Dynamic Response Analysis of Composite Tether Structure to Airborne Wind Energy System Under Impulsive Load
Total Page:16
File Type:pdf, Size:1020Kb
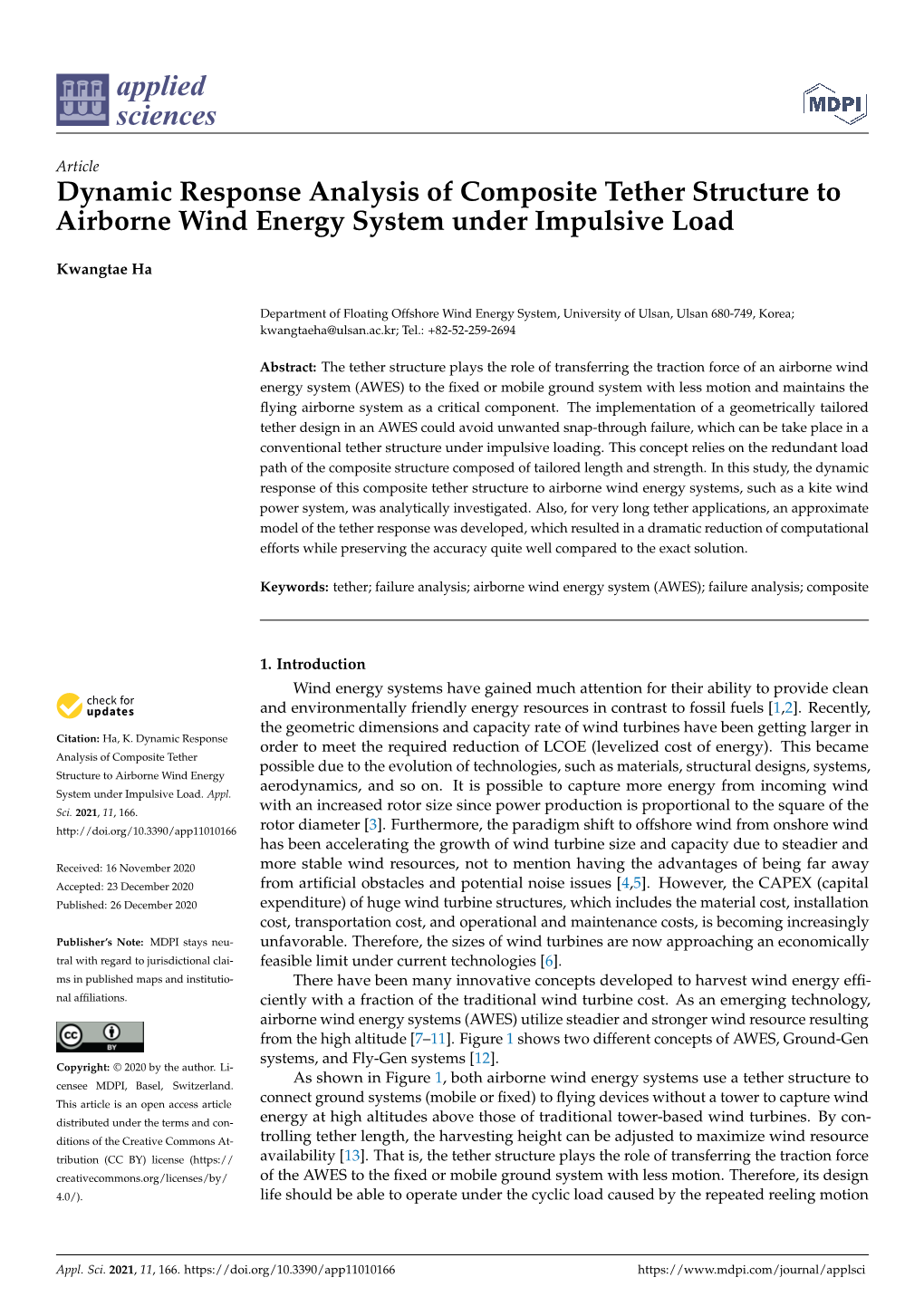
Load more
Recommended publications
-
Design and Access Statement April 2015 FULBECK AIRFIELD WIND FARM DESIGN and ACCESS STATEMENT
Energiekontor UK Ltd Design and Access Statement April 2015 FULBECK AIRFIELD WIND FARM DESIGN AND ACCESS STATEMENT Contents Section Page 1. Introduction 2 2. Site Selection 3 3. Design Influences 7 4. Design Evolution, Amount, Layout and Scale 9 5. Development Description, Appearance and Design 14 6. Access 16 Figures Page 2.1 Site Location 3 2.2 Landscape character areas 4 2.3 1945 RAF Fulbeck site plan 5 2.4 Site selection criteria 6 4.1 First Iteration 10 4.2 Second Iteration 11 4.3 Third Iteration 12 4.4 Fourth Iteration 13 5.1 First Iteration looking SW from the southern edge of Stragglethorpe 14 5.2 Fourth Iteration looking SW from the southern edge of 14 Stragglethorpe 5.3 First Iteration looking east from Sutton Road south of Rectory Lane 15 5.4 Fourth Iteration looking east from Sutton Road south of Rectory Lane 15 6.1 Details of temporary access for turbine deliveries 16 EnergieKontor UK Ltd 1 May 2015 FULBECK AIRFIELD WIND FARM DESIGN AND ACCESS STATEMENT 1 Introduction The Application 1.8 The Fulbeck Airfield Wind Farm planning application is Context 1.6 The Environmental Impact Assessment (EIA) process also submitted in full and in addition to this Design and Access exploits opportunities for positive design, rather than merely Statement is accompanied by the following documents 1.1 This Design and Access Statement has been prepared by seeking to avoid adverse environmental effects. The Design which should be read together: Energiekontor UK Ltd (“EK”) to accompany a planning and Access Statement is seen as having an important role application for the construction, 25 year operation and in contributing to the design process through the clear Environmental Statement Vol 1; subsequent decommissioning of a wind farm consisting of documentation of design evolution. -
Wind Power: Energy of the Future It’S Worth Thinking About
Wind power: energy of the future It’s worth thinking about. »Energy appears to me to be the first and unique virtue of man.« Wilhelm von Humboldt 2 3 »With methods from the past, there will be no future.« Dr. Bodo Wilkens Wind power on the increase »Environmental protection is an opportunity and not a burden we have to carry.« Helmut Sihler When will the oil run out? Even if experts cannot agree on an exact date, one thing is certain: the era of fossil fuels is coming to an end. In the long term we depend on renewable sources of energy. This is an irrefutable fact, which has culminated in a growing ecological awareness in industry as well as in politics: whereas renewable sources of energy accounted for 4.2 percent of the total consumption of electricity in 1996, the year 2006 registered a proportion of 12 per- cent. And by 2020 this is to be pushed up to 30 percent. The growth of recent years has largely been due to the use of wind power. The speed of technical development over the past 15 years has brought a 20-fold rise in efficiency and right now wind power is the most economical regenerat- ive form there is to produce electricity. In this respect, Germany leads the world: since 1991 more than 19.460 wind power plants have been installed with a wind power capacity of 22.247 MW*. And there is more still planned for the future: away from the coastline, the offshore plants out at sea will secure future electricity supplies. -
Assessment of the Effects of Noise and Vibration from Offshore Wind Farms on Marine Wildlife
