General Disclaimer One Or More of the Following Statements May Affect
Total Page:16
File Type:pdf, Size:1020Kb
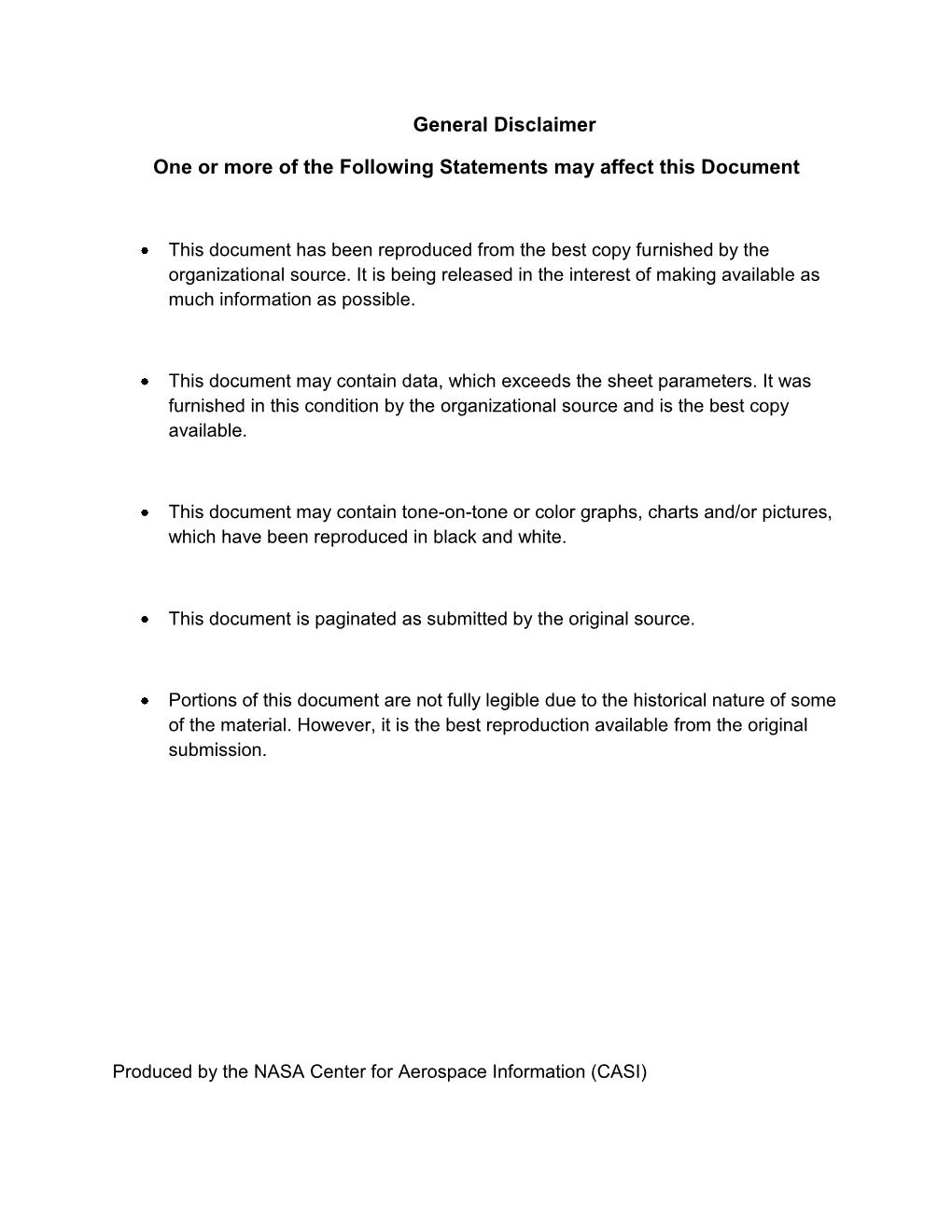
Load more
Recommended publications
-
To Delta-Based Bidirectional Model Transformations: the Symmetric Case
From State- to Delta-based Bidirectional Model Transformations: the Symmetric Case Zinovy Diskin1, Yingfei Xiong1, Krzysztof Czarnecki1, Hartmut Ehrig2, Frank Hermann2;3, and Fernando Orejas4 1 Generative Software Development Lab, University of Waterloo, Canada fzdiskin,yingfei,[email protected] 2 Institut f¨urSoftwaretechnik und Theoretische Informatik, Technische Universit¨atBerlin, Germany, [email protected] 3 Interdisciplinary Center for Security, Reliability and Trust, Universit´edu Luxembourg, [email protected] 4 Departament de Llenguatges i Sistemes Inform`atics, Universitat Polit`ecnicade Catalunya, Barcelona, Spain, [email protected] Abstract. A bidirectional transformation (BX) keeps a pair of interre- lated models synchronized. Symmetric BX are those for which neither model in the pair fully determines the other. We build two algebraic frameworks for symmetric BXs, with one correctly implementing the other, and both being delta-based generalizations of known state-based frameworks. We identify two new algebraic laws|weak undoability and weak invertibility, which capture important semantics of BX and are use- ful for both state- and delta-based settings. Our approach also provides a flexible tool architecture adaptable to different user's needs. 1 Introduction Keeping a system of models mutually consistent (model synchronization) is vital for model-driven engineering. In a typical scenario, given a pair of inter-related models, changes in either of them are to be propagated to the other to restore consistency. This setting is often referred to as bidirectional model transforma- tion (BX) [3]. As noted by Stevens [15], despite early availability of several BX tools on the market, they did not gain much user appreciation because of semantic issues. -
Quarterly Launch Report
Commercial Space Transportation QUARTERLY LAUNCH REPORT Featuring the launch results from the previous quarter and forecasts for the next two quarters 1st Quarter 1998 U n i t e d S t a t e s D e p a r t m e n t o f T r a n s p o r t a t i o n • F e d e r a l A v i a t i o n A d m i n i s t r a t i o n A s s o c i a t e A d m i n i s t r a t o r f o r C o m m e r c i a l S p a c e T r a n s p o r t a t i o n QUARTERLY LAUNCH REPORT 1 1ST QUARTER 1998 REPORT Objectives This report summarizes recent and scheduled worldwide commercial, civil, and military orbital space launch events. Scheduled launches listed in this report are vehicle/payload combinations that have been identified in open sources, including industry references, company manifests, periodicals, and government documents. Note that such dates are subject to change. This report highlights commercial launch activities, classifying commercial launches as one or more of the following: • Internationally competed launch events (i.e., launch opportunities considered available in principle to competitors in the international launch services market), • Any launches licensed by the Office of the Associate Administrator for Commercial Space Transportation of the Federal Aviation Administration under U.S. -
The Evolution of Commercial Launch Vehicles
