WIAC Draft V2.Indd
Total Page:16
File Type:pdf, Size:1020Kb
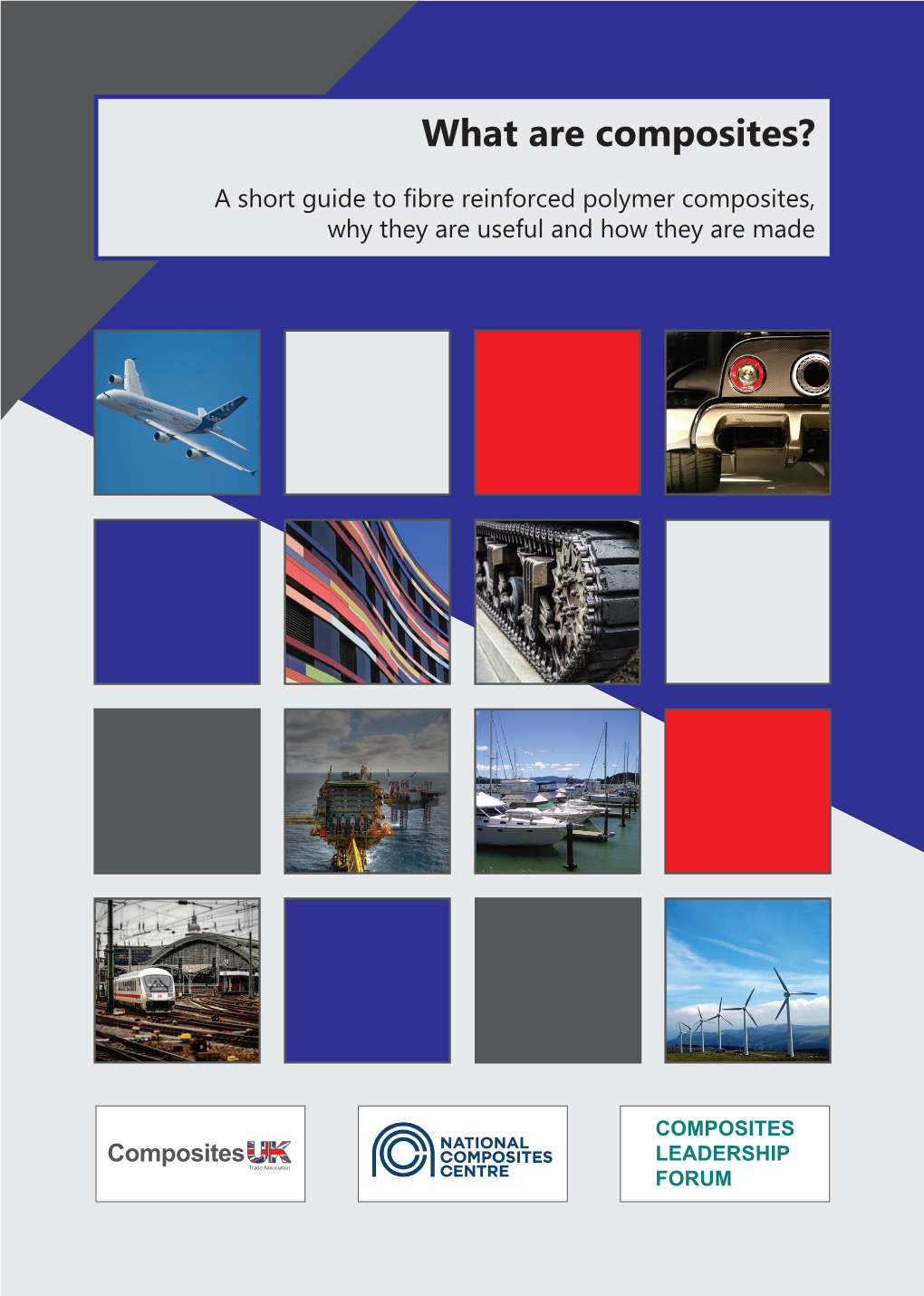
Load more
Recommended publications
-
Jec Composite Award Winners
BROCHURE AWARD ASIA 2009 ok:COUV 12P AWARD 6/10/09 11:33 Page 1 BROCHURE AWARD ASIA 2009 ok:COUV 12P AWARD 6/10/09 11:33 Page 2 Edito Innovation is a winning strategy! Ever increasingly, businesses are facing change like never before. Numerous driving forces to this change include a rapidly expanding marketplace and increasing competition, diversity amongst consumers, and availability to new forms of technology. Creativity and innovation are undoubtedly key to success! The 2009 JEC Asia Innovations bring ground-breaking improvements in new materials and processes with the following distinctions for new materials: - nanotech composites blended with organic nano-particles for a one-piece “jointless” ice hockey stick with the right combination of opposing features – flex, band, stiffness and whip, - loaded surface tissues with increased anti-flame-smoke-toxicity qualities particularly for mass transit and building applications, - polyester concrete made from selected fine sand hardened by unsaturated polyester resin for production of pipes with excellent corrosion resistance and earthquake-proof properties, - vegetal fibers or matrix such as renewable cellulose reinforcement for a brand new environment-friendly surfboard. Concerning thermoplastics or thermosets processes: - a new technique of laser-assisted thermoplastic tape placement enabling the fully automatic production of light- weight components for the aerospace industry, - a new cost-effective application for radio telescopes which clearly demonstrates the potential of composite materials for the construction of radio antennas in the size range of 10 m to 15 m, - an application for wholly new-designed rail insulators for the airport rail lines connecting airports to downtown, - a new winding process for non axi-symmetric profiles with integral-end dome winding for tankers, - an application featuring special hulls made entirely out of carbon and glass fibers composites for ultra-fast interceptor boats. -
Analysis of Failure Pressures of Composite Cylinders with a Polymer Liner of Type IV CNG Vessels A
World Academy of Science, Engineering and Technology International Journal of Mechanical and Mechatronics Engineering Vol:7, No:1, 2013 Analysis of Failure Pressures of Composite Cylinders with a Polymer Liner of Type IV CNG Vessels A. Hocine, A. Ghouaoula, F. Kara Achira, and S.M. Medjdoub Gas storage consists of keeping the gas at room temperature Abstract—The present study deals with the analysis of the under pressure in a cylinder. The first tanks were type I, cylindrical part of a CNG storage vessel, combining a plastic entirely of metal would be too heavy for storage of CNG. liner and an over wrapped filament wound composite. Three kind of Storage cylinders for compressed natural gas (CNG) used in polymer are used in the present analysis: High density Polyethylene vehicles are pressure vessels that have been traditionally HDPE, Light low density Polyethylene LLDPE and finally blend of LLDPE/HDPE. The effect of the mechanical properties on the produced using isotropic materials, such as steel and aluminum behavior of type IV vessel may be then investigated. In the present [2]. paper, the effect of the order of the circumferential winding on the A notable improvement of this first technology is to stacking sequence may be then investigated. Based on mechanical reinforce the cylinder by filament winding composite just on considerations, the present model provides an exact solution for the cylindrical section (type II). Currently, two solutions have stresses and deformations on the cylindrical section of the given good satisfaction tanks type III metallic liner - vessel under thermo-mechanical static loading. The result show a good behavior of HDPE liner compared to the other plastic materials. -
