NTSB-AAR-79-18- C .3
Total Page:16
File Type:pdf, Size:1020Kb
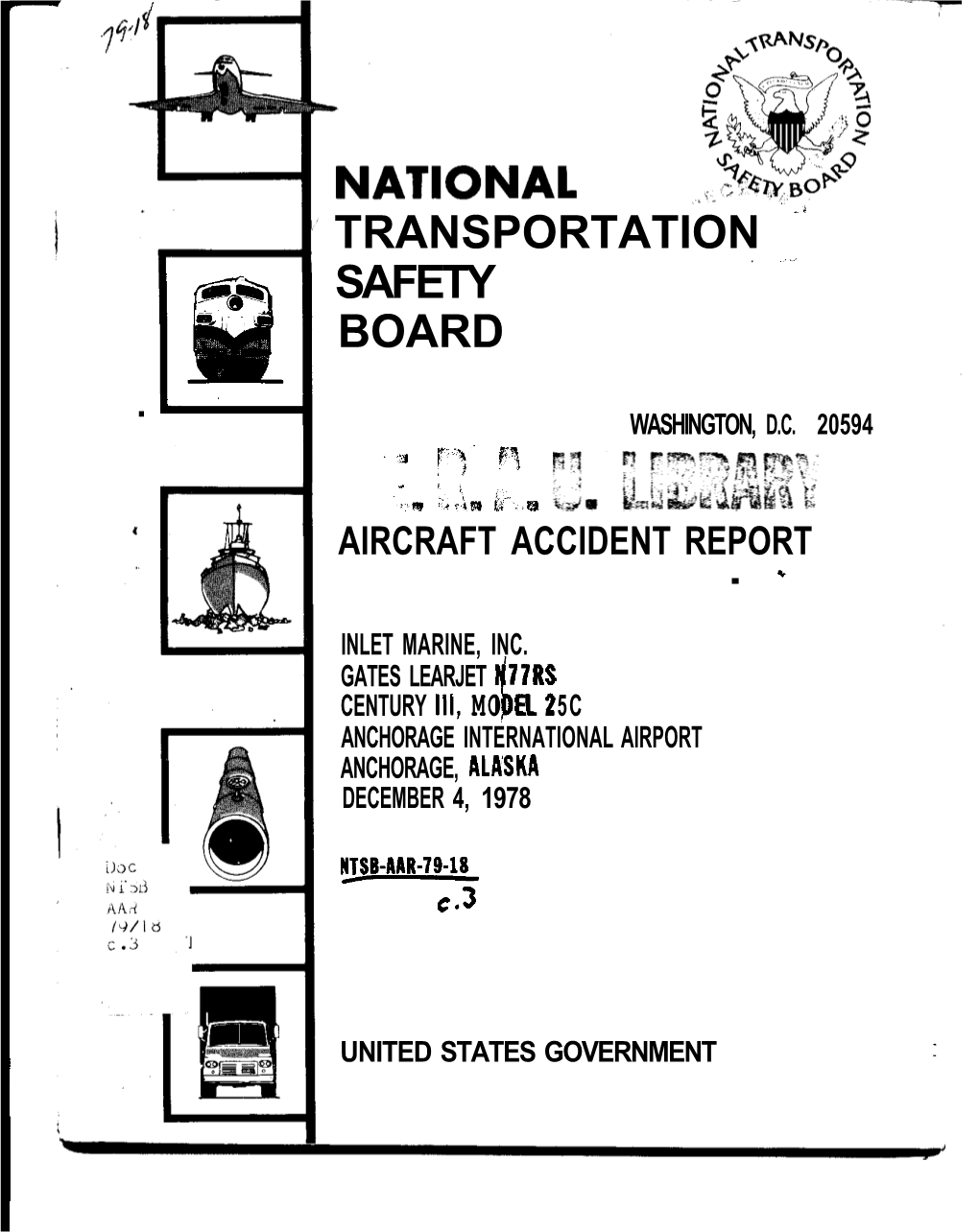
Load more
Recommended publications
-
Aviation Wheel Well and Platform Stands Df071556
AVIATION WHEEL WELL AND PLATFORM STANDS DF071556 SA LIFT FE AVIATION WHEEL WELL AND PLATFORM STANDS F . A C L L IN PR N OTECTIO DESCRIPTION The Aviation Wheel Well and Platform Stand has been designed for maintenance access points for multiple aircraft. The lowered position is designed to clear wheel well entry points and has been tested and is operational on both Airbus and Boeing wide body aircraft. Optional telescopic side rails ensure safety compliant access to the forward and AFT lower cargo holds. The Aviation Wheel Well and Platform Stand is hydraulically actuated via a foot pump and has collapsible guardrails. The platform stand can also be used to service engines, pylons, radome and AFT fuselage points. Our Professional Engineers can design custom models based on your specific requirements. PRODUCT FEATURES • Anti-slip, anti-fatigue ladder steps WHAT OUR CUSTOMERS ARE SAYING • Hydraulically actuated “We use them in both the line and hangar maintenance to • Collapsible guardrails accomplish work on the engine and pylons for our wide • Corrosion and Skydrol®-resistant powder coat finish body aircraft. These stands are an excellent solution to a • Fail-safe hydraulic cylinder locks long-standing problem — providing fall safety protection • Optional front and rear guardrails and gates in difficult to access areas.” • Split wheel castors for easy movement • Designed and tested in accordance with ANSI-ASC A14.7 and BS EN 131.7, DIN EN 12312-8, EN 1915-1, and includes CE Certification BENEFITS • Fall restraint tie points • Optional extension -
(12) Patent Application Publication (10) Pub. No.: US 2013/0099053 A1 Barmichev Et Al
US 2013 0099053A1 (19) United States (12) Patent Application Publication (10) Pub. No.: US 2013/0099053 A1 Barmichev et al. (43) Pub. Date: Apr. 25, 2013 (54) MID-WING MULTI-DECK AIRPLANE B64C 9/00 (2006.01) B64C I/I) (2006.01) (75) Inventors: Sergey D. Barmichev, Kirkland, WA B64C25/10 (2006.01) (US); Mithra M.K.V. Sankrithi, Lake B64C II/00 (2006.01) Forest Park, WA (US); Kevin M. Retz, (52) U.S. Cl. Bothell, WA (US) USPC ........... 244/102 R; 24.4/73 R: 244/65: 244/91 (73) Assignee: THE BOEING COMPANY, Irvine, CA (57) ABSTRACT (US) An airplane comprises a twin-deck fuselage in which an (21) Appl. No.: 13/276,357 upper deck Support structure is utilized for carry-through of a mid-mount main wing box. The main landing gear of the (22) Filed: Oct. 19, 2011 airplane is mounted to the fuselage and is stowed in a non pressurized area below the main wing box (enabled due to an Publication Classification optimized wing box geometry). A pressurized passageway/ cargo/galley complex separates the main landing gear box (51) Int. Cl. and the main wing box. The upper deck is continuous, while B64D II/00 (2006.01) the lower deck is separated by the wheel wells into two B64C I/20 (2006.01) distinct fore and aft areas (for either cargo or passengers). The B64D I3/02 (2006.01) airplane further comprises an integrated vertical fin and an B64D 27/2 (2006.01) aft-extended pressurized deck area for reduced double-deck B64C I/06 (2006.01) wetted area. -
Specification and Description