ASSESSMENT OF THE EFFECTS OF NOISE AND VIBRATION FROM OFFSHORE WIND FARMS ON MARINE WILDLIFE ETSU W/13/00566/REP DTI/Pub URN 01/1341 Contractor University of Liverpool, Centre for Marine and Coastal Studies Environmental Research and Consultancy Prepared by G Vella, I Rushforth, E Mason, A Hough, R England, P Styles, T Holt, P Thorne The work described in this report was carried out under contract as part of the DTI Sustainable Energy Programmes. The views and judgements expressed in this report are those of the contractor and do not necessarily reflect those of the DTI. First published 2001 i © Crown copyright 2001 EXECUTIVE SUMMARY Main objectives of the report Energy Technology Support Unit (ETSU), on behalf of the Department of Trade and Industry (DTI) commissioned the Centre for Marine and Coastal Studies (CMACS) in October 2000, to assess the effect of noise and vibration from offshore wind farms on marine wildlife. The key aims being to review relevant studies, reports and other available information, identify any gaps and uncertainties in the current data and make recommendations, with outline methodologies, to address these gaps. Introduction The UK has 40% of Europe ’s total potential wind resource, with mean annual offshore wind speeds, at a reference of 50m above sea level, of between 7m/s and 9m/s. Research undertaken by the British Wind Energy Association suggests that a ‘very good ’ site for development would have a mean annual wind speed of 8.5m/s. The total practicable long-term energy yield for the UK, taking limiting factors into account, would be approximately 100 TWh/year (DTI, 1999). -
GCEP Energy Tutorial Wind 101 Patrick Riley October 14, 2014
GCEP Energy Tutorial Wind 101 Patrick Riley October 14, 2014 Imagination at work. Agenda • Introduction & fundamentals • Wind resource • Aerodynamics & performance • Design loads & controls • Scaling • Farm Considerations • Technology Differentiators • Economics • Technology Development Areas GCEP Wind 101| 14 October 2014 2 © 2014 General Electric Company – All rights reserved Power from Wind Turbines Power in Wind 1 3 Pwind = 2 r v Area v = wind speed Extractable Power from Wind turbine Importance of site identification (local wind resource) & understanding of wind shear 1 3 Pwind = 2 cp r v Area Area = rotor swept area Power increases with rotor2 Cp = power coefficient a measure of aerodynamic efficiency of extracting energy from the wind GCEP Wind 101| 14 October 2014 3 © 2014 General Electric Company – All rights reserved Configurations Horizontal-Axis (HAWT) Vertical-Axis (VAWT) Upwind vs. Downwind Lift Based (Darrieus) vs. Drag-Based (Savonius) Source: http://en.wikipedia.org/wiki/File:Darrieus-windmill.jpg Source: http://en.wikipedia.org/wiki/File:Savonius-rotor_en.svg Copyright 2007 aarchiba, used with permission. Copyright 2008 Ugo14, used with permission. Source: http://en.wikipedia.org/wiki/File:Wind.turbine.yaw.system.configurations.svg Copyright 2009 Hanuman Wind, used with permission. Number of Blades Airborne Wind Turbine Source: http://en.wikipedia.org/wiki/File:Water_Pumping_ Source: http://en.wikipedia.org/wiki/File:Airborne_wind_generator-en.svg Windmill.jpg Copyright 2008 James Provost, used with permission. Copyright 2008 Ben Franske, used with permission. GCEP Wind 101| 14 October 2014 4 © 2014 General Electric Company – All rights reserved Utility-Scale Turbine Types Convergence of industry Horizontal axis Upwind 3 blades Variable rotor speed Active (independent) pitch Main differentiators Direct drive vs. -
Chapter 1 History
