INDUCTION DIVERSITY Elotherm and IAS Overview SMS GROUP Leaders in Plant Construction and Machine Engineering
Total Page:16
File Type:pdf, Size:1020Kb
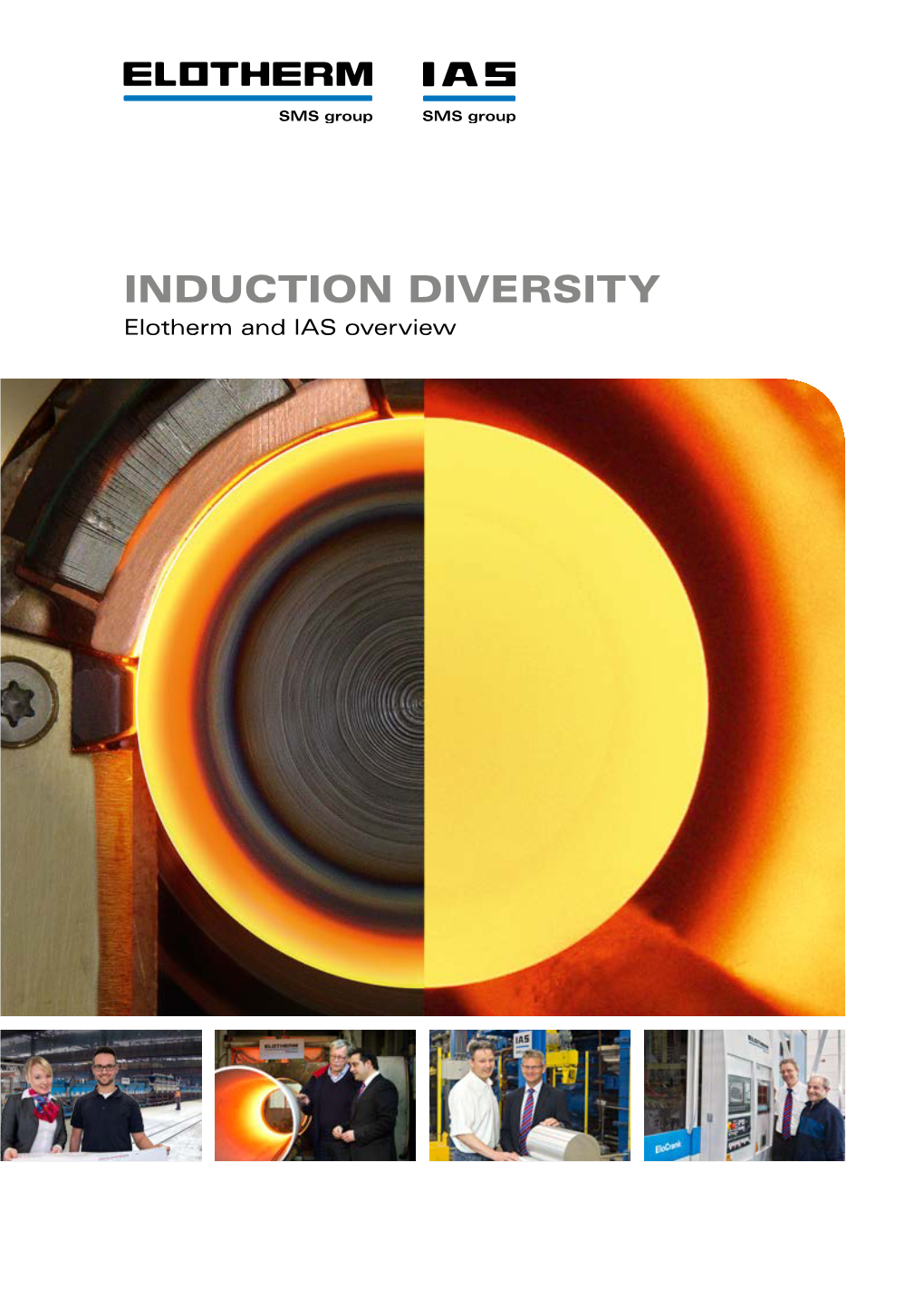
Load more
Recommended publications
-
Welding Process Reference Guide
Welding Process Reference Guide gas arc welding…………………..GMAW -pulsed arc…………….……….GMAW-P atomic hydrogen welding……..AHW -short circuiting arc………..GMAW-S bare metal arc welding…………BMAW gas tungsten arc welding…….GTAW carbon arc welding……………….CAW -pulsed arc……………………….GTAW-P -gas……………………………………CAW-G plasma arc welding……………..PAW -shielded……………………………CAW-S shielded metal arc welding….SMAW -twin………………………………….CAW-T stud arc welding………………….SW electrogas welding……………….EGW submerged arc welding……….SAW Flux cord arc welding…………..FCAW -series………………………..…….SAW-S coextrusion welding……………...CEW Arc brazing……………………………..AB cold welding…………………………..CW Block brazing………………………….BB diffusion welding……………………DFW Diffusion brazing…………………….DFB explosion welding………………….EXW Dip brazing……………………………..DB forge welding…………………………FOW Flow brazing…………………………….FLB friction welding………………………FRW Furnace brazing……………………… FB hot pressure welding…………….HPW SOLID ARC Induction brazing…………………….IB STATE BRAZING WELDING Infrared brazing……………………….IRB roll welding…………………………….ROW WELDING (8) ultrasonic welding………………….USW (SSW) (AW) Resistance brazing…………………..RB Torch brazing……………………………TB Twin carbon arc brazing…………..TCAB dip soldering…………………………DS furnace soldering………………….FS WELDING OTHER electron beam welding………….EBW induction soldering……………….IS SOLDERING PROCESS WELDNG -high vacuum…………………….EBW-HV infrared soldering…………………IRS (S) -medium vacuum………………EBW-MV iron soldering……………………….INS -non-vacuum…………………….EBW-NV resistance soldering…………….RS electroslag welding……………….ESW torch soldering……………………..TS -
