Harvesting, Drying, and Storing Malting Barley
Total Page:16
File Type:pdf, Size:1020Kb
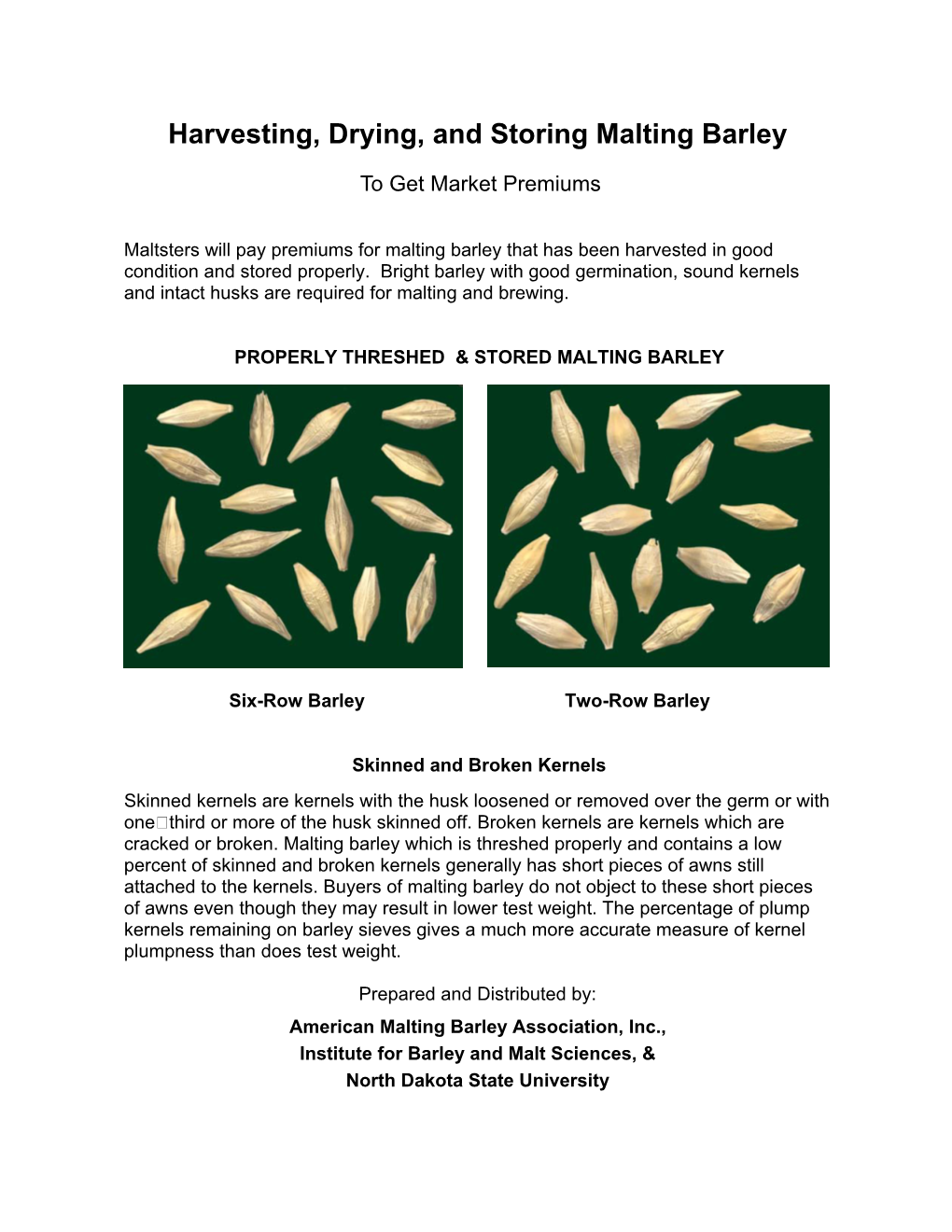
Load more
Recommended publications
-
Classification of Wheat Varieties Grown in the United States in 1949
Technical Bulletin No. 1083 March 1954 /' Classification of Wheat Varieties Grown in the United States in 1949 By B. B. BAYLES Principal Agronomist and J. ALLEN CLARK Senior Agronomist Field Crops Research Bran~h United States Department of Agriculture, Washingtc'll, D. C. For gale by the Superintendent of Documents, WaehinMlon 25, D. C. • Price 70 cent. 66 TECHNICAL BULLETIN 1083, U. S. DEPT. OF AGRICULTURE to strong; spike apically awnleted, fusi Distribution.-Estimated area in 1949, form, middense to dense, inclined; glumes 452,427 acres (fig. 32). glabrous, white with black stripes, mid long, wide; shoulders wide, oblique to LOFTHOUSE square; beaks mid wide, obtuse, 0.5 mm. long; awnlets 3 to 10 mm. long, some Description.-Plant winter habit mid tim,;s incurved; kernels red, midlong, se:;tson, midtall; ste:n white,. midstrong; semlhard, ovate; germ midsized· crease s~lke awnleted, fusIform, mlddense, in midwide, middeep; cheeks rounded; brush cllped_; glumes glabrous, white, midlong, midsized, midlong. ml~wlde; should~rs wanting to narrow, History.-Kanqueen (C. 1. 12762) was oblIque; beaks WIde, obtuse, 1 mm. long; developed by Earl G. Clark, the farmer awnlets several, 5 to 30 mill. long; wheat breeder of Sedgwick, Kans., and kernels red, mic_llon.g, sof~, ovate; germ first offered for sale in the fall of 1949. small; crease mldwlde, mlddeep; cheeks It was sold in small lots in all sections usually angular; brush small, midlong. of Kansas. There is some confusion as to the VIGO identity of this variety. It frequently has been referred to as white-kerneled Description.-Plant' winter habit, mid and often is confused with the Kofod variety. -
Gluten Free Grains
Gluten-free Grains A demand-and-supply analysis of prospects for the Australian health grains industry A report for the Rural Industries Research and Development Corporation by Grant Vinning and Greg McMahon Asian Markets Research Pty Ltd September 2006 RIRDC publication no. 05/011 RIRDC project no. AMR–10A © 2006 Rural Industries Research and Development Corporation All rights reserved ISBN 1 74151 110 0 ISSN 1440-6845 Gluten-free Grains: a demand-and-supply analysis of prospects for the Australian grains industry Publication no. 05/011 Project no. AMR–10A The information contained in this publication is intended for general use to assist public knowledge and discussion and to help improve the development of sustainable industries. The information should not be relied upon for the purpose of a particular matter. Specialist and/or appropriate legal advice should be obtained before any action or decision is taken on the basis of any material in this document. The Commonwealth of Australia, the Rural Industries Research and Development Corporation, and the authors or contributors do not assume liability of any kind whatsoever resulting from any person’s use of or reliance on the content of this document. This publication is copyright. However, RIRDC encourages wide dissemination of its research results, providing the Corporation is clearly acknowledged. For any inquiries concerning reproduction, telephone the Publications Manager on 02 6272 3186. Researcher contact details Grant Vinning Greg McMahon Asian Markets Research Asian Markets Research 22 Kersley Road 22 Kersley Road KENMORE QLD 4069 KENMORE QLD 4069 Phone: 07 3378 0042 Phone: 07 3378 0042 Email: [email protected] Email: [email protected] In submitting this report, the researchers have agreed to RIRDC publishing this material in its edited form. -
