LICK OBSERVATORY LASER OPERATIONS 1.0 Reason for Issue
Total Page:16
File Type:pdf, Size:1020Kb
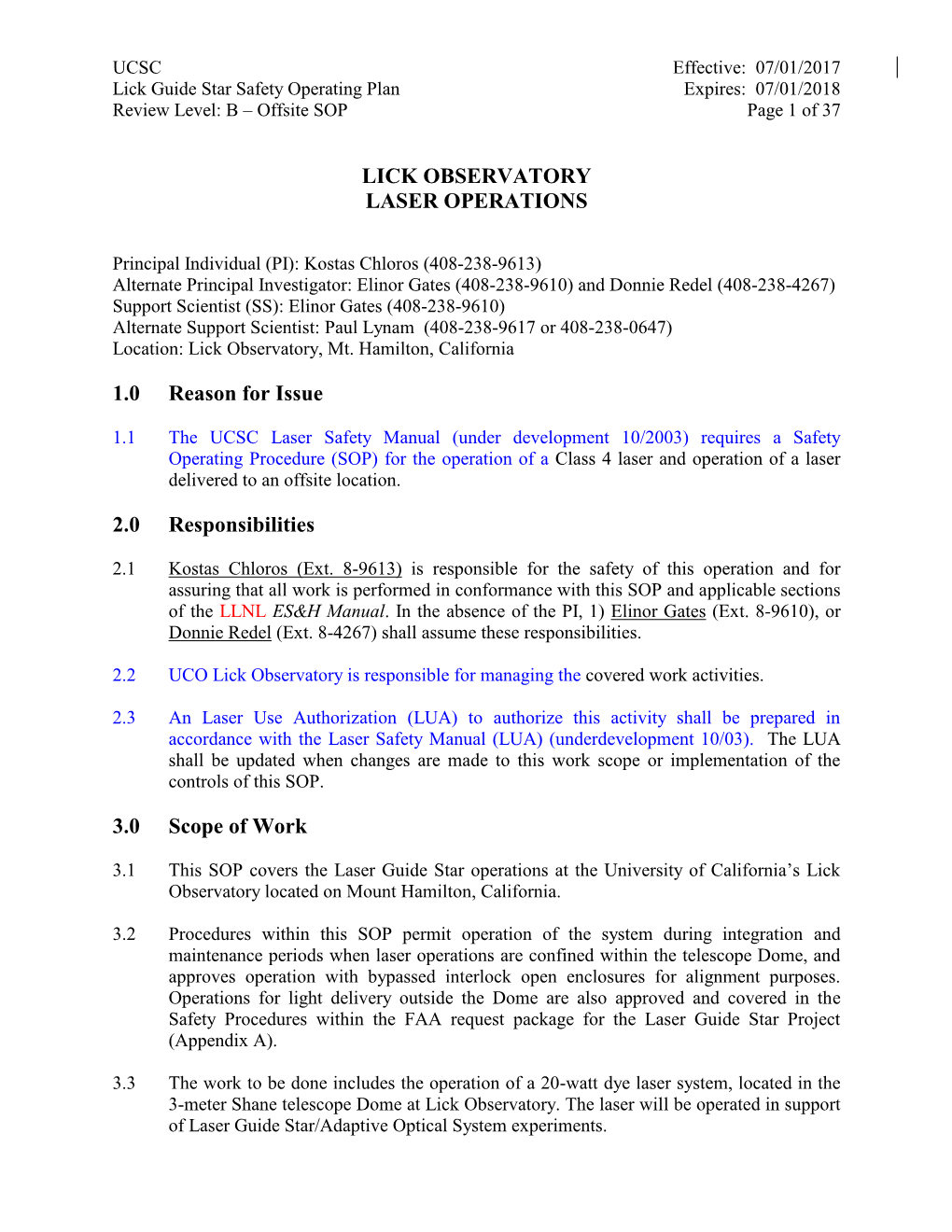
Load more
Recommended publications
-
Evergreen • East Hills Vision Strategy Project San José, California
DRAFT EIR for the EVERGREEN • EAST HILLS VISION STRATEGY PROJECT SAN JOSÉ, CALIFORNIA State Clearinghouse Number: 2005102007 City of San José File Numbers: GP05-08-01A and PDC05-050 GP05-08-01B and PDC05-051 GP05-08-01C and PDC05-048 GP05-08-01D and PDC05-049 GP05-08-01E and PDC05-052 GP05-08-01F and PDC05-053 CITY OF SAN JOSÉ FEBRUARY 2006 TABLE OF CONTENTS SECTION 1. INTRODUCTION, BACKGROUND, & PROJECT OBJECTIVES .........1 1.1 Introduction .........................................................1 1.2 Project Location .....................................................1 1.3 Background .........................................................1 1.4 Project Objectives ...................................................10 1.5 Uses of the EIR .....................................................12 1.5.1 Lead and Responsible CEQA Agencies ............................12 1.5.2 Level of Environmental Review Provided by this EIR ................12 SECTION 2. DESCRIPTION OF THE PROPOSED PROJECT ......................28 2.1 Land Use Development Scenarios ......................................28 2.1.1 Introduction and Overview ......................................28 2.1.2 Development Scenarios for the Arcadia Property ....................33 2.1.3 Development Scenarios for the Pleasant Hills Golf Course Property .....38 2.1.4 Development Scenarios for the Berg/IDS Property ...................42 2.1.5 Development Scenarios for the Legacy Partners Property ..............48 2.1.6 Development Scenarios for the Evergreen Valley College Property ......51 2.1.7 Other General Plan Amendments .................................55 2.2 Transportation and Community Amenity Projects ..........................56 2.2.1 Operational Improvements on U.S. 101 ............................61 2.2.2 Reconfigure White Road between Ocala Avenue and Aborn Road ......63 2.2.3 Reconfigure Ocala Avenue between Capitol Expwy and White Road ....63 2.2.4 Improvements along Capitol Expwy between Quimby Rd. -
Five-Year Review of the UC Observatories (UCO)
UNIVERSITY OF CALIFORNIA, ACADEMIC SENATE BERKELEY • DAVIS • IRVINE • LOS ANGELES • MERCED • RIVERSIDE • SAN DIEGO • SAN FRANCISCO SANTA BARBARA • SANTA CRUZ Kum-Kum Bhavnani Chair of the Assembly of the Academic Senate Telephone: (510) 987-9303 Faculty Representative to the Regents Email:[email protected] University of California 1111 Franklin Street, 12th Floor Oakland, California 94607-5200 July 1, 2020 THERESA MALDONADO, VICE PRESIDENT RESEARCH AND INNOVATION Re: Five-Year Review of the UC Observatories (UCO) Dear Theresa, At its June 24, 2020 meeting, the Academic Council approved the attached Five-Year Review of the UC Observatories (UCO) Multicampus Research Unit (MRU). Following procedures outlined in the Compendium, the review was performed by a Joint Senate Review Committee, led by the University Committee on Research Policy (UCORP) with input from the University Committee on Planning and Budget (UCPB) and the Coordinating Committee on Graduate Affairs (CCGA). The Review Committee recommends renewing the UCO as an MRU unit for five years, and also makes recommendations for strengthening the UCO in the areas of budget and administrative transparency, governance, student participation in research, and education and outreach. We request that that you forward the report to the UCO director. The Academic Council appreciates