Pressure Reduction Enhancing the Production of 5-Hydroxymethylfurfural from Glucose in Aqueous Phase Catalysis System
Total Page:16
File Type:pdf, Size:1020Kb
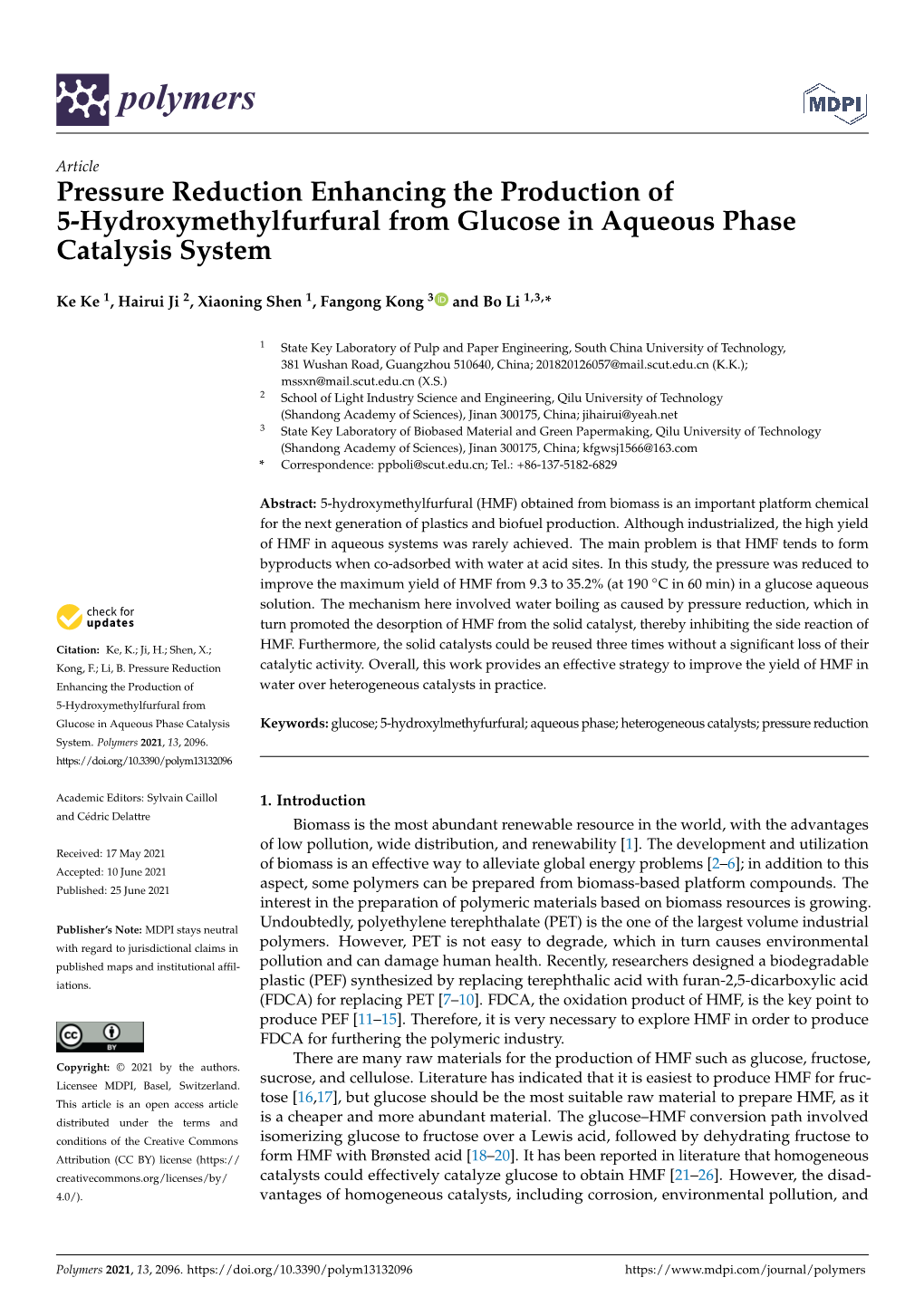
Load more
Recommended publications
-
Chemical Yields from Low-Temperature Pyrolysis of CCA-Treated Wood
United States Department of Agriculture Chemical Yields Forest Service from Low-Temperature Forest Products Laboratory Pyrolysis of CCA-Treated Research Paper Wood FPL–RP–652 Qirong Fu Dimitris S. Argyropolous Lucian A. Lucia David C. Tilotta Stan T. Lebow Abstract Acknowledgment Low-temperature pyrolysis offers a feasible option for This project was supported by a grant from the Advanced wood-waste management and the recovery of a variety of Housing Research Center. useful chemicals. The effect of chromated copper arsenate (CCA) wood preservative on the yield and composition of Contents various pyrolysis products was investigated in the present Page research. A novel quantitative 31P nuclear magnetic reso- nance (NMR) spectroscopy methodology has been devel- Introduction ..........................................................................1 oped to quantify levoglucosan and levoglucosenone from Management Options for Reuse .......................................1 the pyrolysate of CCA-treated and untreated wood. The CCA treatment of wood had a notable effect on the charac- Low-Temperature Pyrolysis .............................................2 teristics of the carbohydrate-derived degradation products Experimental ........................................................................2 of tar. In particular, yields of the important pharmaceutical precursors levoglucosan and levoglucosenone were elevated Materials ..........................................................................2 by 3 and 4.5 times, respectively, when compared -
Solid Phosphoric Acid Catalysts Based on Mesoporous Silica For
Solid phosphoric acid catalysts based on mesoporous silica for levoglucosenone production via cellulose fast pyrolysis J. A. Santander a*, M. Alvarez a, V. Gutierrez b, M. A. Volpe b. a Instituto de Química del Sur, INQUISUR (CONICET-UNS), Av. Alem 1253, Bahía Blanca (8000), Argentina. b Planta Piloto de Ingeniería Química, PLAPIQUI (CONICET-UNS), Florida 7500, Bahía Blanca (8000), Argentina *Corresponding author, José A. Santander, e-mail address: [email protected], phone number: +54 0291 4595101 ext. 3592 Abstract BACKGROUND: Biochemicals are interesting alternatives for biomass valorization owing to their much higher added value compared to biofuels and energy products. Several methods for the production of valuable chemicals such as levoglucosenone (LGO) via thermochemical processes over solid acid catalysts are being investigated due to their important advantages compared to conventional biomass acid impregnation techniques. The present work explores the synthesis of catalytic materials for the production of this platform molecule. Accepted Article This article has been accepted for publication and undergone full peer review but has not been