Introduction to Magnesium Alloys
Total Page:16
File Type:pdf, Size:1020Kb
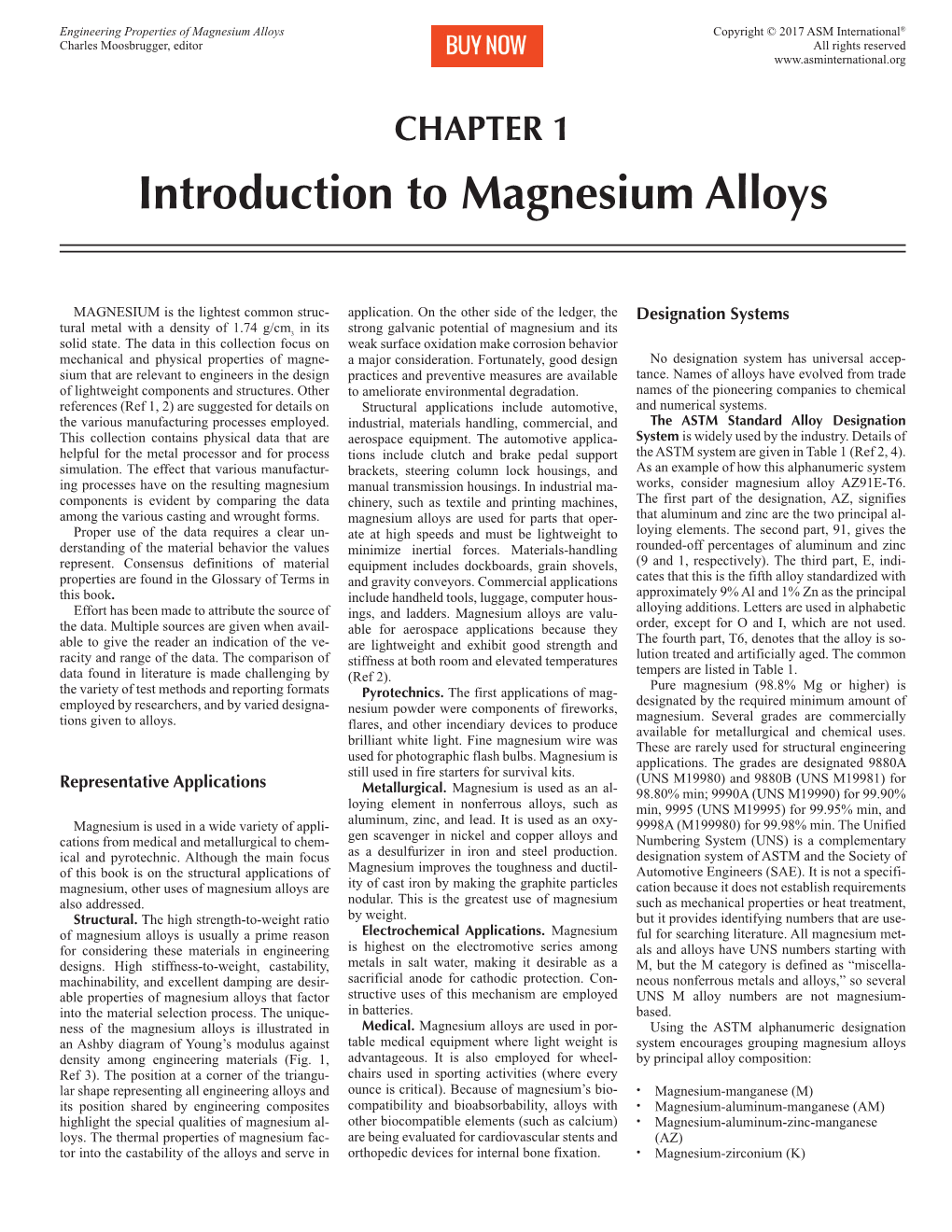
Load more
Recommended publications
-
Investigating the Durability of Structures by Dana Saba Bachelor of Engineering, Mcgill University, Montréal, 2011
Investigating the Durability of Structures by Dana Saba Bachelor of Engineering, McGill University, Montréal, 2011 Submitted to the Department of Civil and Environmental Engineering in Partial Fulfillment of the Requirements for the Degree of Master of Engineering in Civil and Environmental Engineering at the Massachusetts Institute of Technology June 2013 © 2013 Massachusetts Institute of Technology. All rights reserved. Signature of Author: Department of Civil and Environmental Engineering May 10th, 2013 Certified by: Jerome J. Connor Professor of Civil and Environmental Engineering Thesis Supervisor Certified by: Rory Clune Massachusetts Institute of Technology Thesis Reader Accepted by: Heidi Nepf Chair, Departmental Committee for Graduate Students 2 Investigating the Durability of Structures by Dana Saba Submitted to the Department of Civil and Environmental Engineering in May 10, 2013, in Partial Fulfillment of the Requirements for the Degree of Master of Engineering in Civil and Environmental Engineering Abstract The durability of structures is one of primary concerns in the engineering industry. Poor durability in design may result in a structure losing its performance to the extent where structural integrity is no longer satisfied and human lives are at stake. Moreover, the associated costs of maintenance and repair due to inadequate design considerations are high. Thus, designing for durable structures not only helps sustain our infrastructure, it also reduces future costs. This thesis identifies the key factors that define and impact durability, with particular attention paid to the effect of material choice on overall durability. This follows a study of the different deteriorating mechanisms that wood, steel and reinforced concrete undergo over time, and the different enhancement techniques used to reduce the adverse effects of these mechanisms. -
Material Quantities in Building Structures and Their Environmental Impact
Material quantities in building structures and their environmental impact by Catherine De Wolf B.Sc., M.Sc. in Civil Architectural Engineering Vrije Universiteit Brussel and Université Libre de Bruxelles, 2012 Submitted to the Department of Architecture in Partial Fulfillment of the Requirements for the Degree of Master of Science in Building Technology at the Massachusetts Institute of Technology June 2014 © 2014 Massachusetts Institute of Technology. All rights reserved. Signature of Author: Department of Architecture May 9, 2014 Certified by: John A. Ochsendorf Professor of Architecture and Civil and Environmental Engineering Thesis Supervisor Accepted by: Takehiko Nagakura Associate Professor of Design and Computation Chair of the Department Committee on Graduate Students John E. Fernández Professor of Architecture, Building Technology, and Engineering Systems Head, Building Technology Program Co-director, International Design Center, MIT Thesis Reader Frances Yang Structures and Sustainability Specialist at Arup Thesis Reader “It is […] important to remember that unlike operational carbon emissions the embodied carbon cannot be reversed” Craig Jones, Circular Ecology Material quantities in building structures and their environmental impact by Catherine De Wolf Submitted to the Department of Architecture in Partial Fulfillment of the Requirements for the Degree of Master of Science in Building Technology on May 9, 2014. Thesis Supervisor: John Ochsendorf Title Supervisor: Professor of Architecture and Civil and Environmental Engineering -
