FINAL PROGRAM Current As of July 14, 2021
Total Page:16
File Type:pdf, Size:1020Kb
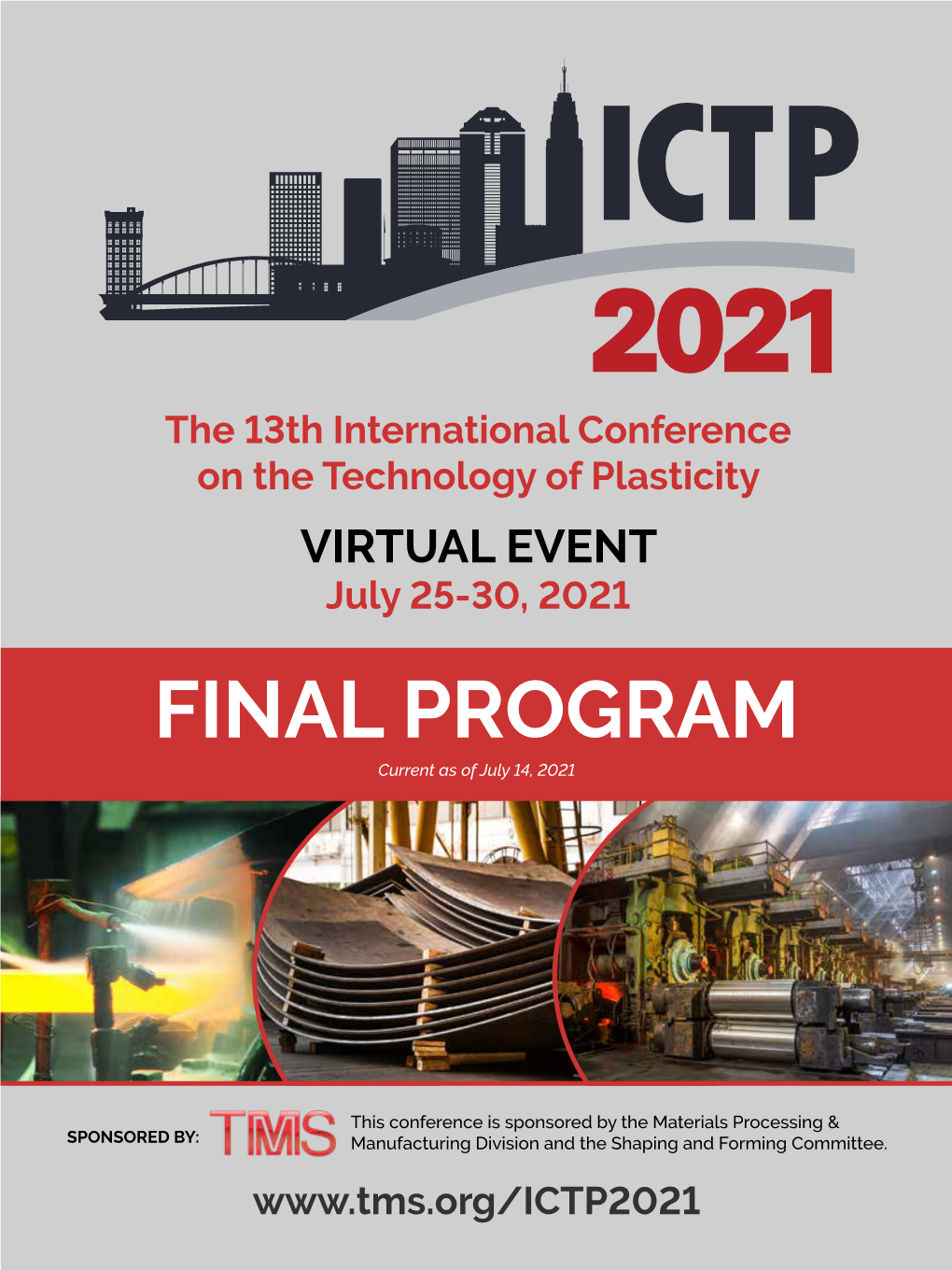
Load more
Recommended publications
-
Listening to Metal Lost Art, Page 90
GREASE | GEAR | DATA | KNOW-HOW LISTENING TO METAL LOST ART, PAGE 90 ROADANDTRACK.COM AUGUST 2015 89 LOST ART BY SAM SMITH THE ENGLISH WHEEL HOW TWO HANDS AND AN OLD-WORLD TOOL MADE SOME OF THE SEXIEST CAR BODIES IN HISTORY. mericans call it an English wheel, but the English call it a wheeling machine. It’s technically a rolling hammer—two steel drums A that can form sheetmetal into complex curves. In the wrong hands, an English wheel can turn a flat piece of alloy into sine-waved trash. In the right ones, it can make the fender of a Ferrari 250 Testa Rossa in a few hours. Or just about anything else you can build from curved metal. Legend holds that the first wheeling machines appeared in medieval France. They supplanted part of traditional blacksmithing, where men used mallets and shot bags to pound out flat armor or coachwork. The American name came in the 20th century, when the tool pollinated here from English panelbeaters. It had a brief affair with mass production, but the machine’s flexibility and skill demand made it perfect for low-volume work. Wheels helped birth early grand-prix cars, Bonneville record setters, most of Europe’s classic sports racers, and many of history’s great aircraft. Versions still shape NASCAR bodies and new Morgans, and they’re the backbone of countless custom and restoration shops. The English wheel has a reputation as a black art, the stuff of British cottages. To better understand it, we visited Fournier Enterprises, in Michigan’s Shelby Township. -
NYSBA Summer 2020 I Vol
NYSBA Summer 2020 I Vol. 13 I No. 2 New York Dispute Resolution Lawyer A publication of the Dispute Resolution Section of the New York State Bar Association Viral Changes in ADR During the Pandemic Webcam Main Screen To view the participants and to share or view documents Laptop To log into the videocall platform and LiveNote for transcripts Mic-audio Tablet For electronic bundle Cell To keep open line with team members © 2020 – Patricia Saiz. All rights reserved. nysba.org/dispute CLE Online On-Demand Save on the following programs when purchased as a single bundle! Go to the below website for more information on the programs provided. Advocacy in Presumptive ADR 5.5 MCLE Credits Segment 1: Segment 2: How to Value the Case for How-To: Effective Settlement, Mediation and Representation Of Clients Other ADR Processes During Video Mediation Recorded April 22, 2020 Recorded April 27, 2020 1.0 MCLE Credit 1.5 MCLE Credits Segment 3: Segment 4: Preparing For Your First Or Tactical Decisions That Counsel Next Mediation And Selecting And The Client Must Often Your Mediator Make While Participating In Mediation: Part 1 Recorded April 29, 2020 Recorded June 16, 2020 1.0 MCLE Credit 1.0 MCLE Credit Segment 5: Buy all 5 programs for a discounted price Tactical Decisions That Go to: NYSBA.ORG/ADRBUNDLE Counsel & The Client Must • NYSBA Members: $250.00 Often Make: Part 2 • Non-Members: $750.00 As a Section benefit, Dispute Resolution members will save on the following programs Recorded June 29, 2020 when purchased as a single bundle! 1.0 MCLE Credit • Dispute Resolution Section Members: $100.00 Table of Contents Special Issue: Viral Changes to ADR in the Pandemic Page Message from the Chair 5 (Laura Kaster) Advocacy in Presumptive ADR Message from the Co-Editors in Chief 7 (Edna Sussman, Laura Kaster and Sherman Kahn) 5.5 MCLE Credits Dispute Resolution Section News Interview with Shervica Gonzalez: Winner of the Judith Kaye 2019 Tournament’s Best Advocate Award 8 (Leslie Berkoff) Ethical Compass Moving Your Mojo Online 11 (Elayne E. -
