Turbofan Engine Bypass Ratio As a Function of Thrust and Fuel Flow
Total Page:16
File Type:pdf, Size:1020Kb
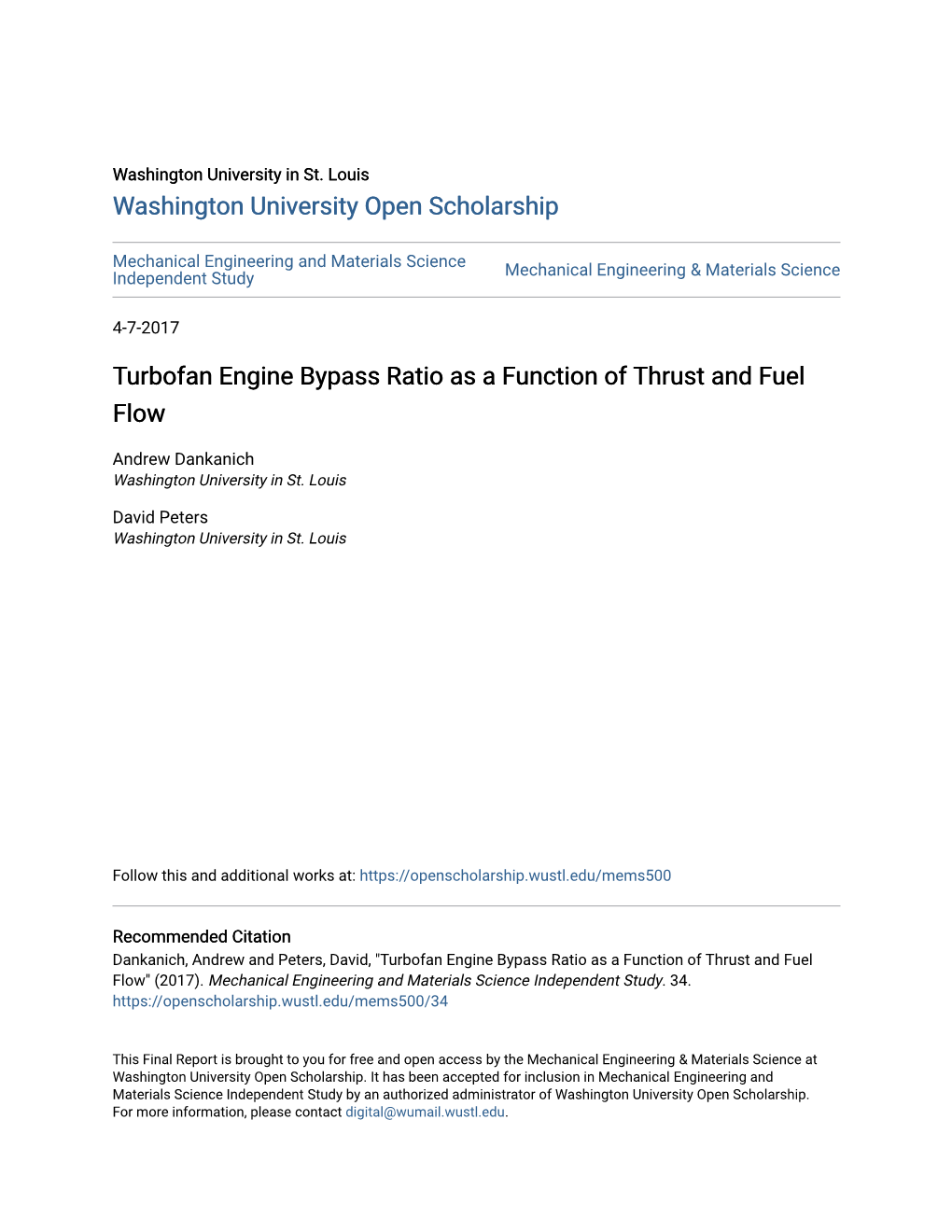
Load more
Recommended publications
-
Aerospace Engine Data
AEROSPACE ENGINE DATA Data for some concrete aerospace engines and their craft ................................................................................. 1 Data on rocket-engine types and comparison with large turbofans ................................................................... 1 Data on some large airliner engines ................................................................................................................... 2 Data on other aircraft engines and manufacturers .......................................................................................... 3 In this Appendix common to Aircraft propulsion and Space propulsion, data for thrust, weight, and specific fuel consumption, are presented for some different types of engines (Table 1), with some values of specific impulse and exit speed (Table 2), a plot of Mach number and specific impulse characteristic of different engine types (Fig. 1), and detailed characteristics of some modern turbofan engines, used in large airplanes (Table 3). DATA FOR SOME CONCRETE AEROSPACE ENGINES AND THEIR CRAFT Table 1. Thrust to weight ratio (F/W), for engines and their crafts, at take-off*, specific fuel consumption (TSFC), and initial and final mass of craft (intermediate values appear in [kN] when forces, and in tonnes [t] when masses). Engine Engine TSFC Whole craft Whole craft Whole craft mass, type thrust/weight (g/s)/kN type thrust/weight mini/mfin Trent 900 350/63=5.5 15.5 A380 4×350/5600=0.25 560/330=1.8 cruise 90/63=1.4 cruise 4×90/5000=0.1 CFM56-5A 110/23=4.8 16 -
Noise Reduction Technologies for Turbofan Engines
NASA/TM—2007-214495 Noise Reduction Technologies for Turbofan Engines Dennis L. Huff Glenn Research Center, Cleveland, Ohio September 2007 NASA STI Program . in Profile Since its founding, NASA has been dedicated to the • CONFERENCE PUBLICATION. Collected advancement of aeronautics and space science. The papers from scientific and technical NASA Scientific and Technical Information (STI) conferences, symposia, seminars, or other program plays a key part in helping NASA maintain meetings sponsored or cosponsored by NASA. this important role. • SPECIAL PUBLICATION. Scientific, The NASA STI Program operates under the auspices technical, or historical information from of the Agency Chief Information Officer. It collects, NASA programs, projects, and missions, often organizes, provides for archiving, and disseminates concerned with subjects having substantial NASA’s STI. The NASA STI program provides access public interest. to the NASA Aeronautics and Space Database and its public interface, the NASA Technical Reports Server, • TECHNICAL TRANSLATION. English- thus providing one of the largest collections of language translations of foreign scientific and aeronautical and space science STI in the world. technical material pertinent to NASA’s mission. Results are published in both non-NASA channels and by NASA in the NASA STI Report Series, which Specialized services also include creating custom includes the following report types: thesauri, building customized databases, organizing and publishing research results. • TECHNICAL PUBLICATION. Reports of completed research or a major significant phase For more information about the NASA STI of research that present the results of NASA program, see the following: programs and include extensive data or theoretical analysis. Includes compilations of significant • Access the NASA STI program home page at scientific and technical data and information http://www.sti.nasa.gov deemed to be of continuing reference value. -