CITATION CJ3+ SPECIFICATION AND DESCRIPTION REVISION C JANUARY 2021 SERIAL NUMBER 525B0610 TO TBD SPECIFICATION AND DESCRIPTION CITATION CJ3+ SERIAL NUMBER 525B0610 TO TBD JANUARY 2021 REVISION C TABLE OF CONTENTS LIST OF FIGURES ..............................................................................................................................iv INTRODUCTION ..................................................................................................................................1 THE AIRCRAFT................................................................................................................................... 2 1. GENERAL DESCRIPTION ....................................................................................................2 1.1 Certifi cation...................................................................................................................... 2 1.2 Purchaser’s Responsibility......................................................................................... 2 1.3 Approximate Dimensions .......................................................................................... 5 1.4 Design Weights and Capacities .............................................................................. 5 2. PERFORMANCE .................................................................................................................... 5 3. DESIGN LIMITS ...................................................................................................................... 6 4. FUSELAGE ...............................................................................................................................7 -
Throttles Only Control.P65
INTERpilot – 2004 THROTTLES ONLY CONTROL (TOC) 10 Steps to a Survivable Landing Following Loss of Normal Flight Control Captains Terry Lutz, Air Line Pilots Association, International and Brian Greeves, Hong Kong Air Line Pilots' Association Captain Terry Lutz Captain Brian Greeves Few emergencies in commercial aviation are more terrifying to the flight crew than loss of normal flight control. The July 1989 United Airlines DC-10 accident in Sioux City, Iowa and the November 2003 missile attack on the DHL A-300 departing Baghdad are examples where the crew lost all hydraulically powered flight controls. In both cases, the flight crew regained flight path control using throttles only, and were able to bring the airplane to a less than precise touchdown at an airport. Modern aircraft are exceptionally well designed, numerous systems failures, including rapid particularly from the standpoint of reliability and decompression, the crew had to deal with large pitch redundancy in the flight control system. Using failure oscillations and loss of directional control with throttles analysis techniques that consider all known failure alone. They were able to extend the landing gear, but modes and their subsequent effects on the flight as the crew explored what flight control remained, control system, modern flight control systems are they were unable to avoid hitting a mountain and 520 designed for a failure probability of 10-9 or less. Loss lives were lost. of flight control accidents that have happened over the The Boeing Company conducted their own tests after last 30 years have occurred because of an unpredicted this accident, and were able to successfully slow a event such as fan disk failure, aft pressure bulkhead Boeing B-747-200 from cruise configuration and speed failure, or loss of a cargo door. -
Aircraft Energy Efficiency Laminar Flow Control Glove Flight Conceptual Design Study
