IEEE Paper Template in A4 (V1)
Total Page:16
File Type:pdf, Size:1020Kb
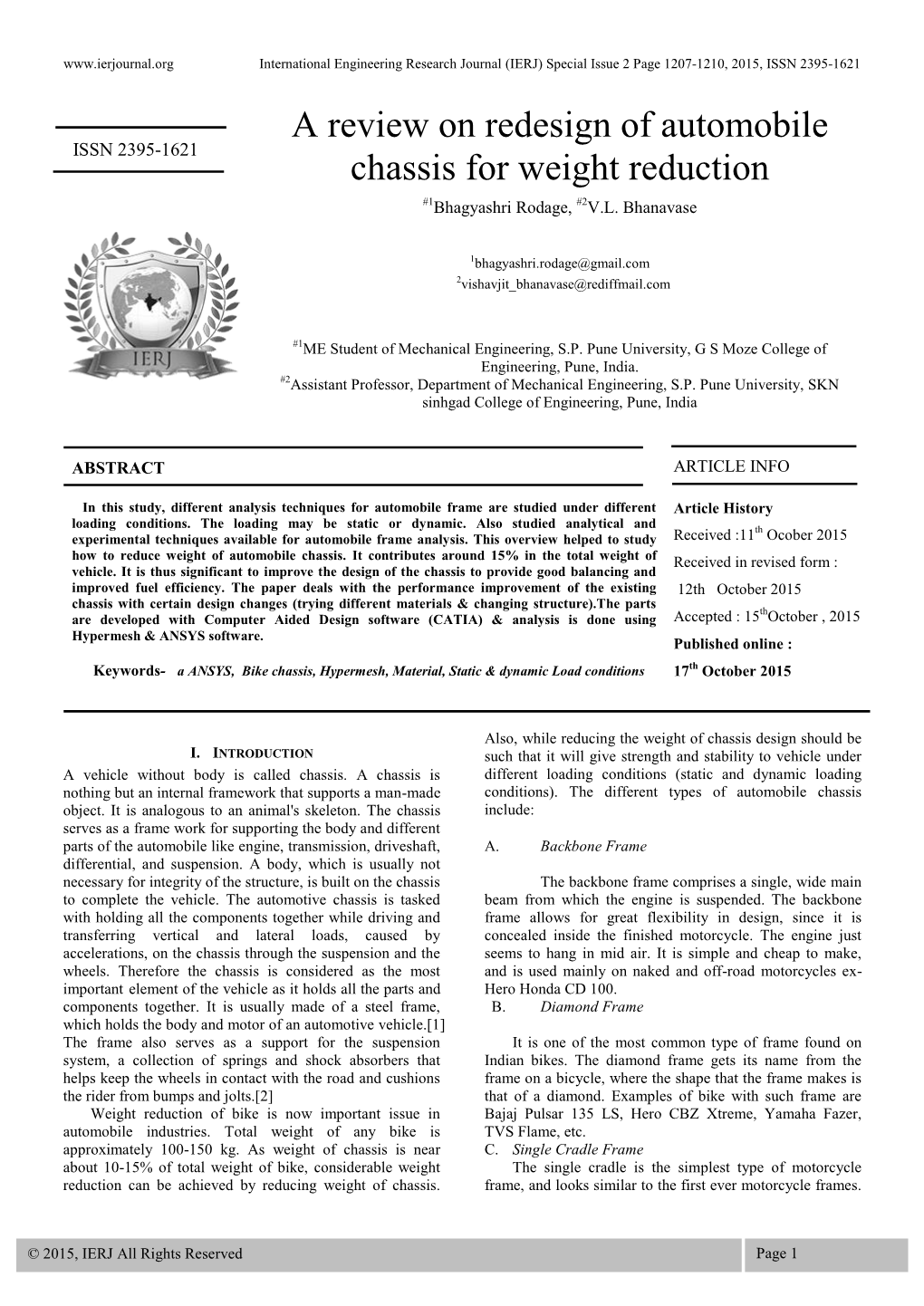
Load more
Recommended publications
-
HRP LIST.Xlsx
INDEX SL. NO. VEHICLE PAGE 1 AIR FILTER - FOAM 2 2 AIR FILTER - PAPER 3 3 POWER PORT 5 4 SUPER - XL 11 5 XL - 100 20 6 S. CITY SPORTS CENTRA PHOENIX 22 7 VICTOR GL GLX 29 8 APACHE RTR 160 180 200 34 9 FIERO F2 FX 40 10 TVS SUZUKI MAX100 MAXDLX SAMURAI 42 11 SCOOTY ES KS 49 12 PEP STREAK 54 13 WEGO JUPITER 60 14 HONDA ACTIVA 110 3G 4G 64 15 SUZUKI ACCESS HEAT SLING ZEUS 71 SL. NO. ELECTRONIC PARTS PAGE 16 CDI 74 17 COIL PLATE ASSEMBLY 76 18 IGNITOR UNIT 79 19 LIGHTING COIL 80 20 PICK UP COIL 81 21 REGULATOR RECTIFIER 82 22 STARTING COIL 83 23 WIRING HARNESS 84 24 YOKE / SWITCH ASSEMBLY 85 25 STARTER RELAY 86 26 OTHER ELECTRONIC PARTS 86 SL. NO. GASKETS PAGE 27 FULL GASKETS 88 28 HALF GASKETS / DC KIT 90 29 CLUTCH GASKET 92 30 MAGNET GASKET 94 31 GEAR BOX GASKET 95 1 of 95 AIR FILTER - FOAM ITEM CODE AIR FILTER - FOAM UNIT MRP HSN CODE GST HRPA1 AIR FILTER FOAM BAJAJ AVENGER EACH 71 8421 18 HRPA2 AIR FILTER FOAM BAJAJ DISCOVER EACH 53 8421 18 HRPA3 AIR FILTER FOAM BAJAJ DISCOVER 150 EACH 69 8421 18 HRPA4 AIR FILTER FOAM BAJAJ KB 4S/BOXER/CALIBER 115/CT 100 EACH 48 8421 18 HRPA5 AIR FILTER FOAM BAJAJ M-80 4S EACH 42 8421 18 HRPA6 AIR FILTER FOAM BAJAJ PLATINA EACH 52 8421 18 HRPA7 AIR FILTER FOAM BAJAJ PULSAR 150/180 EACH 47 8421 18 HRPA8 AIR FILTER FOAM BAJAJ PULSAR UG3 EACH 64 8421 18 HRPA9 AIR FILTER FOAM BAJAJ XCD 125/135 EACH 58 8421 18 HRPA10 AIR FILTER FOAM HERO CBZ/AMBITION EACH 145 8421 18 HRPA11 AIR FILTER FOAM HERO PUCH EACH 42 8421 18 HRPA12 AIR FILTER FOAM HERO SPLENDOR/PASSION EACH 55 8421 18 HRPA13 AIR FILTER FOAM HERO STREET -
TWO WHEELERS : MOTOR CYCLES M/S Royal Enfield Motors Ltd M/S Bajaj Auto Ltd M/S Honda Motorcycle & Scooter India Pvt. Ltd M
TWO WHEELERS : MOTOR CYCLES M/s Royal Enfield Motors Ltd Sl No. Index No. Nomenclature 1 63022-E Motor Cycle 350cc STD (12 Volt) Bullet Electra 2 63107-X Bullet Classic 500 3 64003-P Classic 500 Desert Strom 499cc 4 64004-H Thunderbird UCE 350cc 5 64005-I Classic 350cc 346 6 64006-S Bullet Electra UCE 346cc M/s Bajaj Auto Ltd Sl No. Index No. Nomenclature 1 63024-P Motor Cycle Bajaj Pulsar DTSi (150cc Electric Start) 2 63029-K Motor Cycle Bajaj Discover DTS-Si (Electric Start) 3 63030-X Motor Cycle Bajaj Discover 150 cc (Electric Start) 4 63032-D Bajaj Platina Motor Cycle DZ-02 (100cc) Alloy Wheel 5 63174-A Bajaj Platina 125 (With Electric Start) 6 63175-D