Investigation of Concrete Pumping Effects on Air
Total Page:16
File Type:pdf, Size:1020Kb
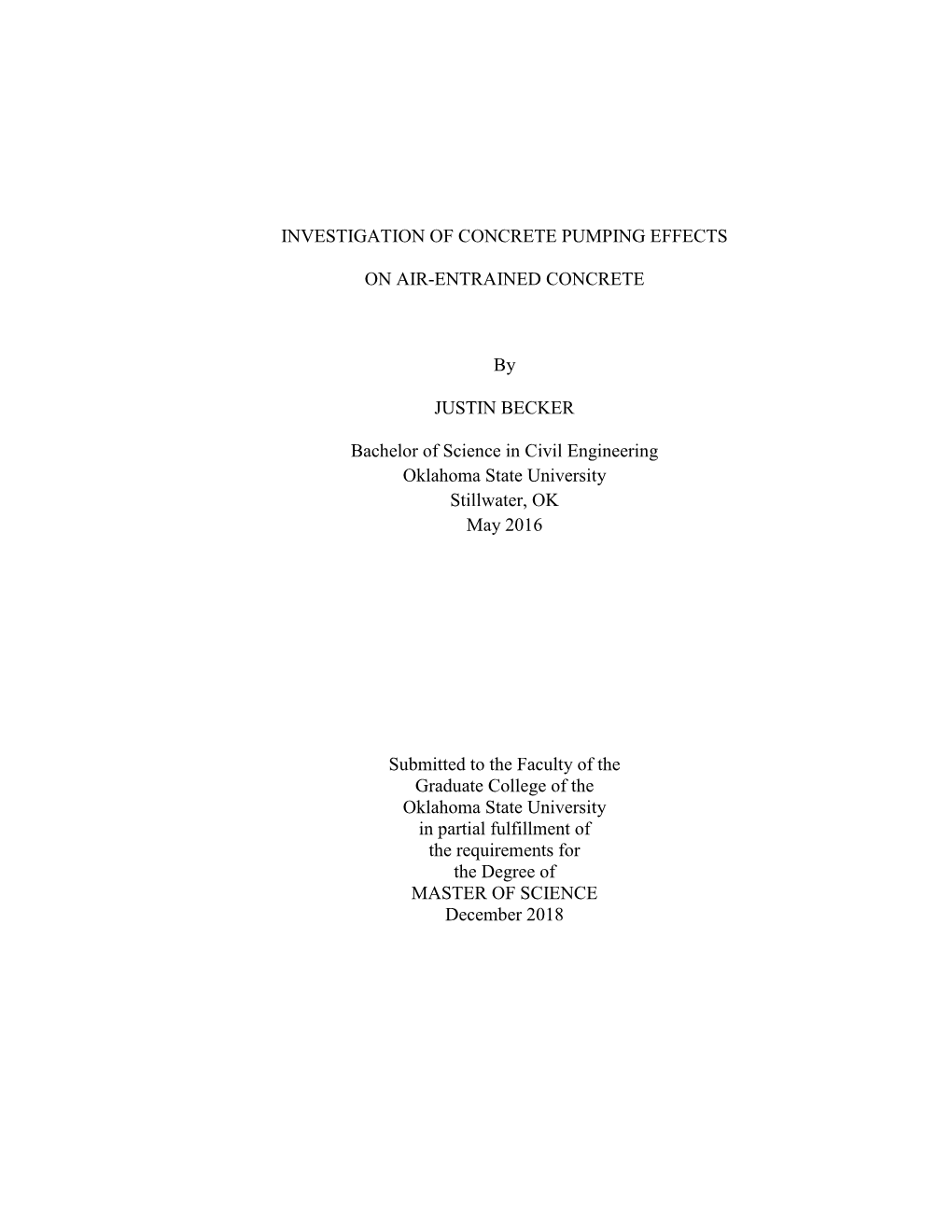
Load more
Recommended publications
-
Guidelines for the Safe Operation of Concrete Pumps
AMERICAN CONCRETE PUMPING ASSOCIATION CERTIFIED OPERATOR STUDY GUIDE Guidelines for the safe operation of concrete pumps Version 03.11.03 National Office Headquarters 606 Enterprise Drive Lewis Center, OH 43035 Phone: 614-431-5618 Fax: 614-431-6944 www.concretepumpers.com 8:30am to 5:30pm Eastern Time Monday through Friday American Concrete Pumping Association Certification Program for Concrete Pump Operators OBJECTIVES To raise the professional standards of the concrete pumping industry in general, and of concrete pump operators, in particular To improve the safety awareness and practice of concrete pump operators To encourage continuing education of concrete pump operators To assist in an operator’s development and self-improvement To award recognition to concrete pump operators who meet the qualifications of certification 1 INDEX Page 4 WHAT IS CERTIFICATION? 4 QUALIFICATIONS 5 TESTING PROCESS 6 VALIDATION 6 SECURITY/COST 7 GENERAL SAFETY - What is a concrete pump operator expected to know? 10 TECHNICAL 13 GROUT & PEA ROCK PUMPS 16 LINE PUMPS - General & High Pressure - ACPA recommendations - High-rise pumping - Compressed air cleanout 21 MULTIPLE SECTION BOOM PUMPS - Safety regulations – mobile concrete pumps equipped with placing boom - Three-Section Boom - Four-Section Boom - 50-Meter and Larger 32 SEPARATE PLACING BOOMS - All placing booms - Diesel-driven placing booms - Electrically driven placing booms - Completion of the pour 36 SAFETY HAND SIGNALS 2 WHAT IS CERTIFICATION? Most importantly, what does certification mean? ACPA Certification is the only industry-recognized certification program which provides a written assessment of an operator’s knowledge regarding concrete pump safety. The purpose of certification is to increase the safety awareness of concrete pump operators and to assist in an operator’s development and self-improvement. -
Guide to Concrete Repair Second Edition
ON r in the West August 2015 Guide to Concrete Repair Second Edition Prepared by: Kurt F. von Fay, Civil Engineer Concrete, Geotechnical, and Structural Laboratory U.S. Department of the Interior Bureau of Reclamation Technical Service Center August 2015 Mission Statements The U.S. Department of the Interior protects America’s natural resources and heritage, honors our cultures and tribal communities, and supplies the energy to power our future. The mission of the Bureau of Reclamation is to manage, develop, and protect water and related resources in an environmentally and economically sound manner in the interest of the American public. Acknowledgments Acknowledgment is due the original author of this guide, W. Glenn Smoak, for all his efforts to prepare the first edition. For this edition, many people were involved in conducting research and field work, which provided valuable information for this update, and their contributions and hard work are greatly appreciated. They include Kurt D. Mitchell, Richard Pepin, Gregg Day, Jim Bowen, Dr. Alexander Vaysburd, Dr. Benoit Bissonnette, Maxim Morency, Brandon Poos, Westin Joy, David (Warren) Starbuck, Dr. Matthew Klein, and John (Bret) Robertson. Dr. William F. Kepler obtained much of the funding to prepare this updated guide. Nancy Arthur worked extensively on reviewing and editing the guide specifications sections and was a great help making sure they said what I meant to say. Teri Manross deserves recognition for the numerous hours she put into reviewing, editing and formatting this Guide. The assistance of these and numerous others is gratefully acknowledged. Contents PART I: RECLAMATION'S METHODOLOGY FOR CONCRETE MAINTENANCE AND REPAIR Page A. -
