Developing an Analytical Model and Computing Tool for Optimizing Lapping Operations of Flat Objects Made of Alloyed Steels
Total Page:16
File Type:pdf, Size:1020Kb
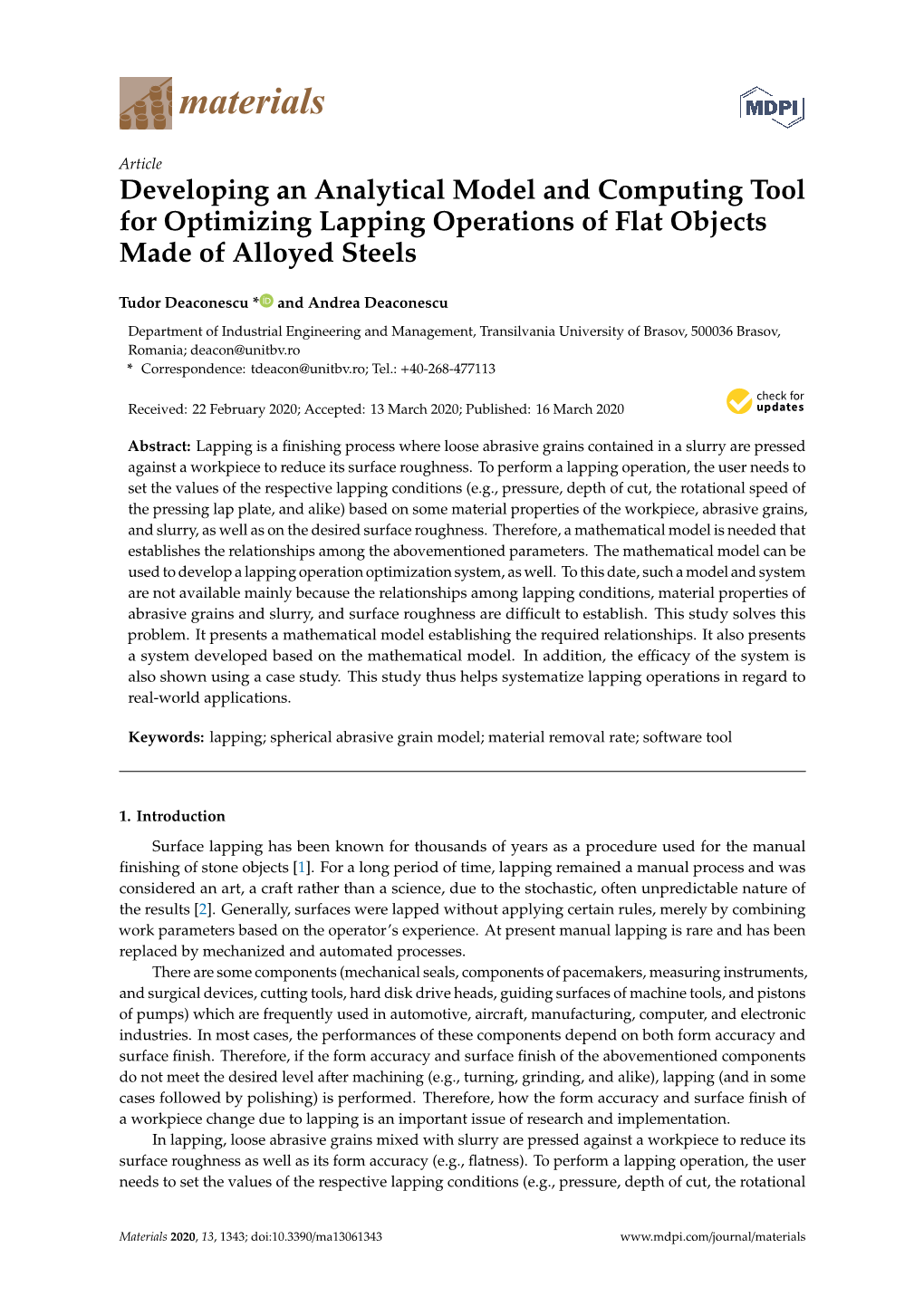
Load more
Recommended publications
-
Review of Superfinishing by the Magnetic Abrasive Finishing Process
High Speed Mach. 2017; 3:42–55 Review Article Open Access Lida Heng, Yon Jig Kim, and Sang Don Mun* Review of Superfinishing by the Magnetic Abrasive Finishing Process DOI 10.1515/hsm-2017-0004 In the conventional lapping process, loose abrasive Received May 2, 2017; accepted June 20, 2017 particles in the form of highly-concentrated slurry are of- ten used. The finishing mechanism then involves actions Abstract: Recent developments in the engineering indus- between the lapping plate, the abrasive, and the work- try have created a demand for advanced materials with su- piece, in which the abrasive particles roll freely, creating perior mechanical properties and high-quality surface fin- indentation cracks along the surface of the workpiece, ishes. Some of the conventional finishing methods such as which are then removed to finally achieve a smoother sur- lapping, grinding, honing, and polishing are now being re- face [1]. The lapping process typically is not used to change placed by non-conventional finishing processes. Magnetic the dimensional accuracy due to its very low material re- Abrasive Finishing (MAF) is a non-conventional superfin- moval rate. Grinding, on the other hand, is used to achieve ishing process in which magnetic abrasive particles inter- the surface finish and dimensional accuracy of the work- act with a magnetic field in the finishing zone to remove piece simultaneously [2]. In grinding, fixed abrasives are materials to achieve very high surface finishing and de- used by bonding them on paper or a plate for fast stock burring simultaneously. In this review paper, the working removal. -
Big Performance
AUGUST 2008 / VOLUME 60 / ISSUE 8 All images: Sunnen Products A motorcycle connecting rod is honed to a diameter of 1.4173", +0.0001"/-0.0003", with roundness of 0.00008", straightness of 0.00004" and cylindricity of 0.0001". Small Engines, By Rich Moellenberg, Sunnen Products Co. Big Performance Honing of cylinder bores improves sealing and component life to help small internal combustion engines increase power density and reduce exhaust emissions. changing federal regulatory climate that targets their big brothers on the NASCAR circuit, these reduced emissions and noise has led to a con- engines are also beginning to share a performance- vergence of design goals for both small internal enhancing technology used for racecar and most combustion engines and automotive engines other auto engines—honing. Honing optimizes the in the last decade. Today, small-engine OEMs cylinder bore’s geometry, surface finish and dimen- are striving for higher power densities (producing sional accuracy, boosting power density, extending more horsepower and torque from an engine with life and lowering emissions. the same physical size), lower fuel consumption and The fit between the piston and bore, along with lower emissions, all while controlling costs. the quality of the surface contact between the two, Engines for outdoor power equipment, ATVs, influences power output, combustion efficiency, snowmobiles, motorcycles and outboard motors, emissions, component life and vibration. The pre- along with many piston-type air and refrigeration cision of bore geometry (roundness, straightness, compressors, share a common operating principle— cylindricity and diameter) and surface finish play a piston reciprocates in a cylinder bore. -