Applications of Aluminium Alloys in Civil Engineering
T. Dokšanović i dr. Primjene aluminijskih legura u građevinarstvu ISSN 1330-3651 (Print), ISSN 1848-6339 (Online) https://doi.org/10.17559/TV-20151213105944 APPLICATIONS OF ALUMINIUM ALLOYS IN CIVIL ENGINEERING Tihomir Dokšanović, Ivica Džeba, Damir Markulak Subject review Although aluminium is a long known structural material, its use is not in accordance with the benefits achieved by its implementation. There are several reasons for such an adverse state. Those that stand out are the late development of a regulative framework for the design of structures, and still the need for improvement, lack of knowledge on application examples and not stressed enough potential areas of use. However, positive trends are present and aluminium alloys are competitive, especially if their positive properties can be utilized and negative properties diminished through purpose oriented design approach. Given examples present good application utilization of aluminium alloys characteristics, and shown new application research can provide directions for further expansion of competitiveness. Structural uses are grouped in suitable areas of application and put into local and global context. Keywords: bridge; façade; refurbishment; roof system; seismic Primjene aluminijskih legura u građevinarstvu Pregledni članak Iako je aluminij već dugo prisutan konstrukcijski materijal, uporaba mu nije u skladu s dobrobitima koji se ostvaruju njegovom primjenom. Nekoliko je uzročnika takvog stanja. Ističu se relativno kasni razvoj normativnog okvira za dimenzioniranje konstrukcija, i još uvijek potreba za poboljšanjem, nedovoljna raširenost saznanja o primjenama te nedostatno naglašena potencijalna područja primjene. Međutim, pozitivni trendovi su prisutni, a legure aluminija su konkurentne, posebno ako se njegova pozitivna svojstva mogu iskoristiti, a negativna umanjiti kroz proračunski pristup orijentiran prema namjeni. -
Designing for Durability CONTINUING EDUCATION Strategies for Achieving Maximum Durability with Wood-Frame Construction Sponsored by Rethink Wood
EDUCATIONAL-ADVERTISEMENT Designing for Durability EDUCATION CONTINUING Strategies for achieving maximum durability with wood-frame construction Sponsored by reThink Wood rchitects specify wood for many Examples of wood buildings that have (glulam), cross laminated timber (CLT), and reasons, including cost, ease and stood for centuries exist all over the world, nail-laminated timber, along with a variety A efficiency of construction, design including the Horyu-ji temple in Ikaruga, of structural composite lumber products, are versatility, and sustainability—as well as Japan, built in the eighth century, stave enabling increased dimensional stability and its beauty and the innate appeal of nature churches in Norway, including one in Urnes strength, and greater long-span capabilities. and natural materials. Innovative new built in 1150, and many more. Today, wood These innovations are leading to taller, technologies and building systems are also is being used in a wider range of buildings highly innovative wood buildings. Examples leading to the increased use of wood as a than would have been possible even 20 years include (among others) a 10-story CLT structural material, not only in houses, ago. Next-generation lumber and mass timber apartment building in Australia, a 14-story schools, and other traditional applications, products, such as glue-laminated timber timber-frame apartment in Norway, but in larger, taller, and more visionary wood buildings. But even as the use of wood is expanding, one significant characteristic of wood buildings is often underestimated: their durability. Misperceptions still exist that buildings made of materials such as concrete or steel last longer than buildings made of wood. -