Metalized Plastic Articles and Methods Thereof Metallisierte Kunststoffartikel Und Verfahren Dafür Articles Plastiques Métallisés Et Procédés Associés
(19) TZZ Z¥_T (11) EP 2 420 593 B1 (12) EUROPEAN PATENT SPECIFICATION (45) Date of publication and mention (51) Int Cl.: of the grant of the patent: C23C 18/20 (2006.01) H05K 3/42 (2006.01) 03.04.2013 Bulletin 2013/14 C23C 18/32 (2006.01) C23C 18/38 (2006.01) H05K 3/38 (2006.01) H05K 3/46 (2006.01) (2006.01) (2006.01) (21) Application number: 11173897.7 C25D 5/12 C25D 5/56 H05K 3/18 (2006.01) (22) Date of filing: 14.07.2011 (54) Metalized Plastic Articles and Methods Thereof Metallisierte Kunststoffartikel und Verfahren dafür Articles plastiques métallisés et procédés associés (84) Designated Contracting States: •ZHOU,Liang AL AT BE BG CH CY CZ DE DK EE ES FI FR GB 518118 Shenzhen (CN) GR HR HU IE IS IT LI LT LU LV MC MK MT NL NO • MIAO, Weifeng PL PT RO RS SE SI SK SM TR 518118 Shenzhen (CN) • ZHANG, Xiong (30) Priority: 19.08.2010 CN 201010260236 518118 Shenzhen (CN) (43) Date of publication of application: (74) Representative: Gulde Hengelhaupt Ziebig & 22.02.2012 Bulletin 2012/08 Schneider Patentanwälte - Rechtsanwälte (73) Proprietor: BYD Company Limited Wallstrasse 58/59 Shenzhen 518118 (CN) 10179 Berlin (DE) (72) Inventors: (56) References cited: • GONG, Qing EP-A1- 1 650 249 US-A- 3 546 011 518118 Shenzhen, (CN) US-A- 4 767 665 US-A- 5 162 144 Note: Within nine months of the publication of the mention of the grant of the European patent in the European Patent Bulletin, any person may give notice to the European Patent Office of opposition to that patent, in accordance with the Implementing Regulations. -
Commingled Yarn Spinning for Thermoplastic/Glass Fiber Composites
fibers Article Commingled Yarn Spinning for Thermoplastic/Glass Fiber Composites Niclas Wiegand and Edith Mäder * Leibniz-Institut für Polymerforschung Dresden e.V., Dresden D-01069, Germany; [email protected] * Correspondence: [email protected]; Tel.: +49-351-465-8305 Academic Editor: Stephen C. Bondy Received: 25 April 2017; Accepted: 17 July 2017; Published: 20 July 2017 Abstract: Online commingled yarns were spun with three different polymeric matrices, namely polypropylene (PP), polyamide (PA) and polylactic acid (PLA) and glass fibers. Tailored sizings were applied for the three matrices and the resulting mechanical performance of unidirectional composites was evaluated and compared. Significant improvements in the fiber/matrix bonding were achieved by employed sizing chemistry in order to achieve multifunctional interphases. The pure silane coupling agents provide the best performance for all matrices investigated. However, an additional film former has to be added in order to achieve fiber processing. Film formers compatible to the matrices investigated were adapted. The consolidation behavior during isothermal molding was investigated for polypropylene matrix. Different fiber volume contents could be realized and the resulting mechanical properties were tested. Keywords: commingled yarns; Polypropylene; Polyamide; Polylactic Acid; sizing; glass fibers; thermoplastic composites; multifunctional interphase 1. Introduction Thermoplastic polymer matrices enable to manufacture composites at very short cycle times which makes them feasible for high volume productions. In contrast to thermosetting composites, they exhibit better impact resistance, higher toughness, recyclability and in the case of polylactic acid (PLA), even biodegradability. However, fiber impregnation is more difficult due to the high melt viscosity of the thermoplastic matrix. Different impregnation techniques have been proposed and performed. -