A Comparison of Combustor-Noise Models – AIAA 2012-2087
A Comparison of Combustor-Noise Models – AIAA 2012-2087 Lennart S. Hultgren, NASA Glenn Research Center, Cleveland, OH 44135 Summary The present status of combustor-noise prediction in the NASA Aircraft Noise Prediction Program (ANOPP)1 for current- generation (N) turbofan engines is summarized. Several semi-empirical models for turbofan combustor noise are discussed, including best methods for near-term updates to ANOPP. An alternate turbine-transmission factor2 will appear as a user selectable option in the combustor-noise module GECOR in the next release. The three-spectrum model proposed by Stone et al.3 for GE turbofan-engine combustor noise is discussed and compared with ANOPP predictions for several relevant cases. Based on the results presented herein and in their report,3 it is recommended that the application of this fully empirical combustor-noise prediction method be limited to situations involving only General-Electric turbofan engines. Long-term needs and challenges for the N+1 through N+3 time frame are discussed. Because the impact of other propulsion-noise sources continues to be reduced due to turbofan design trends, advances in noise-mitigation techniques, and expected aircraft configuration changes, the relative importance of core noise is expected to greatly increase in the future. The noise-source structure in the combustor, including the indirect one, and the effects of the propagation path through the engine and exhaust nozzle need to be better understood. In particular, the acoustic consequences of the expected trends toward smaller, highly efficient gas- generator cores and low-emission fuel-flexible combustors need to be fully investigated since future designs are quite likely to fall outside of the parameter space of existing (semi-empirical) prediction tools. -
Comparison of Helicopter Turboshaft Engines
Comparison of Helicopter Turboshaft Engines John Schenderlein1, and Tyler Clayton2 University of Colorado, Boulder, CO, 80304 Although they garnish less attention than their flashy jet cousins, turboshaft engines hold a specialized niche in the aviation industry. Built to be compact, efficient, and powerful, turboshafts have made modern helicopters and the feats they accomplish possible. First implemented in the 1950s, turboshaft geometry has gone largely unchanged, but advances in materials and axial flow technology have continued to drive higher power and efficiency from today's turboshafts. Similarly to the turbojet and fan industry, there are only a handful of big players in the market. The usual suspects - Pratt & Whitney, General Electric, and Rolls-Royce - have taken over most of the industry, but lesser known companies like Lycoming and Turbomeca still hold a footing in the Turboshaft world. Nomenclature shp = Shaft Horsepower SFC = Specific Fuel Consumption FPT = Free Power Turbine HPT = High Power Turbine Introduction & Background Turboshaft engines are very similar to a turboprop engine; in fact many turboshaft engines were created by modifying existing turboprop engines to fit the needs of the rotorcraft they propel. The most common use of turboshaft engines is in scenarios where high power and reliability are required within a small envelope of requirements for size and weight. Most helicopter, marine, and auxiliary power units applications take advantage of turboshaft configurations. In fact, the turboshaft plays a workhorse role in the aviation industry as much as it is does for industrial power generation. While conventional turbine jet propulsion is achieved through thrust generated by a hot and fast exhaust stream, turboshaft engines creates shaft power that drives one or more rotors on the vehicle. -