through the copyediting, typesetting, pagination and proofreading process, which may lead to differences between this version and the Version of Record. Please cite this article as doi: 10.1002/jctb.5795 This article is protected by copyright. All rights reserved. RESULTS: Aluminum-loaded SBA-15 mesoporous silica and the corresponding solid phosphoric acid catalysts were prepared, characterized by TEM, FT-IR, MAS NMR, NH3-TPD, N2 adsorption, ICP-AES and titration of “free H3PO4”, and tested in cellulose fast pyrolysis. Post synthesis Al deposition on the silica support produced an increase of bio-oil yield and LGO amount in pyrolysis products. -
Bio-Solvents: Synthesis, Industrial Production and Applications Novisi K
Chapter Bio-Solvents: Synthesis, Industrial Production and Applications Novisi K. Oklu, Leah C. Matsinha and Banothile C.E. Makhubela Abstract Solvents are at the heart of many research and industrial chemical processes and consumer product formulations, yet an overwhelming number are derived from fossils. This is despite societal and legislative push that more products be produced from carbon-neutral resources, so as to reduce our carbon footprint and environmental impact. Biomass is a promising renewable alternative resource for producing bio-solvents, and this review focuses on their extraction and synthesis on a laboratory and large scale. Starch, lignocellulose, plant oils, animal fats and proteins have been combined with creative synthetic pathways, novel technolo- gies and processes to afford known or new bio-derived solvents including acids, alkanes, aromatics, ionic liquids (ILs), furans, esters, ethers, liquid polymers and deep eutectic solvents (DESs)—all with unique physiochemical properties that warrant their use as solvation agents in manufacturing, pharmaceutical, cosmet- ics, chemicals, energy, food and beverage industries, etc. Selected bio-solvents, conversion technologies and processes operating at commercial and demonstration scale including (1) Solvay’s Augeo™ SL 191 renewable solvent, (2) Circa Group’s Furacell™ technology and process for making levoglucosenone (LGO) to produce dihydrolevoglucosenone (marketed as Cyrene™), (3) Sappi’s Xylex® technology and demonstration scale processes that aim to manufacture precursors for bio- solvents and (4) Anellotech’s Bio-TCat™ technology and process for producing benzene, toluene and xylenes (BTX) are highlighted. Keywords: bio-solvents, renewable resources, green chemistry, biorefinery, biomass 1. Introduction Air quality deterioration, environmental, health and safety issues have raised serious concerns over continued processing of fossil-based feedstocks in producing chemical products such as fuels and solvents. -
Catalytic Dehydration of Levoglucosan to Levoglucosenone Using Brønsted Solid Acid Catalysts in Tetrahydrofuran Green Chemistry
