Application Guide to Ximopac-Mo001 and Mo003 Mo-Based Proprietary Metathesis Catalysts Formulated in Paraffin
Total Page:16
File Type:pdf, Size:1020Kb
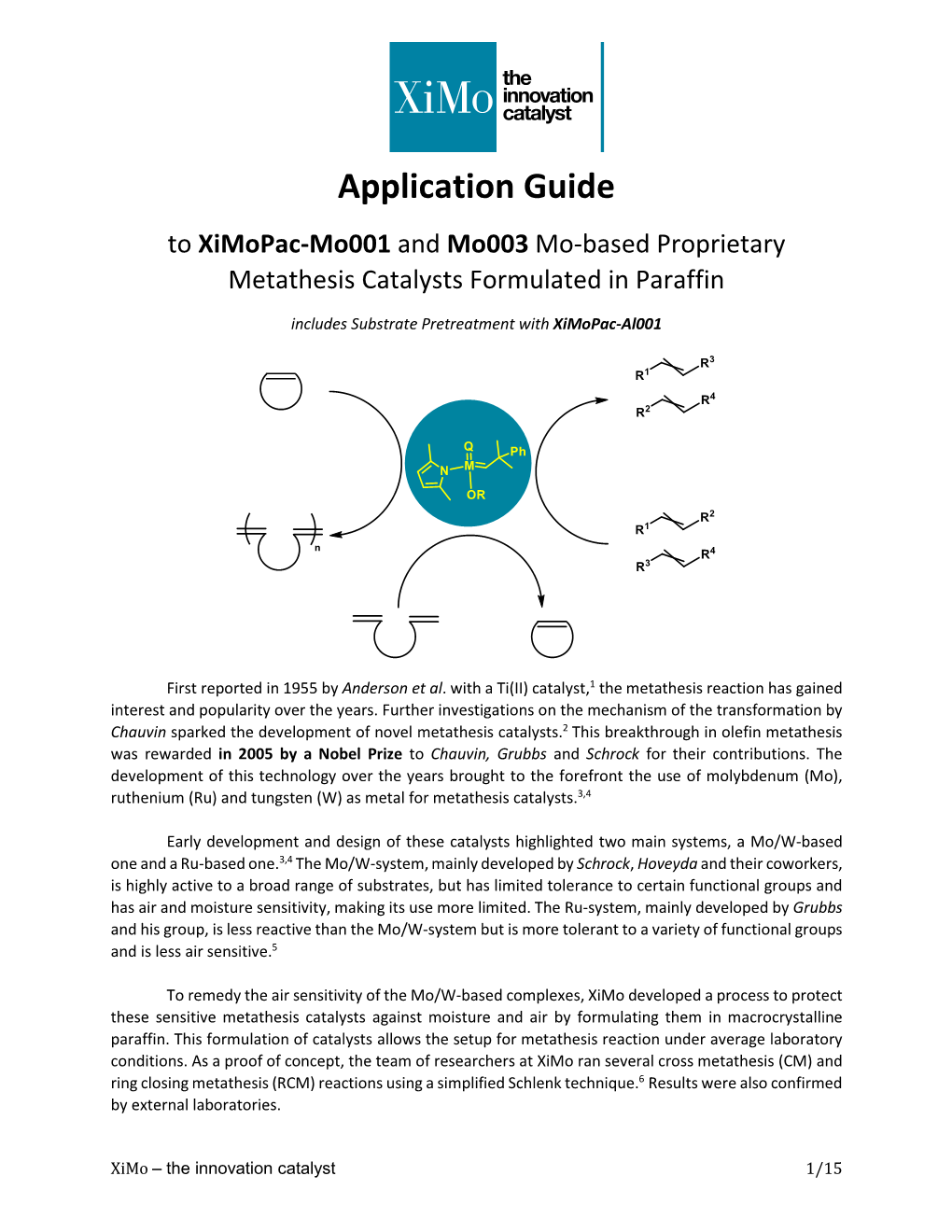
Load more
Recommended publications
-
Novel Synthesis of Polyhydrogenated Fullerenes
NOVEL SYNTHESIS OF POLYHYDROGENATED FULLERENES A thesis submitted in partial fulfillment of the requirements for the degree of Master of Science By ANGELA M. CAMPO B.S. in Chemistry, Wright State University 2001 2010 Wright State University WRIGHT STATE UNIVERSITY SCHOOL OF GRADUATE STUDIES October 21 , 2010 I HEREBY RECOMMEND THAT THE THESIS PREPARED UNDER MY SUPERVISION BY Angela M. Campo ENTITLED Novel Synthesis of polyhydrogenated fullerenes BE ACCEPTED IN PARTIAL FULFILLMENT OF THE REQUIREMENTS FOR THE DEGREE OF Master of Science . ______________________________ Eric Fossum, Ph.D. Thesis Director ______________________________ Kenneth Turnbull, Ph.D. Chair, Chemistry Department Committee on Final Examination College of Science and Mathematics _________________________________ Eric Fossum, Ph.D. _________________________________ Kenneth Turnbull, Ph.D. _________________________________ Daniel Ketcha, Ph.D. _________________________________ Douglas Dudis, Ph.D. _________________________________ Andrew T. Hsu, Ph.D. Dean, School of Graduate Studies ABSTRACT Campo, Angela M. M.S., Department of Chemistry, Wright State University, 2010. Novel synthesis of polyhydrogenated fullerenes Hydrogenated fullerenes are of interest as a starting material in metal fulleride synthesis. By reacting C60H2 with various metals, alloyed metal fullerides could be produced. To achieve this goal, first a reliable synthesis of C60H2 must be determined. C60H2 is difficult to synthesis exclusively; C60H4 and C60H6 are also produced. Reduction of C60 with NaBH4 produced a mixture of products as well as excessive unreacted C60. Attempts to modify this reaction to achieve C60H2 exclusively were unsuccessful. A novel route was explored by reducing C60 with thiophenol. This reaction produced C60H2 after 4 days. In an effort to speed up the reaction time, C60 was reduced with Zn(Cu) and thiophenol as a proton source. -
Materials Engineering, Characterization, and Applications of the Organic- Based Magnet, V[TCNE]
Materials engineering, characterization, and applications of the organic- based magnet, V[TCNE] DISSERTATION Presented in Partial Fulfillment of the Requirements for the Degree Doctor of Philosophy in the Graduate School of The Ohio State University By Megan Harberts Graduate Program in Physics The Ohio State University 2015 Dissertation Committee: Professor Ezekiel Johnston-Halperin, Advisor Professor Jay Gupta Professor Annika Peter Professor William Putikka Copyright by Megan Harberts 2015 Abstract Organic materials have advantageous properties such as low cost and mechanical flexibility that have made them attractive to complement traditional materials used in electronics and have led to commercial success, especially in organic light emitting diodes (OLEDs). Many rapidly advancing technologies incorporate magnetic materials, leading to the potential for creating analogous organic-based magnetic applications. The