IIIIII~IIIIIIIIIIIIIIIIIIIIIIIIIIIIIIIIIIIIIIIIIIIIIIIIIII1III1 3 1176 00133 9846 NASA Technical Memorandum 80054 1 I , NASA-TM-8005419790011929 ! AIRCRAFT ENERGY EFFICIENCY LAMINAR FLOW CONTROL GLOVE FLIGHT CONCEPTUAL DESIGN STUDY Andrew S. Wright JANUARY 1979 NI\S/\ National Aeronautics and Space Administration Langley Research Center Hampton, Virginia 23665 \\\\\\\\\ \\\\ \\\\ \\\\\ \\\\\ \\\\\ \\\\\ \\\\ \\\\ NF00545 1 Report No I 2 Government Accession No 3 Recipient's Catalog No NASA TM 80054 4 Title and Subtitle 5 Report Date Aircraft Energy Efficiency Laminar Flow Control 6 Performing Organization Code Glove Flight Conceptual Design Study 7 Author(s) 8 Performing Organization Report No Andrew S. Wright I---------------------------~ 10 Work Unit No 9 Performing Organization Name and Address 514 .. 55 .. 03-21 NASA, Langley Research Center Hampton, Virginia 23665 11 Contract or Grant No I-__________________________~ 13 Type of Report and Period Covered 12 Sponsoring Agency Name and Address Technical Memorandum National Aeronautics and Space Administration Washington, DC 20546 14 Sponsoring Agency Code 15 Supplementary Notes 16 Abstract A conceptual design study of a laminar flow control glove applied to the wing of a short to medium range jet transport with aft mounted engines has been completed. Two suction surfaces were studied--aslotted aluminum glove concept and a woven stainless steel mesh porous glove concept. The laminar flow control glove and a dummy glove with a modified supercritical airfoil, ducting, modified wing leading and trailing edges, modified flaps and an LFC trim tab were applied to the wing after slot spacing suction parameters, and compression power were determined. The results of the study show that a laminar flow control glove can be applied to the wing of a jet transport with an appropriate suction system installed. -
Hondajet Model HA-420
Honda Aircraft Company PILOT’S OPERATING MANUAL HondaJet Model HA-420 Original Issue: December 10, 2015 Revision B2: March 3, 2017 This Pilot’s Operating Manual is supplemental to the current FAA Approved Airplane Flight Manual, HJ1-29000-003-001. If any inconsistencies exist between this Pilot’s Operating Manual and the FAA Approved Airplane Flight Manual, the FAA Approved Airplane Flight Manual shall be the governing authority. These commodities, technology, or software were exported from the United States in accordance with the Export Administration Regulations. Diversion contrary to U.S. law is prohibited. P/N: HJ1-29000-005-001 Copyright © Honda Aircraft Company 2016 FOR TRAINING PURPOSES ONLY Honda Aircraft Company Copyright © Honda Aircraft Co., LLC 2016 All Rights Reserved. Published by Honda Aircraft Company 6430 Ballinger Road Greensboro, NC 27410 USA www.hondajet.com Copyright © Honda Aircraft Company 2016 FOR TRAINING PURPOSES ONLY Honda Aircraft Company LIST OF EFFECTIVE PAGES This list contains all current pages with effective revision date. Use this list to maintain the most current version of the manual: Insert the latest revised pages. Then destroy superseded or deleted pages. Note: A vertical revision bar in the left margin of the page indicates pages that have been added, revised or deleted. MODEL HA-420 PILOT’S OPERATING MANUAL Title Page ...................................................................... March 3, 2017 Copyright Page ............................................................. March 3, 2017 List of Effective Pages .................................................. March 3, 2017 Record of Revisions ..................................................... March 3, 2017 Record of Temporary Revisions ................................... March 3, 2017 List of Service Bulletins ............................................... March 3, 2017 Documentation Group .................................................. March 3, 2017 SECTION 1 – SYSTEMS DESCRIPTION Pages 1 – 232 .......................................................... -