Effect of Aluminum Oxide and Silicon Carbide Abrasive Type on Stainless Steel Ground Surface Integrity
EFFECT OF ALUMINUM OXIDE AND SILICON CARBIDE ABRASIVE TYPE ON STAINLESS STEEL GROUND SURFACE INTEGRITY MUHD SYAKIR BIN ABDUL RAHMAN Report submitted in partial fulfillment of the requirements for the award of Bachelor of Mechanical Engineering with Manufacturing Faculty of Mechanical Engineering UNIVERSITI MALAYSIA PAHANG DECEMBER 2010 ii SUPERVISOR’S DECLARATION I hereby declare that I have checked this project and in my opinion, this project is adequate in terms of scope and quality for the award of the degree of Bachelor of Mechanical Engineering. Signature: Name of Supervisor: DR. MAHADZIR BIN ISHAK @ MUHAMMAD Position: LECTURER OF MECHANICAL ENGINEERING Date: 6 DECEMBER 2010 iii STUDENT’S DECLARATION I hereby declare that the work in this report is my own except for quotations and summaries which have been duly acknowledged. The report has not been accepted for any degree and is not concurrently submitted for award of other degree. Signature: Name: MUHD SYAKIR BIN ABDUL RAHMAN ID Number: ME07013 Date: 6 DECEMBER 2010 v ACKNOWLEDGEMENTS In the name of Allah, the Most Benevolent, the Most Merciful. First of all I wish to record immeasurable gratitude and thankfulness to the One and The Almighty Creator, the Lord and Sustainers of the universe, and the Mankind in particular. It is only had mercy and help that this work could be completed and it is keenly desired that this little effort be accepted by Him to be some service to the cause of humanity. I would like to express my sincere gratitude to my supervisor DR. Mahadzir Bin Ishak @ Muhammad for his germinal ideas, invaluable guidance, continuous encouragement and constant support in making this research possible. -
Geometric Modeling of Engineered Abrasive Processes Andres L
Rochester Institute of Technology RIT Scholar Works Articles 2005 Geometric Modeling of Engineered Abrasive Processes Andres L. Carrano Rochester Institute of Technology James B. Taylor Rochester Institute of Technology Follow this and additional works at: http://scholarworks.rit.edu/article Recommended Citation Carrano AL, Taylor JB. Geometric modeling of engineered abrasive processes. J Manuf Process 2005;7(1):17–27. https://doi.org/ 10.1016/S1526-6125(05)70078-5 This Article is brought to you for free and open access by RIT Scholar Works. It has been accepted for inclusion in Articles by an authorized administrator of RIT Scholar Works. For more information, please contact [email protected]. *Geometric Modeling of Engineered Abrasive Processes* Carrano, Andres L Abstract One of the common issues that arises in abrasive machining is the inconsistency of the surface roughness within the same batch and under identical machining conditions. Recent advances in engineered abrasives have allowed replacement of the random arrangement of minerals on conventional belts with precisely shaped structures uniformly cast directly onto a backing material. This allows for abrasive belts that are more deterministic in shape, size, distribution, orientation, and composition. A computer model based on known tooling geometry was developed to approximate the asymptotic surface profile that was achievable under specific loading conditions. Outputs included the theoretical surface parameters, R^sub q^, R^sub a^, R^sub v^, R^sub p^, R^sub t^, and R^sub sk^. Experimental validation was performed with a custom-made abrader apparatus and using engineered abrasives on highly polished aluminum samples. Interferometric microscopy was used in assessing the surface roughness. -
A Gentle Introduction to Abrasive (Waterjet) Machining Brought to You by the MIT Fablab Staff