Bajaj Discover 125 Drum Brake (Electric Start) 7 63176-E Bajaj Pulsar 135 LS (With Electric Start) 8 63177-L Bajaj Pulsar 180 (With Electric Start) 9 63178-P Bajaj Pulsar 220 (Without Full Fairing) (With Electric Start) 10 63179-H Bajaj Pulsar 220 F (With Full Fairing) (With Electric Start) 11 63180-I Bajaj Avenger 220 (With Electric Start) 12 64000-D Bajaj Discover 125 ST DTS-I Electric Start Disc Brake 13 64001-E Bajaj Discover 125 DTS-I Electric Start Disc Brake 14 64002-L Bajaj Discover 100 DTS-I Electric Start 4 Gears Drum Brake M/s Honda Motorcycle & Scooter India Pvt. Ltd Sl No. Index No. Nomenclature 1 63009-A Motor Cycle Honda CB Shine Self Drum Alloy (125 cc) 2 63010-D ‘Honda’ Unicorn (Self) Motor Cycle 4 Stroke Single Cylinder Air Cooled 150 cc 3 63122-L Honda CB Twister (Self Disc Alloy) 110cc 4 63124-H Honda CBR 150R STD 149.4cc 5 63125-I Honda ‘CBF Stunner’ (Self Disk Alloy) 125 cc 6 63128-K Honda CBR 150R DLX 149.4cc 7 63188-L Honda CB Trigger (STD) 149.1cc 8 63189-P Honda Dream Yuga (Self Drum Alloy) 109cc 9 63190-H Honda CB Twister 110cc (Self Drum Alloy) 10 63193-T Honda Dream Yuga (Kick Drum Alloy) 109cc 11 63194-K Honda Dream NEO (Kick Drum Spoke) 109cc 12 63195-X Honda Dream NEO (Kick Drum Alloy) 109cc 13 63196-A Honda Dream NEO (Self Drum Spoke) 109cc 14 63197-D Honda CBR 250R STD 249.6cc 15 63198-E Honda CBR 250R ABS 249.6cc M/s TVS Motor Company Ltd Sl No. -
TRADING LIST.Xlsx
ACCELERATOR GRIP W/PIPE [SET OF 2] UNIT PRICE ACC. GRIP SET OF 2 SPLENDOR SET 19 ACC. GRIP SET OF 2 SUPER SPLENDOR SET 19 ACC. GRIP SET OF 2 KARIZMA SET 19 ACC. GRIP SET OF 2 CBZ OE SET 19 ACC. GRIP SET OF 2 HERO HONDA OE SET 19 ACC. GRIP SET OF 2 ACTIVA SET 19 ACC. GRIP SET OF 2 UNICORN SET 19 ACC. GRIP SET OF 2 PULSAR SET 19 ACC. GRIP SET OF 2 CALIBER SET 19 ACC. GRIP SET OF 2 KB OE SET 19 ACC. GRIP SET OF 2 KB 4S SET 19 ACC. GRIP SET OF 2 CT-100 SET 19 ACC. GRIP SET OF 2 DISCOVER SET 19 ACC. GRIP SET OF 2 PLATINA SET 19 ACC. GRIP SET OF 2 RX-100 SET 19 ACC. GRIP SET OF 2 YBX OE SET 19 ACC. GRIP SET OF 2 FIERO OE SET 19 ACC. GRIP SET OF 2 SUZUKI OE SET 19 ACC. GRIP SET OF 2 VICTOR OE SET 19 ACC. GRIP SET OF 2 TVS CENTRA SET 19 ACC. GRIP SET OF 2 TVS STAR CITY SET 19 ACC. GRIP SET OF 2 ADRENO OE SET 19 ACC. GRIP SET OF 2 FREEDOM OE SET 19 ACC. GRIP SET OF 2 ELECTRA SET 19 ACC. GRIP SET OF 2 BULLET NEW OE SET 19 ACC. GRIP SET OF 2 TVS SCOOTY OE SET 19 ACC. GRIP SET OF 2 TVS SUPER XL SET 19 ACC. GRIP SET OF 2 TVS SCOOTY PEP SET 19 ACC. GRIP SET OF 2 K.HONDA OE SET 19 ACC. -
