The Development of a Hydraulic Hybrid Vehicle Laboratory: Integrating Education and Research
Total Page:16
File Type:pdf, Size:1020Kb
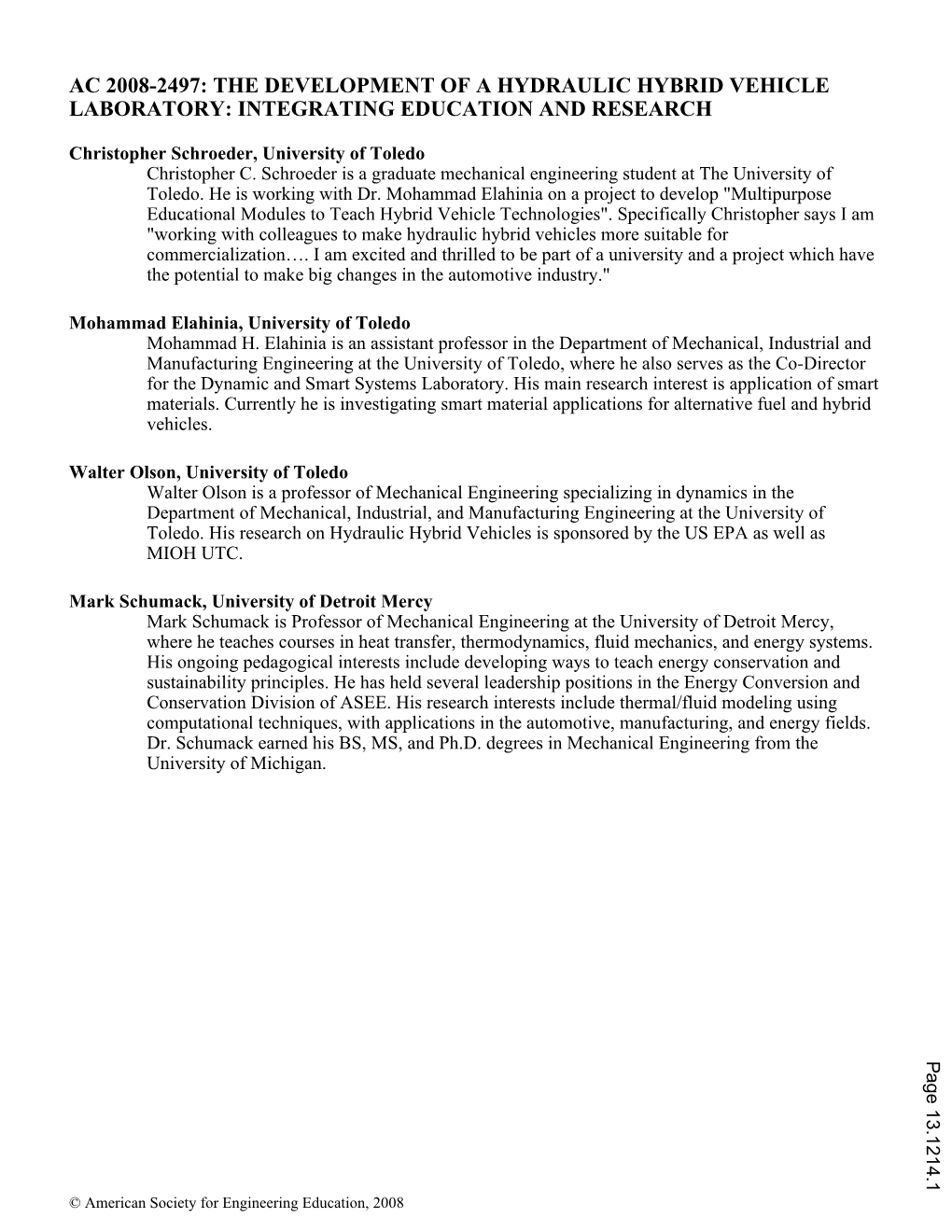
Load more
Recommended publications
-
780 Solid Waste Maintenance Technician
780 Solid Waste Maintenance Technician Nature of Work This is skilled mechanical and maintenance work performing a variety of activities associated with the repair and routine maintenance of a variety of solid waste trucks and machinery used for solid waste operations. Activities associated with the job include performing routine preventive maintenance, safety inspections and repair work on all trucks, machinery and equipment, changing and repairing large truck tires, and assisting with building maintenance and repair activities. Additional activities include diagnosing vehicle components and/or equipment malfunctions, performing minor body work and welding and fabricating parts when required, repairing hydraulic equipment located at convenience centers and assisting with transfer station and landfill operations when necessary. Job duties require considerable knowledge and experience in vehicle repair and maintenance, hydraulics, welding, air conditioning repair and metal fabrication, considerable knowledge of building maintenance and repair activities, good organizational, interpersonal and decision making skills and sufficient strength and agility to perform the physically demanding aspects of the job in a variety of weather conditions. Job performance is evaluated by the Solid Waste Director through review of daily repair work and preventive maintenance activities on trucks and machinery, level of support provided for building maintenance activities, accuracy of job related information related to the procurement and purchase of parts and equipment, diagnostic capabilities and quality of the repair work performed. Illustrative Examples of Work -Performs minor repair work and preventive maintenance activities on solid waste trucks, vehicles, machinery and equipment. -Troubleshoots and diagnoses equipment malfunctions to determine needed repairs. -Rebuilds and/or repairs electrical, cooling, suspension, and braking components and systems. -
Estimating Reversible Pump-Turbine Characteristics
A WATER RESOURCES TECHNICAL PUBLICATION ENGINEERING MONOGRAPH NO. 39 Estimating Reversible Pump-TurbineCharacteristics UNtTED STATES DEPARTMENT OF THE INTERIOR BUREAU OF RECLAMATlON MS-230 (l-76) Bureau of Reclamation TECHNICAL REiPORT STANDARD TITLE PAG 3. RECIPIENT’S CATALOG NO. 4. TITLE AND SUBTITLE 5. REPORT DATE Estimating Reversible Pump-Turbine December 1977 Characteristics 6. PERFORMING ORGANIZATION CODE 7. AUTHOR(S) 6. PERFORMING ORGANIZATION REPORT NO. R. S. Stelzer and R. N. Walters Engineering Monograph 39 9. PERFORMING ORGANIZATION NAME AND ADDRESS 10. WORK UNIT NO. Engineering and Research Center Bureau of Reclamation 11. CONTRACT OR GRANT NO. Denver, CO 80225 13. TYPE OF REPORT AND PERIOD COVERED 2. SPONSORING AGENCY NAME AND ADDRESS Same 14. SPONSORING AGENCY CODE 5. SUPPLEMENTARY NOTES 6. ABSTRACT The monograph presents guidelines for designers who plan or maintain pump-turbine installations. Data are presented on recent installations of pump-turbines which include figures showing operating characteristics, hydraulic performance, and sizing of the unit. Specific speed, impeller/ runner diameter, and the best efficiency head and discharge were aelectei as the criteria that characterize the unit performance. 7. KEY WORDS AND DOCUMENT ANALYSIS I. DESCRIPTORS-- / pumped storage/ *pump turbines/ powerplants/ reversible turbines/ Francis turbines/ pumps/ power head/ turbine efficiency/ specific speed/ cavitation index/ hydraulic machinery/ design criteria ). IDENTIFIERS-- / Flatiron Powerplant, CO/ Mt. Elbert Pumped-Storage Power- plant, CO/ Grand Coulee Pumping Plant, WA/ San Luis Pumping-Generating/ Senator Wash Dam, CA/ :. COSATI Field/Group 13G COWRR: 1307.1 6. DISTRIBUTION STATEMENT 19. SECURITY CLASS pt. NO. OF PAGI ITHIS REPORT) \voiloble from the National Technical Information Service, Operations UNCLASSIFIED division, Springfield. -
