One-Bath Pretreatment for Enhanced Color Yield of Ink-Jet Prints Using Reactive Inks
Total Page:16
File Type:pdf, Size:1020Kb
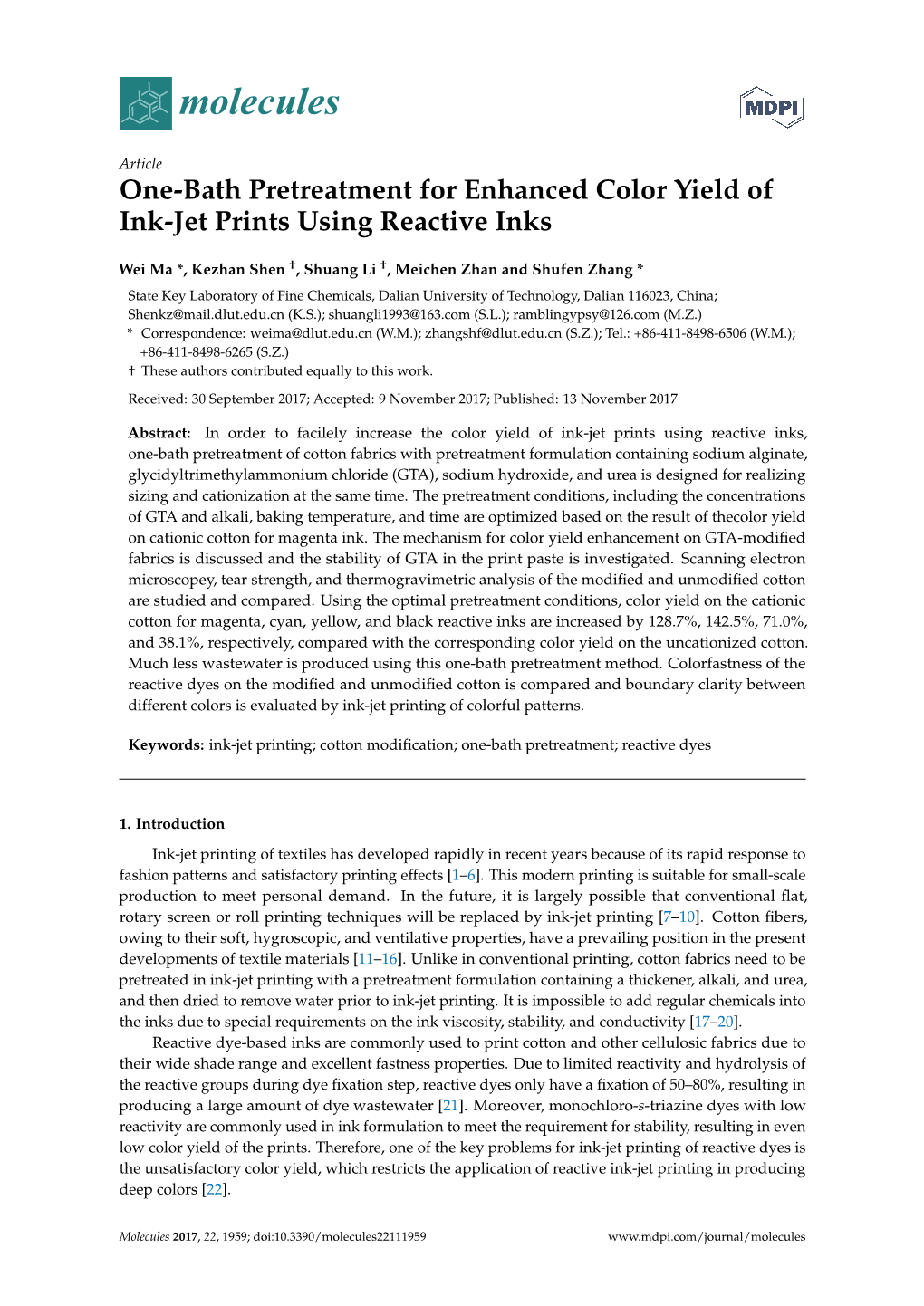
Load more
Recommended publications
-
A Comparison of the Patterns Formed by Primary Textile Structures and Their Photographic Abstraction
Rochester Institute of Technology RIT Scholar Works Theses 9-22-1976 A comparison of the patterns formed by primary textile structures and their photographic abstraction Pamela Perlman Follow this and additional works at: https://scholarworks.rit.edu/theses Recommended Citation Perlman, Pamela, "A comparison of the patterns formed by primary textile structures and their photographic abstraction" (1976). Thesis. Rochester Institute of Technology. Accessed from This Thesis is brought to you for free and open access by RIT Scholar Works. It has been accepted for inclusion in Theses by an authorized administrator of RIT Scholar Works. For more information, please contact [email protected]. Thesis Proposal for the Master of Fine Arts De gree Collee;e of Fine and Applj_ed .Arts Rochester Institute of Technology Title: A Comparison of the Fatterns Formed by Primary Textile structures and their Phot ographic Abstraction Submitted by: Pamela Anne Perlman Date: September 22, 1976 Thesis Co mm it te~: Nr . Donald Du jnowski I-Ir. I,l az Lenderman hr. Ed 1iiller Depart~ental Approval : Date :-:--g---li6~-r-71-b-r-/ ----- ---------~~~~~'~~~r------------------------- Chairman of the School for American Craftsme:l: ___-r-----,,~---- ____ Da t e : ---.:...,'?7~JtJ--J7~i,-=-~ ___ _ Chairr.ian of the Gr3.duate Prog:rarn: ------------------------~/~~/~. --- Date: ___________________~ /~~,~~;j~~, (~/_' ~i~/~: 7 / Final Committee Decision: Date: ----------------------- Thesis Proposal for the Master of Fine Arts Degree College of Fine and Applied Arts Rochester Institute of Technology Title: A Comparison of the Patterns Frmed by Primary Textile Structures and their Photographic Abstraction My concern in textiles is with structure and materials. I v/ould like to do v/all hangings based on primary textile structures such as knotting, looping, pile, balanced weaves, and tapestry. -
Eco-Friendly Functional Resist Printing for Viscose Fabrics
International Design Journal Volume 10 Issue 2 Article 35 2020 Eco-Friendly Functional Resist Printing for Viscose Fabrics Abeer Ibrahim Fathallah; Textile Printing, Dyeing and Finishing Department, Faculty of Applied Arts, Helwan University, [email protected], [email protected] El-Amir M. Emam; Textile Printing, Dyeing and Finishing Department, Faculty of Applied Arts, Helwan University., [email protected] Mahmoud A. Ali Textile Printing, Dyeing and Finishing Department, Faculty of Applied Arts, Helwan University., [email protected] Follow this and additional works at: https://digitalcommons.aaru.edu.jo/faa-design Part of the Art and Design Commons Recommended Citation Fathallah;, Abeer Ibrahim; Emam;, El-Amir M.; and Ali, Mahmoud A. (2020) "Eco-Friendly Functional Resist Printing for Viscose Fabrics," International Design Journal: Vol. 10 : Iss. 2 , Article 35. Available at: https://digitalcommons.aaru.edu.jo/faa-design/vol10/iss2/35 This Article is brought to you for free and open access by Arab Journals Platform. It has been accepted for inclusion in International Design Journal by an authorized editor. The journal is hosted on Digital Commons, an Elsevier platform. For more information, please contact [email protected], [email protected], [email protected]. 