2017-2018 College Catalog
2017-18 LAKESHORE TECHNICAL COLLEGE CATALOG Table of Contents Accounting* . 2 IT-Network Specialist . 82 Accounting Assistant. 4 IT-Web and Software Developer . 84 Administrative Professional. 6 Machine Tool Operation. 86 Advanced EMT . 8 Machinist Apprentice . 88 Agribusiness Science & Technology* . 10 Maintenance Mechanic/Millwright Apprentice . 90 Agriculture Technician . 12 Maintenance Mechanic. 92 Auto Collision Repair & Refinish Technician . 14 Maintenance Technician Apprentice. 94 Automotive Maintenance Technician . 16 Maintenance Technician . 96 Broadcast Captioning . 18 Manufacturing Management* . 98 Business Management . 20 Marketing. 100 Carpentry Apprentice . 22 Mechanical Computer Aided Drafting. 102 Child Care Apprentice . 24 Mechanical Design Technology . 104 Child Care Services . 26 Medical Assistant* . 106 CNC Technician*. 28 Medical Coding Specialist* . 108 Court Reporting . 30 Nuclear Technology* . 110 Criminal Justice-Law Enforcement*. 32 Nursing Assistant . 112 Criminal Justice-Law Enforcement Embedded Academy. 34 Nursing-Associate Degree* . 114 Culinary Arts. 36 Office Assistant . 116 Culinary Technical Diploma . 38 Ophthalmic Medical Assistant . 118 Dairy Herd Management* . 40 Paralegal . 120 Dental Assistant . 42 Paramedic Technician . 122 Early Childhood Education* . 44 Pharmacy Services Management. 124 Electro-Mechanical Technology* . 46 Pharmacy Technician*. 126 Emergency Medical Technician . 48 Plumbing Apprentice. 128 Emergency Medical Technician – Paramedic . 50 Practical Nursing*. 130 Energy Management Technology . 52 Quality Assurance Technician*. 132 Environmental Engineering-Waste & Water Technology. 54 Quality Process Improvement . 134 Fire Medic . 56 Radiation Safety/Health Physics* . 136 Food Manufacturing and Processing . 58 Radiography. 138 Graphic & Web Design . 60 Sales Representative . 140 Health Care Technician . 62 Security and Corrections . 142 Health Information Management . 64 Sheet Metal Apprentice . 144 Health Unit Coordinator. 66 Supply Chain Assistant . 146 Horticulture Technician . 68 Supply Chain Management* . -
Manufacturing at Double the Speed
Journal of Materials Processing Technology 229 (2016) 729–757 Contents lists available at ScienceDirect Journal of Materials Processing Technology jo urnal homepage: www.elsevier.com/locate/jmatprotec Manufacturing at double the speed a,∗ b c d Julian M. Allwood , Tom H.C. Childs , Adam T. Clare , Anjali K.M. De Silva , e a c a Vimal Dhokia , Ian M. Hutchings , Richard K. Leach , David R. Leal-Ayala , c f g h Stewart Lowth , Candice E. Majewski , Adelaide Marzano , Jörn Mehnen , e i g j j i Aydin Nassehi , Erdem Ozturk , Mark H. Raffles , Raj Roy , Islam Shyha , Sam Turner a Department of Engineering, University of Cambridge, United Kingdom b School of Mechanical Engineering, University of Leeds, United Kingdom c Institute for Advanced Manufacturing, University of Nottingham, United Kingdom d Department of Engineering, Glasgow Caledonian University, United Kingdom e Department of Mechanical Engineering, University of Bath, United Kingdom f Department of Mechanical Engineering, University of Sheffield, United Kingdom g School of Mechanical and Aerospace