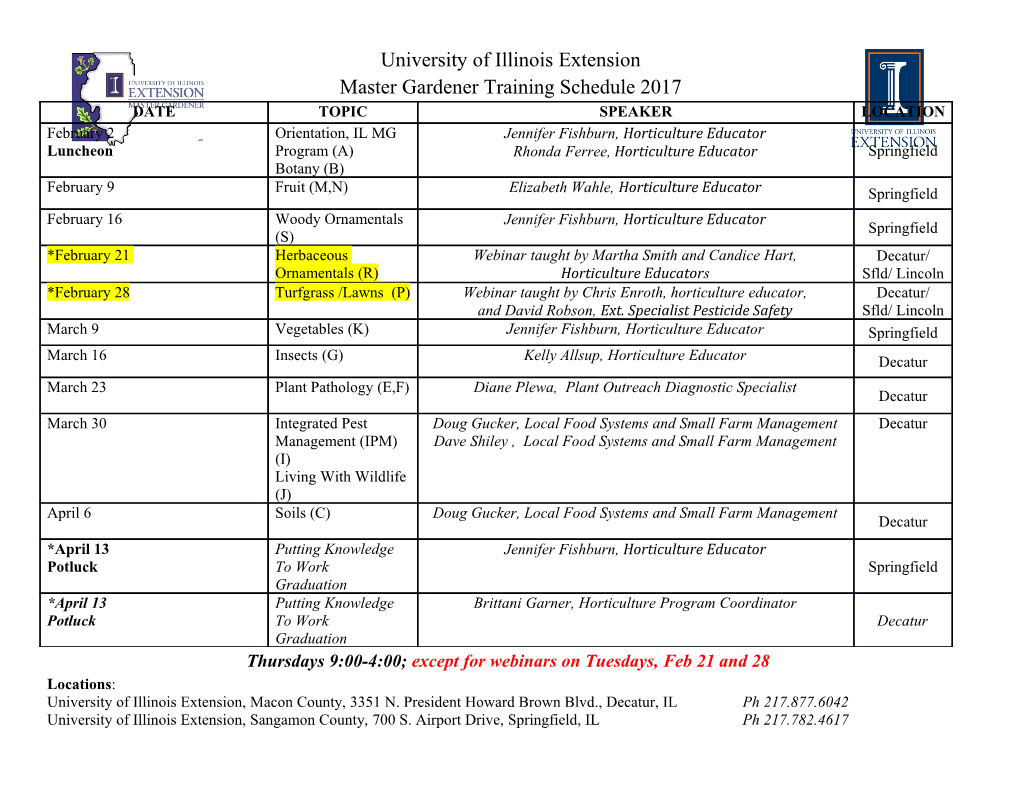
applied sciences Article Dynamic Response Analysis of Composite Tether Structure to Airborne Wind Energy System under Impulsive Load Kwangtae Ha Department of Floating Offshore Wind Energy System, University of Ulsan, Ulsan 680-749, Korea; [email protected]; Tel.: +82-52-259-2694 Abstract: The tether structure plays the role of transferring the traction force of an airborne wind energy system (AWES) to the fixed or mobile ground system with less motion and maintains the flying airborne system as a critical component. The implementation of a geometrically tailored tether design in an AWES could avoid unwanted snap-through failure, which can be take place in a conventional tether structure under impulsive loading. This concept relies on the redundant load path of the composite structure composed of tailored length and strength. In this study, the dynamic response of this composite tether structure to airborne wind energy systems, such as a kite wind power system, was analytically investigated. Also, for very long tether applications, an approximate model of the tether response was developed, which resulted in a dramatic reduction of computational efforts while preserving the accuracy quite well compared to the exact solution. Keywords: tether; failure analysis; airborne wind energy system (AWES); failure analysis; composite 1. Introduction Wind energy systems have gained much attention for their ability to provide clean and environmentally friendly energy resources in contrast to fossil fuels [1,2]. Recently, the geometric dimensions and capacity rate of wind turbines have been getting larger in Citation: Ha, K. Dynamic Response order to meet the required reduction of LCOE (levelized cost of energy). This became Analysis of Composite Tether possible due to the evolution of technologies, such as materials, structural designs, systems, Structure to Airborne Wind Energy aerodynamics, and so on. It is possible to capture more energy from incoming wind System under Impulsive Load. Appl. Sci. 2021, 11, 166. with an increased rotor size since power production is proportional to the square of the http://doi.org/10.3390/app11010166 rotor diameter [3]. Furthermore, the paradigm shift to offshore wind from onshore wind has been accelerating the growth of wind turbine size and capacity due to steadier and Received: 16 November 2020 more stable wind resources, not to mention having the advantages of being far away Accepted: 23 December 2020 from artificial obstacles and potential noise issues [4,5]. However, the CAPEX (capital Published: 26 December 2020 expenditure) of huge wind turbine structures, which includes the material cost, installation cost, transportation cost, and operational and maintenance costs, is becoming increasingly Publisher’s Note: MDPI stays neu- unfavorable. Therefore, the sizes of wind turbines are now approaching an economically tral with regard to jurisdictional clai- feasible limit under current technologies [6]. ms in published maps and institutio- There have been many innovative concepts developed to harvest wind energy effi- nal affiliations. ciently with a fraction of the traditional wind turbine cost. As an emerging technology, airborne wind energy systems (AWES) utilize steadier and stronger wind resource resulting from the high altitude [7–11]. Figure1 shows two different concepts of AWES, Ground-Gen systems, and Fly-Gen systems [12]. Copyright: © 2020 by the author. Li- censee MDPI, Basel, Switzerland. As shown in Figure1, both airborne wind energy systems use a tether structure to This article is an open access article connect ground systems (mobile or fixed) to flying devices without a tower to capture wind distributed under the terms and con- energy at high altitudes above those of traditional tower-based wind turbines. By con- ditions of the Creative Commons At- trolling tether length, the harvesting height can be adjusted to maximize wind resource tribution (CC BY) license (https:// availability [13]. That is, the tether structure plays the role of transferring the traction force creativecommons.org/licenses/by/ of the AWES to the fixed or mobile ground system with less motion. Therefore, its design 4.0/). life should be able to operate under the cyclic load caused by the repeated reeling motion Appl. Sci. 2021, 11, 166. https://doi.org/10.3390/app11010166 https://www.mdpi.com/journal/applsci Appl. Sci. 2021, 11, x FOR PEER REVIEW 2 of 12 controlling tether length, the harvesting height can be adjusted to maximize wind re- source availability [13]. That is, the tether structure plays the role of transferring the trac- tion force of the AWES to the fixed or mobile ground system with less motion. Therefore, Appl. Sci. 2021, 11, 166 its design life should be able to operate under the cyclic load caused by the repeated2 ofreel- 12 ing motion and to endure the specific breaking strength limit entailed by a certain form of snap loading caused by unexpected impulsive forces [14]. Since the tether is an extremely andcritical to endure component, the specific it should breaking be designed strength limitaccording entailed to bya fail-safe a certain rule form [15]. of snap To avoid loading the causedaccidental by unexpected failure of the impulsive tether under forces [unexpected14]. Since the snap tether loading, is an extremely the tether critical should compo- be de- nent,signed it should to increase be designed the capacity according of energy to a fail-safedissipation rule [15]. To avoid the accidental failure of the tether under unexpected snap loading, the tether should be designed to increase the capacity of energy dissipation. (a) Ground-Gen system (b) Fly-Gen system FigureFigure 1. 