387 Abeer Fathllah et al. Eco-Friendly Functional Resist Printing for Viscose Fabrics Abeer I. Fathallah, Textile Printing, Dyeing and Finishing Department, Faculty of Applied Arts, Helwan University, [email protected] El-Amir M. Emam Textile Printing, Dyeing and Finishing Department, Faculty of Applied Arts, Helwan University. Mahmoud A. Ali Textile Printing, Dyeing and Finishing Department, Faculty of Applied Arts, Helwan University. Abstract: Keywords: This study focused on demonstrates improving the antibacterial activity and Eco-Friendly, White Resists white resist printing for viscose fabrics in one step. -
C-20 Second Year Diploma Curriculum Textile Technology
Government of Karnataka Department of Collegiate and Technical Education C-20 Second Year Diploma Curriculum Textile Technology Curriculum Development Cell, DTE 2021-22 Government of Karnataka DEPARTMENT OF COLLEGIATE AND TECHNICAL EDUCATION Curriculum Structure III Semester Scheme of Studies- Diploma in Textile Technology CIE SEE Hours per week Marks Marks Sl.No. Course Code Course Name /week L T P Credits Max Min Max Min Teaching CIE marks) Grade Point Total Marks Department Min Marks for SGPA and CGPA Assigned Grade Total contact hrs Course Category / Passing (including Integrated Courses 1 PC/TX 20TX31P YARN MANUFACTURE-II 3 1 4 8 6 60 24 40 16 100 40 2 PC/ TX 20TX32P FABRIC FORMING-I 3 1 4 8 6 60 24 40 16 100 40 3 PC/ TX 20TX33P COLORATION OF TEXTILES 3 1 4 8 6 60 24 40 16 100 40 4 PC/ TX 20TX34P TEXTILE TESTING-I 3 1 4 8 6 60 24 40 16 100 40 Audit Course Both SGPA & CGPA 5 AU/KA 20KA31T !ಾ#ತ% &ಂಚನ-II/ ಬಳ/ೆ ಕನ2ಡ-II 2 0 0 2 2 50 20 - - 50 20 Total 14 4 16 34 26 290 116 160 64 450 180 *PC: Programme Core:: AU-Audit Course:: KA: Kannada:: L: Lecture:: T: Tutorial:: P: Practice Department of Collegiate and Technical Education, Government of Karnataka 1 Government of Karnataka DEPARTMENT OF COLLEGIATE AND TECHNICAL EDUCATION Curriculum Structure IV Semester Scheme of Studies- Diploma in Textile Technology CIE SEE Hours per week Marks Marks Sl.No. Course Code Course Name Category / /week L T P Credits Max Min Max Min Teaching CIE marks) Grade Point Total Marks Department Min Marks for SGPA and CGPA Assigned Grade Total contact hrs Course -
Synthesis of Novel Reactive Dyes for Textile Applications CHEMISTRY
Synthesis of Novel Reactive Dyes for Textile Applications By Umme Habibah Siddiqua (M.Phil UAF) 2009-ag-107 A Thesis Submitted in Partial Fulfillment of the Requirements for the Degree of DOCTOR OF PHILISOPHY IN CHEMISTRY DEPARTMENT OF CHEMISTRY AND BIOCHEMISTRY FACULTY OF SCIENCES UNIVERSITY OF AGRICULTURE FAISALABAD 2016 i ii iii My Affectionate Parents Whose esteemed love enabled me to get the success and whose hearts are always beating to wish for me maximum felicity in life. iv v ACKNOWLEDGEMENT All praises to Almighty ALLAH, the creator, dominant, self