Green Volume 21 Number 18 21 September 2019 Pages 4827–5132 Chemistry Cutting-edge research for a greener sustainable future rsc.li/greenchem ISSN 1463-9262 PAPER Nelson Cardona-Martínez et al. Catalytic dehydration of levoglucosan to levoglucosenone using Brønsted solid acid catalysts in tetrahydrofuran Green Chemistry PAPER Catalytic dehydration of levoglucosan to levoglucosenone using Brønsted solid acid Cite this: Green Chem., 2019, 21, 4988 catalysts in tetrahydrofuran Oscar Oyola-Rivera, a Jiayue He, b George W. Huber, b James A. Dumesic b and Nelson Cardona-Martínez *a We studied the production of levoglucosenone (LGO) via levoglucosan (LGA) dehydration using Brønsted solid acid catalysts in tetrahydrofuran (THF). The use of propylsulfonic acid functionalized silica catalysts increased the production of LGO by a factor of two compared to the use of homogeneous acid catalysts. We obtained LGO selectivities of up to 59% at 100% LGA conversion using solid Brønsted acid catalysts. Received 8th May 2019, Water produced during the reaction promotes the solvation of the acid proton reducing the activity and Accepted 10th July 2019 the LGO production. Using solid acid catalysts functionalized with propylsulfonic acid reduces this effect. DOI: 10.1039/c9gc01526d The hydrophilicity of the catalyst surface seems to have an effect on reducing the interaction of water rsc.li/greenchem with the acid site, improving the catalyst stability. 1. Introduction fast pyrolysis, at yields of up to 45%.18 The production of LGO has been mainly studied via acid-catalyzed pyrolysis of LGA – Lignocellulosic biomass is one of the most abundant carbon and cellulose using acid catalysts.11,15,19 21 Two routes have sources in the world and has the potential of becoming an been proposed for the acid-catalyzed conversion of LGA to important source for the renewable production of commodity LGO. -
(12) United States Patent (10) Patent No.: US 9,018,423 B2 Allgeier Et Al
USOO90 18423B2 (12) United States Patent (10) Patent No.: US 9,018,423 B2 Allgeier et al. (45) Date of Patent: *Apr. 28, 2015 (54) PRODUCTION OF ALPHA, OMEGA-DIOLS 3,933,930 A 1/1976 Dougherty et al. 4,254,059 A 3/1981 Grey 4400,468 A 8, 1983 Faber (71) Applicant: : du Pets Neo: 4,401,823. A 8, 1983 Arena ompany, Wilmington, DE (US) 4,780,552. A 10/1988 Wambach et al. - 0 5, 112,994 A 5/1992 Koseki et al. (72) Inventors: Alan Martin Allgeier, Wilmington, DE 5,210,335 A 5/1993 Schuster et al. (US); Torren Ryan Carlson, New 5,412,111 A 5/1995 Matsumoto et al. Castle, DE (US); David Richard 5,538,891 A 7/1996 Schneider et al. s 5,696,303 A 12/1997 Darsow et al. Corbin, West Chester, PA (US); 5,981,769 A 1 1/1999 Baur et al. Wathudura Indika Nama De Silva, 6,008,418 A 12/1999 Baur et al. Wilmington, DE (US); Ekaterini 6,087,296 A 7/2000 Harper et al. Koroves.si. Wilmington, DE (US); Carl 5.8 f 1 13s Shayner et al. G E.g. SR DE (SS). 6,403,845 B1 6/2002 PfeffingerOlt et al. et al. oachin C Ritter, Wilmington, 6,407.294 B1 6/2002 Breitscheidel et al. (US); H David Rosenfeld, Drumore, PA 6,433,192 B1 8/2002 Fischer et al. (US); Sourav Kumar Sengupta, 6,462,220 B1 10/2002 Luyken et al. Wilmington, DE (US) 6,593,481 B1 7/2003. -
Sulfonate Ionic Liquid As a Stable and Active Catalyst for Levoglucosenone Production from Saccharides Via Catalytic Pyrolysis