1.Examples Examples of of airborne airborne wind wind energy energy systems systems (AWES) (AWES) [12 [12].]. InIn this this paper, paper, the the AWES AWES is simply is simply modeled mode asled a two-pointas a two-point mass structuremass structure with a tetherwith a connection,tether connection, where thewhere small the masssmall representsmass represents a flying a flying airborne airborne system system such such as a as kite a kite or flyingor flying aircraft, aircraft, and and the the other other big big mass mass corresponds corresponds to to a grounda ground station station with with little little move- move- ment.ment. The The benefit benefit of of this this tailoring tailoring concept, concept, applicable applicable to to the the airborne airborne wind wind turbine turbine system system underunder impulsive impulsive tensile tensile loading, loading, was was analytically analytically investigatedinvestigated inin aa previousprevious studystudy [16[16].]. Often,Often, there there are are cases cases in in which which the the tether tether length length can can increase increase to to up up to to 1000 1000 m m to to access access windwind resources resources at at extremely extremely high high altitudes altitudes above above 500 500 m. m. In In this this work, work, an an approximate approximate techniquetechnique for for such such a a long long tether tether was was developed developed in in order order to to reduce reduce the the computational computational costs costs dramaticallydramatically whilewhile providingproviding goodgood accuracy,accuracy, even even when when compared compared to to the the original original full full modeling.modeling. TheThe approximated tether tether modeling modeling de developedveloped in in this this paper paper could could be applicable be appli- cableto the to mooring the mooring systems systems of floating of floating wind windturbine turbine systems. systems. The efficient The efficient and light and design light designwill bepossible will bepossible by applying by applying optimization optimization techniques techniques such as suchgenetic as geneticalgorithms algorithms or gradi- orent-based gradient-based optimization optimization to maximize to maximize the energy the energy capacity capacity or to find or to the find advanced the advanced tether tethergeometry geometry [17–21] [17 –21]. 2.2. Concept Concept of of a a Tailored Tailored Tether Tether TheThe original original concept concept of of the the tether tether to to be be used used for for AWES AWES application application was was addressed addressed in in detail in [16,22], where a one-dimensional flexible composite was proposed. The tether detail in [16,22], where a one-dimensional flexible composite was proposed. The tether structure consisted of a matrix and high-strength fibers and was designedwith supplemen- structure consisted of a matrix and high-strength fibers and was designedwith supple- tary and additional load paths in case of sequential failures. Figure2a shows the schematic Appl. Sci. 2021, 11, x FOR PEER REVIEW mentary and additional load paths in case of sequential failures. Figure3 of 12 2a shows the sche- concept modeled in drawing software and Figure2b shows the physically manufactured matic concept modeled in drawing software and Figure 2b shows the physically manu- demonstration of the tether made of the elastomer matrix and high-strength glass fiber. factured demonstration of the tether made of the elastomer matrix and high-strength glass fiber. x3 x2 O (a) (b) FigureFigure 2. 2. AA schematic schematic concept concept of of a a tether tether structure structure ( (aa)) and and its its physically physically manufactured manufactured example example (b). (b). A tailored structural member was conceptually designed to generate a yield-type re- sponse with applicability to the arrest of a moving body. The structural member com- prised a primary load path, called the primary element, connected in parallel to a longer secondary load path, called the secondary element, at a pair of common nodes. Both pri- mary and secondary elements were combined to form the connector element, which had the sum of the cross-sectional areas of both elements. When external loads were applied to the system in the longitudinal direction, the main elements and connectors were sub- jected to the tension loads. If all the main elements had the same geometric and material distributions, the failure probabilities of the main elements were the same.
Details
-
File Typepdf
-
Upload Time-
-
Content LanguagesEnglish
-
Upload UserAnonymous/Not logged-in
-
File Pages12 Page
-
File Size-