Identifying and Assessing the Risks in the Supply Chain
Total Page:16
File Type:pdf, Size:1020Kb
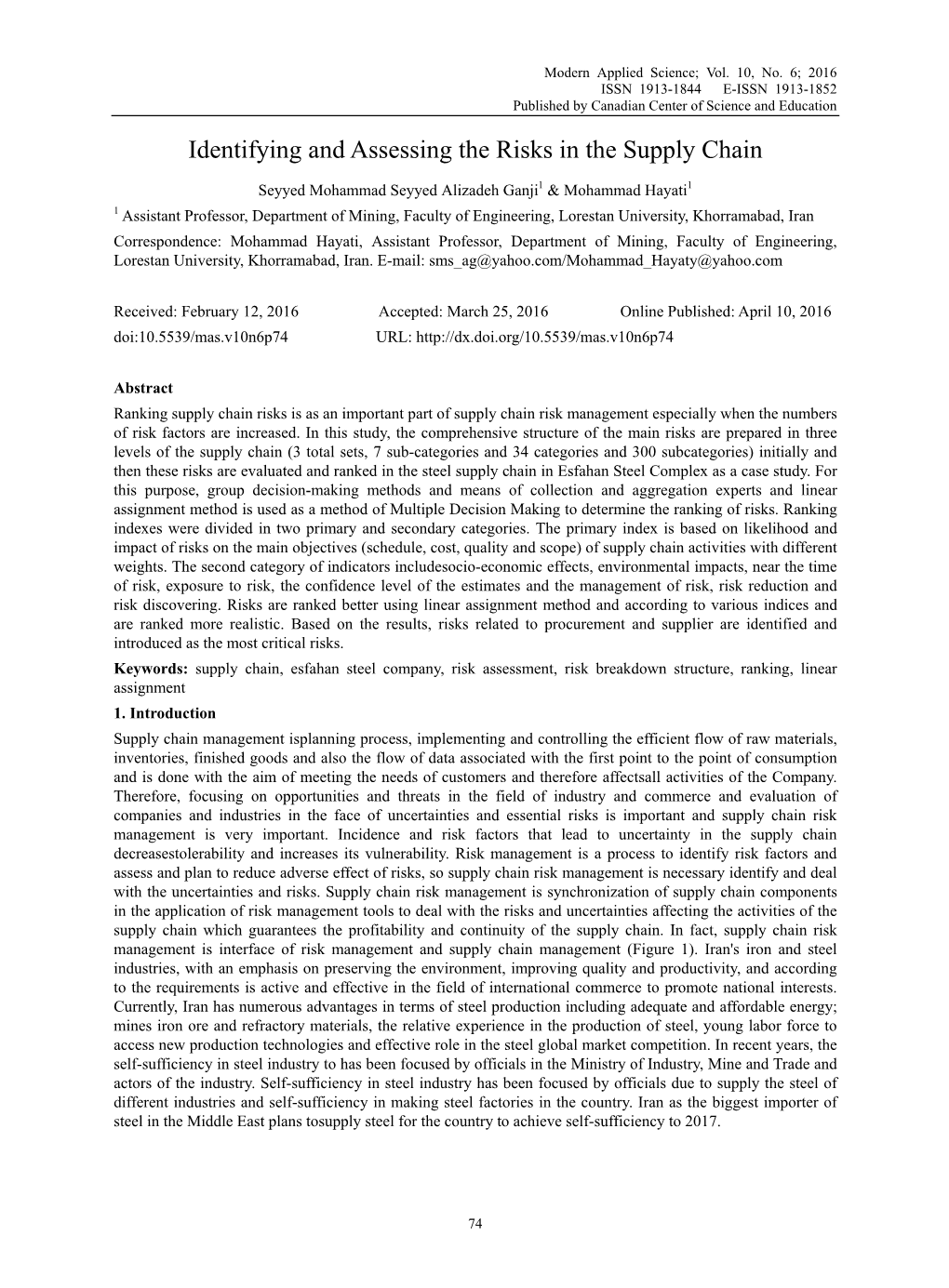
Load more
Recommended publications
-
Risk Management for Engineers
Risk Management for Engineers Course No: B02-013 Credit: 2 PDH Boris Shvartsberg, Ph.D., P.E., P.M.P. Continuing Education and Development, Inc. 22 Stonewall Court Woodcliff Lake, NJ 07677 P: (877) 322-5800 [email protected] Table of Contents 1. INTRODUCTION ................................................................................................................................... 2 2. DEFINITION OF RISK. RISK PLANNING ........................................................................................... 2 2.1. RISK IDENTIFICATION .................................................................................................................................. 3 2.2. RISK ANALYSIS ........................................................................................................................................... 3 2.3. RISK RESPONSE ........................................................................................................................................... 5 3. RISK BREAKDOWN STRUCTURE (RBS)............................................................................................ 6 4. DEALING WITH RISKS AT A PROJECT LEVEL ............................................................................... 8 5. RISKS SPECIFIC TO ELECTRICAL UTILITY COMPANIES ............................................................ 9 6. CASE STUDY - RENOVATION OF MAIN STREET SUBSTATION .................................................. 10 6.1. DESCRIPTION ............................................................................................................................................ -
ESE Paper 1 |IRMS | Ipate What Is Work Breakdown Structure?