Fourth Quarter 2001 Quarterly Launch Report 8 The Evolution of Commercial Launch Vehicles INTRODUCTION LAUNCH VEHICLE ORIGINS On February 14, 1963, a Delta launch vehi- The initial development of launch vehicles cle placed the Syncom 1 communications was an arduous and expensive process that satellite into geosynchronous orbit (GEO). occurred simultaneously with military Thirty-five years later, another Delta weapons programs; launch vehicle and launched the Bonum 1 communications missile developers shared a large portion of satellite to GEO. Both launches originated the expenses and technology. The initial from Launch Complex 17, Pad B, at Cape generation of operational launch vehicles in Canaveral Air Force Station in Florida. both the United States and the Soviet Union Bonum 1 weighed 21 times as much as the was derived and developed from the oper- earlier Syncom 1 and the Delta launch vehicle ating country's military ballistic missile that carried it had a maximum geosynchro- programs. The Russian Soyuz launch vehicle nous transfer orbit (GTO) capacity 26.5 is a derivative of the first Soviet interconti- times greater than that of the earlier vehicle. nental ballistic missile (ICBM) and the NATO-designated SS-6 Sapwood. The Launch vehicle performance continues to United States' Atlas and Titan launch vehicles constantly improve, in large part to meet the were developed from U.S. Air Force's first demands of an increasing number of larger two ICBMs of the same names, while the satellites. Current vehicles are very likely to initial Delta (referred to in its earliest be changed from last year's versions and are versions as Thor Delta) was developed certainly not the same as ones from five from the Thor intermediate range ballistic years ago. -
THE BASICS of COLOR PERCEPTION and MEASUREMENT the Basics of Color Perception and Measurement
THE BASICS OF COLOR PERCEPTION AND MEASUREMENT The Basics Of Color Perception and Measurement This is a tutorial about color perception and measurement. It is a self teaching tool that you can read at your own pace. When a slide has all information displayed, the following symbols will appear on the lower left side of the screen To go back one slide click. To advance one slide click. To exit the presentation press the Escape key on your keyboard. Contents There are five sections to this presentation: Color Perception Color Measurement Color Scales Surface Characteristics and Geometry Sample Preparation and Presentation If you wish to jump to a specific section click above on the appropriate name or click below to advance to the next slide. COLOR PERCEPTION Things Required To See Color A Light Source An Object An Observer Visual Observing Situation LIGHT SOURCE OBSERVER OBJECT Visual Observing Situation The visual observing model shows the three items necessary to perceive color. To build an instrument that can quantify human color perception, each item in the visual observing situation must be represented as a table of numbers. Light Source Light Source A light source emits white light. When light is dispersed by a prism, all visible wavelengths can be seen. Sunlight Spectrum Light Source Visible light is a small part of the electromagnetic spectrum. The wavelength of light is measured in nanometers (nm). The CIE wavelength range of the visible spectrum is from 360 to 780 nm. A plot of the relative energy of light at each wavelength creates a spectral power distribution curve quantifying the characteristics of the light source. -
Which Color Differencing Equation Should Be Used?