The Relative Ripening Rate of the Grain and Straw of Ten Varieties Of
The relative ripening rate of the grain and straw of ten varieties of oats by Frank C Petr A THESIS Submitted to the Graduate Faculty in partial fulfillment of the requirements for the degree of Master of Science in Agronomy Montana State University © Copyright by Frank C Petr (1952) Abstract: Ten varieties of oats were compared for rapidity of dessication of the straw following maturity of the grain at Bozeman in 1951. Moisture content of the grain and straw was determined at nine consecutive 3-day intervals commencing 30 days after the heading date of each variety. The oat varieties were assigned maturity ratings of early, midearly, midseason, midlate, and late on the basis of heading date. The moisture content of the straw decreased slowly at successive stages and remained relatively high for all varieties throughout the experiment. No significantr differences in straw moisture at the final harvest were evident between varieties. The moisture content of the grain receded rapidly in all the varieties during the first four 3-day intervals. During the 24 days between the first and final harvest of each variety the grain moisture decreased from an average of 43.2 percent to 17.0 percent. The developmental period of the kernel apparently was shorter in Maganski 044 than in the other varieties in the test as indicated by the tendency of the grain to start dessicating in a shorter time after heading. Differential shattering resulting from hail was observed. Mission and Aberystwyth S84 were most resistant. Mission apparently derived its shatter resistance from its Markton parent, which was. -
Why Serious Bakers Have Mother Issues Andrea Strong
Why Serious Bakers Have Mother Issues Andrea Strong A sourdough starter, also known as a "mother." [Photograph: Shutterstock] They came from all over Europe—a village in Poland, a farm in Tuscany, a town in Bordeaux. They were carried across the continent, and trekked from the Old Country to the New World. There were arrests and clashes with the police. But through a combination of luck and love, they arrived in New York City where they now work quietly, often in the small hours of the morning. Not many people have even seen them; just a modest, elite group of artisans truly know them intimately. The bakers know their mothers, and these are their stories. But, wait, perhaps I should clarify. These aren't their actual mothers, as in the women who gave birth to them, who raised them, who are now, undoubtedly, the subject of therapy for one 45- minute hour per week. No, no. These are their "mothers"—also known as madre, seed, chef, and levain. Natural yeasts starters destined for some of the world's best sourdough breads, typically born of a combination of apples, grapes, and honey, left to ferment on a warm windowsill and grow a frosting of wild yeast and Lactobacillus bacteria. Yup, those mothers. [Photograph: Vicky Wasik] Mind you, starters do share qualities often associated with matriarchs (...and pets)—they often inspire love-hate relationships marked by serious dependency. Unlike commercial yeast, which requires little more than sugar and warm water to activate, mothers are needy. They demand regular feedings of flour and water in order to produce the organic acids, alcohols, and carbon dioxide necessary to make bread do that cool thing it does: rise. -