Structural Composite Materials Tailored for Damping
L Journal of Alloys and Compounds 355 (2003) 216–223 www.elsevier.com/locate/jallcom S tructural composite materials tailored for damping D.D.L. Chung* Composite Materials Research Laboratory, University at Buffalo, State University of New York, Buffalo, NY 14260-4400, USA Abstract This paper reviews the tailoring of structural composite materials for damping. By the use of the interfaces and viscoelasticity provided by appropriate components in a composite material, the damping capacity can be increased with negligible decrease, if any, of the stiffness. In the case of cement–matrix composites, the use of silica fume as an admixture results in increases in both the damping capacity and the storage modulus. In the case of continuous fiber polymer–matrix lightweight composites, the use of submicron-diameter discontinuous carbon filaments as an interlaminar additive is more effective than the use of an interlaminar viscoelastic layer in enhancing the loss modulus when the temperature exceeds 50 8C. Surface treatment of the composite components is important. In the case of steel reinforced concrete, the steel reinforcing bar (rebar) contributes much to the damping, but appropriate surface treatment of the rebar further enhances the damping. 2003 Elsevier Science B.V. All rights reserved. Keywords: Disordered systems; Polymers; Elastomers and plastics; Surfaces and interfaces; Elasticity; Anharmonicity 1 . Introduction [2–4] is the goal of the structural material tailoring described in this review paper. The development of materials for vibration and acoustic Vibrations are undesirable for structures, due to the need damping has been focused on metals and polymers [1]. for structural stability, position control, durability (par- Most of these materials are functional materials rather than ticularly durability against fatigue), performance, and noise practical structural materials due to their high cost, low reduction. -
Structural Materials
OPTI 222 Mechanical Design in Optical Engineering Structural Materials Beryllium Among the light metals, beryllium is characterized by its out-standing combination of properties--low density (0.067 lb/in3), high strength (60 psi), good thermal properties, low cross-section, to thermal neutrons and high melting point (2300 °F). The use of beryllium has nevertheless been restricted by its poor ductility and low resistance to impact, as well as by factors of its toxicity and high cost. Some of the properties of beryllium are summarized as follows: 1. Density: Beryllium "has a relatively low density of 0.067 lbs/in3. This is slightly higher than the density of magnesium and about two-thirds that of aluminum. 2. Modulus of Elasticity: The modulus of elasticity of Beryllium high, being 3.1 x 104 kg/mm2 (44 x 106 psi). This combined with its low density, makes it attractive as a light, but stiff, material. 3. Tensile Properties: The mechanical properties of beryllium are affected by the method of production. Hot-pressed beryllium has a room temperature ultimate tensile strength of around 60 Ksi with a ductility of 0.5 - 0.3%. Beryllium retains its strength at high temperatures; even at 600 °C, it has an ultimate tensile strength of about 25 Ksi. Above 250 °C, its ductility rises to a level in excess of 10%. The fatigue strength of beryllium is high, being in excess of 80% of the ultimate tensile strength. Its room temperature impact strength, however, is negligible and in this respect it performs more like a ceramic than a metal. -