Estimation of Weld Quality in High-Frequency Electric Resistance Welding with Image Processing
Kim March 2007 LAYOUT:Layout 1 2/8/07 2:30 PM Page 71 WELDING RESEARCH Estimation of Weld Quality in High-Frequency Electric Resistance Welding with Image Processing An image analysis algorithm can estimate the weld quality by using the weld image data during high-frequency electric resistance welding BY D. KIM, T. KIM, Y. W. PARK, K. SUNG, M. KANG, C. KIM, C. LEE, AND S. RHEE ABSTRACT. In high-frequency electric duction welding method, an induction coil surface is compressed by the squeeze resistance welding (HF-ERW), the weld is used in inducing high-frequency current roller, excreting oxided material from the quality is determined by the welding phe- to generate heat. In high-frequency resis- melting surface to generate a weld. The nomenon in the welding spot proximity. tance welding, on the contrary, a contac- molten part of the pipe generated by the Methods to eliminate or minimize defects, tor is applied to the workpiece to directly resistance heat contains oxided material therefore, include real-time monitoring of provide the current (Ref. 1). High- on account of exposure to the air. There- the weld quality and problem solving as frequency induction welding is primarily fore, if the oxided material is not com- problems arise. It is possible to estimate used in joining small-diameter steel pipes, pletely excreted during compression, and weld quality qualitatively by using the weld while HF-ERW is used in joining large- oxided material remains in the welding image data during HF-ERW. A method to diameter steel pipes. part as an impurity, the weld quality be- predict the weld quality using image pro- The characteristic of HF-ERW is the re- comes degraded. -
Can We Use Induction Heating to Weld Steel As a Fusion Welding Process?
