Conceptual Development of Quiet Turbofan Engines for Supersonic Aircraft
Total Page:16
File Type:pdf, Size:1020Kb
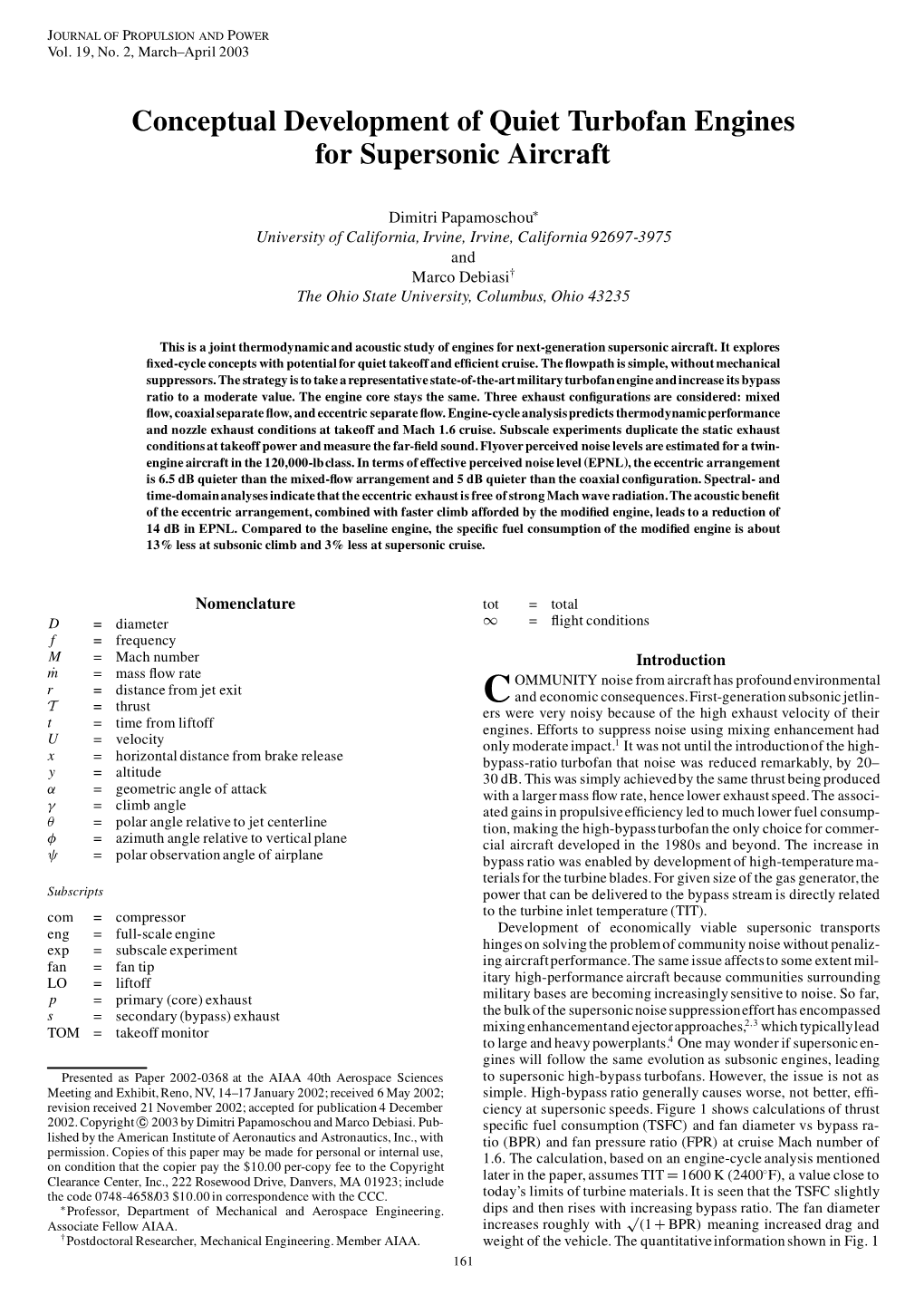
Load more
Recommended publications
-
Aerospace Engine Data
AEROSPACE ENGINE DATA Data for some concrete aerospace engines and their craft ................................................................................. 1 Data on rocket-engine types and comparison with large turbofans ................................................................... 1 Data on some large airliner engines ................................................................................................................... 2 Data on other aircraft engines and manufacturers .......................................................................................... 3 In this Appendix common to Aircraft propulsion and Space propulsion, data for thrust, weight, and specific fuel consumption, are presented for some different types of engines (Table 1), with some values of specific impulse and exit speed (Table 2), a plot of Mach number and specific impulse characteristic of different engine types (Fig. 1), and detailed characteristics of some modern turbofan engines, used in large airplanes (Table 3). DATA FOR SOME CONCRETE AEROSPACE ENGINES AND THEIR CRAFT Table 1. Thrust to weight ratio (F/W), for engines and their crafts, at take-off*, specific fuel consumption (TSFC), and initial and final mass of craft (intermediate values appear in [kN] when forces, and in tonnes [t] when masses). Engine Engine TSFC Whole craft Whole craft Whole craft mass, type thrust/weight (g/s)/kN type thrust/weight mini/mfin Trent 900 350/63=5.5 15.5 A380 4×350/5600=0.25 560/330=1.8 cruise 90/63=1.4 cruise 4×90/5000=0.1 CFM56-5A 110/23=4.8 16 -
2. Afterburners
2. AFTERBURNERS 2.1 Introduction The simple gas turbine cycle can be designed to have good performance characteristics at a particular operating or design point. However, a particu lar engine does not have the capability of producing a good performance for large ranges of thrust, an inflexibility that can lead to problems when the flight program for a particular vehicle is considered. For example, many airplanes require a larger thrust during takeoff and acceleration than they do at a cruise condition. Thus, if the engine is sized for takeoff and has its design point at this condition, the engine will be too large at cruise. The vehicle performance will be penalized at cruise for the poor off-design point operation of the engine components and for the larger weight of the engine. Similar problems arise when supersonic cruise vehicles are considered. The afterburning gas turbine cycle was an early attempt to avoid some of these problems. Afterburners or augmentation devices were first added to aircraft gas turbine engines to increase their thrust during takeoff or brief periods of acceleration and supersonic flight. The devices make use of the fact that, in a gas turbine engine, the maximum gas temperature at the turbine inlet is limited by structural considerations to values less than half the adiabatic flame temperature at the stoichiometric fuel-air ratio. As a result, the gas leaving the turbine contains most of its original concentration of oxygen. This oxygen can be burned with additional fuel in a secondary combustion chamber located downstream of the turbine where temperature constraints are relaxed. -
Clean Sky 2 JU Work Plan 2014/2015
