Laser Processing of Hard and Ultra-Hard Materials for Micro-Machining and Surface Engineering Applications
Total Page:16
File Type:pdf, Size:1020Kb
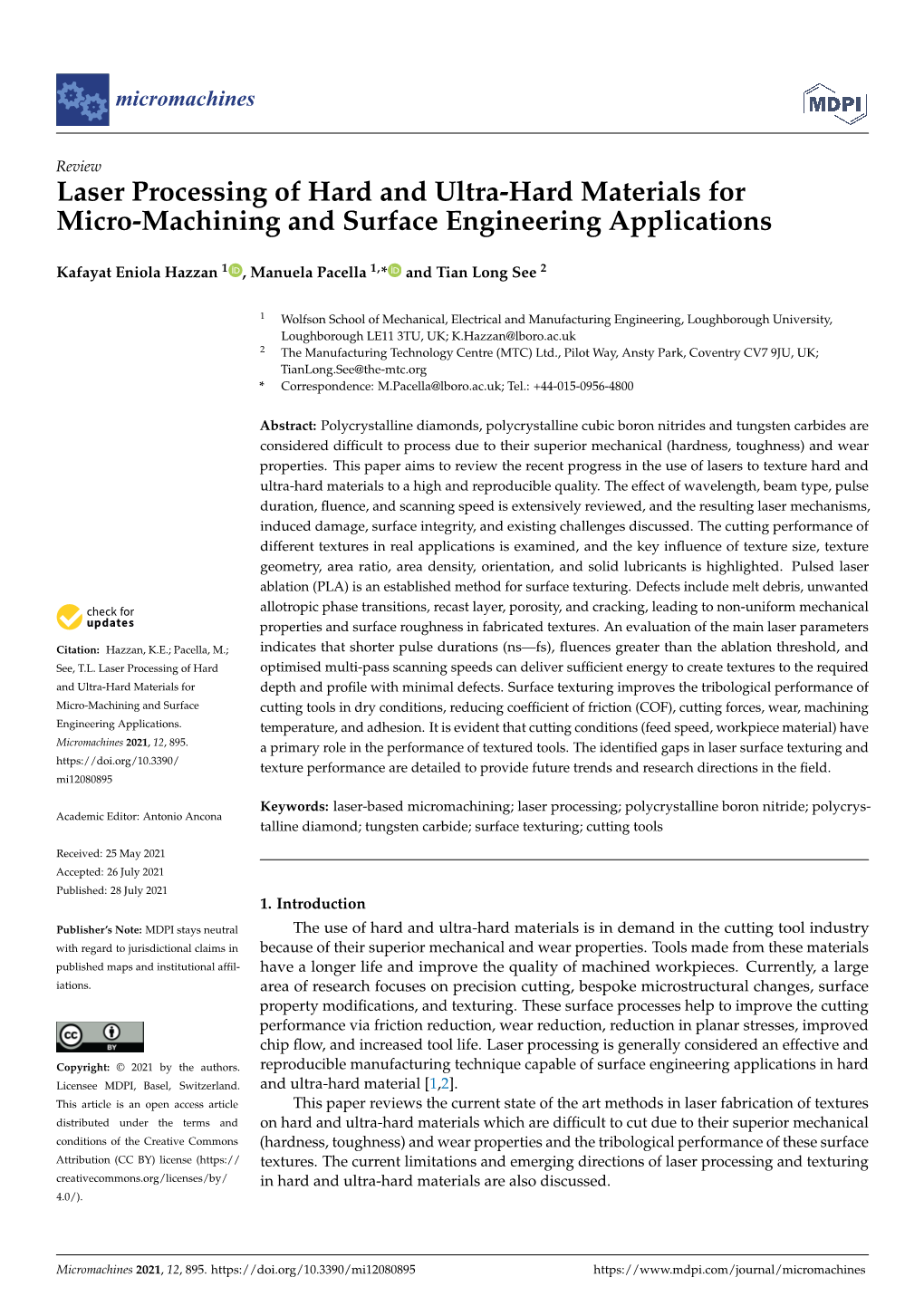
Load more
Recommended publications
-
The Evolution of a Heterogeneous Martian Mantle: Clues from K, P, Ti, Cr, and Ni Variations in Gusev Basalts and Shergottite Meteorites
Earth and Planetary Science Letters 296 (2010) 67–77 Contents lists available at ScienceDirect Earth and Planetary Science Letters journal homepage: www.elsevier.com/locate/epsl The evolution of a heterogeneous Martian mantle: Clues from K, P, Ti, Cr, and Ni variations in Gusev basalts and shergottite meteorites Mariek E. Schmidt a,⁎, Timothy J. McCoy b a Dept. of Earth Sciences, Brock University, St. Catharines, ON, Canada L2S 3A1 b Dept. of Mineral Sciences, National Museum of Natural History, Smithsonian Institution, Washington, DC 20560-0119, USA article info abstract Article history: Martian basalts represent samples of the interior of the planet, and their composition reflects their source at Received 10 December 2009 the time of extraction as well as later igneous processes that affected them. To better understand the Received in revised form 16 April 2010 composition and evolution of Mars, we compare whole rock compositions of basaltic shergottitic meteorites Accepted 21 April 2010 and basaltic lavas examined by the Spirit Mars Exploration Rover in Gusev Crater. Concentrations range from Available online 2 June 2010 K-poor (as low as 0.02 wt.% K2O) in the shergottites to K-rich (up to 1.2 wt.% K2O) in basalts from the Editor: R.W. Carlson Columbia Hills (CH) of Gusev Crater; the Adirondack basalts from the Gusev Plains have more intermediate concentrations of K2O (0.16 wt.% to below detection limit). The compositional dataset for the Gusev basalts is Keywords: more limited than for the shergottites, but it includes the minor elements K, P, Ti, Cr, and Ni, whose behavior Mars igneous processes during mantle melting varies from very incompatible (prefers melt) to very compatible (remains in the shergottites residuum). -
Analogue Sites for Mars Missions: MSL and Beyond
Program and Abstract Volume LPI Contribution No. 1612 Analogue Sites for Mars Missions: MSL and Beyond March 5–6, 2011 • The Woodlands, Texas Sponsors National Aeronautics and Space Administration Lunar and Planetary Institute Conveners Mary Voytek, NASA Headquarters Michael Meyer, NASA Headquarters Victoria Hipkin, Canadian Space Agency Richard Leveille, Canadian Space Agency Shawn Domagal-Goldman, NASA Headquarters Lunar and Planetary Institute 3600 Bay Area Boulevard Houston TX 77058-1113 LPI Contribution No. 1612 Compiled in 2011 by Meeting and Publication Services Lunar and Planetary Institute USRA Houston 3600 Bay Area Boulevard, Houston TX 77058-1113 The Lunar and Planetary Institute is operated by the Universities Space Research Association under a cooperative agreement with the Science Mission Directorate of the National Aeronautics and Space Administration. Any opinions, findings, and conclusions or recommendations expressed in this volume are those of the author(s) and do not necessarily reflect the views of the National Aeronautics and Space Administration. Material in this volume may be copied without restraint for library, abstract service, education, or personal research purposes; however, republication of any paper or portion thereof requires the written permission of the authors as well as the appropriate acknowledgment of this publication. Abstracts in this volume may be cited as Author A. B. (2011) Title of abstract. In Analogue Sites for Mars Missions: MSL and Beyond, p. XX. LPI Contribution No. 1612, Lunar and Planetary Institute, Houston. ISSN No. 0161-5297 Preface This volume contains abstracts that have been accepted for presentation at the workshop on Analogue Sites for Mars Missions: MSL and Beyond, March 5–6, 2011, The Woodlands, Texas. -