International Journal of Scientific Engineering and Research (IJSER) ISSN (Online): 2347-3878 Index Copernicus Value (2015): 62.86 | Impact Factor (2015): 3.791 Can We Use Induction Heating to Weld Steel as a Fusion Welding Process? Hani A. Almubarak1, Abdulaziz I. Albannai2 Abstract: Using heat is very important for forming, joining, or treating most metals. Heat can be applied to metal by different processes, such as flame, ARC, friction, furnaces, and induction heating. This paper will focus on induction heating process, how it works, its advantages, applications, and if it can be used for welding steel as a fusion welding process? Using some sources is significant to buildup our point of view in this paper about using induction heating process for welding a steel as fusion welding. Keywords: Induction heating, steel, welding, and fusion 1. Introduction In the next figure (2),it is showing the “Eddy Currents” (black arrows in work-piece) flow against the electrical Induction heating uses high frequency electricity to heat resistivity of the metal work-piece. Without any direct electrically conductive materials (usually a metal). Eddy contact between the metal part and the inductor, this currents are generated within the metal where the metal generates a localized and precise heat .Both magnetic and resistance leads to its heating. This is done by the effect of non-magnetic parts can be heated in this way. This effect is the electromagnetic induction. The heat is generated inside related to the "Joule effect", a scientific formula expressing the work-piece, which is very efficient and a non-contact the relationship between heat produced by electrical current process. -
Induction Weld Seam Characterization of Continuously Roll Formed TRIP690 Tubes
metals Article Induction Weld Seam Characterization of Continuously Roll Formed TRIP690 Tubes Alexander Bardelcik * and Bharathwaj Thirumalai Ananthapillai School of Engineering, College of Engineering and Physical Sciences, University of Guelph, Guelph, ON N1G 2W1, Canada; [email protected] * Correspondence: [email protected]; Tel.: +1-519-824-4120 Received: 5 March 2020; Accepted: 20 March 2020; Published: 25 March 2020 Abstract: The weld seam characteristics of continuously roll formed and induction seam welded TRIP690 tubes were examined in this work. These tube are subsequently used in automotive hydroforming applications, where the weld seam characteristics are critical. The induction seam welds are created through a solid-state welding process and it was shown that by increasing the induction frequency by 26%, the weld seam width within the heat affected zone (HAZ) reduced due to a plateau in the hardness distribution which was a result of a delay in the transformation of martensite. 2D hardness distribution contours were also created to show that some of the weld conditions examined in this work resulted in a strong asymmetric hardness distribution throughout the weld, which may be undesirable from a performance perspective. An increase in the pressure roll force was also examined and revealed that a wider total weld seam width was produced likely due to an increase in temperature which resulted in more austenitization of the sheet edge prior to welding. The ring hoop tension test (RHTT) was applied to the tube sections created in this work. A Tensile and Notch style ring specimen were tested and revealed excellent performance for these welds due to high peak loads (~17.2 kN) for the Notch specimens (force deformation within weld) and lower peak loads (~15.2 kN) for the Tensile specimens for which fracture occurred in the base metal. -
Analysis of Induction Heating System for High Frequency Welding
FACTA UNIVERSITATIS Ser: Elec. Energ. Vol. 25, No 3, December 2012, pp. 183 - 191 DOI: 10.2298/FUEE1203183I ANALYSIS OF INDUCTION HEATING SYSTEM FOR HIGH FREQUENCY WELDING Ilona Iatcheva, Georgi Gigov, Georgi Kunov, Rumena Stancheva Technical University of Sofia, Bulgaria Abstract. The aim of the work is the investigation of induction heating system used for longitudinal, high frequency pipe welding.Coupled electromagnetic and temperature field distribution has been studied in order to estimate system efficiency and factors influencing the quality of the welding process and required energy. The problem was considered as three dimensional. Time harmonic electromagnetic and transient thermal field has been solved using finite element method and COMSOL 4.2 software package. Key words: induction heating, high frequency welding, 3D analysis, finite element method, coupled field problem 1. INTRODUCTION Technologies based on induction