MF3092 Harvest Management of Canola
Harvest Management of Canola Michael Stamm, Department of Agronomy Kraig Roozeboom, Department of Agronomy Johnathon Holman, Southwest Research-Extension Center Canola harvest requires appropriate timing and manage- Producers should begin with the settings for rapeseed or ment of operations. Because canola is prone to shattering, canola in the operator’s manual. Adjustments should be made harvest planning must begin well before the crop is ripe. The based on what is coming out the back of the combine. Because longer a ripe canola crop stands in the field, the greater the risk canola seed is small, it is a good idea to have a roll of duct tape, for shattering by wind and severe weather. caulk, or axle grease handy to plug holes in combines and trucks. Shattering losses from severe weather can be devastating, Check for grain losses ahead of the combine (shattering), behind ranging from 5 percent to 75 percent of total crop yield. As a the header (header loss), and behind the combine (tailings). result, some producers prepare their canola before harvest to Begin with setting cylinder speed between 450 and reduce the risks of shattering. There are four harvest/prepara- 650 rpm, which is about one-half to two-thirds of the speed tion methods used in the southern Great Plains: direct cutting, used when harvesting wheat. Set the concave clearances at desiccation, pushing, and swathing. Advantages and disadvan- ¾ inch in the front and 1/8 to ¼ inch in the rear. Canola seed tages of each method are discussed in this publication. Proper threshes easily from the seedpods. -
Issue #35, Fall 2016
California Issue #35, Fall 2016 Single Red Rice plant, RReseiarcch Boae rd mid-season for fields infested with weedy rice. It Weedy Rice is up to the rice in - dustry to make Folks, we have a problem. We can sure infested fields deny it, ignore it, or hope it will go away are managed to re - – but we still have a problem. We hope duce infestation you will engage with us and work to levels and eventu - eradicate weedy rice (a.k.a. red rice) in ally get rid of this California. weed. Could it be a big problem here? Let’s Do we know all the answers yet – No. look at the South. Timothy Blank, CA The researchers and farm advisors have Crop Improvement Association, states put together Best Management Practices that high infestations in the South have re - with our current knowledge. Here is sulted in yield reductions of over 60%. A what you can do today: 2008 survey in Arkansas found that 62% of rice fields are infested to some degree. Before Harvest California has been fortunate. Over Weedy rice plants are easiest to iden - the last 100 years of rice production tify at the heading stage, here, there have been periodic infesta - UCANR brochure, tions. Most of these infestations were http://rice.ucanr.edu/files/239170.pdf. Weedy eradicated or have been taken out of rice The three consistent characteristics are rice can production. So things have gone well – 1) red colored bran, 2) shattering, and 3) be up to 2003 when weedy rice was found seed dormancy. -
Evaluation of Anti-Inflammatory and Atheroprotective Properties Of
