LSS Project Management 1
Total Page:16
File Type:pdf, Size:1020Kb
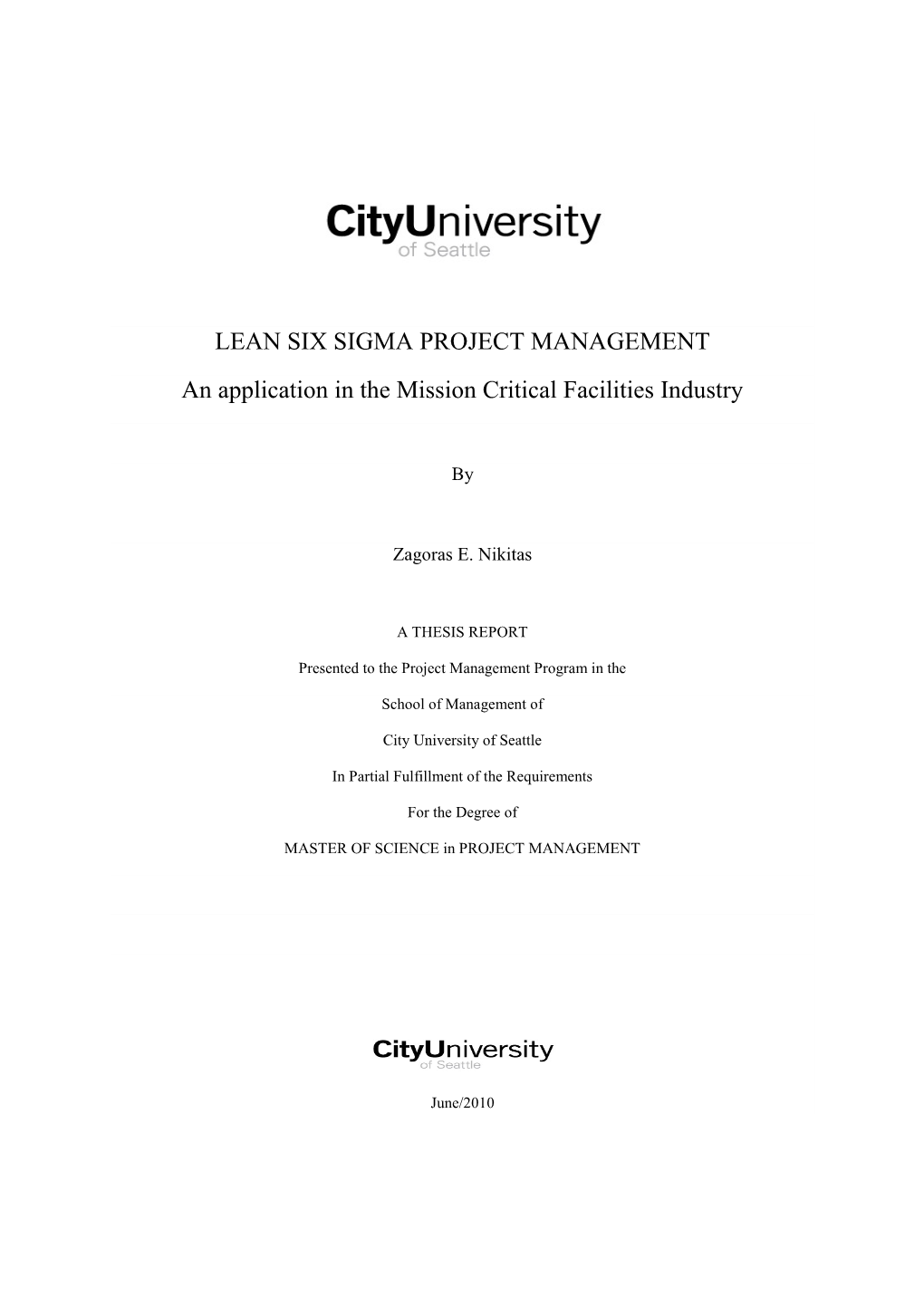
Load more
Recommended publications
-
Identifying the Effects of Lean Construction Principles on Variability of Project Duration a Thesis Submitted to the Graduate Sc
IDENTIFYING THE EFFECTS OF LEAN CONSTRUCTION PRINCIPLES ON VARIABILITY OF PROJECT DURATION A THESIS SUBMITTED TO THE GRADUATE SCHOOL OF NATURAL AND APPLIED SCIENCES OF THE MIDDLE EAST TECHNICAL UNIVERSITY BY HACI HÜSEYİN EROL IN PARTIAL FULFILLMENT OF THE REQUIREMENTS FOR THE DEGREE OF MASTER OF SCIENCE IN CIVIL ENGINEERING JUNE 2014 Approval of the thesis: IDENTIFYING THE EFFECTS OF LEAN CONSTRUCTION PRINCIPLES ON VARIABILITY OF PROJECT DURATION submitted by HACI HÜSEYİN EROL in partial fulfillment of the requirements for the degree of Master of Science in Civil Engineering Department, Middle East Technical University by, Prof. Dr. Canan Özgen Dean, Graduate School of Natural and Applied Sciences Prof. Dr. Ahmet Cevdet Yalçıner Head of Department, Civil Engineering Prof. Dr. İrem Dikmen Toker Supervisor, Civil Engineering Dept., METU Prof. Dr. M. Talat Birgönül Co-Supervisor, Civil Engineering Dept., METU Examining Committee Members: Assoc. Prof. Dr. Rıfat Sönmez Civil Engineering Dept., METU Prof. Dr. İrem Dikmen Toker Civil Engineering Dept., METU Prof. Dr. M. Talat Birgönül Civil Engineering Dept., METU Asst. Prof. Dr. Aslı Akçamete Civil Engineering Dept., METU Gülşah Dağkıran, M. Sc. GAMA Holding Date: 20.06.2014 I hereby declare that all information in this document has been obtained and presented in accordance with academic rules and ethical conduct. I also declare that, as required by these rules and conduct, I have fully cited and referenced all material and results that are not original to this work. Name, Last name : Hacı Hüseyin Erol Signature : iv ABSTRACT IDENTIFYING THE EFFECTS OF LEAN CONSTRUCTION PRINCIPLES ON VARIABILITY OF PROJECT DURATION Erol, Hacı Hüseyin M.Sc., Department of Civil Engineering Supervisor: Prof. -
CRC.Press-Lean.IT.Enabling.And
Praise for Lean IT “A great read on how to apply Lean principles to IT. These tools really work to improve IT’s perfor- mance and credibility.” — Niel Nickolaisen, CIO Headwaters, Inc.; co-author of Stand Back and Deliver: Accelerating Business Agility “A groundbreaking synthesis, examining IT operations, project management, software devel- opment, and governance through a Lean lens. Taut, subtly reasoned, and laced with the kind of brilliant insights that only come from practicing masters. Required reading for IT executives, archi- tects, and project managers.” — Charles Betz, author of Architecture and Patterns for IT Service Management, Resource Planning, and Governance, and practicing Fortune 20 enterprise architect “A superb primer for anyone interested in learning about Lean. Their work will help business lead- ers understand the arcane machinations of IT while giving IT professionals a common language to talk to the business.” David Almond, Administrator, Office of Transformation for the Department of Administrative Services; former CIO, Oregon Department of Revenue “Do most IT organizations waste effort? They do. Can this book transform your thinking and jumpstart your efforts to eliminate waste and optimize the business value of IT? You bet!” Kurt Milne, Executive Director, IT Process Institute “Finally! A practical Lean transformation blueprint that includes information systems and the IT organization, while addressing the essential element of human engagement across the enterprise. You can easily digest their lessons and learn how to adapt and apply to your specific organization. This is the key to business alignment the IT industry has been searching for.” Andrew Rome, Talent & Organizational Performance executive of an 80,000-person global IT Management firm “A deft application of Lean concepts and techniques to a central challenge we all face: how to increase effectiveness of investments in IT people and systems and the value they bring to enterprise processes. -