heating are widely used in industry due to their advantages: high energy efficiency, excellent product quality, very good accuracy in heating of certain zones in a short time, clean operating conditions [1]-[3]. Induction heating has a great variety of industrial applications [4]: induction hardening, induction tempering, induction brazing, induction bonding, induction welding, induction annealing, induction pre and post-heating, induction forging, induction melting, induction straight- ening, induction plasma production, etc. The object of the study in this investigation is an induction heating system, used for high frequency longitudinal pipe welding. The aim of the research and motivation for car- rying out the work is the necessity of development, analyzing and estimating of the system. The main task is to define and then to determine optimal factors and parameters influencing the welding process quality and required energy. -
Induction Welding of High Performance Thermoplastic Composites
Induction welding of high performance thermoplastic composites Focused heat generation in weld zones of carbon fiber laminates by magnetic field manipulation and carbon fiber susceptors M.C. Dhondt Student no: 4274318 Induction welding of high performance thermoplastic composites Focused heat generation in weld zones of carbon fiber laminates by magnetic field manipulation and carbon fiber susceptors by M.C. Dhondt to obtain the degree of Master of Science at the Delft University of Technology, Student number: 4274318 Project duration: February 18, 2019 – December 20, 2019 Thesis committee: Dr.-Ing. Jan Stüve, TU Delft Prof. C.A. Dransfeld, TU Delft Dr.ing. S. Giovani Pereira Castro, TU Delft M.Sc. Niklas Menke DLR Preface Before you lies the dissertation “Induction welding of high performance thermoplastic com- posites: focused heat generation in weld zones of carbon fiber laminates by magnetic field manipulation and carbon fiber susceptors”. It has been written to obtain a master’s degree in Aerospace Structures and Materials from the Delft University of Technology. The thesis was sponsored by and executed at the German Aerospace Center (DLR) in Stade, Germany. This report is written for anybody interested in induction welding of thermoplastic composites with some background knowledge on composites. It can be read to gain knowledge on the principles of induction welding of thermoplastic composites, to get familiarized with its current state of the art, to get to know about the influence the magnetic field direction has on the heating of multidirectional laminates, to learn about what carbon fiber material heats up more than average and whether this can be used as a benefit in induction welding. -
Introduction to Welding Engineering
1 Introduction to Welding Engineering 1.1. History and Development of Welding The first historical reference about welding is given in Bible and Tubal-Cain was the first smith who forged the instruments of bronze and iron. About 5000 years back the forge, hammer, anvil, bellows and fire heaters were used for forging. It was in the year 1887 that Thomas Fletcher of Warrington invented various blow pipes for burning hydrogen or coal gas with air or oxygen. The bicycle frames were manufactured with the help of these blow pipes. This type of blow pipe is used even today where acetylene gas is used in place of hydrogen or coal gas. In 1892, acetylene gas was first discovered by Thomas Leopold Wilson of North Carolina. In 1886, two Frenchmen, the Brins brothers formed a company for the liquefaction of air from which pure oxygen was obtained. The only acetylene welding blow pipe was invented by Fouche and Picard. Volta, after whom the term volt is named, demonstrated in 1800 that the electric arc could be used for melting iron wire and the process of fusion of metals by electricity was born. A swedish marine engineer thought of protecting the arc with an inert gas. This gas, he produced by applying a flux to the electrode. The flux melts and vaporises in the intense heat of the welding arc, protects the molten metal from the air and can be used to add alloying elements to the welding wire. Many advances have been made since these early days. Auto- mation has added to them, welding arcs and cutting flames, electronically guided arc, gas combined with electricity in hydrogen, helium and argon arcs. -
Welding Thermoplastic Composites