Engineering, Queen’s University Belfast, United Kingdom h Manufacturing Department, Cranfield University, United Kingdom i Advanced Manufacturing Research Centre, University of Sheffield, United Kingdom j Department of Mechanical & Construction Engineering, Northumbria University, United Kingdom a r t i c l e i n f o a b s t r a c t Article history: The speed of manufacturing processes today depends on a trade-off between the physical processes of Received 22 July 2015 production, the wider system that allows these processes to operate and the co-ordination of a supply Received in revised form 18 October 2015 chain in the pursuit of meeting customer needs. -
Air Tools Catalogue
SHEET METAL EQUIPMENT 121 ECKOLD HF80CH HANDFORMER This is a manually operated machine which is suitable for shrinking, stretching, punching, notching and edging in metal sheets and proles up to 16 gauge. It is supplied with a set of FWA405SSP shrinker and FWR407SSP stretcher jaws. Many other optional jaws are available. Capacity Adj. Stainless Working Shipping Reach x Gap Steel Alum. Steel Height Weight Weight 3”R x 16 ga. 14 ga. 19 ga. 32-1/2” to 53 lbs. 69 lbs. 2-1/4” G 44-1/2” Optional Jaw Assembly Shrinking Jaws Stretching Jaws Specialty Jaws FWA405SSP(STD) FWR407SSP (STD) LSW1SSP Punching Jaws HS40ASSP Beaked HSR60SSP Beaked AK250 Edging Jaws HLFA70SSP Nomar HFLR70SSP Nomar ASW442SSP Notching HLA60SSP Nomar Beaked Jaws HLR60SSP Nomar Beaked ECKOLD PA80 PNEUMATIC DRIVE KIT The PA80 drive unit is a power assist for the HF80CH Handformer. By adding this unit to the handformer you will have both hands free to hold and guide your work piece. Every application of the air foot pedal results in a single working stroke. The amount of pressure applied to the project depends on how much you step on the pedal. HF80CH shown with PA80 attached. To order assembled, use part number HF80CH-702. S H E E ECKOLD HZ51 HAND PLIER T Manually operated, plier type tool which cacn be used for 3 dierent ranges of applications. By simply changing the jaws, M shrinking, stretching or clinching operations can be achieved. Clinching is the joining of 2 sheets of metal without using rivets, bolts, staples, welds, etc. Jaws are not included and must be ordered separately. -
Technical Data
OPERATOR’S MANUAL ENGLISH WHEEL MODEL: EW-30 Baileigh Industrial, Inc. P.O. Box 531 Manitowoc, WI 54221-0531 Phone: 920.684.4990 Fax: 920.684.3944 [email protected] REPRODUCTION OF THIS MANUAL IN ANY FORM WITHOUT WRITTEN APPROVAL OF BAILEIGH INDUSTRIAL, INC. IS PROHIBITED. Baileigh Industrial, Inc. does not assume and hereby disclaims any liability for any damage or loss caused by an omission or error in this Operator’s Manual, resulting from accident, negligence, or other occurrence. Rev. 12/2016 © 2016 Baileigh Industrial, Inc. Table of Contents THANK YOU & WARRANTY .......................................................................................... 1 INTRODUCTION ............................................................................................................. 3 GENERAL NOTES .......................................................................................................... 3 SAFETY INSTRUCTIONS .............................................................................................. 4 SAFETY PRECAUTIONS ............................................................................................... 6 Dear Valued Customer: ................................................................................................... 6 TECHNICAL SPECIFICATIONS ..................................................................................... 8 TECHNICAL SUPPORT ................................................................................................. 8 UNPACKING AND CHECKING CONTENTS ................................................................. -
