Five-Stage Electric Starter
Total Page:16
File Type:pdf, Size:1020Kb
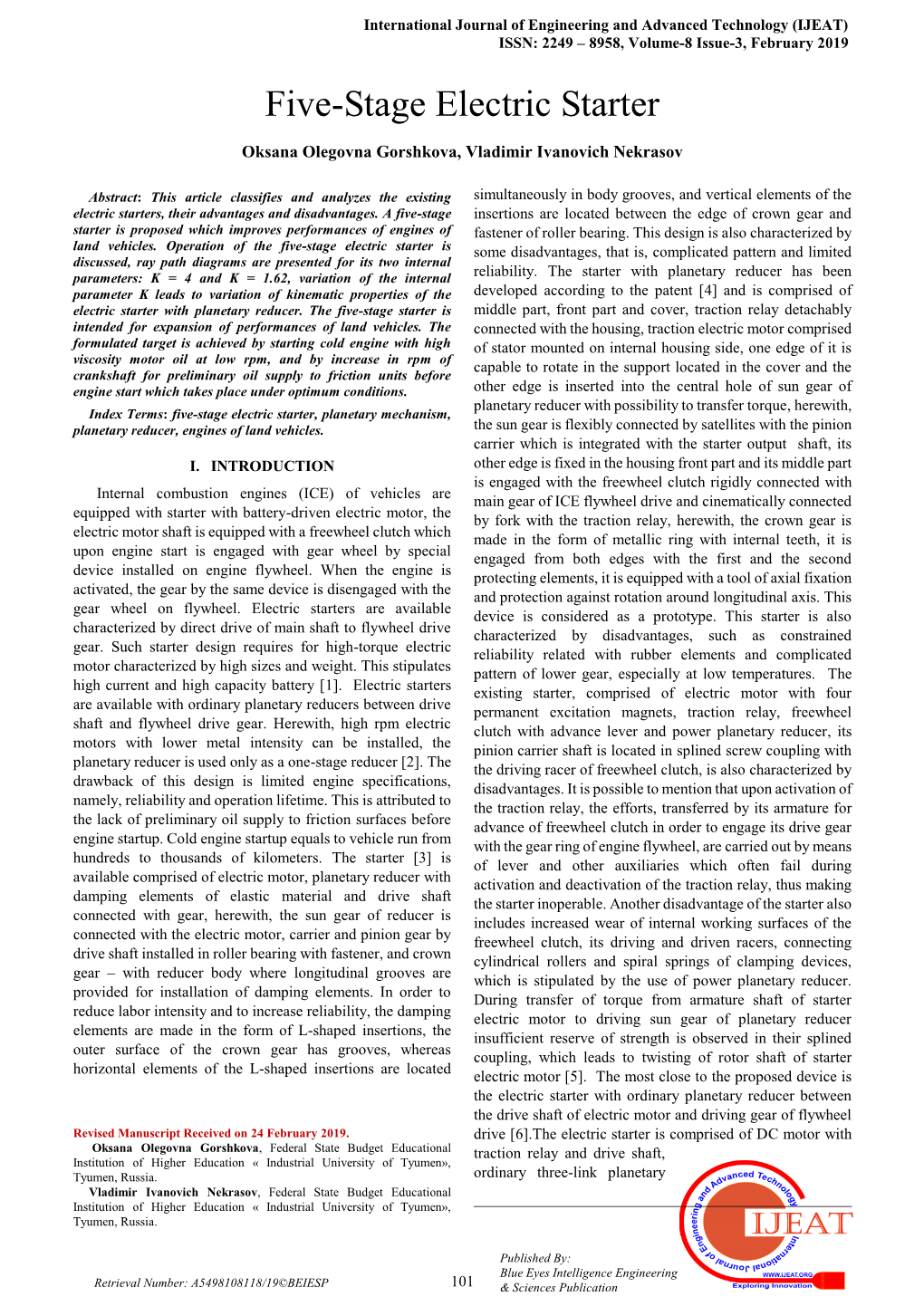
Load more
Recommended publications
-
Playing with Gears
174_LEGO_02 10/25/01 3:11 PM Page 17 Chapter 2 Playing with Gears Solutions in this chapter: I Counting Teeth I Gearing Up and Down I Riding That Train: The Geartrain I Worming Your Way: The Worm Gear I Limiting Strength with the Clutch Gear I Placing and Fitting Gears I Using Pulleys, Belts, and Chains I Making a Difference: The Differential 17 174_LEGO_02 10/25/01 3:11 PM Page 18 18 Chapter 2 • Playing with Gears Introduction You might find yourself asking: Do I really need gears? Well, the answer is yes, you do. Gears are so important for machines that they are almost their symbol: Just the sight of a gear makes you think machinery. In this chapter, you will enter the amazing world of gears and discover the powerful qualities they offer, trans- forming one force into another almost magically.We’ll guide you through some new concepts—velocity, force, torque, friction—as well as some simple math to lay the foundations that will give you the most from the machinery.The concepts are not as complex as you might think. For instance, the chapter will help you see the parallels between gears and simple levers. We invite you once again to experiment with the real things. Prepare some gears, beams, and axles to replicate the simple setups of this chapter. No descrip- tion or explanation can replace what you learn through hands-on experience. Counting Teeth A single gear wheel alone is not very useful—in fact, it is not useful at all, unless you have in mind a different usage from what it was conceived for! So, for a mean- ingful discussion, we need at least two gears. -
Design and Development of Open Differential for Transmission System of Quad Bike
International Research Journal of Engineering and Technology (IRJET) e-ISSN: 2395-0056 Volume: 05 Issue: 12 | Dec 2018 www.irjet.net p-ISSN: 2395-0072 Design and Development of Open Differential for Transmission System of Quad Bike Utkarsha Chaudhari1, Prathamesh Sangelkar2, Prajval Vaskar3 1,2,3Department of Mechanical Engineering, Sinhgad Academy of Engineering, Kondhwa ---------------------------------------------------------------------***---------------------------------------------------------------------- Abstract – A differential is an important torque 2. ANALYTICAL CALCULATIONS transmitting device in most of the rear wheel drive vehicles. An ATV is a vehicle which is used to ride in off-road terrains; 2.1 Primary Calculations for Gear Reduction hence continuous application of traction is a vital factor which showcases its performative aspect. The paper describes Input Data: designing and manufacturing an open differential for an off road ATV (Quad Bike) so that the vehicle maneuvers sharp Turning radius of vehicle: - 3m corners without losing traction to the driving wheels. Rear Track width: - 40” Rear tire diameter: - 23” Key Words: Open differential, traction difference, ANSYS, CREO, gear, pinion, centre pin. 1. INTRODUCTION A differential is a gear train with three shafts that has the property that the rotational speed of one shaft is the average of the speeds of the others, or a fixed multiple of that average. In automobiles, the differential allows the outer drive wheel to rotate faster than the inner drive wheel during a turn. This is necessary when the vehicle turns, making the wheel that is travelling around the outside of the turning curve roll farther and faster than the other. The average of the rotational speed of the two driving wheels equals the input rotational speed of the drive shaft. -