OPPORTURI Unt
US010173410B2 (12 ) United States Patent ( 10 ) Patent No. : US 10 , 173 ,410 B2 Nardiello et al. (45 ) Date of Patent: Jan . 8 , 2019 ( 54 ) DEVICE AND METHOD FOR 3D PRINTING ( 56 ) References Cited WITH LONG - FIBER REINFORCEMENT U . S . PATENT DOCUMENTS (71 ) Applicant: Northrop Grumman Systems 2 , 800 ,683 A * 7 / 1957 Teichmann .. B29C 47 / 023 Corporation , Falls Church , VA (US ) 156 / 143 (72 ) Inventors : Jerrell A . Nardiello , Hicksville , NY 3 , 375 ,550 A * 4 / 1968 Klein . .. .. .. B29C 47 /023 (US ) ; Robert J . Christ , Brentwood , 425 / 114 NY (US ) ; John A . Crawford , Miller (Continued ) Place , NY (US ) ; John S . Madsen , Commack , NY (US ) FOREIGN PATENT DOCUMENTS ( 73 ) Assignee : Northrop Grumman Systems DE 102010049195 11 /2012 Corporation , Falls Church , VA (US ) OTHER PUBLICATIONS ( * ) Notice : Subject to any disclaimer , the term of this Gray IV , R . et al ; Effects of processing conditions on short TLCP patent is extended or adjusted under 35 fiber reinforced FDM parts ; Rapid Prototyping Journal, vol . 4 , No. U . S . C . 154 ( b ) by 444 days . 1 , 1998 ; pp . 14 - 25 ; MCB University Press — ISSN 1355 -2546 . (21 ) Appl. No. : 14 / 961 ,989 ( Continued ) ( 22 ) Filed : Dec . 8 , 2015 Primary Examiner — Yogendra N Gupta Assistant Examiner — Emmanuel S Luk (65 ) Prior Publication Data ( 74 ) Attorney , Agent, or Firm — Patti & Malvone Law US 2017 /0157851 A1 Jun . 8 , 2017 Group , LLC (51 ) Int . Ci. ( 57 ) ABSTRACT B29C 67 / 00 ( 2017 .01 ) A process and device for 3D printing parts incorporating B33Y 10 /00 ( 2015 .01 ) long - fiber reinforcements in an advanced composite mate rial is disclosed . A nozzle for a 3D printing device receives (Continued ) a polymer material and a reinforcing fiber through separate ( 52 ) U .S . -
Additives for Thermoset Composites
C M Y K Contacts worldwide Additives for Thermoset Composites Asia BASF East Asia Regional Headquarters Ltd. Formulation Additives by BASF 45/F, Jardine House No. 1 Connaught Place Central Hong Kong [email protected] Europe BASF SE Formulation Additives 67056 Ludwigshafen Germany [email protected] North America BASF Corporation 11501 Steele Creek Road Charlotte, NC 28273 USA [email protected] South America BASF S.A. Rochaverá - Crystal Tower Av. das Naçoes Unidas, 14.171 Morumbi - São Paulo-SP Brazil [email protected] BASF SE ED2 0319e Formulation Additives Dispersions & Pigments Division 67056 Ludwigshafen Germany www.basf.com/formulation-additives The data contained in this publication are based on our current knowledge and experience. In view of the many factors that may affect processing and application of our product, these data do not relieve processors from carrying out their own investigations and tests; neither do these data imply any guarantee of certain properties, nor the suitability of the product for a specific purpose. Any descriptions, drawings, photographs, data, proportions, weights, etc. given herein may change without prior information and do not constitute the agreed contractual quality of the product. The agreed contractual quality of the product results exclusively from the statements made in the product specification. It is the responsibility of the recipient of our product to ensure that any proprietary rights and existing laws and legislation are observed. When handling these products, advice and information given in the safety data sheet must be complied with. Further, protective and workplace hygiene measures adequate for handling chemicals must be observed. -