International Circular of Graphic Education and Research, No. 6, 2013 science & technology Which color differencing equation should be used? Martin Habekost Keywords: Colour differencing, Color, CIE, Colorimetry, Differencing, Delta E Color differencing equations have been in used for quite some time. In 1976 the CIE released the ΔEab-formula, weighting02_Habekost_Formulas function (kLSL), a chroma weighting function All these equations try to overcome the drawbacks of which is still widely used in industry and in research. This formula has its drawback and a number of other (kCSC), a hue weighting function (kHSH), an interactive the L*a*b-color space by introducing correction terms to color differencing formulas have been issued that try to accommodate how the human observer perceives color term between chroma and hue differences for improv- the non-uniform L*a*b*-color space. differencing in different areas of the color space. Trained and untrained observers in regards to judging color ing the performance for blue colors and a factor (RT) for differences were asked to rank color differences of test colors. In both cases the ΔE2000 formula corresponded * *2 *2 *2 rescalingEab the LCIELab aa*-axis bfor improving performance 2. Application of various ΔE-equations best with the way both groups of observers perceived these color differences. When industry experts were asked for grey colours. to rank perceived color differences without having a standard to compare to the CMC1:1 formula corresponds The CIE was not the only body that released a color In this paper three individual studies have been well with their observations. Although the ΔE2000 is mathematically more complicated than the ΔEab formula differencing equation2 to address2 the shortcomings2 of combined to achieve a better understanding of the the TC130 is mentioning guideline values (not official standard values) for evaluating process colors in the ISO L* C* h* 12646-2 procedure in its latest draft version. -
9750400 Structural Coating Materials Comments From
9750400 STRUCTURAL COATING MATERIALS COMMENTS FROM INTERNAL/INDUSTRY REVIEW Ananth Prasad (850) 942-1405 [email protected] Comments: (11-30-20, Internal) In review of the proposed Specification Change for 9750400, we have the following questions / concerns: Specification 975-4 now includes Aluminum Poles, Pedestals and Posts. Sections 649 and 646 are specifically addressed but not Section 715. Question #1; How will 715 pay items be covered by the 975-4 proposed specification change? Response: Section 715 has also been revised to cover the paint requirements for conventional light poles. Additional language has been added to 975 for clarity. ****************************************************************************** Scott Arnold (850) 414-4273 [email protected] Comments: (12-10-20, Internal) I think you referenced the wrong Section for the coating properties, see comments in attached file. Response: Thank you for your comment. Change made. ****************************************************************************** Frank Rea (352) 256-0456 [email protected] Comments: (12-18-21, Industry) Frank Rea, PCS, Consulex 8.0 delta E*ab units is a rather large difference. The human eye can detect a difference of 0.5 units. Also, the delta E*ab is calculated from three values: delta L*, delta a*, and delta b*. If the delta E*ab difference is influenced by any one value and not the others, the color difference can be undesirable but still meet the 8.0 delta E*ab unit difference requirement. Consulex recommends a delta E*ab difference after 5 years that does not exceed 3.0 units. Response: This additional change would be outside the scope of the current proposed changes. -
A Delta RENEWED a Guide to Science-Based Ecological Restoration in the Sacramento-San Joaquin Delta