______________________________________________________________________________ What is Work Breakdown Structure? A Work Breakdown Structure (WBS) is a deliverable-oriented hierarchical division of the project work to be executed by team to accomplish the objectives and produce the required deliverables (outputs). The WBS is the Work Breakdown Structure. It is a hierarchical representation of the elements (tasks) that comprise a project. Creating a Work Breakdown Structure does just as the name implies, breaking down the work into smaller chunks that everyone can chew. A project seems very overwhelming at first, and the WBS helps stop these feelings. A quick glance at the WBS allows everyone on the _____________________________________________________________________________________ YourPedia |ESE Paper 1 |IRMS | iPATE For more details visit us at: www.yourpedia.in or call at 98552-73076 ______________________________________________________________________________ project team to see what has been done, and what needs to be done. The WBS is a very important part of project management for this very reason. It is prepared during the planning phase of project management. On the basis of WBS, effective project planning, execution, controlling, monitoring & reporting can be done. All the work contained within the WBS is to be identified, estimated, scheduled, and budgeted. _____________________________________________________________________________________ YourPedia |ESE Paper 1 |IRMS | iPATE For more details visit us at: www.yourpedia.in or call at 98552-73076 ______________________________________________________________________________ Work Breakdown Structure Diagram The Work Breakdown Structure (WBS) is developed to establish a common understanding of project scope. It is a hierarchical description of the work that must be done to complete the deliverables of a project. Each descending level in the WBS represents an increasingly detailed description of the project deliverables. -
A Risk Breakdown Structure for Public Sector Construction Projects
A Risk Breakdown Structure for Public Sector Construction Projects Marie Dalton Centre for Research in the Management of Projects, Manchester Business School, The University of Manchester (email: [email protected]) Abstract This research is part of a wider project (ProRIde) focusing on the risk identification stage of the risk management process. The specific remit of the study is to analyse the text of National Audit Office (NAO) reports to identify recurring risk sources on public sector construction projects. A textual analysis software, QSR N6, is used to code the data. The risk source information in organised and presented in a Risk Breakdown Structure (RBS), a hierarchical presentation of risk sources. The output of this study represents a contribution to knowledge in that it is empirically derived – many risk identification support tools are compiled on an ad•hoc basis through brainstorming or personal experience. This research takes advantage of a rich existing database and employs a systematic methodology to develop an RBS that is specific to the context of public sector construction projects. Keywords: Public sector procurement, construction, risk identification, risk breakdown structures, QSR N6 1. Introduction 1.1 Overview of the ProRIde project ProRIde (Project Risk Identification) is an EPSRC•funded project (GR/R51452) concerned specifically with the risk identification phase of the risk management process (see Figure 1). Concurrent studies within the ProRIde project examine risk identification by individual project managers [1] and work is starting on group dynamics. Comprehensive risk identification is central to the relevance and effectiveness of the subsequent risk management process [2] • unidentified risk sources remain as unknown and unmanaged threats to the project objectives. -
Development Project Management
DEVELOPMENT PROJECT MANAGEMENT Project Management Associate (PMA) Certification Learning Guide 2016 GUIDE PM4R: PROJECT MANAGEMENT FOR RESULTS Página 0 AUTHORS Rodolfo Siles, PMP, and Ernesto Mondelo, PMP. TECHNICAL REVISION Harald Modis, PMP; Galileo Solís, PMP; John Cropper, Prince2; Victoria Galeano, PMP, and Roberto Toledo, PMP. FOURTH EDITION UPDATE 2015 Ricardo Sánchez Orduña, PMP. IDB COLLABORATORS Matilde Neret; Carolina Aclan; Nydia Díaz; Rafael Millan; Juan Carlos Sánchez; Jorge Quinteros; Roberto García; Beatriz Jellinek; Eugenio Hillman; Masami Yamamori; Víctor Shiguiyama; Juan Manuel Leano; Gabriel Nagy, PMP; Samantha Pérez; Cynthia Smith, and Pablo Rolando. SPECIAL RECOGNITION To the team members that contributed to the validation of the course contents and methodology. Paraguay Ada Verna, Adilio Celle, Alcides Moreno, Álvaro Carrón, Amado Rivas, Amilcar Cazal, Carmiña Fernández, Carolina Centurión, Carolina Vera, Cesar David Rodas, Daniel Bogado, Diana Alarcón, Eduardo Feliciangeli, Félix Carballo, Fernando Santander, Gloria Rojas, Gonzalo Muñoz, Hernán Benítez, Hugo García, Ignacio Correa, Joaquín Núñez, Jorge Oyamada, Jorge Vergara, José Demichelis, Juan Jacquet, Laura Santander, Lourdes Casanello, Luz Cáceres, Mabel Abadiez, Malvina Duarte, Mariano Perales, Marta Corvalán, Marta Duarte, Nelson Figueredo, Nilson Román, Noel Teodoro, Nohora Alvarado, Norma López, Norma Ríos, Oscar Charotti, Patricia Ruiz, Reinaldo Peralta, Roberto Bogado, Roberto Camblor, Rocío González, Simón Zalimben, and Sonia Suárez. Bolivia Alex Saldías, Amelia López, Ana Meneses, Boris Gonzáles, Christian Lündstedt, Debbie Morales, Edgar Orellana, Fernando Portugal, Francisco Zegarra, Freddy Acebey, Freddy Gómez, Gabriela Sandi, Georgia Peláez, Gilberto Moncada, Gina Peñaranda, Gonzalo Huaylla, Hugo Weisser, Iván Iporre, Jorge Cossio, Joyce Elliot, Karin Daza, Leticia Flores, Luis Yujra, Marcelino Aliaga, Margarita Ticona, María Fernanda Padrón, Mónica Sanabria, Nicolás Catacora, Rommy Verástegui, Rossana Fernández, Rossina Alba, Salvador Torrico, and Santiago Rendón. -
