Vertical Farming: a Summary of Approaches to Growing Skywards by Beacham, A.M., Vickers, L.H
Total Page:16
File Type:pdf, Size:1020Kb
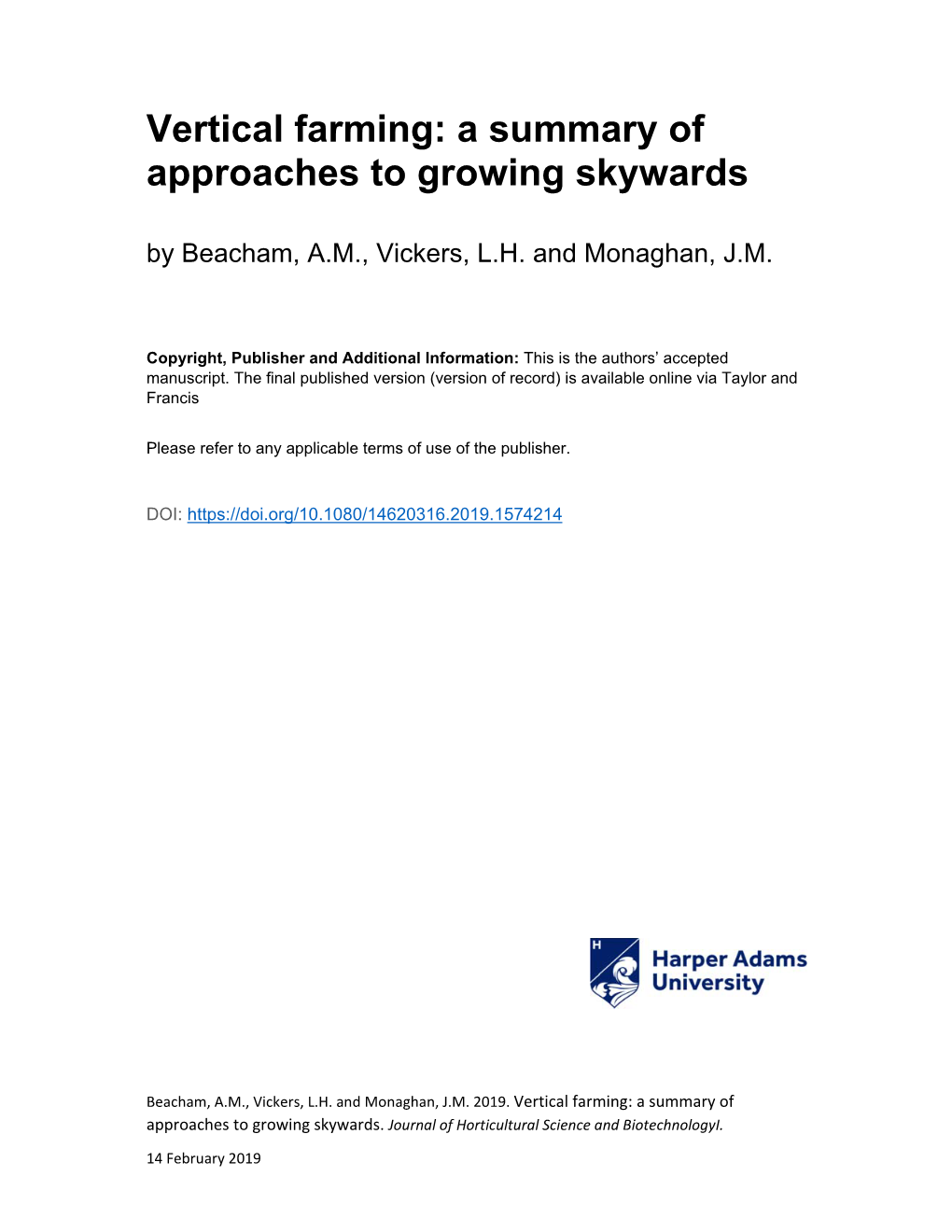
Load more
Recommended publications
-
Linda Sierra
Jason D. Licamele, Ph.D. P.O. Box 25035 / Scottsdale, AZ 85255 [email protected] Agriculture & Biological Systems Engineer Keywords: biotechnology, agriculture, aquaculture, fisheries, plant production, natural products, bioenergy, bioprocessing, ecosystems, food science, greenhouse engineering, horticulture, hydroponics, fisheries, algae, environment, natural resources, water resources, bioprospecting, sustainability - Biological systems engineer, marine biologist, ecologist, environmental scientist, and biotechnologist with commercial operations and research experience leading, designing, developing, executing, and managing projects. - Innovative applied scientist and engineer with a multitude of skills, a patent portfolio, over 20 years of commercial experience in the aquaculture, agriculture, food, and bioenergy industries with a focus on environmental sustainability and resource management. - Experienced entrepreneur and consultant effectively developing global relationships with business, legal, non- governmental organizations, academic, and government organizations via strong communication, interpersonal skills, leadership qualities, and dedication to mission. - Skilled in project design, project management, experimental design, data management, and data translation with a unique ability to critically analyze and effectively communicate information to all levels of audiences. - Professional scientist and engineer with experience in business, production, research and development, intellectual property development, technology -
Trends in Aquaponics
Trends in Aquaponics Chris Hartleb University of Wisconsin-Stevens Point Northern Aquaculture Demonstration Facility Aquaponics Innovation Center Aquaponics • Integrated & soilless • Continuous year-round • Free of biocides production • Conservative use of water, space & • Meets socio-economic challenges labor – Urban, peri-urban, rural • Produces both vegetable & protein crop – Locavore movement Aquaponic Systems UVI Design Fish tanks Raft tank Water pump Clarifier (solids filter) Degassing tank Mineralization tanks & biofilter Air pump Plant Production Systems • Raft (Revised agriculture float technology) – Deep water culture • Large volume water • Root aeration • Nutrient uptake: High • Media based – Biofiltration in media – Clogging & cleaning present – Nutrient uptake: High • Nutrient film technique – Low volume water – Less system stability – Nutrient uptake: Low Modified Designs • Vertical farming – Living walls – Vertical • Robotics • Complete artificial light Who’s Growing using Aquaponics? Love, Fry, Li, Hill, Genello, Simmons & Thompson. 2015. Commercial aquaponics production and profitability: Findings from an international survey. Aquaculture 435:67-74. How Many is That? • Limited survey response • Most likely underestimated number and location Types of Aquaponics • Scalable: – Hobby and Home food production – Farmers market food production – Social & Community systems – Commercial food production – Education – Research Aquaculture North America January/February 2018 • Trends driving the seafood sector – Climate change impact -
Review Article Suitable Substrate for Optimal Crop Growth Under
Journal of Scientific Agriculture 2018,2: 62-65 doi: 10.25081/jsa.2018.v2.860 http://updatepublishing.com/journals/index.php/jsa ISSN: 2184-0261 R E VIEW A RTICLE SUITABLE SUBSTRATE FOR OPTIMAL CROP GROWTH UNDER PROTECTED FARMS–AN ASSESSMENT AMARESH SARKAR*, MRINMOY MAJUMDER Department of Civil Engineering, National Institute of Technology, Agartala, PIN-799046, Tripura, India ABSTRACT An attempt has been made in this paper, to review crop growing substrates for protected farms. Optimal substrate type and volume for different crops cultivar is different. Substrate selection is a critical factor for optimal production of high-quality vegetables. Crop root orientation and depth determine the type and volume of substrate required which is very important