Hydraulic Machinery • Turbine Is a Device That Extracts Energy from a Fluid (Converts the Energy Held by the Fluid to Mechanical Energy)
Hydraulic Machines power point presentation Slides has been adapted from Hydraulic Machines, K. Subramanya 2016-2017 Prepared by Dr. Assim Al-Daraje 1 Chapter (1 Part 1) Prepared by Dr. Assim Al-Daraje INTRODUCTION 2 Hydraulic machinery • Turbine is a device that extracts energy from a fluid (converts the energy held by the fluid to mechanical energy) • Pumps are devices that add energy to the fluid (e.g. pumps, fans, blowers and compressors). 3 INTRODUCTION Fluid-flow machines are very broadly classified as turbo-machines and positive displacement machines. A turbo-machine is a device that adds energy to a fluid or extracts energy from the fluid by virtue of a rotating system of blades. These machines require a rotating element called rotor and relative motion between the fluid and the rotor. 4 If the machine adds energy it is called a pump; if it extracts energy it is called a turbine. The fluid to be pumped can be in incompressible mode throughout its passage in the machine or compressibility effects may come in to picture at different phases of its interaction in the machine. If the fluid is water, the pump device is labeled as water pump. 5 Turbines • J.V. Poncelet first introduced the idea of the development of mechanical energy through hydraulic energy • Modern hydraulic turbines have been developed by L.A. Pelton (impulse), G. Coriolis and J.B. Francis (reaction) and V Kaplan (propeller) 6 A-Pelton Wheel, B-Francis, Turbine, C-Kaplan Turbine 7 Pelton (impulse) 8 9 Kaplan (propeller) 10 11 Turbines • Hydro electric power is the most remarkable development pertaining to the exploitation of water resources throughout the world • Hydroelectric power is developed by hydraulic turbines which are hydraulic machines. -
Theoretical Simulation of Static and Dynamic Behavior of Electro-Hydraulic Servo Valves
Scientific Bulletin of the The 6th International Conference on Politehnica University of Timisoara Hydraulic Machinery and Hydrodynamics Transactions on Mechanics Special issue Timisoara, Romania, October 21 - 22, 2004 THEORETICAL SIMULATION OF STATIC AND DYNAMIC BEHAVIOR OF ELECTRO-HYDRAULIC SERVO VALVES Victor BALASOIU, Prof.* Mircea Octavian POPOVICIU, Prof. Department of Hydraulic Machinery Department of Hydraulic Machinery “Politehnica” University of Timisoara “Politehnica” University of Timisoara Ilare BORDEASU, Assoc. Prof. Department of Hydraulic Machinery “Politehnica” University of Timisoara *: Bv Mihai Viteazu 1, 300222, Timisoara, Romania, Tel.: (+40) 256 403681, Fax: (+40) 256 403700, (+) 256 4030682, Email: [email protected], [email protected] ABSTRACT The electro-hydraulic servo-valves (EHSV) as in- range Yoi and the clearance J over the linearity degree terface in automatic hydraulic systems are in essence and the magnitude of the adjusted flow. hydroelectric directional control valves with cylindrical The model of the dynamic equilibrium of the spool spool, with integral reaction. The output quantity valve is defined starting with the computation of forces (flow rate, pressure) is modified proportional with acting on the spool. Introducing the concept of interac- the control signal (voltage, current) together link tion between the aggregate components nozzle-spool- (electrical, hydraulic or mechanical). Both the manner distributor it was defined the mathematical model for in which the reaction signal is produced and the the directional spool valve as a whole. position of the information circuit where it is applied, After defining the transfer function, both analyze characterises the type but also static and dynamic and syntheses of performances were possible for the behavior of the servo valve. -