Welding thermoplastic composites Multiple methods advance toward faster robotic welds using new technology for increased volumes and larger aerostructures. By Ginger Gardiner / Senior Editor » Unlike composites made with a thermoset matrix, thermoplastic composites (TPCs) require neither complex chemical reactions nor lengthy curing processes. Thermoplastic prepregs require no refrig- eration, offering practically infinite shelf life. The polymers used in aerospace TPCs — polyphenylene sulfide (PPS), polyetherimide (PEI), polyetheretherketone (PEEK), polyetherketoneketone (PEKK) and polyarylketone (PAEK) — offer high damage toler- ance in finished parts, as well as moisture and chemical resistance and, thus, do not degrade in hot/wet conditions. And they can be remelted, promising benefits in repair and end-of-life recyclability. But perhaps the greatest driver for TPC use in developing aircraft is the ability to join components via fusion bonding/welding. It Induction welded window frame for TPC fuselage presents an attractive alternative to the conventional methods — This compression molded short CF/PPS reinforcement ring, induction welded to mechanical fastening and adhesive bonding — used to join ther- a TenCate CF/PPS CETEX skin by KVE Composites (Den Haag, The Netherlands), moset composite (TSC) parts. demonstrates how window frames could be assembled in future TPC airframes. As defined in the widely cited paper, “Fusion Bonding/Welding Source | KVE Composites / Photo | Ginger Gardiner 50 SEPTEMBER 2018 CompositesWorld Welding ThermoplasticsNEWS FIG. 1 Advanced Thermoplastic Composite Welding Technologies of Thermoplastic Composites,” by Ali Yousefpour, National Resistance welding Research Council Canada (Ottawa, ON, Canada), “The process of Along with KVE Composites Group (The Hague, The Nether- fusion-bonding involves heating and melting the polymer on the lands), GKN Fokker is an acknowledged leader in TPC welding bond surfaces of the components and then pressing these surfaces development (see Learn More, p. -
Principles of High Frequency Induction Tube Welding
PRINCIPLES of INDUCTION TUBE WELDING PRINCIPLES OF HIGH FREQUENCY INDUCTION TUBE WELDING By JOHN WRIGHT Electronic Heating Equipment, Inc. Sumner, Washington Page 1 © 1997 Electronic Heating Equipment, Inc. Page 1 PRINCIPLES of INDUCTION TUBE WELDING Introduction and it is inductance rather than resistance that governs current flow at high frequencies. This is High Frequency induction welding accounts for the sometimes refered to as “proximity effect”. majority of welded tubing produced worldwide, yet it is still a largely misunderstood process. Part of the It can be seen from this that there are two main reason is that the process is very forgiving, however a paths along which current can flow when a voltage is thorough understanding of it can lead to higher applied or induced across the edges of the strip. The product yields and quality. key to operating a high frequency welder efficiently is to direct the majority of the current along the faying Principals of operation edges where it does useful work in heating them, and minimise the wasteful parasitic current that flows around the inside surface of the tube.This is done by Induction welding is a form of Electrical Resistance making the impedance of the vee low relative to that Welding (ERW) in which the large rotary trans- of the I.D. surface. former common in low frequency ERW is replaced by a “virtual transformer” consisting of the work coil Function of impeder (primary winding) and the tube itself (secondary winding). A ferromagnetic core inside the tube has a similar role to the laminated iron core in a conven- The first tool we have is called an impeder because it tional transformer. -
0021998315614991 Publication Date 2016 Document Version Final Published Version Published in Journal of Composite Materials
Delft University of Technology Modeling and experimental investigation of induction welding of thermoplastic composites and comparison with other welding processes Gouin O'Shaughnessey, Patrice; Dube, M; Fernandez Villegas, Irene DOI 10.1177/0021998315614991 Publication date 2016 Document Version Final published version Published in Journal of Composite Materials Citation (APA) Gouin O'Shaughnessey, P., Dube, M., & Fernandez Villegas, I. (2016). Modeling and experimental investigation of induction welding of thermoplastic composites and comparison with other welding processes. Journal of Composite Materials, 50(21), 2895-2910. https://doi.org/10.1177/0021998315614991 Important note To cite this publication, please use the final published version (if applicable). Please check the document version above. Copyright Other than for strictly personal use, it is not permitted to download, forward or distribute the text or part of it, without the consent of the author(s) and/or copyright