Fuel Development for Advanced Reactors Jon Carmack National Technical Director
Total Page:16
File Type:pdf, Size:1020Kb
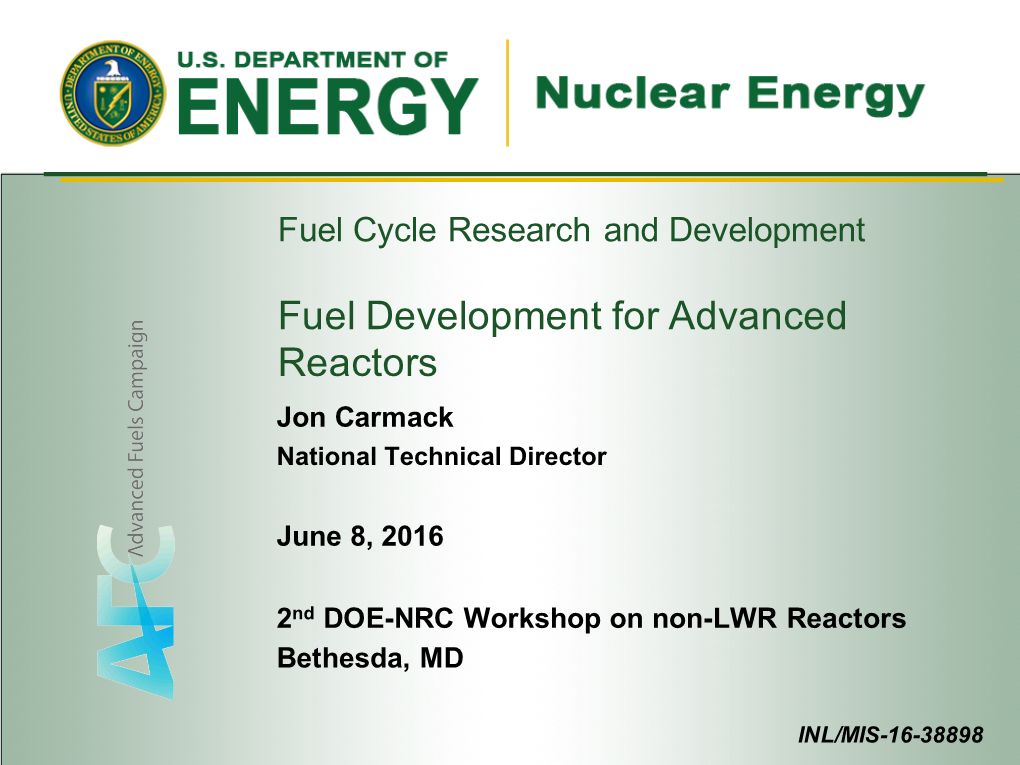
Load more
Recommended publications
-
Corrosion of Refractories by Denis A
A Chapter in the Refractories Handbook, edited by Charles A. Schacht, and to be published by Marcel Dekker, Inc., New York, NY 10016 Corrosion of Refractories by Denis A. Brosnan, PhD, PE Clemson University Clemson, SC 29634-0971 Introduction Refractories are used at elevated temperatures for structural purposes and they are used in many cases to contain a high temperature corrosive environment. This corrosive environment usually contains liquid (melted) phases that participate in chemical reactions with the refractory at the elevated temperatures resulting in refractory consumption or wear. It is usually not immediately obvious, but the oxidation and reduction state of the environment (as “redox” conditions or oxygen “activity”) can participate in and influence the chemical reactions that take place. Along with chemical reactions during corrosion, physical changes occur that may be accelerated by the corrosion process. Corrosion of refractories can be defined for the purposes of this discussion as follows: Corrosion of Refractories – refractory wear by loss of thickness and mass from the exposed face of the refractory as a consequence of chemical attack by a corroding fluid in a process in which the refractory and the corroding fluid react approaching chemical equilibrium in the zone of contact between the refractory and the fluid. It is an essential point that corrosion reactions proceed in a direction toward localized chemical equilibrium. This means that phase equilibrium diagrams can be used to analyze corrosion situations and to predict chemical strategies to minimize corrosion and wear rates. This gives persons interested in refractory corrosion two options. The first is to view corrosion as a chemical and physical process without a detailed application of phase equilibrium diagrams – called the “phenomenological approach”. -
Untraditional Synthesis of Boron-Containing Superhard and Refractory Materials - a Review B
G.J. E.D.T., Vol. 2(1) 2013:21-26 ISSN 2319 – 7293 UNTRADITIONAL SYNTHESIS OF BORON-CONTAINING SUPERHARD AND REFRACTORY MATERIALS - A REVIEW B. Agyei-Tuffour1,2, E. Annan1,2, E. R. Rwenyagila1, E. Ampaw1, E. Arthur1, K. Mustapha1, S. Kolawole1, W. O. Soboyejo1,3, & D. D. Radev1,4 1Department of Materials Science and Engineering, African University of Science and Technology, Abuja-Nigeria 2Department of Materials Science and Engineering, Private Mail Bag, University of Ghana, Legon-Accra. 3Department of Mechanical and Aerospace Engineering, Princeton University, USA. 4Institute of General and Inorganic Chemistry, Bulgaria Academy of Sciences, Sofia-Bulgaria Abstract Boron-containing ceramics find large application in production of superhard and high-temperature materials with application in nuclear and aerospace techniques, military industry etc. The synthesis methods are decisive for the complexity of chemical, morphological and technological properties of these materials. The traditional high-temperature synthesis methods have some disadvantages leading to inconstancy of the product composition due to the boron evaporation, degradation of the furnace materials and contamination of the products, high energy losses etc. Here we show the advantages of some untraditional synthesis methods like direct mechanical synthesis and self propagating high-temperature synthesis (SHS) in the production of titanium diboride (TiB2), zirconium diboride (ZrB2) and production of dense boron carbide (B4C) based materials. Using SEM, TEM, XRD and analytical chemical methods, it was shown that diborides of titanium and zirconium have appropriate properties for production of dense ceramic materials. Using the method of mechanically-assisted sintering high-dense B4C-based ceramic materials was obtained. It was shown that the mechanical properties of materials obtained by pressureless sintering are close or overcome the corresponding properties of boron carbide densified by the method of hot pressing. -
Research Memorandum