existing and sustainer, who enabled me to accomplish this project and all respect is for his last Prophet MUHAMMAD (Peace and Blessing of Allah Be Upon Him) who is forever a torch of guidance and knowledge in our life. I pay my humble gratitude to my worthy supervisor Dr. Shaukat Ali, Dept. of Chemistry, University of Agriculture, Fasisalabad and Co-Supervisor Dr. Tanveer Hussain, Dept. of Textile Processing, National Textile University, Faisalabad for their absorbing attitude, constant guidance, timely suggestions, inspiration and encouragement throughout my studies. I offer my cordial and profound thanks to Prof. Dr. Haq Nawaz Bhatti Chairman, Dept. of Chemistry, University of Agriculture, Fasisalabad and Prof. Dr. Asgher Bajwa for their co-operation, valuable suggestions and guidance during my research and compilation of my thesis. I am lucky enough to have the support of many good friends. Special thanks are extended to Asma Hanif, Anum Sahar, Asma Tufail, Sana Sadaf, Sana Nosheen, Shazia Muzzafar for their prayers, moral support and sincere suggestions. I want to express my gratitude, deep appreciation and very special thanks to Textile processing staff of the National Textile University, Faisalabad, without their help, moral support and encouragement it would not be possible for me to complete my degree in such a good way. -
B.Tech FT R2020
SRI MANAKULA VINAYAGAR ENGINEERING COLLEGE (An Autonomous Institution) Puducherry B.TECH. FASHION TECHNOLOGY ACADEMIC REGULATIONS 2020 (R-2020) CURRICULUM AND SYLLABI 2 Academic curriculum and syllabi R-2020 COLLEGE VISION AND MISSION VISION To be globally recognized for excellence in quality education, innovation and research for the transformation of lives to serve the society. MISSION M1: Quality Education : To provide comprehensive academic system that amalgamates the cutting edge technologies with best practices. M2: Research and Innovation : To foster value-based research and innovation in collaboration with industries and institutions globally for creating intellectuals with new avenues. M3: Employability and : To inculcate the employability and entrepreneurial skills through Entrepreneurship value and skill based training. M4: Ethical Values : To instill deep sense of human values by blending societal righteousness with academic professionalism for the growth of society. DEPARTMENT VISION AND MISSION Vision To be the premier institution for the graduates to excel in technical and professional competencies with a multi-faceted approach by raising the standard to be a trend-setter and job-provider in the ever-growing Fashion Industry across the globe. Mission M1: Quality of Education : To educate students with high-impact experiential learning environment through relevant curriculum M2: Research and Innovation : To inculcate research oriented curriculum in order to equip them to appraise the real-world problems and formulate feasible solutions. M3: Industrial and Societal needs : To guide them in design forecasting by learning the dynamic trend In fashion industry and changes in customer preferences. M4: Global Participants : To impart hands-on training to students with state of the art infrastructure and to provide conducive atmosphere for teaching and learning M5: Employability : To prepare and equip the graduates according to the latest Fashion Trends. -