SECTION 346 Is Deleted and the Following Substituted
Dev346PC PORTLAND CEMENT CONCRETE – PERFORMANCE CONCRETE FOR INLAND AND SLIGHTLY TO MODERATELY AGGRESSIVE ENVIRONMENTS. (REV 9-23-14) SECTION 346 is deleted and the following substituted: PORTLAND CEMENT CONCRETE – PERFORMANCE CONCRETE FOR INLAND AND SLIGHTLY TO MODERATELY AGGRESSIVE ENVIRONMENTS 346-1 Description. Use concrete composed of a mixture of portland cement, aggregate, water, and, where specified, admixtures, pozzolan and ground granulated blast furnace slag. Deliver the portland cement concrete to the site of placement in a freshly mixed, unhardened state. Obtain concrete from a plant that is currently on the list of Producers with Accepted Quality Control Programs. Producers seeking inclusion on the list shall meet the requirements of 105-3. If the concrete production facility’s Quality Control Plan is suspended, the Contractor is solely responsible to obtain the services of another concrete production facility with an accepted Quality Control Plan or await the re-acceptance of the affected concrete production facility’s Quality Control Plan prior to the placement of any further concrete on the project. There will be no changes in the contract time or completion dates. Bear all delay costs and other costs associated with the concrete production facility’sWithout Quality Control Plan acceptance or re- acceptance. 346-2 Materials. 346-2.1 General: Meet the following requirements: Coarse Aggregate ................................Authorization..................................... Section 901 Fine Aggregate*Use ............................... -
Recommendations for Pumping Self-Consolidating Concrete
Mixing Strength With Satisfaction TECHNICAL REPORT RECOMMENDATIONS FOR PUMPING SELF-CONSOLIDATING CONCRETE Using self-consolidating concrete in vertical and overhead FORMWORK applications has become an accepted and proven concrete repair method. Based on the orientation of the • Formwork should be designed to be stronger than normal concrete formwork, repair, pumping self-consolidating concrete can be the in order to account for the hydraulic pressure exerted by the self-consolidating required method of placement for this material. However, concrete and any additional pressure from pumping. pumping can also be the preferred method of application, over form-and-pour techniques, as it can save time • Formwork should be designed to allow for air to escape from high points in and money. the form and provide points to observe the progression of the pour. If necessary 13 mm (½ inch) plastic tubing can be placed at extremely high points, to ensure King provides self-consolidating concrete technology that the air is pushed out of the form. in a pre-packaged solution. Our company offers MS-S6 Self-Consolidating Concrete for shallow depth • Minimum hose and valve sizes should be 38 mm (1½ inches) for MS-S6 repairs of 25 mm (1 inch) to 75 mm (3 inches) and Self-Consolidating Concrete and 50 mm (2 inches) for MS-S10 Self-Consolidating MS-S10 Self-Consolidating Concrete for full depth repairs Concrete. of 50 mm (2 inches) or greater. When pumping MS-S6 • Different types of valves can be used to connect hoses to the formwork, although Self-Consolidating Concrete or MS-S10 Self-Consolidating the most common type is the guillotine valve which can be seen in Figure 1. -
Issue of the Concrete Beton for 2011, It Is a Good Time to Refl Ect on What Has Happened This Year in the Industry, and in Concrete Society Circles