General Vertical Files Anderson Reading Room Center for Southwest Research Zimmerman Library
“A” – biographical Abiquiu, NM GUIDE TO THE GENERAL VERTICAL FILES ANDERSON READING ROOM CENTER FOR SOUTHWEST RESEARCH ZIMMERMAN LIBRARY (See UNM Archives Vertical Files http://rmoa.unm.edu/docviewer.php?docId=nmuunmverticalfiles.xml) FOLDER HEADINGS “A” – biographical Alpha folders contain clippings about various misc. individuals, artists, writers, etc, whose names begin with “A.” Alpha folders exist for most letters of the alphabet. Abbey, Edward – author Abeita, Jim – artist – Navajo Abell, Bertha M. – first Anglo born near Albuquerque Abeyta / Abeita – biographical information of people with this surname Abeyta, Tony – painter - Navajo Abiquiu, NM – General – Catholic – Christ in the Desert Monastery – Dam and Reservoir Abo Pass - history. See also Salinas National Monument Abousleman – biographical information of people with this surname Afghanistan War – NM – See also Iraq War Abousleman – biographical information of people with this surname Abrams, Jonathan – art collector Abreu, Margaret Silva – author: Hispanic, folklore, foods Abruzzo, Ben – balloonist. See also Ballooning, Albuquerque Balloon Fiesta Acequias – ditches (canoas, ground wáter, surface wáter, puming, water rights (See also Land Grants; Rio Grande Valley; Water; and Santa Fe - Acequia Madre) Acequias – Albuquerque, map 2005-2006 – ditch system in city Acequias – Colorado (San Luis) Ackerman, Mae N. – Masonic leader Acoma Pueblo - Sky City. See also Indian gaming. See also Pueblos – General; and Onate, Juan de Acuff, Mark – newspaper editor – NM Independent and -
Glossary Glossary
Glossary Glossary Albedo A measure of an object’s reflectivity. A pure white reflecting surface has an albedo of 1.0 (100%). A pitch-black, nonreflecting surface has an albedo of 0.0. The Moon is a fairly dark object with a combined albedo of 0.07 (reflecting 7% of the sunlight that falls upon it). The albedo range of the lunar maria is between 0.05 and 0.08. The brighter highlands have an albedo range from 0.09 to 0.15. Anorthosite Rocks rich in the mineral feldspar, making up much of the Moon’s bright highland regions. Aperture The diameter of a telescope’s objective lens or primary mirror. Apogee The point in the Moon’s orbit where it is furthest from the Earth. At apogee, the Moon can reach a maximum distance of 406,700 km from the Earth. Apollo The manned lunar program of the United States. Between July 1969 and December 1972, six Apollo missions landed on the Moon, allowing a total of 12 astronauts to explore its surface. Asteroid A minor planet. A large solid body of rock in orbit around the Sun. Banded crater A crater that displays dusky linear tracts on its inner walls and/or floor. 250 Basalt A dark, fine-grained volcanic rock, low in silicon, with a low viscosity. Basaltic material fills many of the Moon’s major basins, especially on the near side. Glossary Basin A very large circular impact structure (usually comprising multiple concentric rings) that usually displays some degree of flooding with lava. The largest and most conspicuous lava- flooded basins on the Moon are found on the near side, and most are filled to their outer edges with mare basalts. -