CHAPTER 1 HISTORY 1.0 INTRODUCTION Since early recorded history, people have been harnessing the energy of the wind. Wind energy propelled boats along the Nile River as early as 5000 B.C. By 200 B.C., simple windmills in China were pumping water, while vertical-axis windmills with woven reed sails were grinding grain in Persia and the Middle East. New ways of using the energy of the wind eventually spread around the world. By the 11th century, people in the Middle East were using windmills extensively for food production; returning merchants and crusaders carried this idea back to Europe. The Dutch refined the windmill and adapted it for draining lakes and marshes in the Rhine River Delta. When settlers took this technology to the New World in the late 19th century, they began using windmills to pump water for farms and ranches, and later, to generate electricity for homes and industry. Industrialization, first in Europe and later in America, led to a gradual decline in the use of windmills. The steam engine replaced European water-pumping windmills. In the 1930s, the Rural Electrification Administration's programs brought inexpensive electric power to most rural areas in the United States. However, industrialization also sparked the development of larger windmills to generate electricity. Commonly called wind turbines, these machines appeared in Denmark as early as 1890. In the 1940s the largest wind turbine of the time began operating on a Vermont hilltop known as Grandpa's Knob. This turbine, rated at 1.25 megawatts in winds of about 30 mph, fed electric power to the local utility network for several months during World War II. -
Design of a Kite-Powered Water Pump and Airborne Wind Turbine Andrew Ross Lybarger Worcester Polytechnic Institute
Worcester Polytechnic Institute Digital WPI Major Qualifying Projects (All Years) Major Qualifying Projects April 2012 Design of a Kite-Powered Water Pump and Airborne Wind Turbine Andrew Ross Lybarger Worcester Polytechnic Institute Daniel Joseph Nyren Worcester Polytechnic Institute Jennifer M. Gill Worcester Polytechnic Institute John William Wilder Worcester Polytechnic Institute Kyle Steven Bartosik Worcester Polytechnic Institute Follow this and additional works at: https://digitalcommons.wpi.edu/mqp-all Repository Citation Lybarger, A. R., Nyren, D. J., Gill, J. M., Wilder, J. W., & Bartosik, K. S. (2012). Design of a Kite-Powered Water Pump and Airborne Wind Turbine. Retrieved from https://digitalcommons.wpi.edu/mqp-all/2406 This Unrestricted is brought to you for free and open access by the Major Qualifying Projects at Digital WPI. It has been accepted for inclusion in Major Qualifying Projects (All Years) by an authorized administrator of Digital WPI. For more information, please contact [email protected]. Abstract The goal of this project was two-fold, to adapt the existing WPI Kite Power System to pump water, and to develop a new airborne energy system that harvests electricity from the wind using a turbine suspended from a large kite. This project is a continuation of ongoing research at Worcester Polytechnic Institute in the area of using high altitude kites to extract energy from the wind. These high altitude kites can operate at higher altitudes than wind turbines where there is an increase in wind speed and therefore, available power. The main objectives of the water pump project were to retrofit the existing WPI Kite Power System with a low-cost mechanical water pump for use in developing nations, and to build and test a head simulation valve that can simulate deeper well depths for use in system testing. -
Electric Earth Index