A Gentle Introduction to Abrasive (Waterjet) Machining Brought to you by the MIT FabLab Staff. In this brief two part tutorial we will give you a jump start toward making your first project parts utilizing the Department of Architecture’s new OMAX waterjet machine. In Part I we assume that you have access to a computer running the OMAX Layout software required to define new geometry or import your previously defined part geometry and then create tool paths based on this geometry. In Part II we assume that you have access to the actual waterjet machine itself, the OMAX Make software which controls the physical machine, as well as knowledgeable lab monitor or staff member who’ll be able to help with any questions or safety issues that might arise. First, a little background information about abrasive machining: The OMAX 2652 is a relatively new type of machine tool which uses a very high pressure (> 50k psi) stream of water and garnet abrasive to cut virtually any kind of material by eroding the material along an arbitrarily complex tool path that you define, leaving a thin (~0.025”), kerf. Both thin and thick materials such as aluminum, steel and stainless steel, plastics such Plexiglas and Lexan, rubber, brick and glass, and even wood may be cut on a waterjet. Material thickness can range from 1/16” through 4”, even when cutting very hard materials. Some special precautions and procedures are required for cutting brittle or very thin materials. The procedures and techniques required to use the OMAX waterjet are pretty straightforward and quick to learn. -
UC Berkeley Consortium on Deburring and Edge Finishing
UC Berkeley Consortium on Deburring and Edge Finishing Title Advancing Cutting Technology Permalink https://escholarship.org/uc/item/7hd8r1ft Authors Byrne, G. Dornfeld, David Denkena, B. Publication Date 2003 Peer reviewed eScholarship.org Powered by the California Digital Library University of California Advancing Cutting Technology G. Byrne1 (1), D. Dornfeld2 (1), B. Denkena3 1 University College Dublin, Ireland 2 University of California, Berkeley, USA 3 University of Hannover, Germany Abstract This paper reviews some of the main developments in cutting technology since the foundation of CIRP over fifty years ago. Material removal processes can take place at considerably higher performance levels 3 in the range up to Qw = 150 - 1500 cm /min for most workpiece materials at cutting speeds up to some 8.000 m/min. Dry or near dry cutting is finding widespread application. The superhard cutting tool materi- als embody hardness levels in the range 3000 – 9000 HV with toughness levels exceeding 1000 MPa. Coated tool materials offer the opportunity to fine tune the cutting tool to the material being machined. Machining accuracies down to 10 µm can now be achieved for conventional cutting processes with CNC machine tools, whilst ultraprecision cutting can operate in the range < 0.1µm. The main technological developments associated with the cutting tool and tool materials, the workpiece materials, the machine tool, the process conditions and the manufacturing environment which have led to this advancement are given detailed consideration in this paper. The basis for a roadmap of future development of cutting tech- nology is provided. Keywords: Cutting, Material Removal, Process Development ACKNOWLEDGEMENTS geometrie”. -
Grinding and Other Abrasive Processes