Clean Sky 2 Joint Undertaking Amendment nr. 2 to Work Plan 2014-2015 Version 7 – March 2015 – Important Notice on the Clean Sky 2 Joint Undertaking (JU) Work Plan 2014-2015 This Work Plan covers the years 2014 and 2015. Due to the starting phase of the Clean Sky 2 Joint Undertaking under Regulation (EU) No 558/204 of 6 May 2014 the information contained in this Work Plan (topics list, description, budget, planning of calls) may be subject to updates. Any amended Work Plan will be announced and published on the JU’s website. © CSJU 2015 Please note that the copyright of this document and its content is the strict property of the JU. Any information related to this document disclosed by any other party shall not be construed as having been endorsed by to the JU. The JU expressly disclaims liability for any future changes of the content of this document. ~ Page intentionally left blank ~ Page 2 of 256 Clean Sky 2 Joint Undertaking Amendment nr. 2 to Work Plan 2014-2015 Document Version: V7 Date: 25/03/2015 Revision History Table Version n° Issue Date Reason for change V1 0First9/07/2014 Release V2 30/07/2014 The ANNEX I: 1st Call for Core-Partners: List and Full Description of Topics has been updated and regards the AIR-01-01 topic description: Part 2.1.2 - Open Rotor (CROR) and Ultra High by-pass ratio turbofan engine configurations (link to WP A-1.2), having a specific scope, was removed for consistency reasons. The intent is to publish this subject in the first Call for Partners. -
An Investigation Into the Feasibility of Using a Dual-Combustion Mode Ramjet in a High Mach Number Tactical Missile
Calhoun: The NPS Institutional Archive Theses and Dissertations Thesis Collection 1987 An investigation into the feasibility of using a dual-combustion mode ramjet in a high Mach number tactical missile. Vaught, Clifford B. http://hdl.handle.net/10945/22315 RT OHOOL .13-5002 NAVAL POSTGRADUATE SCHOOL Monterey, California THESIS AN INVESTIGATION INTO THE FEASIBILITY OF USING A DUAL-COMBUSTION MODE RAMJET IN A HIGH MACH NUMBER TACTICAL MISSILE by Clifford B. Vaught September 1987 Thesis Advisor: David W. Netzer Approved for public release; distribution unlimited T 234420 T LJNCIASSIFIED iCut'Tv c\ ASS F<CaTiOn OF Tm.S PaCf REPORT DOCUMENTATION PAGE »(PO«T SKuSiTr Classification lb HfcSTR'O'Vfc MARKINGS UNCLASSIFIED SECURITY ClASSi^CaTiON AuTmORiTy ) distribution/ availability or report Approved for public release; OEClASSiFiCATiON 'OOvVNGRAOiNG SCHEDULE distribution unlimited. PERFORMING ORGANISATION REPORT NUMBER(S) S MON1TOR1NG ORGANISATION REPORT NuMBER(S) NAME Of PERFORMING ORGANISATION 60 OFFICE SYMBOL ?4 NAME OF MON1TOR1NG ORGANISATION (it tppimb'e) aval Postgraduate School 67 Naval Postgraduate School ADORE SS iC/ry Sure tndfiPCode) 'b AOORESSfC.ey Sure »nd ///» Code) Dnterey, California 93943-5000 Monterey, California 93943-5000 I I NAME OF FuNOlNG' SPONSORING Bb OFUCE SYMBOL 9 PROCUREMENT INSTRUMENT lOEN .FiCA t l(JN NUMBER I ORGANISATION (It tpplxjbJ*) aval Weapons Center AODRESS(C-fy Stite *od Zip Cod*) 10 SOURCE OF FuNOiNG NUMBERS PROGRAM PRO;£CT TAS«C WORK UNIT ELEMENT NO NO NO ACCESSION NO lina Lake, California 93555-6001 T; l £ (include le<unty CI*U't<(*tiQn} M INVESTIGATION INTO TILE FEASIBILITY OF USING A DUAL-COMBUSTION I^DDE RAMJET IN A HIGH \G\ NUMBER TACTTCAL MISSILE PERSONA. -
Design of a Turbofan Engine Cycle with Afterburner for a Conceptual UAV
