Experimental Determination of Temperature During Rotary Friction
Total Page:16
File Type:pdf, Size:1020Kb
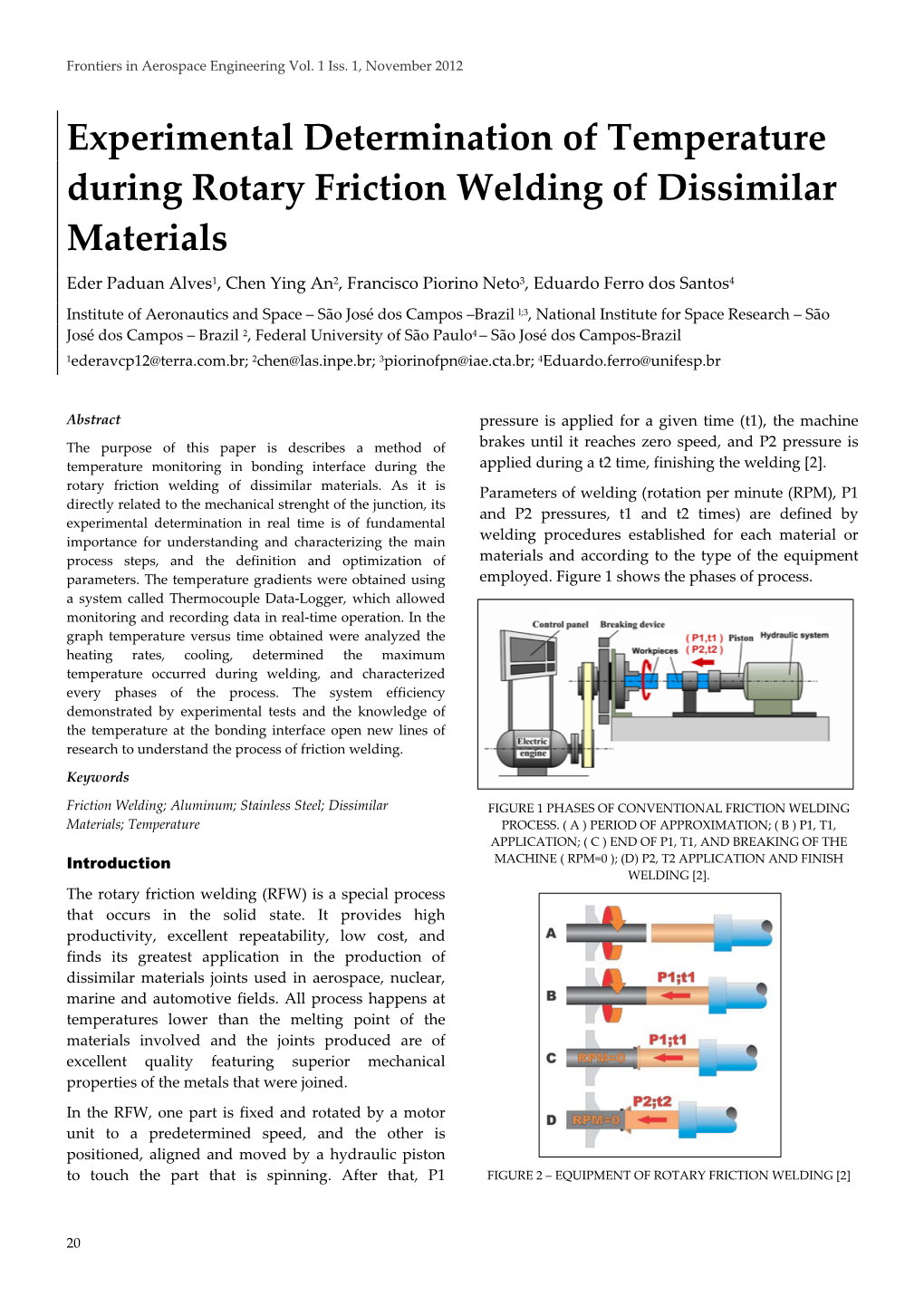
Load more
Recommended publications
-
The Influence of Rotational Speed and Pressure on the Properties of Rotary Friction Welded Titanium Alloy (Ti‐6Al‐4V)
View metadata, citation and similar papers at core.ac.uk brought to you by CORE provided by University of Johannesburg Institutional Repository The influence of rotational speed and pressure on the properties of rotary friction welded Titanium alloy (Ti‐6Al‐4V) MC Zulua and PM Mashininib aUniversity of Johannesburg, Depertment of Mechanical and Industrial Engineering Technology, Doornfontein campus, Johannesburg, 2028, South Africa bUniversity of Johannesburg, Depertment of Mechanical and Industrial Engineering Technology, Doornfontein campus, Johannesburg, 2028, South Africa email address : 215086813student.uj.ac.zaa, [email protected] Abstract This paper presents an investigation of rotary friction welding of 25.4 mm diameter Ti‐6Al‐4V rods. The weld process parameters used for this research were rotational speed, axial pressure and forging time. Only relative speed and axial pressure were the varied parameters while the forging time was kept constant. The mechanical properties of the weld joints were analysed and characterized. The results showed that the rotational speed and friction pressure have significant influence on the tensile strength, microstructure and weld integrity. As rotational speed increased heating time also increased in the weld, as a result, greater volume of material was affected by heat resulting in a wider width of the weld joint. Fine microstructure resulted due to an increased rotational speed and frictional pressure respectively. The oxidation and discolouration of welds were also discussed. Keywords: Rotary friction welding; process parameters; Ti‐6Al‐4V; microstructure; mechanical properties 1. Introduction Titanium alloys are non‐ferrous materials that can be welded by diverse types of welding techniques. Most of the welding processes that have been used in the past with success in joining of Titanium alloys were limited to conventional welding methods [1]. -
Study on the Effect of Energy-Input on the Joint Mechanical Properties of Rotary Friction-Welding
metals Article Study on the Effect of Energy-Input on the Joint Mechanical Properties of Rotary Friction-Welding Guilong Wang 1,2, Jinglong Li 1, Weilong Wang 1, Jiangtao Xiong 1 and Fusheng Zhang 1,* 1 Shaanxi Key Laboratory of Friction Welding Technologies, Northwestern Polytechnical University, Xi’an 710072, China; [email protected] (G.W.); [email protected] (J.L.); [email protected] (W.W.); [email protected] (J.X.) 2 State Key Laboratory of Solidification Processing, Northwestern Polytechnical University, Xi’an 710072, China * Correspondence: [email protected]; Tel.: +86-029-8849-1426 Received: 17 October 2018; Accepted: 3 November 2018; Published: 6 November 2018 Abstract: The objective of the present study is to investigate the effect of energy-input on the mechanical properties of a 304 stainless-steel joint welded by continuous-drive rotary friction-welding (RFW). RFW experiments were conducted over a wide range of welding parameters (welding pressure: 25–200 MPa, rotation speed: 500–2300 rpm, welding time: 4–20 s, and forging pressure: 100–200 MPa). The results show that the energy-input has a significant effect on the tensile strength of RFW joints. With the increase of energy-input, the tensile strength rapidly increases until reaching the maximum value and then slightly decreases. An empirical model for energy-input was established based on RFW experiments that cover a wide range of welding parameters. The accuracy of the model was verified by extra RFW experiments. In addition, the model for optimal energy-input of different forging pressures was obtained. To verify the accuracy of the model, the optimal energy-input of a 170 MPa forging pressure was calculated. -
