New Technology in Blade Design
Total Page:16
File Type:pdf, Size:1020Kb
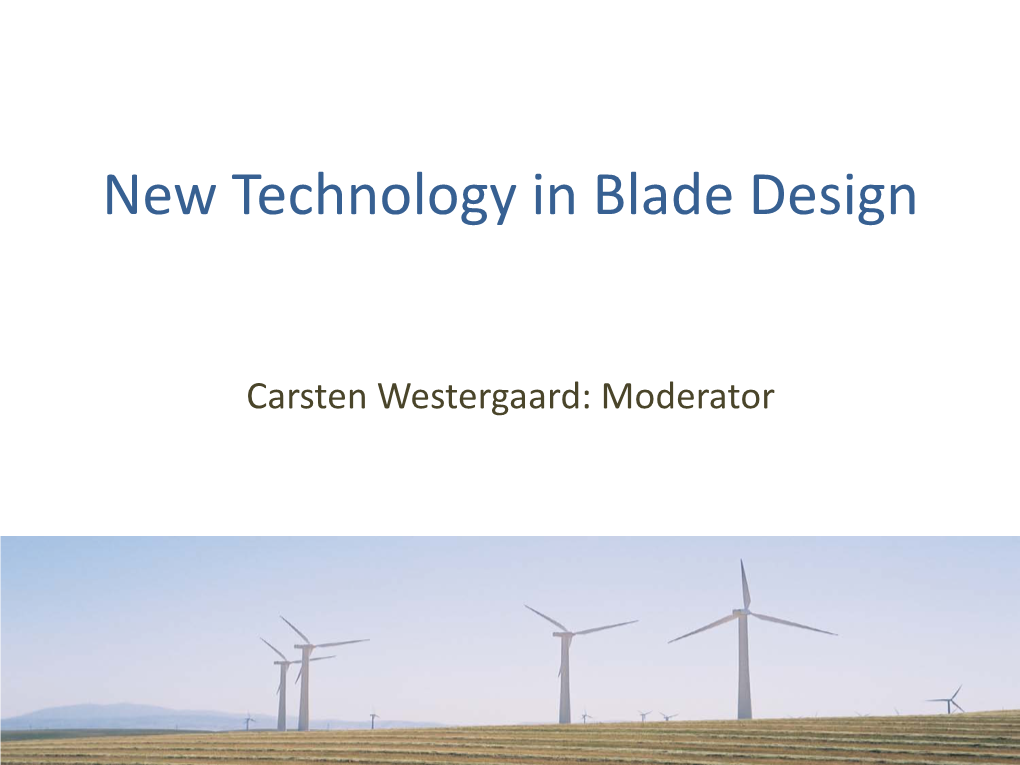
Load more
Recommended publications
-
The Impact of Pitch-To-Stall and Pitch-To-Feather Control on the Structural Loads and the Pitch Mechanism of a Wind Turbine
energies Article The Impact of Pitch-To-Stall and Pitch-To-Feather Control on the Structural Loads and the Pitch Mechanism of a Wind Turbine Arash E. Samani 1,2,* , Jeroen D. M. De Kooning 1,3 , Nezmin Kayedpour 1,2 , Narender Singh 1,2 and Lieven Vandevelde 1,2 1 Department of Electromechanical, Systems and Metal Engineering, Ghent University, Tech Lane Ghent Science Park-Campus A, Technologiepark Zwijnaarde 131, B-9052 Ghent, Belgium; [email protected] (J.D.M.D.K.); [email protected] (N.K.); [email protected] (N.S.); [email protected] (L.V.) 2 FlandersMake@UGent—corelab EEDT-DC, B-9052 Ghent, Belgium 3 FlandersMake@UGent—corelab EEDT-MP, B-9052 Ghent, Belgium * Correspondence: [email protected] Received: 10 July 2020; Accepted: 22 August 2020; Published: 1 September 2020 Abstract: This article investigates the impact of the pitch-to-stall and pitch-to-feather control concepts on horizontal axis wind turbines (HAWTs) with different blade designs. Pitch-to-feather control is widely used to limit the power output of wind turbines in high wind speed conditions. However, stall control has not been taken forward in the industry because of the low predictability of stalled rotor aerodynamics. Despite this drawback, this article investigates the possible advantages of this control concept when compared to pitch-to-feather control with an emphasis on the control performance and its impact on the pitch mechanism and structural loads. In this study, three HAWTs with different blade designs, i.e., untwisted, stall-regulated, and pitch-regulated blades, are investigated. -
Technical, Environmental and Social Requirements of the Future Wind Turbines and Lifetime Extension WP1, Task 1.1
Ref. Ares(2020)3411163 - 30/06/2020 Deliverable 1.1: Technical, environmental and social requirements of the future wind turbines and lifetime extension WP1, Task 1.1 Date of document 30/06/2020 (M 6) Deliverable Version: D1.1, V1.0 Dissemination Level: PU1 Mireia Olave, Iker Urresti, Raquel Hidalgo, Haritz Zabala, Author(s): Mikel Neve (IKERLAN) Wai Chung Lam, Sofie De Regel, Veronique Van Hoof, Karolien Peeters, Katrien Boonen, Carolin Spirinckx (VITO) Mikko Järvinen, Henna Haka (MOVENTAS) Contributor(s): Aitor Zurutuza, Arkaitz Lopez (LAULAGUN) Marcos Suarez, Jone Irigoyen (Basque Energy Cluster) Helena Ronkainen (VTT) 1 PU = Public PP = Restricted to other programme participants (including the Commission Services) RE = Restricted to a group specified by the consortium (including the Commission Services) CO = Confidential, only for members of the consortium (including the Commission Services) This project has received funding from the European Union’s Horizon 2020 research and innovation programme under grant agreement No 851245. 1 D1.1 – Technical, environmental and social requirements of the future wind turbines and lifetime extension This project has received funding from the European Union’s Horizon 2020 research and innovation programme under grant agreement No 851245. 2 D1.1 – Technical, environmental and social requirements of the future wind turbines and lifetime extension Project Acronym INNTERESTING Innovative Future-Proof Testing Methods for Reliable Critical Project Title Components in Wind Turbines Project Coordinator Mireia Olave (IKERLAN) [email protected] Project Duration 01/01/2020 – 01/01/2022 (36 Months) Deliverable No. D1.1 Technical, environmental and social requirements of the future wind turbines and lifetime extension Diss. -
Offshore Technology Yearbook