Eco-Friendly Functional Resist Printing for Viscose Fabrics
387 Abeer Fathllah et al. Eco-Friendly Functional Resist Printing for Viscose Fabrics Abeer I. Fathallah, Textile Printing, Dyeing and Finishing Department, Faculty of Applied Arts, Helwan University, [email protected] El-Amir M. Emam Textile Printing, Dyeing and Finishing Department, Faculty of Applied Arts, Helwan University. Mahmoud A. Ali Textile Printing, Dyeing and Finishing Department, Faculty of Applied Arts, Helwan University. Abstract: Keywords: This study focused on demonstrates improving the antibacterial activity and Eco-Friendly, White Resists white resist printing for viscose fabrics in one step. Chitosan is the Printing, Chitosan, Viscose deacetylated derivative of chitin; it is a functional biopolymer which can be fabrics, Antibacterial, safely used for textile wet process. The efficacy of resisting agent was Reactive Dyes studied in comparison with standard unprinted illuminated fabrics. Results show that an improvement in antibacterial activity and dye blocking. In all cases, the reprinted fabrics were more oversensitive towards Gram positive bacteria than Gram negative bacteria due to bacteria structure. This method can be suitable for eco-friendly resist printing on viscose fabrics. Paper received 25th November 2019, Accepted 26th December 2019, Published 1st of April 2020 INTRODUCTION the textile itself from damage caused by mildew Today, the environmental impacts are now producing microorganisms. becoming an important factor during the selection The actual mechanisms by which antibacterial of wet process of textile industry. However, due to finishes control bacterial growth are extremely increased awareness of the nature of polluting varied, ranging from preventing cell reproduction, textiles effluents, social pressures are increasing blocking of enzymes, and reaction with the cell on textile wet processing units. -
Techniques of Decoration and Coloration
Patterns of Culture ULI T A Techniques of Decoration and Coloration by M. A. Hann Title: Patterns of Culture - Techniques of Decoration and Coloration Author: M. A. Hann Foreword: D. Holdcroft Ars Textrina no.35, a monograph in the Ars Textrina series, published in association with the University of Leeds International Textiles Archive (ULITA) as an accompaniment to the exhibition ‘Patterns of Culture - Techniques of Decoration and Coloration’. Copyright © 2005 The University of Leeds and the author. All rights reserved. ISBN: 0-9549640-0-4 Acknowledgements The organisation of the exhibition, to which this monograph is an accompaniment, was facilitated by the endeavours of Mr J. A. Smith, Mr P. Lawson, Ms B. Thomas and Ms A. Chu. Thanks are also due to Mr I. S. Moxon for reading various proofs of the monograph and for discussions relating to aspects of its contents. The author accepts responsibility for errors or omissions. Foreword The exhibition ‘Patterns of Culture - Techniques of Decoration and Coloration’ focuses on a particular aspect of