Power Hammer, Page 37 Floor Model English Wheel, to Add Are Proud We Retire and Enjoy Life with Their Family
THANK YOU FOR YOUR BUSINESS... M Mittler Bros. Prod- In the fast paced world we live in today, Thank You gets overlooked in too many i t t transactions. At Mittler Bros. we know that without you, our valued customer, we would l e not exist, Thank You. r Our other great strength is our Loyal, Dedicated & Skilled team members. Every B team member’s pride and skill is showcased in the products we produce. Thanks to r each and every one of them & their families for their dedication and support. Check o out our long time employee’s on page 91. s . P As we pass 30 years in business we refl ect on the past with pride and we look r o to the future with what has led us to this point; Innovation. When you look at our d 2011 catalog you will see continued innovation including; - Double Sided Ultimate Tubing Notcher, page 6 4” High Throat Bead Roller, page 17 16 Gauge Sheet Metal Brakes, page 34 Improved Wireless Scales, page 58-59 We also acquired the Metalcraft Tool line from Cal & Joyce Davis who after 22 years have decided to retire and enjoy life with their family. We are proud to add these quality products to our line of sheet metal forming equipment. Power Hammer, page 30 Floor Model English Wheel, page 37 I would like to use my bully pulpit here to encourage you, your family, friends and employees to become more active in government affairs. I am sure that many of you like myself as a business founder, owner, entrepreneur and racer do not like the current direction this country is moving in, that of a larger government with more reg- ulation, increased debt putting a huge burden on those of us who create the wealth that has made this country great. -
Product Brochure for L3455
Auckland: (09) 2717 234 Christchurch: (03) 741 6241 [email protected] www.machineryhouse.co.nz Product Brochure For L3455 L3455 - Professional Sheet Metal Fabrication Book 304 Colour Pages This Book Is For People Who Love Old Cars & Who Want To On Sale Make/Repair Their Old Car's Sheet Metal with Their Own Hands Ex GST Inc GST $78.00 $89.70 $65.22 $75.00 ORDER CODE: L3455 Title: Professional Sheet & Metal Fabrication Book Number of pages (No.): 304 Description This book is for people who love old cars and who want to make their old car's sheet metal better than new with their two hands. The practice of restoring antique cars is a complex, time-consuming , yet incredibly rewarding experience. It taxes your patience and financial resources, but for some of us it is as essential as oxygen. As with all the different facets of auto restoration-soft trim, paint, mechanical work, and more sheet metal repair provides the opportunity to transform the quality of something from extremely bad to extremely good or at least in much better condition than it was. Sheet metal fabrication allows you to make something beautiful out of thin air. Whether you are patching a small rust hole or making an entire fender, at the end of the day (or at least at the end of most days) you will feel good about having made tangible, measurable progress. For people with little experience in shaping metal, the idea of making panels or parts of panels from scratch is more than a little daunting. -