ELECTRIC EARTH INDEX Crystal Equity Research, LLC January 2019 ELECTRIC EARTH INDEX The Earth is dynamic with great forces of energy all around us. As the sun heats the at- mosphere, wind whips across open landscapes. The ocean is under constant wave and tidal movement, sometimes calmly undulating and then furiously churning. Rainfall and melted snow makes the inevitably downhill race to the oceans, only to evaporate and re- peat the same journey. Our great cities and spreading farms lie innocently above a tem- pest of molten rock. The Electric Earth Index includes the companies that are attempting to capture earth’s energy in mechanical designs from wind mills, to wave machines, to solar concentrators. Many investors will miss the solar cell producers. We have included photovoltaic solar cell developers in The Atomics Index, where they fit well with other companies harness- ing the power of the atom. Front Cover Image: “Guatemala Volcano” from CBC GEOTHERMAL GROUP PUBLIC/ COMPANY Country PRIVATE OPERATIONS WEB SITE Altarock Energy, Inc. US Private Geothermal power production http://altarockenergy.com/ Alterra Power (Innergex) Canada INE.TO Geothermal power generation http://www.alterrapower.ca/ Calpine Corp. US Private Geothermal power generation http://www.calpine.com/ Energy Development Corp. Philippines Private Geothermal power generation http://www.energy.com.ph/ Landvirkjun hf Iceland Private Geothermal power generation http://www.landsvirkjun.com/ Melink Corporation US Private Geothermal for HVAC https://melinkcorp.com/ Nether- Mijnwater BV Private Geothermal solutions, mine reclamation http://www.mijnwater.com/ lands Ormat Technologies, Inc. US ORA Geothermal power, recovered energy http://www.ormat.com/ Polaris Infrastructure US PIF.TO Geothermal power generation https://polarisinfrastructure.com/ WaterFurnace International US WFI.TO Residential heating solution http://www.waterfurnace.com/ Stock symbols when provided are assumed to be U.S. -
2013 Annual Report
Town of Brighton MONROE COUNTY, NEW YORK SUSTAINABILITY OVERSIGHT COMMITTEE, SOC 2300 ELMWOOD AVE. * ROCHESTER, NEW YORK 14618 * PHONE (585) 784-5250 *FAX (585) 784-5368 Sustainability Oversight Committee 2013 Year-End Report The Sustainability Oversight Committee (SOC) Policy states, “The Committee shall prepare and submit an annual written report to the Town Board for review during April of each year concerning the activities and work of the Committee. The following document constitutes this annual report which describes the activities undertaken by the committee and the actions that resulted from these activities. 1. Monthly Meetings The SOC met monthly excluding the months of August and December in 2013. A copy of the minutes for each meeting is attached as part of this Year End Report. 2. 2013 Initiatives In January of 2013 the SOC drafted five initiatives to pursue during 2013. The initiatives were defined broadly, so that there is potential for a range of tasks within these areas of interest. A description of the Initiatives and the SOC’s action to date toward pursuing these initiatives are listed below: a. Sustainable Community Rating System Description: Utilize the STAR Community Rating system framework to evaluate the Town's progress against standardized sustainability objectives and evaluation measures and facilitate the Town's future participation in the STAR program. Action to date: The Sustainability Oversight Committee explored the use of the STAR Community Rating System (STAR) to chart a clear path to meaningful action in the Town’s work and to help the Town of Brighton quantify its livability and sustainability achievements. -
State of the Art in the Optimisation of Wind Turbine Performance Using CFD Shourangiz-Haghighi, A., Haghnegahdar, M