holder(s), unless the work is under an open content license such as Creative Commons. Takedown policy Please contact us and provide details if you believe this document breaches copyrights. We will remove access to the work immediately and investigate your claim. This work is downloaded from Delft University of Technology. For technical reasons the number of authors shown on this cover page is limited to a maximum of 10. JOURNAL OF COMPOSITE Article MATERIALS Journal of Composite Materials 2016, Vol. 50(21) 2895–2910 ! The Author(s) 2015 Modeling and experimental investigation Reprints and permissions: sagepub.co.uk/journalsPermissions.nav of induction welding of thermoplastic DOI: 10.1177/0021998315614991 jcm.sagepub.com composites and comparison with other welding processes Patrice Gouin O’Shaughnessey1, Martine Dube´ 1 and Irene Fernandez Villegas2 Abstract A three-dimensional finite element model of the induction welding of carbon fiber/polyphenylene sulfide thermoplastic composites is developed. -
A Comparative Study of Arc Welding and Resistance Welding Processes
November 2017, Volume 4, Issue 11 JETIR (ISSN-2349-5162) A COMPARATIVE STUDY OF ARC WELDING AND RESISTANCE WELDING PROCESSES 1Dr. Kailash Chaudhary Professor Department of Mechanical Engineering Raj Engineering College Jodhpur, India Abstract: This paper makes an in-depth comparative study of arc welding and resistance welding processes. The objective is to present the current challenges and future aspects of these welding processes and their usefulness as fabrication technology. The importan t considerations and application areas of both the techniques are discussed in this paper. 1INTRODUCTION The American Welding Society (AWS) defines welding as “a materials joining process which produces coalescence of materials by heating them to suitable temperatures with or without the application of pressure or by the application of pressure alone and with or with out the use of filler material" [1]. Mechanical parts are often highly complicated in design or large in size. Manufacturing a unit of such a part as a single ent ity is not always possible. However, it can be produced in the form of different components or structures and could be joined by several joining processes to get the complete unit or assembly. It is here that welding has been found the most useful fabrication technology in joining diffe rent components and synthesizing them into a whole system. 2ARC WELDING PROCESS ES One of the most popular and common types of welding in use today is arc welding. It uses an electric arc as the source of hea t to melt and join metals. The arc is formed between the metal being worked on and an electrode connected to the arc welder. -
Radio Frequency Induction Welding of Silver Nanowire Networks for Transparent Heat Films
materials Article Radio Frequency Induction Welding of Silver Nanowire Networks for Transparent Heat Films Jisoo Oh 1,†, Long Wen 1,†, Hyunwoo Tak 1, Heeju Kim 1 , Gyowun Kim 1, Jongwoo Hong 1 , Wonjun Chang 1 , Dongwoo Kim 1 and Geunyoung Yeom 1,2,* 1 School of Advanced Materials Science and Engineering, Sungkyunkwan University, Suwon 16419, Korea; [email protected] (J.O.); [email protected] (L.W.); [email protected] (H.T.); [email protected] (H.K.); [email protected] (G.K.); [email protected] (J.H.); [email protected] (W.C.); [email protected] (D.K.) 2 SKKU Advanced Institute of Nano Technology (SAINT), Sungkyunkwan University, Suwon 16419, Korea * Correspondence: [email protected] † Both authors contributed equally to this work. Abstract: Transparent heat films (THFs) are attracting increasing attention for their usefulness in various applications, such as vehicle windows, outdoor displays, and biosensors. In this study, the effects of induction power and radio frequency on the welding characteristics of silver nanowires (Ag NWs) and Ag NW-based THFs were investigated. The results showed that higher induction frequency and higher power increased the welding of the Ag NWs through the nano-welding at the junctions of the Ag NWs, which produced lower sheet resistance, and improved the adhesion of the Ag NWs. Using the inductive welding condition of 800 kHz and 6 kW for 60 s, 100 ohm/sq of Ag NW thin film with 95% transmittance at 550 nm after induction heating could be decreased to 56.13 ohm/sq, without decreasing the optical transmittance. In addition, induction welding of the Ag NW-based THFs improved haziness, increased bending resistance, enabled higher operating Citation: Oh, J.; Wen, L.; Tak, H.; Kim, H.; Kim, G.; Hong, J.; Chang, W.; temperature at a given voltage, and improved stability.