FLIGHT TEST RESULTS of a SUBSCALE SUPER-STOL AIRCRAFT Christopher B. Courtin, R. John Hansman, Mark Drela
Total Page:16
File Type:pdf, Size:1020Kb
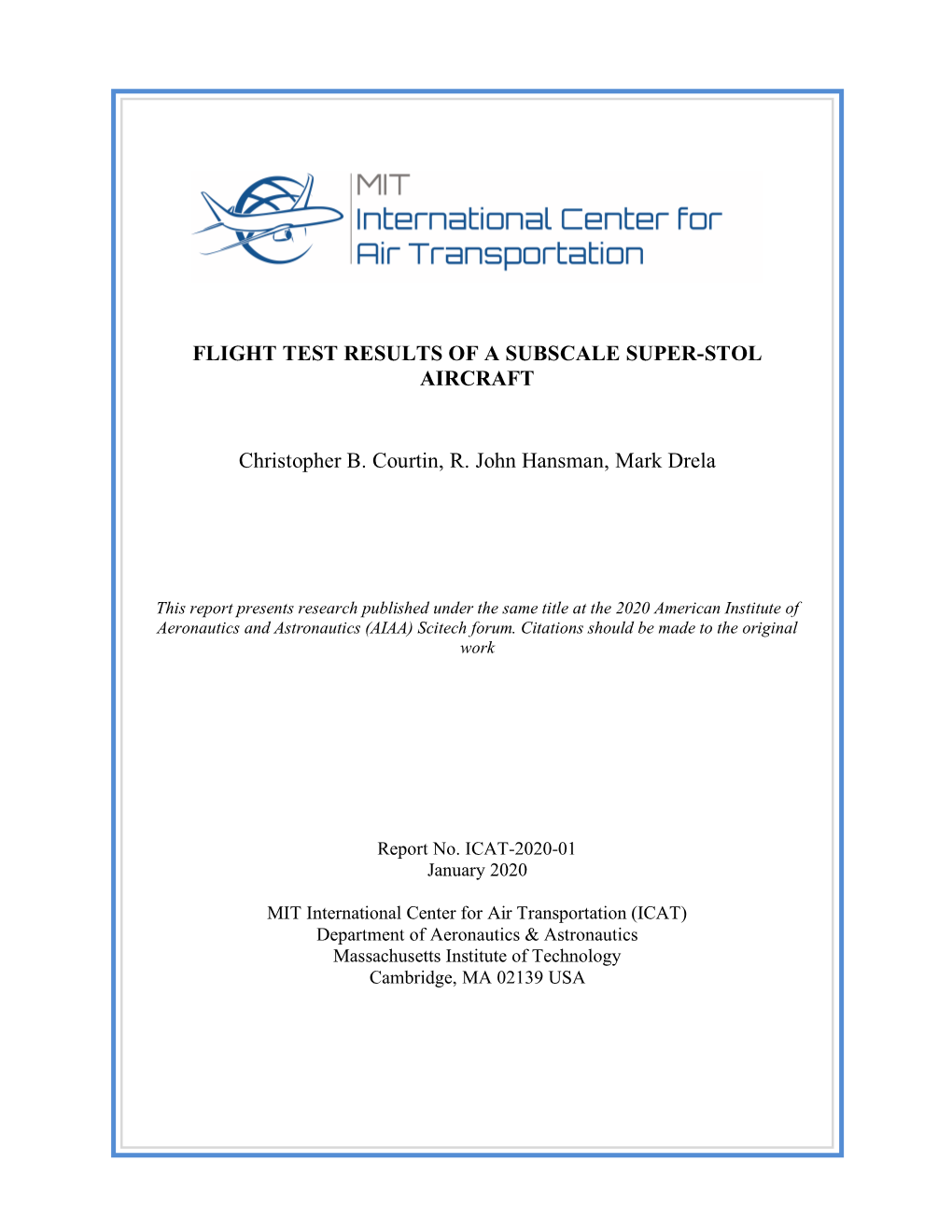
Load more
Recommended publications
-
A Flight Simulation Study of the Simultaneous Non-Interfering
A FLIGHT SIMULATION STUDY OF THE SIMULTANEOUS NON-INTERFERING AIRCRAFT APPROACH A Thesis presented to the Faculty of California Polytechnic State University, San Luis Obispo In Partial Fulfillment of the Requirements for the Degree Master of Science in Aerospace Engineering by Brian Reel May 2009 © 2009 Brian Hogan Reel ALL RIGHTS RESERVED ii COMMITTEE MEMBERSHIP TITLE: A Flight Simulation Study of the Simultaneous Non-Interfering Aircraft Approach AUTHOR: Brian Hogan Reel DATE SUBMITTED: May 2009 COMMITTEE CHAIR: Dr. Daniel Biezad, Cal Poly Aerospace Engineering COMMITTEE MEMBER: Craig Hange, NASA AMES COMMITTEE MEMBER: Dr. Eric Mehiel, Cal Poly Aerospace Engineering COMMITTEE MEMBER: Dr. Frank Owen, Cal Poly Mechanical Engineering COMMITTEE MEMBER: Dr. Kurt Colvin, Cal Poly Industrial/Manufacturing Engineering iii ABSTRACT A Flight Simulation Study of the Simultaneous Non-Interfering Aircraft Approach Brian Hogan Reel Using a new implementation of a NASA flight simulation of the Quiet Short-Haul Research Aircraft, autopilots were designed to be capable of flying both straight in (ILS) approaches, and circling (SNI) approaches. A standard glideslope coupler was sufficient for most conditions, but a standard Proportional-Integral-Derivative (PID) based localizer tracker was not sufficient for maintaining a lateral track on the SNI course. To track the SNI course, a feed-forward system, using GPS steering provided much better results. NASA and the FAA embrace the concept of a Simultaneous, Non-Interfering (SNI) approach as a way to increase airport throughput while reducing the noise footprints of aircraft on approach. The NASA concept for the SNI approach for Short Takeoff and Landing (STOL) aircraft involves a straight in segment flown above the flight path of a normal approach, followed by a spiraling descent to the runway. -
Propulsion and Flight Controls Integration for the Blended Wing Body Aircraft
Cranfield University Naveed ur Rahman Propulsion and Flight Controls Integration for the Blended Wing Body Aircraft School of Engineering PhD Thesis Cranfield University Department of Aerospace Sciences School of Engineering PhD Thesis Academic Year 2008-09 Naveed ur Rahman Propulsion and Flight Controls Integration for the Blended Wing Body Aircraft Supervisor: Dr James F. Whidborne May 2009 c Cranfield University 2009. All rights reserved. No part of this publication may be reproduced without the written permission of the copyright owner. Abstract The Blended Wing Body (BWB) aircraft offers a number of aerodynamic perfor- mance advantages when compared with conventional configurations. However, while operating at low airspeeds with nominal static margins, the controls on the BWB aircraft begin to saturate and the dynamic performance gets sluggish. Augmenta- tion of aerodynamic controls with the propulsion system is therefore considered in this research. Two aspects were of interest, namely thrust vectoring (TVC) and flap blowing. An aerodynamic model for the BWB aircraft with blown flap effects was formulated using empirical and vortex lattice methods and then integrated with a three spool Trent 500 turbofan engine model. The objectives were to estimate the effect of vectored thrust and engine bleed on its performance and to ascertain the corresponding gains in aerodynamic control effectiveness. To enhance control effectiveness, both internally and external blown flaps were sim- ulated. For a full span internally blown flap (IBF) arrangement using IPC flow, the amount of bleed mass flow and consequently the achievable blowing coefficients are limited. For IBF, the pitch control effectiveness was shown to increase by 18% at low airspeeds. -