Effect of Speed on Hardness in Rotary Friction Welding Process
International Journal of Materials Science ISSN 0973-4589 Volume 12, Number 4 (2017), pp. 635-641 © Research India Publications http://www.ripublication.com Effect of Speed on Hardness in Rotary Friction Welding Process P. Koteswara Rao1, V. Mohan2, N.Surya3*, G. Sai Krishna Prasad4 1, 2, 3,4Assistant Professor, Department of Mechanical Engineering, TKRCET, Hyderabad, Telangana, India. Abstract Aim of this paper was to determine the hardness in rotary friction welding by varying speed. It is a solid state welding technology to join material by applying linear force to join the materials. The work was carried out on modified conventional lathe machine attached with two self chucks, one is in rotational and another one is fixed. The material diameter was used 10 & 14 mm in diameter rods of similar and dissimilar material with four combination of set (MS-MS, MS-Al, Cu-Brass, and Al-Al). It was observed that the value of hardness at HAZ is softer and harder away from the HAZ. Key Term: Lathe Machine; Rotary Friction; Speed; Hardness. INTRODUCTION Friction welding is a solid state joining technique by applying rotational speed and pressure at motion less work piece to join metal without any defect, porosity and no cracks propagation in the weld zone with fine grain structure etc due to thermo mechanical effect [1]. It has wide number of application such as automobile, aerospace, nuclear, electrical, chemical, cryogenic and marine etc [2]. The advantages like no material waste, production time is less and low energy expenditure in it [3]. The factor affecting the weld includes various rotational speeds, frictional load and weld duration [4]. -
Rotary Friction Welding of Inconel 718 to Inconel 600
metals Article Rotary Friction Welding of Inconel 718 to Inconel 600 Ateekh Ur Rehman * , Yusuf Usmani, Ali M. Al-Samhan and Saqib Anwar Department of Industrial Engineering, College of Engineering, King Saud University, Riyadh 11451, Saudi Arabia; [email protected] (Y.U.); [email protected] (A.M.A.-S.); [email protected] (S.A.) * Correspondence: [email protected]; Tel.: +966-1-1469-7177 Abstract: Nickel-based superalloys exhibit excellent high temperature strength, high temperature corrosion and oxidation resistance and creep resistance. They are widely used in high temperature applications in aerospace, power and petrochemical industries. The need for economical and efficient usage of materials often necessitates the joining of dissimilar metals. In this study, dissimilar welding between two different nickel-based superalloys, Inconel 718 and Inconel 600, was attempted using rotary friction welding. Sound metallurgical joints were produced without any unwanted Laves or delta phases at the weld region, which invariably appear in fusion welds. The weld thermal cycle was found to result in significant grain coarsening in the heat effected zone (HAZ) on either side of the dissimilar weld interface due to the prevailing thermal cycles during the welding. However, fine equiaxed grains were observed at the weld interface due to dynamic recrystallization caused by severe plastic deformation at high temperatures. In room temperature tensile tests, the joints were found to fail in the HAZ of Inconel 718 exhibiting good ultimate tensile strength (759 MPa) without a significant loss of tensile ductility (21%). A scanning electron microscopic examination of the fracture surfaces revealed fine dimpled rupture features, suggesting a fracture in a ductile mode. -