UCAL Spare Product Catalogue Full Assembly
Product Catalogue - 2/3 Wheeler/ Gensets Carburettor Assembly Customer UCAL Part Number Applications Vehicle MOQ Bajaj BS29-14 Bajaj Avenger (Aura) 2W 5 BS29-17 Bajaj Avenger UG 2W 5 VM18-231 Bajaj Auto 3W 10 VM18-265 Bajaj Auto CNG 3W 10 VM18-266 Bajaj Auto LPG 3W 10 VM18-251 Bajaj Auto Petrol 3W 10 VM18-268 Bajaj Auto Petrol 3W 10 VM18-232/ VM18-238 Caliber/ Boxer 2W 10 VM16-579 Bajaj BYK (4S) 2W 10 VM18-257 Bajaj Chetak Scooter 2W 10 VM16-613 Bajaj Krystal 2W 10 VM16-556 Bajaj M80 (4S) 2W 10 VM16-539 Bajaj Saffire 100CC(4S) 2W 10 VM12-114 Bajaj Spirit (2S) 2W 10 BS26-176 Bajaj Wind 125cc 2W 5 VM16-614 Bajaj XCD 125cc 2W 10 BS26-165 Pulsar 150cc K1 2W 5 BS26-188 Pulsar 150cc K1UG 2W 5 BS26-221 Pulsar 150cc K1UG2 2W 5 BS26-239 Pulsar 150cc K1UG3 2W 5 BS29-6 Pulsar 180cc 2W 5 BS29-9 Pulsar 180cc K2UG1 2W 5 BS29-13 Pulsar 180cc K2UG2 2W 5 BS29-16 Pulsar 180cc K2UG3 2W 5 BS29-18 Pulsar 200cc 2W 5 TVS VM18-143 & 237 TVS Samurai Max 100R 2W 10 VM12-116,106 & 95 TVS Scooty (CAT/NON-CAT) (2S) 2W 10 VM14-393 TVS Scooty PEP 2W 10 VM14-398 Scooty PEP Plus 90cc N52 2W 10 VM18-241 TVS Victor 110cc 2W 10 VM19-121 TVS Victor 125cc N17 2W 10 VM19-259 Victor 125cc GX (U54) 2W 10 VM19-125 Victor GLX-R 125cc 2W 10 VM18-254 Victor GX 110cc 2W 10 VM18-X31 Victor GX 110cc 2W 10 BS26-230 TVS Apache 150cc U68 2W 5 BS26-253 Apache RTR 160cc U86 2W 5 VM18-273 TVS Auto LPG U76 3W 10 VM18-269 TVS Auto Petrol N46 3W 10 VM17-150 TVS Centra 2W 10 BS26-118 TVS Fiero 2W 5 BS26-184 TVS Fiero F2 2W 5 VM20-419 TVS Flame N90 2W 10 Yamaha VM22-394 Yamaha RX135 4 Speed 2W -
Bajaj Pulsar 150 Dtsi • Bajaj Saffire • Recorded Its Higher Ever Net Sales & Operating Income
•Bajaj Auto Limited is an Indian motorised vehicle- producing company. •Bajaj Auto is a part of Bajaj Group. •Bajaj Auto is the world's third-largest manufacturer of motorcycles and the second-largest in India. • The Forbes Global 2000 list for the year 2005 ranked Bajaj Auto at 1,946. It features at 1639 in Forbes 2011 list. •Bajaj Auto came into existence on 29 November 1945 as M/s Bachraj Trading Corporation Private Limited. • It started off by selling imported two- and three-wheelers in India. •In 1959, it obtained a licence from the government of India to manufacture two- and three-wheelers and it went public in 1960. •In 1970, it rolled out its 100,000th vehicle. •In 1977, it sold 100,000 vehicles in a financial year. •In 1985, it started producing at Waluj near Aurangabad . •In 1986, it sold 500,000 vehicles