Aircraft Requirements for Sustainable Regional Aviation
aerospace Article Aircraft Requirements for Sustainable Regional Aviation Dominik Eisenhut 1,*,† , Nicolas Moebs 1,† , Evert Windels 2, Dominique Bergmann 1, Ingmar Geiß 1, Ricardo Reis 3 and Andreas Strohmayer 1 1 Institute of Aircraft Design, University of Stuttgart, 70569 Stuttgart, Germany; [email protected] (N.M.); [email protected] (D.B.); [email protected] (I.G.); [email protected] (A.S.) 2 Aircraft Development and Systems Engineering (ADSE) BV, 2132 LR Hoofddorp, The Netherlands; [email protected] 3 Embraer Research and Technology Europe—Airholding S.A., 2615–315 Alverca do Ribatejo, Portugal; [email protected] * Correspondence: [email protected] † These authors contributed equally to this work. Abstract: Recently, the new Green Deal policy initiative was presented by the European Union. The EU aims to achieve a sustainable future and be the first climate-neutral continent by 2050. It targets all of the continent’s industries, meaning aviation must contribute to these changes as well. By employing a systems engineering approach, this high-level task can be split into different levels to get from the vision to the relevant system or product itself. Part of this iterative process involves the aircraft requirements, which make the goals more achievable on the system level and allow validation of whether the designed systems fulfill these requirements. Within this work, the top-level aircraft requirements (TLARs) for a hybrid-electric regional aircraft for up to 50 passengers are presented. Apart from performance requirements, other requirements, like environmental ones, Citation: Eisenhut, D.; Moebs, N.; are also included. -
Aviation Investigation Report A04w0114 Upset on Water
Transportation Safety Board Bureau de la sécurité des transports of Canada du Canada AVIATION INVESTIGATION REPORT A04W0114 UPSET ON WATER LANDING BIG RIVER AIR LTD. CESSNA A185F SEAPLANE C-GVYE TALTSON RIVER (FERGUSON’S CABIN) NORTHWEST TERRITORIES 07 JUNE 2004 The Transportation Safety Board of Canada (TSB) investigated this occurrence for the purpose of advancing transportation safety. It is not the function of the Board to assign fault or determine civil or criminal liability. Aviation Investigation Report Upset on Water Landing Big River Air Ltd. Cessna A185F Seaplane C-GVYE Taltson River (Ferguson’s Cabin) Northwest Territories 07 June 2004 Report Number A04W0114 Summary The Cessna A185F seaplane (registration C-GVYE, serial number 18503778) operated by Big River Air Ltd., departed Four Mile Lake, Alberta, on a visual flight rules flight to the Taltson River, Northwest Territories. The purpose of the flight was to transport three passengers to a site on the river known as Ferguson’s Cabin. At approximately 1700 mountain daylight time, as the aircraft was landing on the water near Ferguson’s Cabin, the left float dug in and the left wing struck the water. The aircraft immediately cartwheeled and came to rest floating inverted in the river, with only the bottoms of the floats visible at the surface. The pilot and the front seat passenger sustained serious injuries; however, they managed to exit the submerged and damaged aircraft through a broken window in the left cabin door. Four fishermen in boats responded to the accident, removed the survivors from the cold water, and transported them to a warm shelter. -
A Conceptual Design of a Short Takeoff and Landing Regional Jet Airliner