Manufacturing Services a Single-Source
MANUFACTURING SERVICES MTI offers an affordable, single-source turnkey solution to accommodate your applications by developing and producing your parts to save MTIwelding.com you time, money, and mitigate risk to your parts program. A SINGLE-SOURCE TURNKEY SOLUTION As one of the world’s largest, most experienced friction welding machine builders and integrators, MTI is positioned to be your single source turnkey solution to any Contract Friction Welding need. By providing you access to an array of in-house value-added services to accommodate your applications, we have the ability to process your parts using the latest in friction welding and part handling technology. We also maintain the widest range of friction welding equipment available. Only MTI offers all three types of rotary friction welding. With over 117,000 square feet of production space, we can produce friction-welded parts ranging anywhere in size. From small military aircraft rivets to 55-foot-long Friction Stir Welds, MTI is uniquely qualified to handle all your contract welding needs with the quality you expect. Take advantage of our in-house value-added services including custom design engineering, research and development resources, and pre- and post-weld processing. TECHNOLOGIES As the world leader in the design, manufacture and installation of Friction Welding machines, MTI is able to offer world-class Friction Welding contract services that include: Rotary Friction Linear Friction Friction Stir Plug Welding Welding Welding Welding QUALITY ASSURANCE We calibrate and maintain our machines to keep them at optimum performance so that your last welded part is of the same high quality as your first. -
Rotary Friction Welding of Molybdenum Components
19th Plansee Seminar RM 70/1 Rotary friction welding of molybdenum components M. Stütz*, F. Pixner*, J. Wagner**, N. Reheis**, E. Raiser***, H. Kestler**, N. Enzinger* * IMAT, Graz University of Technology, Austria ** Plansee SE, 6600 Reutte, Austria *** Klaus Raiser GmbH & Co. KG, Germany Abstract Joining of TZM components by inertia rotary friction welding is an established industrial process, but only for welding cross-sections up to 1,500 mm2. Up-scaling to medium-size components up to 5,000 mm2 in a direct drive variant of the process requires further development and more basic understanding of the welding procedure including weld preforms, the clamping system, and machine parameters. Based on the existing process for TZM tubes, the welding parameters were transferred to tubular components of pure molybdenum (Ø 130 x 10 mm, 4,400 mm2). Successful welds were produced showing a fine-grained, defect-free microstructure. However, molybdenum proved to be more challenging than TZM. Particularly high upset rates and motor overload occurred during the friction phase. Therefore, a more mechanism based weld study was carried out with small-size samples under laboratory conditions. The results showed extensive plasticization of the entire weld zone due to higher thermal diffusivity and lower strength of molybdenum compared to TZM. This high upset rate reduces the process window for a reproducible welding procedure significantly. Moreover, a concentrated energy input during the transition from friction to forge phase is required to countervail the high thermal diffusivity of molybdenum. Based on these observations, the feasibility of friction welding of medium-size molybdenum tubes will be discussed. -
Manufacturing and Assembly of Friction Welding Machine for Aluminium