Design of a Turbofan Engine Cycle with Afterburner for a Conceptual UAV BJÖRN MONTGOMERIE Mixed fl ow turbofan schematic FOI is an assignment-based authority under the Ministry of Defence. The core activities are research, method and technology development, as well as studies for the use of defence and security. The organization employs around 1350 people of whom around 950 are researchers. This makes FOI the largest research institute in Sweden. FOI provides its customers with leading expertise in a large number of fi elds such as security-policy studies and analyses in defence and security, assessment of dif- ferent types of threats, systems for control and management of crises, protection against and management of hazardous substances, IT-security an the potential of new sensors. FOI Defence Research Agency Phone: +46 8 555 030 00 www.foi.se Systems Technology Fax: +46 8 555 031 00 FOI-R-- 1835 --SE Scientifi c report Systems Technology SE-164 90 Stockholm ISSN 1650-1942 December 2005 Björn Montgomerie Design of a Turbofan Engine Cycle with Afterburner for a Conceptual UAV FOI-R--1835--SE Scientific report Systems Technology ISSN 1650-1942 December 2005 Issuing organization Report number, ISRN Report type FOI – Swedish Defence Research Agency FOI-R--1835--SE Scientific report Systems Technology Research area code SE-164 90 Stockholm 7. Mobility and space technology, incl materials Month year Project no. December 2005 E830058 Sub area code 71 Unmanned Vehicles Sub area code 2 Author/s (editor/s) Project manager Björn Montgomerie Fredrik Haglind Approved by Monica Dahlén Sponsoring agency Swedish Defense Materiel Administration (FMV) Scientifically and technically responsible Fredrik Haglind Report title Design of a Turbofan Engine Cycle with Afterburner for a Conceptual UAV Abstract A study of two turbofan engine types has been carried out. -
04 Propulsion
Aircraft Design Lecture 2: Aircraft Propulsion G. Dimitriadis and O. Léonard APRI0004-1, Aerospace Design Project, Lecture 4 1 Introduction • A large variety of propulsion methods have been used from the very start of the aerospace era: – No propulsion (balloons, gliders) – Muscle (mostly failed) – Steam power (mostly failed) – Piston engines and propellers – Rocket engines – Jet engines – Pulse jet engines – Ramjet – Scramjet APRI0004-1, Aerospace Design Project, Lecture 4 2 Gliding flight • People have been gliding from the- mid 18th century. The Albatross II by Jean Marie Le Bris- 1849 Otto Lillienthal , 1895 APRI0004-1, Aerospace Design Project, Lecture 4 3 Human-powered flight • Early attempts were less than successful but better results were obtained from the 1960s onwards. Gerhardt Cycleplane (1923) MIT Daedalus (1988) APRI0004-1, Aerospace Design Project, Lecture 4 4 Steam powered aircraft • Mostly dirigibles, unpiloted flying models and early aircraft Clément Ader Avion III (two 30hp steam engines, 1897) Giffard dirigible (1852) APRI0004-1, Aerospace Design Project, Lecture 4 5 Engine requirements • A good aircraft engine is characterized by: – Enough power to fulfill the mission • Take-off, climb, cruise etc. – Low weight • High weight increases the necessary lift and therefore the drag. – High efficiency • Low efficiency increases the amount fuel required and therefore the weight and therefore the drag. – High reliability – Ease of maintenance APRI0004-1, Aerospace Design Project, Lecture 4 6 Piston engines • Wright Flyer: One engine driving two counter- rotating propellers (one port one starboard) via chains. – Four in-line cylinders – Power: 12hp – Weight: 77 kg APRI0004-1, Aerospace Design Project, Lecture 4 7 Piston engine development • During the first half of the 20th century there was considerable development of piston engines. -
An Online Performance Calculator for Ramjet, Turbojet, Turbofan, and Turboprop Engines