The Potential of Turboprops to Reduce Fuel Consumption in the Chinese Aviation System
THE POTENTIAL OF TURBOPROPS TO REDUCE FUEL CONSUMPTION IN THE CHINESE AVIATION SYSTEM Megan S. Ryerson, Xin Ge Department of City and Regional Planning Department of Electrical and Systems Engineering University of Pennsylvania [email protected] ICRAT 2014 Agenda • Introduction • Data collection • Turboprops in the current CAS network • Spatial trends for short-haul aviation • Regional jet and turboprop trade space • Turboprops in the future CAS network 2 1. Introduction – Growth of the Chinese Aviation System Number of Airports • The Chinese aviation system is in a period 300 of rapid growth • China’s civil aviation system grew at a rate 250 244 of 17.6%/year, 1980 - 2009 • Number of airports grew from 77 to 166 and annual traffic volume increasing from 3.43 million to 230 million 200 • The Civil Aviation Administration of China 166 (CAAC) maintains a target of 244 airports 150 across the country by 2020 • The CAAC plans for 80% of urban and suburban areas to be within a 100km (62 100 77 miles) of aviation service by 2020 • Plans also include strengthening hub-and- 50 spoke networks across the country to meet the dual goals of improving the competitiveness and efficiency of domestic 0 and international aviation. 1980 2009 2020 (Planned) 3 1. Introduction – Reform of the Chinese Aviation System • Consolidation Strong national hubs + insufficient regional coverage • Regional commuter airlines could fill this gap by partnering with China’s major carriers and serving the second-tier and emerging hubs (Shaw, 2009) 4 1. Introduction – Aircraft of the Short Haul Chinese Aviation System Narrow Body Jet Fuel per seat: 7.9 gal Regional Jet Fuel per seat: 19.0 gal Turboprop Fuel per seat: 4.35 gal 5 1. -
6. Chemical-Nuclear Propulsion MAE 342 2016
2/12/20 Chemical/Nuclear Propulsion Space System Design, MAE 342, Princeton University Robert Stengel • Thermal rockets • Performance parameters • Propellants and propellant storage Copyright 2016 by Robert Stengel. All rights reserved. For educational use only. http://www.princeton.edu/~stengel/MAE342.html 1 1 Chemical (Thermal) Rockets • Liquid/Gas Propellant –Monopropellant • Cold gas • Catalytic decomposition –Bipropellant • Separate oxidizer and fuel • Hypergolic (spontaneous) • Solid Propellant ignition –Mixed oxidizer and fuel • External ignition –External ignition • Storage –Burn to completion – Ambient temperature and pressure • Hybrid Propellant – Cryogenic –Liquid oxidizer, solid fuel – Pressurized tank –Throttlable –Throttlable –Start/stop cycling –Start/stop cycling 2 2 1 2/12/20 Cold Gas Thruster (used with inert gas) Moog Divert/Attitude Thruster and Valve 3 3 Monopropellant Hydrazine Thruster Aerojet Rocketdyne • Catalytic decomposition produces thrust • Reliable • Low performance • Toxic 4 4 2 2/12/20 Bi-Propellant Rocket Motor Thrust / Motor Weight ~ 70:1 5 5 Hypergolic, Storable Liquid- Propellant Thruster Titan 2 • Spontaneous combustion • Reliable • Corrosive, toxic 6 6 3 2/12/20 Pressure-Fed and Turbopump Engine Cycles Pressure-Fed Gas-Generator Rocket Rocket Cycle Cycle, with Nozzle Cooling 7 7 Staged Combustion Engine Cycles Staged Combustion Full-Flow Staged Rocket Cycle Combustion Rocket Cycle 8 8 4 2/12/20 German V-2 Rocket Motor, Fuel Injectors, and Turbopump 9 9 Combustion Chamber Injectors 10 10 5 2/12/20 -