A delta RENEWED A Guide to Science-Based Ecological Restoration IN THE SACRAMENTO-SAN JOAQUIN DELTA SAN FRANCISCO ESTUARY INSTITUTE AQUATIC SCIENCE CENTER SUGGESTED CITATION San Francisco Estuary Institute-Aquatic Science Center (SFEI-ASC). 2016. A Delta Renewed: A Guide to Science-Based Ecological Restoration in the Sacramento-San Joaquin Delta. Prepared for the California Department of Fish and Wildlife and Ecosystem Restoration Program. A Report of SFEI-ASC’s Resilient Landscapes Program, Publication #799, San Francisco Estuary Institute-Aquatic Science Center, Richmond, CA. Version 1.2, published November 2016. REPORT AVAILABILITY Report is available on SFEI’s website at www.sfei.org/projects/delta-landscapes. Updates to this report will be available here as well. IMAGE PERMISSION Permissions rights for images used in this publication have been specifically acquired for one-time use in this publication only. Further use or reproduction is prohibited without express written permission from the responsible source institution. For permissions and reproductions inquiries, please contact the responsible source institution directly. COVER CREDITS Cover, left to right: NAIP, 2014, detail from the Central Delta; illustrative rendering of an integrated future for the Delta (developed for this report by Yiping Lu, UC Berkeley). Inside back cover: NAIP, 2014. Title page: photograph by Shira Bezalel (SFEI-ASC). A delta RENEWED A Guide to Science-Based Ecological Restoration in the Delta A Report of the Delta Landscapes Project: Management Tools -
Color Management of Desktop Input Devices: Quantitative Analysis of Profile Quality
Western Michigan University ScholarWorks at WMU Master's Theses Graduate College 12-2003 Color Management of Desktop Input Devices: Quantitative Analysis of Profile Quality Xiaoying Rong Follow this and additional works at: https://scholarworks.wmich.edu/masters_theses Part of the Construction Engineering and Management Commons Recommended Citation Rong, Xiaoying, "Color Management of Desktop Input Devices: Quantitative Analysis of Profile Quality" (2003). Master's Theses. 4760. https://scholarworks.wmich.edu/masters_theses/4760 This Masters Thesis-Open Access is brought to you for free and open access by the Graduate College at ScholarWorks at WMU. It has been accepted for inclusion in Master's Theses by an authorized administrator of ScholarWorks at WMU. For more information, please contact [email protected]. COLOR MANAGEMENT OF DESKTOP INPUT DEVICES: QUANTITATITIVE ANALYSIS OF PROFILE QUALITY by Xiaoying Rong A Thesis Submitted to the Faculty of The Graduate College in partial fulfillment of the requirements for the Degree of Master of Science Department of Paper Engineering, Chemical Engineering and Imaging Western Michigan University Kalamazoo, Michigan December 2003 Copyright by Xiaoying Rong 2003 ACKNOWLEDGMENTS First, I would like to thank my advisors Dr. Dan Fleming and Dr. Abbay Sharma for guiding me to finish this thesis. Thanks for showing me the new technology in the graphic arts industry that I have been working on for over seven years. Thanks for your encouragement. Next, I would like to thank Ms. Lois Lemon forall the good times we worked together as your teaching assistant and as friends. Finally, I would like to thank my parents, Xiuling Cao and Zhongqi Rong, for supporting and encouraging me at all times. -
Delta Narratives-Saving the Historical and Cultural Heritage of The
