Preliminary Design Guidelines for Poraver-Based Lightweight Concrete
Total Page:16
File Type:pdf, Size:1020Kb
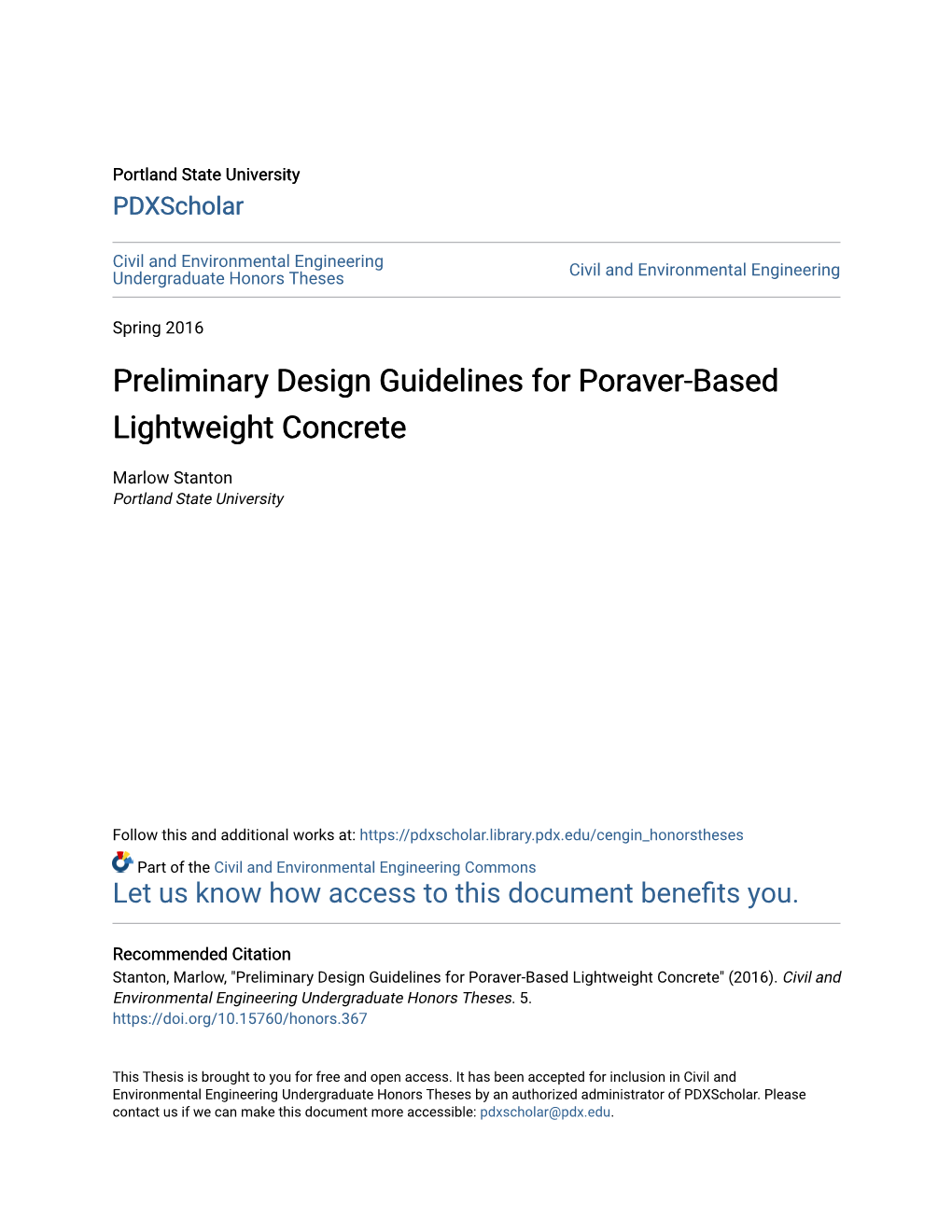
Load more
Recommended publications
-
Guide to Concrete Repair Second Edition
ON r in the West August 2015 Guide to Concrete Repair Second Edition Prepared by: Kurt F. von Fay, Civil Engineer Concrete, Geotechnical, and Structural Laboratory U.S. Department of the Interior Bureau of Reclamation Technical Service Center August 2015 Mission Statements The U.S. Department of the Interior protects America’s natural resources and heritage, honors our cultures and tribal communities, and supplies the energy to power our future. The mission of the Bureau of Reclamation is to manage, develop, and protect water and related resources in an environmentally and economically sound manner in the interest of the American public. Acknowledgments Acknowledgment is due the original author of this guide, W. Glenn Smoak, for all his efforts to prepare the first edition. For this edition, many people were involved in conducting research and field work, which provided valuable information for this update, and their contributions and hard work are greatly appreciated. They include Kurt D. Mitchell, Richard Pepin, Gregg Day, Jim Bowen, Dr. Alexander Vaysburd, Dr. Benoit Bissonnette, Maxim Morency, Brandon Poos, Westin Joy, David (Warren) Starbuck, Dr. Matthew Klein, and John (Bret) Robertson. Dr. William F. Kepler obtained much of the funding to prepare this updated guide. Nancy Arthur worked extensively on reviewing and editing the guide specifications sections and was a great help making sure they said what I meant to say. Teri Manross deserves recognition for the numerous hours she put into reviewing, editing and formatting this Guide. The assistance of these and numerous others is gratefully acknowledged. Contents PART I: RECLAMATION'S METHODOLOGY FOR CONCRETE MAINTENANCE AND REPAIR Page A. -
207.1R-96 Mass Concrete
ACI 207.1R-96 Mass Concrete Reported by ACI Committee 207 Gary R. Mass Woodrow L. Burgess* Chairman Chairman, Task Group Edward A. Abdun-Nur* Robert W. Cannon David Groner Walter H. Price*† Ernest K. Schrader* Fred A. Anderson* Roy W. Carlson Kenneth D. Hansen Milos Polivka Roger L. Sprouse Richard A. Bradshaw, Jr.* James L. Cope* Gordon M. Kidd Jerome M. Raphael* John H. Stout Edward G. W. Bush James R. Graham* W. Douglas McEwen Patricia J. Roberts Carl R. Wilder James E. Oliverson* *Members of the task group who prepared this report. †Deceased Members of Committee 207 who voted on the 1996 revisions: John M. Scanlon John R. Hess Chairman Chairman, Task Group Dan A. Bonikowsky James L. Cope Michael I. Hammons Meng K. Lee Ernest K. Schrader Robert W. Cannon Luis H. Diaz Kenneth D. Hansen Gary R. Mass Glenn S. Tarbox Ahmed F. Chraibi Timothy P. Dolen James K. Hinds Robert F. Oury Stephen B. Tatro Allen J. Hulshizer Synopsis cause excessive seepage and shortening of the service life of the structure, or may be esthetically objectionable. Many of the principles in mass con- crete practice can also be applied to general concrete work whereby certain Mass concrete is “any volume of concrete with dimensions large enough to economic and other benefits may be realized. require that measures be taken to cope with generation of heat from hydra- tion of the cement and attendant volume change to minimize cracking.” The design of mass concrete structures is generally based on durability, This report contains a history of the development of mass concrete practice economy, and thermal action, with strength often being a secondary con- and discussion of materials and concrete mix proportioning, properties, cern. -
Thermal Cracking of Concrete