the significant time and effort the Review Committee spent in preparing and writing this report. In particular, I want to recognize the substantial contributions and outstanding leadership of UCORP Chair Andrew Baird. Please do not hesitate to contact me if you have additional questions. Sincerely, Kum-Kum Bhavnani, Chair Academic Council cc: Academic Council UCORP Senate Directors Review of University of California Observatories (UCO) ________________________________________________________________ University Committee on Research Policy (UCORP) (Lead Committee) University Committee on Planning and Budget (UCPB) Coordinating Committee on Graduate Affairs (CCGA) May 19, 2020 l. -
City Manager's Update July 11, 2019
July 11, 2019 Department of Public Safety Hosts Third Youth Leadership Academy The Department of Public Safety (DPS) hosted its third annual Youth Leadership Academy from June 17 to 27. Twenty-seven students entering grades 7 through 9 participated in the two-week program. Participants learned valuable skills in communication, conflict resolution, character building, decision making, and goal setting. They also received information about cyber-safety, bullying, and lifetime fitness. This program was funded by a grant from the Bureau of State and Community Corrections. For information about the Youth Leadership Academy, contact Elaine Ketell at 408-730-7234 or [email protected]. Water Quality Information Available Online The City of Sunnyvale’s Water Quality Report (Consumer Confidence Report), is now available. Our goal is to provide residents with high- quality, safe, reliable drinking water that meets every federal and state water requirement. Sunnyvale analyzes more than 20,000 water samples annually. The report lets customers know where the drinking water comes from, how it is treated to make it safe, the results of water quality monitoring and other important information about water quality. This information is provided in compliance with requirements established by the U.S. Environmental Protection Agency and the California Department of Health Services. If you have any questions or need further information, please contact Kevin Woodworth, Water Distribution Supervisor at 408-730-7900 or [email protected]. Update Sunnyvale 7/11/19 Sunnyvale DPS Deploys UAV in Search for a Missing Person On Monday, June 24, Sunnyvale DPS utilized its newly formed Unmanned Aerial Vehicle (UAV) unit on its maiden deployment. -
Lick Observatory Records: Photographs UA.036.Ser.07
http://oac.cdlib.org/findaid/ark:/13030/c81z4932 Online items available Lick Observatory Records: Photographs UA.036.Ser.07 Kate Dundon, Alix Norton, Maureen Carey, Christine Turk, Alex Moore University of California, Santa Cruz 2016 1156 High Street Santa Cruz 95064 [email protected] URL: http://guides.library.ucsc.edu/speccoll Lick Observatory Records: UA.036.Ser.07 1 Photographs UA.036.Ser.07 Contributing Institution: University of California, Santa Cruz Title: Lick Observatory Records: Photographs Creator: Lick Observatory Identifier/Call Number: UA.036.Ser.07 Physical Description: 101.62 Linear Feet127 boxes Date (inclusive): circa 1870-2002 Language of Material: English . https://n2t.net/ark:/38305/f19c6wg4 Conditions Governing Access Collection is open for research. Conditions Governing Use Property rights for this collection reside with the University of California. Literary rights, including copyright, are retained by the creators and their heirs. The publication or use of any work protected by copyright beyond that allowed by fair use for research or educational purposes requires written