National Transportation Safety Board Aviation Accident Final Report
National Transportation Safety Board Aviation Accident Final Report Location: COLO SPRINGS, CO Accident Number: FTW98FA074 Date & Time: 12/21/1997, 0626 MST Registration: N100BE Aircraft: Beech A100 Aircraft Damage: Destroyed Defining Event: Injuries: 2 Fatal, 1 Serious Flight Conducted Under: Part 135: Air Taxi & Commuter - Non-scheduled Analysis The pilot was cleared for an ILS DME approach to runway 17L. During the final stage of the approach, the aircraft entered fog and disappeared from view of the control tower personnel. Radar and radio communications were lost also. After searching for 31 minutes, the aircraft was found by airport operations personnel over half way down the runway and 600 feet east of the runway. There was no evidence the aircraft touched down on the runway. The aircraft was configured with the landing gear up and the flaps deployed. Missed approach procedures require the flaps and landing gear to be retracted after initiating the procedure. The decision height for the approach is 6,384 feet msl (200 feet above ground level) and the required RVR for a 14 CFR Part 135 flight to commence and approach is 2400 (1/2 mile). When on the glide slope, the decision height is 0.4 miles from the runway touchdown zone. Examination of the airplane did not disclose evidence of mechanical malfunction.. Probable Cause and Findings The National Transportation Safety Board determines the probable cause(s) of this accident to be: Failure of the pilot to follow IFR Procedures and maintain the minimum descent altitude (MDA). A related factor was fog. Findings Occurrence #1: IN FLIGHT COLLISION WITH TERRAIN/WATER Phase of Operation: MISSED APPROACH (IFR) Findings 1. -
1. INTRODUCTION the Environmental Control System (ECS)
Canadair Regional Jet 100/200 - Environmental Control System 1. INTRODUCTION The environmental control system (ECS) provides temperature and pressure regulated air for heating, ventilating and pressurizing the flight and passenger compartments. Exhaust air, from the compartments, is used to ventilate the avionics and cargo compartments, before being dumped overboard through two outflow valves. For ground operations, pneumatic air to operate the ECS can be obtained from: A ground air supply cart connected to the aircraft The auxiliary power unit (APU) Either or both engines. During flight, the engines normally supply bleed air for operating the air-conditioning, pressurization, and avionics cooling systems. ECS warnings and cautions are displayed on the engine indication and crew alerting system (EICAS) primary page. ECS advisory and status messages are displayed on the EICAS status page. Views of the aircraft ECS temperature, pressure, valve positions and system status indications are displayed on the EICAS ECS synoptic page. Page 1 Canadair Regional Jet 100/200 - Environmental Control System AFT PRESSURE RAM AIR FLIGHT PASSENGER CABIN BULKHEAD INLET COMPARTMENT GASPER SYSTEM OUTFLOW VALVES (2) DUAL POSITION LEGEND VALVE Pressurized and conditioned by air conditioning system. Pressurized by air SOV DISTRIBUTION MANIFOLD exhausted from RAM cockpit/cabin AIR no temperature LP GROUND control. LEFT CONDITIONED RIGHT Heated by exhaust PACK AIR PACK air from CONNECTION electronics chassis. PACK PRSOV’s Unpressurized 10 TH 10 TH STAGE STAGE L/H ISOL R/H SOV SOV AUXILIARY GROUND POWER POWER UNIT UNIT (HIGH PRESSURE PNEUMATIC SUPPLY) Tvyvsvrq 7ypx 9vht h A v t r ' Page 2 Canadair Regional Jet 100/200 - Environmental Control System 1. -