An Online Performance Calculator for Ramjet, Turbojet, Turbofan, and Turboprop Engines Evan P. Warner∗ Virginia Tech, Blacksburg, VA, 24061, USA This paper documents the theory, equations, and assumptions behind an HTML-based online performance calculator for ramjet, turbojet, turbofan, and turboprop engines. Based on inputs of design parameters, flight con- ditions, and engine parameters, the specific thrust (()), thrust specific fuel consumption ()(), propulsive efficiency ([ ?), thermal efficiency ([Cℎ), and overall efficiency ([0) will be output for the engine of interest. Several sample cases are analyzed to verify the functionality of the calculator. These sample cases are derived from engines associated with Virginia Tech, which include: Pratt & Whitney’s PT6A-20 and JT15D-1, Honeywell’s TFE731-2B, and the Rolls Royce Trent 1000. With the help of this calculator, students will now be able to verify their air-breathing jet engine performance value calculations. This calculator is available here. I. Nomenclature "0 = Ambient Mach Number 2 ?1 = Specific Heat of the Burner W0 = Ambient Specific Heat Ratio 2 ?C = Specific Heat of the Turbine W3 = Diffuser Specific Heat Ratio 2 ? 5 = Specific Heat of the Fan W2 = Compressor Specific Heat Ratio )0 = Ambient Static Temperature W1 = Burner Specific Heat Ratio ?0 = Ambient Static Pressure WC = Turbine Specific Heat Ratio ?4 = Exit Static Pressure W= = Nozzle Specific Heat Ratio '08A = Gas Constant for Air W 5 = Fan Specific Heat Ratio '?A>3 = Gas Constant for the Products of Fuel/Air Mixture W= 5 = Fan Nozzle -
Characteristics of the Specific Fuel Consumption for Jet Engines
1 Project Characteristics of the Specific Fuel Consumption for Jet Engines Author: Artur Bensel Supervisor: Prof. Dr.-Ing. Dieter Scholz, MSME Delivery Date: 31.08.2018 Faculty of Engineering and Computer Science Department of Automotive and Aeronautical Engineering 2 DOI: https://doi.org/10.15488/4316 URN: http://nbn-resolving.org/urn:nbn:de:gbv:18302-aero2018-08-31.016 Associated URLs: http://nbn-resolving.org/html/urn:nbn:de:gbv:18302-aero2018-08-31.016 © This work is protected by copyright The work is licensed under a Creative Commons Attribution-NonCommercial-ShareAlike 4.0 International License: CC BY-NC-SA http://creativecommons.org/licenses/by-nc-sa/4.0 Any further request may be directed to: Prof. Dr.-Ing. Dieter Scholz, MSME E-Mail see: http://www.ProfScholz.de This work is part of: Digital Library - Projects & Theses - Prof. Dr. Scholz http://library.ProfScholz.de Published by Aircraft Design and Systems Group (AERO) Department of Automotive and Aeronautical Engineering Hamburg University of Applied Science This report is deposited and archived: Deutsche Nationalbiliothek (http://www.dnb.de) Repositorium der Leibniz Universität Hannover (http://www.repo.uni-hannover.de) This report has associated published data in Harvard Dataverse: https://doi.org/10.7910/DVN/LZNNL1 3 Abstract Purpose of this project is a) the evaluation of the Thrust Specific Fuel Consumption (TSFC) of jet engines in cruise as a function of flight altitude, speed and thrust and b) the determina- tion of the optimum cruise speed for maximum range of jet airplanes based on TSFC charac- teristics from a). Related to a) a literature review shows different models for the influence of altitude and speed on TSFC. -
Design and Control of a Variable Geometry Turbofan with an Independently Modulated Third Stream