Offshore Technology Yearbook 2 O19 Generation V: power for generations Since we released our fi rst offshore direct drive turbines, we have been driven to offer our customers the best possible offshore solutions while maintaining low risk. Our SG 10.0-193 DD offshore wind turbine does this by integrating the combined knowledge of almost 30 years of industry experience. With 94 m long blades and a 10 MW capacity, it generates ~30 % more energy per year compared to its predecessor. So that together, we can provide power for generations. www.siemensgamesa.com 2 O19 20 June 2019 03 elcome to reNEWS Offshore Technology are also becoming more capable and the scope of Yearbook 2019, the fourth edition of contracts more advanced as the industry seeks to Wour comprehensive reference for the drive down costs ever further. hardware and assets required to deliver an As the growth of the offshore wind industry offshore wind farm. continues apace, so does OTY. Building on previous The offshore wind industry is undergoing growth OTYs, this 100-page edition includes a section on in every aspect of the sector and that is reflected in crew transfer vessel operators, which play a vital this latest edition of OTY. Turbines and foundations role in servicing the industry. are getting physically larger and so are the vessels As these pages document, CTVs and their used to install and service them. operators are evolving to meet the changing needs The growing geographical spread of the sector of the offshore wind development community. So is leading to new players in the fabrication space too are suppliers of installation vessels, cable-lay springing up and players in other markets entering vessels, turbines and other components. -
Expertise in Bearing Technology and Service for Wind Turbines the Company
Expertise in Bearing Technology and Service for Wind Turbines The Company Expertise through knowledge and experience FAG Kugelfischer is the pioneer of the For over 30 years, INA and FAG have Monitoring systems, lubricants, mounting rolling bearing industry. In 1883, Friedrich designed and produced bearing arrange- and maintenance tools. In this way, Fischer designed a ball mill that was the ments for wind turbines. Within Schaeffler Schaeffler Group Industrial helps to historic start of the rolling bearing industry. Group Industrial, the specialists from achieve low operating costs for wind INA began its path to success in 1949 the business unit “Wind power” work turbines. with the development of the needle closely with designers, manufacturers Core skills roller and cage assembly by Dr. Georg and operators of wind turbines. This Schaeffler – a stroke of genius that has resulted in unbeatable know-how: • Wide range of application-specific helped the needle roller bearing to make as early as the concept phase, detailed bearing designs, intensive ongoing its breakthrough in industry. Schaeffler attention is paid to customer require- product development Group Industrial with its two strong ments. Bearing selection and documen- • Soundly-based consultancy by brands, INA and FAG, today has not only tation are backed up by sophisticated experienced engineers a high performance portfolio in rolling calculation methods. Products developed • Optimum application of customer bearings but also, through joint research to a mature technical level -
Aeroelastic Simulation of Wind Turbine Dynamics
Aeroelastic Simulation of Wind Turbine Dynamics by Anders Ahlstr¨om April 2005 Doctoral Thesis from Royal Institute of Technology Department of Mechanics SE-100 44 Stockholm, Sweden Akademisk avhandling som med tillst˚and av Kungliga Tekniska h¨ogskolan i Stock- holm framl¨agges till offentlig granskning f¨or avl¨aggande av teknologie doktorsexamen fredagen den 8:e april 2005 kl 10.00 i sal M3, Kungliga Tekniska h¨ogskolan, Valhalla- v¨agen 79, Stockholm. c Anders Ahlstr¨om 2005 Abstract The work in this thesis deals with the development of an aeroelastic simulation tool for horizontal axis wind turbine applications. Horizontal axis wind turbines can experience significant time varying aerodynamic loads, potentially causing adverse effects on structures, mechanical components, and power production. The needs for computational and experimental procedures for investigating aeroelastic stability and dynamic response have increased as wind turbines become lighter and more flexible. A finite element model for simulation of the dynamic response of horizontal axis wind turbines has been developed. The developed model uses the commercial finite element system MSC.Marc, focused on nonlinear design and analysis, to predict the structural response. The aerodynamic model, used to transform the wind flow field to loads on the blades, is a Blade-Element/Momentum model. The aerody- namic code is developed by The Swedish Defence Research Agency (FOI, previously named FFA) and is a state-of-the-art code incorporating a number of extensions to the Blade-Element/Momentum formulation. The software SOSIS-W, developed by Teknikgruppen AB was used to generate wind time series for modelling different wind conditions. -