4.1 Potential Facilities List FY 17-18
FY 2017-2018 Annual Report Permittee Name: City of San José Appendix 4.1 FAC # SIC Code Facility Name St Num Dir St Name St Type St Sub Type St Sub Num 820 7513 Ryder Truck Rental A 2481 O'Toole Ave 825 3471 Du All Anodizing Company A 730 Chestnut St 831 2835 BD Biosciences A 2350 Qume Dr 840 4111 Santa Clara Valley Transportation Authority Chaboya Division A 2240 S 7th St 841 5093 Santa Clara Valley Transportation Authority - Cerone Division A 3990 Zanker Rd 849 5531 B & A Friction Materials, Inc. A 1164 Old Bayshore Hwy 853 3674 Universal Semiconductor A 1925 Zanker Rd 871 5511 Mercedes- Benz of Stevens Creek A 4500 Stevens Creek Blvd 877 7542 A.J. Auto Detailing, Inc. A 702 Coleman Ave 912 2038 Eggo Company A 475 Eggo Way 914 3672 Sanmina Corp Plant I A 2101 O'Toole Ave 924 2084 J. Lohr Winery A 1000 Lenzen Ave 926 3471 Applied Anodize, Inc. A 622 Charcot Ave Suite 933 3471 University Plating A 650 University Ave 945 3679 M-Pulse Microwave, Inc. A 576 Charcot Ave 959 3672 Sanmina Corp Plant II A 2068 Bering Dr 972 7549 San Jose Auto Steam Cleaning A 32 Stockton Ave 977 2819 Hill Bros. Chemical Co. A 410 Charcot Ave 991 3471 Quality Plating, Inc. A 1680 Almaden Expy Suite 1029 4231 Specialty Truck Parts Inc. A 1605 Industrial Ave 1044 2082 Gordon Biersch Brewing Company, Inc. A 357 E Taylor St 1065 2013 Mohawk Packing, Div. of John Morrell A 1660 Old Bayshore Hwy 1067 5093 GreenWaste Recovery, Inc. -
Martian Crater Morphology
ANALYSIS OF THE DEPTH-DIAMETER RELATIONSHIP OF MARTIAN CRATERS A Capstone Experience Thesis Presented by Jared Howenstine Completion Date: May 2006 Approved By: Professor M. Darby Dyar, Astronomy Professor Christopher Condit, Geology Professor Judith Young, Astronomy Abstract Title: Analysis of the Depth-Diameter Relationship of Martian Craters Author: Jared Howenstine, Astronomy Approved By: Judith Young, Astronomy Approved By: M. Darby Dyar, Astronomy Approved By: Christopher Condit, Geology CE Type: Departmental Honors Project Using a gridded version of maritan topography with the computer program Gridview, this project studied the depth-diameter relationship of martian impact craters. The work encompasses 361 profiles of impacts with diameters larger than 15 kilometers and is a continuation of work that was started at the Lunar and Planetary Institute in Houston, Texas under the guidance of Dr. Walter S. Keifer. Using the most ‘pristine,’ or deepest craters in the data a depth-diameter relationship was determined: d = 0.610D 0.327 , where d is the depth of the crater and D is the diameter of the crater, both in kilometers. This relationship can then be used to estimate the theoretical depth of any impact radius, and therefore can be used to estimate the pristine shape of the crater. With a depth-diameter ratio for a particular crater, the measured depth can then be compared to this theoretical value and an estimate of the amount of material within the crater, or fill, can then be calculated. The data includes 140 named impact craters, 3 basins, and 218 other impacts. The named data encompasses all named impact structures of greater than 100 kilometers in diameter. -
Program and Abstracts of 2017 Congress / Programme Et Résumés