Uncovering All of the Risks on Your Projects Vol
PM World Journal Uncovering All Of The Risks On Your Projects Vol. V, Issue IX – September 2016 by Paul Burek, PMP, CSM www.pmworldjournal.net Second Edition Uncovering All Of The Risks On Your Projects1 Paul Burek, PMP, CSM Solutions Cube Group LLC Abstract Through my experience working with project teams, in many industries, on hundreds of projects, I have learned that although Project Managers (PMs) are expected to manage risk on their projects, many times they end up fighting fires and managing the problems that result from unmanaged or unknown risks. There are many reasons why Project Managers avoid Risk Management and resort to firefighting project problems. Common perceptions PMs have are: My project won’t hurt anybody Our company has a “kill the messenger” syndrome, so it is best not to bring up risks Firefighting is rewarded, the more problems I can solve, the better I look Failure is not an option, so why focus on risks, our team won’t allow them to impact the project Risk is inevitable, so why bother trying to avoid or manage it. Another underlying reason for not managing risk on projects, or not managing it well, is because the Project Manager does not have the right tools and techniques for risk management. It all too common for PMs to understand risk management theory, but not be skilled in the transformation of this theory into practical application. Effective risk management includes engaging the project stakeholders throughout the entire risk management process: identifying, assessing, responding to and managing risks throughout the life of the project. -
(Work Breakdown Structure) for Safety Planning of Cable Stayed Bridge Project
Proceedings of the International Conference on Industrial Engineering and Operations Management Bandung, Indonesia, March 6-8, 2018 Development of Risk-Based Standardized WBS (Work Breakdown Structure) for Safety Planning of Cable Stayed Bridge Project Gilang Satrio Department of Civil Engineering University of Indonesia Depok, Jawa Barat, Indonesia [email protected], [email protected] Prof. Dr. Ir. Yusuf Latief, MT. Department of Civil Engineering University of Indonesia Depok, Jawa Barat, Indonesia [email protected] Abstract In a project plan, the Work Breakdown Structure (WBS) has been defined as the total representation of the work or stage, including from start to finish the project has a role in project quality. WBS has many roles in every construction project such as buildings, bridges, roads, and many more. In many condition, many bridge construction projects in Indonesia are not in line with planning in terms of schedules and costs, therefore the importance of WBS development especially the risk-based bridge construction project. The result of the following research are expected to be a reference in bridge construction projects. The result indicates taht standarized WBS consist of 4 primary level and 2 complementary levels, with 9 dominant risk variables on safety performance, and recommended risk responses as the developement. Keywords Project Management, Cable Stayed Bridge, Risk Management, Safety Plan, Work Breakdown System 1. Introduction Successful project management depends on a well-planned for assigning, scheduling, and controlling progress of the resources [1]. One importnat factor of a construction project performance is the compliance with safety plan and safety procedure [2]. In case of safety, the high number work accidents and casualties caused many negative impacts, such as financial loss [3]. -
Riskyproject Is a Unique Tool, Which Gives You a Simple Answer on The
RiskyProject Applications RiskyProject is a unique tool, which gives you a simple answer on the common question: What will happen to your project schedule if certain risks occur?" Project planning and scheduling David Rutt, Manager, Greyhound Canada Estimations Project managers can use RiskyProject for planning, scheduling, quantitative risk analysis, and Project risk management performance measurement of projects with multiple risks and uncertainties. Project performance RiskyProject allows managers to improve their ability to predict the course of projects and determine measurement how risks and uncertainties will affect the project. It can help increase the chance that project will be on time and on budget. Industries RiskyProject employs our patent pending Event Chain Methodology for quantitative risk analysis. Information technology Event Chain Methodology is