foods Article Evaluation of Anti-Inflammatory and Atheroprotective Properties of Wheat Gluten Protein Hydrolysates in Primary Human Monocytes Sergio Montserrat-de la Paz 1 , Noelia M. Rodriguez-Martin 2, Alvaro Villanueva 2, Justo Pedroche 2, Ivan Cruz-Chamorro 1,3 , Francisco Millan 2 and Maria C. Millan-Linares 2,4,* 1 Department of Medical Biochemistry, Molecular Biology and Immunology, School of Medicine, Universidad de Sevilla, Av. Dr. Fedriani 3, 41071 Seville, Spain; [email protected] (S.M.-d.l.P.); [email protected] (I.C.-C.) 2 Department of Food & Health, Instituto de la Grasa, CSIC. Ctra. de Utrera Km. 1, 41013 Seville, Spain; [email protected] (N.M.R.-M.); [email protected] (A.V.); [email protected] (J.P.); [email protected] (F.W.) 3 Instituto de Biomedicina de Sevilla, IBiS (Universidad de Sevilla, HUVR, Junta de Andalucía, CSIC), Av. Manuel Siurot s/n, 41013 Seville, Spain 4 Cell Biology Unit, Instituto de la Grasa, CSIC. Ctra. de Utrera Km. 1, 41013 Seville, Spain * Correspondence: [email protected]; Tel.: +34-954-61-15-50 Received: 21 May 2020; Accepted: 29 June 2020; Published: 30 June 2020 Abstract: Bioactive protein hydrolysates have been identified in several sources as possible agents in the prevention and treatment of many diseases. A wheat gluten (WG) concentrate was hydrolyzed by Alcalase under specific conditions. The resulting hydrolysates were evaluated by in vitro cell-free experiments leading to the identification of one bioactive WG protein hydrolysate (WGPH), which was used at 50 and 100 µg/mL on primary human monocytes. Reactive oxygen species (ROS) and nitrite levels and RT-qPCR and ELISA techniques were used to analyze the functional activity of WGPH. -
Pod Shattering: a Homologous Series of Variation Underlying Domestication and an Avenue for Crop Improvement
agronomy Review Pod Shattering: A Homologous Series of Variation Underlying Domestication and an Avenue for Crop Improvement Ezgi Ogutcen 1,†, Anamika Pandey 2,† ID , Mohd Kamran Khan 2,†, Edward Marques 3, R. Varma Penmetsa 4 ID , Abdullah Kahraman 5 and Eric J. B. von Wettberg 3,* ID 1 Department of Plant Sciences, University of Saskatchewan, Saskatoon, SK 57N 5E8, Canada; [email protected] 2 Department of Soil Science and Plant Nutrition, Faculty of Agriculture, Selcuk University, Konya 42079, Turkey; [email protected] (A.P.); [email protected] (M.K.K.) 3 Department of Plant and Soil Sciences, University of Vermont, Burlington, VT 05405, USA; [email protected] 4 Department of Plant Sciences, University of California Davis, Davis, CA 95616, USA; [email protected] 5 Department of Field Crops, Faculty of Agriculture, Harran University, Sanliurfa 63300, Turkey; [email protected] * Correspondence: [email protected]; Tel.: +1-802-6565-9117 † These authors contributed equally to this work. Received: 10 June 2018; Accepted: 1 August 2018; Published: 3 August 2018 Abstract: In wild habitats, fruit dehiscence is a critical strategy for seed dispersal; however, in cultivated crops it is one of the major sources of yield loss. Therefore, indehiscence of fruits, pods, etc., was likely to be one of the first traits strongly selected in crop domestication. Even with the historical selection against dehiscence in early domesticates, it is a trait still targeted in many breeding programs, particularly in minor or underutilized crops. Here, we review dehiscence in pulse (grain legume) crops, which are of growing importance as a source of protein in human and livestock diets, and which have received less attention than cereal crops and the model plant Arabidopsis thaliana. -
New Technologies for Whole Wheat Processing: Addressing Milling and Storage Issues