Evaluation on Failure Analysis of an Automobile Differential Pinion Assembly (IJIRST/ Volume 1 / Issue 12 / 054)
IJIRST –International Journal for Innovative Research in Science & Technology| Volume 1 | Issue 12 | May 2015 ISSN (online): 2349-6010 Evaluation on Failure Analysis of an Automobile Differential Pinion Assembly Ronak P Panchal Pratik B. Umrigar M.E. Student Department of Automobile Engineering Department of I.C. Engine & Automobile GTU, Mahesana, India GTU, Mahesana, India Abstract Bevel gears have become a subject to research interest because the dynamicload, attention of the noise level during operation and demand for lighter and smaller. In such type of gears there is a problems of failures contact at meshing the teeths. This can be avoided or minimized by proper method analysis and modification of the different gear parameters. This thesis presents characteristics of a bevel gear in dynamic condition involving meshing stiffness and other stresses produce. The purpose of this thesis is by using numerical approach to develop theoretical model of bevel gear and to determine the effect of meshing gear tooth stresses by taking material case hardened alloy steel (15Ni4Cr1) . To estimate the meshing stiffness, three-dimensional solid models for different number of teeth are generated by Solid works and the numerical solution is done in Ansys which is a finite element analysis. Keywords: Design of Spiral Bevel Gear, Analysis of Spiral Bevel Gear _______________________________________________________________________________________________________ I. INTRODUCTION Gear is a mechanical device used in transmission systems that allows rotational force to be transferred to another gears . The gear teeth allow force to be fully transmitted without slip and depending on the configuration can transmit forces at different speeds, torques, and even in a different directions. -
Design and Fabrication of Shaft Drive for Two Wheelers
International OPEN ACCESS Journal Of Modern Engineering Research (IJMER) Design and Fabrication of Shaft Drive for two Wheelers K.Vinoth Kumar1, Kari Naga Nikhil2, Kakollu Manoj Kumar3, Kaza Sai Sravan4, K.Subha Theja5 1,2,3,4,5Student, Department Of Mechanical Engineering R.M.K College Of Engineering & Technology, Thiruvallur , India 1. Abstract 1.1 Role Of Automobile In Our Day To Day Life In modern world the living status were developed and developing more equipped. The automobile takes a great part in the development, since it plays a major key in daily life while automobile is concern two wheeler i.e.(motor cycles and bike) it plays very important role because it saves the time of traveller by reaching the target place very faster. Although it saves the time, it makes lots of noise by the chain drive and also makes greasy over the parts of the bike by the chain drive lubrication. It leads to lot of maintenance cost. So by keeping maintenance as the main concept in our mind we had planned to do this project. 1.2 Proposed Method A shaft-driven two wheeler is a two wheeler that uses a drive shaft instead of a chain to transmit power from the pedals to the wheel arrangement. Shaft drives were introduced over a century ago, but were mostly supplanted by chain-driven two wheelers due to the gear ranges possible with sprockets and derailleur. Recently, due to advancements in internal gear technology, a small number of modern shaft-driven two wheelers have been introduced. Shaft-driven bikes have a large bevel gear where a conventional bike would have its chain ring. -