in a financial year . •In 1995, it rolled out its ten millionth vehicle and produced and sold one million vehicles in a year. • 1961–1971 – Vespa 150 • 1971 – three-wheeler goods carrier • 1972 – Bajaj Chetak • 1976 – Bajaj Super • 1975 – Bajaj Priya • 1981 – Bajaj M-50 • 1986 – Bajaj M-80, Kawasaki Bajaj KB100 • 1990 – Bajaj Sunny • 1994 – Bajaj Classic • 1998 – Kawasaki Bajaj Caliber, Bajaj Super 99 • 2001 – Eliminator, Bajaj Pulsar, Caliber Croma • 2004 – Bajaj KT 100, New Bajaj Chetak 4-stroke, Bajaj Discover DTS-I • 2005 – Bajaj Wave, Bajaj Avenger, Bajaj Discover 112 • 2006 – Bajaj Platina • 2009 – Bajaj Pulsar 220 DTS-i, Bajaj Discover 100 DTS-Si, Kawasaki Ninja 250R • 2011 – Bajaj Discover 125 • 2012 – KTM Duke 200 • -
Continues Improvement
Desh ki Dhadkan Dhak Dhak Go By: o “Hero” is the brand name used by the Munjal brothers for their flagship company Hero Cycles Ltd. o A joint venture between the Hero Group and Honda Motor Company was established in 1984 as the Hero Honda Motors Limited at Dharuhera India. o During the 1980s, the company introduced motorcycles that were popular in India for their fuel economy and low cost. o A popular advertising campaign based on the slogan 'Fill it - Shut it - Forget it' that emphasised the motorcycle's fuel efficiency helped the company grow at a double-digit pace since inception. o Hero Honda has three manufacturing facilities based at Dharuhera, Gurgaon in Haryana and at Hardwar in Uttarakhand. These plants together are capable of churning out 3 million bikes per year. o Hero Honda has a large sales and service network with over 4,500 dealerships and service points across India. o During the fiscal year 2008-09, the company sold 3.7 million bikes, a growth of 12% over last year. In the same year, the company had a market share of 57% in the Indian market. o Hero Honda sells more two wheelers than the second, third and fourth placed two-wheeler companies put together. Hero Honda's bike Hero Honda Splendor, the world's largest- selling motorcycle for the years 2001-2003, selling more than one million units per year. o Total unit sales of 54,02,444 two-wheelers, growth of 17.44 per cent o Total net operating income of Rs. 19401.15 Crores, growth of 22.32 per cent o Net profit after tax at Rs. -
2 Wheeler Engie Product List.Xlsx