The Influence of Gear Micropump Body Asymmetry on Stress Distribution
POLISH MARITIME RESEARCH 1 (93) 2017 Vol. 24; pp. 60-65 10.1515/pomr-2017-0007 THE INFLUENCE OF GEAR MICROPUMP BODY ASYMMETRY ON STRESS DISTRIBUTION Wacław Kollek, Prof. Piotr Osiński Urszula Warzyńska Wrocław University of Science and Technology, Poland ABSTRACT The paper presents the results of numerical calculations of stress distributions in the gear micropump body for applications in hydraulic systems, especially in the marine sector. The scope of the study was to determine the most favorable position of bushings and pumping unit in the gear pump body in terms of stress and displacement distribution in the pump housing. Fourteen cases of gear pump bushings and pumping unit locations were analyzed: starting from the symmetrical position relative to the central axis of the pump, up to a position shifted by 2.6 mm towards the suction channel of the pump. The analysis of the obtained calculation results has shown that the most favorable conditions for pump operation are met when the bushings are shifted by 2.2 mm towards the suction channel. In this case the maximal stress was equal to 109 MPa, while the highest displacement was about 15µm. Strength and stiffness criteria in the modernized pump body were satisfied. Keywords: gear micropump, microhydraulics, finite element method 17, 19, 20, 21, 22]. The development of modern gear units is INTRODUCTION associated with the following trends: increasing operating pressure [6, 18], improving total efficiency [4, 10, 15, 18, 23], Gear pumps are the most common group of positive reducing pressure pulsations [3, 18, 25], minimizing weight displacement pumps used in hydrostatic drive systems as [15] and noise [11, 14, 16], and reducing dynamic loads [7, 12, power generators, as well as in lubrication systems in various 13, 19]. -
Hydraulics & Oil Power Systems Automation Guidebook
PDHonline Course M523 (8 PDH) _____________________________________________________ Hydraulics & Oil Power Systems Automation Guidebook – Part 2 Instructor: Jurandir Primo, PE 2014 PDH Online | PDH Center 5272 Meadow Estates Drive Fairfax, VA 22030-6658 Phone & Fax: 703-988-0088 www.PDHonline.org www.PDHcenter.com An Approved Continuing Education Provider www.PDHcenter.com PDHonline Course M523 www.PDHonline.org HYDRAULICS & OIL POWER SYSTEMS AUTOMATION GUIDEBOOK – PART 2 CONTENTS: INTRODUCTION BASIC PRINCIPLES OF HYDRAULICS HYDRAULIC OIL PROPERTIES HYDRAULIC DRIVE SYSTEMS HYDRAULIC SYSTEMS – BASIC CALCULATIONS HYDRAULIC VALVES TYPES AND FUNCTIONS OF VALVES DIRECTIONAL CONTROL VALVES CYLINDERS AND ACTUATORS CYLINDER CONTROL DIAGRAMS HYDRAULICS & PNEUMATICS - DIFFERENCES BASIC ELECTRO-HYDRAULIC CONTROL HYDRAULICS – SOFTWARE SIMULATIONS HYDRAULICS & PNEUMATICS – BASIC DESCRIPTION HYDRAULICS – TRAINING LINKS AND REFERENCES ©2014 Jurandir Primo Page 1 of 116 www.PDHcenter.com PDHonline Course M523 www.PDHonline.org INTRODUCTION: The word hydraulics is a derivative of the Greek words hydro (meaning water) and aulis (meaning tube or pipe). Originally, the science of hydraulics only covered the physical behavior of water at rest and in motion. The use has broadened its meaning, to include compressed air or gases and oil com- pounds and other confined liquids commonly used under controlled pressure to do some work. Hydraulics can be defined as the engineering science that pertains to liquid pressure and flow. This study includes the manner in which liquids act in tanks, cylinders, hoses, valves and pipes, dealing with their properties and the common ways of utilizing these properties to create motion. It includes the laws of floating bodies and the behavior of fluids under various conditions, and ways of directing this flow to useful ends, as well as many other related subjects and applications. -