semiconducting ferrimagnet, vanadium tetracyanoethylene, V[TCNE]x~2, exhibits room temperature magnetic ordering which makes it an attractive candidate. My research is focused on development of thin films of V[TCNE]x~2 through advancement in growth, materials engineering, and applications. My thesis is broken up into two sections, the first which provides background and details of V[TCNE]x~2 growth and characterization. The second section focuses on advances beyond V[TCNE]x~2 film growth. The ordering of the chapters is for the ease of the reader, but encompasses work that I led and robust collaborations that I have participated in. V[TCNE]x~2 films are deposited through a chemical vapor deposition process (CVD). My advancements to the growth process have led to higher quality films which have higher magnetic ordering temperatures, more magnetically homogenous samples, and extremely narrow ferromagnetic resonance (FMR) linewidths. -
Functionalization of AFM Tips with Click Chemistry
Functionalization of AFM tips with Click Chemistry Hermann J. Gruber, Institute of Biophysics, Johannes Kepler University, Gruberstrasse 40, 4020 Linz, Austria – Europe [email protected] Terms and conditions 1. If you publish data obtained with this manual, you are expected to cite the link from where it can be downloaded ( http://www.jku.at/biophysics/content ). 2. Our manuals are often updated. Only the newest version should be used. Please check whether you have the latest version. The date is obvious from the file name. 3. Copy right: You are entitled to distribute this manual, provided that the document is not split or altered in any way . 4. Exclusion of warranty: The procedures described in this manual have successfully been applied by different users in our laboratory. We have done our best to provide descriptions that will enable reproduction in other laboratories. Nevertheless, failure may occur due to impurities or ingredients/components or circumstances which cannot be foreseen. 5. Scope: The procedures have been optimized for AFM tip functionalization. They may work in related fields but the optimal parameters may be different. For instance, much slower coupling will occur on protein-resistant surfaces. 6. You are kindly asked for feed-back concerning errors, unexpected results, or potential hazards not foreseen at present. 10_AFM_tip_click_chemistry_2016_05_06 1 [email protected] AFM tips with click chemistry short version for risks and details see full length procedure 1. Aminofunctionalization of the cantilever(s) (see AFM_tip_aminofunctionalization). 2. Dissolve 1 portion of Azide-PEG-NHS (1 mg) in chloroform (0.5 mL), transfer the solution into the reaction chamber, add triethylamine (30 µL) and mix. -
Alkali Metal Complexes of Silyl-Substituted Ansa-(Tris)Allyl Ligands: Metal-, Co-Ligand- and Substituent-Dependent Stereochemistry