A Conceptual Design of a Short Takeoff and Landing Regional Jet Airliner Andrew S. Hahn 1 NASA Langley Research Center, Hampton, VA, 23681 Most jet airliner conceptual designs adhere to conventional takeoff and landing performance. Given this predominance, takeoff and landing performance has not been critical, since it has not been an active constraint in the design. Given that the demand for air travel is projected to increase dramatically, there is interest in operational concepts, such as Metroplex operations that seek to unload the major hub airports by using underutilized surrounding regional airports, as well as using underutilized runways at the major hub airports. Both of these operations require shorter takeoff and landing performance than is currently available for airliners of approximately 100-passenger capacity. This study examines the issues of modeling performance in this now critical flight regime as well as the impact of progressively reducing takeoff and landing field length requirements on the aircraft’s characteristics. Nomenclature CTOL = conventional takeoff and landing FAA = Federal Aviation Administration FAR = Federal Aviation Regulation RJ = regional jet STOL = short takeoff and landing UCD = three-dimensional Weissinger lifting line aerodynamics program I. Introduction EMAND for air travel over the next fifty to D seventy-five years has been projected to be as high as three times that of today. Given that the major airport hubs are already congested, and that the ability to increase capacity at these airports by building more full- size runways is limited, unconventional solutions are being considered to accommodate the projected increased demand. Two possible solutions being considered are: Metroplex operations, and using existing underutilized runways at the major hub airports. -
The Influence of Wing Loading on Turbofan Powered Stol Transports with and Without Externally Blown Flaps
https://ntrs.nasa.gov/search.jsp?R=19740005605 2020-03-23T12:06:52+00:00Z NASA CONTRACTOR NASA CR-2320 REPORT CXI CO CNI THE INFLUENCE OF WING LOADING ON TURBOFAN POWERED STOL TRANSPORTS WITH AND WITHOUT EXTERNALLY BLOWN FLAPS by R. L. Morris, C. JR. Hanke, L. H. Pasley, and W. J. Rohling Prepared by THE BOEING COMPANY WICHITA DIVISION Wichita, Kans. 67210 for Langley Research Center NATIONAL AERONAUTICS AND SPACE ADMINISTRATION • WASHINGTON, D. C. • NOVEMBER 1973 1. Report No. 2. Government Accession No. 3. Recipient's Catalog No. NASA CR-2320 4. Title and Subtitle 5. Reoort Date November. 1973 The Influence of Wing Loading on Turbofan Powered STOL Transports 6. Performing Organization Code With and Without Externally Blown Flaps 7. Author(s) 8. Performing Organization Report No. R. L. Morris, C. R. Hanke, L. H. Pasley, and W. J. Rohling D3-8514-7 10. Work Unit No. 9. Performing Organization Name and Address The Boeing Company 741-86-03-03 Wichita Division 11. Contract or Grant No. Wichita, KS NAS1-11370 13. Type of Report and Period Covered 12. Sponsoring Agency Name and Address Contractor Report National Aeronautics and Space Administration Washington, D.C. 20546 14. Sponsoring Agency Code 15. Supplementary Notes This is a final report. 16. Abstract The effects of wing loading on the design of short takeoff and landing (STOL) transports using (1) mechanical flap systems, and (2) externally blown flap systems are determined. Aircraft incorporating each high-lift method are sized for Federal Aviation Regulation (F.A.R.) field lengths of 2,000 feet, 2,500 feet, and 3,500 feet, and for payloads of 40, 150, and 300 passengers, for a total of 18 point-design aircraft. -
Aircraft of Today. Aerospace Education I