Manufacturing Flat and Cylindrical Laminates and Built up Structure Using Automated Thermoplastic Tape Laying, Fiber Placement, and Filament Winding
MANUFACTURING FLAT AND CYLINDRICAL LAMINATES AND BUILT UP STRUCTURE USING AUTOMATED THERMOPLASTIC TAPE LAYING, FIBER PLACEMENT, AND FILAMENT WINDING Mark A. Lamontia, Steve B. Funck, Mark B. Gruber, Ralph D. Cope, PhD, Brian J. Waibel, and Nanette M. Gopez Accudyne Systems, Inc., 134B Sandy Drive, Newark, DE, USA19713 ABSTRACT Automated thermoplastic filament winding, tape laying, and fiber placement have been demonstrated by manufacturing thermoplastic-reinforced carbon-fiber laminates and stiffened parts using in situ consolidation. Material feedstock requirements were met with polyimide and polyetherketone placement-grade tows and tapes from Cytec Engineered Materials. The thermoplastic in situ heads integrate material deposition with a polymer process that combines preheating, generation of layer-to-layer intimate contact, interlayer bond development by reptation healing, consolidation/squeeze flow, and freezing/void compression in the laminate. The in situ winding process combines sequential [0 °] tape laying and filament winding to fabricate [0 °/90 °] and [0 °/90 °/±θ°] monocoque and ring-stiffened cylinders from polyetherketone composite material systems with outstanding property translation. Finished parts and systems have been commercialized. The automated fiber placement process has been developed for flat skins with twelve simultaneous 6.35mm (0.25-in) tow placement or one 76mm (3-in) tape placement capability. Thermoplastic and cross-linking composites and coated titanium foils have been placed. A large number of demonstration parts have been fabricated including flat laminates with and without padups, stringer- and honeycomb-stiffened skins, and TiGr (interleaved Titanium and Gr aphite/thermoplastic layers) skins alone or sandwiching Titanium-honeycomb core. In general, 85% to 100% property translation is available with in situ processing, and 100% if post-autoclaved cured, for example to advance a cross-linking polyimide resin. -
Shaping Processes for Polymer Matrix Composites (PMC) General
ME477 Fall 2004 General Classification Hand lay-up Automated Shaping Processes for Open Mold Tape laying Compression Closed Mold Polymer Matrix Composites Continuous- Molding Fibers Pultrusion Resin Transfer Molding (PMC) FRP Filament Composites Winding Tube rolling Others 1. Starting Materials for PMC Metals Shaping Spray-up Process Open Mold Compression 2. Open Mold Processes Molding Ceramics Polymer Transfer 3. Closed Mold Processes Closed Mold Molding Short- Injection 4. Filament Winding Fibers Molding Glass Rubber Centrifugal 5. Pultrusion Processes Casting Others Continuous 6. Other PMC Shaping Proceess Laminating 1 2 Polymer and Reinforcement Combining • In a PMC, polymer and reinforcing phase (fibers, • Prepreg Prepregs particles and flakes) are processed separately – Polymers – Thermoplastics, Thermosets on most molding compounds & Elastomers with carbon black – Reinforcing fibers Resin Bath • Roving(Untwisted strands)-> Woven roving • Sheet Molding Compounds • Yarn (Twisted strands)-> Cloth (SMC) – polymer sheet • Mat – a felt made of randomly oriented short fibers cuts to • Thick Molding Compounds + + shape called preforms which are impregnate with resin. (TMC) – thicker polymer + + • They are subsequently combined into sheet composites. • Bulk Molding Compounds (BMC) – polymer billets + + – Combining Matrix and Reinforcement in a intermediated form called prepregs or sheet-, thick- SMC, TMC & BMC or bulk-molding compounds before shaping. 3 4 Open Mold Process Hand Lay-up & Spray-up • Mold – Negative or positive mold • Lay-up -