State of the Art in the Optimisation of Wind Turbine Performance Using CFD Shourangiz-Haghighi, A., Haghnegahdar, M. A., Wang, L., Mussetta, M., Kolios, A. & Lander, M. Author post-print (accepted) deposited by Coventry University’s Repository Original citation & hyperlink: Shourangiz-Haghighi, A, Haghnegahdar, MA, Wang, L, Mussetta, M, Kolios, A & Lander, M 2019, 'State of the Art in the Optimisation of Wind Turbine Performance Using CFD', Archives of Computational Methods in Engineering, vol. (In-Press), pp. (In-Press). https://dx.doi.org/10.1007/s11831-019-09316-0 DOI 10.1007/s11831-019-09316-0 ISSN 1134-3060 ESSN 1886-1784 Publisher: Springer The final publication is available at Springer via http://dx.doi.org/s11831-019- 09316-0 Copyright © and Moral Rights are retained by the author(s) and/ or other copyright owners. A copy can be downloaded for personal non-commercial research or study, without prior permission or charge. This item cannot be reproduced or quoted extensively from without first obtaining permission in writing from the copyright holder(s). The content must not be changed in any way or sold commercially in any format or medium without the formal permission of the copyright holders. This document is the author’s post-print version, incorporating any revisions agreed during the peer-review process. Some differences between the published version and this version may remain and you are advised to consult the published version if you wish to cite from it. Archives of Computational Methods in Engineering State of the art in the optimisation of wind turbine performance using CFD --Manuscript Draft-- Manuscript Number: ARCO-D-18-00267 Full Title: State of the art in the optimisation of wind turbine performance using CFD Article Type: Original Paper Funding Information: Abstract: Wind energy has received increasing attention in recent years due to its sustainability and geographically wide availability. -
Current and Expected Airspace Regulations for Airborne Wind Energy Systems
Chapter 29 Current and Expected Airspace Regulations for Airborne Wind Energy Systems Volkan Salma, Richard Ruiterkamp, Michiel Kruijff, M. M. (René) van Paassen and Roland Schmehl Abstract Safety is a major factor in the permitting process for airborne wind en- ergy systems. To successfully commercialize the technologies, safety and reliability have to be ensured by the design methodology and have to meet accepted standards. Current prototypes operate with special temporary permits, usually issued by local aviation authorities and based on ad-hoc assessments of safety. Neither at national nor at international level there is yet a common view on regulation. In this chapter, we investigate the role of airborne wind energy systems in the airspace and pos- sible aviation-related risks. Within this scope, current operation permit details for several prototypes are presented. Even though these prototypes operate with local permits, the commercial end-products are expected to fully comply with interna- tional airspace regulations. We share the insights obtained by Ampyx Power as one of the early movers in this area. Current and expected international airspace regula- tions are reviewed that can be used to find a starting point to evidence the safety of airborne wind energy systems. In our view, certification is not an unnecessary bur- den but provides both a prudent and a necessary approach to large-scale commercial deployment near populated areas. 29.1 Introduction Due to the emerging interest in airborne wind energy (AWE), a considerable number of prototype installations is approaching the stage of commercial development. As Volkan Salma Richard Ruiterkamp Michiel Kruijff Ampyx Power· B.V., Lulofsstraat 55 Unit· 13, 2521 AL The Hague, The Netherlands Volkan Salma (B) M. -
Optimum Sizing of Stand-Alone Hybrid Pv/Wind Systems