DOCUMENT RESUME ED 068 287 SE 014 551 AUTHOR Sayler, D. S. TITLE Aircraft of Today. Aerospace EducationI. INSTITUTION Air Univ.,, Maxwell AFB, Ala. JuniorReserve Office Training Corps. SPONS AGENCY Department of Defense, Washington, D.C. PUB DATE 71 NOTE 179p. EDRS PRICE MF-$0.65 HC-$6.58 DESCRIPTORS *Aerospace Education; *Aerospace Technology; Instruction; National Defense; *PhysicalSciences; *Resource Materials; Supplementary Textbooks; *Textbooks ABSTRACT This textbook gives a brief idea aboutthe modern aircraft used in defense and forcommercial purposes. Aerospace technology in its present form has developedalong certain basic principles of aerodynamic forces. Differentparts in an airplane have different functions to balance theaircraft in air, provide a thrust, and control the general mechanisms.Profusely illustrated descriptions provide a picture of whatkinds of aircraft are used for cargo, passenger travel, bombing, and supersonicflights. Propulsion principles and descriptions of differentkinds of engines are quite helpful. At the end of each chapter,new terminology is listed. The book is not available on the market andis to be used only in the Air Force ROTC program. (PS) SC AEROSPACE EDUCATION I U S DEPARTMENT OF HEALTH. EDUCATION & WELFARE OFFICE OF EDUCATION THIS DOCUMENT HAS BEEN REPRO OUCH) EXACTLY AS RECEIVED FROM THE PERSON OR ORGANIZATION ORIG INATING IT POINTS OF VIEW OR OPIN 'IONS STATED 00 NOT NECESSARILY REPRESENT OFFICIAL OFFICE OF EOU CATION POSITION OR POLICY AIR FORCE JUNIOR ROTC MR,UNIVERS17/14AXWELL MR FORCEBASE, ALABAMA Aerospace Education I Aircraft of Today D. S. Sayler Academic Publications Division 3825th Support Group (Academic) AIR FORCE JUNIOR ROTC AIR UNIVERSITY MAXWELL AIR FORCE BASE, ALABAMA 2 1971 Thispublication has been reviewed and approvedby competent personnel of the preparing command in accordance with current directiveson doctrine, policy, essentiality, propriety, and quality. -
QUIET CLEAN SHORT-HAUL EXPERIMENTAL ENGINE (QCSEE) Preliminary Under the Wing Flight Propulsion System Analysis Report
NASA CR-134868 QUIET CLEAN SHORT-HAUL EXPERIMENTAL ENGINE (QCSEE) Preliminary Under the Wing Flight Propulsion System Analysis Report February 1976 by Advanced Engineering & Technology Programs Department General Electric Company (IASA-CR-134868) QUIET CLEAN SHORT-HAUL NS0-15088 EXPERIMENTAL ENGINE (QCSEE) PRELIMINARY 1UNDER THE WING FLIGHT PROPULSION SYSTEM lANALYSIS REPORT '(General Electric Co.) "nclas '1261 p HC A12/MF A01 CSCL 21E G3/07 33465 Prepared For National Aeronautics and Space Admiistrati Contract NAS3-18021 FOR EARLY DOMESTIC DISSEMNATION-f9, < %,tj64 Because of its significant early commercial potential, th'is information, which has been developed under a U. S. Government program, is being disseminated within the United States in advance of general publication. This information may be dupli cated and used by the recipient with the express limitation that it not be published. Release of this information to other domestic parties by the recipient shall be made subject to these limitations. Foreign release may be made only with prior NASA approval and appropriate export licenses. This legend shall be marked on any reproduction of this information in whole or in Datepart. forfa general rel ease,)- 0A16/Zyj/ 1.Rep No. 2. Government Accession No. 3. Recipient's Catalog No: NASA CR-134868 4 Titleand Subtitle 5.Report Date QUIET CLEAN SHORT-HAUL EXPERIMENTAL ENGINE PRELIMINARY February 1976 UNDER-THE-WING FLIGHT PROPULSION SYSTEM ANALYSIS REPORT 6. Performing Organization Code 7. Author(s) D. F. Howard, et al 8.Performing Organization Report No. Advanced Engineering and Technology Programs Dept R75AEG349 Group Engineering Division 10. Work Unit No 9 Performing Organization Name and Address General Electric Company 1 Jimson Road 11. -