Delta Narratives: Saving the Historical and Cultural Heritage of The Sacramento-San Joaquin Delta Delta Narratives: Saving the Historical and Cultural Heritage of The Sacramento-San Joaquin Delta A Report to the Delta Protection Commission Prepared by the Center for California Studies California State University, Sacramento August 1, 2015 Project Team Steve Boilard, CSU Sacramento, Project Director Robert Benedetti, CSU Sacramento, Co-Director Margit Aramburu, University of the Pacific, Co-Director Gregg Camfield, UC Merced Philip Garone, CSU Stanislaus Jennifer Helzer, CSU Stanislaus Reuben Smith, University of the Pacific William Swagerty, University of the Pacific Marcia Eymann, Center for Sacramento History Tod Ruhstaller, The Haggin Museum David Stuart, San Joaquin County Historical Museum Leigh Johnsen, San Joaquin County Historical Museum Dylan McDonald, Center for Sacramento History Michael Wurtz, University of the Pacific Blake Roberts, Delta Protection Commission Margo Lentz-Meyer, Capitol Campus Public History Program, CSU Sacramento Those wishing to cite this report should use the following format: Delta Protection Commission, Delta Narratives: Saving the Historical and Cultural Heritage of the Sacramento-San Joaquin Delta, prepared by the Center for California Studies, California State University, Sacramento (West Sacramento: Delta Protection Commission, 2015). Those wishing to cite the scholarly essays in the appendix should adopt the following format: Author, "Title of Essay", in Delta Protection Commission, Delta Narratives: Saving the Historical and Cultural Heritage of the Sacramento-San Joaquin Delta, prepared by the Center for California Studies, California State University, Sacramento (West Sacramento: Delta Protection Commission, 2015), appropriate page or pages. Cover Photo: Sign installed by Discover the Delta; art by Marty Stanley; Photo taken by Philip Garone. -
Design Considerations for a Pressure-Driven Multi-Stage Rocket
University of Tennessee, Knoxville TRACE: Tennessee Research and Creative Exchange Doctoral Dissertations Graduate School 12-2002 Design considerations for a pressure-driven multi-stage rocket Steven Craig Sauerwein University of Tennessee Follow this and additional works at: https://trace.tennessee.edu/utk_graddiss Recommended Citation Sauerwein, Steven Craig, "Design considerations for a pressure-driven multi-stage rocket. " PhD diss., University of Tennessee, 2002. https://trace.tennessee.edu/utk_graddiss/6301 This Dissertation is brought to you for free and open access by the Graduate School at TRACE: Tennessee Research and Creative Exchange. It has been accepted for inclusion in Doctoral Dissertations by an authorized administrator of TRACE: Tennessee Research and Creative Exchange. For more information, please contact [email protected]. To the Graduate Council: I am submitting herewith a dissertation written by Steven Craig Sauerwein entitled "Design considerations for a pressure-driven multi-stage rocket." I have examined the final electronic copy of this dissertation for form and content and recommend that it be accepted in partial fulfillment of the equirr ements for the degree of Doctor of Philosophy, with a major in Aerospace Engineering. Gary A. Flandro, Major Professor We have read this dissertation and recommend its acceptance: Accepted for the Council: Carolyn R. Hodges Vice Provost and Dean of the Graduate School (Original signatures are on file with official studentecor r ds.) To the Graduate Council: I am submitting herewith a dissertation written by Steven Craig Sauerwein entitled "Design Considerations for a Pressure-Driven Multi-Stage Rocket." I have examined the final paper copy of this dissertation for form and content and recommend that it be accepted in partial fulfillment of the requirements for the degree of Doctor of Philosophy, with a major in Aerospace Engineering. -