CIP 42- Thermal Cracking of Concrete WHAT is Thermal Cracking? Thermal cracking occurs due to excessive temperature dif- ferences within a concrete structure or its surroundings. The temperature difference causes the cooler portion to con- tract more than the warmer portion, which restrains the con- traction. Thermal cracks appear when the restraint results in tensile stresses that exceed the in-place concrete tensile strength. Cracking due to temperature can occur in concrete members that are not considered mass concrete. WHY Does Thermal Cracking Occur? Hydration of cementitious materials generates heat for sev- eral days after placement in all concrete members. This heat Thermal cracks in a thick slab dissipates quickly in thin sections and causes no problems. Courtesy CTLGroup In thicker sections, the internal temperature rises and drops slowly, while the surface cools rapidly to ambient tempera- temperature changes. Another factor is a temperature differ- ture. Surface contraction due to cooling is restrained by the ential between a mass concrete member and adjoining ele- hotter interior concrete that doesn’t contract as rapidly as ments. As the mass member cools from its peak temperature, the surface. This restraint creates tensile stresses that can the contraction is restrained by the element it is attached to, crack the surface concrete as a result of this uncontrolled resulting in cracking. Examples are thick walls or dams re- temperature difference across the cross section. In most strained by the foundation. cases thermal cracking occurs at early ages. In rarer instances Other Structures thermal cracking can occur when concrete surfaces are ex- Temperature cracking can occur in structures that are not posed to extreme temperature rapidly. -
Research on Crack Control of Mass Concrete Structure
Insight - Civil Engineering(2018.1) Original Research Article Research on Crack Control of Mass Concrete Structure Honglong Su,Dongtang Duan,Zhibin Lu School of Environment and Municipal Engineering, Tianjin Jiaotong University, Tianjin, China ABSTRACT With the development of economy in our country, the scale of construction has become more and more complicated. This cause the problem of mass concrete cracks in industrial and civil buildings increasingly prominent and become a fairly common problem. The problem of mass cracks in mass concrete is very complex and involves all aspects related to the engineering structure. The control of temperature cracks in mass concrete foundation is related to geotechnical, structural, building materials, construction, environment and other multi-disciplinary. The hydrothermal heat released by the mass concrete in the hardening process which produces a large temperature change, and the resulting of temperature stress is the main factor leading to the occurrence of cracks in the concrete, thus aff ecting the integrity of the structure, water resistance and durability, and become structural hidden dangers. Therefore, the mass concrete in the construction must consider the crack control. The reason and control measures of the temperature cracks of mass concrete are analyzed and summarized. According to the specifi c situation, these measures are applied to the concrete large-scale basic engineering construction, and the material selection, mixing ratio, admixture, construction arrangement and pouring process, conservation and other aspects to take a strict control measures. At the same time the basic position of the internal and external temperature diff erence was monitored. The temperature control measures and monitoring results taken for the basic engineering provide a reference for the construction of similar projects and provide the basis for further theoretical research KEYWORDS: mass concrete; crack control; hydration heat; temperature stress 1. -