Analysis of Differential Crown Gear and Pinion for Axle with Different Materials
ISSN: 2455-2631 © April 2019 IJSDR | Volume 4, Issue 4 Analysis of differential crown gear and pinion for axle with different materials 1Dr. Satypal T. Warghat, 2Dhiraj V. Astonkar, 3Manish P. Bijwe 1Head of Department, 2,3Assistant Professor Department of Mechanical Engineering, Dr. Sau. KamaltaiGawai Institute of Engineering and Technology, Darapur, Tq. Daryapur, Dist. Amravati, Maharashtra 444814 Abstract: The differential can be stated as a gear train used to control the speed and torque to the rear wheels. While taking a turn, the basic requirement of the vehicle is to control the speed of rear wheels so that the vehicle turns smoothly on road surface. The differential mainly consists of three shafts and gear train arrangement. The first shaft is propeller shaft which provides the necessity torque and speed to differential for turn. The other two shafts are axle shafts mounted for each rear wheels. These shafts are attached to propeller shaft by crown gear and pinion arrangement thus making a bevel pair of gears. The two main parts of differential transmission system, one is crown gear which gives allowable speed to turn the vehicle and another is pinion which provides allowable speed and torque for turning the vehicle. Thus, the analysis of such crown gear and pinion makes necessity for strength. The analysis is conducted to verify the best material for the gears in the gear box at high speeds by analyzing von miss stress, deformation and also by considering safety of transmission. The various materials selected for analysis are Grey Cast Iron, Structural Steel, Titanium Alloy and Polyethylene. -
Study of Differential Bevel Gear Through Machining Method
International Journal of Engineering and Technical Research (IJETR) ISSN: 2321-0869, Volume-1, Issue-3, May 2013 STUDY OF DIFFERENTIAL BEVEL GEAR THROUGH MACHINING METHOD Mohd Abbas, Sanjeev Sharma, Vinit Kumar Sharma Straight Path. Abstract— In this paper we have selected the machining method, a cost saving manufacturing process to produce If the left side gear (red) encounters resistance, the planet straight bevel gears without any compromise with quality gear (Green) rotates about the left side gear, in turn applying parameters, then validate the samples taken from vendor as extra rotation to the right side gear (yellow). per our design requirement and to increase Durability & Productivity of Straight Bevel Gears. To validated we have used tractor as a testing equipment and validate the gears to our design specification. Index Terms— Straight Bevel Gear, Spiral Bevel Gear Circular Pitch, Pressure Angle, Pitch Diameter, Tooth Parts. I. INTRODUCTION Power is supplied from the engine, via the gearbox, to a driveshaft, which runs to the drive axle. A pinion gear at the end of the propeller shaft is encased within the differential Figure 2: Differential Dynamics When Vehicle Takes Turn. itself, and it engages with the large crown-wheel. The crown-wheel is attached to a carrier, which holds a set of A general Gear manufacturing process contains the three-four small planetary straight bevel gears. The three following process- planetary gears are set up in such a way that the two outer gears (the side gears) can rotate in opposite directions relative to each other. The pair of side gears drive the axle shafts to each of the wheels. -