President’s Message As this is the fi nal issue of the Concrete Beton for 2011, it is a good time to refl ect on what has happened this year in the industry, and in Concrete Society circles. he year started with concern over The Concrete Society has been as busy the outlook for 2011 with many as ever this year; with no global crunch Tpredicting a contraction in the being felt by the Head Offi ce staff. The construction industry. This has clearly appointment of the CEO, John Sheath, been evident with very competitive at the start of this year has brought tendering and reduced demand for with it a tangible difference to the way materials. Material price increases in which the Society strives to serve do not appear to have followed the its members. This effort has gone into discounting offered by consultants aligning the Society with the latest and contractors, with some steady legislation, which governs the way we increases seen at regular periods operate in South Africa. throughout the year in ‘base’ construc- The focus of many discussions in As we look forward to the Christmas tion materials. the Society is how we can best serve break, I want to take this opportunity But the year has ended with a lit- our members. How can we ensure to wish all - a blessed and safe holi- tle more optimism creeping into the that we remain a relevant contributor day - and trust that 2012 will bring industry. While the outlook for 2012 to the construction industry land- some new challenges and many new does not look rosy by any stretch of the scape and not just become another opportunities. -
37Th Annual WRMCA Concrete Design Awards
37th Annual WRMCA Concrete Design Awards View the presentation - https://www.youtube.com/watch?v=OfNbHcUDVzg&t=5s Sponsored by - Carew Concrete & Supply, Euclid Chemical, GRT-Mapei, Riv/Crete Ready Mix, Sika Corporation, and ACI Wisconsin AGRICULTURAL – SPRING BREEZE DAIRY The dairy farm required extreme engineering design skill and coordination on the part of many companies. The farming complex is the latest addition to a partnership of five families who own and operate several farms throughout Wisconsin. More than 11,000 cubic yards of ready-mix concrete was used to construct new facilities that allowed the farm to grow from 1,800 to 3,500 cows. In all, ready-mix was used to construct a manure pit, several barns, a storage shed, a milking parlor and pathways connecting buildings. This immense job required three different contractors to operate onsite. All three contractors relied on the same supplier for the ready-mixed concrete. This system required a great deal of coordination to make sure the right trucks were getting to the right contractor. In addition, there were more than 20 different design mixes used throughout this job. Project Team Members Concrete Supplier: County Materials Corporation Contractor: Milis Flatwork Contractor: Spiegelberg Implement Contractor: Everlasting Concrete Engineer: Keller, Inc. Engineer: Roach & Associates, LLC COMMERCIAL –ABBEY MARINA HARBOR RENOVATION This project consisted of a complete renovation of the Abbey Marina Harbor in Fontana, WI. The Abbey Marina is a 407-slip full- service boating facility. The entire perimeter of the harbor was redone with a new seawall and sidewalks along with a boat ramp, patios, and curb and gutter. -
Check List for Bridge Deck Placement