permission from the copyright owner. Responsibility for obtaining permissions, and for any use rests exclusively with the user. Preferred Citation Lick Observatory Records: Photographs. UA36 Ser.7. Special Collections and Archives, University Library, University of California, Santa Cruz. Alternative Format Available Images from this collection are available through UCSC Library Digital Collections. Historical note These photographs were produced or collected by Lick observatory staff and faculty, as well as UCSC Library personnel. Many of the early photographs of the major instruments and Observatory buildings were taken by Henry E. Matthews, who served as secretary to the Lick Trust during the planning and construction of the Observatory. -
BULLETIN Into
DEPABTMENT OF THE INTEEIOE BULLETIN OF THK UNITED STATES INTo. 147 WASHINGTON GOVERNMENT PRINTING OFFICE 189C UNITED STATES GEOLOGICAL SUEVEY CHARLES B. AVALCOTT, DIRECTOR EARTHQUAKES IN CALIFORNIA IN 1895 BY CHARLES D. PERRINE ASSISTANT ASTRONOMER IN CHARGE OF EARTHQUAKE OBSERVATIONS AT THE LICK OBSERVATORY WASHINGTON GOVEENMENT PRINTING OFFICE 1896 CONTENTS. Pago. Letter of transmittal.......................................................... 7 Introduction.................................................................. 9 Instruments.............................................................. 9 Scale of measurements ............................................ ........ 10 Differences 'of intensity................................................... 10 Stations.................................................................. 12 Chronologic record, 1895 ...................................................... 13 Index ........................................................................ 23 5 LETTER OF TRANSMITTAL. UNIVERSITY OF CALIFORNIA, LICK OBSERVATORY, Mount Hamilton, August 2d, 1896. SIR: I beg to transmit herewith the report of earthquakes observed at Mount Hamilton and throughout California in the year 1895, com piled by Mr. Perrine, and trust that it may be printed as a bulletin, as in previous years. Yours, very truly, EDWARD S. HOLDEN, Director Licit Observatory. Hon. 0. D. WALCOTT, Director United States Geological Survey. 7 EARTHQUAKES IN CALIFORNIA IN 1895. By CHARLES D. PERRINE. INTRODUCTION. The following paper is -
Settler Colonialism and the Making of the Lick Observatory, 1846-1919
Excerpts from Noble Hills: Settler Colonialism and the Making of the Lick Observatory, 1846-1919 One Sunday afternoon in late August 1861, a reverend, a topographer, and a botanist, set out to summit the mountain. They had met nearly a decade earlier in upstate New York, where the botanist, William Brewer, was teaching in the town where the Reverend Laurentine Hamilton was a minister.1 When Brewer was recruited by the California Geological Survey at the turn of the 1860s, Hamilton had also moved to California to work as a preacher for a small mining town. The two men rekindled their friendship, and along with the topographer Charles and Hoffman, they set out to survey the mountain.2 As they made their way towards the summit, navigating through fields of brush, the Reverend Hamilton rushed ahead of the others and declared himself first to the top.3 As they returned to their office, Brewer and Hoffman debated what to name the mountain. Brewer made “diligent inquiries” into whether it had a previous name, but found none, and so they decided to name it Mount Hamilton in honor of their friend the minister who had beat them to the summit.4 It is Mount Hamilton on which the Lick Observatory was established in 1888, and still operates today. Of course, the mountain did have a name – possibly many—before Brewer, Hoffman, and Hamilton’s excursion. Spanish colonists had named it La Sierra de Santa Isabel decades before.5 But Brewer and Hoffman had treated the mountain as terra nullius – empty land – and assumed upon themselves the power to name it. -