High Pressure Ratio Intercooled Turboprop Study
E AMEICA SOCIEY O MECAICA EGIEES 92-GT-405 4 E. 4 S., ew Yok, .Y. 00 h St hll nt b rpnbl fr ttnt r pnn dvnd In ppr r n d n t tn f th St r f t vn r Stn, r prntd In t pbltn. n rnt nl f th ppr pblhd n n ASME rnl. pr r vlbl fr ASME fr fftn nth ftr th tn. rntd n USA Copyright © 1992 by ASME ig essue aio Iecooe uoo Suy C. OGES Downloaded from http://asmedigitalcollection.asme.org/GT/proceedings-pdf/GT1992/78941/V002T02A028/2401669/v002t02a028-92-gt-405.pdf by guest on 23 September 2021 Sundstrand Power Systems San Diego, CA ASAC NOMENCLATURE High altitude long endurance unmanned aircraft impose KFT Altitude Thousands Feet unique contraints on candidate engine propulsion systems and HP Horsepower types. Piston, rotary and gas turbine engines have been proposed for such special applications. Of prime importance is the HIPIT High Pressure Intercooled Turbine requirement for maximum thermal efficiency (minimum specific Mn Flight Mach Number fuel consumption) with minimum waste heat rejection. Engine weight, although secondary to fuel economy, must be evaluated Mls Inducer Mach Number when comparing various engine candidates. Weight can be Specific Speed (Dimensionless) minimized by either high degrees of turbocharging with the Ns piston and rotary engines, or by the high power density Exponent capabilities of the gas turbine. pps Airflow The design characteristics and features of a conceptual high SFC Specific Fuel Consumption pressure ratio intercooled turboprop are discussed. The intended application would be for long endurance aircraft flying TIT Turbine Inlet Temperature °F at an altitude of 60,000 ft.(18,300 m). -
The Historical Fuel Efficiency Characteristics of Regional Aircraft from Technological, Operational, and Cost Perspectives
The Historical Fuel Efficiency Characteristics of Regional Aircraft from Technological, Operational, and Cost Perspectives Raffi Babikian, Stephen P. Lukachko and Ian A. Waitz* Department of Aeronautics and Astronautics Massachusetts Institute of Technology 77 Massachusetts Ave., Cambridge, MA 02139 ABSTRACT To develop approaches that effectively reduce aircraft emissions, it is necessary to understand the mechanisms that have enabled historical improvements in aircraft efficiency. This paper focuses on the impact of regional aircraft on the U.S. aviation system and examines the technological, operational and cost characteristics of turboprop and regional jet aircraft. Regional aircraft are 40% to 60% less fuel efficient than their larger narrow- and wide-body counterparts, while regional jets are 10% to 60% less fuel efficient than turboprops. Fuel efficiency differences can be explained largely by differences in aircraft operations, not technology. Direct operating costs per revenue passenger kilometer are 2.5 to 6 times higher for regional aircraft because they operate at lower load factors and perform fewer miles over which to spread fixed costs. Further, despite incurring higher fuel costs, regional jets are shown to have operating costs similar to turboprops when flown over comparable stage lengths. Keywords: Regional aircraft, environment, regional jet, turboprop 1. INTRODUCTION The rapid growth of worldwide air travel has prompted concern about the influence of aviation activities on the environment. Demand for air travel has grown at an average rate of 9.0% per year since 1960 and at approximately 4.5% per year over the last decade (IPCC, 1999; FAA, 2000a). Barring any serious economic downturn or significant policy changes, various * Contact author: 617-253-0218 (phone), 617-258-6093 (fax), [email protected] (email) 1 organizations have estimated future worldwide growth will average 5% annually through at least 2015 (IPCC, 1999; Boeing, 2000; Airbus, 2000). -