SHAPING the WORLD SINCE 1980 Mittlerbros.Com a Few Words from Our President
2016 SHAPING THE WORLD SINCE 1980 mittlerbros.com A few words from our President: To those of you who have read this page many times, thank you, and to first time readers, welcome and thank you for your interest in our company. Without all of you, none of this would be possible - THANK YOU FOR YOUR BUSINESS! We have added a number of new products this year and hope you’ll find them useful in your work. We are always open to your input and suggestions for new products. Once again, thank you for allowing me the privilege of this bully pulpit. While we gained a majority in the Senate and strengthened the majority in Congress, we still have an out of control President who acts independently, has no respect for Congress, the rule of law or the majority of the American people. We face a very important election in 2016 and I urge you and everyone in your sphere of influence to TURN OUT AND VOTE! It is important that you make your voice heard. As you view the candidates I also suggest that you think about the future you want not only for yourself, but also for your children and grandchildren. Do you want a larger government that takes more of what you work hard for or a smaller, less imposing government? I think I know what many independent, entrepreneurial business owners will want. So again, I suggest you break all the rules and talk to your family, employees and other groups that you are a part of to tell your own story and who you think is the best candidate for the job. -
Atkins Technical Journal 2
02 Technical Journal Papers 016 - 033 Plan Design Enable I am delighted to introduce you to the second issue of the Technical Journal. This journal continues to bring together technical papers that have been produced across the Atkins Group by our own exceptionally talented members of staff. It showcases the technical excellence that thrives within Atkins, featuring papers from disciplines such as aerospace, bridges, buildings, environment, highways, intelligent transport systems and water. Atkins is a multinational engineering and design consultancy, providing expertise to help resolve complex challenges presented by the built and natural environment. As a large organisation, with around 18,000 people, Atkins has many very strong technical abilities. To assist in meeting our customers increasing demand for a complex mix of services drawn from a number of our businesses around the world, our Technical Networks were launched at the 2008 Atkins Group Conference. These networks will ensure we consistently identify, share, celebrate and promote our technical expertise to deliver excellence. The networks are chaired by our most respected specialists, providing leadership in their appointed network, and it is through these Network Chairs that many of the papers have been collected. The papers contained in this journal demonstrate how we rise to the challenges presented to us and provide our clients with innovative, cost effective and sustainable solutions. I hope you enjoy the papers presented as much as we enjoyed producing them. Chris Hendy -
DOC4F86D853B8DF9.Pdf