for optimal crop growth and maximum profit. Growing crops on substrates in protected skyscrapers would not only mitigate the need for more land, it produces growing space vertically. Keywords: Substrate, Nutrient solution, Controlled environment agriculture INTRODUCTION structure can also be constructed on non-cultivable soil and urban roof-tops [21]. The amount of solar radiation, Food need is increasing globally as the inhabitants are which provides the energy to evaporate moisture from the increasing. Protected farming is a popular technique for substrate and the plant, is the major factor. Other growing vegetables all seasons regardless of location and important factors include air temperature, wind speed, and climate. The most innovative technology for plants humidity level [11]. The plant canopy size and shape growing in greenhouses is growing plants in mineral influences light absorption, reflection, and the rate at substrates such as rock wool, vermiculite, perlite, zeolite, which water evaporates from the soil. -
LED Lighting Systems for Horticulture: Business Growth and Global Distribution
sustainability Review LED Lighting Systems for Horticulture: Business Growth and Global Distribution Ivan Paucek 1, Elisa Appolloni 1, Giuseppina Pennisi 1,* , Stefania Quaini 2, Giorgio Gianquinto 1 and Francesco Orsini 1 1 DISTAL—Department of Agricultural and Food Sciences and Technologies, Alma Mater Studiorum—University of Bologna, 40127 Bologna, Italy; [email protected] (I.P.); [email protected] (E.A.); [email protected] (G.G.); [email protected] (F.O.) 2 FEEM—Foundation Eni Enrico Mattei, 20123 Milano, Italy; [email protected] * Correspondence: [email protected] Received: 4 August 2020; Accepted: 5 September 2020; Published: 11 September 2020 Abstract: In recent years, research on light emitting diodes (LEDs) has highlighted their great potential as a lighting system for plant growth, development and metabolism control. The suitability of LED devices for plant cultivation has turned the technology into a main component in controlled or closed plant-growing environments, experiencing an extremely fast development of horticulture LED metrics. In this context, the present study aims to provide an insight into the current global horticulture LED industry and the present features and potentialities for LEDs’ applications. An updated review of this industry has been integrated through a database compilation of 301 manufacturers and 1473 LED lighting systems for plant growth. The research identifies Europe (40%) and North America (29%) as the main regions for production. Additionally, the current LED luminaires’ lifespans show 10 and 30% losses of light output after 45,000 and 60,000 working hours on average, respectively, while the 1 vast majority of worldwide LED lighting systems present efficacy values ranging from 2 to 3 µmol J− (70%). -
*Ponics (Why Google Is Suspects That My Kids Are Drug Dealers and Why We’Re Looking for a Food-Safe Fencepost)
*ponics (Why Google is suspects that my kids are drug dealers and why we’re looking for a food-safe fencepost) Roger Meike (pronounced “Mike,” FYI) PARC - but not what this project is about Saturday, July 20, 13 Roger Meike • Currently working at PARC • Technologist/Maker/Entrepreneur... Dork! • ..and I have the ham radio license to prove it! Saturday, July 20, 13 keyword: spaughts Saturday, July 20, 13 The challenge • Advice from Mike: Pick a topic that interests you • I now work on a software project at PARC, so I don’t have HW to talk about • I’m busy so I don’t do as much fun stuff at home as I would like • Everything I do in hardware these days is more sketchy than a sketch Saturday, July 20, 13 Slow Jam Sketch • If you use really slow material, is it still sketching? • i.e. working with biological and chemical constraints • The story: Why Google is pretty sure my kids are drug dealers and why I’m looking for a food-safe fencepost • Let the children lead the way • And so the story begins... Saturday, July 20, 13 Items of Interest KE6HFO KE6HFP Saturday, July 20, 13 Saturday, July 20, 13 Saturday, July 20, 13 Saturday, July 20, 13 Saturday, July 20, 13 Items of Interest KJ6KEB KI6TGN KE6HFO KE6HFP Saturday, July 20, 13 Saturday, July 20, 13 Hydroponics System Reservoir with pump and float switch Saturday, July 20, 13 Types of Hydroponic Systems • Ebb and flow system o Water level is fluctuated • Wick System o Simplest System • Drip system or Dutch Bucket o Bucket with a drip system type water supply • Deep water culture (DWC) o Roots -