FULL PAPER DOI: 10.1002/ejic.200900618 Alkali Metal Complexes of Silyl-Substituted ansa-(Tris)allyl Ligands: Metal-, Co-Ligand- and Substituent-Dependent Stereochemistry Scott A. Sulway,[a] Roman Girshfeld,[a] Sophia A. Solomon,[a] Christopher A. Muryn,[a] Jordi Poater,[b] Miquel Solà,[b] F. Matthias Bickelhaupt,*[c] and Richard A. Layfield*[a] Keywords: Allyl ligands / Lithium / Sodium / Potassium / Stereochemistry 2 The structures of alkali metal complexes of silyl-substituted [L {K(OEt2)2}2KLi(µ4-OtBu)]2 (7), in which the lithium tert- 3– 1 ansa-tris(allyl) ligands [RSi(C3H3SiMe3)3] (R = Me, L ;or butoxide by-product is incorporated into a hexa(allylpotas- 2 1 1 Ph, L ) are discussed. Triple deprotonation of L H3 by sium) macrocycle. Triple deprotonation of L H3 with nBuLi 1 1 nBuNa/tmeda affords [L {Na(tmeda)}3](4) in which the so- and the terdentate Lewis base pmdeta results in [L Li- n dium cations are complexed by η -allyl ligands and the silyl (pmdeta)}3](8), in which the three allyl groups do not µ- substituents adopt [exo,exo][endo,exo]2 stereochemistries in bridge between lithium cations, resulting in an [exo,exo]3 one crystallographically disordered form and [endo,exo]3 in stereochemistry of the silyl substituents. NMR spectroscopic 2 another. Triple deprotonation of L H3 with nBuLi/tmeda re- studies reveal complicated solution-phase behaviour for 4, 6 2 sults in the formation of [L {Li(tmeda)}3](5), the structure of and 7, whereas the solid-state structures of 5 and 8 are pre- which features silyl substituents with [exo,exo]2[endo,exo] served in solution. -
Structural, Optical, and Electrical Properties of Pbse Nanocrystal Solids Treated Thermally Or with Simple Amines Matt Law,* Joseph M
Published on Web 04/09/2008 Structural, Optical, and Electrical Properties of PbSe Nanocrystal Solids Treated Thermally or with Simple Amines Matt Law,* Joseph M. Luther, Qing Song, Barbara K. Hughes, Craig L. Perkins, and Arthur J. Nozik* National Renewable Energy Laboratory, Golden, Colorado 80401 Received January 3, 2008; E-mail: [email protected]; [email protected] Abstract: We describe the structural, optical, and electrical properties of films of spin-cast, oleate-capped PbSe nanocrystals that are treated thermally or chemically in solutions of hydrazine, methylamine, or pyridine to produce electronically coupled nanocrystal solids. Postdeposition heat treatments trigger nanocrystal sintering at ∼200 °C, before a substantial fraction of the oleate capping group evaporates or pyrolyzes. The sintered nanocrystal films have a large hole density and are highly conductive. Most of the amine treatments preserve the size of the nanocrystals and remove much of the oleate, decreasing the separation between nanocrystals and yielding conductive films. X-ray scattering, X-ray photoelectron and optical spectroscopy, electron microscopy, and field-effect transistor electrical measurements are used to compare the impact of these chemical treatments. We find that the concentration of amines adsorbed to the NC films is very low in all cases. Treatments in hydrazine in acetonitrile remove only 2-7% of the oleate yet result in high-mobility n-type transistors. In contrast, ethanol-based hydrazine treatments remove 85-90% of the original oleate load. Treatments in pure ethanol strip 20% of the oleate and create conductive p-type transistors. Methylamine- and pyridine-treated films are also p-type. These chemically treated films oxidize rapidly in air to yield, after short air exposures, highly conductive p-type nanocrystal solids. -