Apply Lean Thinking in Project Management
Chi Pham Ngoc Lan Apply Lean Thinking in Project Management Helsinki Metropolia University of Applied Sciences Bachelor of Engineering Media Engineering Thesis 21 April 2015 Abstract Author(s) Chi Pham Ngoc Lan Title Apply Lean thinking in project management Number of Pages 47 pages + 3 appendices Date 5 May 2010 Degree Bachelor of Engineering Degree Programme Media Engineering Specialisation option Audio Visual Technology, Quality Management Instructor(s) Aarne Klemetti, Senior Lecturer The purpose of this thesis was to study the effects of Lean Thinking in Project Manage- ment and how applying Lean Project Management could enhance the productivity of pro- ject work. The study was carried using theoretical research and collecting empirical data from three interviews and one case study at a local company. At the end of the study, the major project management problems at the company were identified and analyzed following Lean Principles. It was also pointed out where there is a need to adjust and modify Lean Thinking in order to efficiently apply it in project work. The case study also demonstrates the intinital effects of using Lean tools in more dynamic en- vironment as marketing projects. The results of this study show how using Lean principles can solve problems in project management activities, demonstrate the potential and suggest a suitable approach to ap- plying Lean Thinking in business. Keywords project management, Lean thinking, Lean principles, Kan- ban, waste, Mura, Muri, Muda Contents 1 Introduction 1 2 Methodology 3 2.1 -
Enabling and Sustaining Your Lean Transformation
Lean IT Enabling and Sustaining Your Lean Transformation Steven C. Bell • Michael A. Orzen Productivity Press Taylor & Francis Group 270 Madison Avenue New York, NY 10016 © 2011 by Steven C. Bell and Michael A. Orzen Productivity Press is an imprint of Taylor & Francis Group, an Informa business No claim to original U.S. Government works Printed in the United States of America on acid-free paper 10 9 8 7 6 5 4 3 2 1 International Standard Book Number: 978-1-4398-1756-8 (Hardback) This book contains information obtained from authentic and highly regarded sources. Reasonable efforts have been made to publish reliable data and information, but the author and publisher cannot assume responsibility for the validity of all materials or the consequences of their use. The authors and publishers have attempted to trace the copyright holders of all material reproduced in this publication and apologize to copyright holders if permission to publish in this form has not been obtained. If any copyright material has not been acknowledged please write and let us know so we may rectify in any future reprint. Except as permitted under U.S. Copyright Law, no part of this book may be reprinted, reproduced, trans- mitted, or utilized in any form by any electronic, mechanical, or other means, now known or hereafter invented, including photocopying, microfilming, and recording, or in any information storage or retrieval system, without written permission from the publishers. For permission to photocopy or use material electronically from this work, please access www.copyright. com (http://www.copyright.com/) or contact the Copyright Clearance Center, Inc. -