Marabu Pad Printing Ink Chart
MARABU PAD PRINTING INK CHART PAD PAD PAD PAD PAD-SCREEN PAD-SCREEN PAD PAD PAD-SCREEN PAD-SCREEN PAD-SCREEN PAD-SCREEN PAD-SCREEN SCREEN-PAD TAMPAFLEX TAMPAGRAPH TAMPASTAR TAMPAPLUS TAMPAPOL TAMPAPUR TAMPATECH TAMPACURE GLASS INK LIBRASTAR MARAFLEX MARALOX MARAPROP MARAPUR PRODUCT TPF TPGR TPR TPL TPY TPU TPT TPC (UV) GL HF FX LX PP PU INFORMATION DEGREE OF HIGH GLOSS GLOSSY GLOSSY GLOSSY GLOSSY HIGH GLOSS HIGH GLOSS HIGH GLOSS SATIN GLOSS GLOSSY SATIN GLOSS HIGH GLOSS SATIN GLOSS HIGH GLOSS GLOSS DRYING FAST FAST VERY FAST VERY FAST FAST MEDIUM MEDIUM FAST MEDIUM FAST FAST SLOW FAST SLOW TYPE OF DRYING REACTIVE PHYSICAL PHYSICAL PHYSICAL PHYSICAL REACTIVE REACTIVE REACTIVE REACTIVE PHYSICAL PHYSICAL PHYSICAL PHYSICAL REACTIVE INK SYSTEM - 2C 1C or 2C 1C OR 2C 1C or 2C 1C or 2C 2C 2C 1C or 2C 2C 1C or 2C 1C 1C 1C 2C COMPONENTS RUB AND INTERIOR AND CHEMICAL CHEMICAL GASOLINE GASOLINE GASOLINE DISHWASHER SCRATCH, OUTDOOR RESISTANCE CHEMICALS MECHANICAL CHEMICALS CHEMICALS ALCOHOL MEDIUM OUTDOOR HIGH FLEXIBILITY ALCOHOL ALCOHOL ALCOHOL ALCOHOL PROOF DOMESTIC USECHEMICAL RESISTANT CLEANERS AND MECHANICAL THERMOPLASTIC UNIVERSAL USE, GOOD HALOGEN FREE, EXCELLENT GOOD GOOD FADE AND ELASTOMERS, GOOD DISHWASHER NON PRE- QUALITIES UNIVERSAL USE UNIVERSAL USE GOOD HIGH RESISTANCE PRINTABILITY, HIGH RESISTANCE CANADIAN LAMINATING PRINTABILITY, WEATHER SOFT-TOUCH RESISTANCE PROOF TREATED PP PRINTABILITY LONG POT LIFE STANDARDS ABILITY VERY MILD RESISTANCE VARNISHES AUXILLIARIES TPF TPGR TPR TPL TPY TPU TPT TPC (UV) GL HF FX LX PP PU TPV,TPV2,TPV3 -
Biodegradable Continuous Fibre Reinforced Composites Based on Hybrid Yarns
TH 18 INTERNATIONAL CONFERENCE ON COMPOSITE MATERIALS BIODEGRADABLE CONTINUOUS FIBRE REINFORCED COMPOSITES BASED ON HYBRID YARNS T. Lehtonen1*, J. Tuominen1, J. Rausch2, E. Mäder2* 1 Vivoxid Ltd., Turku, Finland 2 Dept. Composite Materials, Leibniz-Institut für Polymerforschung Dresden e.V. (Leibniz Institute of Polymer Research), Dresden, Germany * Corresponding author ([email protected]), ([email protected]) Keywords: biodegradability, glass fibre, polylactide, mechanical properties 1 Introduction medical device sector as well as manufacture of “green” composites for car and commodity plastic During the last four decades the biodegradable industries. polymers have found their place in special applications in biomedical and technical fields. [1-4] The hybrid yarn technology is one method to However, their worldwide production volumes are manufacture continuous fibre reinforced thermoplas- still marginal compared with non-biodegradable tics [8]. Its main advantages are related to the high polymers. One of the major restricting factors for the degree of flexibility regarding the final shape of the wider use of biodegradable polymers in the field of composites as well as to the high fibre volume load bearing medical devices, packaging, and contents and the correspondingly high mechanical consumer goods is the lack of mechanical properties properties of the composites. and cost of goods. For instance, one of the most In this work latest results of processing continuous widely used biodegradable polymers, polylactide GF/PLA hybrid yarns, composites thereof and (PLA), for non-load bearing medical devices, fibres, mechanical as well as interface properties will be nonwovens, films, and disposable articles is a presented. comparably hard and brittle material. Regarding to mechanical properties of PLA no significant improvements have been achieved since the 2 Experimental development of self-reinforced PLA [5]. -