Cumulative Bio-Bibliography University of California, Santa Cruz June 2020
Cumulative Bio-Bibliography University of California, Santa Cruz June 2020 Puragra Guhathakurta Astronomer/Professor University of California Observatories/University of California, Santa Cruz ACADEMIC HISTORY 1980–1983 B.Sc. in Physics (Honours), Chemistry, and Mathematics, St. Xavier’s College, University of Calcutta 1984–1985 M.Sc. in Physics, University of Calcutta Science College; transferred to Princeton University after first year of two-year program 1985–1987 M.A. in Astrophysical Sciences, Princeton University 1987–1989 Ph.D. in Astrophysical Sciences, Princeton University POSITIONS HELD 1989–1992 Member, Institute for Advanced Study, School of Natural Sciences 1992–1994 Hubble Fellow, Astrophysical Sciences, Princeton University 1994 Assistant Astronomer, Space Telescope Science Institute (UPD) 1994–1998 Assistant Astronomer/Assistant Professor, UCO/Lick Observatory, University of California, Santa Cruz 1998–2002 Associate Astronomer/Associate Professor, UCO/Lick Observatory, University of California, Santa Cruz 2002–2003 Herzberg Fellow, Herzberg Institute of Astrophysics, National Research Council of Canada, Victoria, BC, Canada 2002– Astronomer/Professor, UCO/Lick Observatory, University of California, Santa Cruz 2009– Faculty Director, Science Internship Program, University of California, Santa Cruz 2012–2018 Adjunct Faculty, Science Department, Castilleja School, Palo Alto, CA 2015 Visiting Faculty, Google Headquarters, Mountain View, CA 2015– Co-founder, Global SPHERE (STEM Programs for High-schoolers Engaging in Research -
The LICK OBSERVER
Volume 2 Winter 2014 Number 1 University of California Observatories Lick Observatory Est. 1888 The LICK OBSERVER UC OBSERVATORIES DIRECTOR’S REMARKS by Sandra Faber • Interim Director The stars still shine careful tuning, APF’s precision b r i g h t l y o v e r L i c k Doppler spectrograph works exactly Observatory! Despite as planned and can measure planetary Planets near Earth-size come with various amounts of gas (white), on top of a rocky core and thin layer of UC’s announced cutoff of tugs slower than the speed of a human water (blue). Te APF can distinguish the purely rocky planets from those with large amounts of gas. operating funds for Lick walk. We foresee that APF will be the APF AND KEPLER: IN TANDEM TOWARD EARTH- by 2018, observers still premier telescope for exoplanet use the telescopes nightly from all discovery in the next decade. LIKE PLANETS By Geoffrey Marcy • UCB Astronomer corners of the UC system and While dedicated Lick mountain staff inspiring new technology is, as usual, are tending to these dazzling new Among the 100 billion layer of hydrogen and helium gas, like being developed. The second- machines, other staff and friends are stars in our Milky Way, Jupiter and Neptune, suffocating any generation Shane adaptive optics (AO) seeing to the future of Lick. This how many contain chances for life? system began commissioning on the issue of the Newsletter announces the habitable planets, and The APF telescope and its Levy Shane 3-meter reflector in November. formation of the Lick Observatory how many contain Spectrometer are perfectly suited to By next summer, this advanced AO Council. -