DESIGN AND CONTROL OF A VARIABLE GEOMETRY TURBOFAN WITH AN INDEPENDENTLY MODULATED THIRD STREAM DISSERTATION Presented in Partial Fulfillment of the Requirements for the Degree Doctor of Philosophy in the Graduate School of The Ohio State University By Ronald J. Simmons, M.S. * * * * * The Ohio State University 2009 Dissertation Committee: Professor Meyer Benzakein, Adviser Professor Richard Bodonyi Approved by Professor Jeffrey Bons Professor Jen-Ping Chen Adviser Professor Nicholas J. Kuprowicz Aerospace Engineering Graduate Program Distribution Statement A: Unlimited Distribution. Cleared for Public Release by AFRL/WS Public Affairs Case Number 88ABW-2009-1697 The views expressed in this article are those of the author and do not reflect the official policy or position of the United States Air Force, Department of Defense, or the U.S. Government. ABSTRACT Abstract Emerging 21st century military missions task engines to deliver the fuel efficiency of a high bypass turbofan while retaining the ability to produce the high specific thrust of a low bypass turbofan. This study explores the possibility of satisfying such competing demands by adding a second independently modulated bypass stream to the basic turbofan architecture. This third stream can be used for a variety of purposes including: providing a cool heat sink for dissipating aircraft heat loads, cooling turbine cooling air, and providing a readily available stream of constant pressure ratio air for lift augmentation. Furthermore, by modulating airflow to the second and third streams, it is possible to continuously match the engine‟s airflow demand to the inlet‟s airflow supply thereby reducing spillage and increasing propulsive efficiency. This research begins with a historical perspective of variable cycle engines and shows a logical progression to proposed architectures. -
TF-CLAWS: Candidate Low-Bypass, Mixed-Flow Turbofan Engine for a Next Generation Trainer
TF-CLAWS: Candidate Low-Bypass, Mixed-Flow Turbofan Engine for a Next Generation Trainer Faculty Advisors: Saeed Farokhi and Ray Taghvi Team Lead: Kyle P. Thompson Department of Aerospace Engineering Team Members: May 16, 2016 Daniel Fought Charles Yeo Timothy Luna Weiting Liu Zachary Smith ______________________________________________________________________________ TF-CLAWS: Candidate Low-Bypass, Mixed-Flow Turbofan Engine for a Next Generation Trainer Design Team: Daniel Fought #555924 Timothy Luna #665663 Weiting Liu #578948 Zachary Smith #665532 Kyle P. Thompson #665630 Team Lead Charles Yeo #508019 Faculty Advisors: Dr. Saeed Farokhi #005092 Dr. Ray Taghavi #024860 ______________________________________________________________________________ Aerospace Engineering Department i ______________________________________________________________________________ Abstract The TF-CLAWS is a two-spool, mixed flow, low bypass ratio turbofan engine designed as a candidate for an advanced trainer capable of replacing the T-38. The performance of the TF- CLAWS is shown to be superior to the engine currently installed on the T-38, the J85-GE-5A afterburning turbojet engine. The TF-CLAWS offers extreme performance gains over the baseline engine, providing a significantly lower TSFC for all major flight conditions, less overall engine weight, significantly lower fuel costs, and drastic increases to range and supersonic dash flight time duration. The improvements and technologies employed in the TF-CLAWS are presented as follows. Engine Component -
A Parametric Analysis of a Turbofan Engine with an Auxiliary Bypass Combustion Chamber – the Turboaux Engine