Performance Analysis of Bicycle Driven by Gear and Shaft Transmission System
INTERNATIONAL JOURNAL FOR RESEARCH IN EMERGING SCIENCE AND TECHNOLOGY, VOLUME-3, ISSUE-4, APR-2016 E-ISSN: 2349-7610 Performance Analysis of Bicycle Driven By Gear and Shaft Transmission System Vijayan.S.N1, Prabin.K.B2, Venkatasubramanian.D3, Pon madasamy.M4 and Sakthivel.M5 1Assistant Professor, Department of Mechanical Engineering, Karpagam Institute of Technology, Coimbatore, TamilNadu, India. 2,3,4,5UG Student, Department of Mechanical Engineering, Karpagam Institute of Technology, Coimbatore, TamilNadu, India Email [email protected] ABSTRACT The normal bicycle is the one of the medium of the travelling and used for riding, sports, riding in off road purposes. In recent years many accidents occurred in off-road riding bicycle due to the lack of torque required to drive and land the bicycle in its position and continue the ride safely specially in sports bicycle. The aim of this work is to overcome these problems by introducing new mechanical transmission system with the help of internal gear technology called shaft driven system to maximize the torque of off-road bicycle using gear and shaft transmission system with normal riding condition. A shaft driven bicycle is a bicycle that uses a shaft drive instead of a chain drive which contains two set of bevel gear at both the ends to make a new kind of transmission system and transmit motion through 90 degrees angle. It replaces the traditional methods and reduces the accidents to the hill riders. Keywords: bicycle, shaft, torque, transmission system. 1. INTRODUCTION The design of bevel gear produces less vibration and less noise A shaft-driven bicycle is a bicycle that uses a drive shaft than conventional straight-cut or spur-cut gear with the instead of a chain to transmit power from the pedals to the rear straight teeth. -
Analysis of Crown Pinion of a Differential Gear Box in Rear Axle to Improve Crown Life by Replacing Material with Existing One
© 2018 JETIR July 2018, Volume 5, Issue 7 www.jetir.org (ISSN-2349-5162) Analysis of Crown Pinion of a Differential Gear Box in Rear Axle To Improve Crown Life by Replacing Material with Existing One Prerana U. Jiwane Prof. (Dr.) Prashant D. Deshmukh Dhirajkumar K. More Research Scholar, M.E. - Professor & Project Guide Asst. Professor CAD/CAM & Robotics, Dept. of Mechanical Engg. Dept. of Mechanical Engg. Datta Meghe COE, Datta Meghe COE, Datta Meghe COE, Airoli, Navi Mumbai, India Airoli, Navi Mumbai, India Airoli, Navi Mumbai, India Abstract: Differential is an essential component of transmission system. The differential is designed to drive a pair of wheels with equal torque while allowing them to rotate at different speeds. For achieving different speed, gear train of differential must be designed in such a way that gears must transmit different speeds with efficient torque. In this project, regular metal used for gear is replaced by upgraded material to reduce vibrations and increase torque. In this project work, bevel pinion and crown gear present in the differential assembly is redesigned. The selected crown gear is the existing part of the SAFARI, the passenger car. In this project the crown and pinion material is replaced by upgraded material with more strength and durability of the gear set. Bevel pinion and crown gear are High efficiency gears (98 and higher) which can transfer power across non-intersecting shafts. Spiral bevel gears transmit loads evenly and are easy going than straight bevel.Here, Crown Gear is designed and analyzed for different speeds at 1200 rpm, 2000 rpm and 4000 rpm. -