Hydraulic Machinery Made Easy
Product Catalogue 2017 Hose I Fittings I Accessories Hydraulic Machinery Made Easy The Easy Choice for Lubrication & Hydraulics PB 1 Dear Customer, Welcome to the Armadillo Group third edition of Hydraulic hose and fitting product guide. Are you looking for another solution to those problems you often have in this industry? Or maybe you are just looking for the good old fashioned service you use to get? Or maybe your problem lies deeper in a maze of technical jargon? Whatever your problem is, our aim is to fill the gap, to provide the easy choice in lubrication and hydraulics. With products sourced from quality suppliers all over the globe we are sure to be able to meet your expectations. Having one of the best stock holdings in the country we are able to offer premium service when you need it most. We hope this catalogue will be of assistance to you not only as a product guide but as a handy reference for threads, hose sizes and other technical information and we look forward to hearing from you soon. Best Regards TheThe Team Team at Armadillo Group The Easy Choice for Lubrication & Hydraulics | www.armadillogroup.com.au CONTENTS CONTENTS Introduction and Information Section 1 9 - 22 Adaptors Section 2 23 - 28 Hose Tails Section 3 29 - 31 4 Wires Hose Tails Section 4 32 - 36 4 Wires Hose Tails Section 5 37 - 48 Ferrules Section 6 49 - 52 Hose Section 7 53 - 57 Hydraulic Components Section 8 58 - 73 Technical HOSE TAIL NOMENCLATURE RHCM 05 12 08 Hose Connector Hose Tail Size Style Thread Size NOTE: Please note Armadillo Group refers to thread sizes only, not dash size as this is universal language. -
Energy Efficiency Comparison of Hydraulic Accumulators And
energies Article Energy Efficiency Comparison of Hydraulic Accumulators and Ultracapacitors Jorge Leon-Quiroga 1, Brittany Newell 1, Mahesh Krishnamurthy 2, Andres Gonzalez-Mancera 3 and Jose Garcia-Bravo 1,* 1 Purdue Polytechnic School of Engineering Technology, Purdue University, West Lafayette, IN 47907, USA; [email protected] (J.L.-Q.); [email protected] (B.N.) 2 Department of Electrical and Computer Engineering, Illinois Institute of Technology, Chicago, IL 60616, USA; [email protected] 3 Department of Mechanical Engineering, Universidad de los Andes, Bogota 111711, Colombia; [email protected] * Correspondence: [email protected] Received: 21 February 2020; Accepted: 20 March 2020; Published: 2 April 2020 Abstract: Energy regeneration systems are a key factor for improving energy efficiency in electrohydraulic machinery. This paper is focused on the study of electric energy storage systems (EESS) and hydraulic energy storage systems (HESS) for energy regeneration applications. Two test benches were designed and implemented to compare the performance of the systems under similar operating conditions. The electrical system was configured with a set of ultracapacitors, and the hydraulic system used a hydraulic accumulator. Both systems were designed to have the same energy storage capacity. Charge and discharge cycle experiments were performed for the two systems in order to compare their power density, energy density, cost, and efficiency. According to the experimentally obtained results, the power density in the hydraulic accumulator was 21.7% higher when compared with the ultracapacitors. Moreover, the cost/power ($/Watt) ratio in the hydraulic accumulator was 2.9 times smaller than a set of ultracapacitors of the same energy storage capacity. -