Old Dominion University ODU Digital Commons Mechanical & Aerospace Engineering Theses & Dissertations Mechanical & Aerospace Engineering Fall 12-2020 A Parametric Analysis of a Turbofan Engine with an Auxiliary Bypass Combustion Chamber – The TurboAux Engine Kaleab Fetahi Old Dominion University, [email protected] Follow this and additional works at: https://digitalcommons.odu.edu/mae_etds Part of the Mechanical Engineering Commons, Thermodynamics Commons, and the Transportation Commons Recommended Citation Fetahi, Kaleab. "A Parametric Analysis of a Turbofan Engine with an Auxiliary Bypass Combustion Chamber – The TurboAux Engine" (2020). Master of Science (MS), Thesis, Mechanical & Aerospace Engineering, Old Dominion University, DOI: 10.25777/55dp-vd74 https://digitalcommons.odu.edu/mae_etds/330 This Thesis is brought to you for free and open access by the Mechanical & Aerospace Engineering at ODU Digital Commons. It has been accepted for inclusion in Mechanical & Aerospace Engineering Theses & Dissertations by an authorized administrator of ODU Digital Commons. For more information, please contact [email protected]. A PARAMETRIC ANALYSIS OF A TURBOFAN ENGINE WITH AN AUXILIARY BYPASS COMBUSTION CHAMBER – THE TURBOAUX ENGINE by Kaleab Fetahi B.S. May 2019, Old Dominion University M.S. December 2020, Old Dominion University A Thesis Submitted to the Faculty of Old Dominion University in Partial Fulfillment of the Requirements for the Degree of MASTER OF SCIENCE MECHANICAL ENGINEERING OLD DOMINION UNIVERSITY December 2020 Approved by: Sharan Asundi (Director) Arthur C. Taylor (Co-Director) Adem Ibrahim (Member) ii ABSTRACT A PARAMETRIC ANALYSIS OF A TURBOFAN ENGINE WITH AN AUXILIARY BYPASS COMBUSTION CHAMBER – THE TURBOAUX ENGINE Kaleab Fetahi Old Dominion University, 2020 Director: Dr. Sharan Asundi A parametric study of a novel turbofan engine with an auxiliary combustion chamber, nicknamed the TurboAux engine is presented. -
Airbus Technical Magazine April 2020
Airbus technical magazine April 2020 #65 FAST Flight Airworthiness Support Technology FAST app: all articles to read, share, comment Newsfeed by Airbus app: short, relevant news for customers FAST FAST and Newsfeed apps are downloadable to your preferred device Cover photo: A350 cockpit Airbus technical magazine FAST magazine articles, primarily dedicated to Airbus commercial aircraft customers, are written by technical FAST app: all articles to read, share, comment #65 experts and focus on what is informative and useful. Newsfeed by Airbus app: short, relevant news for customers Learn about innovations and evolutions to Airbus aircraft, as well as best practices to help optimise fleet performance. And see where Airbus is working, sometimes with key players in the industry, to continue to support customers and prepare the future. Switching to the FAST app will enable you to share FAST and comment. Any changes in preference can be Flight Airworthiness Support Technology sent to your field service or to the editor. • Chief Editor: Deborah Buckler And for short news updates for customers, get the • Writing support: Newsfeed by Airbus app (see opposite). - Beetroot: Tom Whitney, - Parkinson Stephens Editorial: Ed Parkinson, Kate Redfern, Geoff Poulton • Design: Pont Bleu • Cover images: A. Tchaikovski and H. Gousset, Master Films • Printer: Amadio • Authorisation for reprinting FAST magazine articles: Propulsion system 04 [email protected] integration FAST magazine availability: From design to entry-into-service On the FAST app (see QR code opposite page) Airbus website: www.aircraft.airbus.com/support-services/publications/ The defining moment 14 Making it easier to choose ISSN 1293-5476 cabin options Photo copyright Airbus.