A Comparison of Lean Construction with Project Production Management
PPI POSITION PAPER A Comparison of Lean Construction with Project Production Management Edited by Ram G. Shenoy, PhD Technical Director, Project Production Institute, [email protected] ABSTRACT Project Management aims to address the myriad technical, human, organizational and managerial issues encountered during project execution [1]. Over the past two decades, different variants have emerged, including Lean Project Management, Agile Project Management, Scrum, Theory of Constraints and Extreme Project Management, to name a few. Lean Construction [2,36,54] utilizes concepts originally from Lean manufacturing and applies them specifically to the delivery of projects in the construction sector. Despite the proliferation of different “flavors” of project management, major capital project outcomes in construction and in other industries remain poor [3 – 5]. Industry practitioners face a confusing array of differing methodologies, each claiming to address poor project performance. The Institute’s mission is to explain how Project Production Management (PPM) addresses the gap between today’s poor project performance and what is possible, thereby differentiating PPM from other methodologies. Here, we focus on a comparison between PPM and Lean Construction. We trace the historical evolution of Lean Construction from its roots in Lean manufacturing, highlighting the operations science foundation underlying Lean and PPM. Lean Construction covers aspects of project governance, organization of project stakeholders and the work activities -
Lean Introduction Via Pilot and Toolbox to Global Factory Network
LAURA NIKKOLA-KUUSISTO LEAN INTRODUCTION VIA PILOT AND TOOLBOX TO GLOBAL FACTORY NETWORK Master’s thesis Examiners: Professor Kari T. Koskinen, Dr. Eeva Järvenpää Examiner and topic approved by the council meeting of Department of Me- chanical Engineering and Industrial Sys- tems 13.8.2014 i ABSTRACT TAMPERE UNIVERSITY OF TECHNOLOGY Master’s Degree Program in Department of Mechanical Engineering and Industrial Sys- tems NIKKOLA-KUUSISTO, LAURA: Lean introduction via pilot and Toolbox to global factory network Master of Science Thesis, 96 pages, 20 Appendix pages April 2016 Major: Production Engineering Examiners: Professor Kari T. Koskinen, Dr. Eeva Järvenpää Keywords: Lean, kaizen, visual management, value stream Metso One Factory Initiative management made a decision to implement lean into its processes in order to eliminate waste, reduce lead times and manage all value streams in a more efficient way. In this thesis the initial stages of a lean transformation including pilot projects and lean tools research in Metso One Factory were studied and documented. Lean tools were researched using many literary sources and their suitability for Metso’s purposes was evaluated. Suitable tools were collected into One Factory Lean Toolbox including a summary of the tool’s theory and for some tools a template ready to use in practice. Two product groups in need of improvement were selected as pilot projects by upper management and their purpose was to become proof of concept in the lean trans- formation. It was found that not all lean tools are suitable for a global One Factory Lean Toolbox because some may be too specific for One Factory’s purposes. -
Lean and Agile Project Management How to Make Any Project Better, Faster, and More Cost Effective