RUPTURE CURED. Wheat
BEST DOLLAR W EEKLY IN NORTH-WESTERN OHIO. V O L . 11 DELTA, OHIO, FRIDAY MORNING, OCTOBER 11, 1895. NO. 19 PERSONAI. PARAGHtPHH. SHALL CUBA BE FRRKT SOUK «V(H3BSTIOKS ABOIT i n m .TONcoi'NTV coru r o f Local News, Town and County. TH E COl’MTV 1-AIM . c o m m o n r i .E A S . Fresh From the Court House. No international question has arisen SARGENT BROS. Whosoever will may come to the Miss Flo Bourquln Is visiting friends Now that the county fair is a tiling Realty Transfers. Adanlulstra In Fayette this week. since the days France attempted to cam p lire Tuesday evening. of the past as far as 1W(5 is concerned tors' Affairs, Marriage Licen set up u crowned head In M exico lias SPECIAL REPORT TO T11E ATLAS. & we may properly make some sugges s e s , E t c . SAXTON. Camp lire at W olcott’s next Tuesday A tty . E verett is in Wauseon ti)I• arisen in which Americans naturally evening, everybody is invited. week attending court. tions. It is a fact, so we are inform Common Pleas Court convened last take so much Interest. The Cubans ed by some of the directors, that two Monday with the Hon. John M. Sheets Probate Court. Three short shrill whistles Tuesday Mrs. Dr. Bishop Is visiting friends understand Dlls condition and natur thousand more tickets were sold at as presiding judge. The docket Is an W. E. Fowle^ugd V. V. Cutting ally look this way for sympathy, and Now is t ie time afternoon at 3 o'clock called for a cold at Zanesville this week. -
Innovation in the Analysis of Weathering-Induced Color
Material Testing Product and Technology News Volume 40 ® Issue 86 SunSpots Spring 2010 Innovation in the Analysis of Weathering-Induced Color Changes in Plastics Atlas collaborates with Underwriters Laboratories By Thomas Kilian, Dr. Kurt Engelsing, Dr. Peter Heidemeyer, to advance testing for and Dr. Martin Bastian, Süddeutsches Kunststoff-Zentrum (SKZ), solar industry. Würzburg, Germany Page 13 Abstract Developing formulations for colored plastic products often requires color stability tests involving lengthy outdoor weathering. Currently, the only method for reducing this outdoor weathering time is accelerated artificial weathering. With the goal of saving even more time, a new color measurement system (Catscope, ERT- Optik GmbH) was investigated in this research project. The Catscope was developed for investigating weathering- In This Issue induced color changes in paint systems. With paint samples, color changes can be accurately measured after a short exposure time and then extrapolated for longer weathering times. The purpose 11 of this study was to investigate the suitability of Catscope for the measurement of weathering-induced color changes in plastics. After Affordable SEPAP Serves verifying the reproducibility of Catscope measurements for plastics, Multiple Industries the results were correlated with a conventional spectrophotometer measurement. In addition, some new extrapolation functions were tested in order to adjust the prediction for plastic parts. 11 Experimental New Xenotest® 220/220+ Sample Preparation Unveiled To investigate weathering-induced color changes in colored plastics, test plates were produced by injection molding using a Battenfeld TM 1300/525+130 machine with a two-cavity mold for 12 test plates with different surface structures (polished, brushed Atlas’ Launches Program to finish and two different spark erosion structures).