Cooling and Insulating Systems for Mass Concrete --`````,,,,``,,,`,,```,`,,,,,`-`-`,,`,,`,`,,`
daneshlink.com ACI 207.4R-05 (Reapproved 2012) Cooling and Insulating Systems for Mass Concrete --`````,,,,``,,,`,,```,`,,,,,`-`-`,,`,,`,`,,`--- Reported by ACI Committee 207 Copyright American Concrete Institute Provided by IHS under license with ACI Licensee=University of Texas Revised Sub Account/5620001114, User=wer, srdtgert No reproduction or networking permitted without license from IHS Not for Resale, 01/26/2015 01:17:36 MST Daneshlink.com daneshlink.com First printing October 2005 Cooling and Insulating Systems for Mass Concrete Copyright by the American Concrete Institute, Farmington Hills, MI. All rights reserved. This material may not be reproduced or copied, in whole or part, in any printed, mechanical, electronic, film, or other distribution and storage media, without the written consent of ACI. The technical committees responsible for ACI committee reports and standards strive to avoid ambiguities, omissions, and errors in these documents. In spite of these efforts, the users of ACI documents occa- sionally find information or requirements that may be subject to more than one interpretation or may be incomplete or incorrect. Users who have suggestions for the improvement of ACI documents are requested to contact ACI. ACI committee documents are intended for the use of individuals who are competent to evaluate the significance and limitations of its content and recommendations and who will accept responsibility for the application of the material it contains. Individuals who use this publication in any way assume all risk and accept total responsibility for the application and use of this information. All information in this publication is provided “as is” without warranty of any kind, either express or implied, including but not limited to, the implied warranties of merchantability, fitness for a particular purpose or non-infringement. -
Proportioning for Mass Concrete
Proportioning for Mass Concrete Darrell F. Elliot,FACI Technical Service Manager Buzzi Unicem USA What is Mass Concrete? ACI defines Mass Concrete as “any volume of concrete with dimensions large enough to require that measures be taken to cope with generation of heat from hydration of the cement and attendant volume change to minimize cracking.” ACI does not specify an exact minimum thickness, depends on many factors Hoover Dam - 660 ft (200 m) wide base Traditional Mass Concrete Mixes Low strength requirements 56 or 90 days to achieve strength Very large coarse aggregate Very low cement contents Type IV or Type II(MH) High SCM replacements Mat Foundations, Houston Volume PSI ENRON Building 11,000 5,000 5 Houston Center 8,500 6,000 1000 Main 12,000 M D Anderson (2) 12,000 Mass Concrete For mass placements, ACI 207 and U. S. Army Corps of Engineers recommend: Cement or combination of cement with GGBFS and/or fly ash that achieves a maximum Heat of Hydration of 70 cal/gm at 7 days. Critical Temperature Limits o o Tmax < 165 F (75 C) ∆∆∆T < 35 oF (20 oC) Why these Limits? o o Tmax < 165 F (75 C) Potential to bypass ettringite phase, resulting in DEF ∆∆∆T < 35 oF (20 oC) Thermal Stress of different expansion & contraction Heating and Cooling Initial heat generated As outside cools, inside The quicker the peak, remains hot. the higher the peak As inside cools, it (less cooling time) contracts & pulls away from perimeter, cracks Time-Temperature Plot Cracking in Top of Pile Cap Heat Energy Calculating the change in temperature in a system may be accomplished by using the following formula: Change in Temperature = Heat gained or lost . -