Lean and Agile Project Management How to Make Any Project Better, Faster, and More Cost Effective Lean and Agile Project Management How to Make Any Project Better, Faster, and More Cost Effective Terra Vanzant Stern, PhD Boca Raton London New York CRC Press is an imprint of the Taylor & Francis Group, an informa business A P R O D UCTIV I T Y PRE SS BOOK CRC Press Taylor & Francis Group 6000 Broken Sound Parkway NW, Suite 300 Boca Raton, FL 33487-2742 © 2017 by Terra Vanzant Stern CRC Press is an imprint of Taylor & Francis Group, an Informa business No claim to original U.S. Government works Printed on acid-free paper Version Date: 20161121 International Standard Book Number-13: 978-1-4987-3916-0 (Hardback) This book contains information obtained from authentic and highly regarded sources. Reasonable efforts have been made to publish reliable data and information, but the author and publisher cannot assume responsibility for the valid- ity of all materials or the consequences of their use. The authors and publishers have attempted to trace the copyright holders of all material reproduced in this publication and apologize to copyright holders if permission to publish in this form has not been obtained. If any copyright material has not been acknowledged please write and let us know so we may rectify in any future reprint. Except as permitted under U.S. Copyright Law, no part of this book may be reprinted, reproduced, transmitted, or uti- lized in any form by any electronic, mechanical, or other means, now known or hereafter invented, including photocopy- ing, microfilming, and recording, or in any information storage or retrieval system, without written permission from the publishers. -
Improving Lean Project Management with Customer Value Centered Practices
Improving Lean Project Management with Customer Value Centered Practices Leena Saari Master’s Thesis Degree Programme in Information Systems Management 2016 Abstract Päiväys 17.5.2016 Author Leena Saari Degree programme Masters’ Degree Programme in Information System Management, Haaga-Helia University of Applied Sciences. Thesis title Number of pages Improving Lean Project Management and appendix pages with Customer Value Centered Practices 60 + 14 The aim of this Masters’ Thesis is to investigate how software development project managers gain understanding on customer value and ensure customer value goal align- ment in their present software development projects and to provide customer value goal utilizing best practices for Fujitsu Finland software development project management. The thesis theory basis handle customer value and lean project management as a con- cept, customer value goal setting and monitoring in continuous improvement context and in guiding high-performing project teams. The empirical part of this action study was conducted at Fujitsu Finland Helsinki Office from September 2015 to March 2016. It started by constructing the present situation of customer value utilization using interviews, queries and workshops with a focus on follow- ing three improvement areas; customer value goals, shared understanding of customer value among the project team and customer value driven continuous improvement. After analyzing the areas, a suitable Best Practices Documentation for Understanding and En- suring Customer Value Alignment in Projects is developed together with a workshop team consisting mainly of software development project managers. As a result the project managers’ level of customer value understanding was improved and the feedback on the best practices was positive, so the instructions could be accepted for a pilot project to be started after this research.