CE 378 Water Resources Engineering Term: Spring 2013 CE 378 Water Resources Engineering (3)
CE 378 Water Resources Engineering Term: Spring 2013 CE 378 Water Resources Engineering (3). Three hours 1:00 to 1:50 M, W and F, room 254 Hardaway Hall Instructor: Robert E. Pitt, Ph.D., P.E., BCEE, D. WRE Office: 1005A Bevill Office Hours: M and W 3 to 4 pm; when in town, or by appointment; by email anytime Phone: (205) 348-2684 e-mail: [email protected] (UA) or [email protected] (home) TA: Redahegn Sileshi ([email protected]) Catalog Mechanics of steady and unsteady flow in closed and open conduits, hydrology; water Description supply and wastewater disposal. Prerequisites Dynamics (AEM 264) and Fluid Mechanics (AEM 311); or Fluid Flow Operations (ChE 304) Co requisites none Course This course is directed to applications of fluid mechanics, hydrology, and hydraulics as Objectives they apply to the discipline of water resources engineering. Topics covered include flow in closed conduits and open channels, hydraulic machinery (pumps), and surface water hydrology and statistical methods. Student projects will be directed to simple designs of sustainable urban water-use and water-control systems. At the successful completion of this course, the student will be able to apply the fundamental principles of conservation of mass, momentum and energy to the practical solution of both analysis and design problems in closed and open conduit flows, and will understand the performance characteristics of pumps. The student will also be introduced to hydrology and to methods of quantification of hydrologic uncertainty. Course Website Located at: http://unix.eng.ua.edu/~rpitt/Class/Water%20Resources %20Engineering/WREMainPage.htm Required Texts There are no required texts for the class, as much of the reference material is readily and References available from several sources, including the class website noted above. -
Design and Evaluation of Hydraulic Suspension Without Spring In
CORE Metadata, citation and similar papers at core.ac.uk Provided by MAT Journals Journal of Mechanical and Mechanics Engineering Volume 4 Issue 2 Design And Evaluation Of Hydraulic Suspension Without Spring In LMV K.Ravishankar1, S.Anandakumar2 1PG Student, Dept of MechanicalEngg, ShreeVenkateshwara HI Tech Engineering College, Gobichettipalayam, Tamilnadu 2Assistant professor, Dept of Mechanical Engg, Shree Venkateshwara HI Tech Engineering College, Gobichettipalayam, Tamilnadu [email protected], [email protected] Abstract - The suspension is the backbone of all Apart from that safe driving plays an important vehicles its principle function is to safely carry the role in automobile. When the level of maximum load for all designed operating conditions. suspension reduces it leads to increase in noise. This project defines design and evaluation of By using hydraulic suspension we can reduce hydraulic suspension without spring in LMV. Shock the vibration and also improve riding comfort. reduction is an important characteristic which reduces Auto manufacturers are still trying to catch up with the vibration of the vehicle and carries the load safely. the combination of features offered by this hydraulic In this project a hydraulic suspension is used to suspension system, typically by adding layers of produce hydraulic pressure that negates external complexity to an ordinary steel spring mechanical forces acting on the vehicle. As a result, the system. suspension system is able to control vehicle movement freely and continuously. This control ACTIVE SUSPENSION capability makes it possible to provide higher levels of ride comfort and vehicle dynamics which obtained A. INTRODUCTION OF ACTIVE SUSPENSION with conventional suspension systems. The design A suspension is self-propelledequipmentit controls was done using CREO PARAMETRIC 2.0 and the the upright movement of all the wheels via an model is imported to Proficy / SCADA (IFix version onboard system reasonably than the effort being 4.0) for evaluation. -