TECHNOLOGICAL EDUCATIONAL INSTITUTE OF WESTERN GREECE DEPARTMENT OF MECHANICAL ENGINEERING MASTER COURSE OF “RENEWABLE ENERGY SYSTEMS” THESIS OPTIMUM SIZING OF STAND-ALONE HYBRID PV/WIND SYSTEMS MSc STUDENT: PAPPAS KONSTANTINOS SUPERVISOR: KAPLANIS SOCRATES PROFESSOR PATRA 2016 PROLOGUE The present issue is the thesis conducted at the MSc course of "Renewable Energy Systems" of the Dpt of the Mechanical Engineering at the Technological Educational Institute of Western Greece. The subject deals with the simulation of a hybrid energy system constituted of photovoltaic, wind turbine and batteries as a storage bank of the produced energy and targets to the most cost-effective configuration. The increasing use of hybrid power systems based on renewable energy, as an alternative to conventional fuels, provide in many cases reliable and economic solutions, especially in isolated areas without access to the national electricity distribution network. RES are also preferred due to the fact that their carbon footprint is considerably low or zero. An analytic dynamic iterative algorithm is developed in this work for the calculation of the hybrid system from renewable energy at which hourly meteorological data, load demand profile and technical data of the components of the system are imported. Technical power criteria are used for the evaluation of the reliability of the system and the most cost effective solution is provided. I am extremely grateful to my primarily supervisor Dr. Eleni Kaplanis for her valuable advices and our wonderful cooperation, and thereafter to my supervisor professor Socrates Kaplanis, for his valuable assistance, guidance and patience he has shown during all this period. Pappas Konstantinos July 2016 Statutory Student Declaration: The undersigned student I am aware of the consequences of the Law on plagiarism and certify that I am the author of this thesis, I have mentioned in my bibliography all the sources they have used and received ideas or data. -
Social Acceptance, Environmental Impact and Politics
Concerted Action on Offshore Wind Energy in Europe NNE5-1999-00562 Social Acceptance, Environmental Impact and Politics Table of contents 1 Introduction...................................................................................................................................... 2 2 Environmental Impact. ..................................................................................................................... 3 2.1 Environmental Impact Assessment............................................................................................ 3 2.2 Biological impacts. ................................................................................................................... 4 2.2.1 Birds ................................................................................................................................. 5 2.2.2 Sea mammals .................................................................................................................. 10 2.2.3 Fish................................................................................................................................. 11 2.2.4 Seabed and benthos ......................................................................................................... 12 2.2.5 Hydrography, sea currents and water quality ................................................................... 13 2.3 Effects from accidents............................................................................................................. 13 2.4 Visual effect. .........................................................................................................................