SPECIALIST PUBLISHERS TEE OF TECHNICAL AND FREE Publishing Ltd MODELLING BOOKS 2012 CATALOGUE THE LONDON MODEL HOW TO MAKE A HOT AIR AEROPLANEA MODERN PROPELLER VERSION OF THE WENFORD - A BEATTIE 2-4-0 GETTING THE BEST OUT OF ENGINEERING EXHIBITION ENGINE THAT RUNS! CARRYINGGRASSHOPPER WAGON ESCAPMENT TANK IN 7¼" GAUGE GAS FIRING A 5" GAUGE STEPHENSON’S VALVE GEAR MY SWAN SONG? A 7¼" LOCOMOTIVE GAUGE GWR KING SLITTING SAW ARBORS Our range includes books PUBLISHERS OF on the following: BOILERMAKING THE INTERNATIONAL NOW 4 EXTRA PAGES DEVOTED TO WORKSHOP PROJECTS! MODEL BOAT4 SHOW EXTRA PAGES CASTING & FOUNDRY WORK VISIT DEVOTED TO WORKSHOP PROJECTS! WARWICKSHIRE EXHIBITION CENTRE 11th-13th NOVEMBER 2011 ELECTRIC MOTORS W GUI HO DE S I E FOR THE N E LONDON S I R D F MODEL E ENGINEERING GARDEN RAILWAYS EXHIBITION M ALEXANDRA PALACE A 20th - 22nd K JANUARY T 2012 I E S SU VI RE YO U HOT AIR ENGINES IN YOUR WORKSHOP Engineering in Miniature features LATHE WORK CONSTRUCTION: ‘WESSIE’ - THE LNWR ALL YOU NEED CONSTRUCTION: BUILDING A GWR 12 TON VAN 0-8-0 HEAVY GOODS ENGINETHE MYFORD IN 5" GAUGE £3.10 constructional articles on all aspects of CONSTRUCTION: ‘WESSIE’ - THE LNWR 0-8-0 QUARTER SCALE TO KNOW ABOUT SUPER 7 SCREW TECHNICAL: INDEXABLE HEXAGON TECHNICAL: THE STORY OF A FLASH-STEAM HEAVY GOODS LOCOMOTIVE IN 5" GAUGE RAY MEAD MINIATURETURBINE-POWERED CUTTING HYDROPLANE CLUTCH, CHUCK JAWS MODEL ENGINEERING OR SCREW CUTTING TECHNICAL: ALL YOU NEED TO KNOW ABOUT MAY 2011 MAY EJECTORS AND REPORT:£2.95 WHISSENDINE MINIATURE STEAM REPORT: THE RINGSTEAD FOUNDRY AT THE MINIATURE EJECTORS AND INJECTORS SINGLE CYLINDER RALLY 2011 model engineering. -
MODEL T28964 22" HEAVY-DUTY BENCHTOP ENGLISH WHEEL OWNER's MANUAL (For Models Manufactured Since 12/18)
MODEL T28964 22" HEAVY-DUTY BENCHTOP ENGLISH WHEEL OWNER'S MANUAL (For models manufactured since 12/18) COPYRIGHT © FEBRUARY, 2019 BY GRIZZLY INDUSTRIAL, INC. WARNING: NO PORTION OF THIS MANUAL MAY BE REPRODUCED IN ANY SHAPE OR FORM WITHOUT THE WRITTEN APPROVAL OF GRIZZLY INDUSTRIAL, INC. #ES20233 PRINTED IN CHINA V1.02.19 This manual provides critical safety instructions on the proper setup, operation, maintenance, and service of this machine/tool. Save this document, refer to it often, and use it to instruct other operators. Failure to read, understand and follow the instructions in this manual may result in fire or serious personal injury—including amputation, electrocution, or death. The owner of this machine/tool is solely responsible for its safe use. This responsibility includes but is not limited to proper installation in a safe environment, personnel training and usage authorization, proper inspection and maintenance, manual availability and compre- hension, application of safety devices, cutting/sanding/grinding tool integrity, and the usage of personal protective equipment. The manufacturer will not be held liable for injury or property damage from negligence, improper training, machine modifications or misuse. Some dust created by power sanding, sawing, grinding, drilling, and other construction activities contains chemicals known to the State of California to cause cancer, birth defects or other reproductive harm. Some examples of these chemicals are: • Lead from lead-based paints. • Crystalline silica from bricks, cement and other masonry products. • Arsenic and chromium from chemically-treated lumber. Your risk from these exposures varies, depending on how often you do this type of work. To reduce your exposure to these chemicals: Work in a well ventilated area, and work with approved safety equip- ment, such as those dust masks that are specially designed to filter out microscopic particles.