Int. J. Mech. Eng. & Rob. Res. 2014 P Nandhakumar et al., 2014 ISSN 2278 – 0149 www.ijmerr.com Vol. 3, No. 2, April 2014 © 2014 IJMERR. All Rights Reserved Research Paper MANUFACTURING AND ASSEMBLY OF FRICTION WELDING MACHINE FOR ALUMINIUM G Selvakumar1, R Maguteeswaran1, P Nandhakumar1*, M Sathish1, E Vignesh1 and A Peramanan1 *Corresponding Author: P Nandhakumar, [email protected] Friction welding method is one of the most simple, economical and highly productive methods in joining similar and dissimilar metals. It is widely used in the automotive, aircraft and aerospace industrial applications. For many applications it is often necessary to join aluminium (6061) to make finished part. In this project the main aim is to weld the small thickness of aluminum (6061) plates for that friction welding machine used is of higher cost. Here the aim is reduce the cost of friction welding machine with simple parts like three phase A.C induction motor, bush, frame stand, friction tool, universal vice, vertical moving bed, horizontal moving bed, etc. The result expected would be of same strength as that of old friction welding machine. It is very easy and at same time production time is very much reduced. This machine is best suitable for mass production. Keywords: Aluminium, Friction tool, Production INTRODUCTION frames, structural work, tanks, furniture, boilers, general repair work and ship building. At most Welding in all metal working industries welding is used. Welding is a process of joining similar metals by the application of heat. Welding can be Welding Defined done with or without the application of Welding is define by the American Welding pressure. -
A Review Paper on Rotary Friction Welding Nisarg Shete1, S
International Conference on Ideas, Impact and Innovation in Mechanical Engineering (ICIIIME 2017) ISSN: 2321-8169 Volume: 5 Issue: 6 1557 – 1560 _____________________________________________________________________________________________ A Review Paper on Rotary Friction Welding Nisarg Shete1, S. U. Deokar2 1Undergraduate, Department of Mechanical Engineering,SKNCOE Vadgaon , [email protected] 2Asst. Prof., Department of Mechanical Engineering, SKNCOE Vadgaon, [email protected] ABSTRACT Friction welding is a non-conventional pressure welding process It is considered most viable alternative to overcome the difficulties faced in conventional joining technique. Mostly used for joining material with varying physical and mechanical properties. We have mainly focused on Rotary Friction Welding (RFW). Our main objective is to understand the fundamental understanding of Friction Welding. In this process kinetic energy is converted into heat energy thereby producing high quality weld and unusually high efficiency coefficient. Keywords: Friction, Continuous-drive Friction Welding (CDFW), Inertial Friction Welding (IFW), Rotary Friction Welding (RFW) ----------------------------------------------------------------------------------------------------------------------------- 1. Introduction Friction Welding is a variation of pressure welding method, in which the welded connection is formed without melting the metal, by joint plastic deformation of the pieces to be welded with the help of heat resulting from friction. Here we generate large amount of localised intense heat generation and deformation results in less energy consumption and highly strong weld. As it is a solid state welding process the process does not form molten pool thereby eliminating the solidification errors. FW can join two different materials having different thermal and mechanical properties without compromising the strength of weld. FW is preferred over conventional processes because of low cost, highly precise operations, repeatability and reliability. -