Investigation of Wind Mill Yaw Bearing Using E-Glass Material
ISSN(Online): 2319-8753 ISSN (Print): 2347-6710 International Journal of Innovative Research in Science, Engineering and Technology (An ISO 3297: 2007 Certified Organization) Website: www.ijirset.com Vol. 6, Issue 9, September 2017 Investigation of Wind Mill Yaw Bearing Using E-Glass Material Maharshi Singh, L.Natrayan, M.Senthil Kumar. School of Mechanical and Building Sciences, VIT University, Chennai, Tamilnadu, India. ABSTRACT: Wind-turbine yaw drive endures to display a high rate of rapid failure in meanness of use of the best in current design performs. Subsequently yaw bearing is one of the priciest components of a yaw drive in wind turbine, higher-than-expected failure tariffsgrowth cost of energy. Supreme of the difficulties in wind-turbine yaw drive appear to discharge from bearings. Yaw bearing is located between the Tower and Nacelle portion of the Wind Turbine and slews shadow the wind way.The modelling of yaw bearing is done using Pro-E and fatigue life and static loading capacity are investigated by ANSYS. There is a gear positioned on the outer ring of the bearing and the Yaw Drive Motor is mated with this gear. The gear controls the angle control relative to the direction of the wind. This bearing gathering consists of an Outer ring, Inner ring, balls, and seal. Surviving yaw bearing made up of Carbon and Low Alloyed steels, High Alloyed Steels and Super Alloys. In this yaw bearing constitutes fairly accurate 25 tons of weight. So we categorical to diminish the weight of yaw bearings using composite materials. KEYWORDS:Yaw Bearing,Composite Material, Ansys, Fatigue Life, Yaw Drive, Static Load. -
Technical Documentation Wind Turbine Generator Systems 3.6-137 - 50/60 Hz
GE Renewable Energy -Original- Technical Documentation Wind Turbine Generator Systems 3.6-137 - 50/60 Hz Technical Description and Data imagination at work © 2017 General Electric Company. All rights reserved. GE Renewable Energy -Original- www.gepower.com Visit us at https://renewables.gepower.com Copyright and patent rights All documents are copyrighted within the meaning of the Copyright Act. We reserve all rights for the exercise of commercial patent rights. 2017 General Electric Company. All rights reserved. This document is public. GE and are trademarks and service marks of General Electric Company. Other company or product names mentioned in this document may be trademarks or registered trademarks of their respective companies. imagination at work General_Description_3.6-DFIG-137-xxHz_3MW_EN_r03.docx. GE Renewable Energy -Original- Technical Description and Data Table of Contents 1 Introduction ..................................................................................................................................................................................................... 5 2 Technical Description of the Wind Turbine and Major Components ................................................................................... 5 2.1 Rotor .......................................................................................................................................................................................................... 6 2.2 Blades ...................................................................................................................................................................................................... -
A New Era for Wind Power in the United States