RM ESOG21 NACA RESEARCH MEMORANDUM SO:ME PROPER TIES OF BER YLLIUM OXIDE AND BERYLLIUM OXIDE - COLUMBIUM CERAMALS By C. F. Robards and J. J. Gangler " Lewis Flight Propulsion Laboratory Cleveland, Ohio NATIONAL ADVISORY COMMITTEE FOR AERONAUTICS WASHINGTON March 2 , 1951 NACA RM E5OG21 NATIONAL ADVISORY COMMITTEE FOR AERONAUTICS RESEARCH MEMORANDUM SOME PROPERTIES OF BERYLLIUM OXIDE AND BERYLLIUM OXIDE - COLUMBIUM CERAMALS By C. F. Robards and J. J . Gangler SUMMARY Because of the potentially excellent refractory properties of beryllium oxide, a brief investigation was made of its short time tensile strength at a temperature of 18000 F and relative thermal-shock resistance from temperatures of 18000 and 2000° F to room temperature. The effect of additions of 2, 5, 8, 10, 12, and 15 percent by weight of columbium metal on the thermal-shock resistance of beryllium oxide was studied. Metallographic examination indicated that the metallic phase coalesced into pockets. Beryllium oxide had a tensile strength as high as 6160 :9ounds per square inch at 18000 F. The original columbium underwent a phase change, as indicated by X-ray analysis of the ceramals. The addition of columbium up to 15 percent by weight failed to improve the resistance to thermal shock. The phase change and the failure of the columbium to 'vet the beryllium oxide may explain the poor thermal-shock resistance of these ceramals. INTRODUCTION Beryllium oxide BeO has the highest thermal-shock resistance of the better-known oxide bodies. In an effort to extend the life of this material in thermal shock, an attempt was made at the NACA Lewis laboratory to use a metallic binder in the manner that has been successful in the carbide-tool industry. -
High-Temperature Properties of Magnesia-Refractory Brick Treated with Oxide and Salt Solutions
Q [R I 1898o I PLEASEDO NOT REMOVEFROM LIBRARY ()' ~ Bureau of Mines Report of Investigations/1985 ~ ~ High-Temperature Properties of Magnesia-Refractory Brick Treated With Oxide and Salt Solutions By James P. Bennett UNITED STATES DEPARTMENT OF THE INTERIOR Report of Investigations 8980 High-Temperature Properties of Magnesia-Refractory Brick Treated With Oxide and Salt Solutions By James P. Bennett UNITED STATES DEPARTMENT OF THE INTERIOR Donald Paul Hodel, Secretary BUREAU OF MINES Robert C. Horton, Director Research at the Tusca loo sa Research Center is carried out under a memorandum of agreement be tween . the Bureau of Mines, U.S. Department of the Interior, and the University of Alaba ma. Library of Congress Cataloging in Publication Data: Bennett, James P. (James Philip), 1951- High-temperature properties of magnesia-refractory brick treated with oxide and salt solutions. (Report of investigations 8980) Bi bl iography: p. 11. Supt. of Docs. no.: I 28.23: 8980. 1. Magnesia brick-Thermal properties. 2. Oxides. 3. Salt. 1. Title. II. Series: Report of investigations (United States. Bureau of Mines) ; 8980. TN23.C43 (TA418.26] 622s l669',821 85-600138 CONTENTS AbsIntroduction................................................................... tract ••••••••••••••••••••••••••••••••••••••••••••••••••••••••••••••••••••••• 2 Refractory brick and sample preparation........................................ 2 Treatment procedure--solutions and techniques.................................. 4 Results and discussion........................................................ -
Electric Arc Furnace (EAF) Refractory Concept Solutions
STEEL INDUSTRY ELECTRIC ARC FURNACES STEEL INDUSTRY CALDERYS PERFORMANCE YOU CAN TRUST For all industries with extreme temperatures and working conditions, Calderys is there for you. Combining a global network with local expertise, we offer customised solutions wherever you are: from monolithic refractory to bricks and precast shapes to a full range of engineering and installation services. KEY POINTS Over 100 years of refractory experience Over 2 300 employees across 33 countries 19 plants in 16 countries totaling 600 000 tons capacity Annual revenue of over € 500 million 1 Global Technology Centre and 15 Customisation Labs 150 major projects implemented every year Wholly-owned subsidiary of Imerys Group 2 STEEL INDUSTRY OUR VALUE TO THE STEELMAKING INDUSTRY The world leader in monolithic refractory solutions, Calderys has a full product and service portfolio to adapt to the refractory needs of steelmakers. We ensure that we propose products most suitable for your process requirements and deliver