CHECK LIST FOR BRIDGE DECK PLACEMENT A) APPROVALS: 1) PLACEMENT PROCEDURES 2) MIX DESIGN 3) OVERHANG FORMS AND SHOP DRAWINGS FOR S.I.P. FORMS 4) CURING WATER B) PRIOR TO PLACEMENT OF CONCRETE: 1) CHECK TO SEE THAT NO FORMS OR OTHER MATERIAL IS WELDED IN THE TENSION AREAS. 2) CHECK TO SEE THAT FORMS ARE MORTAR TIGHT 3) CHECK CLEARANCE OF REINFORCEMENT BAR BOTTOM MAT 4) CHECK AND RECORD CLEARANCE OF REINFORCMENT BAR TOP MAT BY RUNNING THE PAVING MACHINE THROUGHOUT THE ENTIRE DECK AREA. 5) CHECK FOR RIGIDITY OF THE REINFORCEMENT BAR MAT, AND EMPLOY ENOUGH CHAIRS FOR PROPER SUPPORT. 6) CHECK FOR TIES ON REINFORCEMENT BARS AT EVERY INTERSECTION, AND CHECK THAT THE TIE IS BENT DOWN 7) CHECK SCREED RAIL FOR THE CORRECT CAMBER, AND USE A COMPUTER PROGRAM IF APPLICABLE 8) CHECK THE FINISHING MACHINE FOR THE CORRECT DECK TEMPLATE, AND FOR POSSIBLE WEAR ON THE UNDERSIDE (STRINGLINE THE PAVING MACHINES RAILS, MARK LEGS FOR SHACKLE DOWN 1.0’) 9) CLEAN DECK, BLOW OUT OR WASH 10) TOUCH UP ANY BARE STEEL OR REINFORCEMENT BARS 11) RECORD “DRY RUN” REINFORCEMENT BAR CLEARANCES AND DEPTH CHECKS 12) SLAB BOLSTERS 3’ C/C C) PRIOR TO RELEASING CONCRETE: 1) HAVE A BULKHEAD AND PLASTIC COVERS ON HAND FOR AN EMERGENCY SHUT-DOWN 2) DOES THE CONTRACTOR HAVE ALL EQUIPMENT NECESSARY FOR THE DECK PLACEMENT, AND IS IT ALL FUNCTIONING? 3) IS STANDBY EQUIPMENT AT THE JOB SITE, ESPECIALLY IF PUMPING? 4) DOES THE CONTRACTOR HAVE SUFFICIENT PERSONNEL ON SITE? 5) DO YOU HAVE AN ADEQUATE CONCRETE DELIVERY SCHEDULE? 6) DECIDE ON THE PROPER RETARDATION REQUIRED FOR THE DECK PLACEMENT DECK CHECK 1) RUN BIDWELL FOR CONCRETE OPERATION 2) CHECK CLEARENCE ON REBARS – DEPTH CHECKS, RECORD MEAS. -
Pumping of Concrete Mixtures: Rheology, Lubrication Layer Properties and Pumping Pressure Assessment
Pumping of Concrete Mixtures: Rheology, Lubrication Layer Properties and Pumping Pressure Assessment by Jan Vosahlik B.S., Czech Technical University in Prague, 2012 M.S., Kansas State University, 2014 AN ABSTRACT OF A DISSERTATION submitted in partial fulfillment of the requirements for the degree DOCTOR OF PHILOSOPHY Department of Civil Engineering College of Engineering KANSAS STATE UNIVERSITY Manhattan, Kansas 2018 Abstract Pumping is the most utilized placement technique to deliver fresh concrete from the concrete mixer to the formwork on construction site. Compared to other available placement methods, such as bucket-and-crane or conveyor belts, pumping offers superior placement rates while reducing the required labor cost. Despite the fact that concrete pumping has been utilized on job sites around the world since the early 1960s, there is still a lack of knowledge, supported by research evidence, as to what affects concrete pumpability and how pumping changes concrete properties both in the plastic and hardened state. A four-phase research study was carried out to: (1) improve the existing methodology of rheological characterization of the lubrication layer formed during pumping, (2) evaluate the effect of concrete mixture constituents and proportioning on rheological properties of concrete and the lubrication layer, (3) asses the effect of pumping and pumping pressure on concrete fresh properties and the air void system under controlled conditions, and (4) to evaluate the effect of pumping on concrete fresh properties and the air void system in the field conditions. In the first phase of this research program, a correction procedure was developed evaluating 3D flow at the bottom of the cylindrical concrete interface rheometer. -
Advanced Construction and Building Technology for Society