Chapter 4 Wind Vision: A New Era for Wind Power in the United States 1 Table of Contents Message from the Director ..................................................................................................................................... xiii Acronyms .......................................................................................................................................................................xv Executive Summary: Overview ...........................................................................................................................xxiii Contents of Table Executive Summary: Key Chapter Findings ..................................................................................................xxvii ES.1 Introduction ........................................................................................................................................................................xxvii ES.1.1 Project Perspective and Approach ......................................................................................................................xxvii ES.1.2 Understanding the Future Potential for Wind Power ....................................................................................xxix ES.1.3 Defining a Credible Scenario to Calculate Costs, Benefits, and Other Impacts .....................................xxxi ES.2 State of the Wind Industry: Recent Progress, Status and Emerging Trends ................................................xxxiv ES.2.1 Wind Power Markets and Economics ................................................................................................................xxxv -
Advanced Wind Turbine Program Next Generation Turbine Development
A national laboratory of the U.S. Department of Energy Office of Energy Efficiency & Renewable Energy National Renewable Energy Laboratory Innovation for Our Energy Future Advanced Wind Turbine Subcontract Report NREL/SR-500-38752 Program Next Generation May 2006 Turbine Development Project June 17, 1997 — April 30, 2005 GE Wind Energy, LLC Tehachapi, California NREL is operated by Midwest Research Institute ● Battelle Contract No. DE-AC36-99-GO10337 Advanced Wind Turbine Subcontract Report NREL/SR-500-38752 Program Next Generation May 2006 Turbine Development Project June 17, 1997 — April 30, 2005 GE Wind Energy, LLC Tehachapi, California NREL Technical Monitor: S. Schreck Prepared under Subcontract No. ZAM-7-13320-26 National Renewable Energy Laboratory 1617 Cole Boulevard, Golden, Colorado 80401-3393 303-275-3000 • www.nrel.gov Operated for the U.S. Department of Energy Office of Energy Efficiency and Renewable Energy by Midwest Research Institute • Battelle Contract No. DE-AC36-99-GO10337 NOTICE This report was prepared as an account of work sponsored by an agency of the United States government. Neither the United States government nor any agency thereof, nor any of their employees, makes any warranty, express or implied, or assumes any legal liability or responsibility for the accuracy, completeness, or usefulness of any information, apparatus, product, or process disclosed, or represents that its use would not infringe privately owned rights. Reference herein to any specific commercial product, process, or service by trade name, trademark, manufacturer, or otherwise does not necessarily constitute or imply its endorsement, recommendation, or favoring by the United States government or any agency thereof. -
Blade Bearing Spares
IMO - Spares you can trust! 2-row 4-point contact ball pitch bearing often used as spare part in original configuration in cases of • inadequate lubrication • fair wear and tear • raceway corrosion (ingress of water) • stress corrosion (cracking rings through bolt holes) • component failures (broken balls, core crushing, surface fatigue & spalling, false brinelling) • grease leakage IMO pitch bearings spares include design and quality improvements to address these known failure modes to ensure it lasts longer than the original. T-Solid – a patented 3-raceway/3-ring design with load independent contact angle. Strongly recommended in cases of prematurely failing pitch bearings due to • raceway edge loading (contact ellipse truncation, edge break) • cage wear and fracture • heavily deforming