PTA-Li) Towards Organotin, Silicon, and Boron Chlorides
University of Nevada, Reno Reactivity of 1,3,5-triaza-7-phosphaadamantane-6-yllithium (PTA-Li) Towards Organotin, Silicon, and Boron Chlorides A thesis submitted in partial fulfillment of the requirements for the degree of Master of Science in Chemistry by June Pinky T. Acay Dr. Brian J. Frost/Thesis Advisor December, 2014 ! Copyright!by!June!Pinky!T.!Acay!2014! All!Rights!Reserved! ! THE GRADUATE SCHOOL We recommend that the thesis prepared under our supervision by JUNE PINKY T. ACAY Entitled Reactivity Of 1,3,5-Triaza-7-Phosphaadamantane-6-Yllithium (PTA-Li) Towards Organotin, Silicon, And Boron Chlorides be accepted in partial fulfillment of the requirements for the degree of MASTER OF SCIENCE Brian J. Frost, Ph.D., Advisor Vincent J. Catalano, Ph.D., Committee Member Michael P. Branch, Ph.D., Graduate School Representative David W. Zeh, Ph.D., Dean, Graduate School December, 2014 i Abstract In this thesis, the synthesis and preliminary characterization of a library of 1,3,5- triaza-7-phosphaadamantane derivatives with Sn, Si, and B moieties are presented. Various electrophiles were reacted with lithiated PTA (PTA-Li) including SnR3Cl, SnR2Cl2, SiR2Cl2 (R=CH3, Ph), and BR2Cl (R=Cy, Ph). The α-stannylated PTA, PTA- SnMe3, was successfully isolated along with the oxide, O=PTA-SnMe3, characterized through solution NMR (31P{1H}, 13C{1H}, 119Sn{1H}, and 1H) and ESI-MS. These water soluble compounds are also soluble in other organic solvents like chloroform, methylene chloride, hexanes, pentane, etc. PTA-SnMe3 has been found to oxidize in solution but is more stable in the solid state. -
Growth of Lithium Hydride Thin Films from Solutions: Towards Solution Atomic Layer Deposition of Lithiated Films
Growth of lithium hydride thin films from solutions: Towards solution atomic layer deposition of lithiated films Ivan Kundrata*1,2,3, Karol Fröhlich1,3, Lubomír Vančo4, Matej Mičušík5 and Julien Bachmann2,6 Full Research Paper Open Access Address: Beilstein J. Nanotechnol. 2019, 10, 1443–1451. 1Institute of Electrical Engineering, SAS, Dúbravská cesta 9, 841 04 doi:10.3762/bjnano.10.142 Bratislava, Slovakia, 2Friedrich-Alexander University of Erlangen-Nürnberg, Dept. Chemie and Pharmacy, Chair ”Chemistry of Received: 14 February 2019 Thin Film Materials”, Cauerstr. 3, 91058 Erlangen, Germany, 3Centre Accepted: 25 June 2019 of Excellence for Advanced Materials Application SAS, Dúbravská Published: 18 July 2019 cesta 5807/9, 841 04, Bratislava, Slovakia, 4STU Centre for Nanodiagnostics, Slovak University of Technology in Bratislava, This article is part of the thematic issue "Chemical thin coating methods Vazovova 5, 812 43 Bratislava, Slovakia, 5Polymer Institute, Slovak for functional nanomaterials". Academy of Sciences, Dúbravská cesta 9, 845 41 Bratislava, Slovakia and 6Saint Petersburg State University, Institute of Associate Editor: J. J. Schneider Chemistry, Universitetskii pr. 26, 198504 St. Petersburg, Russia © 2019 Kundrata et al.; licensee Beilstein-Institut. Email: License and terms: see end of document. Ivan Kundrata* - [email protected] * Corresponding author Keywords: lithiated thin films; lithium hydride; solution atomic layer deposition (sALD) Abstract Lithiated thin films are necessary for the fabrication of novel solid-state batteries, including the electrodes and solid electrolytes. Physical vapour deposition and chemical vapour deposition can be used to deposit lithiated films. However, the issue of confor- mality on non-planar substrates with large surface area makes them impractical for nanobatteries the capacity of which scales with surface area. -