Éclat Manufacturing Co. 2-Hari Om Industrial Area, At. Kothariya, Rajkot – 360004 Gujarat. Mob: +91-9016267354 E: [email protected] Engine Valve For Export Only HERO HONDA Part No. Suitabel For INR (Pc) É2V -01.120.00 Hero Honda CD-100 46.00 É2V -01.120.01 Hero Honda SS 46.00 É2V -01.120.02 Hero Honda Joy 46.00 É2V -01.120.03 Hero Honda Passion 46.00 É2V -01.120.04 Hero Honda Dawn 46.00 É2V -01.120.05 Hero Honda Splendor 46.00 É2V -01.120.06 Hero Honda Street 46.00 É2V -01.120.07 Hero Honda Sleek 46.00 É2V -01.120.08 Hero Honda CD-Deluxe 46.00 É2V -01.120.09 Hero Honda Super Splendor 59.80 É2V -01.120.10 Hero Honda Smart 59.80 É2V -01.120.11 Hero Honda Glamore 59.80 É2V -01.120.12 Hero Honda Karizma 69.00 É2V -01.120.13 Hero Honda CBZ 69.00 É2V -01.120.14 Hero Honda Ambition - 653 c.c 69.00 É2V -01.120.15 Hero Honda Ambition - 655 c.c 69.00 É2V -01.120.16 Hero Honda Achiver 69.00 BAJAJ AUTO Part No. Suitabel For INR (Pc) É2V -01.120.17 K.B-4 Stroke 46.00 É2V -01.120.18 Bajaj Caliber 46.00 É2V -01.120.19 Bajaj CT-100 / Platina 46.00 É2V -01.120.20 Bajaj Boxer 46.00 É2V -01.120.21 Bajaj Chetak 4 stroke 59.80 É2V -01.120.22 Bajaj M-40 4 Strokes 59.80 É2V -01.120.23 Bajaj BYK 59.80 É2V -01.120.24 Bajaj Sapphire 59.80 É2V -01.120.25 Bajaj 3/W 4 Stroke 69.00 É2V -01.120.26 Bajaj Legend 69.00 É2V -01.120.27 Bajaj Pulsar 150 DTS-i 69.00 É2V -01.120.28 Bajaj 3/W 4 Strokes (CNG) 69.00 É2V -01.120.29 Bajaj Wind-125 69.00 É2V -01.120.30 Bajaj Discover 150 cc 69.00 É2V -01.120.31 Bajaj Discover DTS-I / 150 74.75 É2V -01.120.32 Bajaj Discover 100 cc 69.00 É2V -01.120.33 Bajaj Discover Digital 69.00 É2V -01.120.34 Bajaj Pulsar 655 cc 110.40 É2V -01.120.35 Bajaj XCD 69.00 É2V -01.120.36 Bajaj Pulsar 140 DTS-i 74.75 É2V -01.120.37 Bajaj Pulsar 200 /220 DTS-i 74.75 LML Part No. -
Cyberabad Police to Auction 2061 Abandoned / Unclaimed Vehicles
Cyberabad Police To Auction 2061 Abandoned / Unclaimed Vehicles Sl.No Vehicle No Type of Vehicle Sl.No Vehicle No Type of Vehicle 1 Chetak 35E96C61094144 1013 AP01N1673 SplendorPlus 2 CBZ 07OBMM10621 1014 AP28BK4556 Passion Plus 3 Passion Plus AP13C4031 1015 AP28AN0453 SPLENDOR 4 Passion Plus AP28AX7859 1016 AP16S2618 SPLENDER 5 Passion Plus AP28AS4754 1017 AP21G9894 SPLENDOR 6 Passion Plus AP11AG1650 1018 AP09BB7315 TVS XL SUPER 7 Splendor+ AP22S5682 1019 AP23Q2651 Stunner 8 Passion Plus 07OBMM10621 1020 AP28AV2315 Passion Plus 9 Bajaj CT-100 AP22K3219 1021 AP29R3551 Pulsar150 10 Chetak AP09AC7138 1022 AP28AV4596 CBZ 11 Chetak AP36P9305 1023 AP09BX6452 Activa 12 Chetak 35E96J30388 1024 AP28AF6229 SPLENDOR 13 Passion Plus AP9BQ1534 1025 AP09BX2320 Mahindra Rodeo 14 Splendor+ AP22AE0496 1026 AP28BD1516 Passion Plus 15 Passion Pro (Hero Honda) AP21AK1319 1027 