GRINDING AND OTHER ABRASIVE PROCESSES •Grinding •Related Abrasive Process ©2002 John Wiley & Sons, Inc. M. P. Groover, “Fundamentals of Modern Manufacturing 2/e” Abrasive Machining Material removal by action of hard, abrasive particles usually in the form of a bonded wheel •Generally used as finishing operations after part geometry has been established y conventional machining •Grinding is most important abrasive processes •Other abrasive processes: honing, lapping, superfinishing, polishing, and buffing ©2002 John Wiley & Sons, Inc. M. P. Groover, “Fundamentals of Modern Manufacturing 2/e” Why Abrasive Processes are Important •Can be used on all types of materials •Some can produce extremely fine surface finishes, to 0.025 m (1 -in) •Some can hold dimensions to extremely close tolerances ©2002 John Wiley & Sons, Inc. M. P. Groover, “Fundamentals of Modern Manufacturing 2/e” Grinding Material removal process in which abrasive particles are contained in a bonded grinding wheel that operates at very high surface speeds •Grinding wheel usually disk-shaped and precisely balanced for high rotational speeds ©2002 John Wiley & Sons, Inc. M. P. Groover, “Fundamentals of Modern Manufacturing 2/e” The Grinding Wheel •Consists of abrasive particles and bonding material Abrasive particles accomplish cutting Bonding material holds particles in place and establishes shape and structure of wheel ©2002 John Wiley & Sons, Inc. M. P. Groover, “Fundamentals of Modern Manufacturing 2/e” Grinding Wheel Parameters •Abrasive material •Grain size •Bonding material •Wheel grade •Wheel structure ©2002 John Wiley & Sons, Inc. M. P. Groover, “Fundamentals of Modern Manufacturing 2/e” Abrasive Material Properties •High hardness •Wear resistance •Toughness •Friability - capacity to fracture when cutting edge dulls, so a new sharp edge is exposed ©2002 John Wiley & Sons, Inc. -
Grinding Grinding Is the Most Common Form of Abrasive Machining. It Is Acutting Process Which Engages an Abrasive Tool Whose
Grinding Grinding is the most common form of abrasive machining. It is acutting process which engages an abrasive tool whose cutting elements are grains of abrasive material known as grit. The grits are held together by a suitable bonding material to give shape of an abrasive tool. Advantages of grinding • dimensional accuracy • good surface finish • good form and locational accuracy • applicable to both hardened and unhardened material. Applications of grinding •surface finishing • slitting and parting • descaling, deburring • stock removal (abrasive milling) • finishing of flat as well as cylindrical surface • grinding of tools and cutters and resharpening of the same . Conventional grinding machines are classified as: (a) Surface grinding machine (b) Cylindrical grinding machine (c) Internal grinding machine (d) Tool and cutter grinding machine a)Surface grinding machine: This machine may be similar to a milling machine used mainly to grind flat surface. However, some types of surface grinders are also capable of producing contour surface with formed grinding wheel. Basically there are four different types of surface grinding machines characterised by the movement of their tables and the orientation of grinding wheel spindles as follows: • Horizontal spindle and reciprocating table • Vertical spindle and reciprocating table • Horizontal spindle and rotary table • Vertical spindle and rotary table B)Cylindrical grinding machine This machine is used to produce external cylindrical surface. The surfaces may be straight, tapered, steps or profiled. Broadly there are three different types of cylindrical grinding machine as follows: 1. Plain centre type cylindrical grinder 2. Universal cylindrical surface grinder 3. Centreless cylindrical surface grinder Plain centre type cylindrical grinder Universal cylindrical surface grinder Centreless grinder C)Internal grinding machine This machine is used to produce internal cylindrical surface. -
New Highly Efficient Methods of Machining Metals