Catalysts 2013, 3, 757-773; doi:10.3390/catal3040757 OPEN ACCESS catalysts ISSN 2073-4344 www.mdpi.com/journal/catalysts Article Sulfonate Ionic Liquid as a Stable and Active Catalyst for Levoglucosenone Production from Saccharides via Catalytic Pyrolysis Shinji Kudo 1,*, Zhenwei Zhou 2, Kento Yamasaki 2, Koyo Norinaga 1 and Jun-ichiro Hayashi 1 1 Institute for Materials Chemistry and Engineering, Kyushu University, 6-1 Kasuga Koen, Kasuga 816-8580, Japan; E-Mails: [email protected] (K.N.); [email protected] (J.-i.H.) 2 Interdisciplinary Graduate School of Engineering Sciences, Kyushu University, 6-1 Kasuga Koen, Kasuga 816-8580, Japan; E-Mails: [email protected] (Z.Z.); [email protected] (K.Y.) * Author to whom correspondence should be addressed; E-Mail: [email protected]; Tel.: +81-92-583-7793; Fax: +81-92-583-7793. Received: 25 July 2013; in revised form: 5 September 2013 / Accepted: 18 September 2013 / Published: 30 September 2013 Abstract: In this study, various types of ionic liquids (ILs) were examined for catalytic activity in the pyrolysis of cellulose for the production of levoglucosenone, which is a valuable and versatile compound for the synthesis of a variety of novel compounds. Cellulose was simply mixed with the ILs and subjected for the pyrolysis, typically at 300 °C, to produce volatile products, including levoglucosenone, separated from the ILs phase. The type of IL anion significantly affected the catalysis, and the use of ILs bearing sulfonate anion resulted in distinguished yields of levoglucosenone and IL recoveries for the reutilization. -
Synthetic Study of Levoglucosenone
University of Montana ScholarWorks at University of Montana Graduate Student Theses, Dissertations, & Professional Papers Graduate School 1982 Synthetic study of levoglucosenone Maria G. Essig The University of Montana Follow this and additional works at: https://scholarworks.umt.edu/etd Let us know how access to this document benefits ou.y Recommended Citation Essig, Maria G., "Synthetic study of levoglucosenone" (1982). Graduate Student Theses, Dissertations, & Professional Papers. 8143. https://scholarworks.umt.edu/etd/8143 This Thesis is brought to you for free and open access by the Graduate School at ScholarWorks at University of Montana. It has been accepted for inclusion in Graduate Student Theses, Dissertations, & Professional Papers by an authorized administrator of ScholarWorks at University of Montana. For more information, please contact [email protected]. COPYRIGHT ACT OF 1976 Th is is an unpublished m a nu sc ript in w hich c o pyr ig h t sub s i s t s . Any further r e p r in t in g of it s contents must be approved BY th e a u th o r . MANSFIELD L ibrary U n iv e r s it y of Montana nATpi 19R2 Reproduced with permission of the copyright owner. Further reproduction prohibited without permission. Reproduced with permission of the copyright owner. Further reproduction prohibited without permission. A SYNTHETIC STUDY OF LEVOGLUCOSENONE by Maria G. M. Essig B.S., University of California, Irvine, 1979 Presented in partial fulfillm ent of the requirements for the degree of Master of Science UNIVERSITY OF MONTANA 1982 Approved by: Chairman of Examiners DecTn, Graduate Schïïb F -^ / / - ^ ^ Date Reproduced with permission of the copyright owner. -