New Materials Grown from Ca/Li Flux David A
Florida State University Libraries Electronic Theses, Treatises and Dissertations The Graduate School 2011 New Materials Grown from Ca/Li Flux David A. Lang Follow this and additional works at the FSU Digital Library. For more information, please contact [email protected] THE FLORIDA STATE UNIVERSITY COLLEGE OF ARTS AND SCIENCES NEW MATERIALS GROWN FROM CA/LI FLUX By DAVID A. LANG A Thesis submitted to the Department of Chemistry and Biochemistry in partial fulfillment of the requirement for the degree of Master of Science Degree Awarded: Summer 2011 The members of the committee approve the thesis of David Lang defended on June 22, 2011. _______________________________________ Susan Latturner Professor Directing Thesis _______________________________________ Albert E. Stiegman Committee Member _______________________________________ Oliver Steinbock Committee Member Approved: _____________________________________ William Cooper, Associate Chair, Department of Chemistry and Biochemistry The Graduate School has verified and approved the above-named committee members. ii TABLE OF CONTENTS List of Tables iv List of Figures v Abstract vi Chapter 1: Introduction to flux synthesis 1 1.1 Metal flux 1 1.2 Alkaline earth/alkali metal fluxes 2 1.3 Expected products of synthesis in Ca/Li flux 5 1.3.1 Zintl phases 5 1.3.2 Intermetallics 6 1.3.3 Hydrogen storage materials 7 1.4 Characterization of products 7 1.4.1 Elemental analysis 8 1.4.2 X-ray diffraction 8 1.4.3 NMR 9 1.4.4 Protolysis, hydriding and dehydriding 10 1.4.5 Band structure calculations 10 Chapter 2: LiCa2C3H 11 2.1 Introduction 11 2.2 Experimental procedure 11 2.3 Results and discussion 15 Chapter 3: LiCa7Si3H3 23 3.1 Introduction 23 3.2 Experimental procedure 23 3.3 Results and discussion 25 3.4 Thermo-volumetric measurements 31 Chapter 4: LiCa7Ge3H3 and LiCa11Ge3OH4 32 4.1 Introduction 32 4.2 Experimental procedure 32 4.3 Results and discussion 35 4.4 Future work 40 Chapter 5: Conclusions and future work 41 5.1 Ca/S/C 41 5.2 Ca/B/C 43 References 45 Biographical sketch 48 iii LIST OF TABLES 2.1. -
Novel Synthesis of Polyhydrogenated Fullerenes
Wright State University CORE Scholar Browse all Theses and Dissertations Theses and Dissertations 2010 Novel Synthesis of Polyhydrogenated Fullerenes Angela Campo Wright State University Follow this and additional works at: https://corescholar.libraries.wright.edu/etd_all Part of the Chemistry Commons Repository Citation Campo, Angela, "Novel Synthesis of Polyhydrogenated Fullerenes" (2010). Browse all Theses and Dissertations. 