decorated textiles: techniques of coloration and patterning, particularly resist dyeing (including tie-and- dye, ikat and batik) as well as printing with the assistance of blocks and stencils. The monograph is published to accompany the exhibition with the same title; the latter includes textiles from India, Pakistan, Indonesia, Malaysia, Japan and West Africa. D. Holdcroft (Chairman of the ULITA Committee) Price of the monograph: £5.00. All proceeds to ULITA CONTENTS Contents Foreword. 1. Introduction. 2. Block / Stencil Printing. 2.1 Direct Printing. 2.2 Resist Printing. 2.3 Mordant Printing. 2.4 Discharge Printing. -
Aplikasi Campuran Alginat Dari Sargassum Crassifolium Dan Gum
Aplikasi Campuran Alginat dari Sargassum crassifolium dan Gum.................(Subaryono et al.) APLIKASI CAMPURAN ALGINAT DARI Sargassum crassifolium DAN GUM SEBAGAI PENGENTAL TEXTILE PRINTING Applications of the Mixture of Alginate from Sargassum crassifolium with Gum as a Textile Printing Thickener Subaryono1*, Tazwir1, Amir Husni2, Ustadi2, dan Yudi Pranoto3 1 Balai Besar Penelitian dan Pengembangan Pengolahan Produk dan Bioteknologi Kelautan dan Perikanan, Jl. K.S. Tubun Petamburan VI, Jakarta Pusat, Indonesia 2 Jurusan Perikanan Fakultas Pertanian UGM, Yogyakarta, Indonesia 3 Fakultas Teknologi Pertanian UGM, Yogyakarta, Indonesia * Korespondensi Penulis: [email protected] Diterima: 10 Juli 2015; Disetujui: 12 Oktober 2015 ABSTRAK Penelitian aplikasi campuran alginat dari Sargassum crassifolium dan gum untuk meningkatkan viskositas alginat sebagai pengental pada textile printing telah dilakukan. Viskositas campuran alginat dengan guar gum, gum arab, dan locust bean gum diamati pada penyimpanan selama 8 jam. Produk terbaik diujikan sebagai pengental pada textile printing. Campuran alginat dengan guar gum pada perbandingan 90:10 dan 80:20 meningkatkan viskositas dan stabilitas alginat selama penyimpanan. Campuran alginat dengan gum arab dan locust bean gum akan menurunkan viskositas alginat sehingga tidak sesuai untuk aplikasi textile printing. Aplikasi campuran alginat dengan guar gum 90:10 dan 80:20 sebagai pengental pada tekstil printing menghasilkan produk akhir yang setara dengan pengental komersial manutex. KATA KUNCI: alginat, guar gum, locust bean gum, gum arab, textile printing ABSTRACT Research on applications of the mixture of alginate from Sargassum crassifolium with various gum to increase alginate viscosity as a thickener in textile printing has been carried out. Viscosity of the mixture of alginate with guar gum, locust bean gum and arabic gum was observed during 8 hours storage. -
Optimizing Printing Conditions on Mulberry Silk Wool
International Journal of Applied and Natural Sciences (IJANS) ISSN(P): 2319-4014; ISSN(E): 2319-4022 Vol. 6, Issue 5, Aug – Sep 2017; 131-134 © IASET OPTIMIZING PRINTING CONDITIONS ON MULBERRY SILK/WOOL BLENDED FABRIC WITH VINYL SULPHONE REACTIVE DYES (REACTIVE ORANGE 7 DYE, REACTIVE ORANGE 12 DYE) SUSHILA & SANDEEP BAINS Department of Apparel and Textile Science, College of Home Science, Punjab Agricultural University, Ludhiana, Punjab, India ABSTRACT The present study was conducted to investigate the conceivable outcomes of