1 Sponsors | Commanditaires Gold Sponsors | Commanditaires d’or Silver Sponsors | Commanditaires d’argent Other Sponsors | Les autres Commanditaires 2 Contents Sponsors | Commanditaires .......................................................................................................................... 2 Welcome from the Premier of Ontario .......................................................................................................... 5 Bienvenue du premier ministre de l'Ontario .................................................................................................. 6 Welcome from the Mayor of Toronto ............................................................................................................ 7 Mot de bienvenue du maire de Toronto ........................................................................................................ 8 Welcome from the Minister of Fisheries, Oceans and the Canadian Coast Guard ...................................... 9 Mot de bienvenue de ministre des Pêches, des Océans et de la Garde côtière canadienne .................... 10 Welcome from the Minister of Environment and Climate Change .............................................................. 11 Mot de bienvenue du Ministre d’Environnement et Changement climatique Canada ................................ 12 Welcome from the President of the Canadian Meteorological and Oceanographic Society ...................... 13 Mot de bienvenue du président de la Société canadienne de météorologie et d’océanographie ............. -
Special Catalogue Milestones of Lunar Mapping and Photography Four Centuries of Selenography on the Occasion of the 50Th Anniversary of Apollo 11 Moon Landing
Special Catalogue Milestones of Lunar Mapping and Photography Four Centuries of Selenography On the occasion of the 50th anniversary of Apollo 11 moon landing Please note: A specific item in this catalogue may be sold or is on hold if the provided link to our online inventory (by clicking on the blue-highlighted author name) doesn't work! Milestones of Science Books phone +49 (0) 177 – 2 41 0006 www.milestone-books.de [email protected] Member of ILAB and VDA Catalogue 07-2019 Copyright © 2019 Milestones of Science Books. All rights reserved Page 2 of 71 Authors in Chronological Order Author Year No. Author Year No. BIRT, William 1869 7 SCHEINER, Christoph 1614 72 PROCTOR, Richard 1873 66 WILKINS, John 1640 87 NASMYTH, James 1874 58, 59, 60, 61 SCHYRLEUS DE RHEITA, Anton 1645 77 NEISON, Edmund 1876 62, 63 HEVELIUS, Johannes 1647 29 LOHRMANN, Wilhelm 1878 42, 43, 44 RICCIOLI, Giambattista 1651 67 SCHMIDT, Johann 1878 75 GALILEI, Galileo 1653 22 WEINEK, Ladislaus 1885 84 KIRCHER, Athanasius 1660 31 PRINZ, Wilhelm 1894 65 CHERUBIN D'ORLEANS, Capuchin 1671 8 ELGER, Thomas Gwyn 1895 15 EIMMART, Georg Christoph 1696 14 FAUTH, Philipp 1895 17 KEILL, John 1718 30 KRIEGER, Johann 1898 33 BIANCHINI, Francesco 1728 6 LOEWY, Maurice 1899 39, 40 DOPPELMAYR, Johann Gabriel 1730 11 FRANZ, Julius Heinrich 1901 21 MAUPERTUIS, Pierre Louis 1741 50 PICKERING, William 1904 64 WOLFF, Christian von 1747 88 FAUTH, Philipp 1907 18 CLAIRAUT, Alexis-Claude 1765 9 GOODACRE, Walter 1910 23 MAYER, Johann Tobias 1770 51 KRIEGER, Johann 1912 34 SAVOY, Gaspare 1770 71 LE MORVAN, Charles 1914 37 EULER, Leonhard 1772 16 WEGENER, Alfred 1921 83 MAYER, Johann Tobias 1775 52 GOODACRE, Walter 1931 24 SCHRÖTER, Johann Hieronymus 1791 76 FAUTH, Philipp 1932 19 GRUITHUISEN, Franz von Paula 1825 25 WILKINS, Hugh Percy 1937 86 LOHRMANN, Wilhelm Gotthelf 1824 41 USSR ACADEMY 1959 1 BEER, Wilhelm 1834 4 ARTHUR, David 1960 3 BEER, Wilhelm 1837 5 HACKMAN, Robert 1960 27 MÄDLER, Johann Heinrich 1837 49 KUIPER Gerard P. -