Partial Replacement Coarse Aggregate by EPS
IOSR Journal of Mechanical and Civil Engineering (IOSR-JMCE) e-ISSN: 2278-1684,p-ISSN: 2320-334X, Volume 17, Issue 4 Ser. IV (Jul. – Aug. 2020), PP 42-52 www.iosrjournals.org Partial Replacement Coarse Aggregate by EPS Rajesh Verma1, Ms. Nikita Jain2 1(Student of Civil Engineering Department, MIST Indore/ RGPV Bhopal, India) 2(Assistant professor Civil Engineering Department, MIST Indore/RGPV Bhopal, India) Abstract: Now a day’s concrete plays a major role in construction industry. Availability of construction material is less day by day. So we can introduce a new kind of material in construction industry to reduce the cost as well as user friendly material. The main objective of the project, by using the available waste material to introduced in concrete industry. Fully replacement of concrete is not possible, so we can made an attempt to develop partial replacement of concrete material. In the last few decades there has been rapid increase in the waste materials and by-products. Some of the industrial by-products like GGBS, fly ash, copper slag, steel slag, Expanded polystyrene (EPS) have been successfully replaced for cement and concrete in the construction industry. It reduces the consumption of natural resources. Steel slag is one of the materials that is considered as a by-product (waste material) obtained during the matte smelting and refining of copper. It has the physical properties similar to the fine aggregate, so it can be used as a replacement for fine aggregate in concrete. Likewise replacement of coarse aggregate is done by some materials, which makes the concrete light weight. -
Updating Thermal Data Sets to Better Evaluate Thermal Effects of Concrete
DSO-2015-02 (8530-2016-01) Updating Thermal Data Sets to Better Evaluate Thermal Effects of Concrete Dam Safety Technology Development Program Katie Bartojay, P.E. Catherine Lucero, M.S., E.I.T U.S. Department of the Interior Bureau of Reclamation Technical Service Center Denver, Colorado January 2016 Form Approved REPORT DOCUMENTATION PAGE OMB No. 0704-0188 The public reporting burden for this collection of information is estimated to average 1 hour per response, including the time for reviewing instructions, searching existing data sources, gathering and maintaining the data needed, and completing and reviewing the collection of information. Send comments regarding this burden estimate or any other aspect of this collection of information, including suggestions for reducing the burden, to Department of Defense, Washington Headquarters Services, Directorate for Information Operations and Reports (0704-0188), 1215 Jefferson Davis Highway, Suite 1204, Arlington, VA 22202-4302. Respondents should be aware that notwithstanding any other provision of law, no person shall be subject to any penalty for failing to comply with a collection of information if it does not display a currently valid OMB control number. PLEASE DO NOT RETURN YOUR FORM TO THE ABOVE ADDRESS. 1. REPORT DATE 2. REPORT TYPE 3. DATES COVERED 12-31-2015 Research n/a 4. TITLE AND SUBTITLE 5a. CONTRACT NUMBER n/a Updating Thermal Data Sets to Better Evaluate Thermal Effects of Concrete 5b. GRANT NUMBER n/a 5c. PROGRAM ELEMENT NUMBER n/a 6. AUTHOR(S) 5d. PROJECT NUMBER n/a Katie Bartojay, P.E. 5e. TASK NUMBER Catherine Lucero, M.S., E.I.T. -
Concrete Floors and Moisture