Pages 65885-65887] from the Federal Register Online Via the Government Printing Office [ [FR Doc No: 2014-26330]
[Federal Register Volume 79, Number 215 (Thursday, November 6, 2014)] [Rules and Regulations] [Pages 65885-65887] From the Federal Register Online via the Government Printing Office [www.gpo.gov] [FR Doc No: 2014-26330] –––––––––––––––––––––––––––––––––– DEPARTMENT OF TRANSPORTATION Federal Aviation Administration 14 CFR Part 39 [Docket No. FAA-2014-0288; Directorate Identifier 2013-NM-101-AD; Amendment 39-18009; AD 2014-22-04] RIN 2120-AA64 Airworthiness Directives; The Boeing Company Airplanes AGENCY: Federal Aviation Administration (FAA), DOT. ACTION: Final rule. –––––––––––––––––––––––––––––––––– SUMMARY: We are adopting a new airworthiness directive (AD) for certain The Boeing Company Model DC-9-10, DC-9-20, and DC-9-30 series airplanes. This AD was prompted by an evaluation by the design approval holder (DAH) indicating that the improved (shot-peened) aft fuselage non-ventral pressure bulkhead tee is subject to widespread fatigue damage (WFD). This AD requires repetitive inspections for cracking of the improved (shot-peened) non-ventral aft pressure bulkhead tees, and replacement if necessary. We are issuing this AD to detect and correct fatigue cracking of the improved (shot-peened) non-ventral aft pressure bulkhead tees connecting the bulkhead web to the fuselage, which could result in reduced structural integrity and rapid decompression of the airplane. DATES: This AD is effective December 11, 2014. The Director of the Federal Register approved the incorporation by reference of a certain publication listed in this AD as of December 11, 2014. ADDRESSES: For service information identified in this AD, contact Boeing Commercial Airplanes, Attention: Data & Services Management, 3855 Lakewood Boulevard, MC D800-0019, Long Beach, CA 90846-0001; telephone 206-544-5000, extension 2; fax 206-766-5683; Internet https://www.myboeingfleet.com. -
C-5 Handbook
FOR TRAINING USE ONLY C-5 HANDBOOK FOR TRAINING USE ONLY INTRODUCTION This book is designed to be used as a T.O. title. Example: page 3-1 comes from quick-reference pocket handbook T.O. 1C-5A-2-3/Pneudraulics. describing the systems and subsystems of the C-5 Galaxy aircraft. Basically, the handbook consists of descriptive text relating to pictures or As a training aid, this book gives you the drawings of the airplanes structural and distinct advantage of having the general system components. information of twelve aircraft T.O.s condensed into one handbook. For the most part, pictures and text within the book reflect that of the C-5B model The book is formatted in accordance with aircraft. However, in some cases, the aircraft T.O.s, 1C-5A-2-1 through references to "A-model not modified" and 2-13, with the exception of the 2-11 wiring AF68-213 and AF68-216 "Space diagrams, which, due to the size and Container Module (SCM) airplanes " have content could not be included. Each been included. chapter in the handbook represents an aircraft T.O. starting with the 2-1. ALTHOUGH THIS HANDBOOK IS Additionally, for quick reference DERIVED FROM TECH DATA, IT IS purposes, the first digit of the page NOT INTENDED TO REPLACE THE numbers represents the last number of T.O.s. NOR, WILL IT BE USED AS the T.O. from which the information was SUCH. obtained and the page header reflects the i PRESSURES, READINGS, AND LIMITATIONS ARE SUBJECT TO CHANGE AND ARE ONLY USED IN THIS BOOK TO PROVIDE GENERAL PARAMETERS ii TABLE OF CONTENTS INTRODUCTION . -