Publication 367 Advanced Construction and Building Technology for Society Joint CIB - IAARC Commission on “Customized Industrial Construction” Proceedings of the CIB*IAARC W119 CIC 2012 Workshop “Advanced Construction and Building Technology for Society” Editors: Thomas Bock (Prof. Prof. h. c./SRSTU Dr.-Ing./Univ.Tokio) Christos Georgoulas (Dr.-Ing.) Thomas Linner (Dipl.-Ing.) 24 Oct 2012 Laboratory of Building Realization and Robotics (br)2 Technische Universität München (TUM), Germany Foreword CIB Working Commission, W119 on “Customized Industrial Construction” has been established as the successor of former TG57 on Industrialization in Construction and as a joint CIB-IAARC Commission. Prof Dr Ing Gerhard Girmscheid, ETH Zurich, Switzerland (Coordinator of the former TG57) and Prof Dr Ing Thomas Bock, Technische Universität München, Germany are the appointed Coordinators of this Working Commission. The workshop is hosted by the Chair for Building Realization and Robotics located at TUM within the Bavarian high tech cluster, the Master of Science Course “Advanced Construction and Building Technology” and by IAARC-Academy representing the research training program of the International Association for Automation and Robotics in Construction (IAARC). The workshop will concentrates international researchers, practitioners and selected top-students coming from 8 different professional backgrounds (Architecture, Industrial Engineering, Electrical Engineering, Civil Engineering, Business Science, Interior Design, Informatics, Mechanical Engineering). Industrialization in Construction will become more customer oriented. Systems for adaptable manufacturing and robot technologies will merge the best aspects of industrialization and automation with aspects of traditional manufacturing. Concepts of mass customization can be implemented via the application of robots in construction and building project/product life cycle as prefabrication processes, on site and in service as socio technical systems. -
Precast Polymer Technology Is a Game Changer for Pump Base Foundations Precast Polymer Technology Is a Game Changer for Pump Base Foundations
Precast Polymer Technology is a Game Changer for Pump Base Foundations Precast Polymer Technology is a Game Changer for Pump Base Foundations By: Thomas Kline- Director, Concrete Repair Solutions Introduction In an effort to reduce pump installation costs as well as improve pump reliability, maintenance & reliability professionals are turning to precast polymer concrete pump foundations. This proven foundation technology provides many advantages over conventional pump foundations. Advantages include installation cost savings, improved corrosion resistance in aggressive environments as well as improved overall reliability. Polyshield® precast polymer concrete foundation systems consist of a foundation baseplate shell for rotating pumps and motors (Figure 1). The foundations are constructed of polymer concrete in a one-piece shell. The shell replaces the baseplate, foundation, anchor bolts and grouting system of a traditional pump foundation. The system can be combined with a variety of rotating pump designs, including ANSI1 and ISO2 pumps. Custom-built foundations can meet special pump requirements such as those associated with API3 applications. A prime mover in selecting these types of foundation systems is when pumps are subjected to corrosive service. These foundation systems Figure 1 – Sectional view of a precast polymer concrete pump thrive in corrosive environments because they foundation (Polyshield®) are made from inherently corrosion resistant inert aggregate-filled thermosetting resins such as novolac epoxy or vinyl ester4. Often however, many end users are installing these units in non-corrosive services in new construction as well as repairs or upgrades of existing pump installations for enhanced constructability reasons alone. In new construction, because the need for forming and placing conventional concrete foundations is eliminated along with elimination of anchor bolts, separate base plates, and grouting systems, the time and labor required to install a pump package is dramatically reduced. -