Vertical Farming Sustainability and Urban Implications
Master thesis in Sustainable Development 2018/32 Examensarbete i Hållbar utveckling Vertical Farming Sustainability and Urban Implications Daniela Garcia-Caro Briceño DEPARTMENT OF EARTH SCIENCES INSTITUTIONEN FÖR GEOVETENSKAPER Master thesis in Sustainable Development 2018/32 Examensarbete i Hållbar utveckling Vertical Farming Sustainability and Urban Implications Daniela Garcia-Caro Briceño Supervisor: Cecilia Mark-Herbert Evaluator: Daniel Bergquist Copyright © Daniela Garcia-Caro Briceño, Published at Department of Earth Sciences, Uppsala University (www.geo.uu.se), Uppsala, 2018 Content 1. INTRODUCTION .............................................................................................................................. 1 1.1 PROBLEM FORMULATION ............................................................................................................... 1 1.2 AIM ................................................................................................................................................. 2 1.3 OUTLINE ......................................................................................................................................... 3 2. METHODS ......................................................................................................................................... 4 2.1 RESEARCH APPROACH AND DESIGN ............................................................................................... 4 2.2 RESEARCH DELIMITATIONS ........................................................................................................... -
Aquaponic Growers
TOP TEN MISTAKES MADE BY aquaponic growers BRIGHT Copyright © 2015 TABLE OF CONTENTS IS THIS E-BOOK RIGHT FOR ME? ....................................3 ABOUT THE AUTHOR ......................................................4 ABOUT BRIGHT AGROTECH ..........................................5 THE TOP 10 MISTAKES: 1) UNUSABLE OR HARD-TO-USE FARMS ..........................................6 2) INADEQUATE CIRCULATION/SOLIDS REMOVAL/OR BSA .........7 3) POOR QUALITY WATER ................................................................9 4) UNDERESTIMATING PRODUCTION AND SYSTEM COSTS .........10 5) BIOLOGICAL VIABILITY VS. ECONOMIC VIABILITY....................11 6) CHOOSING THE WRONG CROPS..............................................12 7) SYSTEMS THAT HAVE POOR TRACK RECORDS..........................14 8) LACK OF PEST CONTROL STRATEGY..........................................16 9) GROWERS GET GREEDY .............................................................18 10) FAILURE TO APPROACH MARKETS CREATIVELY......................19 CONCLUSION.................................................................21 2 Back to Top IS THIS EBOOK RIGHT FOR ME? The learning curve of aquaponics is littered with the remains of failed aquaponic ventures and millions of dollars in lost investments. This e-book acts as a guide for beginning aquaponic growers who are interested in operating successful aquaponic systems- whether commercial or hobby systems. This guide will detail 10 of the obstacles which I have encountered again and again on this learning curve -
Development of Hydroponic Production Systems for Strawberry Production