a method of defining and managing uncertainties in different time related including software business and technological processes. development RiskyProject Benefits Engineering and construction Manufacturing Predict the course of your project: determine how risks and uncertainties will affect your project schedule. Pharmaceutical Instantly see which project parameters are the most Petroleum and mining critical: project start, finish date, times, and cost with and many others without risks, plus crucial tasks, critical risks, and project success rate. Improve your ability to manage the course of your project: System Requirements track project performance and risk together, analyze affect of your mitigation efforts. Windows 2000 and higher Make an informed decision: Select project alternatives based on cost and duration. Project 128 MB RAM or more schedules, analyzed in RiskyProject, can be exported to DecisionPro, which generates decision trees associated with project alternatives. -
Risk Management Model of Construction Projects Using WBS Generator Linked 4D CAD
Risk Management Model of Construction Projects Using WBS Generator linked 4D CAD Chang Hak, Kim Sang Bok, Jee Yang Kue. Lee Assoc. Prof. Dept. Civil Eng., ERI Prof. Dept. Civil Eng. Prof. Dept. Civil Eng. Jinju Nat. Univ., Jinju, Korea Gyeongsang Nat. Univ., Jinju, Korea Daelim College, Anyang, Korea [email protected] [email protected] [email protected] Seo Young, Park Hyun Suk, Moon CM & IT Lab., Dep. Civil Eng. Gyeongsang Nat. Univ., Jinju, Korea (Car2112, gitadae)@hanmail.net Abstract The results of the study include a computerized system and a systematic process model for risk management and analysis. This study analyzes the present status of risk management in the construction industry, and then suggests reasonable methods for improved risk management plans. This study defines risk management procedures as preparation, identification, analysis, response and management to manage potential risks in the construction project. The modules for computerizing in this system consist of planning, construction, application of WBS (Work Breakdown Structure) and RBS (Risk Breakdown Structure). The methodology for analyzing construction risk uses fuzzy theory, and the scope of developed system is focused to the contractors. The risk management system suggested in this study operates on the internet, for providing contractors with a useful risk management tool by online system, with web-based menus that is helpful for practical application. Keywords Risk Management System, Work Breakdown Structure (WBS), Fuzzy, 4D 1. IINTRODUCTION In this study, we have reviewed the problems of the Modern construction projects in nature do not allow un- analysis methodologies used to analyze various risks in certain factors and risks depending on the experiences construction industry and proposed appropriate analysis and intuition of the contractors and project owners. -
Risk Management Guide
RISK MANAGEMENT GUIDE MINISTRY OF ADVANCED EDUCATION AND LABOUR MARKET DEVELOPMENT GOVERNMENT OF BRITISH COLUMBIA Table of Contents 1 Risk Management Framework ...................................................................................................... 1 1.1 Purpose ............................................................................................................................ 1 1.2 Objective .......................................................................................................................... 1 1.3 Benefits of Risk Management ............................................................................................... 1 1.4 Risk Defined ...................................................................................................................... 1 1.5 Methodology Overview ...................................................................................................... 2 2 Framework Requirements and Expectations Guide ......................................................................... 4 2.1 Requirements ..................................................................................................................... 4 2.2 Suggested Effort Guide ....................................................................................................... 4 3 Risk Planning ............................................................................................................................. 6 3.1 Roles & Responsibilities ...................................................................................................... -
Event Chain Methodology in Project