Series 500: Concrete
ATM 501 Sampling Freshly Mixed Concrete SAMPLING FRESHLY MIXED CONCRETE WAQTC TM 2 Following are guidelines for the use of WAQTC FOP for WAQTC TM 2 by the State of Alaska DOT&PF. 1. Under required Apparatus, Apparatus for wet sieving, add the following clarification: Mixes with aggregates larger than 1.5 inch apparatus for wet sieving, including: a sieve(s), conforming to AASHTO M 92 (ASTM E11), minimum of 2 ft2 (0.19 m2) of sieving area, 1.5 inch screen openings, and conveniently arranged and supported so that the sieve can be shaken rapidly by hand. Delete and Replace Procedure 3. • Sampling from pump or conveyor placement systems Obtain sample after a minimum of 1/2 m3 (1/2 yd3) of concrete has been discharged. Obtain samples after all of the pump slurry has been eliminated. Perform sampling by repeatedly passing a receptacle through the entire discharge system or by completely diverting the discharge into a sample container. Do not lower the pump arm from the placement position to ground level for ease of sampling, as it may modify the air content of the concrete being sampled. Do not obtain samples from the very first or last portions of the batch discharge. With • Sampling from pump or conveyor placement systems The Department will take all samples from the delivery truck discharge. Obtain sample after a minimum of 1/2 m3 (1/2 yd3) of concrete has been discharged. Do not obtain samples from the very first or last portions of the batch discharge. Alaska Test Methods Manual 501-1 Effective April 20, 2021 This page intentionally left blank. -
Soil Stabilization and Underground Shotcrete
A quarterly publication of the American Shotcrete Association MAGAZINE ShotcreteVolume 13, Number 1 Winter 2011 www.shotcrete.org Soil Stabilization and Underground Shotcrete 2011 ASA Buyers Guide Included Circle #29 on reader response form—page 64 Shotcrete is a quarterly publication of the American Shotcrete Volume 13, Number 1 Association. For information about this publication or about Winter 2011 membership in the American Shotcrete Association, please contact ASA Headquarters at: American Shotcrete Association 38800 Country Club Dr. Farmington Hills, MI 48331 Features Phone: (248) 848-3780 • Fax: (248) 848-3740 E-mail: [email protected] 8 Underground Shotcreting Web site: www.shotcrete.org George D. Yoggy 12 Shotcrete in China’s Longest Tunneling Project Kelly Blickle 16 Wet-Mix for a Traditionally Dry-Mix Application Chuck Pulver The opinions expressed in Shotcrete are those of the authors and do not necessarily represent the position of the editors or 18 Equipment Selection— the American Shotcrete Association. The Key to a Successful Soil Nailing Project Copyright © 2011 Craig McDonald Executive Director Chris Darnell Advertising/Circulation Manager Melissa M. McClain Departments Technical Editors Patrick Bridger, Dan Millette, and Ted Sofis 2 President’s Message — Patrick Bridger Graphic Design Susan K. Esper, Colleen E. Hunt, 4 Staff Editorial — Chris Darnell Ryan M. Jay, Gail L. Tatum 20 Shotcrete Corner — Tara Brown, Patrick Giroux, and Joe Hutter Editing Carl R. Bischof, Karen Czedik, 24 Shotcrete Calendar Kelli R. Slayden, Denise E. Wolber 25 Goin’ Underground — Mike Ballou NEW! Publications Committee Ted W. Sofis (Chair), Michael Ballou, Edward Brennan, Patrick Bridger, 26 Technical Tip — Simon Reny and Marc Jolin Oscar Duckworth, Charles S.