy – could figure significantly in Modernist environments. His extensive accomplishments are now the subject of an exhibition at the Vitra Design Museum in Weil am Rhein, Germany, and an accompanying catalogue, both entitled “Alexander Girard: A Designer’s Universe.” FULL STORY ON PAGE 17… IIDANY 2016 Color Invasion: Carnevale di Venezia While the annual IIDANY Color Invasion is mostly a party, at its heart it is a fundraising celebration of creativity, inclusiveness and charity. The Color Invasion gives design professionals a CITED: fabulous night out in Manhattan, and a chance to do some good “SCIENCE DOES NOT KNOW for design students as well as children in need. -
2020 United States Disc Golf Championship®
2020 United States Disc Golf Championship® Winthrop University - Rock Hill, South Carolina Official Qualifying Procedure Revised 7.21.20 Overview All current, dues-paid members in good standing of the Professional Disc Golf Association are eligible to qualify for the 2020 United States Disc Golf Championship (USDGC). The USDGC is a PDGA Major, therefore all competitors must have a current PDGA membership and must have passed the PDGA Official certification exam in order to compete. Those gaining USDGC eligibility should register for the event as quickly as possible. Exempt from Qualifying and Special Invitations All previous United States Disc Golf Champions receive an automatic invitation to the 2020 USDGC: Ken Climo (1999, 2000, 2002, 2004, 2007) Paul McBeth (2015, 2018) Barry Schultz (2001, 2003, 2006) Steve Brinster (2013) Will Schusterick (2010, 2012, 2014) Nikko Locastro (2009) James Conrad (2019) Nate Doss (2008) Nathan Sexton (2017) David Feldberg (2005) Jeremy Koling (2016) The top 10 from the 2019 USDGC receive an automatic invitation to the 2020 USDGC: James Conrad (1) Eagle Wynne McMahon (7) Jeremy Koling (2) Nathan Queen (9) Nikko Locastro (2) Adam Hammes (10) Chris Clemons (4) Joel Freeman (10) Chris Dickerson (5) Nathan Sexton (10) Philo Brathwaite (6) Albert Tamm (10) Alex Russell (7) The following tournament champions will receive an automatic invitation to the 2020 USDGC: 2020 United States Amateur Champion (MA1) Event Status Pending 2020 Deaf National Champion (MPO) Event Status Pending 2020 Open Women World Champion (FPO) Event Canceled due to COVID-19 2020 United States Masters Champion (MP40) Event Canceled due to COVID-19 2020 Men’s Advanced World Champion (MA1) Event Canceled due to COVID-19 2020 United States Women’s Champion (FPO) Event Canceled for USDGC purposes 2020 Men’s Collegiate National Champion (MA1) Event Canceled for USDGC purposes Note: Exempt athletes must register on or before August 31, 2020. -
Dr. John G. Duesler, Jr. Media Relations (215)913-0569 [email protected]
Professional Disc Golf Association a t the International Disc Golf Center Wildwood Park , 3828 Dogwood Lane Appling, GA 30802 706- 261- 6342 o r 2 1 5 - 913- 0569 http://www.DiscGolfPlanet.tvpdga. c o m [email protected] Partners FOR IMMEDIATE RELEASE Contact: Dr. John G. Duesler, Jr. Media Relations (215)913-0569 [email protected] Europe’s Best to Challenge United States’ Best for Presidents Cup October 5th at Winthrop University in Rock Hill, South Carolina “Ryder Cup of Disc Golf” to Land on American Soil for First Time in Sport’s Most Prestigious Team Competition Emphasizing “Honor Above All” Appling, Georgia (September 21, 2010)--The emerging sport of disc golf is preparing to celebrate its global success at the Presidents Cup team competition on October 5, 2010 at Winthrop University in Rock Hill, South Carolina. Teams will be comprised of the top six male and top two female European qualifiers, who will face-off against their United States counterparts. The format is similar to traditional golf’s Ryder Cup, and each team will be playing for the honor of representing their nations. This event will kick-off a week-long schedule of competition, as the United States Disc Golf Championship will follow at Winthrop University October 6-9, 2010. “We are very excited about finally bringing this world-class event to America for the first time,” explained Jussi Meresmaa, the Presidents Cup tournament director from Tampere, Finland. “Though our European teams have been competitive in the first three years of the event, the disc golfers from the US have simply been better. -