ITEM 6 Composite Production Composite
ITEM 6 Composite Production Composite CATEGORY II ~ ITEM 6 CATEGORY Production Produced by Equipment, “technical-data” and procedures for the production of struc- companies in tural composites usable in the systems in Item 1 as follows and specially designed components, and accessories and specially designed software • France therefor: • Germany (a) Filament winding machines of which the motions for positioning, • Italy wrapping and winding fibres can be coordinated and programmed in • Japan three or more axes, designed to fabricate composite structures or • Netherlands laminates from fibrous or filamentary materials, and coordinating and • Russia programming controls; • United Kingdom • United States Note to Item 6: (1) Examples of components and accessories for the machines covered by this entry are: moulds, mandrels, dies, fixtures and tooling for the preform pressing, curing, casting, sintering or bonding of composite structures, laminates and manufactures thereof. Nature and Purpose: Filament winding machines lay strong fibers coated with an epoxy or polyester resin onto rotating mandrels in prescribed pat- terns to create high strength-to-weight ratio composite parts. The winding machines look and operate like a lathe. After the winding operation is com- pleted, the part requires autoclave and hydroclave curing. Method of Operation: First, a mandrel is built to form the proper inner di- mensions required by the part to be created. The mandrel is mounted on the filament winding machine and rotated. As it spins, it draws continuous fiber from supply spools through an epoxy or polyester resin bath and onto the outer surface of the mandrel. After winding, the mandrel and the part built up on it are removed from the machine, and the part is allowed to cure be- fore the mandrel is removed in one of a variety of ways. -
Composites Manufacturing
Composites Manufacturing ME 338: Manufacturing Processes II Instructor: Ramesh Singh; Notes: Prof. Singh/ Ganesh Soni 1 Composites ME 338: Manufacturing Processes II Instructor: Ramesh Singh; Notes: Prof. Singh/ Ganesh Soni 2 What is a composite Material? • Two or more chemically distinct materials combined to have improved properties – Natural/synthetic – Wood is a natural composite of cellulose fiber and lignin. • Cellulose provides strength and the lignin is the "glue" that bonds and stabilizes the fiber. • Bamboo is a wood with hollow cylindrical shape which results in a very light yet stiff structure. Composite fishing poles and golf club shafts copy this design. – The ancient Egyptians manufactured composites! • Adobe bricks are a good example which was a combination of mud and straw ME 338: Manufacturing Processes II Instructor: Ramesh Singh; Notes: Prof. Singh/ Ganesh Soni 3 COMPOSITES A composite material consists of two phases: • Primary – Forms the matrix within which the secondary phase is imbedded – Any of three basic material types: polymers, metals, or ceramics • Secondary – Referred to as the imbedded phase or called the reinforcing agent – Serves to strengthen the composite (fibers, particles, etc.) – Can be one of the three basic materials or an element such as carbon or boron ME 338: Manufacturing Processes II Instructor: Ramesh Singh; Notes: Prof. Singh/ Ganesh Soni 4 Types of composite materials There are five basic types of composite materials: Fiber , particle , flake , laminar or layered and filled composites. ME