2. Afterburners
2. AFTERBURNERS 2.1 Introduction The simple gas turbine cycle can be designed to have good performance characteristics at a particular operating or design point. However, a particu lar engine does not have the capability of producing a good performance for large ranges of thrust, an inflexibility that can lead to problems when the flight program for a particular vehicle is considered. For example, many airplanes require a larger thrust during takeoff and acceleration than they do at a cruise condition. Thus, if the engine is sized for takeoff and has its design point at this condition, the engine will be too large at cruise. The vehicle performance will be penalized at cruise for the poor off-design point operation of the engine components and for the larger weight of the engine. Similar problems arise when supersonic cruise vehicles are considered. The afterburning gas turbine cycle was an early attempt to avoid some of these problems. Afterburners or augmentation devices were first added to aircraft gas turbine engines to increase their thrust during takeoff or brief periods of acceleration and supersonic flight. The devices make use of the fact that, in a gas turbine engine, the maximum gas temperature at the turbine inlet is limited by structural considerations to values less than half the adiabatic flame temperature at the stoichiometric fuel-air ratio. As a result, the gas leaving the turbine contains most of its original concentration of oxygen. This oxygen can be burned with additional fuel in a secondary combustion chamber located downstream of the turbine where temperature constraints are relaxed. -
Helicopter Turboshafts
Helicopter Turboshafts Luke Stuyvenberg University of Colorado at Boulder Department of Aerospace Engineering The application of gas turbine engines in helicopters is discussed. The work- ings of turboshafts and the history of their use in helicopters is briefly described. Ideal cycle analyses of the Boeing 502-14 and of the General Electric T64 turboshaft engine are performed. I. Introduction to Turboshafts Turboshafts are an adaptation of gas turbine technology in which the principle output is shaft power from the expansion of hot gas through the turbine, rather than thrust from the exhaust of these gases. They have found a wide variety of applications ranging from air compression to auxiliary power generation to racing boat propulsion and more. This paper, however, will focus primarily on the application of turboshaft technology to providing main power for helicopters, to achieve extended vertical flight. II. Relationship to Turbojets As a variation of the gas turbine, turboshafts are very similar to turbojets. The operating principle is identical: atmospheric gases are ingested at the inlet, compressed, mixed with fuel and combusted, then expanded through a turbine which powers the compressor. There are two key diferences which separate turboshafts from turbojets, however. Figure 1. Basic Turboshaft Operation Note the absence of a mechanical connection between the HPT and LPT. An ideal turboshaft extracts with the HPT only the power necessary to turn the compressor, and with the LPT all remaining power from the expansion process. 1 of 10 American Institute of Aeronautics and Astronautics A. Emphasis on Shaft Power Unlike turbojets, the primary purpose of which is to produce thrust from the expanded gases, turboshafts are intended to extract shaft horsepower (shp). -