University of Nebraska - Lincoln DigitalCommons@University of Nebraska - Lincoln Dissertations, Theses, & Student Research in Food Science and Technology Food Science and Technology Department Winter 11-29-2012 New Technologies for Whole Wheat Processing: Addressing Milling and Storage Issues Andres F. Doblado-Maldonado University of Nebraska-Lincoln, [email protected] Follow this and additional works at: https://digitalcommons.unl.edu/foodscidiss Part of the Food Chemistry Commons, and the Food Processing Commons Doblado-Maldonado, Andres F., "New Technologies for Whole Wheat Processing: Addressing Milling and Storage Issues" (2012). Dissertations, Theses, & Student Research in Food Science and Technology. 31. https://digitalcommons.unl.edu/foodscidiss/31 This Article is brought to you for free and open access by the Food Science and Technology Department at DigitalCommons@University of Nebraska - Lincoln. It has been accepted for inclusion in Dissertations, Theses, & Student Research in Food Science and Technology by an authorized administrator of DigitalCommons@University of Nebraska - Lincoln. NEW TECHNOLOGIES FOR WHOLE WHEAT PROCESSING: ADDRESSING MILLING AND STORAGE ISSUES by Andrés Felipe Doblado Maldonado A THESIS Presented to the Faculty of The Graduate College at the University of Nebraska In Partial Fulfillment of Requirements For the Degree of Master of Science Major: Food Science and Technology Under the Supervision of Professor Devin J. Rose Lincoln, Nebraska November, 2012 NEW TECHNOLOGIES FOR WHOLE WHEAT PROCESSING: ADDRESSING MILLING AND STORAGE ISSUES Andrés Felipe Doblado Maldonado, M.S. University of Nebraska, 2012 Adviser: Devin J. Rose Whole wheat flour production and demand has increased dramatically during the last decade due to evidence supporting the benefits of whole grains in the diet. -
Agronomic Crop Science Report
AGRONOMIC CROP SCIENCE REPORT Research Extension EVALUATION OF AN ALTERNATIVE GRASS SEED HARVEST SYSTEM TO FACILITATE RESIDUE HANDLING 1/ Harold Youngberg and Don Grabe 2/ Introduction Rapid straw removal from the field is an important part of any change in the present system of handling grass seed residues. The present harvest system includes cutting the grass at a relatively well-defined stage of maturity, which isin general the stage when the seed matures to a point of shattering. The straw is swathed and placed in rows and allowed to dry for 7-10 days before threshing. To utilize the straw after threshing, it must be collected and transported from the field to a central collection place or to the point of utilization. It has been proposed that the harvest system be modified to provide for moving the straw and seed to a central point soon after cutting. The unthreshed straw would be made into loose bales after cutting. The material would then be moved from the field to a central point for threshing.This system allows the residue to be,removed from the field shortly after cutting and permits field sanitation to start two to three weeks earlier than pos- sible under the current system. In addition, the residue (including the chaff, a byproduct lost under the current system) would be available at a central point for further processing. A number of potential problems with this system are immediately apparent. One immediate problem is how seed quality will be affected by enclosing the unthreshed materialin a relatively high-moisture-content bale. -
Performance Cereal Crops Tanana River Valley Alaska