Recent Industrial Scenario of Rotary Friction Welding
International Journal for Research in Engineering Application & Management (IJREAM) ISSN : 2454-9150 Special Issue - AMET-2019 Recent Industrial Scenario Of Rotary Friction Welding Technology and It’s Applications - A Review 1Rajsing Pardeshi, 2Pramod Patil, 3Saurabh Surashe, 4Pravin Shinde, 5Prof. V.V. Kulkarni 5Assistant professor, (Workshop), MITCOE, Kothrud, Pune, India. [email protected], [email protected], [email protected], [email protected], [email protected] ABSTRACT: Friction welding which was first applied to cutting tools in metal processing industry has found several applications. Friction welding obtained by frictional heat & it’s a commercial process, friction welding has found several applications in different manufacturing processes with the advancement in technology. The first studies of friction welding in England were carried out by the Welding Institute in 1961.By modifying the friction welding; the Caterpillar Tractor Co. in the USA developed the method of inertia welding in 1962. Many researchers are still working on the thermal analysis and basic parameter, tool development of various types of friction welding processes. With these advances, it has found several applications in Engineering, Naval & offshore industry. Friction welding is used welding process in industries like automobile industries, aeronautical industries etc. and heavy duty industries. In this literature review paper the various processes and applications of friction welding has discussed theoretically. Keywords: Rotary friction, linear friction, Inertia friction, Friction stirs welding. I. INTRODUCTION circular rods. Rotary friction welding is a type of friction welding in which one component is rotated against the Friction welding is a solid state welding process or it is also other; it is the most commonly used process among the called as a forge welding, where welding takes place by the friction welding. -
Friction Welding of Aluminium Alloy 6063 with Copper
E3S Web of Conferences 170, 02004 (2020) https://doi.org/10.1051/ e3s conf/202017002004 EVF'2019 Friction welding of Aluminium Alloy 6063 with copper Yashwant Chapke1,*, Dinesh Kamble1 ,and Saoud Md. Salim Shaikh2 1Vishwakarma Institute of Information Technology, Pune 411048, India 2Sinhgad Academy of Engineering, Pune 411048, India. Abstract Friction welding process is a forging welding process in which work piece are joined due to heat produced by friction between two joining surfaces and upset pressure is applied by non-rotating work piece. Joining of aluminum alloy with dissimilar material is important research area to focus on as maximum aircraft structures havexx Aluminum alloy frame and aerospace designers familiar with Aluminum alloy and its design considerations. After comparison of mechanical properties and application of light weight alloys aluminum alloys, tungsten, stainless steel and copper, copper selected as dissimilar material to join with Aluminum alloy AA6063. AA 6063 also known as architectural alloy selected based upon its properties. This dissimilar joint of AA6063 and Copper has application in electrical conductors as copper is good electrical conductivity and used in maximum electrical conductors. In this research work AA6063 joined with Copper successfully using Rotary Friction Welding process. Through process study effective process parameters like Friction Pressure, Upset Pressure, Spindle Speed, and Friction Time identified and their effect on weld joint strength were studied.Testing for measuring UTS of friction welded joint conducted. Using DOE tool optimized set process parameters for friction welding identified and their effect on weld joint strength studied experimentally. Maximum UTS of 222.787 MPa for Friction welded joint achieved, bend test also performed on friction welded samples. -