Ye. Dlugash, Junior specialist student T. Rishan, teacher of technology of machine-building, research advisor N. Barbelko, PhD in Pedagogy, language advisor Berdychiv College of Industry, Economics and Law NEW HIGHLY EFFICIENT METHODS OF MACHINING METALS The requirements to quality and reliability of mechanical parts are constantly increased. New highly efficient methods of machining metals are used for increasing the firmness of details to the wear, resistance to corrosion to the action of aggressive substances and improvement of other operating indexes. These machining methods have already found wide application in a modern engineering, such as the electrophysical and electrochemical machining methods. This article deals with such new highly efficient machining methods of metals as electrical discharge, ultrasonic, beam and electrochemical machining methods. Main advantages of these methods are: possibility of machining of difficult form parts with playback of instrument form; a capacity to treat of materials of any hardness and viscosity; possibility of machining of the curvilinear and spiral holes, producing of the very small holes, narrow and deep slots; absence of distortions of materials structures; possibility to use of instruments, which made of less durable materials than workpiece; an increasing of the labour productivity and simplification of equipment during treatment of especially difficult parts. All types of electrophysical and electrochemical machining methods can be divided into such categories: electrical discharge, electrochemical, ultrasonic, electron beam and combined. In all these methods of machining removal of assumption is made due to electric or chemical erosion. The general disadvantage of these machining methods is a substantial increasing of energy intensity of processes. -
ABSTRACT Kametz, David Austin. Precision Fabrication and Development of Charging and Testing Methods of Fixed-Abrasive Lapping P
ABSTRACT Kametz, David Austin. Precision Fabrication and Development of Charging and Testing Methods of Fixed-Abrasive Lapping Plates. (Under the direction of Dr. Thomas A. Dow.) The recording head industry is one of the dominant users of advanced ceramics such as alumina, silicon nitride, silicon carbide and AlTiC. The high hardness of these materials makes diamond the optimal abrasive for machining. One challenge when manufacturing recording heads for rigid disk drives is to generate surfaces that are both planar and smooth. Flatness tolerances are in the range of a few tens of nanometers to a few hundred nanometers per millimeter of length [1]. Roughness tolerances are in the range of a few nanometers to the subnanometer range [1]. Fixed-abrasive lapping, sometimes called nanogrinding, is a common method of machining used on ceramics. Fixed- abrasive lapping is generally a two-body abrasive process, with the abrasive grain fixed in the lapping plate that produces an extremely smooth surface due to the controlled depth of cut. The process of fabricating a quality fixed-abrasive lapping plate is a lengthy and sometimes demanding process. The goals of this research are to investigate the current fabrication process for improvements in surface texture quality, charging time and waste reduction of abrasive as well as the development of methods and equipment capable of estimating the lapping qualities of the plate during it’s fabrication process. The improvement of this process will reduce plate fabrication time and improve lapping performance. Current processes used to fabricate a plate can require 2 hours or more, and often the lapping quality of the plate is unknown until it is used. -