Expressions of Climate Perturbations in Western Ugandan Crater Table 3
EGU Journal Logos (RGB) Open Access Open Access Open Access Advances in Annales Nonlinear Processes Geosciences Geophysicae in Geophysics Open Access Open Access Natural Hazards Natural Hazards and Earth System and Earth System Sciences Sciences Discussions Open Access Open Access Atmospheric Atmospheric Chemistry Chemistry and Physics and Physics Discussions Open Access Open Access Atmospheric Atmospheric Measurement Measurement Techniques Techniques Discussions Open Access Open Access Biogeosciences Biogeosciences Discussions Discussion Paper | Discussion Paper | Discussion Paper | Discussion Paper | Open Access Open Access Clim. Past Discuss., 9, 5183–5226, 2013 Climate www.clim-past-discuss.net/9/5183/2013/ Climate CPD doi:10.5194/cpd-9-5183-2013 of the Past of the Past © Author(s) 2013. CC Attribution 3.0 License. Discussions 9, 5183–5226, 2013 Open Access Open Access This discussion paper is/has been under review for the journal ClimateEarth of the System Past (CP). Earth System Expressions of Please refer to the corresponding final paper in CP if available. Dynamics Dynamics climate perturbations Discussions in western Ugandan Open Access ExpressionsGeoscientific of climate perturbationsGeoscientific inOpen Access crater Instrumentation Instrumentation K. Mills et al. western UgandanMethods and crater lake sedimentMethods and Data Systems Data Systems records during the last 1000 yr Discussions Open Access Open Access Title Page Geoscientific 1,2 1Geoscientific 1 3 4 K. Mills , D. B. Ryves , N. J. Anderson , C. L. BryantModel, and -
Intrepid Travel Company Travel, You Can Rest Assured You’Re Travelling to Improve the Planet
2020 AFRICA & THE MIDDLE EAST SMALL LOCAL SUSTAINABLE GROUPS LEADERS TRAVEL WeIntrepid are all Every Intrepid adventure starts with curiosity. A desire to understand, to learn something new, to challenge beliefs and push boundaries. To switch on our out-of-office alerts, to say farewell to daily routines, to have fun. For some, being Intrepid means trying a dish they can’t pronounce, or learning the salsa in a Cuban bar. It’s climbing a mountain, or an encounter with a silverback gorilla. For others, it’s packing for a solo adventure, getting out of that bubble of familiarity, and making new friends in all corners of the globe. Whether you’ve been travelling for years or you’ve never left home, we want to lead you to those moments of discovery, to satisfy that curiosity, to be Intrepid. Because now, more than ever, the world needs more Intrepid people. more destinations, more ways to travel We run thousands of trips in a range of styles 01 and visit every continent on earth. And we do it all with our signature attention to detail and passion for real life experiences. Our destination experts are constantly scouring the globe for Why sights and experiences to share – so you can discover your choose new favourite place, or explore a guidebook staple Intrepid from a new perspective. 04 Luxor, Egypt The ultimate Legendary 03 itineraries local leaders We know this is your trip of a lifetime, and we’re Get ready to go beyond the main streets committed to making it unforgettable. Our and into the heart of a destination. -
50 Years of Petrology