Improving the Performance of Magnesium Alloys for Automotive Applications
High Performance and Optimum Design of Structures and Materials 531 Improving the performance of magnesium alloys for automotive applications R. O. Hussein & D. O. Northwood Department of Mechanical, Automotive and Materials Engineering, University of Windsor, Canada Abstract Magnesium and its alloys are attractive to the automotive industry for their inherent light-weight which leads to highly fuel-efficient design. However, due to a low melting temperature (650°C), magnesium has relatively poor elevated temperature mechanical properties, e.g., creep. This has, therefore, restricted its use in applications such as engine components. Magnesium is also a highly reactive metal and has inherently poor corrosion and wear resistance. Improved corrosion and wear performance can be obtained through alloying and microstructural engineering. However, for enhanced corrosion and tribological properties, the use of surface engineering techniques involving coatings is mandatory. Plasma Electrolytic Oxidation (PEO), also known as “Micro-Arc Oxidation (MAO)”, has been used to successfully produce oxide layers on magnesium alloys with excellent tribological and corrosion resistant properties. By controlling the PEO process parameters, uniform, relatively pore-free and well adhered coatings can be produced which can provide adequate corrosion protection. The coating requirements for good tribological properties are somewhat different than for good corrosion performance. However, good tribological performance combined with good corrosion performance can -
Machining Magnesium – Datasheet
DATASHEET DATASHEET • Machining Magnesium 254 † Magnesium is the lightest structural metal and Table 1. Relative power and comparative machinability of metals. exhibits excellent machinability. Some of the AISI - B1112 Relative advantages of machining magnesium compared to Metal machinability power other commonly used metals include: index (%) Magnesium alloys 1.0 500 • Low power required – approximately 55% of that Aluminium alloys 1.8 300 required for Al Mild steel 6.3 50 • Fast machining – employing the use of high cutting speeds, large feed rates and greater depths of cut Titanium alloys 7.6 20 • Excellent surface finish – extremely fine and smooth surface achieved Speeds, feeds and depths of cut • Well broken chips – due to the free-cutting qualities of magnesium The potential for high speed machining of • Reduced tool wear – leading to increased tool life magnesium alloys is usually only limited by the stability of the component in the clamping device, To fully exploit and enjoy the advantages of chip extraction or the rotation speed or accuracy machining magnesium, it is important that the unique limits of the tool or machine. Some relative cutting characteristics of the metal are understood. speeds using HSS tools are given in Table 2. Cutting speeds are also dependant on the tool material. Cutting power and machinabilty Higher speeds can be enjoyed with the use of carbide or poly-crystalline diamond (PCD) tooling. The mean specific cutting force (ks1.1) of magnesium is 280 N/mm2, this is much lower than that of In general, cutting speeds are between aluminium (approx 640 N/mm2). The result of this 200 – 1800 m/min with feed rates greater than means that there is a reduced load on the cutter and 0.25 mm/rev for turning and boring operations. -