Understanding Cellulose Primary and Secondary
UNDERSTANDING CELLULOSE PRIMARY AND SECONDARY PYROLYSIS REACTIONS TO ENHANCE THE PRODUCTION OF ANHYDROSACCHARIDES AND TO BETTER PREDICT THE COMPOSITION OF CARBONACEOUS RESIDUES By ZHOUHONG WANG A dissertation submitted in partial fulfillment of the requirements for the degree of DOCTOR OF PHILOSOPHY WASHINGTON STATE UNIVERSITY Department of Biological Systems Engineering DECEMBER 2013 To the Faculty of Washington State University: The members of the Committee appointed to examine the dissertation of ZHOUHONG WANG find it satisfactory and recommend that it be accepted. ___________________________________ Manuel Garcia-Pérez, Ph.D., Chair ___________________________________ Armando G. McDonald, Ph.D. ___________________________________ Su Ha, Ph.D. ___________________________________ Shyam S. Sablani, Ph.D. ii ACKNOWLEDGMENT I would like to thank Dr. Manuel Garcia-Perez for his support and advice during my PhD studies. It’s my great honor to learn from his passion on research and his oversight of my research. I would like to thank my committee members: Dr. Armando McDonald, Dr. Su Ha, and Dr. Shyam Sablani for their kind guidance and continued participation. I would like to thank Prof. Sascha Kersten for the support during my visit to his group (Sustainable Process Technology (original Thermal Chemical Conversion of Biomass), University of Twente, the Netherlands). Thanks to all the members in SPT group (Prof Wim van Swaaij, Prof. Jean-Paul Lange, Prof. van den Berg, Dr. Wim Brilman, Dr. Louis van der Ham, Dr. Guus van Rossum, Dr. BoeloSchuur, Dr. Roel Westerhof, Dr. Michal Gramblicka, Johan Agterhorst, Karst van Bree, Erna Fränzel-Luiten, Benno Knaken, Yvonne Bruggert-ter Huurne, Maria Castellvi Barnes, Laura Garcia Alba, Stijn Oudenhoven, Rens Contact, Ying Du, Xiaohua Li, Jeroen de Graaf, Joram Boegborn, Tim Hilbert, Michiel van Kuppevelt) for the help and joy they kindly offered. -
J. Anal. Appl. Pyrolysis 82 (2008) 140–144
This article appeared in a journal published by Elsevier. The attached copy is furnished to the author for internal non-commercial research and education use, including for instruction at the authors institution and sharing with colleagues. Other uses, including reproduction and distribution, or selling or licensing copies, or posting to personal, institutional or third party websites are prohibited. In most cases authors are permitted to post their version of the article (e.g. in Word or Tex form) to their personal website or institutional repository. Authors requiring further information regarding Elsevier’s archiving and manuscript policies are encouraged to visit: http://www.elsevier.com/copyright Author's personal copy J. Anal. Appl. Pyrolysis 82 (2008) 140–144 Contents lists available at ScienceDirect Journal of Analytical and Applied Pyrolysis journal homepage: www.elsevier.com/locate/jaap Understanding the pyrolysis of CCA-treated wood Part II. Effect of phosphoric acid Qirong Fu, Dimitris S. Argyropoulos *, David C. Tilotta, Lucian A. Lucia Organic Chemistry of Wood Components Laboratory, Department of Forest Biomaterials Science & Engineering, North Carolina State University, Raleigh, NC 27695-8005, USA ARTICLE INFO ABSTRACT Article history: The pyrolysis process of chromated copper arsenate-treated wood impregnated with phosphoric acid (2– Received 15 February 2007 6 wt.%) has been investigated using a Kugelrohr short-path distillation apparatus. The presence of Accepted 22 February 2008 phosphoric acid is shown to change the overall pyrolysis kinetics and yields of products resulting in a Available online 7 March 2008 decrease in the amount of volatile products and an increase in the char formation. The yield of levoglucosan was found to decrease in the presence of relatively higher concentrations of phosphoric Keywords: acid, while the yield of levoglucosenone increased. -
Selectively Production of Levoglucosenone from Cellulose Via Catalytic Fast Pyrolysis
Selectively Production of Levoglucosenone from Cellulose via Catalytic Fast Pyrolysis Qian Le Guangzhou Institute of Energy Conversion Liqun Jiang ( [email protected] ) Guangzhou Institute of Energy Conversion https://orcid.org/0000-0002-8541-7539 Zengli Zhao Guangzhou Institute of Energy Conversion Research Article Keywords: Levoglucosenone, Magnetic solid acid, Catalytic fast pyrolysis, Cellulose Posted Date: March 12th, 2021 DOI: https://doi.org/10.21203/rs.3.rs-280794/v1 License: This work is licensed under a Creative Commons Attribution 4.0 International License. Read Full License 1 Selectively production of levoglucosenone from 2 cellulose via catalytic fast pyrolysis 3 Le Qiana,b, Liqun Jianga,*, Zengli Zhaoa 4 aCAS Key Laboratory of Renewable Energy, Guangdong Provincial Key Laboratory of New and 5 Renewable Energy Research and Development, Guangzhou Institute of Energy Conversion, 6 Chinese Academy of Sciences, Guangzhou 510640, China 7 bNano Science and Technology Institute, University of Science and Technology of China, Suzhou 8 215000, China 9 10 *Corresponding author: Tel: +86-020-87057721 Fax: +86-020-87057737 11 E-mail: [email protected] 12 13 Abstract 14 Levoglucosenone (LGO) has a wide range of utilization in the field of organic synthesis. Magnetic 15 solid acid (Fe3O4/C-SO3H600) was used in fast pyrolysis of cellulose to produce LGO. It was 16 demonstrated that the catalyst could promote the pyrolysis of cellulose to produce LGO, but the 17 yield was affected by the pyrolysis temperature and the relative amount of catalyst. The yield of 18 LGO reached 20.0 wt% from catalytic fast pyrolysis of cellulose at 300 °C, which was 19 significantly higher than that from cellulose (0.3 wt%). -
Differentiation of Acids in Their Effects on Pretreatment