PERFORMANCE CEREAL CROPS in the TANANA RIVER VALLEY ALASKA 1982 F. J. W ooding Professor of Agronomy j. H. McBeath nt Professor of Plant Pathology S. Frost nt Pathology Research Aide J. T. Hanscom Agronomy Research Aide R. M. Van Veldhuizen Agronomy Research Aide G. M. Delucchi Graduate Research Assistant AGRICULTURAL EXPERIMENT STATION School of Agriculture and Land Resources Management University of Alaska James V. Drew, Director February 1983 UNIVERSITY OF ALASKA Dr. Jay B arton...................................................................................................................................... President Dr. Patrick J. O’R ourke ..................................................... Chancellor, University of Alaska, Fairbanks Dr. William Phillips ..........................................................................Vice Chancellor for Academic Affairs Dr. Keith B. M a th e r............................................... Vice Chancellor for Research and Advanced Study Dr. James V. D rew ................... Dean, School of Agriculture and Land Resources Management, and Director, Agricultural Experiment Station BOARD OF REGENTS Donald B. Abel, Jr. Herbert C. Lang Hugh B. Fate, Jr., D.M.D., Past President Sara T. Hannan Thomas J . Miklautsch Edward B. Rasmuson, Past President John Shively Roy Huhndorf Ann Parrish Ruth Burnett Gordon Evans The Agricultural Experiment Station at the University of Alaska provides station publica tions and equal educational and employment opportunities to all, regardless of race, color, reli gion, national origin, sex, age, disability, or status as a Vietnam era or disabled veteran. In order to simplify terminology, trade names of products or equipment may have been used in this publication. No endorsement of products or firms mentioned is intended, nor is criticism implied of those not mentioned. Material appearing herein may be reprinted provided no endorsement of a commercial pro duct is stated or implied. -
15 Development and Marketing of Perennial Grains with Benefits for Human Health and Nutrition
PERENNIAL CROPS FOR FOOD SECURITY PROCEEDINGS OF THE FAO EXPERT WORKSHOP AGRO-SYSTEMS, ECOLOGY AND NUTRITION 15 DEVELOPMENT AND MARKETING OF PERENNIAL GRAINS WITH BENEFITS FOR HUMAN HEALTH AND NUTRITION David C. Sands1, Alice Pilgeram1, Cindy E. Morris2 1 Montana State University, Plant Bio-Sciences PO Box 3150, Bozeman, MT, 59717-3150 USA Email: [email protected], [email protected] 2 INRA, UR0407 Pathologie Végétale F-84143 Montfavet cedex, France Email: [email protected] ABSTRACT “The Breeder’s Dilemma - The Conflict Between Yield and Nutrition” addresses the challenge of breeding for highly nutritious grains when yield is the predominant selection criterion (Morris and Sands, 2006). Perennial grasses, in particular those that have already been used as food sources by indigenous peoples, offer an opportunity to develop sustainable and nutritious grain crops from genetic resources that have not been subjected to rigorous selection for yield. To date, our team has developed and commercialized two perennial grass crops and evaluated their nutrition profiles. Indian Rice Grass (IRG, Achnatherum hymenoides ) was used by indigenous people in the western United States. Grain from this perennial grass was consumed as a staple as early as 7 000 years ago, long before maize was cultivated. The grains are smaller, and much higher in protein and essential amino acid content compared to wheat. These seeds shatter 208 15 DEVELOPMENT AND MARKETING OF PERENNIAL GRAINS WITH BENEFITS FOR HUMAN HEALTH AND NUTRITION and have a vernalization trait that suggests that they have not been domesticated in the modern agronomic sense. The grain can be ground into dark and flavourful, gluten-free flour that was marketed as Montina™.