AP28CG6063 SplendorPlus 16 Passion Plus AP28AC4062 1028 AP10AW8374 Pulsar150 17 Passion Plus AP09AH1704 1029 AP13N4195 Passion Plus 18 Bajaj CD-Delux AP28AZ0992 1030 AP28BH7509 Pulsar150 19 Passion Plus AP11S4631 1031 AP28BD6597 BAJAJ CT100 20 Splendor+ AP28AJ7466 1032 AP28AT1821 Yamaha 21 Bajaj Discover AP22AD0794 1033 AP28CK5815 Shine 22 Hero Honda AP22AW5427 1034 GJ15SS7534 Unicon 23 Bajaj Platina AP22AD6536 1035 AP15AL8228 Passion Plus, 24 Activa AP28CF8282 1036 AP05BP1485 PLATINA 25 Suzuki AP25A7861 1037 AP28CC9455 Activa 26 Chetak AP11E2578 1038 TS05ED6807 DISCOVER 150 27 Splendor AP10M2063 1039 AP10AG1126 Splendor Plus 28 Bajaj CT-100 AP29K7603 1040 AP28AX5624 Activa 29 Splendor+ -
Belts / Oil Seals / Rubber Parts / Engine Valves Control Cables / Blinkers / Blinkers Stay / Electrical Parts W.E.F 01
PRODUCT CATALOGUE 2 & 3 Wheelers Belts / Oil seals / Rubber Parts / Engine Valves Control Cables / Blinkers / Blinkers Stay / Electrical Parts W.e.f 01. 04. 2019 OIL SEALS Vehicle Make / Model - Product Dimensions in mm OD - JK Pioneer Ref No. Seal Type Application ID - HT1 - HT2 Part No. BAJAJ KB 100 / KB 125 / RTZ Crank Case Output Shaft 30-10-1014 37 - 25 - 6 11MBU 7291 Crank Shaft LH 30-10-1013 40 - 20 - 7 13M 7290 Front Hub 15 - 10 - 10.5 MRP 7294 Front Brake Drum 30-15-1033 38 - 18 - 5 / 10 31MBUSPL 7295 Front Fork 30-18-1022 42 - 30 - 11 13MBUSPL 8168 Front Fork 30-18-1022 42 - 30 - 11 13MBUSPL 8168N Front Fork 30181022 42 - 30 - 10.5 13MBUSPL 7448 Gear Shift Shaft Inside 30-10-1011 20 - 12 - 5 11MRT 7289 Kick Shaft 30-10-1142 26 - 16 - 6 13MRT 7292 Rear Hub Coupling 30-15-1082 42 - 26 - 8 31MBUSPL 7296 Rear Shock Absorber 22-10-8 13MBUSPL 7434 Engine Kit (7289, 7290, 7291, 7292, 7293, Kit 9008 7294, 7857, 7858 - Each 1 No) BAJAJ 4S CHAMPION, CALIBER, BOXER (CT & AT), CT100, WIND125, PLATINA Crank Case LH / Top Gear 39 1080 19 32 - 22 - 5.5 11MBU 9291 Crank Case LH / Top Gear 39 1080 19 32 - 22 - 5.3 11MBU 1940 Crank Case LH / Top Gear 39 1080 19 32 - 22 - 5.5 11MB 7650 Crank Shaft RH 30 1046 19 18 - 10 - 5 31MBUSPL 7649 Disc Brake (Wind 125) DP151004 50 - 40 - 4.5 31MBU 9551 Engine Cover Clutch Lever 30 1041 19 20 - 12 - 5.5 13M 9288 Engine Cover Clutch Lever 30 1041 19 20 - 12 - 5.5 13M 7647 Front Fork 42 - 30 - 11 12MBU 8392 Front Brake Panel 31 1510 14 58 - 43 - 7 31MBUSPL 2009 Front Fork DL 1810 80 42 - 30 - 11 12MBUSPL 8035 -
No. HONDA No. BAJAJ