Toronto City Centre Airport – Chronology and Planning Issues Summary
1 Toronto City Centre Airport – Chronology and Planning Issues Summary Explanatory Notes: The following is a chronology of events, decisions, issues and policies related to the history of the Toronto island airport, summarized by City Planning staff. The number in brackets following each item is a cross-reference to the Bibliography. 1928 The City Board of Control asked the Harbour Board to report "on developing the West Island Sand Bar for a seaplane, flying boat, and amphibian airplane base". (8) 1937 The Harbour Commissioner agreed that “two airports should be built: a major one on the Island site and an auxiliary one at Malton”. (8) 1939 Toronto City Centre Airport opened as the Port George VI Airport. (26) 1953 A traffic control system was installed at the airport to accommodate the increase of business training flights. This was updated in 1960 when a radio control system was installed. (8) 1957 The City transferred the ownership of Malton Airport to the Federal Government, which assumed the responsibility for it in exchange for providing improvements to the Island Airport, including a new 4,000-foot (1,220 metre) runway, the installation of navigation and landing systems, and lights to assist night flying. An airport ferry to the island was also put into service. (34) 1961 The improvements referenced above were implemented. They involved extending the site by adding landfill on the east and west extremities of the island, constructing the 4,000-foot (1,220 metre) runway, and a system of paved taxiways. A new twin-bay hangar was built at the same time, and the lighting to assist night flying was added. -
Synergistic Airframe-Propulsion Interactions and Integrations
NASA/TM-1998-207644 Synergistic Airframe-Propulsion Interactions and Integrations A White Paper Prepared by the 1996-1997 Langley Aeronautics Technical Committee Steven F. Yaros, Matthew G. Sexstone, Lawrence D. Huebner, John E. Lamar, Robert E. McKinley, Jr., Abel 0. Torres, Casey L. Burley, Robert C. Scott, and William J. Small Langley Research Center, Hampton, Virginia National Aeronautics and Space Administration Langley Research Center Hampton, Virginia 23681-2199 March 1998 Available from the following: NASA Center for AeroSpace Information (CASH National Technical Information Service (NTIS) 800 Elkridge Landing Road 5285 Port Royal Road Linthicum Heights, MD 21090-2934 Springfield, VA 22161-2171 (703) 487-4650 (301) 621-0390 Executive Summary This white paper documents the work of the NASA Langley Aeronautics Technical Committee from July 1996 through March 1998 and addresses the subject of Synergistic Airframe-Propulsion Interactions and Integrations (SnAPII). It is well known that favorable Propulsion Airframe Integration (PAD is not only possible but Mach number dependent -- with the largest (currently utilized) benefit occurring at hypersonic speeds. At the higher speeds the lower surface of the airframe actually serves as an external precompression surface for the inlet flow. At the lower supersonic Mach numbers and for the bulk of the commercial civil transport fleet, the benefits of SnAPII have not been as extensively explored. This is due primarily to the separateness of the design process for airframes and propulsion systems, with only unfavorable interactions addressed. The question 'How to design these two systems in such a way that the airframe needs the propulsion and the propulsion needs the airframe?' is the fun- damental issue addressed in this paper. -
C-130J Super Hercules Whatever the Situation, We'll Be There