printing mulberry silk/wool blended fabric with vinyl sulphone reactive dyes. Sodium alginate concentration, steaming time and steaming temperature were optimized for the printing. Samples were assessed for CIE L*a*b* values and K/S value before and after washing and percent fixation was additionally recorded.Printed samples were also assessed for colour fastness to various agencies. KEYWORDS: Blend, Printing, Reactive Orange 7 Dye, Reactive Orange 12 Dye, Silk, Vinyl Suphone Dyes, Wool INTRODUCTION The art of dyeing and printing is more than the application of dyestuffs to the yarn or fabric. Textile printing is the process of applying colour to fabric in definite patterns or design so it is also termed as localized dyeing. It is the art of taking impressions, from characters or figures, on paper, linen, silk, and other fabrics. Textile printing is related to dyeing, in plain dyeing the whole fabric is uniformly covered with one colour, and in printing one or more colours are applied to it in certain parts only, and in sharply defined patterns.The early societies of the India were familiar with resist dyeing and this may well have been the first form of textile printing. -
Obiko Art Wear Archive Project
TEXTILE ARTS COUNCIL FINE ARTS MUSEUMS OF SAN FRANCISCO OBIKO ART WEAR ARCHIVE PROJECT Feather collar by K.Lee Manuel “Electra” 1988. Photo: David Reese The Obiko ArtWear Archive documents and celebrates the work of Bay Area clothing and jewelry designers whose work was showcased at Sandra Sakata’s renowned boutique, Obiko. In the 1970s- through the 1990s, one-of-a-kind Art Wear blossomed in a culture that embraced global design. The influence of Asian and African ethnic costume and textile techniques is particularly evident in the aesthetic of this remarkable era. The archive includes a collection of designers’ work, four fashion shows, oral histories, photos and memories. The Textile Art Council hopes that the archive will be a great discovery and resource for future generations. © 2014 Textile Arts Council Fine Arts Museums of San Francisco, all rights reserved | Design: Nancy Rosenblum, Frisco Graphics OBIKO ART WEAR ARCHIVE PROJECT TABLE OF CONTENTS 1. Acknowledgements 2. History 3. Designers 4. Audio Interviews 5. Videos OBIKO ART WEAR ARCHIVE PROJECT ACKNOWLEDGEMENTS Jean Cacicedo Ana Lisa Hedstrom Thank Yous OBIKO ART WEAR ARCHIVE PROJECT | ACKNOWLEDGE- MENTS JEAN CACICEDO The hand-crafted garments and accessories that emerged in late 1960s and 1970s America played a significant role in our cultural identity. One-of-a-kind wearables emerged on both the east and west coasts, drawing on an anti-fashion street style approach. Two seminal galleries, Julie:Artisans in New York City and Obiko in San Francisco, provided a showcase for this work. I began my career on the east coast in the late 60s during an extraordinary time consumed by nationwide political protests and self expression. -
Pnme Layer Ink Ioyer Thermal Transfer Ribbon U.S