Microstructure and Mechanical Properties of Elektron 21 Alloy After Heat Treatment
VOLUME 20 ISSUES 1-2 of Achievements in Materials January-February and Manufacturing Engineering 2007 Microstructure and mechanical properties of Elektron 21 alloy after heat treatment A. Kiełbus* Division of Materials Science and Metallurgy, Silesian University of Technology, ul. Krasińskiego 8, 40-019, Katowice, Poland * Corresponding author: E-mail address: [email protected] Received 27.10.2006; accepted in revised form 15.11.2006 Materials AbstrAct Purpose: Elektron 21 is new magnesium based casting alloy contains neodymium, gadolinium and zinc for used to at 200°C. It is a Mg-RE-Zn-Zr alloy designed for aerospace and specialty application ns. This alloy has high strength, good corrosion resistance and excellent castability. The aim of the research was to determine the effect of heat treatment parameters on the microstructure and mechanical properties of Elektron 21 magnesium alloy Design/methodology/approach: Solution treatment was performed at 520°C/8h with water cooling. Ageing treatments were performed at 200°C/4÷96h and then quenched in air. The microstructure was characterized by JEM 2010 ARP microscope The examination of the mechanical properties was conducted on an MTS-810 servo hydraulic machine at two temperatures: ambient (ca. 20°C) and 200°C. Hardness measurements by Vickers method were performed on a ZWICK/ZHV50 hardness tester. Findings: The microstructure of the cast alloy consists of α-Mg phase matrix with precipitates of intermetallic phase Mg12(Ndx,Gd1-x) at grain boundaries. After solution treatment the Mg12(Ndx,Gd1-x) phase dissolves in the matrix. The aging treatment applied after solution treatment with air-cooling caused precipitation of a β”, β’ and β intermetallic phases. -
Elektron® WE54
DATASHEET DATASHEET • 466 Elektron® WE54 † Elektron WE54 is a high strength fully heat Heat treatment treatable magnesium based casting alloy for use The alloy develops its properties in the fully heat at temperatures up to 300˚C. The alloy develops treated (T6) condition ie: 8 hours at 525˚C, high strength properties at elevated temperatures, Hot water or polymer quench or air cool, without containing either silver or thorium. Age for 16 hours at 250˚C, Air cool. Applications Physical properties The excellent retention of properties at elevated Specific gravity 1.85 temperatures and improved corrosion resistance Coefficient of thermal expansion 27.0 x 10-6K-1 will be of interest to designers of power systems, Thermal conductivity 52 Wm-1K-1 transmissions, missiles, high performance cars and Specific heat 960 Jkg-1K-1 other high technology applications. Electrical resistivity 173 nΩm Modulus of elasticity 44.1 GPa Prolonged use of this alloy (ie in excess of 1000 Poissons ratio 0.3 hours) at temperatures in the range 100˚C–250˚C Melting range 545–640˚C may result in the loss of ductility. An alternative alloy Damping index 0.17 is Elektron WE43. Brinell hardness 85 Specifications Design data AECMA MG-C96001 Minimum specification tensile properties AMS 4426 ISO 16220 ASTM B80 WE54A-T6 0.2% Proof stress 170 MPa BS2970 MAG14-TF Tensile strength 250 MPa UNS M18410 Elongation 2% ISO 16220: MC95310 Chemical composition Yttrium 4.75–5.5% Heavy rare earths* 1.0–2.0% Neodymium 1.5–2.0% Zirconium 0.4% min Magnesium Balance *Heavy rare earth fraction contains mainly Yb, Er, Dy, and Gd. -
ACHIEVING ULTRAFINE GRAINS in Mg AZ31B-O ALLOY by CRYOGENIC FRICTION STIR PROCESSING and MACHINING