Elimination of Honing Stick Mark in Rack Tube B.Parthiban11, N.Arul Kumar2, K.Gowtham Kumar3, P.Karthic4, R.Logesh Kumar5 Assistant Professor, Dept
ISSN(Online) : 2319-8753 ISSN (Print) : 2347-6710 International Journal of Innovative Research in Science, Engineering and Technology (An ISO 3297: 2007 Certified Organization) Website: www.ijirset.com Vol. 6, Issue 3, March 2017 Elimination of Honing Stick Mark in Rack Tube B.Parthiban11, N.Arul Kumar2, K.Gowtham Kumar3, P.Karthic4, R.Logesh Kumar5 Assistant Professor, Dept. of Mechanical Engineering, Jay Shriram Group of Institutions. Tiruppur, Tamilnadu, India UG Student, Dept. of Mechanical Engineering, Jay Shriram Group of Institutions. Tiruppur, Tamilnadu, India.2,3,4,5 ABSTRACT: The main objective of the project is to reduce the tool tip mark produced during honing process in rack tube manufacturing. Rack tube is used in power steering, the hydraulic fluid acts inside the cylinder walls. Honing is an internal finishing process that uses abrasive particles on a rotating tool to produce extremely accurate dimensions and smooth surface finish. Similar to grinding and lapping process the abrasive particles are mounted on the rotating tool. During machining process tool have the working motion (both rotating and reciprocating motion). Work piece does not perform any motion. By the application of pressure acting on the tool, the tip marks are produced inside the work piece. To overcome this draw back. By changing the grain size of the hone stone the tool tip mark has been reduced and productivity increased KEYWORDS: honing machine, stick mark, spindle, abrasive stick I. INTRODUCTION Honing is an internal finishing process that uses abrasives on a rotating tool to produce extremely accurate holes that require a very smooth finish. Honing is a low velocity abrasive machining process in which a tool called hone carries out a combined rotary and reciprocating motion. -
Mechanical Performance of Abrasive Sandpaper Made with Palm Kernel
Journal of the Mechanical Behavior of Materials 2021; 30:28–37 Research Article Hameed Sa’ad, Bamidele D. Omoleyomi, Elijah A. Alhassan*, Ezekiel O. Ariyo, and Taiwo Abadunmi Mechanical performance of abrasive sandpaper made with palm kernel shells and coconut shells https://doi.org/10.1515/jmbm-2021-0004 Received Oct 07, 2020; accepted Mar 01, 2021 1 Introduction Abstract: The use of agricultural wastes as additives for An increase in population coupled with a corresponding other valuable products has been the focus of many re- increase in demand for agricultural products has resulted search efforts because of their availability, inherent prop- in enormous generations of agricultural wastes that pose erties, and environmental friendliness. Palm kernel shells a challenge to farmers in terms of their proper handling, (PKS) and coconut shells (CNS) are agricultural solid end management, and disposal. Most often in Nigeria’s farm- products obtainable from the cracking of their fruit nuts. ing perspective, these wastes have near-zero commercial In this study, PKS and CNS were used to produce abrasive or economic usage hence constituting a menace to the en- sandpaper following established procedures. The mechani- vironment [1]. Their alternative utilization as raw materi- cal properties of the sandpaper produced were established. als for other valuable products has recently gained atten- Material for application in abrasive operations must exhibit tion among researchers. Hence, an increased interest in maximum hardness and compressive strength, minimal the effective and efficient ways of appropriating agricul- wear rate, water absorption, and density. Results showed a tural wastes as an alternative source of raw materials [2, 3].