Annex 13 Chapter 1 Unincorpoarted Areas Without Local Fire Protection
Santa Clara County Community Wildfire Protection Plan Annex 13 – Unincorporated Areas without Local Fire Protection ANNEX 13 CHAPTER 1 UNINCORPOARTED AREAS WITHOUT LOCAL FIRE PROTECTION There are areas in Santa Clara County that are not within any local government fire protection organization’s jurisdiction. Specifically the Mt. Hamilton area, San Antonio Valley, Pacheco Pass, and the portion of the Stanford University campus outside the City of Palo Alto. Fire protection in these unincorporated areas is the responsibility of the County of Santa Clara, but there is no state statute or local ordinance that requires providing any services. Most of the these unincorporated areas are designated State Responsibility Areas (SRAs) by state law, and therefore the California Department of Forestry and Fire Protection (CAL FIRE) has jurisdiction for wildland fire protection in SRAs. CAL FIRE does not have jurisdictional responsibility for non-wildland fire emergencies, but will respond as a good Samaritan or through mutual aid during the fire season when they staff their fire stations. The Stanford University campus outside the City of Palo Alto is wildland but is designated a Local Responsibility Area (LRA); therefore, CAL FIRE has no jurisdictional responsibility. Since all these areas are unincorporated, land use planning, building permit processes, and local ordinances and regulations are under the jurisdiction of the County Board of Supervisors. The County Fire Marshal has jurisdiction for new construction permit fire/building code approval and inspection. There are no maintenance or defensible space inspections conducted by the Fire Marshal. CHAPTER 1 MT HAMILTON AND SAN ANTONIO VALLEY The Mt. Hamilton and San Antonio Valley area of eastern Santa Clara County is characterized as open space lands owned by public agencies and private ranches. -
Silicon Valley Images of America" Author: Sam Shueh Call Number: 979.473 S56 Indexed by Shirley Hunt
Index for "Silicon Valley Images of America" Author: Sam Shueh Call number: 979.473 S56 Indexed by Shirley Hunt Last Name/Place First Name page # Image type Other information 1890 ledger shows School expense Evergreen 40 photo Adobe headquarters San Jose San Jose 108 photo Founded 1982 to make desktop publishing software Aerial view of Sunnyvale 1940 Sunnyvale 57 photo Agnew clock tower rebuilt after 1906 Agnew Village 70 photo Well known as mental hospital until 1960s Agnew Development Center 1887 Agnew Village 68 photo Construction in process Agnew Development Center 1888 Agnew Village 68 photo Construction nearly complete Air intake on subsonic wind tunnel Mountain View 54 photo Current Alviso Port used for supply transport Alviso 112 photo Later used for yachts Amdahl Gene 2 photo 1963 IBM event demo of S/360 mainframe computer Apple Computer ad Apple-1 Cupertino 105 photo Photo 1976 Apple headquarters 1 Infinite Loop Cupertino 82 photo Apple release of iPhone NY store New York 106 photo People stood in line overnight before the release Assorted disk drives from startups Santa Clara 103 photo Computer Museum Assorted PCs created by companies Santa Clara 103 photo Computer Museum Babbage computer demonstrated Mountain View 92 photo Computer Museum Bank of Italy 1st and 2nd street San Jose 89 photo Photo 1890 Bank of Italy 1st and Santa Clara St. San Jose 89 photo Photo 1930s Bankrupt corporate property Mountain View 55 photo Bicycle race, 35th Annual Los Gatos 126 photo Photo 2008 Blackberry Farm golf course Santa Clara 77 photo Photo current day Bombers parked outside hangars Moffett Field 50 photo Bookmobile in Almaden garage 1967 Santa Clara County 116 photo Bubb family gathering Cupertino 86 photo Photo 19th century C.J. -