to you superior refractory performance and reliable services. We are able to do so by combining our innovative product range and modern installation techniques with end-to-end project management. Value Optimisation Offering tailor-made solutions that meet the commercial and technical requirements for optimal performance. Complete Refractory Solutions We offer a full range of refractory products to meet the process needs of modern Steelmaking. Technology Expertise Ensuring the best possible equipment availability and productivity at the lowest total refractory cost per ton of steel produced, whilst adhering to strict environmental and safety regulations in operations. 3 STEEL INDUSTRY CALDERYS A TRUSTED SUPPLIER IN THE STEEL INDUSTRY A world leader in Refractory Solutions, Calderys has the complete product and service portfolio for all applications. -
Criteria for a Recommended Standard
Background photo on cover by James Lockey, M.D.: Photomicrograph of a rat lung in inhalation studies with airborne fibers. Inset photo on cover, courtesy of Kevin H. Dunn: NIOSH industrial hygienist performing air sampling to evaluate engineering controls in simulated work ac- tivities using RCF materials. Criteria for a Recommended Standard Occupational Exposure to Refractory Ceramic Fibers DEPARTMENT OF HEALTH AND HUMAN SERVICES Centers for Disease Control and Prevention National Institute for Occupational Safety and Health This document is in the public domain and may be freely copied or reprinted. Disclaimer Mention of any company or product does not constitute endorsement by the National Institute for Occupational Safety and Health (NIOSH). In addition, citations to Web sites external to NIOSH do not constitute NIOSH endorsement of the sponsoring organizations or their programs or prod- ucts. Furthermore, NIOSH is not responsible for the content of these Web sites. Ordering Information To receive documents or other information about occupational safety and health topics, contact NIOSH at NIOSH Publications Dissemination 4676 Columbia Parkway Cincinnati, OH 45226–1998 Telephone: 1–800–35–NIOSH (1–800–356–4674) Fax: 1–513–533–8573 E-mail: [email protected] or visit the NIOSH Web site at www.cdc.gov/niosh DHHS (NIOSH) Publication No. 2006–123 May 2006 Safe • Healthier • PeopleTM ii Refractory Ceramic Fibers Foreword When the U.S. Congress passed the Occupational Safety and Health Act of 1970 (Public Law 91– 596), it established the National Institute for Occupational Safety and Health (NIOSH). Through the Act, Congress charged NIOSH with recommending occupational safety and health standards and describing exposure limits that are safe for various periods of employment. -
AISI | Electric Arc Furnace Steelmaking
http://www.steel.org/AM/Template.cfm?Section=Articles3&TEMPLATE=/CM/HTMLDisplay.cfm&CONTENTID=12308 Home Steelworks Home Electric Arc Furnace Steelmaking By Jeremy A. T. Jones, Nupro Corporation SIGN UP to receive AISI's FREE e-news! Read the latest. Email: Name: Join Courtesy of Mannesmann Demag Corp. FURNACE OPERATIONS The electric arc furnace operates as a batch melting process producing batches of molten steel known "heats". The electric arc furnace operating cycle is called the tap-to-tap cycle and is made up of the following operations: Furnace charging Melting Refining De-slagging Tapping Furnace turn-around Modern operations aim for a tap-to-tap time of less than 60 minutes. Some twin shell furnace operations are achieving tap-to-tap times of 35 to 40 minutes. 10/3/2008 9:36 AM http://www.steel.org/AM/Template.cfm?Section=Articles3&TEMPLATE=/CM/HTMLDisplay.cfm&CONTENTID=12308 Furnace Charging The first step in the production of any heat is to select the grade of steel to be made. Usually a schedule is developed prior to each production shift. Thus the melter will know in advance the schedule for his shift. The scrap yard operator will prepare buckets of scrap according to the needs of the melter. Preparation of the charge bucket is an important operation, not only to ensure proper melt-in chemistry but also to ensure good melting conditions. The scrap must be layered in the bucket according to size and density to promote the rapid formation of a liquid pool of steel in the hearth while providing protection for the sidewalls and roof from electric arc radiation. -