Copyright Notice: Materials published by ProjectDecisions.org may not be published elsewhere without prior written consent of ProjectDecisions.org. Requests for permission to reproduce published materials should state where and how the material will be used. Event Chain Methodology In Details Lev Virine, Ph.D., [email protected] Michael Trumper, [email protected] ProjectDecisions.org Abstract This paper is a detailed description of event chain methodology: schedule network analysis and an uncertainty modeling technique for project management. Event chain methodology focuses on identifying and managing the events and event chains that affect projects. Event chain methodology improves the accuracy of project planning simplifying the modeling and analysis of uncertainties in the project schedules. As a result, it helps to mitigate the negative impact of cognitive and motivational biases related to project planning. Introduction Virtually all projects are affected by multiple risks and uncertainties. These uncertainties are difficult to identify and analyze which can lead to inaccurate project schedules. Due to such uncertainties, most projects do not proceed exactly as planned. In many cases, they lead to project delays, cost overruns, and even project failures. Therefore, creating accurate project schedules, which reflect potential risks and uncertainties remains one of the main challenges in project management. Flyvbjerg, Holm and Buhl (2002; 2004; 2005) reviewed technical, psychological and political explanations for inaccurate scheduling and forecasting. They found that strategic misrepresentation under political and organizational pressure expressed by project planners as well as cognitive biases play major role in inaccurate forecasting. In other words project planner either unintentionally due to some psychological biases or intentionally under organizational pressure come up with wrong estimations. -
A Review of Project Risk Management Mohamed, H.F.-Projects Contracts Department - Petroleum Marine Services Company
International Journal of Scientific & Engineering Research, Volume 7, Issue 10, October-2016 1147 ISSN 2229-5518 A Review of Project Risk Management Mohamed, H.F.-Projects Contracts Department - Petroleum Marine Services Company Abstract: Since project risk management is of particular importance in the execution of all projects, special attention should be given to large scale projects as they have many areas of risk through the whole project life cycle. During the preliminary phase of the project life cycle, important strategic decisions are taken thus a professional risk management is needed in this phase to improve the identification and implementation of suitable response actions. This review paper contains a review of recent research relating to project risk management. It presents an overview of the basic concepts in risk management by conducting its different processes, projects lessons learned, and projects debriefing methods. It considers project risk management using the technique of risk breakdown structure. Related areas of risk management in large projects are called upon in this paper so this paper can act as a source document for further study. The risk cube technique and questionnaire survey technique which are two of the simplest and effective techniques in the risk load of the various project elements are discussed within this paper .Finally the risk elements associated with executing large scale projects influence the time; cost, technical achievement, and quality are discussed and concluded. Keywords: Project risk management -Project life cycle - Risk processes - Basic concepts - Project preliminary Phase - Projects Lessons learned – Projects debriefing methods – Risk Breakdown Structure – RBS- project risk cube – questionnaire Survey - time - cost - technical achievement – quality —————————— —————————— 1. -
NDOT Risk Management and Risk-Based Cost Estimation
RISK MANAGEMENT AND RISK-BASED COST ESTIMATION GUIDELINES August 2021 This page is left intentionally blank NEVADA DEPARTMENT OF TRANSPORTATION RISK MANAGEMENT AND RISK-BASED COST ESTIMATION GUIDELINES The goal of this manual is to provide guidance to NDOT personnel and consultants in best practice methods of risk management and risk-based cost estimation. It is recognized that guidelines cannot provide entirely complete and practical guidance applicable to all situations and cannot replace experience and sound judgment. As such, deviations from these guidelines may, in some cases, be unavoidable or otherwise justifiable. Procedure for Guideline Revisions The guideline will be periodically revised or updated. For edits or updates, contact the Project Management Division at (775) 888-7321. All updates will be available on the Project Management Division SharePoint Portal which should be visited regularly for updated information. Responsibility: The Project Management Division is responsible for edits and updates to this document. Temporary Revisions: Temporary revisions will be issued by the Project Management Division to reflect updated/revised procedures. These will be reflected on dated errata sheet(s) posted on the Project Management Division SharePoint Portal. Scheduled Revisions: As deemed necessary by the Project Management Chief, the Project Management Chief will assemble a Review Team for reviewing the guidelines and errata sheets to determine if a revised edition of the guidelines is required. The Project Management Division Chief will evaluate and approve the recommendations of the team for revisions to the guidelines. Risk Management and Page i Risk-Based Cost Estimation Guidelines August 2021 Foreword These guidelines address the first step in NDOT project management’s vision of achieving statewide uniformity and consistency of project cost estimates and department-wide priority on estimating, managing, and controlling costs.