Improving Engine Efficiency Through Core Developments
IMPROVING ENGINE EFFICIENCY THROUGH CORE DEVELOPMENTS Brief summary: The NASA Environmentally Responsible Aviation (ERA) Project and Fundamental Aeronautics Projects are supporting compressor and turbine research with the goal of reducing aircraft engine fuel burn and greenhouse gas emissions. The primary goals of this work are to increase aircraft propulsion system fuel efficiency for a given mission by increasing the overall pressure ratio (OPR) of the engine while maintaining or improving aerodynamic efficiency of these components. An additional area of work involves reducing the amount of cooling air required to cool the turbine blades while increasing the turbine inlet temperature. This is complicated by the fact that the cooling air is becoming hotter due to the increases in OPR. Various methods are being investigated to achieve these goals, ranging from improved compressor three-dimensional blade designs to improved turbine cooling hole shapes and methods. Finally, a complementary effort in improving the accuracy, range, and speed of computational fluid mechanics (CFD) methods is proceeding to better capture the physical mechanisms underlying all these problems, for the purpose of improving understanding and future designs. National Aeronautics and Space Administration Improving Engine Efficiency Through Core Developments Dr. James Heidmann Project Engineer for Propulsion Technology (acting) Environmentally Responsible Aviation Integrated Systems Research Program AIAA Aero Sciences Meeting January 6, 2011 www.nasa.gov NASA’s Subsonic -
Session 6:Analytical Approximations for Low Thrust Maneuvers
Session 6: Analytical Approximations for Low Thrust Maneuvers As mentioned in the previous lecture, solving non-Keplerian problems in general requires the use of perturbation methods and many are only solvable through numerical integration. However, there are a few examples of low-thrust space propulsion maneuvers for which we can find approximate analytical expressions. In this lecture, we explore a couple of these maneuvers, both of which are useful because of their precision and practical value: i) climb or descent from a circular orbit with continuous thrust, and ii) in-orbit repositioning, or walking. Spiral Climb/Descent We start by writing the equations of motion in polar coordinates, 2 d2r �dθ � µ − r + = a (1) 2 2 r dt dt r 2 d θ 2 dr dθ aθ + = (2) 2 dt r dt dt r We assume continuous thrust in the angular direction, therefore ar = 0. If the acceleration force along θ is small, then we can safely assume the orbit will remain nearly circular and the semi-major axis will be just slightly different after one orbital period. Of course, small and slightly are vague words. To make the analysis rigorous, we need to be more precise. Let us say that for this approximation to be valid, the angular acceleration has to be much smaller than the corresponding centrifugal or gravitational forces (the last two terms in the LHS of Eq. (1)) and that the radial acceleration (the first term in the LHS in the same equation) is negligible. Given these assumptions, from Eq. (1), dθ r µ d2θ 3 r µ dr ≈ ! ≈ − (3) 3 2 5 dt r dt 2 r dt Substituting into Eq.