Nonmetallic Inclusions in the Secondary Aluminium Industry For
NONMETALLIC INCLUSIONS IN THE SECONDARY ALUMINUM INDUSTRY FOR THE PRODUCTION OF AEROSPACE ALLOYS Bernd Prillhofer1, Helmut Antrekowitsch1,2, Holm Böttcher3, Phil Enright4 1Christian Doppler Laboratory for secondary metallurgy of non-ferrous metals, Franz-Josef-Str. 18, Leoben, 8700, Austria 2Chair for non-ferrous metals, University of Leoben, Franz-Josef-Str. 18, Leoben, 8700, Austria 3AMAG rolling GmbH, post office box 32, Ranshofen, 5282, Austria 4N-Tec Limited, Watery Lane, Hook Norton, Oxfordshire, OX155NW, England Keywords: melt quality, Prefil®, process evaluation, operating windows Abstract All the investigations have been performed in co-operation with Austria Metall AG (AMAG), Austria and in part with N-Tec, Due to enormous growth of the secondary aluminum industry and England. the required increase in melt quality, the development of methods for inclusion removal has become highly important. To produce Process layout high quality aerospace alloys with very low inclusion contents, casthouses must analyze and optimize their production processes The casting facility at AMAG for the production of 7xxx series from the beginning to the end. Nowadays, there are several ingots consists of a single melting furnace, two casting furnaces, a methods available for process evaluation and the determination of SNIF P140, a ceramic foam filter unit and an electro magnetic inclusion level from one step to another. Furthermore, the most casting pit for 4 ingots (see Figure 1). important parameters for control of the final inclusion level have CFF Box to be investigated. Grain Refiner Addition • two horizontal 17‘‘ filter • amount of grain refiner This paper characterizes the change of the inclusion content for according to Opticast the alloy AA 7075 during standard casthouse processing. -
Mechanical and Physical Properties of Silica Bricks Production From
Australian Journal of Basic and Applied Sciences, 3(2): 418-423, 2009 ISSN 1991-8178 Mechanical and Physical Properties of Silica Bricks Produced from Local Materials Mohammed A. Alnawafleh Tafila Technical University Abstract: The samples were prepared by the semi-dry method, moulding pressure was 50N/mm2. After drying at 110EC, the samples were burnt at 1450EC. The fired samples were investigated to determine their physical properties, such as specific gravity, porosity, compressive strength, thermal shock resistance and refractoriness under load (RUL). Results obtained indicated that the compressive strength increases with increasing temperature at 1450EC. A maximum expansion at temperature below 600EC was observed. The test for the shock resistance showed that 9 heat cycles were required at 900EC before destruction. Key words: INTRODUCTION Refractories are ceramics materials of pyrometric cone indicator greater than cone 26(1580EC). Refractory materials are used in the linings of furnaces, kilns, ovens, melting pots ect. to confine the heat to the ware. While chamotte bricks are largely used in the lining of melting pots and the sintering zones of cement kilns, silica bricks find widespread use in kiln roofs where resistance against vapors and gases. Until this time Jordan and other neghbouring countries have not sofar taken up the production of refractory-bricks. Silicon dioxide, which is one of the most abundant materials, occurs in nature primarily as quartz. In combination with basic oxides it froms a large group of minerals known as silcates. Silica is also known in other forms such as chert, flint, chalsadony and opal, which are hydrated from of silica (Chester, 1973). -
The Effect of Changes in Heart Rate on the Refractory Period of the Heart