Airframes and Systems
Airframes and Systems I. Fuselage II. Cockpit and Cabin Window III. Wing IV. Stabilizing surfaces V. Landing gear VI. Flight controls (construction and operation) VII. Hydraulics VIII. Air Driven System (Piston Engine) IX. Air Driven System (Turbo propeller And Jet Aircraft) X. Non-pneumatic operated de-ice and anti-ice systems XI. Fuel System Fuselage: 1.What are the most frequent used materials in a monocoque or semi-monocoque structure? A) Wood. B) Composite fibres. C) Aluminium or magnesium alloy. D) Steel. A framework of truss type fuselage is used in: A) Supersonic aircraft B) Medium range commuter type turbo-props C) Heavy wide bodied subsonic turbo-fan aircraft D) Light training aircraft mainly A semi-monocoque fuselage has... in the longitudinal direction. Together with the frames, they resist... moments and axial forces. The skin panels are loaded mainly in... A) Bars, buckling, bending. B) Stringers, bending, shear. C) Spars, torsion, shear. D) Stringers, bending, buckling. Aircraft structures consists mainly of: A) Magnesium alloy sheets with aluminium rivets and titanium or steel at points requiring high strength. B) Light alloy steel sheets with copper rivets and titanium or steel materials at points requiring high strength. C) Aluminium alloy sheets and rivets with titanium or steel materials at points requiring high strength. D) Aluminium sheets and rivets with titanium or steel materials at points requiring high strength. What is the purpose of the stringers? A) To absorb the torsional and compressive stresses. B) To support the primary control surfaces. C) To produce stress risers. D) To prevent buckling and bending by supporting and stiffening the skin. -
Losing the Cabin
FLIGHTOPS Insights on civil aircraft depressurization. BY MARK LACAGNINA the A cabin depressurization likely will be survived if it is recognized early and the appropriate emergency procedures are con- ducted expeditiously, according to a recent report by the Australian Transport Safety Bureau (ATSB). © Copyright 2006 iStockphoto© Copyright WWW.FLIGHTSAFETY.ORG | AVIATIONSAFETYWORLD | OCTOBER 2006 | 33 FLIGHTOPS © Copyright 2006 iStockphoto iting a paucity of studies of accidents and light on how often such events occur, why they incidents involving cabin depressuriza- occur and what happens when they occur.1 tion in civil aircraft, ATSB delved into Sifting through 8,302 accidents, 95 seri- more than 30 years of data to throw more ous incidents (near accidents) and 151,941 C incidents that occurred in Australia from Jan. 1, 1975, through March 31, 2006, researchers Pressurization Failure Events by Five-Year Periods identified 517 as “pressurization failure events.” Figure 1 shows the events grouped in five-year 140 periods. “The apparent increase in depres- 120 s t surization [events] from 1985–1989 to a peak n 100 e v E in 2000–2004 may be due to several factors, f 80 o r such as changes in reporting and recording of e 60 b events, differences in aircraft fleet composition m 40 u N with each epoch, differences in hours flown per 20 five-year period, etc.,” the report said. “In the 0 1975–79 1980–84 1985–89 1990–94 1995–99 2000–04 absence of more information, it is not possible Five-Year Period to attribute any specific significance to this ap- Source: Australian Transport Safety Bureau parent trend.” Table 1 shows that two-thirds of the events Figure 1 occurred in airline operations.