Design of Chain Differential for a Race Car International Journal Of
International Journal of ChemTech Research CODEN (USA): IJCRGG, ISSN: 0974-4290, ISSN(Online):2455-9555 Vol.10 No.3, pp 225-228, 2017 Design of Chain Differential for a Race Car Bridjesh P*1, Vinayak J2, Teja N3 and Madhu S4 1,2,3,4Department of Mechanical Engineering, MLR Institute of Technology, Hyderabad, 500043, India. Abstract : This present study addresses the issue of acceleration efficiency by discussing the overall design of sprocket chain open differential. A special focus on sprocket and the material employed in production of chain differential and factors that leads to sprocket failure. It is an approach to invent the effective current methodology and technologies available to enhance to the overall differential and to avoid sprocket failure due to sprocket cracking. In particular, the effectiveness of certain steel alloys in resisting creep and fracture in differential sprocket. The effectiveness of hardening in protecting the sprocket substrate from cracking when exposed to load acting on it. Keywords: Design, Chain differential, Race car. Introduction The Differential is device which necessarily excludes the usage of gears and is mostly suitable for transmitting torque and turns through 3 shafts to receive one input and deliver to outputs this out puts later combine and forms the overall sum, difference, or average of the input 1 1. Open differential incorporates the adaptation of planetary gear set mechanism that enables to disturb torque evenly between drive axles and permit wheels to rotate and varying speeds 2. The input shafts facilities the transmission of torque from the drive line to the rig gear outside the differential carrier. -
Download the September/October 2001 Issue In
At G/,eas,on Cutting Tools, WE'RE TAKING PLATING IPlating Bath CIRCLE 110 GleasonCuttjng Toolsfa.cUity, Loves Park, IL. Our Loves Parle grinding' wheel plating facility is ,one,of the war/d's most advanced. Here's the alternative . ouree you've always wanted for ,.. your CBN and diamond grinding wheels. OUf plating facility now gives us the capability to produce a fun line of high-precision bevel and cylindrical electro-plated Ini.WgI'.mIftI I.' .. metal-bonded, single-layer, _ .._51 TaItIW'.IOI~""----,to 0011 replatable CBN and 2AS3" _ '. • diamond grinding wheeJs IUlln1l1l _ ..... QM. _. hrlll_Z·1 for use with any modem --T-.ProIl. --I!;....PI!I" ..r '"IIf.'ItI CNC profile grinding, gear --T~1In ~~ "2-"-0" ..... 1 20.:12'1 honing, grinding ".....IIIIIIII oCt'iODI'" -,-Jlctidil 22iM!iO"' or gear ---~rDIII'" JitdM 2215217 [22.'MO"I22.111O") Qra.nI"'" n ..,. TT 0 mt" Ie.!nOr 10 !I3&n machine. Higher stock removal rates, lower cost-per Typlcall grInding wheell customer' lest workpiece, longer wheel life, coupon Inspection report. and more consistent quality are the result We also offer fast turn-around and short delivery times from a stock wheel blank inventory in a variety of configurations and sizes. Get quick rum-around on stripping and replating services too. Hall 2 Stand C 10 Gleason Cutti 9 Tools CORPORATION t-....I ....... II I 1351 Windsor Road Phone: 815-877-8900 Beeth #132 ;[II 1]11 • I II. Loves Park, Il6H11 USA Fax: 815-8n·0264 Website: www.gleason.com IE-Mail:gctcCgleason.tom THE LATEST INNOVATION .IN HOSSING. -
Study and Test to Confirm Automobile Drivetrain Components To