UvA-DARE (Digital Academic Repository) The effect of changes in heart rate on the refractory period of the heart Janse, M.J. Publication date 1971 Document Version Final published version Link to publication Citation for published version (APA): Janse, M. J. (1971). The effect of changes in heart rate on the refractory period of the heart. Mondeel. General rights It is not permitted to download or to forward/distribute the text or part of it without the consent of the author(s) and/or copyright holder(s), other than for strictly personal, individual use, unless the work is under an open content license (like Creative Commons). Disclaimer/Complaints regulations If you believe that digital publication of certain material infringes any of your rights or (privacy) interests, please let the Library know, stating your reasons. In case of a legitimate complaint, the Library will make the material inaccessible and/or remove it from the website. Please Ask the Library: https://uba.uva.nl/en/contact, or a letter to: Library of the University of Amsterdam, Secretariat, Singel 425, 1012 WP Amsterdam, The Netherlands. You will be contacted as soon as possible. UvA-DARE is a service provided by the library of the University of Amsterdam (https://dare.uva.nl) Download date:26 Sep 2021 THE EFFECT OF CHANGES IN HEART RATE ON THE REFRACTORY PERIOD OF THE HEART THE EFFECT OF C1IANGES IN HEART RATE ON THE REFRACTORY PERIOD OF THE HEART ACADEMISCH PROEFSCHRIFT TER VERKRIJGING VAN DE GRAAD VAN DOCTOR IN DE GENEESKUNDE AAN DE UNIVERSITEIT V AN AMSTERDAM, OP GEZAG VAN DE RECTOR MAGNIFICUS, Mr. -
Boron Nitride Solid Components for Refractory, Insulation, Kiln Furniture and Molten Metal
Boron Nitride solid components for refractory, insulation, kiln furniture and molten metal Available in variety of grades, Combat® Boron Nitride Solids are a wise choice for applications where electrical isolation, thermal shock resistance, corrosion resistance, refractoriness, inertness or high thermal conductivity is important. These features enable a variety of applications in high-temperature manufacturing space. Some of the examples are - • High temperature electrical insulators and vacuum furnace supports which require electrical resistivity, high temperature strength, thermal shock resistance and low chemical reactivity • Crucibles and containers for high purity molten metals • Insulators and source fixtures for ion implantation systems which require high temperature purity and electrical insulation • Radar components and antenna windows which require exacting electrical and thermal properties • Setterplates for the processing of other advanced materials which require stable, inert surfaces • Nozzles for powdered metal spraying Boron Nitride aqueous coatings for high temperature mold release and protection Combat® Boron Nitride Coatings are entirely inorganic, composed of boron nitride powder and a high temperature bond phase. Supplied in a liquid form, these coatings can be applied by brushing, spraying or dipping to a variety of porous and non-porous materials including graphite, metals, ceramics and organics. Boron Nitride coatings offer excellent lubrication, mold release and surface protection in light metal processing, secondary -
Background Document for Aluminosilicate Refractory Ceramic
1(7) 6 February 2014 Backgr ou nd document for Aluminosilicate Refractory Ceramic Fibres (Al-RCF) Document developed in the context of ECHA’s fifth Recommendation for the inclusion of substances in Annex XIV Information comprising confidential comments submitted during public consultation or relating to content of Registration dossiers, which is of such nature that it may potentially harm the commercial interest of companies if it was disclosed, is provided in a confidential annex to this document. 1. Identity of the substance Aluminosilicate Refractory Ceramic Fibres are fibres covered by index number 650-017-00-8 in Annex VI, part 3, table 3.1 of Regulation (EC) No 1272/2008 of the European Parliament and of the Council of 16 December 2008 on classification, labelling and packaging of substances and mixtures, and fulfil the three following conditions: a) oxides of aluminium and silicon are the main components present (in the fibres) within variable concentration ranges b) fibres have a length weighted geometric mean diameter less two standard geometric errors of 6 or less micrometres (µm) c) alkaline oxide and alkali earth oxide (Na2O+K2O+CaO+MgO+BaO) content less or equal to 18% by weight Chemical name: Aluminosilicate Refractory Ceramic Fibres EC Number: - CAS Number: - IUPAC Name: - 2. Background information 2.1. Intrinsic properties Aluminosilicate Refractory Ceramic Fibres (Al-RCF) were identified as a Substance of Very High Concern (SVHC) in accordance with Article 57 (a) as they are classified in Annex VI, part 3, Table 3.1 (the list of harmonised classification and labelling of hazardous substances) of Regulation (EC) No 1272/2008 as carcinogen, Carc.