Development of Hydroponic Production Systems for Strawberry Production Principle Investigators and Cooperators: Principal Investigators: Lead PI Co-PI Dr. Michael Timmons Dr. Neil Mattson Professor, Cornell University Associate Professor, Cornell University Department of Biological & Department of Horticulture Environmental Engineering 49D Plant Science, Ithaca NY 14853 302 Riley-Robb Hall, Ithaca, NY 14853 (607) 255-0621 (607) 255-1630 [email protected] [email protected] Project Manager: Mr. Matthew Moghaddam Department of Horticulture, Cornell University [email protected] Background and Justification: New York consumers have limited access to fresh, high quality, locally grown produce at competitive pricing with imported product. It is well known that consumers place an added value on locally produced products. This then provides an opportunity for the small-scale producer and that opportunity can be partially addressed through aquaponics and product diversification. Strawberries are a highly favored fruit, yet almost all strawberries are imported into the New York State markets. NY ranked eighth in strawberry production in 2014 with 3.2 million pounds, but falls far behind the top five states (CA 2758 million lbs. per year, FL 207 M, OR 15, NC 15, WA 10, MI 4.5, WI 3.8, PA 3.3 M) (USDA, 2014). This domestic production comes from 56,000 acres of which only 22 acres are from greenhouse operations. This is in sharp contrast to Japan where 12,990 acres are greenhouse grown from a total country production of 14,876 acres. Historical production methods (field grown) need not prevent adaptation of new methods (greenhouse) as demonstrated in Mexico that had no history of strawberry production. -
The Vertical Farm: a Review of Developments and Implications for the Vertical City
buildings Review The Vertical Farm: A Review of Developments and Implications for the Vertical City Kheir Al-Kodmany Department of Urban Planning and Policy, College of Urban Planning and Public Affairs, University of Illinois at Chicago, Chicago, IL 60607, USA; [email protected] Received: 10 January 2018; Accepted: 1 February 2018; Published: 5 February 2018 Abstract: This paper discusses the emerging need for vertical farms by examining issues related to food security, urban population growth, farmland shortages, “food miles”, and associated greenhouse gas (GHG) emissions. Urban planners and agricultural leaders have argued that cities will need to produce food internally to respond to demand by increasing population and to avoid paralyzing congestion, harmful pollution, and unaffordable food prices. The paper examines urban agriculture as a solution to these problems by merging food production and consumption in one place, with the vertical farm being suitable for urban areas where available land is limited and expensive. Luckily, recent advances in greenhouse technologies such as hydroponics, aeroponics, and aquaponics have provided a promising future to the vertical farm concept. These high-tech systems represent a paradigm shift in farming and food production and offer suitable and efficient methods for city farming by minimizing maintenance and maximizing yield. Upon reviewing these technologies and examining project prototypes, we find that these efforts may plant the seeds for the realization of the vertical farm. The paper, however, closes by speculating about the consequences, advantages, and disadvantages of the vertical farm’s implementation. Economic feasibility, codes, regulations, and a lack of expertise remain major obstacles in the path to implementing the vertical farm. -
Risk of Human Pathogen Internalization in Leafy Vegetables During Lab-Scale Hydroponic Cultivation
horticulturae Review Risk of Human Pathogen Internalization in Leafy Vegetables During Lab-Scale Hydroponic Cultivation Gina M. Riggio 1, Sarah L. Jones 2 and Kristen E. Gibson 2,* 1 Cellular and Molecular Biology Program, Department of Food Science, University of Arkansas, Fayetteville, AR 72701, USA; [email protected] 2 Department of Food Science, University of Arkansas, Fayetteville, AR 72704, USA; [email protected] * Correspondence: [email protected]; Tel.: +1-479-575-6844 Received: 13 February 2019; Accepted: 7 March 2019; Published: 15 March 2019 Abstract: Controlled environment agriculture (CEA) is a growing industry for the production of leafy vegetables and fresh produce in general. Moreover, CEA is a potentially desirable alternative production system, as well as a risk management solution for the food safety challenges within the fresh produce industry. Here, we will focus on hydroponic leafy vegetable production (including lettuce, spinach, microgreens, and