HF NO. DOT-TSC-NHTSA-79-1 1 .1 DOT HS-803 855 18.5 .A 34 JJ NO, STUDY AND TEST TO CONFIRM AUTOMOB I LB- DOT- department of TSO- DR I VETRAI N COMPONENTS TO IMPROVE KWSA- TRANSPORTATION FUEL 79-11 ECONOMY v.l JUL 2 4 1979 VOLUME 1 library HI STORY OF THE AUTOMOBILE TRANSMISSION IN THE UNITED STATES Donald A. Hurter, Philip G. Gott, Carl A. Gottesman Arthur D . Li ttl e , Inc . Acorn Park Cambridge MA 02140 OfJjM/v, MAY 1979 INTERIM REPORT DOCUMENT IS AVAILABLE TO THE PUBLIC THROUGH THE NATIONAL TECHNICAL INFORMATION SERVICE, SPRINGFIELD, VIRGINIA 22161 r Prepared for U.S. DEPARTMENT OF TRANSPORTATION. National Highway Traffic Safety Administration Office of Research and Development Washington DC 20590 NOTICE This document is disseminated under the sponsorship of the Department of Transportation in the interest of information exchange. The United States Govern- ment assumes no liability for its contents or use thereof. NOTICE The United States Government does not endorse pro- ducts or manufacturers. Trade or manufacturers' names appear herein solely because they are con- sidered essential to the object of this report. y 1 I Technical Report Documentation Page 1 . Report No. 2. Government Accession Nc 3. Recipient's Catalog No. DOT HS-803 855 If' 4. Title and Subtitle 5. Report Date STUDY AND TEST TO CONFIRM AUTOMOBILE DRIVETRAIN May 1979 SA' COMPONENTS TO IMPROVE FUEL ECONOMY VOLUME I, HISTORY 6. Performing Organization Code -li 9.OF THE AUTOMOBILE TRANSMISSION IN THE UNITED STATES 8.10. Performing Organization Report No. 78471 7. -
Ildar Ilgizarovich Salaehov 4.Pmd
BIOSCIENCES BIOTECHNOLOGY RESEARCH ASIA, June 2016. Vol. 13(2), 859-864 Development of a Gear Box of the Truck Ildar Ilgizarovich Salakhov*, Ildus Rifovich Mavleev, Ildar Rafisovich Shamsutdinov, Damir Imamutdinovich Nuretdinov and Niyaz Ilgizarovich Salakhov Naberezhnochelninsky Institute (branch) «Kazan Federal University», Russian Federation, 423812, Naberezhnye Chelny, pr.Syuyumbike, 10A, http://dx.doi.org/10.13005/bbra/2107 (Received: 14 February 2016; accepted: 13 April 2016) The kinematic scheme hydromechanical differential high-torque CVT. Developed the design of the continuously variable transmission of the truck with a high-torque differential hydromechanical CVT. Key words: hydra-mechanical gear train, continuously variable transmission, differential hydra- mechanical variator, mechanical diagram, high-torque differential hydra-mechanical variator. Continuous variable transmission to operate at high pressure values enables to combine effectively the engine * Provide automatic torque control on the performance with different modes of the vehicle output shaft, without control systems, operation. However, the existing mechanical depending on the changes in the external continuous variable transmissions have a load and the control range of trucks1. significant disadvantage - the maximum transmittable torque of 300 ÷ 350 H-M, which 2 High torque differential hydro-mechanical prevents their use in trucks transmissions. The variator (HTHMV) continuous variable transmissions are still not High torque differential hydro-mechanical widely used in trucks transmissions also due to variator is designed for the continuous automatic their existing significant shortcomings as converting of rotary motion between the motor compared to mechanical speed transmission shaft and the shaft of the working body of the gearbox (size, weight, efficiency, production costs, machinery in order to ensure the optimal mode of etc.).