spe500-01 1st pgs page 1 The Geological Society of America 18888 201320 Special Paper 500 2013 CELEBRATING ADVANCES IN GEOSCIENCE Plates, planets, and phase changes: 50 years of petrology David Walker* Department of Earth and Environmental Sciences, Lamont-Doherty Earth Observatory, Columbia University, Palisades, New York 10964, USA ABSTRACT Three advances of the previous half-century fundamentally altered petrology, along with the rest of the Earth sciences. Planetary exploration, plate tectonics, and a plethora of new tools all changed the way we understand, and the way we explore, our natural world. And yet the same large questions in petrology remain the same large questions. We now have more information and understanding, but we still wish to know the following. How do we account for the variety of rock types that are found? What does the variety and distribution of these materials in time and space tell us? Have there been secular changes to these patterns, and are there future implications? This review examines these bigger questions in the context of our new understand- ings and suggests the extent to which these questions have been answered. We now do know how the early evolution of planets can proceed from examples other than Earth, how the broad rock cycle of the present plate tectonic regime of Earth works, how the lithosphere atmosphere hydrosphere and biosphere have some connections to each other, and how our resources depend on all these things. We have learned that small planets, whose early histories have not been erased, go through a wholesale igneous processing essentially coeval with their formation. -
Martian Subsurface Properties and Crater Formation Processes Inferred from Fresh Impact Crater Geometries
Martian Subsurface Properties and Crater Formation Processes Inferred From Fresh Impact Crater Geometries The Harvard community has made this article openly available. Please share how this access benefits you. Your story matters Citation Stewart, Sarah T., and Gregory J. Valiant. 2006. Martian subsurface properties and crater formation processes inferred from fresh impact crater geometries. Meteoritics and Planetary Sciences 41: 1509-1537. Published Version http://meteoritics.org/ Citable link http://nrs.harvard.edu/urn-3:HUL.InstRepos:4727301 Terms of Use This article was downloaded from Harvard University’s DASH repository, and is made available under the terms and conditions applicable to Other Posted Material, as set forth at http:// nrs.harvard.edu/urn-3:HUL.InstRepos:dash.current.terms-of- use#LAA Meteoritics & Planetary Science 41, Nr 10, 1509–1537 (2006) Abstract available online at http://meteoritics.org Martian subsurface properties and crater formation processes inferred from fresh impact crater geometries Sarah T. STEWART* and Gregory J. VALIANT Department of Earth and Planetary Sciences, Harvard University, 20 Oxford Street, Cambridge, Massachusetts 02138, USA *Corresponding author. E-mail: [email protected] (Received 22 October 2005; revision accepted 30 June 2006) Abstract–The geometry of simple impact craters reflects the properties of the target materials, and the diverse range of fluidized morphologies observed in Martian ejecta blankets are controlled by the near-surface composition and the climate at the time of impact. Using the Mars Orbiter Laser Altimeter (MOLA) data set, quantitative information about the strength of the upper crust and the dynamics of Martian ejecta blankets may be derived from crater geometry measurements.