Disc Golf Course Development
DISC GOLF COURSE DEVELOPMENT Disc golf course design, installation, and programs Your complete disc golf solution Presented by TM 2024 2006 Disc Golf is Inexpensive 2000 and Fun for Everyone. 1800 1515 1600 2003 Top 15 Reasons to Install a Disc Golf Course 1400 1255 2001 15. Disc golf is a low impact, 1348 2002 economical activity that can be added 1200 to most parks in as little as a week. 14. A disc golf course can be designed 1000 902 into under-utilized areas of your 1999 facility. 1001 2000 13. The process of organizing and 800 ordering everything you’ll need 634 1997 786 requires just a few easy choices. 1998 12. Disc golf tends to decrease 600 442 undesirable activity in under-utilized 1995 areas of a park. 543 349 1996 400 305 1993 11. Disc golf is a sport that everyone 1989 409 Innova-Champion can play, regardless of age, ability, or 224 1994 introduces the 180 1986 DISCatcher® Target 1983 328 gender. 1991 200 54 252 10. A single disc golf course can 1979 208 1987 1 1984 entertain ninety or more people at 1975 116 one time. 1982 1975 1980 1985 1990 1995 2000 2006 3 9. Disc golf is great for those not 1977 Disc golf course installations worldwide since 1975 interested in team sports, yet are driven to compete. Disc Golf is One of the World’s 8. Disc golf is a great lifetime sport. Fastest Growing Sports 7. Disc golf is so much fun, you won’t Every year well over 100 new even realize you are exercising. -
2020 United States Disc Golf Championship®
2020 United States Disc Golf Championship® Winthrop University - Rock Hill, South Carolina Official Qualifying Procedure Revised 9.7.20 Overview All current, dues-paid members in good standing of the Professional Disc Golf Association are eligible to qualify for the 2020 United States Disc Golf Championship (USDGC). The USDGC is a PDGA Major, therefore all competitors must have a current PDGA membership and must have passed the PDGA Official certification exam in order to compete. Those gaining USDGC eligibility should register for the event as quickly as possible. Exempt from Qualifying and Special Invitations All previous United States Disc Golf Champions receive an automatic invitation to the 2020 USDGC: Ken Climo (1999, 2000, 2002, 2004, 2007) Paul McBeth (2015, 2018) Barry Schultz (2001, 2003, 2006) Steve Brinster (2013) Will Schusterick (2010, 2012, 2014) Nikko Locastro (2009) James Conrad (2019) Nate Doss (2008) Nathan Sexton (2017) David Feldberg (2005) Jeremy Koling (2016) The top 10 from the 2019 USDGC receive an automatic invitation to the 2020 USDGC: James Conrad (1) Eagle Wynne McMahon (7) Jeremy Koling (2) Nathan Queen (9) Nikko Locastro (2) Adam Hammes (10) Chris Clemons (4) Joel Freeman (10) Chris Dickerson (5) Nathan Sexton (10) Philo Brathwaite (6) Albert Tamm (10) Alex Russell (7) The following tournament champions will receive an automatic invitation to the 2020 USDGC: 2020 United States Amateur Champion (MA1) Event Canceled due to COVID-19 2020 Deaf National Champion (MPO) Event Canceled due to COVID-19 2020 Open Women World Champion (FPO) Event Canceled due to COVID-19 2020 United States Masters Champion (MP40) Event Canceled due to COVID-19 2020 Men’s Advanced World Champion (MA1) Event Canceled due to COVID-19 2020 United States Women’s Champion (FPO) Event Canceled for USDGC purposes 2020 Men’s Collegiate National Champion (MA1) Event Canceled for USDGC purposes Note: Exempt athletes must register on or before August 31, 2020.