raceways (inadequate system stiffness) • jamming balls up to bearing lock-up • inadequate strength or structural durability (cracks through filling plug holes, or near stiffening or lifting plates) Provides for the same form, fit & function. More information: www.t-solid.de Bearing features for long service life: Benchmark IMO seal rings made from 42CrMo4QT patented seal with barbed hook (no pull-out) proven U.S. and EU quality Balls tested up to 2bars (dynamic) and 5bars (static) corrosion protection to the highest level C5 no grease leakage salt spray tested bolt hole corrosion no contamination ingress (dust, moisture) protection field tested on turbines with direct seal non-corroding seal running surfaces exposure to sun and weather induction -
Novel Distributed Lubrication System to Improve the Excessive Wear in Wind Turbine Yaw and Pitch Gears
ADVERTIMENT . La consulta d’aquesta tesi queda condicionada a l’acceptació de les següents condicions d'ús: La difusió d’aquesta tesi per mitjà del servei TDX ( www.tesisenxarxa.net ) ha estat autoritzada pels titulars dels drets de propietat intel·lectual únicament per a usos privats emmarcats en activitats d’investigació i docència. No s’autoritza la seva reproducció amb finalitats de lucre ni la seva difusió i posada a disposició des d’un lloc aliè al servei TDX. No s’autoritza la presentació del seu contingut en una finestra o marc aliè a TDX (framing). Aquesta reserva de drets afecta tant al resum de presentació de la tesi com als seus continguts. En la utilització o cita de parts de la tesi és obligat indicar el nom de la persona autora. ADVERTENCIA . La consulta de esta tesis queda condicionada a la aceptación de las siguientes condiciones de uso: La difusión de esta tesis por medio del servicio TDR ( www.tesisenred.net ) ha sido autorizada por los titulares de los derechos de propiedad intelectual únicamente para usos privados enmarcados en actividades de investigación y docencia. No se autoriza su reproducción con finalidades de lucro ni su difusión y puesta a disposición desde un sitio ajeno al servicio TDR. No se autoriza la presentación de su contenido en una ventana o marco ajeno a TDR (framing). Esta reserva de derechos afecta tanto al resumen de presentación de la tesis como a sus contenidos. En la utilización o cita de partes de la tesis es obligado indicar el nombre de la persona autora. -
Wind Turbine Design Guideline DG03: Yaw and Pitch Rolling DE-AC36-08-GO28308 Bearing Life 5B
Technical Report Wind Turbine Design Guideline NREL/TP-500-42362 DG03: Yaw and Pitch Rolling December 2009 Bearing Life T. Harris J.H. Rumbarger C.P. Butterfield Technical Report Wind Turbine Design Guideline NREL/TP-500-42362 DG03: Yaw and Pitch Rolling December 2009 Bearing Life T. Harris J.H. Rumbarger C.P. Butterfield Prepared under Task No. WE101131 National Renewable Energy Laboratory 1617 Cole Boulevard, Golden, Colorado 80401-3393 303-275-3000 • www.nrel.gov NREL is a national laboratory of the U.S. Department of Energy Office of Energy Efficiency and Renewable Energy Operated by the Alliance for Sustainable Energy, LLC Contract No. DE-AC36-08-GO28308 NOTICE This report was prepared as an account of work sponsored by an agency of the United States government. Neither the United States government nor any agency thereof, nor any of their employees, makes any warranty, express or implied, or assumes any legal liability or responsibility for the accuracy, completeness, or usefulness of any information, apparatus, product, or process disclosed, or represents that its use would not infringe privately owned rights. Reference herein to any specific commercial product, process, or service by trade name, trademark, manufacturer, or otherwise does not necessarily constitute or imply its endorsement, recommendation, or favoring by the United States government or any agency thereof. The views and opinions of authors expressed herein do not necessarily state or reflect those of the United States government or any agency thereof. Available electronically at http://www.osti.gov/bridge Available for a processing fee to U.S. Department of Energy and its contractors, in paper, from: U.S.