University of Macau Undergraduate Civil Engineering Programme
University of Macau Undergraduate Civil Engineering Programme Coordinating Unit: Department of Civil and Environmental Engineering, Faculty of Science and Technology Supporting Unit(s): Nil Course Code: CIVL341 Year of Study: 3 Course Title: Hydraulics II Compulsory/Elective: Compulsory Course Prerequisites: CIVL230 Hydraulics I Prerequisite Entry level fluid mechanics Knowledge: Duration: One semester Credit Units: 4 Class/Laboratory Three hours of lecture and one hour of tutorial and one hour of laboratory per week. Schedule: Laboratory/Software Hydraulics Laboratory Usage: Application of the basic laws of fluid mechanics to hydraulic problems. Analysis of simple and multiple steady pipe flows: branching pipes, pipes in series and parallel, and pipe network; flow measurement in pipe. Unsteady flow in pressure conduits: establishment of steady flow and water hammer. Analysis of pumps and turbines. Pump and system Course Description: characteristics. Steady open channel flow: energy and momentum principles; critical and uniform flow development and their computation; best hydraulic section; gradually varied flow and its profile computation; flow measurement in open channel. Introduction to Hydrology. 1. Apply fundamental principles of fluid mechanics for the solution of practical civil engineering problems of water conveyance in pipes, pipe networks, and open channels. 2. Describe the operating characteristics of hydraulic machinery (pumps and turbines), and the factors affecting their operation and specifications, as well as their operation in Course Objectives: a system. 3. Describe the principles controlling open channel flows including critical, uniform and gradually varied flows. Design of channel section for uniform flow. 4. Introduce some basic topics of engineering hydrology. Upon completion of this course, students should be able to: 1. -
The Hydraulic-Machinery Laboratory at the California Institute of Technology
(Reprinted from the A.S.M.E. Tramactionll for NO'Dember, 1958) The Hydraulic-Machinery Laboratory at the California Institute of Technology BY R. T. KNAPP,' PASADENA, CALIF. Tbis paper gives a description of the arrangement, heads of from 146 ft for the lowest to 444 ft for the highest. equipment, and instrumentation of the hydraulic-ma Very little precedent was available for plants of such size, to chinery laboratory at the California Institute of Tech assist the engineers of the District in answering questions con nology. This laboratory was designed essentially to work cerning maximum permissible head per stage, single- or double with problems involving high heads, high speeds, and suction pumps, optimum speeds, attainable efficiencies, and moderately large powers and rates of flow. The instru desirable operating characteristics. It was felt that a properly ments and equipment permit both speed and precision equipped laboratory would be of great assistance in studying in testing, an overall accuracy ofO.l per cent being attain such problems, and would amply justify the expense required, able. For the past two years the laboratory has been u sed both by savings expected and by the insurance of obtaining the for the study of pumping problems of the Colorado River most satisfactory type of equipment. aqueduct, a project which will have pumps totaling 350,000 The responsibility of supervising the design, construction, and hp when completed. operation of the laboratory was placed in the hands of a group consisting of Professors Th. von Karman, R . L. Daugherty, and HE Hydraulic-Machinery Laboratory is a joint enterprise R .