Markedly different decomposition temperature and products of biomass pyrolysis at low temperature – differentiation of acids in their effects on pretreatment Peifang Yan, Xiumei Liu, Zhanwei Xu, and Zongchao Conrad Zhang* State Key Laboratory of Catalysis, Dalian National Laboratory for Clean Energy, Dalian Institute of Chemical Physics, Chinese Academy of Sciences, Dalian 116023, P. R. China. *E-mail: [email protected]. Dedicated to the 70th anniversary of Dalian Institute of Chemical Physics, CAS Table S1. Characterization of raw and acids pretreated biomass. Entry Samples Cell-wall components (wt.% dry basis)a Ultimate analysis (wt.% dry basis) Cellulose Hemicell. Lignin Ash Others N C H S O 1 Pine 40.9 23.0 27.5 0.7 7.9 0.26 49.4 6.4 0.40 43.8 2 Pine_ H3PO2 38.9 21.0 24.2 0.3 6.8 0.19 49.3 6.6 0.02 44.0 3 Pine_ H3PO4 38.3 20.8 25.7 0.2 6.5 0.21 49.2 6.7 0.06 44.1 4 Pine_ HCl 36.4 10.9 19.3 0.1 1.5 0.20 49.5 6.5 0.10 43.9 5 Poplar 41.5 19.4 23.7 0.8 14.6 0.30 49.4 6.5 / 44.1 6 Poplar_ H3PO2 41.4 20.0 20.1 0.2 10.7 0.31 48.7 6.8 / 44.4 7 Poplar_ H3PO4 40.6 19.0 21.3 0.1 13.7 0.25 49.0 6.8 / 44.1 8 Poplar_ HCl 39.7 7.3 10.1 0.2 2.1 0.21 47.2 6.7 / 46.0 a: Cell-wall compositions, corrected for the measured solid recovery rate. -
Articles and Was Predominately Oxygenated (OOA)
Atmos. Chem. Phys., 11, 10219–10241, 2011 www.atmos-chem-phys.net/11/10219/2011/ Atmospheric doi:10.5194/acp-11-10219-2011 Chemistry © Author(s) 2011. CC Attribution 3.0 License. and Physics Origins and composition of fine atmospheric carbonaceous aerosol in the Sierra Nevada Mountains, California D. R. Worton1,2, A. H. Goldstein1,3, D. K. Farmer4,5, K. S. Docherty4,5,*, J. L. Jimenez4,5, J. B. Gilman4,6, W. C. Kuster6, J. de Gouw4,6, B. J. Williams7, N. M. Kreisberg2, S. V. Hering2, G. Bench8, M. McKay1,**, K. Kristensen9, M. Glasius9, J. D. Surratt10,***, and J. H. Seinfeld11 1Department of Environmental Science, Policy and Management, University of California, Berkeley, CA, 94720, USA 2Aerosol Dynamics Inc., Berkeley, CA, 94710, USA 3Department of Civil and Environmental Engineering, University of California, Berkeley, CA, 94720, USA 4Cooperative Institute for Research in Environmental Sciences, University of Colorado, Boulder, CO, 80309, USA 5Department of Chemistry and Biochemistry, University of Colorado, Boulder, CO, 80309, USA 6NOAA Earth System Research Laboratory, Boulder, CO, 80305, USA 7Energy, Environmental and Chemical Engineering, Washington University, St. Louis, MO, 63130, USA 8Center for Accelerator Mass Spectrometry, Lawrence Livermore National Laboratory, Livermore, CA, 94550, USA 9Department of Chemistry, University of Aarhus, Aarhus C, 8000, Denmark 10Department of Chemistry, California Institute of Technology, Pasadena, CA, 91125, USA 11Departments of Environmental Science and Engineering and Chemical Engineering, California Institute of Technology, Pasadena, CA, 91125, USA *now at: Alion Science and Technology, EPA Office of Research and Development, EPA Research and Development, Research Triangle Park, NC, USA **now at: California Air Resources Board, Sacramento, CA, USA ***now at: Department of Environmental Sciences and Engineering, University of North Carolina at Chapel Hill, Chapel Hill, NC, 27599, USA Received: 1 June 2011 – Published in Atmos.