PLOT NO-37, NEAR JSW STEEL, SIDC ROAD, VERAVAL – SAPAR, RAJKOT, GUJARATDate: , PIN CODE-360024, MO. +91-9664646138 EMAIL: [email protected] PRODUCT– CAMSHAFT ASSEMBLY DATE - 01/02/2021 No. HONDA 1 HERO HONDA / PASSION / CD-100 / HONDA SPLENDOR 2 HERO HONDA C.B.Z / AMBITION 3 H.H SUPER SPLENDER / GLAMOUR 4 HERO HONDA NXG/CD-DELUX / CD DAWN / PASSION PRO 5 HERO HONDA KARIZMA 6 HERO HONDA CBZ X-TREME/ ACHIVER/ HUNK 7 HERO HONDA PLEASURE 8 HERO HONDA STREET 9 HONDA ACTIVA / DIO/ AVIATOR 10 HONDA ACTIVA NEW / ACTIVA 110 / HET / 3G 11 HONDA ETERNO 12 HONDA UNICORN / SHINE/ STUNNER 13 HONDA TWISTER 14 HONDA DRIAM YUGA No. BAJAJ 1 BAJAJ 4-S/ CALIBER/ BOXER 2 BAJAJ PULSAR 135CC 3 BAJAJ PULSAR 150CC / 180CC 4 BAJAJ PULSAR DTSI 150CC / PULSAR DTSI 180CC 5 BAJAJ PULSAR DIGITAL /UG 3/ UG 4 / UG 5 6 BAJAJ DISCOVER 135 / 200 / 220 7 BAJAJ CT-100 8 BAJAJ PLATINA 9 BAJAJ PLATINA 125CC 10 BAJAJ DISCOVER 125 11 BAJAJ XCD 125CC 12 BAJAJ WIND 125CC 13 BAJAJ CHETAK / LEGEND 14 BAJAJ DISCOVER 100CC 15 BAJAJ DISCOVER 150CC 16 BAJAJ M-80 MEJOR / BYK/ SAFIER 17 BAJAJ CNG NEW 175CC 18 BAJAJ CG CNG/ RE 105CC 19 BAJAJ COMPACT 225 CC / RE COMPACT 4S PLOT NO-37, NEAR JSW STEEL, SIDC ROAD, VERAVAL – SAPAR, RAJKOT, GUJARATDate: , PIN CODE-360024, MO. +91-9664646138 EMAIL: [email protected] \ 20 BAJAJ CNG OLD 21 BAJAJ DISCOVER 100CC T 22 BAJAJ DISCOVER 125 ST No. TVS 1 TVS CENTRA /STAR CITY/ STAR SPORTS 2 TVS VICTOR GS 3 TVS SCOOTY PEP (70CC)/ PEP PLUS (90CC)/ TVS STAR / SUPER XL 100 4 TVS APACHE / RTR 5 TVS VICTOR / GLS 6 TVS FLAME 7 TVS WEGO / MEASTRO 8 TVS FIERO 9 TVS KING / APACHE RTR 10 SUZUKI HEAT /HAYATE 11 SUZUKI ACCESS No. -
Tvs Motor Company Limited
TVS MOTOR COMPANY LIMITED Seventeenth Annual Report 2008-2009 TVS MOTOR COMPANY LIMITED Board of Directors Bankers VENU SRINIVASAN STATE BANK OF INDIA Corporate Accounts Group Branch, Chairman & Managing Director Greams Road, Chennai - 600 006. H. LAKSHMANAN STATE BANK OF MYSORE Industrial Finance Branch, T. KANNAN Midford Garden Road, Bangalore - 560 001. C. R. DUA Registered office K. S. BAJPAI Jayalakshmi Estates, 29 (Old No.8), Haddows Road, Chennai - 600 006. R. RAMAKRISHNAN Tel : 044 - 2827 2233 Fax : 044 - 2825 7121 PRINCE ASIRVATHAM Factories Audit Committee Post Box No. 4, Harita, Hosur - 635 109. T. KANNAN Tel : 04344 - 276780 Chairman Fax : 04344 - 276016 C.R. DUA Post Box No. 1, Byathahalli village, R. RAMAKRISHNAN Kadakola Post, Mysore - 571 311. PRINCE ASIRVATHAM Tel : 0821 - 2596560 Fax : 0821 - 2596530/2596533 Investors’ Grievance Committee Bhatian Village, Nalagarh Post & Taluk T. KANNAN Solan District - 174 101. Himachal Pradesh Chairman Tel : 01795 - 220494 VENU SRINIVASAN Fax : 01795 - 220496 R. RAMAKRISHNAN Subsidiary Companies President & CEO Sundaram Auto Components Limited, Chennai K.N. RADHAKRISHNAN TVS Motor Company (Europe) B.V., Amsterdam TVS Motor (Singapore) Pte. Limited, Singapore Executive Vice President - Finance PT. TVS Motor Company Indonesia, Jakarta S.G. MURALI Secretary K.S. SRINIVASAN Contents Page no. Financial Highlights 2 Auditors SUNDARAM & SRINIVASAN Notice to the Shareholders 3 Chartered Accountants, Directors’ Report to the Shareholders 6 23, Sir C.P. Ramaswamy Road, Report on Corporate Governance 14 Alwarpet, Chennai - 600 018. Auditors’ Report to the Shareholders 25 Listing of shares with Madras Stock Exchange Ltd., Chennai. Balance Sheet 28 Bombay Stock Exchange Ltd., Mumbai. Profit and Loss Account 29 The National Stock Exchange of India Ltd., Mumbai. -
HYDERABAD CITY POLICE LIST of UNCLAIMED/ABANDONED VEHICLES Registeration Name of the S.No Make Engine No
HYDERABAD CITY POLICE LIST OF UNCLAIMED/ABANDONED VEHICLES Registeration Name of the S.No Make Engine No. Chassis No. Number Police Station 1 Suzuki Samurai AP10Q2464 7104M965233 7104F911702 Begumbazar 2 Passion Pro AP10AE7645 HA10EC9GM01846 MBLHA10EM9GM01374 -do- 3 Honda Unicorn AP29H3124 KC09E0043794 ME4KC094D58043719 -do- 4 Kawasaki AP28AB2445 DFMBHD71954 DFFBHD10198 -do- 5 HERO HONDA CBZ AP 02 Q 8997 07KBMM02272 07KBMC02428 Kachiguda 6 TVS SPORT AP 10 AS 6740 DF5NB1095478 MD625MF54B1N12709 -do- 7 PASSION PRO AP 29 AH 1220 HA10EC9GD01496 MBLHA10EM9GD02396 -do- 8 Chetak AP 22 D 4398 35MBDJ97370 06FBDJ09081 -do- 9 TVS XL MH 30 AJ 2329 Not found MD621DD1301E33358 -do- 10 Avenger TS09AHTR5697 PDZCGD16714 MD2A85CZ6GCD00825 -do- 11 Chetak AP 28 B 4461 P06M048515 B06M04701 -do- 12 Passion AP28 CP 8858 HA10EB9GA13168 MBLHA10EG9GA02848 -do- 13 Discover AP 11 AH 8327 JNGBSF34487 MD2DSJNZZSCF87658 -do- 14 Chetak AP 31 G 5519 Not found Not found -do- 15 Hero Honda AP 09 AX 8487 Not Found Not found -do- 16 Hero Honda AP 11 Q 7664 05K08M00396 05K09C25551 -do- 17 Kinetic ZX AP 13 F 3063 NIEUJ282879 NIFUJ286648 -do- 18 Kinetic ZX AP 20 G 3778 NIETH208059 NIFTH211922 -do- 19 BAJAJ CT 100 AP 10 AE 4120 DUMBLK03833 DUFBLK22467 -do- 20 BAJAJ CT 100 AP 10 J 7529 7705M858373 770J8812663 -do- 21 BAJAJ CT 100 AP 11 K 7570 DXEBMK29155 MD2DSDXZZMAK28191 -do- 22 CHETAK AP 28 B 6911 06E93F65712 06C93F69028 -do- 23 BAJAJ CT 100 AP 29 F 1006 DUMBLG29426 DUFBLG32913 -do- 24 Hero Honda CD 100 AP 10 571 1 010E250858 010F251156 -do- 25 DISCOVER AP 22 S 0874 JAUBSB00904