University of Kentucky UKnowledge Theses and Dissertations--Manufacturing Systems Engineering Manufacturing Systems Engineering 2011 ACHIEVING ULTRAFINE GRAINS IN Mg AZ31B-O ALLOY BY CRYOGENIC FRICTION STIR PROCESSING AND MACHINING Anwaruddin Mohammed University of Kentucky, [email protected] Right click to open a feedback form in a new tab to let us know how this document benefits ou.y Recommended Citation Mohammed, Anwaruddin, "ACHIEVING ULTRAFINE GRAINS IN Mg AZ31B-O ALLOY BY CRYOGENIC FRICTION STIR PROCESSING AND MACHINING" (2011). Theses and Dissertations--Manufacturing Systems Engineering. 1. https://uknowledge.uky.edu/ms_etds/1 This Master's Thesis is brought to you for free and open access by the Manufacturing Systems Engineering at UKnowledge. It has been accepted for inclusion in Theses and Dissertations--Manufacturing Systems Engineering by an authorized administrator of UKnowledge. For more information, please contact [email protected]. STUDENT AGREEMENT: I represent that my thesis or dissertation and abstract are my original work. Proper attribution has been given to all outside sources. I understand that I am solely responsible for obtaining any needed copyright permissions. I have obtained and attached hereto needed written permission statements(s) from the owner(s) of each third-party copyrighted matter to be included in my work, allowing electronic distribution (if such use is not permitted by the fair use doctrine). I hereby grant to The University of Kentucky and its agents the non-exclusive license to archive and make accessible my work in whole or in part in all forms of media, now or hereafter known. I agree that the document mentioned above may be made available immediately for worldwide access unless a preapproved embargo applies. -
Material Quantities in Building Structures and Their Environmental Impact
Material quantities in building structures and their environmental impact by Catherine De Wolf B.Sc., M.Sc. in Civil Architectural Engineering Vrije Universiteit Brussel and Université Libre de Bruxelles, 2012 Submitted to the Department of Architecture in Partial Fulfillment of the Requirements for the Degree of Master of Science in Building Technology at the Massachusetts Institute of Technology June 2014 © 2014 Massachusetts Institute of Technology. All rights reserved. Signature of Author: Department of Architecture May 9, 2014 Certified by: John A. Ochsendorf Professor of Architecture and Civil and Environmental Engineering Thesis Supervisor Accepted by: Takehiko Nagakura Associate Professor of Design and Computation Chair of the Department Committee on Graduate Students 2 John E. Fernández Professor of Architecture, Building Technology, and Engineering Systems Head, Building Technology Program Co-director, International Design Center, MIT Thesis Reader Frances Yang Structures and Sustainability Specialist at Arup Thesis Reader 3 “It is […] important to remember that unlike operational carbon emissions the embodied carbon cannot be reversed” Craig Jones, Circular Ecology 4 Material quantities in building structures and their environmental impact by Catherine De Wolf Submitted to the Department of Architecture in Partial Fulfillment of the Requirements for the Degree of Master of Science in Building Technology on May 9, 2014. Thesis Supervisor: John Ochsendorf Title Supervisor: Professor of Architecture and Civil and Environmental Engineering Abstract Improved operational energy efficiency has increased the percentage of embodied energy in the total life cycle of building structures. Despite a growing interest in this field, practitioners lack a comprehensive survey of material quantities and embodied carbon in building structures.