EB119 Rough 4 12/7/04 3:35 PM Page 1 Howard Kanare ENGINEERING BULLETIN 119 Concrete Floors and Moisture by Howard M. Kanare An organization of cement companies The National Ready Mixed Concrete Association is the to improve and extend the uses of port- leading industry advocate working to expand and improve land cement and concrete through the ready mixed concrete industry through leadership, pro- market development, engineering, re- motion, education and partnering, ensuring that ready search, education, and public affairs mixed concrete is the building material of choice. work. Abstract: Unwanted moisture in concrete floors causes millions of dollars in damage to buildings annually in the United States. Problems from excessive moisture include deterioration and debonding of floor cover- ings, trip-and-fall hazards, microbial growth leading to reduced indoor air quality, staining and deterioration of building finishes. Understanding moisture in concrete leads to design of floors and flooring systems that provide excellent service for many years. This book discusses sources of moisture, drying of concrete, methods of measuring moisture, construction practices, specifications, and responsibilities for successful floor projects. Keywords: Alkalies, concrete floors, construction practices, floor coverings, flooring, mildew, moisture, moisture-proofing, mold, vapor retarders Reference: Kanare, Howard M., Concrete Floors and Moisture, EB119, Portland Cement Association, Skokie, Illinois, and National Ready Mixed Concrete Association, Silver Spring, Maryland, USA, 2005, 168 pages. About the Author: Howard M. Kanare, Senior Principal Scientist, Construction Technology Laboratories, Inc., 5400 Old Orchard Road, Skokie, Illinois 60077, USA, e-mail: [email protected]. ©2005, Portland Cement Association All rights reserved. No part of this book may be reproduced in any form without permission in writing from the publisher, except by a reviewer who wishes to quote brief passages in a review written for inclusion in a magazine or newspaper. -
Fracture Mechanics of Concrete· Structures
ACI Committee 446 on Fracture Mechanics (1992) (Ba-zant, Z.P. prine. author &chairman). 'Fracture mechanics of concrete: concepts, models and determination of material properties.' Fracture Mechanics of Concrete Structures (Proc. FraMCoS1-lnt. Conf. on Fracture Mechanics of Concrete Structures, Breckenridge, Colorado, June), ed. by Z.P. Baiant, Elsevier Applied Science, London, 1-140 (reprinting of S25). Proceedings of the First International Conference on Fracture Mechanics of Concrete Structures (FraMCoS1) held at Beaver Run Resort, Breckenridge, FRACTURE MECHANICS Colorado, USA, 1-5 June 1992 OF CONCRETE· STRUCTURES organized by Northwestern University in collaboration with the Edited by NSF Science and Technology Center for ZDENEK P. BAZANT Advanced Cement-Based Materials (ACBM) Walter P. Murphy Professor ofCivil Engineering, Northwestern University, Evanston, Illinois, USA and the ACI Committee 446 on Fracture Mechanics under the auspices of the International Association for Bridge and Structural Engineering (IABSE) and the American Concrete Institute (AC!) and sponsored by the US National Science Foundation (NSF) ELSEVIER APPLIED SCIENCE LONDON and NEW YORK XXll Fracture Mechanics Applications in the Analysis of Concrete Repair and Protection Systems (Invited Paper) by H. K. Hilsdorf, M. Giinter,<P. Haardt .................... 951 Crack Formation Due to Hygral Gradients by AM. Alvaredo, F. H. Wittmann ........................ 960 Part, I Analysis of Shrinkage Cracks in Concrete by Fictitious Crack Model by H. Akita, T. Fujiwara, Y. Ozaka .... "",',",",.,','" 967 State-of-Art Report 1 Cracking and Damage in Concrete Due to Non-Uniform Shrinkage by T. Tsubaki, M. K. Das, K. Shitaba .. , ..... , ..... , . , ..... , 971 by Simulation of Thermal Cracks of Mass Concrete in Stage Construction ACI Committee 446, Fracture Mechanics byL-H, Chen, Z-x. -
Progressive Mass Concrete Solutions