herbs), which can be categorized into six types: (1) nutrient film technique (NFT), (2) deep water raft culture (DWC), (3) flood and drain, (4) continuous drip systems, (5) the wick method, and (6) aeroponics. The first five are the most commonly used in the production of leafy vegetables. Each of these systems may confer different risks and advantages in the production of leafy vegetables. This review aims to (i) address the differences in current hydroponic system designs with respect to human pathogen internalization risk, and (ii) identify the preventive control points for reducing risks related to pathogen contamination in leafy greens and related fresh produce products. Keywords: hydroponic; leafy greens; internalization; pathogens; norovirus; Escherichia coli; Salmonella; Listeria spp.; preventive controls 1. -
Aquaponics Systems and Management
Introduction to Aquaponics Systems and Management Patricia Duncan, Ph.D. Georgia Center for Aquaculture Development Cooperative Extension Program, Fort Valley State University Fort Valley, GA What is Aquaponics? Aquaponics combines the culture of aquatic animals in recirculating aquaculture systems (RAS) with the hydroponic cultivation of plants. Hydroponics is the soilless culture of plants in a nutrient solution. Aquaponics vs Hydroponics In Hydroponics, a chemical nutrient solution is provided for the plants In aquaponics, by providing a nutritionally complete, formulated feed to the fish, the required nutrients and minerals will be supplied to the plants through the fish feeding and processing feed. As in all recirculating aquaculture systems (RAS), all the nutrients must be supplied to the fish in the feed since there are no pond organisms available as food. Requirements to Grow Plants in Hydroponic Systems Support for the plant above the solution Aeration of the solution Prevention of light reaching the solution so there will be no growth of algae Proper pH balance Proper nutrients Requirements to Grow Aquatic Animals in Recirculating Aquaculture Systems (RAS) Good Water Quality Optimum temperature Proper pH Sufficient Dissolved Oxygen Good Feed Means to treat animal waste Water Quality Parameters Important to Aquatic Animal Growth and Health Dissolved oxygen Temperature Ammonia Nitrite pH Alkalinity/Hardness Carbon Dioxide/Carbonate Cycle Solids (Total Suspended Solids) Aquaponic Systems which Support Dense -
Hydroponic Vertical Farming — Helping Feed Our Growing Population
Chapter 3: Hydroponic Vertical Farming — Helping Feed Our Growing Population Hydroponic Vertical Farming: Helping Feed Our Growing Population Brief Description: • Barbed valves By 2050, it's estimated that 80 percent of the world's 9.2 billion • Plastic lex net cups population will live in urban areas. In this lesson students will • Seeds or seedlings gain an understanding of what a seed needs in order to grow • Hydroponic fertilizer into a healthy plant, and what a vertical farm is by comparing • Optional: grow lights, pH test kit, thermometer and contrasting this method of food production with conven- tional farming methods. Students will design their own rubric; Background: research best practices; create blueprints; and modify and build he impact that humans have had on Earth include deforesta- a working model of an indoor vertical hydroponic farm through tion, urbanization, desertiication, erosion, poor air and water collaborative eforts using recycled materials. his closed system quality, and changing the low of water. hrough innovative 3: Chapter should last six or more months, which allows students time for techniques such as hydroponic vertical gardening, we can miti- relection, entertainment and a healthy snack. gate some of the efects of urban sprawl. Objective: Hydroponics is a method of growing edible crops in soilless, Lessons Garden Up Your STEMming Students will: nutrient-rich water. Advantages of hydroponic gardening 1. Understand what a seed needs to grow into a healthy include: reduction in runof; less water usage; crops can be plant. grown indoors year-round; plants require less space, and can 2. Know what a vertical farm is and compare and contrast have higher yields.