1023. https://corescholar.libraries.wright.edu/etd_all/1023 This Thesis is brought to you for free and open access by the Theses and Dissertations at CORE Scholar. It has been accepted for inclusion in Browse all Theses and Dissertations by an authorized administrator of CORE Scholar. For more information, please contact [email protected]. NOVEL SYNTHESIS OF POLYHYDROGENATED FULLERENES A thesis submitted in partial fulfillment of the requirements for the degree of Master of Science By ANGELA M. CAMPO B.S. in Chemistry, Wright State University 2001 2010 Wright State University WRIGHT STATE UNIVERSITY SCHOOL OF GRADUATE STUDIES October 21 , 2010 I HEREBY RECOMMEND THAT THE THESIS PREPARED UNDER MY SUPERVISION BY Angela M. Campo ENTITLED Novel Synthesis of polyhydrogenated fullerenes BE ACCEPTED IN PARTIAL FULFILLMENT OF THE REQUIREMENTS FOR THE DEGREE OF Master of Science . ______________________________ Eric Fossum, Ph.D. Thesis Director ______________________________ Kenneth Turnbull, Ph.D. Chair, Chemistry Department Committee on Final Examination College of Science and Mathematics _________________________________ Eric Fossum, Ph.D. _________________________________ Kenneth Turnbull, Ph.D. _________________________________ Daniel Ketcha, Ph.D. _________________________________ Douglas Dudis, Ph.D. _________________________________ Andrew T. Hsu, Ph.D. Dean, School of Graduate Studies ABSTRACT Campo, Angela M. M.S., Department of Chemistry, Wright State University, 2010. -
Arxiv:2007.13784V1 [Physics.App-Ph] 27 Jul 2020 A) Glovebox a in Cleanroom a Orsodn Uhr Lcrncmi:[email protected] Mail: Electronic Author; Corresponding Ao .Gray, J
A Cleanroom in a Glovebox Mason J. Gray,1 Narendra Kumar,1 Ryan O’Connor,1 Marcel Hoek,1 Erin Sheridan,1 Meaghan C. Doyle,1 Marisa L. Romanelli,1 Gavin B. Osterhoudt,1 Yiping Wang,1 Vincent Plisson,1 Shiming Lei,2 Ruidan Zhong,3 Bryan Rachmilowitz,1 He Zhao,1 Hikari Kitadai,4 Steven Shepard,5 Leslie M. Schoop,2 G. D. Gu,3 Ilija Zeljkovic,1 Xi Ling,4, 6, 7 and K.S. Burch1, a) 1)Department of Physics, Boston College, Chestnut Hill, MA. 02467, USA 2)Department of Chemistry, Princeton University, Princeton, NJ. 08544, USA 3)Condensed Matter Physics and Materials Science Department, Brookhaven National Laboratory, Upton, NY. 11973, USA 4)Department of Chemistry, Boston University, Boston, MA. 02215, USA 5)Integrated Sciences Cleanroom Facility, Boston College, Chestnut Hill, MA. 02467, USA 6)Division of Materials Science and Engineering, Boston University, Boston, MA, 02215, USA 7)The Photonics Center, Boston University, Boston, MA. 02215, USA (Dated: 29 July 2020) Keywords: Glovebox, Nanofabrication, 2D Materials arXiv:2007.13784v1 [physics.app-ph] 27 Jul 2020 a)Corresponding author; Electronic mail: [email protected] 1 The exploration of new materials, novel quantum phases, and devices requires ways to prepare cleaner samples with smaller feature sizes. Initially, this meant the use of a clean- room that limits the amount and size of dust particles. However, many materials are highly sensitive to oxygen and water in the air. Furthermore, the ever-increasing demand for a quantum workforce, trained and able to use the equipment for creating and characterizing materials, calls for a dramatic reduction in the cost to create and operate such facilities. -
(12) United States Patent (10) Patent No.: US 8,007,762 B2 Lefenfeld Et Al