The New Telescope/Photometer Optical SETI Project of SETI Institute and the Lick Observatory
Astrobiology Science Conference 2010 (2010) 5211.pdf The New Telescope/Photometer Optical SETI Project of SETI Institute and the Lick Observatory. F. D. Drake1, R. P. S. Stone 2, D. Werthimer3, and S. A. Wright4, 1 SETI Institute, 515 N. Whisman Road, Mountain View CA 94043, [email protected], 2 Lick Observatory, University of California, Santa Cruz, Santa Cruz, California 95064, [email protected] 3 Space Sciences Laboratory, University of California, Berkeley, Berkeley, California, 94720, [email protected] 4 Astronomy Department, University of California, Berkeley, Berkeley, California 94720, [email protected]. Previously, we have conducted a search for brief, telescope, which is a slightly larger aperture than used nanosecond, optical pulses produced by hypothetical in our first project. Each OTA will have its own de- technologies on the planets of some 4600 stars [1]. tector, and these will be used to achieve goal (4) by The rationale for the search was based on the devel- being sensitive to NIR, and perhaps longer, wave- opment at the National Ignition Facility of lasers capa- lengths not captured in our original project. Thus there ble of producing nanosecond pulses of peak power of will be now seven photon streams, which are advanta- the order of a petawatt. Such pulses, when focused geous because they allow more sophisticated and ro- into a narrow beam by a large reflector, of the order of bust analyses of the statistics of the photon stream. perhaps 10 meters diameter, would create a nanosec- Also, the photon stream at each detector will have a ond light pulse which would, in the direction of the lower rate by about a factor of two, of photon arrival, beam, be of the order of thousands of times brighter compared to the streams in our first project, for a star than all the starlight. -
Look Back in Time | SJICIA | Lick Observatory | Exhibit | Silicon Valley
380 S. First Street, San Jose, CA 95113 | Tel. 408.298.8000 © 2016 Metro Newspapers 1 of 2 Finding the Art In Our Stars SJICA partners with Lick Observatory for new exhibit 'Look Back in Time' November 9, 2016 | By Jeffrey Edalatpour For some of us, looking up and out into the depths of space is as unsettling as, say, swimming alongside a blue whale. There's something about the infinity that can make a body feel small. But that's not the case for artist Russell Crotty. Marking the end of his two-year residency at the Institute of the Arts and Sciences at UC Santa Cruz, the San Jose Institute of Contemporary Art is presenting a solo exhibition of Crotty's work. With Look Back in Time — a collaboration between the IAS, the ICA and the Lick Observatory — Crotty, a self- The work of self-made astronomer and artist Russell Crotty is on display at 'Look Back in Time.' made astronomer, presents us with a beautiful interpretation of the stars. The title refers both to the concept of "lookback time" — that the light we see travelling in our telescopes is from the past — and the historical objects on display from the Lick, which opened in 1888. According to Cathy Kimball, ICA's executive director, Look Back was an opportunity, "not only to contextualize Crotty's work, but to really bring it more to life so that you better understand where Russell has come from in his passion and study of astronomy and how in-depth it is." She also described it as a site-specific immersive installation.