US006961076B2 (12) United States Patent (10) Patent N0.: US 6,961,076 B2 Wagner et al. (45) Date of Patent: NOV. 1,2005 (54) REACTIVE DYE PRINTING PROCESS 5,645,888 A 7/1997 Titterington 6,040,269 A * 3/2000 Imoto et a1. ........... .. 428/195.1 (76) Inventors: Barbara Wagner, 1287 Old Colony 6,103,041 A * 8/2000 Wagner et a1. ............ .. 156/230 Rd., Mt. Pleasant, SC (US) 29464; Ming Xu, 2808 Gaston Gate, Mt- FOREIGN PATENT DOCUMENTS Pleasant, SC (US) 29464 EP 87303687.5 11/1987 Notice: Subject to any disclaimer, the term of this EP 933094252 6/1994 patent is extended or adjusted under 35 EP 941038929 9/1994 U_S~C_ 154(k)) by 120 days' EP 951152412 4/1996 GB 2105735 A 3/1983 WO PCT US99 09387 11 1999 (21) Appl. NO.Z 10/853,331 / / / (22) Filed: May 25, 2004 * cited by examiner (65) Prior Publication Data US 2004/0219296 A1 Nov. 4, 2004 Primary EX?mi”@r—K- Feggins (74) Attorney, Agent, or Firm—B. Craig Killough Related US. Application Data (57) ABSTRACT (63) ggélémrlllgaogg £1155 hgagzoongz' i223’ 2133521522 2 A formulation and method of printing an ink or meltable ink application No. 09/322,737, ?led on May 28, 1999, now Pat. layer having reactive dyes or mixtures of reactive dyes and NO- 673487939 disperse dyes as colorants. The ink or ink melt layer also (51) Int. c1.7 ............................................... .. B41J 2/325 includes an alkaline substance, a binder, and Optionally, a (52) US. Cl. ..................................................... .. 347/213 heat-activated Printing additive Permanently bonded color (58) Field of Search .............................. -
Wool Blended Fabric with Vinyl Sulphone Reactive Dye Printing (Reactive Red 198, Reactive Blue 21 Dye)
International Archive of Applied Sciences and Technology Int. Arch. App. Sci. Technol; Vol 8 [4] December 2017: 66-68 © 2017 Society of Education, India IIAAAASSTT [ISO9001: 2008 Certified Organization] ONLINE ISSN 2277- 1565 www.soeagra.com/iaast.html PRINT ISSN 0976 - 4828 CODEN: IAASCA ORIGINAL ARTICLE DOI: .10.15515/iaast.0976-4828.8.4.6668 Value Addition of Mulberry Silk/ Wool Blended Fabric with Vinyl Sulphone Reactive Dye Printing (Reactive Red 198, Reactive Blue 21 Dye) Sushila1 & Sandeep Bains2 1 Department of Apparel and Textile Science, college of home science, Punjab Agricultural University, Ludhiana, Punjab, India 2Department of Apparel and Textile Science, college of home science, Punjab Agricultural University, Ludhiana Punjab, India Email: [email protected] ABSTRACT The present study was taken up to investigate the conceivable outcomes of printing mulberry silk/wool blended fabric with vinyl sulphone reactive dyes (reactive red 198 and reactive blue 21). Sodium alginate concentration, steaming time and steaming temperature were optimized for the printing. Samples were assessed for CIE Lab values and K/S value before and after washing and percent fixation was additionally recorded. Printed samples were also assessed for colour fastness to various agencies. Key words: Blend, printing, reactive red 198 dye, reactive blue 21 dye, silk, vinyl suphone dyes, wool. Received 29.10.2017 Revised 14.11.2017 Accepted 30.11.2017 Citation of this article Sushila & Sandeep Bains. Value Addition of Mulberry Silk/ Wool Blended Fabric with Vinyl Sulphone Reactive Dye Printing (Reactive Red 198, Reactive Blue 21 Dye). Int. Arch. App. Sci. Technol; Vol 8 [4] December 2017 : 66-68.