USO08007762B2 (12) United States Patent (10) Patent No.: US 8,007,762 B2 Lefenfeld et al. (45) Date of Patent: *Aug. 30, 2011 (54) SILICA GEL COMPOSITIONS CONTAINING (58) Field of Classification Search .................. 423/657; ALKAL METALS AND ALKAL METAL 585/400, 469; 502/233,237, 343, 344, 407, ALLOYS 502/411,439 (75) Inventors: Michael Lefenfeld, New York, NY (US); See application file for complete search history. James L. Dye, East Lansing, MI (US) (56) References Cited (73) Assignees: SiGNa Chemistry, Inc., New York, NY (US); Board of Trustees of Michigan State University, East Lansing, MI (US) us. PATENT DOCUMENTS (*) Notice: Subject to any disclaimer, the term of this 1,665,264 A 48,issass et al. patent is extended or adjusted under 35 U.S.C. 154(b) by 0 days. FOREIGN PATENT DOCUMENTS This patent is subject to a terminal dis- JP O9-141097 6, 1997 claimer. (Continue 3 (21) Appl. No.: 12/723,588 OTHER PUBLICATIONS (22) Filed: Mar 12, 2010 (65) Prior Publication Data K.M. Unruh. T.E. Huber, and C.A. Huber, "Melting and freezing behavior of indium metal in porous glasses.” Physical Review B, Sep. US 2010/0166648 A1 Jul. 1, 2010 15, 1993, pp. 9021-9027, vol. 48, No. 12, The American Physical Related U.S. Application Data Society. (60) Continuation of application No. 12/222,533, filed on (Continued) conunuauon(i. R OI applicauonI R N No. 779:...is 89), Illed on a Primary Examiner — Cam N. Nguyen Mar. 28, 2007, now Pat. No. 7,410,567, which is a Sattorney Agent, or Firm — J.A. -
Fabrication of Two-Dimensional Polymers and Two-Dimensional Materials
Fabrication of Two-Dimensional Polymers and Two-Dimensional Materials Dissertation zur Erlangung des Grades „Doktor der Naturwissenschaften“ am Fachbereich Chemie, Pharmazie und Geowissenschaften der Johannes Gutenberg-Universität Mainz vorgelegt von Martin Gerhard Christian Pfeffermann geboren in Offenbach am Main Mainz, 2016 Dekan: 1. Berichterstatter 2. Berichterstatter Tag der mündlichen Prüfung: II Die vorliegende Arbeit wurde in der Zeit von Mai 2013 bis April 2016 am Max-Planck-Institut für Polymerforschung in Mainz im Arbeitskreis von Prof. Dr. Klaus Müllen angefertigt. D77 III IV Meiner Familie V VI Table of Contents Abbreviations .............................................................................................................. IX 1. Motivation .............................................................................................................. 1 2. Two-Dimensional Supramolecular Polymers ......................................................... 7 2.1. Introduction .................................................................................................... 7 2.1.1. CB[8] complexes ..................................................................................... 8 2.1.2. Metal-Ligand Complexes ....................................................................... 11 2.1.3. Two-Dimensional Supramolecular Polymers ......................................... 11 2.1.4. Analysis of Two-Dimensional Supramolecular Polymers ....................... 13 2.2. Target Objective ..........................................................................................