Progressive mass concrete solutions Infastructure issues The opportunity A national infrastructure in need of 150,000 bridges need repairs 1 repairs, coupled with the dawn of 10,000 dams with a new era of public works projects high-hazard potential 2 not seen in decades, is placing large-scale projects such as dams, bridges and buildings under greater scrutiny than ever before. Both the literal and figurative foundations of these projects will be poured in mass quantities of concrete. Two football field-sized precast segments weighing 11,000 and 9,500 tons were floated 27 miles up the Monongahela River and set down atop the drilled shaft foundation to form the new base of the Braddock lock and dam in Pittsburgh, PA. The mix for the segments contained 60% Holcim GranCem® Slag Cement. Using a higher percentage of slag cement in your mass concrete projects delivers strength, durability and eco-efficiency. Challenges with pouring mass concrete. When pouring mass quantities of concrete, it is a common practice to use varying mixes of portland cement or supplemental cementitious materials such as slag cement or fly ash. These mixes are used to help control the amount of heat generated as the concrete cures and Rock and Roll Hall of Fame – Cleveland, OH helps maintain structural integrity. Nearly 17,000 cubic yards of Envirocore™ GranCem® Slag Cement were used in the construction of the museum, including a 10-foot thick foundation Advantages of blended cements. While concrete has not changed much over supporting the structure’s 168 foot tall tower. The foundation for the tower rests under water in the the centuries, engineers and builders are discovering new and improved ways to North Coast Harbor, an inlet of Lake Erie. -
Optimizing the Use of Fly Ash in Concrete
CONCRETE Optimizing the Use of Fly Ash in Concrete By: Michael Thomas, Ph.D., P.Eng., Professor of Civil Engineering, University of New Brunswick Introduction Fly ash is used as a supplementary cementitious material (SCM) in the production of portland cement concrete. A supplementary cementitious material, when used in conjunction with portland cement, contributes to the properties of the hardened concrete through hydraulic or pozzolanic activity, or both. As such, SCM's include both pozzolans and hydraulic materials. A pozzolan is defined as a siliceous or siliceous and aluminous material that in itself possesses little or no cementitious value, but that will, in finely divided form and in the Figure 1. Fly ash, a powder resembling cement, has been used in presence of moisture, chemically react with calcium hydroxide at concrete since the 1930s. (IMG12190) ordinary temperatures to form compounds having cementitious properties. Pozzolans that are commonly used in concrete include fly delays in the rate of construction. These drawbacks become particularly ash, silica fume and a variety of natural pozzolans such as calcined pronounced in cold-weather concreting. Also, the durability of the clay and shale, and volcanic ash. SCM's that are hydraulic in behavior concrete may be compromised with regards to resistance to deicer-salt include ground granulated blast furnace slag and fly ashes with scaling and carbonation. high calcium contents (such fly ashes display both pozzolanic and For any given situation there will be an optimum amount of fly ash hydraulic behavior). that can be used in a concrete mixture which will maximize the The potential for using fly ash as a supplementary cementitious material technical, environmental, and economic benefits of fly ash use without in concrete has been known almost since the start of the last century significantly impacting the rate of construction or impairing the long- (Anon 1914), although it wasn't until the mid-1900s that significant term performance of the finished product.