C-130J Super Hercules Whatever the Situation, We’ll Be There Table of Contents Introduction INTRODUCTION 1 Note: In general this document and its contents refer RECENT CAPABILITY/PERFORMANCE UPGRADES 4 to the C-130J-30, the stretched/advanced version of the Hercules. SURVIVABILITY OPTIONS 5 GENERAL ARRANGEMENT 6 GENERAL CHARACTERISTICS 7 TECHNOLOGY IMPROVEMENTS 8 COMPETITIVE COMPARISON 9 CARGO COMPARTMENT 10 CROSS SECTIONS 11 CARGO ARRANGEMENT 12 CAPACITY AND LOADS 13 ENHANCED CARGO HANDLING SYSTEM 15 COMBAT TROOP SEATING 17 Paratroop Seating 18 Litters 19 GROUND SERVICING POINTS 20 GROUND OPERATIONS 21 The C-130 Hercules is the standard against which FLIGHT STATION LAYOUTS 22 military transport aircraft are measured. Versatility, Instrument Panel 22 reliability, and ruggedness make it the military Overhead Panel 23 transport of choice for more than 60 nations on six Center Console 24 continents. More than 2,300 of these aircraft have USAF AVIONICS CONFIGURATION 25 been delivered by Lockheed Martin Aeronautics MAJOR SYSTEMS 26 Company since it entered production in 1956. Electrical 26 During the past five decades, Lockheed Martin and its subcontractors have upgraded virtually every Environmental Control System 27 system, component, and structural part of the Fuel System 27 aircraft to make it more durable, easier to maintain, Hydraulic Systems 28 and less expensive to operate. In addition to the Enhanced Cargo Handling System 29 tactical airlift mission, versions of the C-130 serve Defensive Systems 29 as aerial tanker and ground refuelers, weather PERFORMANCE 30 reconnaissance, command and control, gunships, Maximum Effort Takeoff Roll 30 firefighters, electronic recon, search and rescue, Normal Takeoff Distance (Over 50 Feet) 30 and flying hospitals. -
Hybrid Buoyant Aircraft: Future STOL Aircraft for Interconnectivity of the Malaysian Islands
Available online at http://docs.lib.purdue.edu/jate Journal of Aviation Technology and Engineering 6:2 (2017) 80–88 Hybrid Buoyant Aircraft: Future STOL Aircraft for Interconnectivity of the Malaysian Islands Anwar ul Haque International Islamic University Malaysia (IIUM) Waqar Asrar Department of Mechanical Engineering, International Islamic University Malaysia (IIUM) Ashraf Ali Omar Department of Aeronautical Engineering, University of Tripoli Erwin Sulaeman Department of Mechanical Engineering, International Islamic University Malaysia (IIUM) Jaffar Syed Mohamed Ali Department of Mechanical Engineering, International Islamic University Malaysia (IIUM) Abstract Hybrid buoyant aircraft are new to the arena of air travel. They have the potential to boost the industry by leveraging new emerging lighter-than-air (LTA) and heavier-than-air (HTA) technologies. Hybrid buoyant aircraft are possible substitutes for jet and turbo- propeller aircraft currently utilized in aviation, and this manuscript is a country-specific (Malaysia) analysis to determine their potential market, assessing the tourism, business, agricultural, and airport transfer needs of such vehicles. A political, economic, social, and tech- nological factors (PEST) analysis was also conducted to determine the impact of PEST parameters on the development of buoyant aircraft and to assess all existing problems of short takeoff and landing (STOL) aircraft. Hybrid buoyant aircraft will not only result in reduction of transportation costs, but will also improve the economic conditions of the region. New airworthiness regulations can lead to greater levels of competition in the development of hybrid buoyant aircraft. Keywords: hybrid buoyant aircraft, green energy, PEST analysis http://dx.doi.org/10.7771/2159-6670.1138 A. ul Haque et al.