Technical Report 09-05
nagra Technical Report 09-05 Critical Review of Welding Technology for Canisters for Disposal of Spent Fuel and High LevelWaste March 2010 5. Pike, C. Allen, C. Punshon, P. Threadgill, M. Gallegillo, B. Holmes, J. Nicholas TWI, Ltd. National Cooperative forthe Disposal of Radioactive Waste Hardstrasse 73 CH-5430 Wettingen Switzerland Tel. +41 56 437 1 1 1 1 www.nagra.ch nagra Technical Report 09-05 Critical Review of Welding Technology for Canisters for Disposal of Spent Fuel and High LevelWaste March 2010 5. Pike, C. Allen, C. Punshon, P. Threadgill, M. Gallegillo, B. Holmes, J. Nicholas TWI, Ltd. National Cooperative forthe Disposal of Radioactive Waste Hardstrasse 73 CH-5430 Wettingen Switzerland Tel. +41 56437 11 11 www.nagra.ch This report was prepared on behalf of Nagra. The viewpoints presented and conclusions reached are those of the author(s) and do not necessarily represent those of Nagra. ISSN 1015-2636 "Copyright © 2010 by Nagra, Wettingen (Switzerland)/All rights reserved. All parts of this work are protected by copyright. Any utilisation outwith the remit of the copyright law is unlawful and liable to prosecution. This applies in particular to translations, storage and processing in electronic systems and programs, microfilms, reproductions, etc." I NAGRA NTB 09-05 Executive Summary Background Nagra is the Swiss national cooperative for the disposal of radioactive waste and is responsible for final disposal of all types of radioactive waste produced in Switzerland. As part of Nagra's long term disposal strategy, plans must be developed for two repositories, one for spent fuel (SF), vitrified high-level waste (HLW) and long-lived intermediate level waste and one for low and intermediate level waste. -
Welded Joints of Low and Medium Carbon Steels, Applying Rotary Friction
International Journal of Recent Technology and Engineering (IJRTE) ISSN: 2277-3878, Volume-8 Issue-6, March 2020 Mechanical Properties and Microstructure, in welded joints of Low and Medium Carbon Steels, Applying Rotary Friction Víctor Alcántara Alza Abstract: The effect of friction welding (FRW) in joints of It is a very advantageous alternative to fusion welds, which medium and low carbon steels on its mechanical properties and presents many defects due rapid cooling, such as porosities, microstructure was studied. AISI 1020 and 1045 steel bars of 12 residual stresses, and fatigue cracks, that start at the foot of mm diameter were used. Welding was carried out on a lathe with the weld and spread through the heat affected zone (HAZ), coupling to control the process parameters. For 1045/1045 joint, the following parameters were used: n = 1400 rpm, Friction depending on the geometry of the joint [5], [6]. All these pressure Pf = (0.8 - 1.0) MPa; Friction time (Tf) = 8 sec; defects or failures cannot be eliminated, but can be reduced Upsetting pressure (Pr) = 5 MPa; Upsetting time (Tr) = 5 sec, with post welding methods that increase production costs. were used. For 1020/1045 joints the parameters that only varied For this reason, solid state welding methods have been were: n = (1000 - 1400) rpm; Pf = (0.7-0.8-1.0) MPa. Tensile tests developed that mitigate these failures that can be catastrophic were carried out on the IMSTRON UNIVERSAL machine under [7]. ASTM E8 standard. Microhardness tests were carried out on There are several methods of friction welding, whose (HV) 0.5 scale, making a longitudinal and transverse scanning application depends on the type of joint and the geometry of profile.